橡胶快速硫化技术
橡胶硫化原理

橡胶硫化原理橡胶硫化是指将橡胶原料加入一定量的硫化剂,在一定的温度和时间下,使其产生化学反应,从而使橡胶原料发生交联,形成橡胶制品的过程。
橡胶硫化的目的是提高橡胶原料的物理力学性能、抗老化性能和耐热性能,从而保证橡胶制品的使用寿命和安全性。
硫化剂的种类及作用常见的硫化剂包括硫、硫代硫酸酯、硫化氢、过硫酸盐、亚硝基化合物等。
其中硫化氢为典型的亲核试剂,为硫化反应提供活化的硫端;过硫酸盐为一种自由基引发剂,可以加速硫化反应的进行。
不同的硫化剂具有不同的反应机理和反应速度,且选用的硫化剂与橡胶种类和用途有关。
一般情况下,硫化速度越快、交联密度越高,橡胶制品的物理力学性能越优良。
硫化工艺的参数橡胶硫化的工艺参数包括硫化温度、硫化时间、硫化剂用量、交联密度、交联结构等。
这些参数之间相互影响,必须合理协调,才能得到优良的橡胶制品。
硫化温度是指橡胶制品在硫化过程中所经历的温度。
温度过高会导致硫化过程过快,造成橡胶制品内部交联密度不均、外部硫化层脆化;温度过低则会导致硫化速度缓慢、硫化程度不足、物理力学性能不好。
一般情况下,橡胶硫化的温度范围为120℃-180℃,不同的硫化剂对应不同的合理温度范围。
硫化剂用量是指在一定的温度、时间下,为了达到预定的交联密度所需的硫化剂量。
硫化剂的用量和硫化剂种类、硫化温度、硫化时间、交联密度等参数有关。
硫化剂用量过多会导致硫化密度过高、物理力学性能不足、成本增加;硫化剂用量过少则会导致硫化程度低、交联密度不足、物理力学性能不好。
一般情况下,硫化剂用量为1%-10%左右。
交联密度是指在橡胶硫化过程中,橡胶分子链之间所形成的交联点的数量和密度。
交联密度直接影响橡胶制品的物理力学性能、热化学性能和耐磨性能等。
交联密度越高,橡胶制品的物理力学性能越好,但过高的交联密度可能导致橡胶制品在低温下脆化;交联密度越低,橡胶制品的导电性和热传导性等性能越好,但是物理力学性能不好,容易脱层、开裂等。
橡胶硫化转移膜

橡胶硫化转移膜橡胶硫化转移膜是一种用于研究橡胶硫化反应的技术。
在橡胶制品的生产中,硫化是必不可少的步骤,它可以使橡胶具有良好的弹性和耐热性。
然而,硫化反应是一个复杂的过程,需要对其进行深入的研究。
橡胶硫化转移膜技术可以帮助我们更好地理解这个过程。
一、什么是橡胶硫化转移膜橡胶硫化转移膜是一种实验技术,用于研究橡胶硫化反应中发生的物质转移过程。
在这个过程中,将一层聚四氟乙烯(PTFE)或其他材料涂在未固化的橡胶表面上,并在其上施加压力和温度。
随着时间的推移,未固化的橡胶将通过扭曲、拉伸和压缩等形变方式与PTFE接触,并将其中一些成分转移到PTFE上形成一个“转移膜”。
二、为什么要使用橡胶硫化转移膜使用橡胶硫化转移膜技术可以帮助我们更好地理解橡胶硫化反应中发生的物质转移过程。
这些转移过程包括:1. 橡胶分子与硫化剂之间的反应,形成交联结构。
2. 硫化剂和其他添加剂在橡胶中的扩散和迁移。
3. 不同种类的橡胶分子之间的相互作用,如交联、聚集和分散等。
通过使用橡胶硫化转移膜技术,可以直接观察这些过程,并对它们进行定量分析。
这有助于我们更好地了解橡胶硫化反应的机理,并为优化生产工艺提供指导。
三、如何制备橡胶硫化转移膜制备橡胶硫化转移膜需要以下步骤:1. 准备未固化的橡胶样品。
通常使用未加工或未热压缩的样品。
2. 准备PTFE片。
PTFE片应该足够大,以覆盖整个样品表面,并且要保证表面光滑平整。
3. 将PTFE片放在未固化的橡胶表面上,并施加适当的压力和温度。
压力和温度的选择应该根据橡胶样品的性质和硫化反应的要求进行调整。
4. 在一定时间内,将PTFE片从橡胶表面上取下,并将其放入适当的溶剂中进行分析。
五、如何分析橡胶硫化转移膜对于制备好的橡胶硫化转移膜,可以通过以下方法进行分析:1. 扫描电子显微镜(SEM):SEM可以用来观察转移膜表面的形貌和结构,并提供有关橡胶硫化反应机理的信息。
2. 能谱分析(EDS):EDS可以用来确定转移膜中不同元素的含量和分布情况。
衬胶硫化的工艺
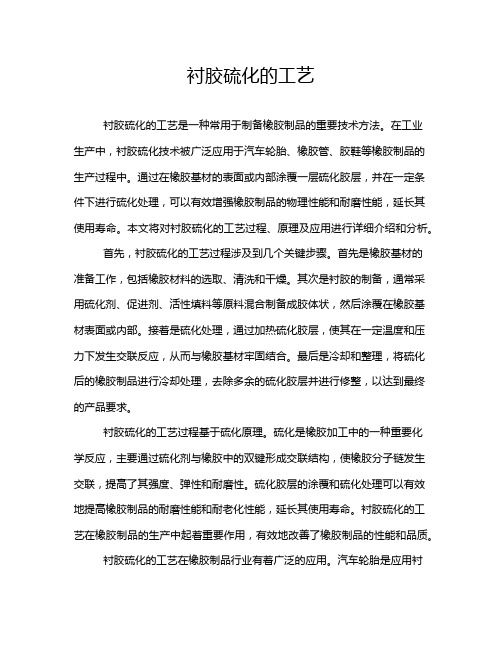
衬胶硫化的工艺衬胶硫化的工艺是一种常用于制备橡胶制品的重要技术方法。
在工业生产中,衬胶硫化技术被广泛应用于汽车轮胎、橡胶管、胶鞋等橡胶制品的生产过程中。
通过在橡胶基材的表面或内部涂覆一层硫化胶层,并在一定条件下进行硫化处理,可以有效增强橡胶制品的物理性能和耐磨性能,延长其使用寿命。
本文将对衬胶硫化的工艺过程、原理及应用进行详细介绍和分析。
首先,衬胶硫化的工艺过程涉及到几个关键步骤。
首先是橡胶基材的准备工作,包括橡胶材料的选取、清洗和干燥。
其次是衬胶的制备,通常采用硫化剂、促进剂、活性填料等原料混合制备成胶体状,然后涂覆在橡胶基材表面或内部。
接着是硫化处理,通过加热硫化胶层,使其在一定温度和压力下发生交联反应,从而与橡胶基材牢固结合。
最后是冷却和整理,将硫化后的橡胶制品进行冷却处理,去除多余的硫化胶层并进行修整,以达到最终的产品要求。
衬胶硫化的工艺过程基于硫化原理。
硫化是橡胶加工中的一种重要化学反应,主要通过硫化剂与橡胶中的双键形成交联结构,使橡胶分子链发生交联,提高了其强度、弹性和耐磨性。
硫化胶层的涂覆和硫化处理可以有效地提高橡胶制品的耐磨性能和耐老化性能,延长其使用寿命。
衬胶硫化的工艺在橡胶制品的生产中起着重要作用,有效地改善了橡胶制品的性能和品质。
衬胶硫化的工艺在橡胶制品行业有着广泛的应用。
汽车轮胎是应用衬胶硫化工艺最广泛的领域之一。
汽车轮胎是汽车的重要零部件,其性能直接影响到汽车的行驶安全和舒适性。
衬胶硫化技术可以有效地提高轮胎的抓地力、耐磨性和耐冲击性,延长了轮胎的使用寿命,提高了汽车的性能和安全性。
此外,在橡胶管、胶鞋等橡胶制品的生产中,衬胶硫化技术也被广泛应用,有效提高了这些制品的性能和品质,满足了不同领域的需求。
总的来说,衬胶硫化的工艺是一种重要的橡胶加工技术,通过涂覆硫化胶层、硫化处理等步骤,可以有效提高橡胶制品的性能和品质。
在橡胶制品的生产中,衬胶硫化技术得到了广泛应用,其中汽车轮胎是最主要的应用领域之一。
橡胶硫化过程的四阶段:起硫、欠硫、正硫和过硫

橡胶硫化过程的四阶段:起硫、欠硫、正硫和过硫胶料在硫化时,其性能随硫化时间变化而变化的曲线,称为硫化曲线。
从硫化时间影响胶料定伸强度的过程来看,可以将整个硫化时间分为四个阶段:硫化起步阶段、欠硫阶段、正硫阶段和过硫阶段。
1)硫化起步阶段(又称焦烧期或硫化诱导期)硫化起步的意思是指硫化时间胶料开始变硬而后不能进行热塑性流动那一点的时间。
硫起步阶段即此点以前的硫化时间。
在这一阶段内,交联尚未开始,胶料在模型内有良好的流动性。
胶料硫化起步的快慢,直接影响胶料的焦烧和操作安全性。
这一阶段的长短取决于所用配合剂,特别是促进剂的种类。
用有超速促进剂的胶料,其焦烧比较短,此时胶料较易发生焦烧,操作安全性差。
在使用迟效性促进剂(如亚磺酰胺)或与少许秋兰姆促进剂并用时,均可取得较长的焦烧期和良好的操作安全性。
但是,不同的硫化方法和制品,对焦烧时间的长短亦有不同要求。
在硫化模压制品时,总是希望有较长的焦烧期,使胶料有充分时间在模型内进行流动,而不致使制品出现花纹不清晰或缺胶等到缺陷。
在非模型硫化中,则应要求硫化起步应尽可能早一些,因为胶料起步快而迅速变硬,有利于防止制品因受热变软而发生变形。
不过在大多数情况下仍希望有较长的焦烧时间以保证操作的。
2)欠硫阶段(又称预硫阶段)硫化起步与正硫化之间的阶段称为欠硫阶段。
在此阶段,由于交联度低,橡胶制品应具备的性能大多还不明显。
尤其是此阶段初期,胶料的交联度很低,其性能变化甚微,制品没有实用意义。
但是到了此阶段的后期,制品轻微欠硫时,尽管制品的抗张强度、弹性、伸长率等尚未达到预想的水平,但其抗撕裂性耐磨性和抗动态裂口性等则优于正硫化胶料。
因此,如果着重要求后几种性能时,制品可以轻微欠硫。
3)正硫阶段大多数情况下,制品在硫化时都必须使之达到适当的交联度,达到适当的我联度的阶段叫做正硫化阶段,即正硫阶段。
在此阶段,硫化胶的各项物理机械性能并非在同一时都达到最高值,而是分别达到或接近最佳值,其综合性能最好。
橡胶怎么快速凝固的原理

橡胶怎么快速凝固的原理一、原料制备
1. 选择好质量的天然橡胶或合成橡胶作为主要原料。
2. 加入硫化剂、促进剂、老化防护剂等配料。
3. 使用开式混炼机充分混炼,使配料均匀分散。
二、加速硫化原理
1. 硫化反应是形成橡胶网络结构的关键过程。
2. 加入硫化促进剂,可以缩短硫化反应时间,提高硫化速率。
3. 常用的硫化促进剂有肽类、硫脲类等有机物。
4. 促进剂可与硫化剂生成活性硫化中间体,加速硫化反应。
三、提高温度
1. 硫化反应属于化学反应,反应速率随温度升高而加快。
2. 通过选择高温硫化工艺,可以大幅缩减硫化用时。
3. 一般采用140-160C进行高温硫化,速度比常温快数倍。
4. 但温度过高会引起橡胶TEXTURE劣化,需控制适宜温度。
四、使用高能辐射
1. 采用电子束或γ射线辐照混炼橡胶,可引发硫化反应。
2. 高能辐射产生的自由基可直接发生硫化反应。
3. 辐射硫化法快速、环保,可精确调控,是新兴的快速硫化技术。
五、注意事项
1. 硫化速率过快会影响产品质量,需要控制适宜。
2. 不同配方及硫化工艺要进行定制优化。
3. 保证硫化均匀一致非常关键,否则会影响制品性能。
4. 快速硫化技术投入使用还需大量数据支撑。
高温快速硫化技术

高温快速硫化技术随着橡胶工业生产的自动化,联动化,高温快速硫化体系被广泛应用。
如注射硫化,电缆的硫化等。
所谓高温硫化是指在180-240度下进行硫化,一般硫化温度每升高10度,硫化时间大约缩短一半。
产量大大提高,但硫化温度升高会使硫化胶物性性能下降。
这和高温硫化时交联密度的下降有关,温度高于160度时,交联密度下降最为明显。
所以硫化温度不是越高越好。
采用多高的硫化温度要综合结合;1,高温硫化体系配合原则;(1),选择耐热胶种,为了减少或消除硫化胶的返原现象,应选则双键含量低的橡胶,各种橡胶的热稳定性不同,极限硫化温度也不同,适用于高温硫化得胶种有,EPDM,IIR,NBR,SBR等。
(2),采用有效或半有效硫化体系,因为CV硫化体系中多硫交联键含量高,在高温下容易产生硫化返原现象。
所以CV 不适于高温快速硫化体系,高温莪快速硫化体系多用于单硫和双硫键含量高的有效EV和伴有效SEV硫化体系。
其硫化胶耐热老化性能好。
一般使用高促低硫和硫载体硫化配合,其中后者采用DTDM最好,胶烧时间和硫化特性范围比较宽,容易满足加工要求,TMTD因为胶烧时间短且诶喷霜严重而受限制。
虽然EV和SEV对高温硫化的效果比CV好但还不够理想。
仍无法彻底解决高温硫化所产生的硫化返原现象和抗屈挠性能差的缺点,应寻找更好的解决方法。
(3),硫化胶的特种配合,为了保持高温下硫化胶的交联密度不变,可以采取增加硫用量,促进剂用量或2者同时增加的方法,但是增加硫的用量会降低硫化效果,并使多硫交联键的含量增加,同时增加硫和促进剂,可使硫化效果不变,可提高硫化效果,这种方法比较好。
在轮胎得到广泛应用。
合成橡胶硫化体系对温度的敏感性比NR低,因此NR和合成橡胶并用显得格外重要,并用后体系即保持了高温硫化时交联密度的稳定性,又保持硫化胶最佳物性,是橡胶制品采用高温硫化、缩短硫化时间,提高生产的有效办法。
2,高温硫化的其它配合特点;高温硫化体系要求硫化速度快,胶烧倾向小,无喷霜现象,所以配合时最好采用耐热胶种,及常量硫磺,高促进剂的方法,另外,对防胶焦,防老系统都有较高得要求。
橡胶硫化工艺技术的对比

橡胶硫化工艺技术的对比橡胶硫化是指将橡胶原料经过一系列的加工工艺,使其在一定的温度和压力下与硫化剂发生化学反应,从而形成交联结构,使橡胶具有良好的弹性和耐用性。
橡胶硫化工艺技术的发展经历了多个阶段,目前主要的硫化工艺技术有热硫化、自发硫化和微波硫化。
热硫化是最早使用的硫化工艺技术,其原理是将橡胶材料和硫化剂混合均匀后,放入硫化机内进行硫化处理。
硫化机会提供一定的温度和压力,使橡胶与硫化剂发生化学反应,形成交联结构。
热硫化的优点是成本低、工艺简单,并且可以用于各种类型的橡胶材料。
但是,热硫化的缺点是硫化时间较长,硫化温度相对较高,容易导致橡胶老化,对环境也有一定的污染。
自发硫化是一种新兴的硫化工艺技术,其原理是利用自发生成的硫化剂来进行硫化。
自发硫化的优点是硫化速度快、硫化温度低,对橡胶材料的老化影响小。
同时,自发硫化还能减少硫化机的能耗和环境污染。
然而,自发硫化的缺点是硫化剂的自发性不稳定,需要进行严密的控制和监测工作。
微波硫化是一种新型的硫化工艺技术,其原理是利用微波加热橡胶材料,使其快速硫化。
微波硫化的优点是硫化速度非常快,能够在数分钟内完成硫化过程;而且微波加热橡胶材料时可以实现内外均匀加热,减少加热不均匀导致的硫化不良问题。
微波硫化还能节约能源和减少环境污染。
不过,微波硫化设备的成本相对较高,操作技术要求更高,需要注意橡胶材料的选择和硫化时间的控制。
综上所述,不同的橡胶硫化工艺技术各有优缺点。
热硫化工艺技术成本低、工艺简单,但是硫化时间长,环境污染较大;自发硫化工艺技术硫化速度快,对橡胶材料老化影响小,但是硫化剂自发性不稳定,需要进行严密的控制;微波硫化工艺技术硫化速度快,能够内外均匀加热橡胶材料,节约能源和减少环境污染,但操作技术要求高和设备成本高。
根据不同的应用场景和要求,可以选择适合的硫化工艺技术。
橡胶硫化促进剂m工艺
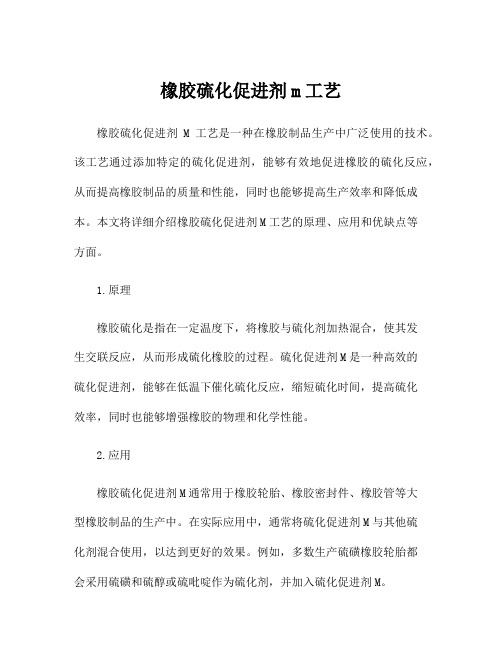
橡胶硫化促进剂m工艺橡胶硫化促进剂M工艺是一种在橡胶制品生产中广泛使用的技术。
该工艺通过添加特定的硫化促进剂,能够有效地促进橡胶的硫化反应,从而提高橡胶制品的质量和性能,同时也能够提高生产效率和降低成本。
本文将详细介绍橡胶硫化促进剂M工艺的原理、应用和优缺点等方面。
1.原理橡胶硫化是指在一定温度下,将橡胶与硫化剂加热混合,使其发生交联反应,从而形成硫化橡胶的过程。
硫化促进剂M是一种高效的硫化促进剂,能够在低温下催化硫化反应,缩短硫化时间,提高硫化效率,同时也能够增强橡胶的物理和化学性能。
2.应用橡胶硫化促进剂M通常用于橡胶轮胎、橡胶密封件、橡胶管等大型橡胶制品的生产中。
在实际应用中,通常将硫化促进剂M与其他硫化剂混合使用,以达到更好的效果。
例如,多数生产硫磺橡胶轮胎都会采用硫磺和硫醇或硫吡啶作为硫化剂,并加入硫化促进剂M。
3.优缺点优点:(1)硫化促进剂M能够缩短硫化时间,提高硫化效率,从而缩短生产周期。
(2)硫化促进剂M能够增强橡胶的物理和化学性能,使橡胶制品具有更好的耐磨、耐老化、耐热等性能,从而提高产品质量和使用寿命。
(3)硫化促进剂M使用方便,容易加工,不会对环境造成污染,符合环保要求。
缺点:(1)硫化促进剂M对一些橡胶品种的硫化效果并不理想,可能会出现硫化不良、硫化不完全等情况。
(2)硫化促进剂M价格较高,成本相对较高,对企业的经济效益有一定的影响。
4.注意事项在使用橡胶硫化促进剂M的过程中,需要注意以下一些事项:(1)硫化促进剂M应按照生产工艺要求控制加入量,过量使用或不当使用会造成反效果。
(2)硫化促进剂M与硫化剂、填料等混合物的过程中应注意搅拌均匀,以避免硫化不均、硫化不完全等现象。
(3)硫化促进剂M在存储和使用过程中应避免受潮、受热或受阳光直射,以保持其良好的性能。
总之,橡胶硫化促进剂M工艺在橡胶制品生产中具有重要的应用价值,能够提高橡胶制品的质量和性能,缩短生产周期,同时也存在一定的局限性和注意事项。
- 1、下载文档前请自行甄别文档内容的完整性,平台不提供额外的编辑、内容补充、找答案等附加服务。
- 2、"仅部分预览"的文档,不可在线预览部分如存在完整性等问题,可反馈申请退款(可完整预览的文档不适用该条件!)。
- 3、如文档侵犯您的权益,请联系客服反馈,我们会尽快为您处理(人工客服工作时间:9:00-18:30)。
橡胶快速硫化技术
中国废塑胶网
对橡胶工业而言,硫化时间长成为提高橡胶工业生产率的瓶颈,并限制了橡胶工业应用领域的迅速发展。
随着各种热塑性弹性体技术的不断成熟,使人们不禁怀疑,是否有一天,热塑性弹性体会成为高弹性橡胶的替代品,而使橡胶退出历史的舞台?对于新技术可能带来的变化今天我们不敢枉下断论,但是,从目前的市场来看,橡胶工业不但没有退缩迹象,反而表现出异常顽强的爆发力。
伴随着市场的快速发展,橡胶加工技术不断成熟,尤其是橡胶快速硫化技术的不断成熟正在弥补橡胶以往硫化时间漫长等不足。
橡胶硫化过程中,温度、压力与时间是三个共同作用的因素。
由于橡胶过热会发生焦烧、性能下降等状况,如何实现高温硫化,进而缩短硫化时间成为不同企业研发的重点。
改善硫化体系以加速硫化过程为越来越多厂家所重视。
各助剂企业也积极推出相应的快速硫化促进剂以抢占市场。
本文特别介绍部分厂家开发的新型加速硫化的助剂产品。
新型硫化剂DTDC
上海京海化工有限公司是中国最早、也是现今最大的不溶性硫磺生产企业。
近年来,公司在完成不溶性硫磺新工艺开发和硫化剂DTDM扩产的同时,分析国际硫化技术的现状和发展趋势,积极研发现代硫化技术前沿的产品。
该公司开发的新型硫化剂DTDC不久将进入市场。
新型硫化剂DTDC因在硫化过程中不产生亚硝胺而备受国际关注,被认为是硫化剂DTDM和二硫化或六硫化秋兰姆的最佳替代品。
由于硫化剂DTDM和秋兰姆产品在硫化温度下裂解释放出的仲胺基分子残片(吗基二甲胺基、二乙胺基、二丁胺基、二戊胺基等)可与亚硝基供给体结合,产生致癌性亚硝胺物质,因此硫化剂DTDM和秋兰姆产品的生产和应用受到欧美国家、政府、国际组织及环境法规的限定与警告。
特别是在2003年5月,在欧盟发表的《未来化学品政策战略》白皮书中将硫化剂DTDM和秋兰姆产品列入限期淘汰的有致癌作用的化学品。
上海京海化工有限公司根据近年来国际橡胶同行对硫化剂DTDM的毒性及其对环境影响的研究成果,正在研制硫化剂DTDM的替代品。
目前,对硫化剂DTDC 的开发已进入环境试验阶段,不久将投放市场。
硫化剂DTDC呈白色结晶形,熔点为120~122℃,活性硫质量分数大于0.19。
用其等量替代硫化剂DTDM,无需改变胶料的配方和工艺。
与硫化剂DTDM相同,硫化剂DTDC可以全部或部分替代硫磺组成有效或半有效硫化体系。
由于硫化剂DTDC在一般硫化条件下可以释放出活性硫,与加入的硫磺在橡胶分子间形成单硫键和双硫键,这种橡胶硫化网络结构可赋予硫化胶优良的耐热性、耐压缩性和高定伸应力。
硫化剂DTDC还具有不喷霜、焦烧安全、硫化速度快的特点,是轮胎等大型模型橡胶制品、耐热橡胶制品、卫生橡胶制品及彩色橡胶制品的最佳硫化剂。
Vulcuren新型硫化剂
要将厚重的橡胶制品硫化,并不是一件容易的事。
因为橡胶的传热性较差,为了迅速使橡胶内部的区域完全硫化,通常需要长时间加热才能实现。
也就是说橡胶材料的表面会过度硫化,并可能在产品内部完全硫化前分解。
橡胶在低温下的硫化是一个可行的方法,虽然这个方法比较温和,但费时较久,而且也不经济。
拜耳橡胶事业处经过长期的不断研究,开发出硫化剂Vulcuren以解决高温硫化问题。
提高硫化温度,而不会造成橡胶制品在长时间加热下的分解,因此缩短了制造过程并提高生产力。
在橡胶硫化时,弹性体会由线型结构变为稳定的交联结构,从而形成橡胶优异的高弹性能。
但是这种交联结构的热稳定性并非特别的好,他们会因长期暴露在高温下而分解。
这种逆转反应会使体积较大的橡胶的硫化失败,而使其物理和化学性质劣化。
与此不同的是,在硫化温度下,Vulcuren会形成奇特的架桥键,在实质上有更好的热稳定性,因此以Vulcuren 来取代部分硫磺,明显地减少了逆转反应。
目前制造体积较大的橡胶制品,例如工程车的橡胶实心轮胎或宽大输送带,因使用Vulcuren,可以使橡胶制品的生产比较快速而且更经济。
此外,产品的物性,例如耐磨性、抗张强度和抗撕裂强度等都可维持在很高的标准。
Pckacil TBzTD
化学名为二硫化四基秋兰姆,是尤尼罗伊尔公司新开发的秋兰姆类促进剂,可替代TMTD(四甲基二硫化秋兰姆)、TMTM(一硫化四甲基秋兰姆)、TETD(二硫化四乙基秋兰姆),加工安全性更好,比TMTD有更长的焦烧时间,可作为天然橡胶、丁橡胶和丁苯橡胶的快速硫化主促进剂或助促进剂,有时也用于PVC橡胶硫化抑制剂。
TBzTD分子量大,熔点高,不易分解,故不产生亚硝胺;其硫化速度稍低于TMTD,其他物性与TMTD几乎相同,目前已成为极具发展潜力的秋兰姆类硫化促进剂新品种。
Santocure TBBS
化学名为N-叔丁基-2-苯并唑次磺胺类促进剂,是一种性能很好的次磺胺类促进剂,由孟山都公司开发。
在天然橡胶、丁苯橡胶、丁二烯橡胶和其并用胶种中使用时,具有硫化速度快和模量高等特点。
一般可单独使用或与少量促进剂一起使用;在轮胎和工业橡胶制品中使用时,需配用氧化锌和硬脂酸,也可用秋兰姆、二硫代氨基甲酸盐、醛胺、胍类促进剂和酸性物质活化。
TBBS以叔丁胺和促进剂M为原料合成,不存在亚硝胺致癌问题,是全球主导的促进剂品种,消费量占全球促进剂消费量的35%以上。
中国也有部分企业进行小规模生产,但由于受原料叔丁胺的制约,未能大规模生产与应用,但其作为环保高效的新型次磺胺类促进剂发展前景很好。
Santocure TBSI
化学名为N-叔丁基双-2-苯并唑次磺胺类促进剂,由孟山都公司开发,在操作温度下非常安全,不产生致癌亚硝胺。
与TBBS相比,TBSI具有分子量大、熔点高30℃以上、热稳定性能好、焦烧时间长、硫化速度快等优点,通常与防焦剂CTP共用,可完全替代TBBS。
另外,TBSI还具有遇水稳定、易于贮存;在硫化天然胶时,可明显提高橡胶的抗硫化返原性;在橡胶与钢丝粘接的化合物中表现良好的性能。
TBSI可用于天然橡胶、丁苯橡胶、顺丁橡胶、异戊橡胶等,尤其适用于硷性较强的炉法炭黑混炼胶料及对抗返原要求很高的厚制品,活性大于目前广泛使用的CBS、NOBS等促进剂。
多功能促进剂TiBTM
化学名为N,N,N’-硫化四异丁基秋兰姆,由美国固持里奇公司开发,为一种既具有次磺胺类促进剂的助促进剂作用,又具有防焦剂作用的多功能促进剂。
在SBR/BR胶料中,TiBTM和CTP分别与TBBS和CBS并用时,两种防焦剂对焦烧延迟作用相同;但TiBTM 还可明显加快硫化速度,而CTP则没有加速硫化的作用,甚至有时会引起硫化速度下降。
试验表明,在SBR/BR之类的合成橡胶体系中,TiBTM可同时发挥防焦剂和助促进剂两种功能。
但在天然橡胶中,TiBTM的防焦效果明显比CTP差,TiBTM主要用作助促进剂;但TiBTM可增加天然橡胶的抗硫化返原性,提高硫化温度、变化硫磺用量及加入白炭黑都不会影响TiBTM防焦烧和加速硫化速度的效果,而且对硫化橡胶的物理性能无不良影响。
不断提高生产效率将是各种技术竞争中不变的主题之一。
在橡胶加工与橡胶助剂的各种技术之中,加速硫化的促进剂技术在推动橡胶工业及其加工技术发展的同时,并将成为各助剂供应商继续研发的重点。