真空镀膜技术
不同真空镀膜技术的原理、优势与缺陷分析
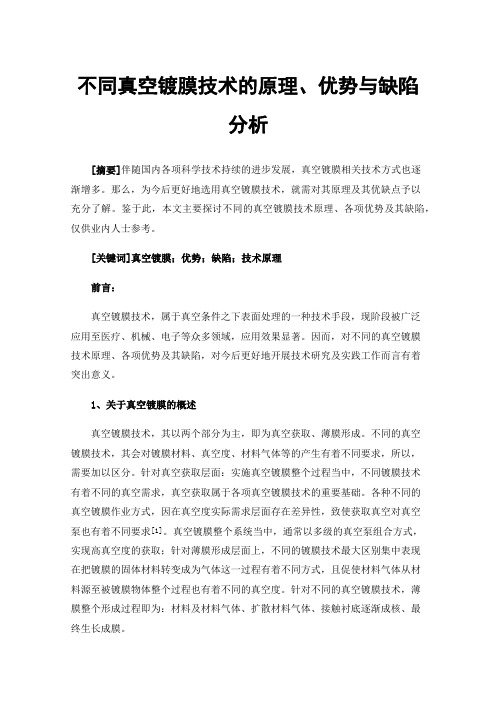
不同真空镀膜技术的原理、优势与缺陷分析[摘要]伴随国内各项科学技术持续的进步发展,真空镀膜相关技术方式也逐渐增多。
那么,为今后更好地选用真空镀膜技术,就需对其原理及其优缺点予以充分了解。
鉴于此,本文主要探讨不同的真空镀膜技术原理、各项优势及其缺陷,仅供业内人士参考。
[关键词]真空镀膜;优势;缺陷;技术原理前言:真空镀膜技术,属于真空条件之下表面处理的一种技术手段,现阶段被广泛应用至医疗、机械、电子等众多领域,应用效果显著。
因而,对不同的真空镀膜技术原理、各项优势及其缺陷,对今后更好地开展技术研究及实践工作而言有着突出意义。
1、关于真空镀膜的概述真空镀膜技术,其以两个部分为主,即为真空获取、薄膜形成。
不同的真空镀膜技术,其会对镀膜材料、真空度、材料气体等的产生有着不同要求,所以,需要加以区分。
针对真空获取层面:实施真空镀膜整个过程当中,不同镀膜技术有着不同的真空需求,真空获取属于各项真空镀膜技术的重要基础。
各种不同的真空镀膜作业方式,因在真空度实际需求层面存在差异性,致使获取真空对真空泵也有着不同要求[1]。
真空镀膜整个系统当中,通常以多级的真空泵组合方式,实现高真空度的获取;针对薄膜形成层面上,不同的镀膜技术最大区别集中表现在把镀膜的固体材料转变成为气体这一过程有着不同方式,且促使材料气体从材料源至被镀膜物体整个过程也有着不同的真空度。
针对不同的真空镀膜技术,薄膜整个形成过程即为:材料及材料气体、扩散材料气体、接触衬底逐渐成核、最终生长成膜。
2、不同的真空镀膜技术基本原理及优缺点2.1在真空热蒸发式镀膜技术层面针对真空热蒸发式镀膜技术的基本原理,即处于真空条件之下,把材料气化后,直接射向至基片沉积,促使特定薄膜形成。
在工艺流程层面上,主要是先把材料蒸发处理或是升华成气态粒子,材料所蒸发出的这些气态粒子从蒸发源处离开后,处于真空腔体内部持续飞行扩散,最终到达基底部位,凝聚成核,材料分子持续沉积后,晶核长大逐渐成膜。
真空镀膜技术和真空镀膜机

薄膜制备技术
2.1 薄膜的物理气相沉积
2.2 薄膜的化学气相沉积
2.3 富森钛金设备开发的溶液镀膜技术
2.4 迪通恒业科技开发的外延制膜技术
第一节
薄膜的物理气相沉积
2.1.1 引言
薄膜生长方法是获得薄膜的关键。薄膜材料的质量和性能不仅依赖于 薄膜材料的化学组成,而且与薄膜材料的制备技术具有一定的关系。 随着科学技术的发展和各学科之间的相互交叉, 相继出现了一些新的 薄膜制备技术。这些薄膜制备方法的出现, 不仅使薄膜的质量在很大 程度上得以改善, 而且为发展一些新型的薄膜材料提供了必要的制备 技术。
第一节
2.1.2 PVD法
一、真空蒸发镀膜法
薄膜的物理气相沉积
要点:
●真空蒸发原理
真空蒸发镀膜法(简称真空 蒸镀)是在真空室中,加热蒸发 容器中待形成薄膜的原材料, 使其原子或分子从表面气化逸 出,形成蒸气流,入射到基片 表面,凝结形成固态薄膜的方 法。
●蒸发源的蒸发特性及膜厚分布 ●蒸发源的类型 ●合金及化合物的蒸发
点源与小平面蒸发源相 比,厚度的均匀性要好
m t0 4 h2 t0 m h2
t 1 t 0 [1 x h2 ]3 2
一些������
t 1 t 0 [1 x h2 ]2
但淀积速率要低得多, 单位质量的原料所得膜 厚1/4
第一节
2.1.2 PVD法
dm
m
cos d
m cos cos mh2 t 2 r (h2 x 2 ) 2
最大厚度:正上方:θ=0,φ=0时:
t0
m h2
t 1 t 0 [1 x h2 ]2
第一节
真空溅射镀膜技术
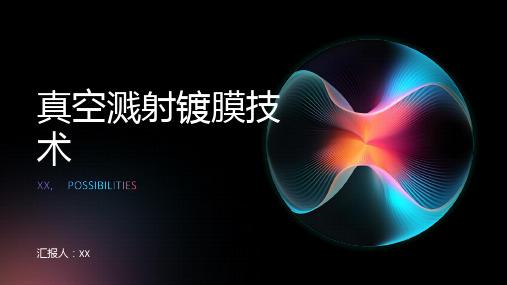
溅射材料:通常采用金属、陶瓷、半导体等材料
溅射过程:高能粒子轰击固体表面,使固体表面的原子或分子获得足够的能量脱离表面,形成溅射现象
溅射镀膜的原理
原理:利用高能粒子轰击靶材,使其表面的原子或分子脱离靶材并沉积在基材上
溅射源:通常是金属或非金属材料,如铝、钛、铬等
脉冲溅射镀膜
原理:利用高压脉冲电源,使靶材表面产生脉冲电场,使靶材表面的原子或分子脱离靶材表面,沉积到基材上形成薄膜。
特点:沉积速率快,膜层致密,膜层厚度均匀,适用于大面积镀膜。
应用:广泛应用于太阳能电池、显示器、半导体等领域。
优点:可以提高膜层的附着力和耐腐蚀性,降低生产成本。
真空溅射镀膜技术的特点
半导体领域
半导体芯片制造:溅射镀膜技术用于制造半导体芯片,如集成电路、存储器等。
半导体封装:溅射镀膜技术用于半导体封装,如引线框架、导线架等。
半导体器件制造:溅射镀膜技术用于制造半导体器件,如晶体管、二极管等。
半导体材料研究:溅射镀膜技术用于研究半导体材料,如硅、锗、砷化镓等。
金属化领域
半导体制造:用于制造集成电路、传感器等电子设备
设备故障处理:遇到设备故障时,及时联系专业人员进行维修
设备维护周期:定期进行设备维护,确保设备正常运行
设备运行中的监控:注意观察设备运行状态,及时调整参数
设备停机后的清理:清理设备内部残留的镀膜材料和杂质
设备启动前的检查:确保电源、气源、水源等正常
设备启动顺序:按照说明书上的要求进行
真空溅射镀膜设备的常见问题及解决方案
原理:利用射频能量使靶材表面原子或分子获得足够的能量,从而被溅射出来
特点:沉积速率快,膜层致密,纯度高
真空镀膜技术

真空镀膜技术一、概述真空镀膜技术是一种利用真空条件下的物理或化学反应,将金属或非金属材料沉积在基材表面形成一层薄膜的技术。
该技术具有广泛的应用领域,包括光学、电子、医疗、环保等。
二、原理真空镀膜技术利用真空条件下的物理或化学反应,将金属或非金属材料沉积在基材表面形成一层薄膜。
其主要原理包括:1. 离子镀膜:利用离子轰击基材表面使其表面活性增强,然后通过离子束轰击目标材料产生离子和原子,最终在基材表面形成一层薄膜。
2. 蒸发镀膜:将目标材料加热至其沸点以上,在真空环境中使其升华并沉积在基材表面形成一层薄膜。
3. 磁控溅射镀膜:利用高能量离子轰击靶材产生靶材原子,并通过磁场控制靶材原子沉积在基材表面形成一层薄膜。
三、设备真空镀膜技术需要使用专门的设备,主要包括:1. 真空镀膜机:包括离子镀膜机、蒸发镀膜机和磁控溅射镀膜机等。
2. 真空泵:用于将反应室内的气体抽出,使其达到真空状态。
3. 控制系统:用于控制反应室内的温度、压力、离子束能量等参数。
四、应用真空镀膜技术具有广泛的应用领域,包括:1. 光学:利用金属或非金属材料在基材表面形成一层反射或透过特定波长光线的薄膜,制作光学器件如反射镜、滤光片等。
2. 电子:利用金属或非金属材料在基材表面形成一层导电或绝缘的薄膜,制作电子元器件如晶体管、集成电路等。
3. 医疗:利用金属或非金属材料在基材表面形成一层生物相容性好的涂层,制作医疗器械如人工关节、心脏起搏器等。
4. 环保:利用金属或非金属材料在基材表面形成一层具有催化作用的薄膜,制作环保设备如汽车尾气净化器、工业废气处理设备等。
五、优势真空镀膜技术具有以下优势:1. 薄膜厚度可控:通过控制反应条件和时间,可以精确控制薄膜的厚度。
2. 薄膜质量高:在真空环境中进行反应,可以避免杂质和气体的污染,从而保证薄膜质量高。
3. 应用广泛:真空镀膜技术可以应用于多种材料和领域,具有广泛的应用前景。
六、挑战真空镀膜技术面临以下挑战:1. 成本高:真空镀膜设备和耗材成本较高,限制了其在大规模生产中的应用。
真空镀膜技术
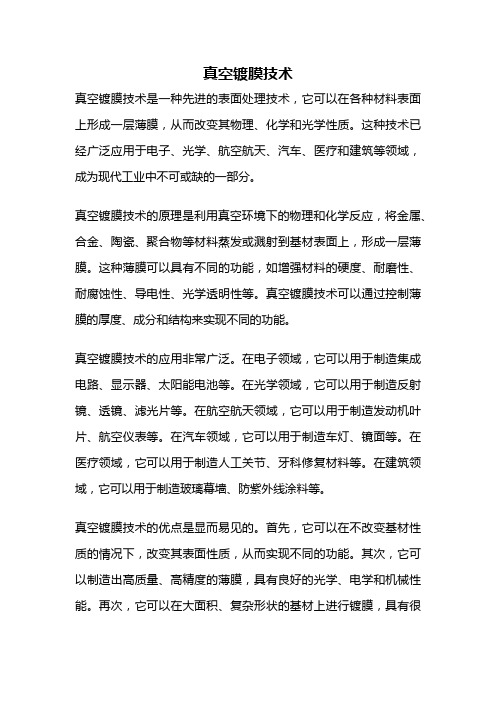
真空镀膜技术真空镀膜技术是一种先进的表面处理技术,它可以在各种材料表面上形成一层薄膜,从而改变其物理、化学和光学性质。
这种技术已经广泛应用于电子、光学、航空航天、汽车、医疗和建筑等领域,成为现代工业中不可或缺的一部分。
真空镀膜技术的原理是利用真空环境下的物理和化学反应,将金属、合金、陶瓷、聚合物等材料蒸发或溅射到基材表面上,形成一层薄膜。
这种薄膜可以具有不同的功能,如增强材料的硬度、耐磨性、耐腐蚀性、导电性、光学透明性等。
真空镀膜技术可以通过控制薄膜的厚度、成分和结构来实现不同的功能。
真空镀膜技术的应用非常广泛。
在电子领域,它可以用于制造集成电路、显示器、太阳能电池等。
在光学领域,它可以用于制造反射镜、透镜、滤光片等。
在航空航天领域,它可以用于制造发动机叶片、航空仪表等。
在汽车领域,它可以用于制造车灯、镜面等。
在医疗领域,它可以用于制造人工关节、牙科修复材料等。
在建筑领域,它可以用于制造玻璃幕墙、防紫外线涂料等。
真空镀膜技术的优点是显而易见的。
首先,它可以在不改变基材性质的情况下,改变其表面性质,从而实现不同的功能。
其次,它可以制造出高质量、高精度的薄膜,具有良好的光学、电学和机械性能。
再次,它可以在大面积、复杂形状的基材上进行镀膜,具有很高的生产效率。
最后,它可以使用多种材料进行镀膜,具有很高的灵活性和适应性。
当然,真空镀膜技术也存在一些挑战和限制。
首先,它需要高昂的设备和技术投入,成本较高。
其次,它对基材表面的处理要求较高,需要进行清洗、抛光等处理,否则会影响薄膜的质量。
再次,它对环境的要求较高,需要在无尘、无湿、无氧的环境下进行。
最后,它的应用范围受到材料的限制,某些材料不适合进行真空镀膜。
总的来说,真空镀膜技术是一种非常重要的表面处理技术,具有广泛的应用前景。
随着科技的不断进步和应用领域的不断扩展,真空镀膜技术将会得到更加广泛的应用和发展。
真空镀膜技术简介

5.现状 5.现状
由于真空镀膜起步较晚,又受真空技术的限制,前期发展较慢, 属于新的技术。目前,国外一些发达的国家应用较为广泛。国内起步 更晚,受技术的限制,应用范围较少,潜力较大,待进一部开发。
(二)
1.常用的镀膜设备(外形) 1.常用的镀膜设备(外形) 常用的镀膜设备 1.1. 电镀法、化学镀法一般是以槽体流水线的形式进行的,设 备较为大型,昂贵。 1.2. 箱式真空镀膜机(立式):单门、双门。 1.3. 卷绕式真空镀膜机(卧式)。 1.4. 间歇式镀膜机(立式):两箱、三箱。 1.5. 大型镀膜流水线:根据客户要求进行设计。 这里没有涉及CVD镀膜设备 这里没有涉及CVD镀膜设备
4.真空蒸镀镀膜机的相关参数和结构1 4.真空蒸镀镀膜机的相关参数和结构 真空蒸镀镀膜机的相关参数和结构1
4.1. 真空蒸镀镀膜机的相关参数 4.1.1. 真空室尺寸 4.1.2. 最高加热温度 4.1.3. 高、低真空泵抽速 4.1.4. 膜厚控制精度 4.1.5. 蒸发器的参数 4.1.6. 离子源的参数 4.1.7. 连续镀层和时间 4.1.8. 充气系统的参数 4.1.9. 深冷的参数 4.1.10. 操作系统、软件 另外:冷却水、压缩空气、电 量
内容概要
(二).镀膜的设备
1.常见的镀膜设备 1.常见的镀膜设备 2.常见的真空镀膜机 2.常见的真空镀膜机 3.各国的真空镀膜机的现状 3.各国的真空镀膜机的现状 4.真空蒸镀镀膜机的相关参数和结构 4.真空蒸镀镀膜机的相关参数和结构
(三).真空镀膜的工艺
1.工艺参数 1.工艺参数 2.塑料件真空镀膜工艺流程 2.塑料件真空镀膜工艺流程 3.镀膜制品的品质参数 3.镀膜制品的品质参数
3.定义2 定义2
电子束加热蒸镀是将膜料放入水冷铜坩埚中,利用高能量密度的 电子束加热,使膜料熔融气化并凝结在基体表面成膜。 为了改善附着力,增加膜的致密性,镀膜前,镀膜过程中辅助离 子束进行轰击的镀膜方法称为离子束辅助蒸镀。
真空镀膜技术工艺流程

真空镀膜技术工艺流程真空镀膜技术是一种在真空条件下将金属薄膜或其他材料沉积到基材表面的工艺。
它广泛应用于光学、电子、汽车、建筑等领域,用于提高材料的光学性能、耐腐蚀性能和装饰性能。
下面将介绍真空镀膜技术的工艺流程。
1. 基材准备首先,需要准备待镀膜的基材。
基材可以是玻璃、塑料、金属等材料,不同的基材需要采用不同的预处理工艺。
通常情况下,基材需要进行清洗、去油、去尘等处理,以确保镀膜的附着力和质量。
2. 蒸发材料准备在真空镀膜工艺中,需要使用一种或多种蒸发材料作为镀膜材料。
这些蒸发材料可以是金属、氧化物、氮化物等。
在镀膜前,需要将这些材料加工成均匀的块状或颗粒状,以便于在真空条件下进行蒸发。
3. 真空系统抽真空在进行镀膜之前,需要将反应室内的气体抽空,建立起一定的真空度。
通常情况下,真空系统会采用机械泵、分子泵等设备进行抽真空,直到达到所需的真空度为止。
4. 加热基材在真空镀膜过程中,基材通常需要加热到一定温度。
加热可以提高蒸发材料的蒸发速率,同时也有助于提高镀膜的致密性和附着力。
加热温度的选择需要根据具体的镀膜材料和基材来确定。
5. 蒸发镀膜当真空度和基材温度达到要求后,开始蒸发镀膜。
蒸发材料被加热后,会蒸发成气体或蒸汽,并沉积到基材表面上。
在镀膜过程中,可以通过控制蒸发材料的温度、蒸发速率和镀膜时间来控制镀膜的厚度和性能。
6. 辅助工艺在镀膜过程中,可能需要进行一些辅助工艺来改善镀膜的性能。
例如,可以通过离子轰击、辅助加热、喷洒惰性气体等手段来提高镀膜的致密性和光学性能。
7. 检测和包装镀膜完成后,需要对镀膜膜层进行检测,以确保其质量和性能符合要求。
常用的检测手段包括光学测量、显微镜观察、机械性能测试等。
最后,对镀膜产品进行包装,以防止镀膜层受到污染或损坏。
总结真空镀膜技术是一种高精度、高效率的表面处理技术,可以为材料赋予特定的光学、电子、机械等性能。
通过控制镀膜工艺流程中的各个环节,可以实现对镀膜膜层厚度、组分、结构和性能的精确控制。
真空镀膜技术基础
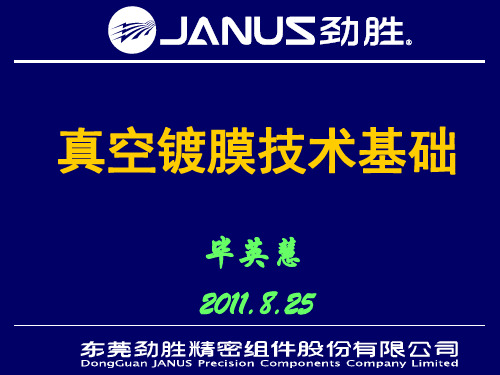
1.玻璃衰减器 2.透镜 3.光圈 4.光电池 5.分光器 6.透镜 7.基片 8.探头 9.靶 10.真空室 11.激光器
图2-10 激光加热式蒸发源
2.3 真空蒸发镀膜机
2.3.1 间歇式真空蒸发镀膜机
1) 立式真空蒸发镀膜机 2) 卧式真空蒸发镀膜机
4)由于在低电压大电流状态下工作,因此较 安全且易于自动控制;
5)阴极寿命长、结构简单。
1.冷却水套 2.空心阴极 3.辅助阳极 4.聚束线圈 5.枪头 6.膜材 7.坩埚 8.聚焦磁场 9.基片
图2-9 空心阴极等离子体电阻式加热式蒸发源
2.2.5 激光加热式蒸发源
---工厂不用,加工精密特殊功能的材料用
真空溅射镀膜
在真空条件下,利用低压等离子体气体 放电中的溅射现象制备薄膜,即真空溅射镀 膜。
图3-1 离子轰击固体表面时发生的物理过程
与溅射率有关的因素
溅射率与靶材有关 溅射率与入射正离子的能量有关 溅射率与入射离子的种类有关 溅射率与离子入射角有关 溅射率与靶材温度有关
溅射镀膜特点
(2)被蒸发材料置于水冷铜坩锅内,可避免坩 埚材料污染,可制备高纯薄膜;
(3)电子束蒸发粒子动能大,有利于获得致密、 结合力好的膜层。
电子束加热蒸发的缺点:
(1)结构较复杂,设备价格较昂贵; (2)若蒸发源附近的蒸气密度高,电子束流和
蒸气粒子之间会发生相互作用,电子的能 量将散失和轨道偏移;同时引起蒸气和残 余气体的激发和电离,会影响膜层质量。
图3-2 直流二极溅射装置原理图
3.2.2 直流三极或四极溅射
1)直流三极溅射
三极溅射中的三极是指阴极、阳极和靶极。 直流三极溅射是在二极溅射装置中引入热灯丝 阴极和与之相对的阳极,灯丝阴极连接机壳接 地(规定电位为零),阳极为50 ~100V。
- 1、下载文档前请自行甄别文档内容的完整性,平台不提供额外的编辑、内容补充、找答案等附加服务。
- 2、"仅部分预览"的文档,不可在线预览部分如存在完整性等问题,可反馈申请退款(可完整预览的文档不适用该条件!)。
- 3、如文档侵犯您的权益,请联系客服反馈,我们会尽快为您处理(人工客服工作时间:9:00-18:30)。
真空镀膜技术磁控溅射膜即物理气相沉积(PVD)金属镀膜不一定用磁控溅射,可以根据成本&工艺需求选择合理的沉积方法,具体有:物理气相沉积(PVD)技术第一节概述物理气相沉积技术早在20世纪初已有些应用,但在最近30年迅速发展,成为一门极具广阔应用前景的新技术。
,并向着环保型、清洁型趋势发展。
20世纪90年代初至今,在钟表行业,尤其是高档手表金属外观件的表面处理方面达到越来越为广泛的应用。
物理气相沉积(Physical Vapor Deposition,PVD)技术表示在真空条件下,采用物理方法,将材料源——固体或液体表面气化成气态原子、分子或部分电离成离子,并通过低压气体(或等离子体)过程,在基体表面沉积具有某种特殊功能的薄膜的技术。
物理气相沉积的主要方法有,真空蒸镀、溅射镀膜、电弧等离子体镀、离子镀膜,及分子束外延等。
发展到目前,物理气相沉积技术不仅可沉积金属膜、合金膜、还可以沉积化合物、陶瓷、半导体、聚合物膜等。
真空蒸镀基本原理是在真空条件下,使金属、金属合金或化合物蒸发,然后沉积在基体表面上,蒸发的方法常用电阻加热,高频感应加热,电子柬、激光束、离子束高能轰击镀料,使蒸发成气相,然后沉积在基体表面,历史上,真空蒸镀是PVD法中使用最早的技术。
溅射镀膜基本原理是充氩(Ar)气的真空条件下,使氩气进行辉光放电,这时氩(Ar)原子电离成氩离子(Ar+),氩离子在电场力的作用下,加速轰击以镀料制作的阴极靶材,靶材会被溅射出来而沉积到工件表面。
如果采用直流辉光放电,称直流(Qc)溅射,射频(RF)辉光放电引起的称射频溅射。
磁控(M)辉光放电引起的称磁控溅射。
电弧等离子体镀膜基本原理是在真空条件下,用引弧针引弧,使真空金壁(阳极)和镀材(阴极)之间进行弧光放电,阴极表面快速移动着多个阴极弧斑,不断迅速蒸发甚至“异华”镀料,使之电离成以镀料为主要成分的电弧等离子体,并能迅速将镀料沉积于基体。
因为有多弧斑,所以也称多弧蒸发离化过程。
离子镀基本原理是在真空条件下,采用某种等离子体电离技术,使镀料原子部分电离成离子,同时产生许多高能量的中性原子,在被镀基体上加负偏压。
这样在深度负偏压的作用下,离子沉积于基体表面形成薄膜。
物理气相沉积技术基本原理可分三个工艺步骤:(1)镀料的气化:即使镀料蒸发,异华或被溅射,也就是通过镀料的气化源。
(2)镀料原子、分子或离子的迁移:由气化源供出原子、分子或离子经过碰撞后,产生多种反应。
(3)镀料原子、分子或离子在基体上沉积。
物理气相沉积技术工艺过程简单,对环境改善,无污染,耗材少,成膜均匀致密,与基体的结合力强。
该技术广泛应用于航空航天、电子、光学、机械、建筑、轻工、冶金、材料等领域,可制备具有耐磨、耐腐饰、装饰、导电、绝缘、光导、压电、磁性、润滑、超导等特性的膜层。
随着高科技及新兴工业发展,物理气相沉积技术出现了不少新的先进的亮点,如多弧离子镀与磁控溅射兼容技术,大型矩形长弧靶和溅射靶,非平衡磁控溅射靶,孪生靶技术,带状泡沫多弧沉积卷绕镀层技术,条状纤维织物卷绕镀层技术等,使用的镀层成套设备,向计算机全自动,大型化工业规模方向发展。
第二节真空蒸镀(一)真空蒸镀原理(1) 真空蒸镀是在真空条件下,将镀料加热并蒸发,使大量的原子、分子气化并离开液体镀料或离开固体镀料表面(升华)。
(2)气态的原子、分子在真空中经过很少的碰撞迁移到基体。
(3)镀料原子、分子沉积在基体表面形成薄膜。
(二)蒸发源将镀料加热到蒸发温度并使之气化,这种加热装置称为蒸发源。
最常用的蒸发源是电阻蒸发源和电子束蒸发源,特殊用途的蒸发源有高频感应加热、电弧加热、辐射加热、激光加热蒸发源等。
(三)真空蒸镀工艺实例以塑料金属化为例,真空蒸镀工艺包括:镀前处理、镀膜及后处理。
真空蒸镀的基本工艺过程如下:(1)镀前处理,包括清洗镀件和预处理。
具体清洗方法有清洗剂清洗、化学溶剂清洗、超声波清洗和离子轰击清洗等。
具体预处理有除静电,涂底漆等。
(2)装炉,包括真空室清理及镀件挂具的清洗,蒸发源安装、调试、镀件褂卡。
(3)抽真空,一般先粗抽至6.6Pa以上,更早打开扩散泵的前级维持真空泵,加热扩散泵,待预热足够后,打开高阀,用扩散泵抽至6×10-3Pa半底真空度。
(4)烘烤,将镀件烘烤加热到所需温度。
(5)离子轰击,真空度一般在10Pa~10-1Pa,离子轰击电压200V~1kV负高压,离击时间为5min~30min,(6)预熔,调整电流使镀料预熔,调整电流使镀料预熔,除气1min~2min。
(7)蒸发沉积,根据要求调整蒸发电流,直到所需沉积时间结束。
(8)冷却,镀件在真空室内冷却到一定温度。
(9)出炉,.取件后,关闭真空室,抽真空至l × l0-1Pa,扩散泵冷却到允许温度,才可关闭维持泵和冷却水。
(10)后处理,涂面漆。
第三节溅射镀膜溅射镀膜是指在真空条件下,利用获得功能的粒子轰击靶材料表面,使靶材表面原子获得足够的能量而逃逸的过程称为溅射。
被溅射的靶材沉积到基材表面,就称作溅射镀膜。
溅射镀膜中的入射离子,一般采用辉光放电获得,在l0-2Pa~10Pa范围,所以溅射出来的粒子在飞向基体过程中,易和真空室中的气体分子发生碰撞,使运动方向随机,沉积的膜易于均匀。
近年发展起来的规模性磁控溅射镀膜,沉积速率较高,工艺重复性好,便于自动化,已适当于进行大型建筑装饰镀膜,及工业材料的功能性镀膜,及TGN-JR型用多弧或磁控溅射在卷材的泡沫塑料及纤维织物表面镀镍Ni及银Ag。
第四节电弧蒸发和电弧等离子体镀膜这里指的是PVD领域通常采用的冷阴极电弧蒸发,以固体镀料作为阴极,采用水冷、使冷阴极表面形成许多亮斑,即阴极弧斑。
弧斑就是电弧在阴极附近的弧根。
在极小空间的电流密度极高,弧斑尺寸极小,估计约为1μm~100μm,电流密度高达l05A /cm2~107A/cm2。
每个弧斑存在极短时间,爆发性地蒸发离化阴极改正点处的镀料,蒸发离化后的金属离子,在阴极表面也会产生新的弧斑,许多弧斑不断产生和消失,所以又称多弧蒸发。
最早设计的等离子体加速器型多弧蒸发离化源,是在阴极背后配置磁场,使蒸发后的离子获得霍尔(hall)加速效应,有利于离子增大能量轰击量体,采用这种电弧蒸发离化源镀膜,离化率较高,所以又称为电弧等离子体镀膜。
由于镀料的蒸发离化靠电弧,所以属于区别于第二节,第三节所述的蒸发手段。
第五节离子镀离子镀技术最早在1963年由D.M.Mattox提出,1972年,Bunshah &Juntz推出活性反应蒸发离子镀(AREIP),沉积TiN,TiC等超硬膜,1972年Moley&Smith发展完善了空心热阴极离子镀,l973年又发展出射频离子镀(RFIP)。
20世纪80年代,又发展出磁控溅射离子镀(MSIP)和多弧离子镀(MAIP)。
(一) 离子镀离子镀的基本特点是采用某种方法(如电子束蒸发磁控溅射,或多弧蒸发离化等)使中性粒子电离成离子和电子,在基体上必须施加负偏压,从而使离子对基体产生轰击,适当降低负偏压后,使离子进而沉积于基体成膜。
离子镀的优点如下:①膜层和基体结合力强。
②膜层均匀,致密。
③在负偏压作用下绕镀性好。
④无污染。
⑤多种基体材料均适合于离子镀。
(二)反应性离子镀如果采用电子束蒸发源蒸发,在坩埚上方加20V~100V的正偏压。
在真空室中导人反应性气体。
如N2、02、C2H2、CH4等代替Ar,或混入Ar,电子束中的高能电子(几千至几万电子伏特),不仅使镀料熔化蒸发,而且能在熔化的镀料表面激励出二次电子,这些二次电子在上方正偏压作用下加速,与镀料蒸发中性粒子发生碰撞而电离成离子,在工件表面发生离化反应,从而获得氧化物(如Te02:Si02、Al203、Zn0、Sn02、Cr203、Zr02、In02等)。
其特点是沉积率高,工艺温度低。
(三)多弧离子镀多弧离子镀又称作电弧离子镀,由于在阴极上有多个弧斑持续呈现,故称作“多弧”。
多弧离子镀的主要特点如下:(1)阴极电弧蒸发离化源可从固体阴极直接产生等离子体,而不产生熔池,所以可以任意方位布置,也可采用多个蒸发离化源。
(2)镀料的离化率高,一般达60%~90%,显著提高与基体的结合力改善膜层的性能。
(3)沉积速率高,改善镀膜的效率。
(4)设备结构简单,弧电源工作在低电压大电流工况,工作较为安全。
英文指"phisical vapor deposition" 简称PVD.是镀膜行业常用的术语.PVD(物理气相沉积)镀膜技术主要分为三类,真空蒸发镀膜、真空溅射镀和真空离子镀膜。
对应于PVD技术的三个分类,相应的真空镀膜设备也就有真空蒸发镀膜机、真空溅射镀膜机和真空离子镀膜机这三种。
近十多年来,真空离子镀膜技术的发展是最快的,它已经成为当今最先进的表面处理方式之一。
我们通常所说的PVD镀膜,指的就是真空离子镀膜;通常所说的PVD 镀膜机,指的也就是真空离子镀膜机。
物理气相沉积(PVD)物理气相沉积是通过蒸发,电离或溅射等过程,产生金属粒子并与反应气体反应形成化合物沉积在工件表面。
物理气象沉积方法有真空镀,真空溅射和离子镀三种,目前应用较广的是离子镀。
离子镀是借助于惰性气体辉光放电,使镀料(如金属钛)气化蒸发离子化,离子经电场加速,以较高能量轰击工件表面,此时如通入CO2,N2等反应气体,便可在工件表面获得TiC,TiN覆盖层,硬度高达2000HV。
离子镀的重要特点是沉积温度只有500℃左右,且覆盖层附着力强,适用于高速钢工具,热锻模等。
物理气相沉积(PVD)技术第一节概述物理气相沉积技术早在20世纪初已有些应用,但在最近30年迅速发展,成为一门极具广阔应用前景的新技术。
,并向着环保型、清洁型趋势发展。
20世纪90年代初至今,在钟表行业,尤其是高档手表金属外观件的表面处理方面达到越来越为广泛的应用。
物理气相沉积(Physical Vapor Deposition,PVD)技术表示在真空条件下,采用物理方法,将材料源——固体或液体表面气化成气态原子、分子或部分电离成离子,并通过低压气体(或等离子体)过程,在基体表面沉积具有某种特殊功能的薄膜的技术。
物理气相沉积的主要方法有,真空蒸镀、溅射镀膜、电弧等离子体镀、离子镀膜,及分子束外延等。
发展到目前,物理气相沉积技术不仅可沉积金属膜、合金膜、还可以沉积化合物、陶瓷、半导体、聚合物膜等。
真空蒸镀基本原理是在真空条件下,使金属、金属合金或化合物蒸发,然后沉积在基体表面上,蒸发的方法常用电阻加热,高频感应加热,电子柬、激光束、离子束高能轰击镀料,使蒸发成气相,然后沉积在基体表面,历史上,真空蒸镀是PVD法中使用最早的技术。
溅射镀膜基本原理是充氩(Ar)气的真空条件下,使氩气进行辉光放电,这时氩(Ar)原子电离成氩离子(Ar+),氩离子在电场力的作用下,加速轰击以镀料制作的阴极靶材,靶材会被溅射出来而沉积到工件表面。