氮氧化物控制原理及技术
NOx的产生机理及排放控制解析

• 高活性CATA.会使二氧化硫氧化成三氧化硫.
SCR喷氨法催化剂反应器置于空气预 热器与静电除尘器之间
空气
NH3+空气
NH3
锅炉
NH3储罐 蒸发器 空气预热器
空气
SCR反应器
静电除 尘器
湿法烟 气脱硫
系统
去烟囱
SCR喷氨法催化剂反应器布置在
• 3.4烟气再循环法
• 4.炉膛喷射脱硝
• 实质为向炉膛喷射某种物质,可在一定温 度条件下还原已生成的一氧化氮,以降低的排 放量。包括喷水法、二次燃烧法、喷氨法。
• 4.1 喷水法反应为: • 但一氧化氮氧化较困难,需喷入臭氧或高锰酸
钾,不现实。
• 4.2喷二次燃料: • 即前述燃料分级燃烧,但二次燃料不会仅选择
举例:固态除渣煤粉炉,当要求NOx排放值为650mg/m3时,所需的NOx降低率为36%。
120
NOx降低率(%)
100
循环床
80
链条炉
抛煤机炉
60
鼓泡床
40
固态除渣煤粉炉
20
液态除渣煤粉炉
0
0 200 400 600 800 1000 1200 1400 1600 1800
NOx排放值(mg/m3)
• 喷入的氨与烟气良好混合是保证脱硝还原反应 充分进行、使用最少量氨达到最好效果的重要 条件。
• 若喷入的氨未充分反应,则泄漏的氨会到锅炉 炉尾部受热面,不仅使烟气飞灰容易沉积在受 热面,且烟气中氨遇到三氧化硫会生成硫酸氨 (粘性,易堵塞空气预热器,并有腐蚀危险)。
• 总之,SNCR喷氨法投资少,费用低,但适用范 围窄,要有良好的混合及反应空间、时间条件。 当要求较高的脱除率时,会造成氨泄漏过大。
氮氧化物的生成机理及防治措施

碳氢化合物燃烧时,分解成 CH、CH2和C2等基团,与 N2发生如下反应
火焰中存在大量O、OH基 团,与上述产物反应
燃料型NOx的形成
燃料中的N通常以原子状态与HC结合,C—N键的键能
较N ≡N 小,燃烧时容易分解,经氧化形成NOx
火焰中燃料氮转化为NO的比例取决于火焰区NO/O2的
比例
NO
燃料中20%~80%的氮转化为NOx O,H,OH
氮氧化物的性质及来源
NOx的性质(续)
NO2:强烈刺激性,来源于NO的氧化,酸沉降
NOx的来源
固氮菌、雷电等自然过程(5×108t/a) 人类活动(5×107t/a)
○ 燃料燃烧占 90% ○ 95%以NO形式,其余主要为NO2
燃烧过程 NOx的形成 机理
形成机理
○ 燃料型NOx ● 燃料中的固定氮生成的NOx
两段燃烧技术
第一段:氧气不足,烟气温 度低,NOx生成量很小
第二段:二次空气,CO、 HC完全燃烧,烟气温度低
先进的低NOx燃烧技术
原理:低空气过剩系数运行技术+分段 燃烧技术
炉膛内整体空气分级的低NOx直流燃烧器
○ 炉壁设置助燃空气(OFA,燃尽风)喷嘴 ○ 类似于两段燃烧技术
先进的低NOx燃烧技术
第九章 氮氧化物污染控制
教学内容 一. 氮氧化物的性质及来源
二. 燃烧过程中氮氧化物的 形成机理
三. 低氮氧化物燃烧技术
四. 烟气脱硝技术
重
点
教学目标
氮氧化物的形成机理,低氮氧 通过本节内容的学习,使学生
化物燃烧技术和烟气脱硝技术。 达到如下要求(1)了解氮氧 化物的性质和主要来源(2)
熟悉氮氧化物的形成机理(3)
SCR系统的工作原理
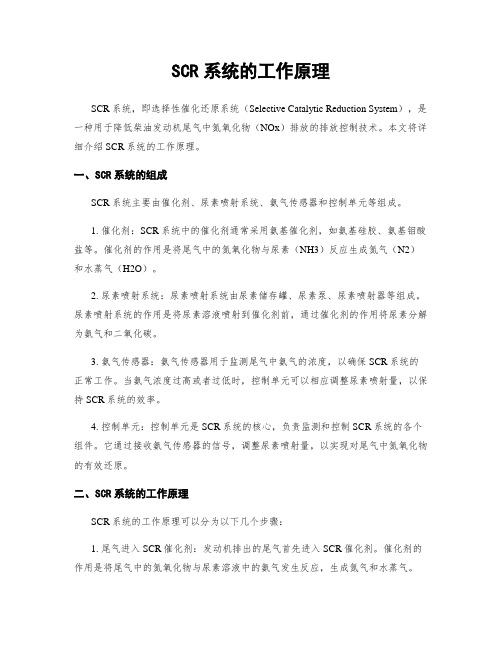
SCR系统的工作原理SCR系统,即选择性催化还原系统(Selective Catalytic Reduction System),是一种用于降低柴油发动机尾气中氮氧化物(NOx)排放的排放控制技术。
本文将详细介绍SCR系统的工作原理。
一、SCR系统的组成SCR系统主要由催化剂、尿素喷射系统、氨气传感器和控制单元等组成。
1. 催化剂:SCR系统中的催化剂通常采用氨基催化剂,如氨基硅胶、氨基钼酸盐等。
催化剂的作用是将尾气中的氮氧化物与尿素(NH3)反应生成氮气(N2)和水蒸气(H2O)。
2. 尿素喷射系统:尿素喷射系统由尿素储存罐、尿素泵、尿素喷射器等组成。
尿素喷射系统的作用是将尿素溶液喷射到催化剂前,通过催化剂的作用将尿素分解为氨气和二氧化碳。
3. 氨气传感器:氨气传感器用于监测尾气中氨气的浓度,以确保SCR系统的正常工作。
当氨气浓度过高或者过低时,控制单元可以相应调整尿素喷射量,以保持SCR系统的效率。
4. 控制单元:控制单元是SCR系统的核心,负责监测和控制SCR系统的各个组件。
它通过接收氨气传感器的信号,调整尿素喷射量,以实现对尾气中氮氧化物的有效还原。
二、SCR系统的工作原理SCR系统的工作原理可以分为以下几个步骤:1. 尾气进入SCR催化剂:发动机排出的尾气首先进入SCR催化剂。
催化剂的作用是将尾气中的氮氧化物与尿素溶液中的氨气发生反应,生成氮气和水蒸气。
2. 尿素喷射:尿素喷射系统会根据氨气传感器的信号,控制尿素喷射量。
尿素喷射器将尿素溶液喷射到催化剂前,尿素在催化剂的作用下分解为氨气和二氧化碳。
3. 氨气与氮氧化物反应:催化剂表面的氨气与尾气中的氮氧化物发生反应,生成氮气和水蒸气。
反应的化学方程式为:4NO + 4NH3 + O2 → 4N2 + 6H2O。
4. 尾气排放:经过SCR系统的处理,尾气中的氮氧化物被还原为无害的氮气和水蒸气。
处理后的尾气通过排气管排出。
三、SCR系统的优势SCR系统具有以下几个优势:1. 高效降低氮氧化物排放:SCR系统能够将尾气中的氮氧化物有效还原,使其排放量大幅降低,符合环保要求。
NOX形成机理-如何控制NOX浓度

NOX形成机理,如何控制NOX浓度1、NOx的危害:氮氧化物(NOx)是重要的空气污染物质,其产生的途径为燃烧火焰在高温下氮气与氧气的化合,以及燃料中的氮成分在燃烧时氧化而成。
氮氧化物的环境危害有二种,在阳光的催化作用下,氮氧化物易与碳氢化物光化反应,造成光雾及臭氧之二次空气污染;此外氮氧化物也易与水气结合成为含有硝酸成分的酸雨。
2、NOx生成机理和特点2.1 NOx生成机理在NOx中,一氧化氮约占90%以上,二氧化氮占5%~10%,产生机理一般分为如下3种:(1)热力型NOx,燃烧时,空气中氮在高温下氧化产生,其中的生成过程是一个不分支连锁反应。
其生成机理可用捷里多维奇(ZELDOVICH)反应式表示,即O2+N→2O+N, O+N2→NO+N, N+O2→NO+O在高温下总生成式为N2+O2→2NO, NO+0.5O2→NO2随着反应温度T的升高,其反应速率按指数规律增加。
当T<1 500 ℃时,NO的生成量很少,而当T>1 500 ℃时,T每增加100 ℃,反应速率增大6~7倍。
(2)快速型NOx,快速型NOx是1971年FENIMORE通过实验发现的。
在碳氢化合物燃料燃烧在燃料过浓时,在反应区附近会快速生成NOx,由于燃料挥发物中碳氢化合物高温分解生成的CH自由基可以和空气中氮气反应生成HCN和N,再进一步与氧气作用以极快的速度生成NOx,其形成时间只需要60 ms,所生成的NOx与炉膛压力的0.5次方成正比,与温度的关系不大。
(3)燃料型NOx,指燃料中含氮化合物,在燃烧过程中进行热分解,继而进一步氧化而生成NOx。
由于燃料中氮的热分解温度低于煤粉燃烧温度,在600~800 ℃时就会生成燃料型NOx。
在生成燃料型NOx过程中,首先是含有氮的有机化合物热裂解产生N,CN,HCN等中间产物基团,然后再氧化成NOx。
由于煤的燃烧过程由挥发份燃烧和焦炭燃烧两个阶段组成,故燃料型NOx的形成也由气相氮的氧化和焦炭中剩余氮的氧化两部分组成。
NOX形成机理,如何控制NOX浓度

NOX形成机理,如何控制NOX浓度1、NOx的危害:氮氧化物(NOx)是重要的空气污染物质,其产生的途径为燃烧火焰在高温下氮气与氧气的化合,以及燃料中的氮成分在燃烧时氧化而成。
氮氧化物的环境危害有二种,在阳光的催化作用下,氮氧化物易与碳氢化物光化反应,造成光雾及臭氧之二次空气污染;此外氮氧化物也易与水气结合成为含有硝酸成分的酸雨。
2、NOx生成机理和特点2.1 NOx生成机理在NOx中,一氧化氮约占90%以上,二氧化氮占5%~10%,产生机理一般分为如下3种:(1)热力型NOx,燃烧时,空气中氮在高温下氧化产生,其中的生成过程是一个不分支连锁反应。
其生成机理可用捷里多维奇(ZELDOVICH)反应式表示,即O2+N→2O+N, O+N2→NO+N, N+O2→NO+O在高温下总生成式为N2+O2→2NO, NO+0.5O2→NO2随着反应温度T的升高,其反应速率按指数规律增加。
当T<1 500 ℃时,NO的生成量很少,而当T>1 500 ℃时,T每增加100 ℃,反应速率增大6~7倍。
(2)快速型NOx,快速型NOx是1971年FENIMORE通过实验发现的。
在碳氢化合物燃料燃烧在燃料过浓时,在反应区附近会快速生成NOx,由于燃料挥发物中碳氢化合物高温分解生成的CH自由基可以和空气中氮气反应生成HCN和N,再进一步与氧气作用以极快的速度生成NOx,其形成时间只需要60 ms,所生成的NOx与炉膛压力的0.5次方成正比,与温度的关系不大。
(3)燃料型NOx,指燃料中含氮化合物,在燃烧过程中进行热分解,继而进一步氧化而生成NOx。
由于燃料中氮的热分解温度低于煤粉燃烧温度,在600~800 ℃时就会生成燃料型NOx。
在生成燃料型NOx过程中,首先是含有氮的有机化合物热裂解产生N,CN,HCN等中间产物基团,然后再氧化成NOx。
由于煤的燃烧过程由挥发份燃烧和焦炭燃烧两个阶段组成,故燃料型NOx的形成也由气相氮的氧化和焦炭中剩余氮的氧化两部分组成。
nsr(nox储存还原)工作原理
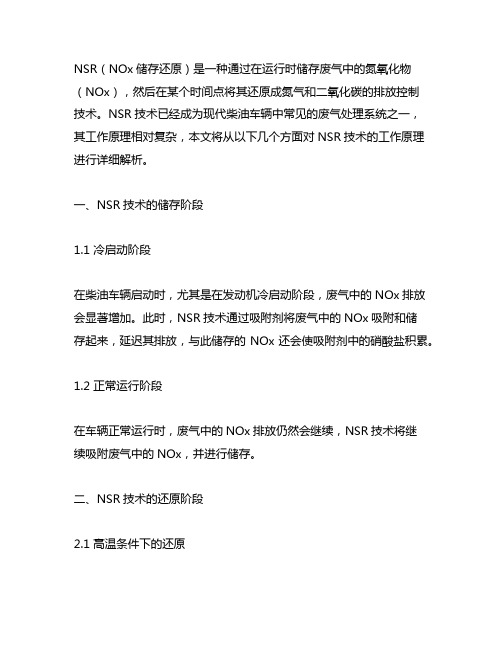
NSR(NOx储存还原)是一种通过在运行时储存废气中的氮氧化物(NOx),然后在某个时间点将其还原成氮气和二氧化碳的排放控制技术。
NSR技术已经成为现代柴油车辆中常见的废气处理系统之一,其工作原理相对复杂,本文将从以下几个方面对NSR技术的工作原理进行详细解析。
一、NSR技术的储存阶段1.1 冷启动阶段在柴油车辆启动时,尤其是在发动机冷启动阶段,废气中的NOx排放会显著增加。
此时,NSR技术通过吸附剂将废气中的NOx吸附和储存起来,延迟其排放,与此储存的NOx还会使吸附剂中的硝酸盐积累。
1.2 正常运行阶段在车辆正常运行时,废气中的NOx排放仍然会继续,NSR技术将继续吸附废气中的NOx,并进行储存。
二、NSR技术的还原阶段2.1 高温条件下的还原在车辆运行一段时间后,发动机温度上升,此时通过调整进气量和喷射正时来增加排气温度,使其达到NOx吸附剂的还原温度。
在这种高温条件下,NOx吸附剂中积累的硝酸盐会被还原为氮气和二氧化碳,然后被释放到大气中。
2.2 燃料喷射调整在NSR技术的还原阶段,还需要通过智能化的燃料喷射系统对喷射正时和喷射量进行精准调整,确保储存的NOx得以完全还原,同时最大程度减少氮氧化物和颗粒物的排放。
三、NSR技术的储存和还原过程中的控制策略在NSR技术的储存和还原过程中,还需要精细的控制策略来保证系统的高效运行。
3.1 温度监测与控制NSR系统需要通过传感器对进气温度、排气温度等参数进行实时监测,并根据监测数据来控制发动机运转状态,从而保证NOx吸附剂的储存和还原温度达到设计要求。
3.2 智能化燃料喷射系统NSR技术中的智能化燃料喷射系统可以根据中央处理器的指令精确控制喷射正时和喷射量,确保NOx的完全还原,并在排放时保持发动机的高效工作状态。
3.3 氮氧化物排放监测为了保证NSR系统的排放性能符合环保标准,还需要配置氮氧化物排放监测仪器,通过对排气中氮氧化物浓度的实时监测来调整和优化系统的工作状态,以达到更高的环保要求。
NOX形成机理-如何控制NOX浓度
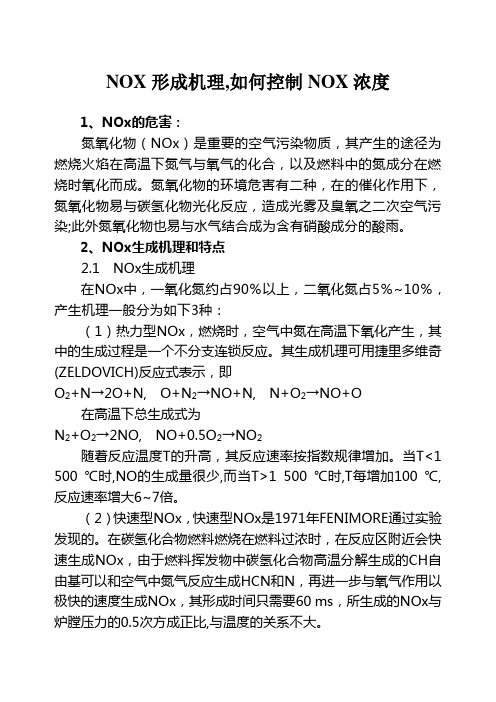
NOX形成机理,如何控制NOX浓度1、NOx的危害:氮氧化物(NOx)是重要的空气污染物质,其产生的途径为燃烧火焰在高温下氮气与氧气的化合,以及燃料中的氮成分在燃烧时氧化而成。
氮氧化物的环境危害有二种,在的催化作用下,氮氧化物易与碳氢化物光化反应,造成光雾及臭氧之二次空气污染;此外氮氧化物也易与水气结合成为含有硝酸成分的酸雨。
2、NOx生成机理和特点2.1 NOx生成机理在NOx中,一氧化氮约占90%以上,二氧化氮占5%~10%,产生机理一般分为如下3种:(1)热力型NOx,燃烧时,空气中氮在高温下氧化产生,其中的生成过程是一个不分支连锁反应。
其生成机理可用捷里多维奇(ZELDOVICH)反应式表示,即O2+N→2O+N, O+N2→NO+N, N+O2→NO+O在高温下总生成式为N2+O2→2NO, NO+0.5O2→NO2随着反应温度T的升高,其反应速率按指数规律增加。
当T<1 500 ℃时,NO的生成量很少,而当T>1 500 ℃时,T每增加100 ℃,反应速率增大6~7倍。
(2)快速型NOx,快速型NOx是1971年FENIMORE通过实验发现的。
在碳氢化合物燃料燃烧在燃料过浓时,在反应区附近会快速生成NOx,由于燃料挥发物中碳氢化合物高温分解生成的CH自由基可以和空气中氮气反应生成HCN和N,再进一步与氧气作用以极快的速度生成NOx,其形成时间只需要60 ms,所生成的NOx与炉膛压力的0.5次方成正比,与温度的关系不大。
(3)燃料型NOx,指燃料中含氮化合物,在燃烧过程中进行热分解,继而进一步氧化而生成NOx。
由于燃料中氮的热分解温度低于煤粉燃烧温度,在600~800 ℃时就会生成燃料型NOx。
在生成燃料型NOx过程中,首先是含有氮的有机化合物热裂解产生N,CN,HCN等中间产物基团,然后再氧化成NOx。
由于煤的燃烧过程由挥发份燃烧和焦炭燃烧两个阶段组成,故燃料型NOx的形成也由气相氮的氧化和焦炭中剩余氮的氧化两部分组成。
NOX控制原理及实际应用

NOX控制原理及实际应用摘要:该发电厂1000MW超超临界燃煤机组锅炉为上海锅炉厂设计制造,单炉膛塔式布置、一次中间再热、四角切圆燃烧、双送风机、双一次风机、双汽动引风机、六台磨煤机。
对大容量燃煤机组来说,切向燃烧技术具有 NOx 排放量低的固有特点。
在利用分段燃烧方法发展先进的低 NOx 控制技术时,切向燃烧过程一直是个有利的因素。
一、控制原理选择性催化还原烟气脱氮法的主要反应是在一定的温度和催化剂的作用下,氨气与烟气中的NOx 反应生成对空气无害的氮气和水汽,目前喷氨调整器以控制烟囱侧出口Nox浓度为目标进行自动调整,一般情况下自动均能有效调节。
燃料中的氮化合物在燃烧过程中氧化反应而生成的NOx。
燃料进入炉膛被加热后,燃料中的氮有机化合物首先被热分解成氰(HCN)、氨(NH4)和CN 等中间产物,它们随挥发份一起从燃料中析出,它们被称为挥发份N。
挥发份N 析出后仍残留在燃料中的氮化合物,被称为焦炭N。
随着炉膛温度的升高及煤粉细度的减小,挥发份N 的比例增大,焦炭N 的比例减小。
挥发份N 中的主要氮化合物是HCN 和NH3,它们遇到氧后,HCN首先氧化成NCO,NCO在氧化性环境中会进一步氧化成NO,如在还原性环境中,NCO 则会生成NH,NH 在氧化性环境中进一步氧化成NO,同时又能与生成的NO 进行还原反应,使NO 还原成N2,成为NO的还原剂。
由氮氧化物(NOx)形成原因可知对NOx 的形成起决定作用的是燃烧区域的温度和过量空气量。
低NOx燃烧技术就是通过控制燃烧区域的温度和空气量(高温、富氧这两个条件都满足后,NOX产量多),以达到阻止NOx生成。
及降低其排放的目的。
二、设备选择本工程烟气脱硝采用选择性催化还原(SCR)脱硝工艺,一炉两个反应器,液氨卸料、储存、蒸发等为公用系统。
烟气脱硝系统包括:1.烟气系统烟气系统是指从锅炉尾部低温省煤器下部引出口至 SCR 反应器本体入口、SCR 反应器本体出口至回转式空预器入口、回转式空预器出口至布袋除尘器进口之间的连接烟道。
- 1、下载文档前请自行甄别文档内容的完整性,平台不提供额外的编辑、内容补充、找答案等附加服务。
- 2、"仅部分预览"的文档,不可在线预览部分如存在完整性等问题,可反馈申请退款(可完整预览的文档不适用该条件!)。
- 3、如文档侵犯您的权益,请联系客服反馈,我们会尽快为您处理(人工客服工作时间:9:00-18:30)。
氮氧化物排放控制原理及新技术李俊华,陈亮,常化振,郝吉明清华大学环境科学与工程系(通讯地址:清华大学环境系,100084,Tel:62771093,email:lijunhua@)摘要:NOx排放量逐年增加,造成区域酸沉降趋势不断恶化,大气中二次颗粒物臭氧(O3)和微细可吸入颗粒物(PM2.5)居高难下,严重影响人体健康和生态环境质量。
本文介绍了我国NOx排放趋势,重点讨论了NOx控制原理及关键控制技术的研究进展。
基于目前烟气脱硝技术存在的问题,提出了脱硝催化剂原材料和制备工艺国产化、针对我国不同煤种研究催化剂适应性的问题,以及下一步燃煤烟气协同污染控制最新研究方向。
关键词:氮氧化物,燃煤烟气,稀燃汽车,排放,脱硝催化剂,协同控制1我国NOx排放现状《国家环境保护“十一五”规划》提出确保实现SO2减排目标,实施燃煤电厂脱硫工程,实施酸雨和SO2污染防治规划,重点控制高架源的SO2和NOx排放,综合改善城市空气环境质量。
随着“十一五”期间对电厂实施烟气脱硫效果明显,大气SO2浓度及硫沉降均有所下降。
但NOx作为一类主要的大气污染物,在我国其排放量仍在增加,不仅对人体健康造成直接危害,同时也不仅会造成空气中NO2浓度的增加、区域酸沉降趋势不断恶化,还会使对流层O3浓度增加,并在空气中形成微细颗粒物(PM),影响大气环境质量[1,2]。
我国以煤为主的能源结构和发电结构,使得燃煤成为NOx的最大来源,全国NOx排放量的67%来自煤炭燃烧,其中燃煤电厂是NOx排放的最大分担者。
2007年全国NOx排放量为1643.4万吨,工业排放NOx1261.3万吨,其中火电厂排放811万吨,占全国NOx排放量的49.4%,占工业NOx排放的64.3%[3]。
今年NOx排放量将达到1800万吨,未来若无控制措施,NOx排放在2020年将达到3000万吨以上,届时我国将成为世界上第一大NOx排放国,污染将进一步加重,污染进一步加重。
我国于2004年1月1日起执行的《火电厂大气污染物排放标准》(GB13223—2003),将新建燃煤电厂的氮氧化物的排放浓度控制在450mg/Nm3。
对于氮氧化物污染严重和环境容量有限的经济发达地区,当地政府提出了更高的排放要求,如北京为了迎接2008年奥运会,将NOx排放标准严格到100mg/Nm3。
因此针对重点源开展NOx排放控制原理及新技术的研究变得十分必要和迫切。
2固定源烟气NOx排放控制原理及技术通常把通过改变燃烧条件来降低燃料燃烧过程中产生的NOx的各种技术措施统称为低NOx燃烧技术。
通常情况下,采用各种低NOx燃烧技术最多仅能降低NOx排放量的50%左右。
因此,当对燃烧设备的NOx排放要求较高时,单纯采用燃烧改进措施往往不能满足排放要求,这就需要采用尾部烟气脱硝技术来进一步降低NOx的排放。
燃烧后烟气脱硝技术是指通过各种物理、化学过程使烟气中的NOx还原或分解为N2,或者以清除含N物质的方式去除NOx。
按反应体系的状态,烟气脱硝技术可大致分为干法(催化法)和湿法(吸收法)两类。
湿法烟气脱硝是指各种利用水或酸、碱、盐及其他物质的水溶液来吸收废气中的NOx,使废气得以净化的工艺技术方法。
但该技术存在一些难以克服的问题造成应用价值有限。
干法烟气脱硝技术主要包括选择性催化还原法(SCR)、选择性非催化还原法(SNCR)、电子束法(EB)、脉冲电晕低温等离子体法(PCIPCP)、SNRB(SOx-NOx-ROx-BOx)联合控制工艺、联合脱硝脱硫技术(SNOx)工艺、固体吸收/再生法等。
与湿法脱硝技术相比,干法脱硝技术效率较高、占地面积较小、不产生或很少产生有害副产物,也不需要烟气加热系统,因此绝大部分电厂锅炉采用干法烟气脱硝技术。
下面重点介绍氨气选择性催化还原法(NH3-SCR)的烟气脱硝技术。
2.1氨气选择性催化还原NOx技术原理氨选择性催化还原NOx(NH3-SCR)脱硝技术是还原剂NH3在催化剂作用下选择性将NOx还原为N2的方法。
对于固定源脱硝来说,主要是采用向温度约为280~420oC的烟气中喷入尿素或氨,将NOx还原为N2和H2O。
如果尿素做还原剂,首先要发生水解反应:NH2-CO-NH2→NH3+HNCO(异氰酸)(1)HNCO+H2O→NH3+CO2(2)氨选择性还原NOx的主要反应式如下:4NH3+4NO+O2→4N2+6H2O(3)8NH3+6NO2→7N2+12H2O(4)2NH3+NO+NO2→2N2+3H2O(5)通过使用适当的催化剂,可以使主反应在200~450oC的温度范围内有效进行。
反应时,排放气体中的NOx和注入的NH3几乎是以1:1物质的量之比进行反应,可以得到80~90%的脱硝率[4]。
NH3-SCR 脱硝技术的关键是催化剂,催化剂的催化性能直接影响到SCR系统的整体脱硝效率。
2.2脱硝SCR催化剂钒基催化剂的有效活性温度区间较宽,对于商用的V2O5-WO3/TiO2和V2O5-MoO3/TiO2,在NH3/NO为1:1的化学当量比情况下,最佳反应温度区间大概在380~420oC之间。
当温度超过这一区间的上限时,NH3氧化的副反应发生,生成N2O和NO,从而降低了NO的转化率[5]。
该催化剂体系中各活性成分的主要作用是:V2O5:钒是其中最主要的活性组分。
钒的担载量通常不超过1%(质量分数)[6],因为较高负载量的V2O5能将SO2氧化成SO3,造成催化剂上硫酸盐沉积,对SCR反应不利[7]。
TiO2:以具有锐钛矿结构的TiO2作为载体主要是因为钒的氧化物在TiO2的表面有很好的分散度;在TiO2载体上SO2氧化生成SO3的反应很弱且可逆[8];同时,在TiO2表面上生成的硫酸盐的稳定性要比其他氧化物如Al2O3和ZrO2差,因此在工业应用过程中硫酸盐不会遮蔽表面活性位,相反这部分少量的硫酸盐还会增强反应活性。
WO3:其含量一般很大,大约能够占到10%(质量分数),主要作用是增加催化剂的活性和热稳定性。
MoO3:MoO3的加入能够提高催化剂活性、防止烟气中的As导致催化剂中毒[9,10]。
但是MoO3抑制As中毒的机理现在还不是很清楚。
其他添加剂:在工程实际应用的蜂窝状催化剂中加入一些硅基的颗粒可以提高催化剂的机械强度,但由于这些硅基颗粒中通常含有一些碱性的阳离子,对催化剂来说是一种毒性物质,因此会造成工程实际应用中催化剂活性有所下降。
3烟气脱硝技术存在的问题及研究方向近年来我国一些厂家通过引进、吸收、消化国外先进脱硝技术,建成了许多脱硝装置。
随后,许多国内厂家也开始引进了催化剂的生产技术,主要有东方凯特瑞引进德国KWH的整套催化剂制备生产线,并在2006年投产运营;北京国电龙源环保工程有限公司引进日本触媒化成的催化剂制备技术,于2008年12月初投入商业运行;重庆远达催化剂公司引进美国Cormetech的催化剂生产技术,并于2009年9月正式投运。
福建大拇指公司,三融环保也分别与日本触媒化成签订了催化剂生产技术引进合同。
另外还有几家也先后开始了建厂工作。
预计到2010年底,全国催化剂总产能可能会达到50000m3以上。
但是,由于外方技术保密和考虑到技术引进成本的问题,从目前这些厂商的技术引进范围来看,基本都没有引进原料生产的技术。
现在主要的原料供货商有日本的石原化工,法国的美礼联等公司,数量很少,而且已经基本形成了稳定的价格体系,使得原料成本难以大幅下降。
此外中国煤质丰富,不同煤种燃烧灰分对催化剂的中毒机制及催化剂的适应性仍需深入研究。
3.1催化剂专用钛白粉国产化目前广泛使用的脱硝催化剂一般都是采用TiO2作为载体,V2O5为活性组份,其中TiO2的用量超过80%。
催化剂用超细晶型钛白粉为锐钛型,采用硫酸法制备,对成品的结晶型式、粒径分布、比表面积等有着非常严格的技术要求,另外还需要严格控制碱金属、硫酸根、SiO2、重金属的含量,经调研目前国内产品尚不能满足要求。
添加了WO3对V2O5-TiO2催化剂的成型性能、反应活性、抗毒性、Brφnsted酸度、催化剂的热稳定性都有较大提高,同时还会抑制SO2的氧化反应。
因此,脱硝催化剂一般都采用钛钨粉作为活性成份的载体。
国外钛钨粉的制备和生产,经过30年的发展已经比较成熟。
目前,国内对此方面的研究并不深入,尚未达到工业化生产的地步。
目前主要存在的问题是普通钛白粉的精制工艺的研究,国内拥有大量的钛白粉生产厂家,主要集中在四川,山东,辽宁等地,产品以金红石型钛白粉为主,一般都同时生产锐钛型产品,但是产品质量基本达不到催化剂产品的性能要求,需要进行精加工处理。
3.2脱硝催化剂的适应性目前国内催化剂制造技术几乎都是引进国外技术,我国与国外的煤质差别很大,具有高钙、高硫、高灰等特点,使得国外催化剂在中国应用适应性差,主要体现在中毒和灰堵等方面。
CaO中毒的主要原因是由于沉积在催化剂表面的CaO与烟气中的SO3反应造成催化剂微孔的堵塞。
反应生成的CaSO4的体积会膨胀14%左右,遮蔽反应活性位,堵塞催化剂表面,影响反应物在催化剂的扩散,中国山西出产的神华、神府煤的灰钙含量均超过20%,与美国PRB煤比较接近,按照美国康宁公司的经验,此类煤催化剂体积耗量将超过普通煤种的一倍以上,而据调研其他催化剂厂实际上在进入中国市场以前基本没有高钙煤的运行业绩,即使是康宁公司,也仅有少量的运行经验,所以此类问题值得深入研究。
砷中毒是引起催化剂钝化的重要因素之一。
砷是大多数煤种中都存在的成分,催化剂的砷中毒是由气态砷的化合物不断聚积,堵塞进入催化剂活性位的通道造成的,As2O3分散到催化剂中并固化在活性、非活性区域,使反应气体在催化剂内的扩散受到限制,且毛细管遭到破坏。
这种由相变引起的催化剂中毒是不可逆的,对SCR运行影响巨大。
烟气灰份中除金属元素外,还含有氟、氯、磷、硫和氮等非金属元素,分别对应氟化物、氯化物、磷酸盐、硫酸盐和硝酸盐等。
一方面,这些化合物可以覆盖在催化剂表面或堵塞催化剂的孔道使催化剂失活,另一方面,氟化物和氯化物也可以与活性组分相互作用,影响催化剂的活性。
氟化物、氯化物、磷酸盐、硫酸盐和硝酸盐等化合物若只是覆盖在催化剂的表面或堵塞催化剂的孔道,可以采用洗脱等去除,但若与活性组分发生了相互作用,这种中毒则是不可逆的。
我国很多电厂燃煤的灰份非常高,达到50g/Nm3以上,催化剂很容易产生严重的磨损现象,导致催化剂机械寿命大大降低,国内早期安装的进口SCR装置已经出现了催化剂磨损严重的故障,并导致锅炉非正常停机。
实际上据了解由于国外电厂用煤普遍经过洗选,含尘量基本在30g/Nm3以下,目前国外催化剂厂商处理的烟气含尘量在30g/Nm3以上的实际业绩是非常有限的,所以开展催化剂耐磨损技术已成为当前该领域的重点研究任务之一。