FMEA 失效分析和可靠性设计
FMEA(失效模式与影响分析)简介

没有影响;事件发生的频率要记录特定的失效原因和机理多长时间发生一次以及发生的几率。
如果为10,则表示几乎肯定要发生,工艺能力为0.33或者ppm大于10000。
5.2检测等级是评估所提出的工艺控制检测失效模式的几率,列为10表示不能检测,1表示已经通过目前工艺控制的缺陷检测。
5.3计算风险优先数RPN(riskprioritynumber)。
RPN是事件发生的频率、严重程度和检测等级三者乘积,用来衡量可能的工艺缺陷,以便采取可能的预防措施减少关键的工艺变化,使工艺更加可靠。
对于工艺的矫正首先应集中在那些最受关注和风险程度最高的环节。
RPN最坏的情况是1000,最好的情况是1,确定从何处着手的最好方式是利用RPN的pareto图,筛选那些累积等级远低于80%的项目。
推荐出负责的方案以及完成日期,这些推荐方案的最终目的是降低一个或多个等级。
对一些严重问题要时常考虑拯救方案,如:一个产品的失效模式影响具有风险等级9或10;一个产品失效模式/原因事件发生以及严重程度很高;一个产品具有很高的RPN值等等。
在所有的拯救措施确和实施后,允许有一个稳定时期,然后还应该对修订的事件发生的频率、严重程度和检测等级进行重新考虑和排序。
在设计和制造产品时,通常有三道控制缺陷的防线:避免或消除故障起因、预先确定或检测故障、减少故障的影响和后果。
FMEA正是帮助我们从第一道防线就将缺陷消灭在摇篮之中的有效工具。
FMEA是一种可靠性设计的重要方法。
它实际上是FMA(故障模式分析)和FEA(故障影响分析)的组合。
它对各种可能的风险进行评价、分析,以便在现有技术的基础上消除这些风险或将这些风险减小到可接受的水平。
及时性是成功实施FMEA的最重要因素之一,它是一个"事前的行为',而不是"事后的行为'。
为达到最佳效益,FMEA必须在故障模式被纳入产品之前进行。
FMEA实际是一组系列化的活动,其过程包括:找出产品/过程中潜在的故障模式;根据相应的评价体系对找出的潜在故障模式进行风险量化评估;列出故障起因/机理,寻找预防或改进措施。
电子元器件的可靠性设计与故障分析

电子元器件的可靠性设计与故障分析电子元器件在现代科技中扮演着至关重要的角色。
然而,由于其特殊的工作环境和复杂的电路设计,电子元器件的可靠性问题一直是制造商和设计者们面临的挑战。
本文将探讨电子元器件可靠性设计的重要性以及故障分析的方法,以便提高产品的质量和性能。
一、电子元器件可靠性设计的重要性电子元器件可靠性设计是保证电子产品正常运行的关键。
当产品的电子元器件失效时,不仅会导致生产停滞和经济损失,更重要的是会对用户的个人安全和财产安全造成威胁。
因此,通过进行可靠性设计,可以将故障率降至最低,确保产品的性能和可靠性。
1.1 材料选择与工艺控制在电子元器件的可靠性设计中,合适的材料选择和工艺控制非常重要。
首先,选择具有高稳定性和低故障率的材料能够减少电子元器件的失效风险。
同时,通过控制工艺参数,如温度、湿度和气压等,可以提高电子元器件的耐久性和稳定性。
1.2 电路设计与布局电子元器件的电路设计和布局直接影响其可靠性。
在电路设计中,合理选择电阻、电容、电感等元器件的数值和型号,能够增强电路的稳定性和抗干扰能力。
此外,合理布局电子元器件,降低电路的电感和电容耦合,有助于减少失效率。
1.3 散热设计与保护措施电子元器件的工作过程中会产生热量,散热设计和保护措施对于提高可靠性至关重要。
合理设计散热装置,保持元器件的温度在安全范围内,可以减少因热失控引起的故障。
此外,通过使用过流保护器、过压保护器等保护装置,可以避免电子元器件被损坏或过载。
二、故障分析的方法当电子元器件发生故障时,对其进行准确的故障分析是修复和改进产品的关键步骤。
下面介绍几种常见的故障分析方法。
2.1 失效模式与效应分析(FMEA)失效模式与效应分析是一种系统地分析电子元器件故障的方法。
通过识别潜在的失效模式和分析其可能的影响,可以有针对性地采取措施来防止故障的发生或减小其影响。
2.2 元器件失效分析元器件失效分析是通过对元器件的物理性能、电性能和结构特征等进行测试和分析,来确定其失效原因。
FMEA是一种可靠性设计的重要方法

FMEA是一种可靠性设计的重要方法FMEA(Failure Mode and Effects Analysis,失效模式及影响分析)是一种可靠性设计的重要方法。
它通过系统性地分析可能的失效模式与其潜在影响,旨在识别并消除或减轻潜在失效的风险,从而提高产品、系统或过程的可靠性。
FMEA的基本原理是先通过分析系统的设计、功能、构造、工作原理等方面,确定可能的失效模式,再分析各失效模式的潜在影响。
FMEA通常包含以下步骤:1.确定FMEA的范围和目的:明确分析的范围和要达到的目标,例如分析一些特定产品的可靠性问题、分析一些特定工作流程的潜在风险等。
明确目的有助于更好地确定分析的重点和方向。
2.组建FMEA团队:FMEA需要多学科的团队参与,例如设计、工程、质量等部门的成员。
他们应具备相应领域的专业知识和经验,能够全面理解和分析系统,从不同角度提出有益意见。
3.收集系统信息:收集系统的设计资料、技术规范、产品手册、相关数据等。
了解系统的设计特点、工作原理、功能要求以及与其他系统的接口等信息。
4.确定分析的对象:确定要分析的系统、产品或过程,并明确分析的边界和范围。
可以将系统划分为不同的子系统或模块进行分析。
5.识别失效模式:通过头脑风暴、故障树分析、过程流程图等方法,系统地识别可能的失效模式。
对于每个失效模式,需要描述其性质、影响范围、持续时间、概率等信息。
6.评估失效影响:对每个失效模式进行量化或定性评估,分析其潜在影响。
包括对产品性能、安全性、可靠性、可用性等方面的影响进行评估,并将其与设计要求进行对比。
7.评估风险严重性:根据失效的潜在影响和频率,评估每个失效模式的风险严重性。
通常使用风险矩阵或风险指数来进行评估和排序。
8.提出改进措施:针对风险严重性较高的失效模式,制定改进措施以减轻或消除潜在失效的风险。
这些措施可以包括改进设计、增加冗余、调整工艺流程等。
9.跟踪和监控改进措施:实施改善措施后,需要对其有效性进行跟踪和监控,以确保风险得到控制并持续改进。
五大工具潜在失效模式与效果分析FMEA
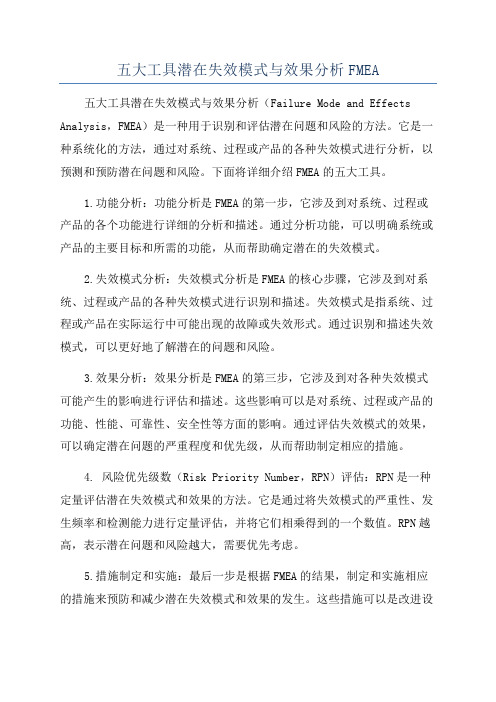
五大工具潜在失效模式与效果分析FMEA 五大工具潜在失效模式与效果分析(Failure Mode and Effects Analysis,FMEA)是一种用于识别和评估潜在问题和风险的方法。
它是一种系统化的方法,通过对系统、过程或产品的各种失效模式进行分析,以预测和预防潜在问题和风险。
下面将详细介绍FMEA的五大工具。
1.功能分析:功能分析是FMEA的第一步,它涉及到对系统、过程或产品的各个功能进行详细的分析和描述。
通过分析功能,可以明确系统或产品的主要目标和所需的功能,从而帮助确定潜在的失效模式。
2.失效模式分析:失效模式分析是FMEA的核心步骤,它涉及到对系统、过程或产品的各种失效模式进行识别和描述。
失效模式是指系统、过程或产品在实际运行中可能出现的故障或失效形式。
通过识别和描述失效模式,可以更好地了解潜在的问题和风险。
3.效果分析:效果分析是FMEA的第三步,它涉及到对各种失效模式可能产生的影响进行评估和描述。
这些影响可以是对系统、过程或产品的功能、性能、可靠性、安全性等方面的影响。
通过评估失效模式的效果,可以确定潜在问题的严重程度和优先级,从而帮助制定相应的措施。
4. 风险优先级数(Risk Priority Number,RPN)评估:RPN是一种定量评估潜在失效模式和效果的方法。
它是通过将失效模式的严重性、发生频率和检测能力进行定量评估,并将它们相乘得到的一个数值。
RPN越高,表示潜在问题和风险越大,需要优先考虑。
5.措施制定和实施:最后一步是根据FMEA的结果,制定和实施相应的措施来预防和减少潜在失效模式和效果的发生。
这些措施可以是改进设计、优化工艺、加强检测和监控等。
通过实施这些措施,可以避免或降低潜在问题和风险的发生。
FMEA是一种非常实用的分析工具,广泛应用于各个行业和领域。
它可以帮助组织识别和评估潜在问题和风险,从而采取预防措施,提高系统、过程或产品的质量和可靠性。
FMEA失效模式和效果分析
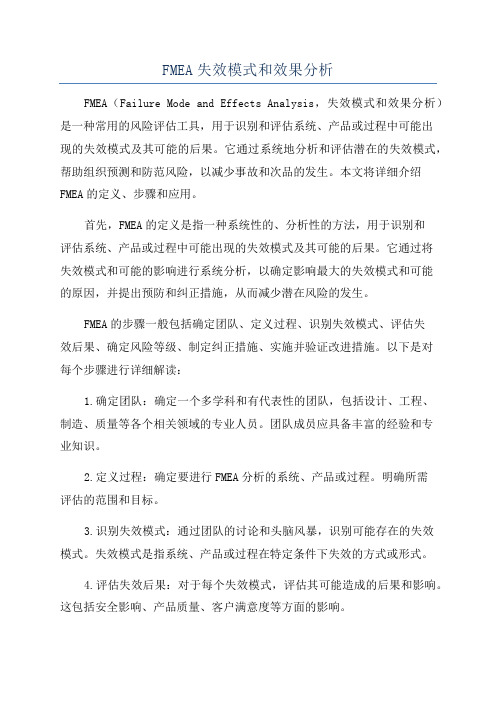
FMEA失效模式和效果分析FMEA(Failure Mode and Effects Analysis,失效模式和效果分析)是一种常用的风险评估工具,用于识别和评估系统、产品或过程中可能出现的失效模式及其可能的后果。
它通过系统地分析和评估潜在的失效模式,帮助组织预测和防范风险,以减少事故和次品的发生。
本文将详细介绍FMEA的定义、步骤和应用。
首先,FMEA的定义是指一种系统性的、分析性的方法,用于识别和评估系统、产品或过程中可能出现的失效模式及其可能的后果。
它通过将失效模式和可能的影响进行系统分析,以确定影响最大的失效模式和可能的原因,并提出预防和纠正措施,从而减少潜在风险的发生。
FMEA的步骤一般包括确定团队、定义过程、识别失效模式、评估失效后果、确定风险等级、制定纠正措施、实施并验证改进措施。
以下是对每个步骤进行详细解读:1.确定团队:确定一个多学科和有代表性的团队,包括设计、工程、制造、质量等各个相关领域的专业人员。
团队成员应具备丰富的经验和专业知识。
2.定义过程:确定要进行FMEA分析的系统、产品或过程。
明确所需评估的范围和目标。
3.识别失效模式:通过团队的讨论和头脑风暴,识别可能存在的失效模式。
失效模式是指系统、产品或过程在特定条件下失效的方式或形式。
4.评估失效后果:对于每个失效模式,评估其可能造成的后果和影响。
这包括安全影响、产品质量、客户满意度等方面的影响。
5.确定风险等级:根据失效模式的后果和可能性,评估其风险等级。
通常使用风险矩阵来划分风险等级,以帮助确定重要性和优先级。
6.制定纠正措施:针对高风险等级的失效模式,制定相应的纠正措施。
这包括预防措施来防止失效的发生,以及纠正措施来解决已经发生的失效。
7.实施并验证改进措施:根据纠正措施的计划,执行相应的改进措施,并进行验证和确认。
确保改进措施的有效性和可行性。
FMEA具有广泛的应用领域。
它可以用于设计过程中的设计FMEA,用于评估产品的可靠性和安全性;也可以用于制造过程中的制造FMEA,用于识别和评估可能导致产品质量问题的制造过程;同时,FMEA还可以用于服务过程中的服务FMEA,用于评估可能影响服务质量和客户满意度的过程。
FMEA在机械设计中的可靠性分析

FMEA在机械设计中的可靠性分析简介在机械设计领域中,可靠性是一个至关重要的指标,决定了产品在使用过程中的稳定性和安全性。
为了评估和提高机械产品的可靠性,工程师们通常会采用FMEA(Failure Mode and Effects Analysis)分析方法。
什么是FMEAFMEA是一种系统性的分析方法,旨在识别产品或系统可能存在的潜在故障模式和故障对系统功能的影响。
通过对潜在故障模式的识别和评估,可以帮助设计团队在设计阶段识别和消除设计缺陷,从而提高产品的可靠性。
FMEA的工作原理FMEA分析通常分为三个关键步骤:识别潜在故障模式、评估潜在故障的影响和严重性、确定并实施改进措施。
在识别潜在故障模式阶段,团队会收集和整理可能的故障模式,包括设备失效、材料损坏、操作错误等。
接着进行评估,根据潜在故障的影响和严重性对它们进行排序,并确定优先处理的故障。
最后,设计团队根据评估结果提出改进和预防措施,避免潜在故障的发生。
FMEA在机械设计中的应用在机械设计中,FMEA的应用可以帮助设计团队避免或减少设计缺陷,降低产品的故障率和维修成本。
通过FMEA分析,设计团队可以识别潜在的故障模式和问题,及早进行改进,确保产品在生产和使用过程中的可靠性和安全性。
例如,在设计一个机械零部件时,可以通过FMEA分析识别可能的故障模式,如材料疲劳、装配不当等,从而改进设计和工艺,提高产品的可靠性。
结论FMEA作为一种重要的分析方法,在机械设计中扮演着关键的角色。
通过FMEA分析,设计团队可以及早发现并解决潜在的故障问题,提高产品的可靠性和安全性。
因此,在机械设计过程中,设计团队应该充分利用FMEA这一工具,从而设计出高质量、可靠性强的机械产品。
失效模式与影响分析FMEA
失效模式与影响分析FMEA失效模式与影响分析(Failure Mode and Effects Analysis, FMEA)是一种常用的质量管理工具,主要用于识别潜在的失效模式及其对系统、产品或流程性能的影响,以便采取相应的预防和纠正措施,提高质量和可靠性。
FMEA的过程通常包括以下几个步骤:1.确定分析范围:确定需要进行FMEA分析的系统、产品或流程,并明确分析的目标。
2.定义失效模式:识别可能的失效模式,即系统、产品或流程可能出现的各种问题、故障或失效,包括设计失效、制造失效、装配失效等。
3.评估失效影响:对每个失效模式进行评估,分析其对系统、产品或流程性能的影响。
评估可以从多个维度进行,如安全性、可靠性、功能性、经济性等。
4.确定失效原因:确定每个失效模式的潜在原因。
可以使用多种工具和方法,如因果图、5W1H、鱼骨图等,来帮助确定失效的根本原因。
5.评估现有控制措施:评估当前已经实施的控制措施对失效模式的效果。
确定哪些失效模式已经通过其他控制措施得到有效控制,哪些失效模式仍然存在较高的风险。
6.制定改进措施:针对高风险的失效模式,制定相应的改进措施。
改进措施可以包括设计改进、工艺改进、培训和教育、检测和监控等。
7.实施并验证改进措施:将改进措施实施到实际生产或运营中,并验证其效果。
跟踪和监控改进措施的实施情况,并对其效果进行评估。
通过进行FMEA分析,可以帮助组织识别和管理潜在的风险,提前采取预防措施,减少系统、产品或流程的失效概率,以实现质量和可靠性的提升。
FMEA分析可以应用于各个领域,如制造业、医疗设备、航空航天、汽车等。
FMEA的应用具有以下几个特点和优势:1.预防导向:FMEA分析主要关注于预防失效模式的发生,通过分析潜在的失效原因和影响,预测可能的失效模式,制定相应的预防措施,从而避免质量问题的发生。
2.多维度评估:FMEA分析不仅关注失效模式的影响对系统、产品或流程的影响,还可以从多个维度进行评估,如安全性、可靠性、功能性、经济性等,以全面了解失效模式的风险。
{品质管理FMEA}FEMA失效模式分析
此处是大标题样稿字样十五字以内F M E A 概 要何谓FMEA:是描述为一组系统化的活动,其目的是:A:发现和评价产品/过程中潜在的失效及其失效效应B:找到能够避免或减少这些潜在失效发生的措施C:将上述整个过程文件化它是对设计过程的更完善化,明确必须做何种设计和过程才能满足顾客的需要。
F M E A 的實施由于尽可能的持续改进产品和过程是企业的趋势,所以使用FMEA作为专门技术应用,以识别并帮助减少潜在的隐忧一直是非常重要的。
对于产品抱怨的研究结果表明,全面实施FMEA能够避免许多抱怨事件的发生。
适时性是成功实施FMEA的最重要因素之一,它是一个“事发前”的行为,而不是“后见之明”的行动。
为打达到最佳效益,FMEA必须在设计或过程失效模式被无意地纳入产品或过程之前进行。
事先花时间适当地完成FMEA分析,能够更容易、低成本地对产品过程进行修改,从而减轻事后修改危机。
FMEA能够减少或消除原因进行预防和矫正而带来更大损失的机会。
FMEA小组应该有充分的沟通和整合。
图一描述了一个FMEA应该被执行的程序,它并不是简单的把表格填满的案 例,而是进一步理解FMEA的程序,以消除风险和计划能确保顾客满意 的适当控制。
当FMEAs被展开,会有三种基本的个案。
每个案例都有不同的领域和重点:个案1:新设计、新技术或新过程。
该FMEA的领域是完成设计、技术或过 程。
个案2:修改现有的设计或过程(假设现有的设计或过程已经有一个FMEA)。
该 FMEA的领域应该在于修改设计或过程,有可能因为某修改和市场历史 反映而有交互影响。
个案3:在一个新的环境、地点或应用上,利用的现有的设计或过程(假设现有 的设计或过程已经有一个FMEA)。
该FMEA的领域是对现有设计或过 程新的环境或地点上的影响分析。
在FMEA的编制工作中,必须明确的指派每个人的职责,但是FMEA的输入还是应该依靠小组努力。
小组应该由知识丰富的人员组成(如:对设计、分析、测试、制造、装配、服务、回收再利用、质量及可靠度等方面的工程人员)FMEA由相关负责组织中的工程师所组成,其可以是OEM如:生产最终产品、供货商,或是分包商。
FMEA失效分析与失效模式分析全
擦伤或损坏)。 由于横向性能差而在锻件中出现分离线的失效现象。
11
在服役条件下由于质量恶化而产生失效的原因包括
过载或未预见的加载条件。 磨损(磨蚀、因过度磨损而咬住、粘住、擦伤、气蚀)。 腐蚀(包括化学接触、应力腐蚀、腐蚀疲劳、脱锌、铸铁石
找出被分析对象的“单点故障”。所谓单点故障是指这种故障单独发 生时,就会导致不可接受的或严重的影响后果。一般说来,如果单点 故障出现概率不是极低的话,则应在设计、工艺、管理等方面采取切 实有效的措施。产品发生单点故障的方式就是产品的单点故障模式。
为制定关键项目清单或关键项目可靠性控制计划提供依据。 为可靠性建模、设计、评定提供信息。 揭示安全性薄弱环节,为安全性设计(特别是载人飞船的应急措施、
16
什么是失效分析?
失效分析:考察失效的构件及失效的情景(模式), 以确定失效的原因。
失效分析的目的:在于明确失效的机理与原因。改 进设计、改进工艺过程、正确地使用维护。
失效分析的主要内容:包括明确分析对象,确定失 效模式,研究失效机理,判定失效原因,提出预防 措施(包括设计改进)。
17
失效分析的要点?
失效模式的判断分为定性和定量分析两个方面。在一般 情况下,对一级失效模式的判断采用定性分析即可。而 对二级甚至三级失效模式的判断,就要采用定性和定量、 宏观和微观相结合的方法。
19
一级失效模式的分类
20 主要失效模式的分类与分级
21
如某型涡轮叶片在第一榫齿处发生断裂,通过断口 的宏观特征可确定一级失效模式为疲劳失效。然后 通过对断口源区和扩展区特征分析和对比,并结合 有限元应力分析等,可作出该叶片的断裂模式为起 始应力较大的高周疲劳断裂的判断,即相当于作出 了三级失效模式的判断。
FEMA潜在失效模式及分析
2021/5/27re Mode Analysis)、FTA(Failure Tree Analysis) FMEA是一种事前行为 FMA是一种事后行为。是对产品/过程已经发生的失效模式分析其产生的原因,评 估其后果及采取纠正措施的一种活动,类似项目的FMA是FMEA的重要输入参数资 料。
严重度:失效模式的后果有多严重?
起因:导致失效模式的原因
频度:失效起因发生的频率如何?
现行控制:探测或防止将失效传递到后续“顾客”的现行方法
探测度:失效模式/起因一旦发生,能否探测得出? 5、FMEA的基本要素和组成部分 FMEA计划、原因、失效模式、后果、频度、探测度、严重度、风险分析和潜 在的失效模式及后果分析解释、执行建议措施并验证其有效性、实施措施。
FMEA是由下到上进行分析的,FTA是由上到下进行分析的。 7、FMEA与失效分析比较 失效分析:
试销已经产生
核心:纠正
诊断已知的失效
指引的是开发和生产
FMEA: 失效还没有产生,可能产生,但不一定会发生
核心:预防
评估风险和潜在失效模式的影响
开始于产品设计和工艺开发活动之前
指引贯穿整个产品周期
2021/5/27
1
3、FMEA的种类 a)SFMEA——系统FMEA b)DEMEA——产品FMEA(设计FMEA) c)PFMEA——过程FMEA(制造/装配FMEA) d)AFMEA——应用FMEA e)SFMEA——服务FMEA f)PFMEA——采购FMEA 4、FMEA的主要概念 功能:该设计/过程要做什么?(设计的意图或者说是目的) 失效模式:设计/产品或过程失效的表现形式 后果:发生失效模式后会怎么样?
b)确定能够消除或减少潜在失效发生机会的措施;
- 1、下载文档前请自行甄别文档内容的完整性,平台不提供额外的编辑、内容补充、找答案等附加服务。
- 2、"仅部分预览"的文档,不可在线预览部分如存在完整性等问题,可反馈申请退款(可完整预览的文档不适用该条件!)。
- 3、如文档侵犯您的权益,请联系客服反馈,我们会尽快为您处理(人工客服工作时间:9:00-18:30)。
化学
吸水性高的缺点:通电水分子扩散,造成电气性质改变 空洞而剥离
焊锡回流中组件模块水分造成模块膨胀和龟裂
失效的原因
静电释放ESD 电迁移 腐蚀和扩散 焊点可靠性 疲劳和潜变 覆晶结合的焊点
静电释放ESD
减少静电释放的措施
增加环境湿度 增加衣服的电导率 带腕带之类 增加ESD训练
电迁移
解决方法 降低电迁移率 1.使用抗电迁移能力好的导体-铜 2.增加晶粒尺寸 3.缩短导线长度
腐蚀和扩散
使用Pt,金等耐腐蚀材料
扩散解决
低温 增加扩散阻挡层
焊点可靠性
潜变(creep) 在高温受力时,假设温度和负载足够大, 则对象会产生塑性应变,称为“潜变” 特点:不可恢复原状
Precon Test T/C Test T/S Test HTST Test T&H Test PCT Test
预处理 温度循环测试 热冲击 高温储藏 温度和湿度 高温蒸煮
失效分析和可靠性设计
失效机制和可靠性设计 失效分析 分析)
可靠性工程研究包括可靠性设计、可靠性
测试及数据分析、失效分析
浴缸曲线
早期失效——内烧过程 平滑部分——过应力失效 磨耗失效——磨耗积累而失效
失效机制及可靠性分析 失效原因:机械 电 以焊锡回流为例 1.有机材料吸水性要低
疲劳
疲劳 指对象受到一个小于机械强度的周期性应 力,经过一段时间(某周期数)之后而断裂 疲劳是大部分金属失效原因
覆晶结合的焊点
由于芯片和基板的热膨胀系数不同 离中心远的焊点受到应力越大,变形大
失效分析
分析仪器和技术
X光绕射分析
电子显微镜 光学显微镜
可靠性测试项目