电液比例位置系统控制的simulink仿真
基于Simulink的比例阀控液压缸的建模与仿真
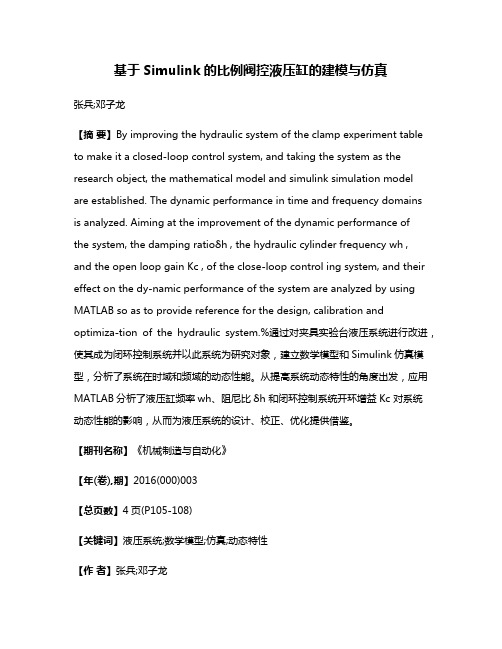
基于Simulink的比例阀控液压缸的建模与仿真张兵;邓子龙【摘要】By improving the hydraulic system of the clamp experiment table to make it a closed-loop control system, and taking the system as the research object, the mathematical model and simulink simulation model are established. The dynamic performance in time and frequency domains is analyzed. Aiming at the improvement of the dynamic performance ofthe system, the damping ratioδh , the hydraulic cylinder frequency wh ,and the open loop gain Kc , of the close-loop control ing system, and their effect on the dy-namic performance of the system are analyzed by using MATLAB so as to provide reference for the design, calibration and optimiza-tion of the hydraulic system.%通过对夹具实验台液压系统进行改进,使其成为闭环控制系统并以此系统为研究对象,建立数学模型和Simulink仿真模型,分析了系统在时域和频域的动态性能。
从提高系统动态特性的角度出发,应用MATLAB分析了液压缸频率wh、阻尼比δh 和闭环控制系统开环增益Kc 对系统动态性能的影响,从而为液压系统的设计、校正、优化提供借鉴。
电液速度控制系统建模与仿真

引言液压伺服系统是以液体压力能为动力的机械量(位移、速度和力)自动控制系统按系统。
控机械量的不同,它又可以分为电液位置伺服系统、电液速度伺服控制系统和电液力控制系统三种。
电液控制系统的基本元件包括电磁阀、电液开关控制阀、光电耦合器、功率放大器、电—机械转换器、普通电液伺服阀(频宽数十赫)、高频电液伺服阀(国内产品 400 赫)、电液比例流量阀、电液比例压力阀、电液比例方向阀、电液复合阀、电液比例泵、电液通断控制阀、电液数字阀、电液数字缸、电液数字泵等。
它们广泛用于机床工业、冶金工业、船舶工业、煤炭工业和工程机械等的控制系统中。
本文要研究的是电液速度控制系统及其仿真分析,是对电液速度控制系统的各个环节进行了数学模型的建立,并应用Matlab/Simulink对电液速度控制系统进行了仿真分析,通过幅频特性和相频特性的变化得到数学模型中各个部分对整个控制系统的影响。
1 绪论液压控制是液压技术领域的重要分支。
近20年来,许多工业部门和技术领域对高响应、高精度、高功率—重量比和大功率液压控制系统的需要不断扩大,促使液压控制技术迅速发展。
特别是控制理论在液压系统中的应用、计算及电子技术与液压技术的结合,使这门技术不论在元件和系统方面、理论与应用方面都日趋完善和成熟,并形成一门学科。
目前液压技术已经在许多部门得到广泛应用,诸如冶金、机械等工业部门及飞机、船舶部门等。
我国于50年代开始液压伺服元件和系统的研究工作,现已生产几种系列电液伺服产品,液压控制系统的研究工作也取得很大进展。
1.1电液控制技术的发展及趋势液压技术的发展与流体力学理论研究相互关联。
自1650年帕斯卡提出静态液体中的压力传播规律--帕斯卡原理以来,1686年牛顿揭示了粘性液体的内摩擦定律,18世纪建立了流体力学的连续性方程。
这些理论的建立为液压技术的发展奠定了理论基础。
从1795年,英国人首先制造出世界上第一台水压机起,液压传动开始进入工程领域。
AMEsim与Matlab_simulink联合仿真技术
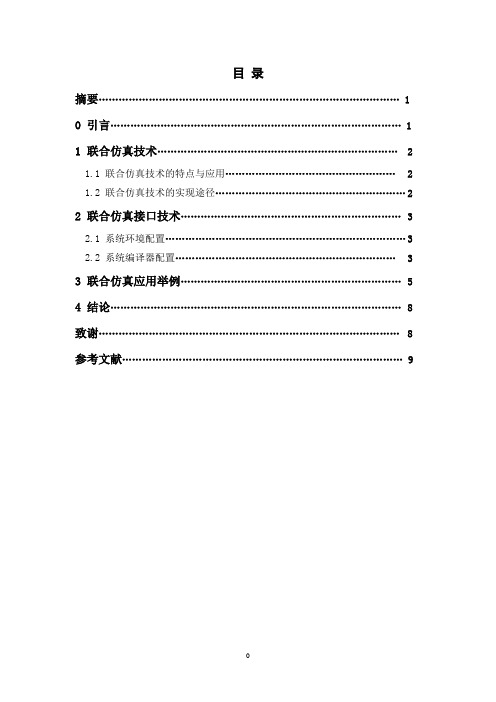
目录摘要 (1)0 引言 (1)1 联合仿真技术 (2)1.1 联合仿真技术的特点与应用 (2)1.2 联合仿真技术的实现途径 (2)2 联合仿真接口技术 (3)2.1 系统环境配置 (3)2.2 系统编译器配置 (3)3 联合仿真应用举例 (5)4 结论 (8)致谢 (8)参考文献 (9)AMESim与Matlab_Simulink联合仿真技术机械电子系0802班李敏M200870228摘要:根据AMESim与Matlab/Simulink软件各自的特点,对两者联合仿真技术进行了研究,解决了联合仿真的接口与实现问题,并把该技术应用于电液位置伺服系统的仿真,取得了良好的效果。
关键词:AMESim;Matlab/Simulink;联合仿真;接口Abstract:United Matlab/Simulink technique with AMESim and Matlab/Simulink was discussed based on their own characteristics. The problem of their interface and realization were solved. As an applied example, Matlab/Simulink of electro hydraulic servo-system was shown. Good results were achieved.Keywords:AMESim;Matlab/Simulink;United simulation;Interface0 引言传统的设计方法往往是通过反复的样品试制和试验来分析该系统是否达到设计要求,结果造成大量的人力和物力投入在样品的试制和试验上。
随着计算机仿真技术的发展,在工程系统的软件设计开发中,大量地采用了数值成型的方法,即通过建立系统的数值模型,利用计算机仿真使得大量的产品设计缺陷在物理成型之前就得到了处理,从而可以使企业在最短的时间、以最低的成本将新产品投放到市场。
基于simulink液位控制PID实验指导书

MCG10型小型过程控制实训系统液位控制实验说明书(simulink)指导老师:王腾飞学生:刘海利大同煤炭职业学院1.1 软件安装本系统是使用matlab软件做检测控制,驱动设备为过程控制实验设备,系统要求先安装matlab软件,再安装REW驱动下载软件。
安装要求win7系统旗舰版,32位系统。
1.2 SIMULINK PID利用SImulink仿真过程控制算法,在网络上已经有很多的范例文件,本实验是利用simulink里的离散PID实现信号采集,信号计算,数据在线实时监视等,最终控制液位达到设定值。
打开simulink library库discrete中的PID Controller (2 DOF),添加程序模板中。
图4.1PID封装模块利用其即可搭建一个简单的PID控制器,模块数据连接端包括ref为参考基准值,下端为反馈信号输入端,右侧是PID输出。
PID的3个参数值Proportional(P)比例,Integral (I)积分,Derivative (D)微分。
图4.2 PID功能设置1.2.1、PID原结构比例积分微分(PID)算法是工业中最常使用的控制算法。
通常,PID用于加热和冷却系统、液面监控、流控制和压力控制应用。
在PID控制中,必须指定过程变量和设定点。
过程变量是要控制的系统参数(例如,温度、压力和流量),设定点是要控制的参数值。
PID控制器可确定控制器的输出值(例如,加热器的功率或值位置),下图为PID原型。
1.2.2控制器使用控制器输出值控制系统,使过程变量接近设定点的值.结构图如下图4.5.图4.5 PID算法结构图1.2.3基于simulink控制的IO接口其中24V电源提供给外部传感器,PWM输出经过了功率放大,支持24V直流水泵,本次利用MCG10小型过程控制设备,内置小型直流潜水泵。
下图为simulink驱动接口。
该设备为Linux系统,在windows计算机系统中完成软件算法编写,通过以太网接口直接将程序下载到控制器中。
电液比例方向阀控位置系统仿真研究
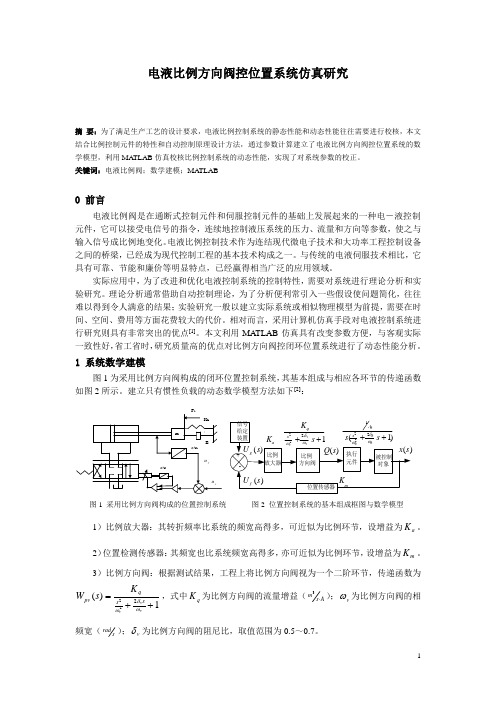
电液比例方向阀控位置系统仿真研究摘 要:为了满足生产工艺的设计要求,电液比例控制系统的静态性能和动态性能往往需要进行校核,本文结合比例控制元件的特性和自动控制原理设计方法,通过参数计算建立了电液比例方向阀控位置系统的数学模型,利用MA TLAB 仿真校核比例控制系统的动态性能,实现了对系统参数的校正。
关键词:电液比例阀;数学建模;MA TLAB0 前言电液比例阀是在通断式控制元件和伺服控制元件的基础上发展起来的一种电-液控制元件,它可以接受电信号的指令,连续地控制液压系统的压力、流量和方向等参数,使之与输入信号成比例地变化。
电液比例控制技术作为连结现代微电子技术和大功率工程控制设备之间的桥梁,已经成为现代控制工程的基本技术构成之一。
与传统的电液伺服技术相比,它具有可靠、节能和廉价等明显特点,已经赢得相当广泛的应用领域。
实际应用中,为了改进和优化电液控制系统的控制特性,需要对系统进行理论分析和实验研究。
理论分析通常借助自动控制理论,为了分析便利常引入一些假设使问题简化,往往难以得到令人满意的结果;实验研究一般以建立实际系统或相似物理模型为前提,需要在时间、空间、费用等方面花费较大的代价。
相对而言,采用计算机仿真手段对电液控制系统进行研究则具有非常突出的优点[1]。
本文利用MA TLAB 仿真具有改变参数方便,与客观实际一致性好,省工省时,研究质量高的优点对比例方向阀控闭环位置系统进行了动态性能分析。
1 系统数学建模图1为采用比例方向阀构成的闭环位置控制系统,其基本组成与相应各环节的传递函数如图2所示。
建立只有惯性负载的动态数学模型方法如下[2]:1)比例放大器:其转折频率比系统的频宽高得多,可近似为比例环节,设增益为a K 。
2)位置检测传感器:其频宽也比系统频宽高得多,亦可近似为比例环节,设增益为m K 。
3)比例方向阀:根据测试结果,工程上将比例方向阀视为一个二阶环节,传递函数为1)(222++=vv vssqpv K s W ωδω,式中q K 为比例方向阀的流量增益(A s m⋅3);v ω为比例方向阀的相频宽(s rad );v δ为比例方向阀的阻尼比,取值范围为0.5~0.7。
基于Simulink的电液比例溢流阀频响仿真_姚佳

qv1=qv2+
V2 E
dp2 dt
+A3
dy dt
(6)
姨 式中 qv2=cd2πD1sinαy
2 ρ
p2
;
V2— ——先导活塞前腔容积,单位为 m3;
cd2— ——主阀阀口流量系数,取 0.62。
根据公式(1)~(6)可以得到以电压信号 ug 为输入,阀
的入口压力 p1 为输出的 SIMULINK 仿真模型。 这里就
qv=qv1+qvz+
V1 E
dp1 dt
+A1
dx dt
(5)
式中 qv— ——进入阀口的总流量,单位为 m3/s;
dR1— ——固定液阻 R1 的直径;
ρ— ——工作油液的密度,取 900kg/m;
E— ——油液体积模量,单位为 Pa;
V1— ——主阀芯下腔容积,单位为 m3;
cd— ——液阻 R1 流量系数,取 0.6;
例溢流阀设计参数。
关键词:电液比例溢流阀;频响特性;Simulink 仿真
中 图 分 类 号 :TH137.5
文 献 标 识 码 :A
文 章 编 号 :1008-0813(2009)02-0038-03
Simulation Frequency Response Characteristic of
Electro-hydraulic Proportional Relief Valve Base on Simulink
图 4 dR1=1.0mm 时压力 p1 频率响应曲线 40
图 6 电液比例溢流阀系统伯德图
仿 真 结 果 表 明 ,固 定 液 阻 的 dR1 值 取 1.4mm,输 入 阀的流量为 60L/min 时, 电液比例溢流阀的压力 p1 有 比较好的响应特性。 从仿真可以看出,普通的电液比例 溢流阀的频响大约为 10Hz 左右。
基于MATLABsimulink的某电液比例调速阀控同步系统仿真
基于MATLAB/Simulink的某电液比例调速阀控同步系统仿真C液压缸总泄漏系数tpP液压缸负载压力L体积弹性模量eA液压缸有杆腔作用面积pq液压缸有杆腔和无杆腔作用面积之比B黏性阻尼系数PU为比例电磁铁初始电压,K为传感器及放大电路增益,fk为节流阀弹簧刚度,sK为比例电磁铁增益,ax为液压缸1输出位移。
1 概述同步系统是液压系统中实现多个执行元件的位移、力或速度相等的回路, 主要类型有机械同步回路、流量控制同步回路和容积控制同步回路等。
图1 系统原理图系统采用的同步回路如图1所示, 液压缸1、2的结构和参数完全相同, 缸1为主动缸, 用普通调速阀控制; 缸2为从动缸, 用电液比例调速阀控制。
位移传感器1和2分别对应地测量缸1和2的位移, 用两传感器测得的差值作为电液比例调速阀的控制信号, 控制液压缸2跟随液压缸1动作, 从而实现两缸同步动作。
液压缸1和2为非对称双作用液压缸。
液压缸伸出时, 供油压力即为系统压力, 回油经过调速阀, 液压缸两腔油压均较大。
液压缸缩回时, 回油压力可忽略, 数学模型较伸出时简单, 可参照出油数学模型构建其模型。
作者仅以液压缸伸出为例建立数学模型。
2 功率键合图本文章以液压缸1的输出作为整个系统的输入,即液压缸1输出唯一为已知,针对液压缸2伸出过程建立功率键合图如下:图2 液压缸2键合图1 )共势结,根据能量流的关系及容性元件C 的特性得下述关系:123L Q Q Q Q =-- (1)其中1.4e L eV V Q P C β∙==211112P q Q A v A v +==311Ltp L Q P C P R ==02(1)e s p V V q P A =+-⋅代入(1)式得:11 (42)e L tp L L P eV q Q C P P A v β∙+=++(2)对上式进行拉氏变换得:.(1).().().().()42e L tp L L P eV s q sQ s C P s P s A Y s β+=++(3)2) 共流结点根据惯性元件I 和转换器TF 的特征关系,得到下列关系式:21345F F F F F =--- (4)其中:2F m a = ; 110F P A =⋅ ;3F F = ;4P F B v =⋅ ;52p F P A =⋅;取(1)e s p F F q P A =--⋅以及12L P P P =- 1s P P = 代入上式得:P L p e m y B y P A F ∙∙∙+⋅=⋅- (5)对上式进行拉氏变换得:2()()()P p L e m s Y s B s Y s A P s F ⋅⋅+⋅⋅=⋅- (6)3 )系统流量方程L dt v Q C x =⋅ (7)阀芯位移方程:0[()]f v a sU K y x x K k --=⋅ (8)对以上两式进行拉式变化得:()()L dt v Q s C X s =⋅ (9)0()()()f af aav sssK K K K U K X s X s Y s k k k ⋅⋅⋅=+⋅-⋅ (10)4) 建立数学模型 联立(3)、(6)、(9)式,可得阀控缸的数学模型:假设液压缸为无阻尼缸, 忽略油液黏性阻尼, 则上式变换为:式中,为液压系统固有频率;为系统阻尼系数。
simulink仿真流程
simulink仿真流程标题,深入了解Simulink仿真流程。
Simulink是一种用于建模、仿真和分析动态系统的工具,它可以帮助工程师们更好地理解和设计复杂的控制系统。
在本文中,我们将深入探讨Simulink的仿真流程,以帮助读者更好地了解如何使用Simulink进行系统仿真。
Simulink仿真流程可以分为以下几个步骤:1. 模型建立,首先,我们需要在Simulink中建立系统的模型。
这可以通过拖放各种组件来实现,包括传感器、执行器、控制器等。
这些组件可以通过连接线连接起来,以构建系统的整体模型。
2. 参数设置,在建立模型后,我们需要设置各个组件的参数,包括传感器的灵敏度、执行器的动态响应等。
这些参数设置将直接影响系统的仿真结果。
3. 信号输入,接下来,我们需要确定系统的输入信号,这可以是一个预先定义的信号,也可以是一个外部输入。
这些输入信号将作为系统的激励,驱动系统进行仿真。
4. 仿真运行,一切就绪后,我们可以开始运行仿真。
Simulink将根据模型和参数设置,以及输入信号,模拟系统的动态行为,并输出相应的仿真结果。
5. 结果分析,最后,我们需要对仿真结果进行分析。
这包括系统的响应曲线、稳定性分析、频域特性等。
通过对仿真结果的分析,我们可以评估系统的性能,并进行必要的调整和优化。
总的来说,Simulink的仿真流程涉及模型建立、参数设置、信号输入、仿真运行和结果分析等多个环节。
通过深入了解Simulink的仿真流程,我们可以更好地利用这一工具来进行系统建模和分析,从而更好地理解和设计复杂的控制系统。
电液比例阀控液压缸系统建模与仿真
本 文搭 建 了 比例 阀控 非 对 称 液压 缸 控 制 系统 , 建 立 了该 系 统 的数 学 模 型 ,着 重 对 阀 控 非 对 称 液 压 缸 的建 模 方 法 进 行 了研 究 ,并 利 用 Maa tb中 的 l Smuik进行 仿真 分析 ,设 计 了 PD控制 器 对 系统 i l n I
进 行校 正 。Biblioteka 2 比例 阀控 液压 缸控 制系统 的数学模型
2 1 阀控非 对称 液压 缸的数 学模 型 .
1 系 统 的 组 成 及 原 理
比例 阀控 非 对 称 液 压 缸 控 制 系 统 的硬 件 组 成 如 图 1 示 ,主要 由滤 油 器 1和 6 所 、溢 流 阀 2、液
广泛 的应 用 。
液压 缸加 载指 定 负 载 (±2 ) 0t ,位 移传 感 器 将 液 压 缸 活 塞 的位 置 信 息 通 过 数 据 采 集 卡传 递 给计 算 机 与 理想 位 移 进行 比较 ,得 出差 值 ,经 过 优 化 处 理 和转 换 输 出控 制 信 号 ,通 过 比例放 大 器 放 大 后 驱 动 电液 比例 方 向 阀工 作 ,从 而 实 现对 液 压 缸 位 置 的精 确控 制 。
n l sswi t b a d c l rt st es s m v at e d sg e I o t l r h e ut h w a h y t m d l sc r ay i t Ma l n ai ae y t i h e in d P D c n r l .T er s l s o t t e s se mo e o — h a b h e oe s h t i r c ,a d h s hg e c u a y a d b t r s b l y atrt e c l r t n e t n a ih ra c r c n et t i t f h a i ai . e a i e b o
电液位置伺服控制系统实验
减小Ki
正常参数
Ki减小为40
Ki变小,ωc=1.53<2.78, ωh=14.8不变,Kg=24.5>19.1
增大Kd1
正常参数
Kd1变大为35
Kd1变大,ωc=2.1<2.78, ωh=17.1>14.8 ,Kg=21.8>19.1
减小Kd1
正常参数
Kd1减小为20
Kd1变小,ωc=3.45>2.78, ωh=12.9<14.8 ,Kg=16.8<19.1
2)阀控缸微分方程
负载流量线性化方程 流量连续性方程
忽略阀腔和管道总容积,油液的压缩性影响忽略
液压缸活塞的动力学平衡方程
3)缸输出位移对伺服阀输入电信号的传递函数 或写成:
2 伪微分反馈控制算法
对输出信号C 微分的积分仍是C,这就说明没有必要对C 进行微分
2
微分反馈控制方框图
伪微分反馈控制方框图
增大Kd2
正常参数
Kd2变大为3.3
Kd2变大,ωc=2.78不变, ωh=14.8不变,Kg=20.4>19.1
减小Kd2
正常参数
Kd2减小为0.6
Kd2变小,ωc=2.95基本不变, ωh=14.8不变,Kg=7.51<19.1
斜坡输入1
正弦输入
正弦输入,幅值5,频率1
正弦输入,幅值5,频率2.95
为能量输出单元在线 性范围内的最大值
为输入信号在线性范 围内的最大值
2
系统开环传递函数
代入系数得到
正常参数时的ωc=2.78, ωh=14.8,Kg=19.1
增大Ki
正常参数
Ki变大为120
Ki变大,ωc=4.39>2.78, ωh=14.8不变,Kg=15<19.1
- 1、下载文档前请自行甄别文档内容的完整性,平台不提供额外的编辑、内容补充、找答案等附加服务。
- 2、"仅部分预览"的文档,不可在线预览部分如存在完整性等问题,可反馈申请退款(可完整预览的文档不适用该条件!)。
- 3、如文档侵犯您的权益,请联系客服反馈,我们会尽快为您处理(人工客服工作时间:9:00-18:30)。
Fm+Y(s)
_
Xv(s)
图2-2
_
Y(s)ΔpxFRf+
Xv(s)
图2-3
Xv(s)+Xp(s)
_
Ff
图2-4
3、基于MATLAB的常规PID控制simulink仿真
Matlab-Simulink仿真框图如图(3-1)所示
图3-1 控制系统的仿真框图
KfR:比例阀反馈杆的反馈系数,数值及单位1000N/m;
先导阀位移转换为压力差环节Δpx=Kp3Y
Kp3:先导液桥压力增益,数值及单位6× pa/m;
压力差传化为输出力的环节:FRf=ΔpxAc;
Ac:主阀控制腔液压作用面积7.065× ;
将力转化为主阀芯位移的环节:m2 +cx +Ksx =FRf Fx
3.3系统的瞬态响应分析
该系统的单位阶跃响应用matlab仿真得到,如图3-4所示:
图3-4 系统的单位阶跃响应
得到瞬态响应的主要指标有:
上升时间 : ;
峰值时间 : ;
最大超调量 : ;
调整时间 : ;
震荡次数 : 6.5
3.4对系统进行PID校正
此图为在matlab中仿真的PID控制器,如图3-5所示。可以通过改变比例环节(P)、积分环节(I)、以及微分环节(D)的系数来改善控制系统的性能。
:液压缸无杆腔活塞面积, ;
:平均活塞面积, ;
:流量增益; :流量压力增益系数;
αD:主阀的流量系数,取0.7;W:面积梯度(开口的总边长),取6.4× ;
:工作油液密度830kg/ ; :流量比, / =0.6864;k: ;
选取 , ;
得 , 1.28 /N·s;
反馈环节:
:位移传感器的放大系数,6.667V/m。
2、电液比例控制系统的建立
2.1电液比例控制系统的回路设计
电液比例控制系统回路如图2-1所示:
图2-1 电液比例控制系统回路
2.2电液比例控制系统的数学模型的建立
六、总的数学模型
分别对环节的微分方程进行拉普拉斯变换。
比例放大器环节:I=Kp1U
Kp1:比例放大器的放大系数,数值及单位0.2A/V。
比例电磁铁环节Fm=Kp2I
所以时间常数 的取值范围定为 。
图3-7 取不同时间常数得到的bode图
再对其输入与扰动引起的响应分别进行分析,如图3-8所示:
图3-8 由输入和干扰引起的响应
绘制了四条阶跃输入引起的响应,由上到下依次为 。最大超调量控制在 ,调整时间 控制在0.5s。满足此条件的 ,对于干扰当 时,误差允许范围取 时,调整时间 。能较快消除干扰引起的误差。
根据上一节所述的PID的调节方法,来选择各环节的系数。图3-5 NhomakorabeaID控制器
在受到阶跃干扰的情况下,如图3-6所示,如果不加校正,当受到10000N的阶跃力作用时,稳态值趋向0.0136m,而实际是0.15m。出现了较大的误差。
图3-6 受到干扰的阶跃响应
进行PID校正
积分时间常数 时的bode图,如图3-7表示,分别用红色、绿色、蓝色表示,其增益交界频率 分别为 , , ,相位裕量 分别为 。当 取值过小时,稳定性会明显变差,所以 应取较大值,而 取较大值还会导致响应变慢。经验表明 是较为合适的。
电液比例位置系统控制的simulink仿真
1、绪论
电液比例技术是从1967年瑞士布格林公司KL比例复合阀研制成功开始的。在比例技术第一阶段,比例技术仅仅是将比例型的电—机械转换器代替电磁铁或调节手柄,阀的结构几乎没有变化,一般不参加反馈,其工作频率仅为l~5HZ,稳态滞环在4~7%之间,多用于开环系统。在比例控制的第二阶段,将耐高压比例电磁铁和比例放大器及各种内反馈原理相结合,使比例元件的工作频宽增加到5~15HZ,稳态滞环减少到3%。可用于开环或闭环控制。在比例技术的第三阶段(20世纪80年代以后),比例技术不断完善,采用了压力、位移、流量内反馈和动压反馈及智能校正、自适应控制等现代控制方法,使比例阀和比例控制系统的稳态和动态响应都进一步提高。
m2:主阀芯质量,数值及单位0.4kg;
cx:主阀芯的动阻尼系数,数值及单位50N·m/s;
Ksx:主阀弹簧刚度,数值及单位5000N/m;
阀控液压缸环节:
:活塞及负载的总质量500kg; :外部干扰力,1000~10000N;
:活塞及负载的粘性阻尼系数10000N·m/s;
:液压缸无杆腔活塞面积, ;
Kp2:比例电磁铁的电流-力增益,数值及单位40.5N/A。
先导阀环节:m1Y +cyYs+KsyY=Fm Fff
m1:先导阀移动部件质量,数值及单位0.05kg;
cy:先导阀粘性阻尼系数,数值及单位10N·m/s;
Ksy:先导阀弹簧刚度,数值及单位1000N/m;
比例阀反馈杆反馈力:Fff=KfR·