聚合物基复合材料的成型工艺
3- 手糊成型工艺

胶液粘度 凝胶时间
配制时需注意: 防止胶液中混入气泡; 配胶量不能过多,每次配量要保证 在树脂凝胶前用完。
④增强材料准备: • • • •
玻璃纤维及其织物 碳纤维 芳纶纤维 其它增强材料 增强材料的种类和规格按设计要求选择。
3.1.2 糊制
1. 表面层
胶衣树脂
3.1.2 糊制
2. 结构层的糊制
固化方法 加热固化方法很多,中小型制品可 在固化炉内加热固化,大型制品可采用 模内加热或红外线加热。
3.1.4 脱模和修整
脱模要保证制品不受损伤。 脱模方法:①顶出脱模 ②压力脱模 ③大型制品 ④复杂制品
脱模
①顶出脱模: 在模具上预埋顶出装置,脱模时转动螺 杆,将制品顶出。
脱模
②压力脱模: 模具上留有压缩空气或水入口,脱 模时将压缩空气或水压入模具和制品之间,同 时用木锤和橡胶锤敲打,使制品和模具分离。
3.1.5 手糊制品厚度与层数计算
(1)手糊制品厚度的预测
t=m×k t-制品厚度 m-材料质量 k-厚度常数
(2)层数计算
医用核磁共振机外壳
化纤公司大型污水池(FRP衬里)
某有色冶炼厂电解铜车间电解槽
2. 设备简单,投资少。 3. 工艺简单。 4. 易于满足产品设计要求。 5. 制品树脂含量较高,耐腐蚀性好。
手糊工艺的缺点
生产效率低,劳动强度大。 产品质量不易控制。 产品性能较低。
3.1.1 手糊成型的准备
①场地 ②模具准备 ③树脂胶液配制 ④增强材料准备
①场地:
手糊成型工作场地的大小,要根据产 品大小和产量决定。 场地要求清洁、干燥、通风良好, 空气温度应保持在15~35℃之间,后加 工整修段,要设有抽风除尘装置。
聚合物基复合材料的设计制备
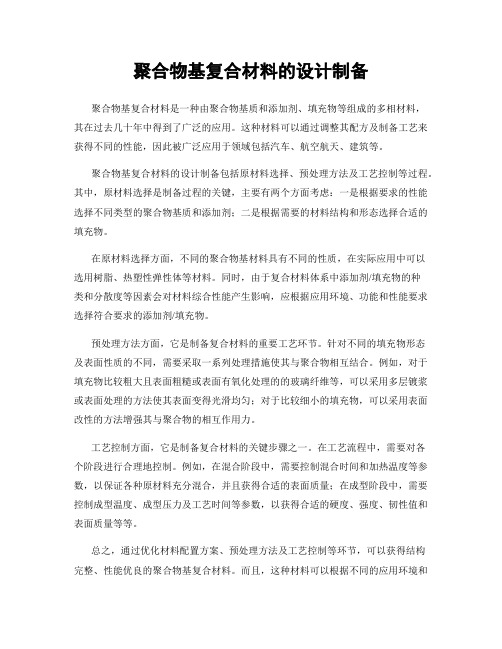
聚合物基复合材料的设计制备聚合物基复合材料是一种由聚合物基质和添加剂、填充物等组成的多相材料,其在过去几十年中得到了广泛的应用。
这种材料可以通过调整其配方及制备工艺来获得不同的性能,因此被广泛应用于领域包括汽车、航空航天、建筑等。
聚合物基复合材料的设计制备包括原材料选择、预处理方法及工艺控制等过程。
其中,原材料选择是制备过程的关键,主要有两个方面考虑:一是根据要求的性能选择不同类型的聚合物基质和添加剂;二是根据需要的材料结构和形态选择合适的填充物。
在原材料选择方面,不同的聚合物基材料具有不同的性质,在实际应用中可以选用树脂、热塑性弹性体等材料。
同时,由于复合材料体系中添加剂/填充物的种类和分散度等因素会对材料综合性能产生影响,应根据应用环境、功能和性能要求选择符合要求的添加剂/填充物。
预处理方法方面,它是制备复合材料的重要工艺环节。
针对不同的填充物形态及表面性质的不同,需要采取一系列处理措施使其与聚合物相互结合。
例如,对于填充物比较粗大且表面粗糙或表面有氧化处理的的玻璃纤维等,可以采用多层镀浆或表面处理的方法使其表面变得光滑均匀;对于比较细小的填充物,可以采用表面改性的方法增强其与聚合物的相互作用力。
工艺控制方面,它是制备复合材料的关键步骤之一。
在工艺流程中,需要对各个阶段进行合理地控制。
例如,在混合阶段中,需要控制混合时间和加热温度等参数,以保证各种原材料充分混合,并且获得合适的表面质量;在成型阶段中,需要控制成型温度、成型压力及工艺时间等参数,以获得合适的硬度、强度、韧性值和表面质量等等。
总之,通过优化材料配置方案、预处理方法及工艺控制等环节,可以获得结构完整、性能优良的聚合物基复合材料。
而且,这种材料可以根据不同的应用环境和需求进行调整,因此具有良好的可塑性和适应性。
在实际应用中,聚合物基复合材料的应用前景非常广阔,预计未来会有更多的领域会应用这种材料。
聚合物复合材料工艺课件
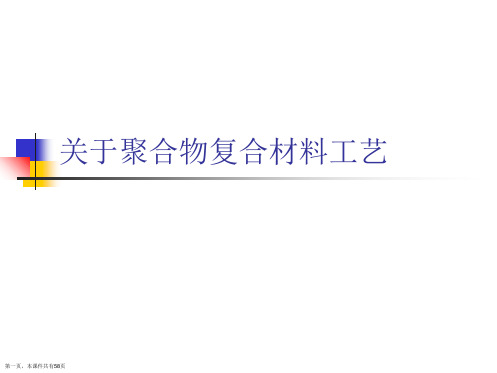
关于聚合物复合材料工艺
第一页,本课件共有58页
料将增强材料粘结在一起的一种成型方法 。
在模具上涂刷含有固化剂的树脂混合物,再在其上铺贴一层按要求剪裁好
的纤维织物,用刷子、压辊或刮刀压挤织物,使其均匀浸胶并排除气泡后,再涂刷树
脂混合物和铺贴第二层纤维织物,反复上述过程直至达到所需厚度为止,然后进行 固化、脱模、后处理及检验等。
第十页,本课件共有58页
第二十一页,本课件共有58页
第二十二页,本课件共有58页
普通列车的前端
普通列车前端体积大,结构较为复杂,
通常采用喷射成型制得
(3) 缠绕成型
芯模
缠绕控制
小车及树脂
纤维
缠绕成型是一种将浸渍了树脂的连续纤维(预浸纱、丝束或布带)通 过缠绕机控制张力和缠绕角,以一定方式按照一定规律缠绕在回转芯模上、 常压下在室温或较高温度下固化成型的一种复合材料制造工艺。
第十一页,本课件共有58页
手糊成型工艺流程
手糊成型常用的树脂体系有不饱和聚酯树脂胶液、环氧树脂胶液;33号胶 衣树脂(间苯二甲酸型胶衣树脂),耐水性好;36PA胶衣树脂,自熄性胶衣树脂( 不透明);39号胶衣树脂,耐热自熄性胶衣树脂;21号胶衣树脂(新戊二醇型) ,耐水煮、耐热、耐污染、柔韧、耐磨胶衣。
第4章 聚合物基复合材料的工艺
4.1 概述 4.2 成型工艺方法 4.3 模具与辅助材料 4.4 复合材料成型用半成品的制备工艺
聚合物基复合材料成型
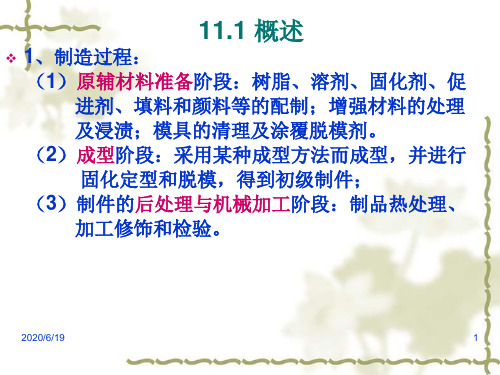
❖ 1、制造过程: (1)原辅材料准备阶段:树脂、溶剂、固化剂、促 进剂、填料和颜料等的配制;增强材料的处理 及浸渍;模具的清理及涂覆脱模剂。 (2)成型阶段:采用某种成型方法而成型,并进行 固化定型和脱模,得到初级制件; (3)制件的后处理与机械加工阶段:制品热处理、 加工修饰和检验。
2020/手糊成型 (2)模压成型 (3)层压或卷制成型 (4)缠绕成型 (5)拉挤成型 (6)离心浇铸成型 (7)树脂传递成型 (8)夹层结构成型 (9)喷射成型(10)真空浸胶成型
(11)挤出成型 (12)注射成型 (13)热塑性片状模塑料热冲压成型
2020/6/19
2020/6/19
8
❖ 2.脱模剂
脱模剂的使用温度应高于固化温度。
脱模剂分外脱模剂和内脱模剂两大类。外脱模剂主要应 用于手糊成型和冷固化系统,内脱模剂主要用于模压成型和 热固化系统。
2020/6/19
9
❖ 11.2.3 手糊工艺过程 1.原材料准备 1)胶液准备 胶液的工艺性:胶液粘度和凝胶时间。 粘度过高不易涂刷和浸透增强材料;粘度过低,在树脂凝胶
(2)石膏和砂:砂:石膏=1:8,加入20%水,混合均匀后制 模。模具制造简单,造价低。但不耐用,易吸湿,模具表面也 需进行封孔处理。适合量少或形状复杂制品。
(3)石蜡:适合形状复杂数量小的制品。 (4)可溶性盐:由磷酸铝(60%~70%)、碳酸钠(30%~40%)、
偏硼酸钠(5%~8%)、石英粉(2%)等组分(质量比),加工成粉 料压制烧结成型。在80℃水中能迅速溶解脱模。用于形状复杂 不易脱模的制品。 (5)低熔点金属:由58%的铋与42%的锡(质量比)制成,熔点 为135℃,制模周期短,可重复使用。 (6)金属:常用的有钢材、铸铝等(不能用铜)。模具不变形,精 度高。适用于大批量小型高精度制品,因制造周期长、成本高。
聚合物基复合材料复习要点 热固性复合材料成型工艺
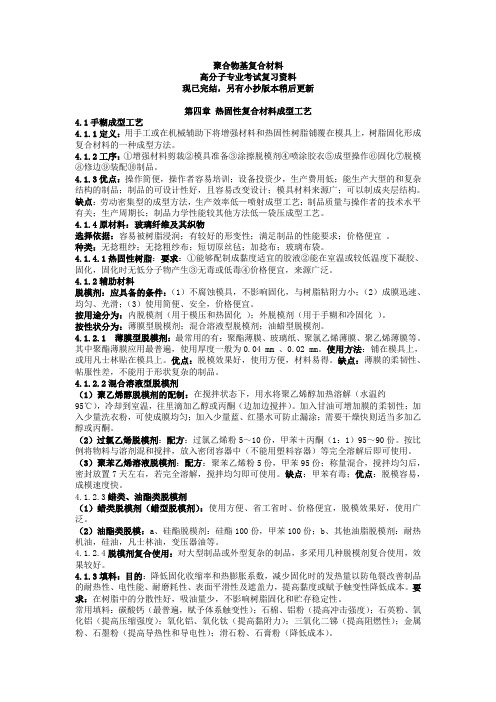
聚合物基复合材料高分子专业考试复习资料现已完结,另有小抄版本稍后更新第四章热固性复合材料成型工艺4.1手糊成型工艺4.1.1定义:用手工或在机械辅助下将增强材料和热固性树脂铺覆在模具上,树脂固化形成复合材料的一种成型方法。
4.1.2工序:①增强材料剪裁②模具准备③涂擦脱模剂④喷涂胶衣⑤成型操作⑥固化⑦脱模⑧修边⑨装配⑩制品。
4.1.3优点:操作简便,操作者容易培训;设备投资少,生产费用低;能生产大型的和复杂结构的制品;制品的可设计性好,且容易改变设计;模具材料来源广;可以制成夹层结构。
缺点:劳动密集型的成型方法,生产效率低—喷射成型工艺;制品质量与操作者的技术水平有关;生产周期长;制品力学性能较其他方法低—袋压成型工艺。
4.1.4原材料:玻璃纤维及其织物选择依据:容易被树脂浸润;有较好的形变性;满足制品的性能要求;价格便宜。
种类:无捻粗纱;无捻粗纱布;短切原丝毡;加捻布;玻璃布袋。
4.1.4.1热固性树脂:要求:①能够配制成黏度适宜的胶液②能在室温或较低温度下凝胶、固化,固化时无低分子物产生③无毒或低毒④价格便宜,来源广泛。
4.1.2辅助材料脱模剂:应具备的条件:(1)不腐蚀模具,不影响固化,与树脂粘附力小;(2)成膜迅速、均匀、光滑;(3)使用简便、安全,价格便宜。
按用途分为:内脱模剂(用于模压和热固化);外脱模剂(用于手糊和冷固化)。
按性状分为:薄膜型脱模剂;混合溶液型脱模剂;油蜡型脱模剂。
4.1.2.1 薄膜型脱模剂:最常用的有:聚酯薄膜、玻璃纸、聚氯乙烯薄膜、聚乙烯薄膜等。
其中聚酯薄膜应用最普遍,使用厚度一般为0.04 mm 、0.02 mm。
使用方法:铺在模具上,或用凡士林贴在模具上。
优点:脱模效果好,使用方便,材料易得。
缺点:薄膜的柔韧性、帖服性差,不能用于形状复杂的制品。
4.1.2.2混合溶液型脱模剂(1)聚乙烯醇脱模剂的配制:在搅拌状态下,用水将聚乙烯醇加热溶解(水温约95℃),冷却到室温,往里滴加乙醇或丙酮(边加边搅拌)。
聚合物基复合材料

聚合物基复合材料
聚合物基复合材料是一种由聚合物基体(如聚合物树脂)和强化材料(如纤维、颗粒等)组成的复合材料。
这种复合材料结合了聚合物的可塑性和强度,以及强化材料的刚度和强度,具有优异的力学性能和工程性能。
聚合物基复合材料的制备通常包括以下几个步骤:
1. 选择合适的聚合物基体,常用的包括聚丙烯、聚酯、环氧树脂等。
2. 选择适当的强化材料,常用的有玻璃纤维、碳纤维、纳米颗粒等。
3. 基体和强化材料进行混合,可以通过热压、挤出、注塑等方法将它们混合在一起。
4. 根据需要进行后续的加工和成型,如冷却、切割、修整等。
聚合物基复合材料具有许多优点,包括:
1. 轻质高强度:与金属相比,聚合物基复合材料具有较低的密度和较高的强度,可以实现轻量化设计。
2. 耐腐蚀性:聚合物基复合材料对化学品和湿气的腐蚀性能较好,不容易受到腐蚀和氧化。
3. 良好的耐热性:聚合物基复合材料通常具有较高的耐热性和耐高温性能。
4. 良好的绝缘性能:聚合物基复合材料具有良好的绝缘性能,适用于电气和电子领域。
5. 自润滑性:聚合物基复合材料中的聚合物基体可以提供良好的自润滑性能,减少了摩擦和磨损。
由于聚合物基复合材料具有以上优点,因此广泛应用于航空航天、汽车、建筑、电子、医疗等领域,成为现代工程材料中的重要一类。
聚合物基复合材料制备
聚合物基复合材料制备制备聚合物基复合材料的关键步骤包括材料选择、增强材料表面处理、复合材料制备和后处理。
首先,选择合适的聚合物基体和增强材料非常重要。
聚合物基体的选择应基于所需的力学性能、热稳定性和化学稳定性等要求。
常见的聚合物基体包括聚丙烯(PP)、聚乙烯(PE)、聚酰亚胺(PI)等。
增强材料可以是颗粒状的纳米材料,如纳米氧化硅、纳米氧化铝等;也可以是纤维状的玻璃纤维、碳纤维、天然纤维等;还可以是片状的石墨烯、石墨等。
其次,增强材料表面处理是增强材料与聚合物基体之间相容性的关键。
表面处理可以通过引入活性基团或进行氧化、酯化等化学修饰来改变增强材料的表面性质。
这样能够增加增强材料与聚合物基体之间的黏附力和相容性,从而提高复合材料的力学性能。
接下来,复合材料的制备是将增强材料均匀地分散在聚合物基体中的过程。
常见的制备方法包括熔融法、溶液法和乳液法。
熔融法是将聚合物基体和增强材料一同加热熔融,然后通过挤出或注塑等工艺形成复合材料;溶液法是将增强材料分散在聚合物溶液中,然后通过旋涂、浸渍等方法制备复合材料;乳液法是将增强材料分散在聚合物乳液中,然后通过自由基聚合或电化学聚合形成复合材料。
最后,制备完成的复合材料还需要进行后处理。
后处理包括热固化、冷却、修饰等工艺。
热固化是将复合材料加热至聚合物基体的玻璃转化温度以上,使聚合物基体发生交联反应,以提高复合材料的力学性能;冷却是通过将复合材料快速冷却到室温来获得所需的结构和性能;修饰是为了改善复合材料的表面性质,如增加润湿性、耐磨性等。
总之,聚合物基复合材料的制备是一个多步骤的过程,需要选取合适的材料、进行表面处理、制备复合材料和进行后处理。
通过精细控制这些步骤,可以得到具有优异力学性能、热稳定性和化学稳定性的聚合物基复合材料。
复合材料工艺
F-35
战 斗 机
复合材料进气道 预形件的编织是在一个大心轴上进行的,将其共分为35块, 以便在固化后分别从心轴上取下。心轴是由五层连续石墨 纤维编织而成,局部达八层厚。编织为一种自动化的经纬 编织法,零件表面纤维拉紧。
接触低压成型工艺
• 接触低压成型工艺的特点是以手工铺放增强材料,浸清树 脂,或用简单的工具辅助铺放增强材料和树脂。接触低压 成型工艺的另一特点,是成型过程中不需要施加成型压力 (接触成型),或者只施加较低成型压力(接触成型后施 加0.01~0.7MPa压力,最大压力不超过2.0MPa)。
原理1、纤维路径在整个缠绕过程中不打滑。 原理2、整个成型过程中,纤维不架桥。 原理3、纤维路径与芯模端部相切。
原理4、整条纤维尽可能均匀地完全覆盖芯模。
大型玻璃钢现场微控整体缠绕贮槽、贮罐,缠绕直径 4000mm-10000mm,缠绕长度为3000--12000mm。
(1)干法缠绕
• 干法缠绕是采用经过预浸胶处理的预浸纱或带,在缠绕机上经加热软 化至粘流态后缠绕到芯模上。
模具检验 及涂脱模 剂
图纸资料 胶液配制
玻璃布处理
预浸料制备
湿法铺陈 干法铺陈
装袋
固化炉 热压罐
模具
脱模 制件 加工和 修饰
试验片
检验区
检验
成
品
性能测试
真空袋成型
②真空袋法 此法是将手糊成型未固化的制品,加盖一层橡胶膜,制品处于橡 胶膜和模具之间,密封周边,抽真空(0.05~0.07MPa),使制品中的气泡 和挥发物排除。真空袋成型法由于真空压力较小,故此法仅用于聚酯和环氧 复合材料制品的湿法成型。
1层贴法
2 沉积法
3 缠绕法 4 编织法
聚合物基复合材料的成型工艺流程
聚合物基复合材料的成型工艺流程下载温馨提示:该文档是我店铺精心编制而成,希望大家下载以后,能够帮助大家解决实际的问题。
文档下载后可定制随意修改,请根据实际需要进行相应的调整和使用,谢谢!并且,本店铺为大家提供各种各样类型的实用资料,如教育随笔、日记赏析、句子摘抄、古诗大全、经典美文、话题作文、工作总结、词语解析、文案摘录、其他资料等等,如想了解不同资料格式和写法,敬请关注!Download tips: This document is carefully compiled by theeditor.I hope that after you download them,they can help yousolve practical problems. The document can be customized andmodified after downloading,please adjust and use it according toactual needs, thank you!In addition, our shop provides you with various types ofpractical materials,such as educational essays, diaryappreciation,sentence excerpts,ancient poems,classic articles,topic composition,work summary,word parsing,copy excerpts,other materials and so on,want to know different data formats andwriting methods,please pay attention!聚合物基复合材料的成型工艺流程详解聚合物基复合材料,以其优异的性能和广泛的应用前景,已经成为了现代工业中的重要材料。
聚合物基复合材料的工艺
3.聚合物基复合材料的工艺(重要)(1)预浸料的制备工艺1.热固性预浸料的制备1)溶液浸渍法。
将树脂基体个组分按规定的比例溶解于低沸点的溶剂中,使之成为一定浓度的溶液,然后将纤维束或织物以规定的速度通过基体溶液,使其浸渍上定量的基体溶液,并通过加热除去溶剂,使树脂得到合适的黏性。
2)热熔法。
分为直接熔融法和胶膜压延法。
2.热塑性预浸料制备。
可分为预浸渍技术与后浸渍技术两类。
(2)手糊成型工艺。
先在磨具上涂刷一层脱膜剂,后加入含固化剂树脂混合物,再在其上铺贴一层按要求剪裁好的纤维织物,用刷子、压辊或刮刀压挤织物,使其均匀浸胶并排除气泡,再涂刷树脂混合物和铺贴第二层纤维织物,反复上述过程直至达到所需厚度为止。
然后再固化、脱膜、修边,得到复合材料制品。
(3)模压成型工艺。
是将一定量的预混料或预浸料加入金属对模内,经加热、加压固化成型的方法。
是广泛使用的对热固性树脂和热塑性树脂都适用的纤维复合材料成型方法。
(4)喷射成型工艺。
将分别混有促进剂和引发剂的不饱和聚酯树脂从喷枪两侧测(或在喷枪内混合)喷出,同时将玻璃纤维无捻粗纱用切割机切断并由喷枪中心喷出,与树脂一起均匀沉积到模具上。
持沉积到一定厚度,用手辊滚压,使纤维浸透树脂、压实并除去气泡,最后固化成制品。
(5)连续缠绕工艺。
一种将浸渍了树脂的纱或丝束缠绕在回转芯模上。
常压下在室温或较高温度下固化成型的一种复合材料制造工艺。
是一种生产各种尺寸回转体的简单有效的方法。
(6)注射成型。
将颗粒状树脂、短纤维送入注射腔内,加热熔化、混合均匀,并以一定的挤出压力,注射到温度较低的密闭模具中,经过冷却定型后,开模便得到复合材料制品。
6.陶瓷基复合材料的制备工艺(成型工艺)(1)等静压成型。
一般等静压指的是湿袋式等静压(也叫湿法等静压),就是将粉料装入橡胶或塑料等可变形的容器中,密封后放入液压油或水等流体介质中,加压获得所需的坯体。
(2)热压铸成型。
热压铸成型是将粉料和蜡(或其他有机高分子黏结剂)混合后,加热使蜡(或其他有机高分子黏结剂)熔化,使混合料具有一定流动性,然后将混合料加压注入模具,冷却后即可得到致密的较硬实的坯体。
- 1、下载文档前请自行甄别文档内容的完整性,平台不提供额外的编辑、内容补充、找答案等附加服务。
- 2、"仅部分预览"的文档,不可在线预览部分如存在完整性等问题,可反馈申请退款(可完整预览的文档不适用该条件!)。
- 3、如文档侵犯您的权益,请联系客服反馈,我们会尽快为您处理(人工客服工作时间:9:00-18:30)。
聚合物基复合材料的成型工艺聚合物基复合材料的性能在纤维与树脂体系确定后,主要决定于成型工艺。
成型工艺主要包括以下两个方面:一是成型,即将预浸料按产品的要求,铺置成一定的形状,一般就是产品的形状;二是固化,即把已铺置成一定形状的叠层预浸料,在温度、时间和压力等因素影响下使形状固定下来,并能达到预期的性能要求。
生产中采用的成型工艺(1) 手糊成型(2)注射成型(3)真空袋压法成型(4)挤出成型(5)压力袋成型 (6)纤维缠绕成型(7)树脂注射和树脂传递成型(8)真空辅助树脂注射成型(9)连续板材成型 (10)拉挤成型(11)离心浇铸成型(12)层压或卷制成型(13)夹层结构成型(14)模压成型(15)热塑性片状模塑料热冲压成型(16)喷射成型(1)手糊成型工艺手糊成型工艺是复合材料最早的一种成型方法,也是一种最简单的方法,其具体工艺过程如下:首先,在模具上涂刷含有固化剂的树脂混合物,再在其上铺贴一层按要求剪裁好的纤维织物,用刷子、压辊或刮刀压挤织物,使其均匀浸胶并排除气泡后,再涂刷树脂混合物和铺贴第二层纤维织物,反复上述过程直至达到所需厚度为止。
然后,在一定压力作用下加热固化成型(热压成型)或者利用树脂体系固化时放出的热量固化成型(冷压成型),最后脱模得到复合材料制品。
其工艺流程如下图所示:为了得到良好的脱模效果和理想的制品,同时使用几种脱模剂,可以发挥多种脱模剂的综合性能。
手糊成型工艺优点①不受产品尺寸和形状限制,适宜尺寸大、批量小、形状复杂产品的生产;②设备简单、投资少、设备折旧费低。
③工艺简单;④易于满足产品设计要求,可以在产品不同部位任意增补增强材料⑤制品树脂含量较高,耐腐蚀性好。
手糊成型工艺缺点①生产效率低,劳动强度大,劳动卫生条件差。
②产品质量不易控制,性能稳定性不高。
③产品力学性能较低。
2.模压成型工艺模压成型工艺是一种古老的技术,早在20世纪初就出现了酚醛塑料模压成型。
模压成型是一种对热固性树脂和热塑性树脂都适用的纤维复合材料成型方法。
模压成型工艺过程将定量的模塑料或颗粒状树脂与短纤维的混合物放入敞开的金属对模中,闭模后加热使其熔化,并在压力作用下充满模腔,形成与模腔相同形状的模制品;再经加热使树脂进一步发生交联反应而固化,或者冷却使热塑性树脂硬化,脱模后得到复合材料制品。
模压成型工艺优点模压成型工艺有较高的生产效率,制品尺寸准确,表面光洁,多数结构复杂的制品可一次成型,无需二次加工,制品外观及尺寸的重复性好,容易实现机械化和自动化等。
模压成型工艺缺点模具设计制造复杂,压机及模具投资高,制品尺寸受设备限制,一般只适合制造批量大的中、小型制品。
模压成型工艺已成为复合材料的重要成型方法,在各种成型工艺中所占比例仅次于手糊/喷射和连续成型,居第三位。
近年来随着专业化、自动化和生产效率的提高,制品成本不断降低,使用范围越来越广泛。
模压制品主要用作结构件、连接件、防护件和电气绝缘等,广泛应用于工业、农业、交通运输、电气、化工、建筑、机械等领域。
由于模压制品质量可靠,在兵器、飞机、导弹、卫星上也都得到应用。
3. 层压成型工艺层压成型工艺,是把一定层数的浸胶布(纸)叠在一起,送入多层液压机,在一定的温度和压力下压制成板材的工艺。
层压成型工艺属于干法压力成型范畴,是复合材料的一种主要成型工艺。
层压成型工艺生产的制品包括各种绝缘材料板、人造木板、塑料贴面板、覆铜箔层压板等。
复合材料层压板的生产工艺流程如下层压成型工艺的优点是制品表面光洁、质量较好且稳定以及生产效率较高。
层压成型工艺的缺点是只能生产板材,且产品的尺寸大小受设备的限制。
4.喷射成型工艺将分别混有促进剂和引发剂的不饱和聚酯树脂从喷枪两侧(或在喷枪内混合)喷出,同时将玻璃纤维无捻粗纱用切割机切断并由喷枪中心喷出,与树脂一起均匀沉积到模具上。
当不饱和聚酯树脂与玻璃纤维无捻粗纱混合沉积到一定厚度时,用手辊滚压,使纤维浸透树脂、压实并除去气泡,最后固化成制品。
其具体工艺流程图如下:喷射成型对所用原材料有一定要求,例如树脂体系的粘度应适中,容易喷射雾化、脱除气泡和浸润纤维以及不带静电等。
最常用的树脂是在室温或稍高温度下即可固化的不饱和聚酯等。
喷射法使用的模具与手糊法类似,而生产效率可提高数倍,劳动强度降低,能够制作大尺寸制品。
用喷射成型方法虽然可以制成复杂形状的制品,但其厚度和纤维含量都较难精确控制,树脂含量一般在60%以上,孔隙率较高,制品强度较低,施工现场污染和浪费较大。
利用喷射法可以制作大蓬车车身、船体、广告模型、舞台道具、贮藏箱、建筑构件、机器外罩、容器、安全帽等。
5. 连续缠绕成型工艺将浸过树脂胶液的连续纤维或布带,按照一定规律缠绕到芯模上,然后固化脱模成为增强塑料制品的工艺过程,称为缠绕工艺。
缠绕工艺流程图如下图所示:缠绕工艺流程图利用连续纤维缠绕技术制作复合材料制品时,有两种不同的方式可供选择:一是将纤维或带状织物浸树脂后,再缠绕在芯模上;二是先将纤维或带状织物缠好后,再浸渍树脂。
目前普遍采用前者。
缠绕机类似一部机床,纤维通过树脂槽后,用轧辊除去纤维中多余的树脂。
为改善工艺性能和避免损伤纤维,可预先在纤维表面徐覆一层半固化的基体树脂,或者直接使用预浸料。
纤维缠绕方式和角度可以通过机械传动或计算机控制。
缠绕达到要求厚度后,根据所选用的树脂类型,在室温或加热箱内固化、脱模便得到复合材料制品。
利用纤维缠绕工艺制造压力容器时,一般要求纤维具有较高的强度和模量,容易被树脂浸润,纤维纱的张力均匀以及缠绕时不起毛、不断头等。
另外,在缠绕的时候,所使用的芯模应有足够的强度和刚度,能够承受成型加工过程中各种载荷(缠绕张力、固化时的热应力、自重等),满足制品形状尺寸和精度要求以及容易与固化制品分离等。
常用的芯模材料有石膏、石蜡、金属或合金、塑料等,也可用水溶性高分材料,如以聚烯醇作粘结剂制成芯模。
连续纤维缠绕技术的优点首先,纤维按预定要求排列的规整度和精度高,通过改变纤维排布方式、数量,可以实现等强度设计,因此,能在较大程度上发挥增强纤维抗张性能优异的特点,其次,用连续纤维缠绕技术所制得的成品,结构合理,比强度和比模量高,质量比较稳定和生产效率较高等。
连续纤维缠绕技术的缺点设备投资费用大,只有大批量生产时才可能降低成本。
连续纤维缠绕法适于制作承受一定内压的中空型容器,如固体火箭发动机壳体、导弹放热层和发射筒、压力容器、大型贮罐、各种管材等。
近年来发展起来的异型缠绕技术,可以实现复杂横截面形状的回转体或断面呈矩形、方形以及不规则形状容器的成型。
6. 拉挤成型工艺拉挤成型工艺中,首先将浸渍过树脂胶液的连续纤维束或带状织物在牵引装置作用下通过成型模而定型;其次,在模中或固化炉中固化,制成具有特定横截面形状和长度不受限制的复合材料,如管材、棒材、槽型材、工字型材、方型材等。
一般情况下,只将预制品在成型模中加热到预固化的程度,最后固化是在加热箱中完成的。
拉挤成型过程中,要求增强纤维的强度高、集束性好、不发生悬垂和容易被树脂胶液浸润。
常用的增强纤维如玻璃纤维、芳香族聚酰胺纤维、碳纤维以及金属纤维等。
用作基体材料的树脂以热固性树脂为主,要求树脂的粘度低和适用期长等。
大量使用的基体材料有不饱和聚酯树脂和环氧树脂等。
另外,以耐热性较好、熔体粘度较低的热塑性树脂为基体的拉挤成型工艺也取得了很大进展。
其拉挤成型的关键在于增强材料的浸渍。
在拉挤成型工艺中,目前常用的方法如热熔涂覆法和混编法。
热熔涂覆法是使增强材料通过熔融树脂,浸渍树脂后在成型模中冷却定型;混编法中,首先按一定比例将热塑性聚合物纤维与增强材料混编织成带状、空芯状等几何形状的织物;然后,利用具有一定几何形状的织物通过热模时基体纤维熔化并浸渍增强材料,冷却定型后成为产品。
拉挤成型的优点①生产效率高,易于实现自动化;②制品中增强材料的含量一般为40%--80%,能够充分发挥增强材料的作用,制品性能稳定可靠;③不需要或仅需要进行少量加工,生产过程中树脂损耗少;④制品的纵向和横向强度可任意调整,以适应不同制品的使用要求,其长度可根据需要定长切割。
拉挤制品的主要应用领域(1)耐腐蚀领域。
主要用于上、下水装置,工业废水处理设备、化工挡板及化工、石油、造纸和冶金等工厂内的栏杆、楼梯、平台扶手等。
(2)电工领域。
主要用于高压电缆保护管、电缆架、绝缘梯、绝缘杆、灯柱、变压器和电机的零部件等。
(3)建筑领域。
主要用于门窗结构用型材、桁架、桥梁、栏杆、支架、天花板吊架等。
(4)运输领域。
主要用于卡车构架、冷藏车箱、汽车笼板、刹车片、行李架、保险杆、船舶甲板、电气火车轨道护板等。
(5)运动娱乐领域。
主要用于钓鱼杆、弓箭杆、滑雪板、撑杆跳杆、曲辊球辊、活动游泳池底板等。
(6)能源开发领域。
主要用于太阳能收集器、支架、风力发电机叶片和抽油杆等。
(7)航空航天领域。
如宇宙飞船天线绝缘管,飞船用电机零部件等。
目前,随着科学和技术的不断发展,正向着提高生产速度、热塑性和热固性树脂同时使用的复合结构材料和方向发展。
生产大型制品,改进产品外观质量和提高产品的横向强度都将是拉挤成型工艺今后的发展方向。
7. 注射成型工艺注射成型是树脂基复合材料生产中的一种重要成型方法,它适用于热塑性和热固性复合材料,但以热塑性复合材料应用最广。
注射成型工艺原理注射成型是根据金属压铸原理发展起来的一种成型方法。
该方法是将颗粒状树脂、短纤维送入注射腔内,加热熔化、混合均匀,并以一定的挤出压力,注射到温度较低的密闭模具中,经过冷却定型后,开模便得到复合材料制品。
注射成型工艺过程包括加料、熔化、混合、注射、冷却硬化和脱模等步骤。
加工热固性树脂时,一般是将温度较低的树脂体系(防止物料在进入模具之前发生固化)与短纤维混合均匀后注射到模具,然后再加热模具使其固化成型。
在加工过程中,由于熔体混合物的流动会使纤维在树脂基体中的分布有一定的各向异性。
如果制品形状比较复杂,则容易出现局部纤维分布不均匀或大量树脂富集区,影响材料的性能。
因此,注射成型工艺要求树脂与短纤维的混合均匀,混合体系有良好的流动性,而纤维含量不宜过高,一般在30%--40%左右。
注射成型法所得制品的精度高、生产周期短、效率较高、容易实现自动控制,除氟树脂外,几乎所有的热塑性树脂都可以采用这种方法成型。
按物料在注射腔中熔化方式分类,常用的注射机有按塞式和螺杆式两种。
由于按塞式注射机塑化能力较低、塑化均匀性差,注射压力损耗大及注射速度较慢等,已很少生产,现在普遍使用的是往复螺杆式注射机。