压铸教程基本知识
压铸技术基础
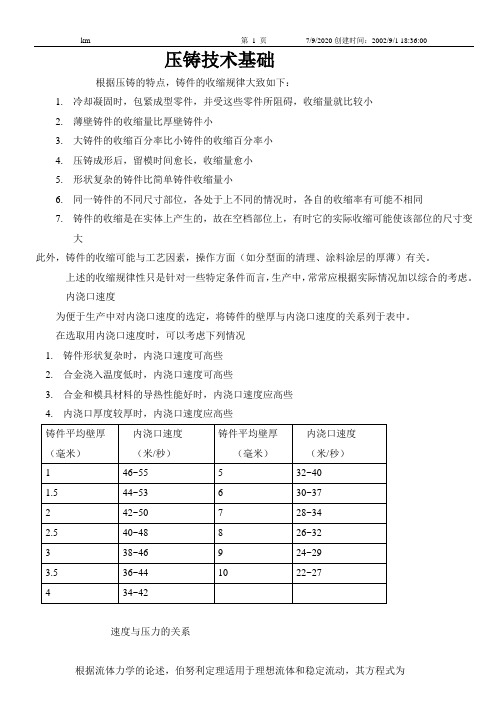
压铸技术基础根据压铸的特点,铸件的收缩规律大致如下:1.冷却凝固时,包紧成型零件,并受这些零件所阻碍,收缩量就比较小2.薄壁铸件的收缩量比厚壁铸件小3.大铸件的收缩百分率比小铸件的收缩百分率小4.压铸成形后,留模时间愈长,收缩量愈小5.形状复杂的铸件比简单铸件收缩量小6.同一铸件的不同尺寸部位,各处于上不同的情况时,各自的收缩率有可能不相同7.铸件的收缩是在实体上产生的,故在空档部位上,有时它的实际收缩可能使该部位的尺寸变大此外,铸件的收缩可能与工艺因素,操作方面(如分型面的清理、涂料涂层的厚薄)有关。
上述的收缩规律性只是针对一些特定条件而言,生产中,常常应根据实际情况加以综合的考虑。
内浇口速度为便于生产中对内浇口速度的选定,将铸件的壁厚与内浇口速度的关系列于表中。
在选取用内浇口速度时,可以考虑下列情况1.铸件形状复杂时,内浇口速度可高些2.合金浇入温度低时,内浇口速度可高些3.合金和模具材料的导热性能好时,内浇口速度应高些4.内浇口厚度较厚时,内浇口速度应高些速度与压力的关系根据流体力学的论述,伯努利定理适用于理想流体和稳定流动,其方程式为p/ρ+gz+1/2q 2=Const它是一维流动问题中最重要的一个关系,而且在整个流体力学的领域里也具有根本的重要性。
它是一个能量守恒的表达式,因为每一项都代表单位质量的能量:第一项是压力所做的功,每二项是由于重力 而引起的势能,而第三项是动能。
于是,按照压铸过程的金属流动来看,压室内熔融金属从冲头速度加速到内浇口的过程,便可根据伯努利方程式列出如下的表示式,即 p n /ρ+gh n +1/2v 2 n =p b /ρ+gh s +1/2v 2c式中p n—内浇口处通过金属流之前的压力(公斤/厘米2) ρ—熔融金属的密度(公斤/厘米3) g —重力加速度(981厘米/秒2) hn —内浇口压力头高度(厘米) v n —内浇口速度(厘米/秒)p b__压室内作用于金属上的压力(公斤/厘米2 ),此处实为填充比压,符号应为pbc ,但为叙述方便,直接用pb 列出hs —压室的压力头高度(厘米) vc —冲头速度(厘米/秒)但是,对于压铸过程来说,对上述表示式可作如下的分析:内浇口处通过金属流之前的压力p n ,在模具上开有足够的排气道的情况下,相当于大气压力,而压室内作用于金属上地压力pb (实为填充比压)则甚大于大气压力,故移项后,pb -p n 的差值与pb 十分接近,所以p n 项可忽略不计。
压铸基本知识
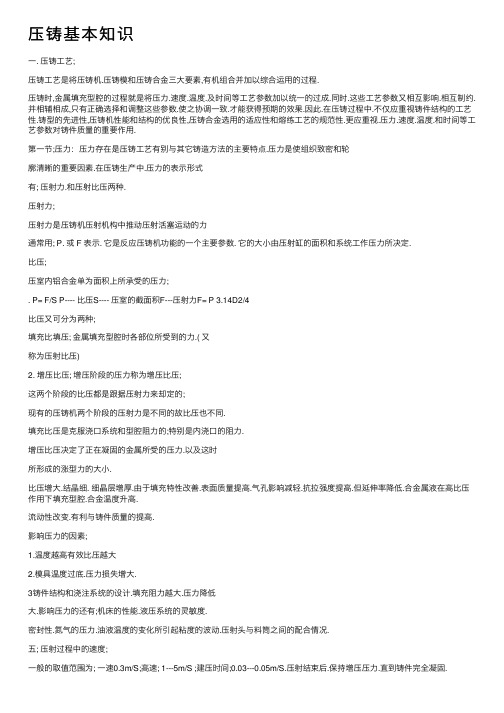
压铸基本知识⼀. 压铸⼯艺;压铸⼯艺是将压铸机.压铸模和压铸合⾦三⼤要素,有机组合并加以综合运⽤的过程.压铸时,⾦属填充型腔的过程就是将压⼒.速度.温度.及时间等⼯艺参数加以统⼀的过成.同时.这些⼯艺参数⼜相互影响.相互制约.并相辅相成,只有正确选择和调整这些参数.使之协调⼀致.才能获得预期的效果.因此.在压铸过程中.不仅应重视铸件结构的⼯艺性.铸型的先进性,压铸机性能和结构的优良性,压铸合⾦选⽤的适应性和熔练⼯艺的规范性.更应重视.压⼒.速度.温度.和时间等⼯艺参数对铸件质量的重要作⽤.第⼀节;压⼒:压⼒存在是压铸⼯艺有别与其它铸造⽅法的主要特点.压⼒是使组织致密和轮廓清晰的重要因素.在压铸⽣产中.压⼒的表⽰形式有; 压射⼒.和压射⽐压两种.压射⼒;压射⼒是压铸机压射机构中推动压射活塞运动的⼒通常⽤; P. 或 F 表⽰. 它是反应压铸机功能的⼀个主要参数. 它的⼤⼩由压射缸的⾯积和系统⼯作压⼒所决定.⽐压;压室内铝合⾦单为⾯积上所承受的压⼒;. P= F/S P---- ⽐压S---- 压室的截⾯积F---压射⼒F= P 3.14D2/4⽐压⼜可分为两种;填充⽐填压; ⾦属填充型腔时各部位所受到的⼒.( ⼜称为压射⽐压)2. 增压⽐压; 增压阶段的压⼒称为增压⽐压;这两个阶段的⽐压都是跟据压射⼒来却定的;现有的压铸机两个阶段的压射⼒是不同的故⽐压也不同.填充⽐压是克服浇⼝系统和型腔阻⼒的;特别是内浇⼝的阻⼒.增压⽐压决定了正在凝固的⾦属所受的压⼒.以及这时所形成的涨型⼒的⼤⼩.⽐压增⼤.结晶细. 细晶层增厚.由于填充特性改善.表⾯质量提⾼.⽓孔影响减轻.抗拉强度提⾼.但延伸率降低.合⾦属液在⾼⽐压作⽤下填充型腔.合⾦温度升⾼.流动性改变.有利与铸件质量的提⾼.影响压⼒的因素;1.温度越⾼有效⽐压越⼤2.模具温度过底.压⼒损失增⼤.3铸件结构和浇注系统的设计.填充阻⼒越⼤.压⼒降低⼤.影响压⼒的还有;机床的性能.液压系统的灵敏度.密封性.氮⽓的压⼒.油液温度的变化所引起粘度的波动.压射头与料筒之间的配合情况.五; 压射过程中的速度;⼀般的取值范围为; ⼀速0.3m/S;⾼速; 1---5m/S ;建压时间;0.03---0.05m/S.压射结束后.保持增压压⼒.直到铸件完全凝固.六; ⽐压的选择铸件⼀般分为两种; 有强度要求和⽆强度要求.⽐压的选择要跟据壁厚来选择;在⼀般情况下.压铸薄臂铸件时.由与型腔中的⾦属液流动阻⼒较⼤.因内浇⼝也薄,所以有较⼤的阻⼒,故要有较⼤的填充⽐压才能保证达到须要的内浇⼝速度.对与厚壁铸件,⼀⽅⾯选定的内浇⼝速度较低,并且⾦属的凝固时间较长,可以采⽤较⼩的填充⽐压;另⼀⽅⾯,为使铸件具有⼀定的致密度,还需要有⾜够的增压⽐压才能满⾜够要求对于形状复杂的铸件,填充⽐压应选择⾼⼀些. 但要考虑合⾦的类别;如合⾦.内浇⼝的速度.压机的合模⼒等因素填充⽐压的⼤⼩,主要是根据所选定的内浇⼝速度计算的.⽽增压⽐压的⼤⼩,主要是根据不同合⾦的类别选⽤不同的数值.当模具排⽓良好且内浇⼝与铸件臂厚设计恰当,可选⼩点,反之就要选⼤点.有⽓密性要求.⾯⼤.壁薄⼀般应为;50---60MPa第⼆节压射速度压射过程中,压射速度既受压⼒的直接影响,⼜与压⼒共同对铸件内部质量,表⾯要求和轮廓清晰程度起着重要作⽤. 速度的表⽰形式常为压射速度和内浇⼝速度,压射速度.压射头推动⾦属向前移动的速度称为压射速度.压射速度⼜分为多级( ⼀般有; 慢速.⼀快.⼆快)慢速; 也叫慢压射速度. 它是指冲头开始运动到封住熔杯⼝的速度⼀快; 也叫⼀级压射速度; 它是指从慢速结束开始到⾦属充满内浇⼝时的速度.⼆快;也叫⼆级压射速度;也叫快压射速度; 它是指从⼀快结束到⾦属全部把型腔填充完全时的速度.⼀快要求压室中的⾦属液充满压室,在既不过多降底合⾦属温度,⼜有利于排除压室中的⽓体的原则下,该阶段的速度应尽量的底,⼀般应底于O.3M/S,⼆快该速度由压铸机的特性决定,现有的国产压铸机⼀般在4-----10m/S,该速度是压铸机的主要参数之⼀,但在保正铸件内外质量的前提下速度越底越好.这样有利于按顺序填充.减少⽓孔的存在.⼆快的作⽤;(1)对铸件⼒学性能的影响;提⾼压射速度.则动能转化为热能,可提⾼合⾦的流动性.有利与消除流痕,冷隔等缺陷.可改变⼒学性能和表⾯质量.但速度过快时.合⾦液呈雾状与⽓体混合,产⽣严重的乱流.⼒学性能下降.铸件局部产⽣针孔.(2); 压射速度对填充特性的影响;提⾼压射速度可改变压射条件.可压铸出质量优良的复杂薄壁铸件.但速度过快时.填充条件恶化,在厚壁铸件中最显著.⼆快速度的选择和该考虑的因素;1; 要考虑熔化潜热,凝固温度范围.2; 模具温度⾼时.压射速度可适当降底;为提⾼模具寿命也可适当限制压射速度.3当铸件壁薄,形状复杂且对表⾯要求⾼时.应采⽤较⾼的压射速度.内浇⼝速度熔融⾦属在冲头作⽤下,经过横浇道到达内浇⼝,然后进⼊型腔,进⼊型腔的快慢.就叫内浇⼝速度.通常采⽤的内浇⼝速度范围是15-----70m/S同发⽣变化,这种变化的熔融⾦属进⼊型腔流动时,由与型腔的型状复杂.厚度不同.模具温度梯度不等因素的影响.流动的速度随时发⽣变化.这个速度称为填充速度.内浇⼝速度的⾼底对铸件⼒学性能的影响极⼤.内浇⼝速度太底.铸件强度就会下降.内浇⼝速度提⾼.强度就会上升.⽽过⾼⼜会导致强度下降.冲头.压射速度.与内浇⼝速度的关系;根据连续性原理;冲头压射速度越⾼.则⾦属流经内浇⼝的速度越快1.速度的选择;在压铸⽣产过程中,速度与压⼒共同对铸件内在质量.表⾯质量和轮廓.清晰度起着重要的作⽤.如果对压铸件的⼒学性能较⾼的要求.则不应选⽤过⼤的内浇⼝速度这样能降底乱流.所造成的涡流.因为涡流中含有空⽓和型腔内的涂料所挥发的⽓体.随着卷⼊涡流内的空⽓和蒸⽓的增多.压铸件内部的⽓孔就会增多.并切⼒学性能明显下降和变坏.如果压铸件是复杂的薄臂件.并切对表⾯质量提出了较⾼的要求.就应该选⽤较⾼的压射速度和内浇⼝速度.这⼀点是⾮常重要的.常⽤的铸件平均壁厚与内浇⼝速度的关系;见下表格;铸件壁厚内浇⼝速度铸件壁厚内浇⼝速度1 46----55 5 32----401.5 44----53 6 30----372 42----50 7 28----342.5 40----48 8 26----323 38----46 9 24----293.5 36----44 10 24----274 34----42以上单为; mm 内浇⼝速度; m/S内浇⼝速度与压射速度和压室直径内浇⼝截⾯积有直关系. 注; 这⼀点⾮常关键.(记住了这⼀点可以解决很多问题)内浇⼝速度可以调整以下三个⽅⾯; ⽣产中想提⾼压射速度1.调整冲头速度;(即;提⾼压射速度.开⼤节流伐)2.改变压室直径;(即;更换熔杯.⼤换⼩)3.改变内浇⼝截⾯积;(既;修模)压⼒; 速度;的分析;⼀快过慢铝液热损失过⼤.对填充不利.过快铝液不稳定易产⽣卷⽓.出现⽓孔.⼆快起点过早.会将料筒⾥的⽓体和浇道⾥的⽓体卷⼊型腔对质量严重不利.当⼆快过早迟.合⾦液会进⼊型腔.在快速来后铝液前沿与后来铝液不能完全融合.型成冷隔.或者流痕.增压起点对压铸件质量的影响;1.增压缸提前动作(也就是增压来的过早)待型腔填充完毕.增压缸活塞动作也终⽌,故⽆法⾏成增压后的⾼⽐压.铸件在较底压⼒下结晶成型.严重影响质量.(铸件内会出现缩孔)2.增压来的过迟(晚)铸件已凝固.增压虽建⽴.但已⽆效.不能起到作⽤.3.正确的增压转换点.应选在型腔基本填补满前.⽴既增压.才能获得预期的效果.4.压射头磨损受阻.压射不畅对⼯艺参数影响很⼤.对4的分析如下;4.1 压射冲头被咬伤卡住.会严重影响压⼒的传递和压射速度的稳定以及铸件质量和⽣产的正常进⾏.原因很多;主要原因是由与温度的影响波动.使压射头与压室的间隙也处与不断变化的状态. 这种间隙变化.在⼤直径的压室中最明显.故压射室直径越⼤.冲头受命越短.压射室浇料⼝下⽅.经常处与⾼温合⾦的冲击下.与上⽅形成明显的温度差,在不同膨胀量的作⽤下.产⽣扭曲.轴线同轴度可偏0.2mm,如果冲头配合间隙⼩与0.1mm压射杆⼜是刚性连接的情况.则冲头拉伤磨损情况会更加严重.故为了发挥压射系统的效率.必需合理选择压室和压射头的配合间隙.并解决温度差的影响.温度压铸过程中.温度对填充的热状态.操作的效率起着重要的作⽤.压铸中所指的温度是;1.浇铸温度;2.模具温度.温度的控制是获得优良铸件的重要因素.1;浇铸温度;汤汋⾥的铝合⾦注⼊料筒时的温度.(这时的温度测量不⽅便,⼀般以保温炉取汤⼝的温度表⽰.下⾯谈浇铸温度的作⽤和影响;随着合⾦液温度的升⾼.⼒学性能有所改变.但超过⼀定限度后.性能会恶化;原因;1.⽓体在合⾦中的溶解度随温度的升⾼⽽增⼤.虽然溶解在合⾦中的⽓体量较少.但在压铸过程中难以排出.对铸件质量是有影响的.2.含铁量随合⾦温度升⾼⽽增加.使流动性降低.结晶粗⼤.性能恶化.3.铝合⾦.镁合⾦随温度升⾼氧化加剧.氧化夹杂物使合⾦性能恶化.因此合⾦过热易产⽣缩孔.裂纹.⽓孔和氧化夹杂物.使产品⼒学性能变差.漏⽓.4.合⾦温度过底.会使成份不均匀,流动性差.影响填充.使产品充型不良.合⾦温度对填充流速有直接影响.浇铸温度过⾼.⽽且在⾼速的作⽤下.易产⽣涡流包⽓,对与凝固温度范围较宽的合⾦可采⽤⾼压.底温.底速.这样有利与型成顺序填充.提⾼铸件质量.但易引起粘模和溶蚀.不利与模具热平衡.降低模具寿命.故正确选择合⾦温度⼗分重要.影响浇铸温度的主要因素;1.合⾦的性质. 熔点. 热容量. 凝固范围;对与凝固范围宽的合⾦,可采⽤底温.底速.⾼压.和较厚的内浇⼝.这样.对厚壁铸件质量可以取得良好的效果.2.铸件结构的复杂成度;3.模具温度;4.⽐压和压射速度;因为动能转化为热能.可使合⾦温度升⾼.合⾦浇铸温度的选择通常在保证成型和所要求的表⾯内在质量的前提下.尽可能采⽤底的温度.(浇铸温度⼀般应⾼与合⾦液相合⾦类别锌合⾦铝合⾦镁合⾦浇铸温度410--450 610--700 640--700 线温度20---30度.)内浇⼝速度对合⾦温度的影响;合⾦液⾼速通过内浇⼝时.因摩擦会使温度升⾼(能量守恒原理.动能转变为热能)如; 当内浇⼝速度为40m/S时.铝合⾦液进⼊型腔时的温度将增加8度.⽽内浇⼝速度越⼤.温度就增加的越多.模具温度在压铸过程中.模具需要⼀定的温度.模具的温度是压铸⼯艺中⼜⼀重要的参数.它对提⾼⽣产率和获得优良铸件有着重要的作⽤.1.模具温度的作⽤和影响;在填充过程中.模具对⾦属液流温度.粘度.流动性.填充时间和填充流态等均有较⼤影响.模具温度过底时.表层冷凝后⼜被⾼速液流激破.产⽣表⾯缺陷.⼤的破碎块会被卡在内浇⼝处.严重影响填充速度和填充效果.使表⾯质量和内在质量下降.严重时产品不能成型.这种情况在⽣产中可经常看到.模具温度过⾼时.虽有利与获得光洁的铸件表⾯.但易出现缩裂和凹陷.2 . 模具温度对合⾦液冷却速度.结晶壮态.收缩应⼒有明显的影响.模具温度过底.收缩应⼒增⼤.铸件易产⽣裂紋.3 . 模具温度对模具寿命影响很⼤,强烈的温度变化.形成复杂的应⼒状态.频繁的应⼒交变.是导致模具过早龟裂的主要原因.4 . 模具温度对铸件尺⼨公差等级有⼀定影响.模具温度稳定则铸件收缩率也相应稳定.5 . 影响模具温度的主要因素;5.1. 合⾦浇注温度.浇注量.热容量.和导热性.5.2 浇注系统和溢流槽的设计.⽤以调整平衡状态.5.3 压铸⽐压和压射速度.5.4 模具设计.( 模具体积⼤.则热容量⼤.模具温度波动⼩.模具材料导热性好.则温度分布就越均衡.有利与改善热平衡5.5 模具合理预热提⾼初温.有利与改善热平衡.可⼤⼤的提⾼模具寿命.5.6 ⽣产频率快.模具温度升⾼.只要保持在⼀定范围对产品和模具都是⼗分有利的.5.7 合理的喷涂能起到隔热和散热的作⽤.6 . 模具温度对铸件⼒学性能的影响;模具温度提⾼.改善了填充条件.使⼒学性提⾼.模具温度过⾼.合⾦液冷却速度就会下降.细晶层(激冷层)厚度减薄.晶粒较粗⼤.强度下降.(漏⽓率升⾼)因此.为了获得质量稳定的优质铸件.必需将模具温度严格地控制在最佳的⼯艺范围内.(最好应⽤模温机)以保证模具在恒定范围内⼯作..7. 模具温度的选择和控制;7.1模具温度的选择应根据铸件的形状. 复杂成度.臂厚.臂厚差浇铸温度.合⾦的性质等因素来综合考虑.(铝合⾦⼀般应在220—280度)7.2模具温度冷却装置;为了获得稳定的模具⼯作温度.宜采⽤模具温度控制装制(即;温控装制.模温机)⽬前我司模具温控⼿段落后.只是通⽔冷却.通⽔量也未加控制.迫切需要以载热油为介质.⽤电⼦温度计进⾏控制.将模具温度稳定在⼯艺范围之内.只有这样才能降低质量的波动.提⾼成品率8 . 模具的热平衡;为了保正⽣产的连续进⾏.模具⼯作温度应保持在⼀定的范围内.这就必需使模具处与热平衡状态.模具热平衡指的是.在每⼀个压铸循环中.⾦属液传给模具的热量.等与冷却系统带⾛的和模具⾃然散发的热量第四节-时间压铸机⼯艺上的时间指的是;1.填充时间;2.增压建⽴时间. (建压时间)3.保压时间;4.留模时间;(冷却时间)5.顶出.顶回时间;6.循环时间;7.压射时间;时间是⼀个多元复合的因素.它与压⼒.速度温度.合⾦液的物理性质.铸件的结构有着密切的关系.(还与内浇⼝的截⾯积有关).所以在压铸⼯艺中是⾄关重要的.1. 填充时间;从⾦属进⼊型腔到型腔被完全充满.所需的时间;铸件填充所需的时间长短.与以上所说的压⼒.速度.温度.以及合⾦.铸件结构有着直接原因.可做分析;如压⼒⼩模具温度底.合⾦温度也底.肯定所需填充时间就长.反之.就短.(⼀般薄臂件填充时间要短.如;散热器.反之.就要长.具体多少为好必需根据实际情况⽽定.跟据经验和计算.铸件平均壁厚与填充时间应选在如下;平均壁厚填充时间平均壁厚填充时间1.0 0.01—0.04 5 0.048—0.0721.5 0.014—0.02 6 0.056—0.0842.0 0.018—0.026 7 0.066—0.102.5 0.022—0.032 8 0.076—0.1163.0 0.028—0.040 9 0.088—0.1383.5 0.034—0.05 10 0.1—0.164.0 0.040—0.062. 填充时间的选择;2.1 合⾦浇铸温度⾼时.填充时间可选长些;2.2. 模具温度⾼时.填充时间可选长些;2.3 .铸件厚壁且离浇⼝远时.填充时间可选长些;3; 增压建压时间;即从压射⽐压上升到增压⽐压所需的时间;从压铸⼯艺上说建压时间越短越好.但是.这个时间受压射系统的增压装置和油路设计的限制.性能很好的压铸机.其最短的建压时间也不会少与10m/s从压铸⼯艺上来说.建压时间的长短.取决与模具中合⾦液的凝固时间.凝固时间少长的合⾦.增压建压时间也可少长.但应短与合⾦液的凝固时间.因此.在机器压射系统和增压装置上.建压时间的可调性是⾮常重要的.若建压时间少长这时合⾦已成半固态或固态.压⼒就⽆法传递.失去了增压的作⽤.(铸件产⽣缩松.漏⽓)4; 保压时间;定义; 即从型腔填满到在增压⽐压作⽤下凝固的这段时间.称为保压时间.保压时间的作⽤;---冲头将压⼒通过还未凝固的料饼.传递到型腔.使正在凝固的⾦属在压⼒作⽤下结晶.从⽽获得致密的铸件.(保压不正常漏⽓⽐例会上升).⼀般来说有以下归率;1.合⾦结晶范围⼤.保压时间应选的长些;2.铸件平均厚度⼤.保压时间应的长些;3.内浇⼝厚.保压时间应选的长些;5 留模时间;定义; 从保压结束到开模顶出铸件的这段时间;⾜够的留.模时间.能够保正铸件在模具内凝固.冷却.使铸件建⽴⾜够的强度.在开模和顶出时.不致产⽣变形和拉裂.留模时间的选择.通常以开模和顶出不变型.不开裂的最短时间为宜.然⽽.过长也不好.降低了⽣产效率.降低了模温.不易脱模.由与合⾦有热脆性和收缩性.⽽引起产⽣裂纹.综上所述.压铸⽣产中的压⼒.速度.温度.时间等⼯艺参数可按下列原则进⾏调整;1.铸件壁越厚.结构越复杂.则压射⼒应越⼤;2.铸件壁越薄.结构越复杂.压射速成应越快;3.铸件壁越厚.留模时间应越长;4.铸件壁越薄.结构越复杂.浇铸温度应越⾼.冲满度的含义;浇⼊料筒⾥的⾦属占料筒总容量的成度.叫压室(或料筒)的充满度;充满度对与卧式冷室压铸机有着特殊的意义.因为.卧式压铸机的料筒在浇⼊合⾦后.并不是完全充满.⽽是在⾦属液⾯上⽅留有⼀定的空间.这个空间所占空间越⼤.存有空⽓就多.压⼊模具中的⽓体就越多.产品中的⽓体含量就多(产品中的⽓孔就越多)⽽充满度太⼩也不好.因为.合⾦在料筒⾥的温度下降的太快.激冷层厚.对填充⼗分不利.⼀般应在40—80%.最好是在65—75%之间.第六节压铸涂料压铸涂料包括;1. 料筒与冲头的配合部位;2.型腔表⾯;3.浇道表⾯;4.活动部位的配合部位; 以上所说的四个⽅⾯都要根据要求喷上或刷上不同润滑材料.这种不同的润滑材料通称为压铸涂料.涂料的正确选择和合理使⽤是⼀个⾮常重要的环节.它对模具寿命.铸件质量.⽣产效率.以及后道⼯续的表⾯处理有着重⼤的影响.涂料必须起到的作⽤;(应具备的特性)1.⾼温下具有良好的润滑作⽤;且发⽓量⼩.闪点⾼.2.具有良好的成膜性.(减⼩铸件与模具之间的摩擦使出模顺利)3. 保温性; 减少瞬间的热扩散.提⾼充型性具体的还可以这样解释;1.挥发点底.在100—150度时.能很快的挥发.不增加或少增加型腔中的⽓体.2.覆盖性好.与⾼温下结成薄膜层.但不易产⽣堆积.3.⽆味.不晰出或分解有害⽓体.4.性能稳定.在规定的保存期内不沉淀.不分解.5.对环境汚染⼩.涂料的使⽤;1.均匀;不要太厚.也不要漏涂.2.涂料的浓度尽可能的⼩;3.涂完后⼀定⽤⽓吹匀;涂料挥发后⽅可合模,压射.不然型腔中有⼤量的⽓体.使铸件产⽣⽓孔.甚⾄这些⽓体产⽣⾼的反压⼒.使铸件成型困难.4.⽣产中应特别注意模具排⽓道的清理.避免涂料聚集堵塞排⽓道.5.对与转弯内凹部位应避免涂料沉积.碳化.(喷完后多吹⽓)。
压铸基础知识
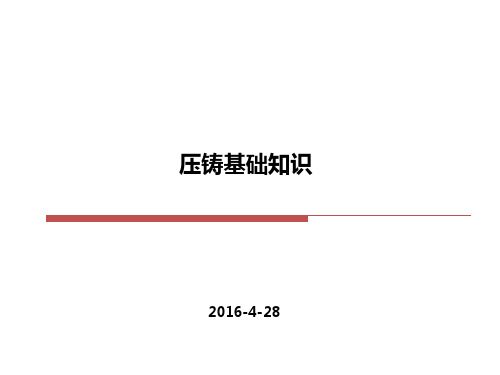
二、压铸的三要素——压铸模
压铸模的结构
成型系统: 就是由优质钢材围成的可以形成零件的空腔。 浇注系统:
就是将合金液引入成型系统,
并排除气体和杂质的通道。 模架系统:
由结构钢组成的用以支撑、定位、导向的结构。
抽芯系统: 解决铸件垂直于开模方向的凹槽和孔洞 成型后出模的 机构。 顶出系统: 就是方便将成型后的铸件从模具内拿下来,并使 顶杆复位。模温系统:保证模具的工作温度。
51
四、压铸机维护与保养 电器部分维护与保养 • (三)外部线路的保养 • 1、每开检查机器外部电器线路,要求完好无损,并且绑 扎牢固。如果电源线护套损坏,应及时装上护套。 • 2、日常的修理过程中,严禁乱搭线路,走线要规范,线 型要符合使用要求,线号要与主电箱引出线号一致,不得 随意更改或丢失。
43
四、压铸机维护与保养 液压系统维护与保养 • 4、每年检修一次液压油泵,检查配流盘,吸、压油工作 腔等相关零件的磨损情况,磨损严重时内泄大,压力损失 大,此时应予以修理或更换。 • 5、每年检查一次换向阀、溢流阀、减压阀、泄荷阀、单 向阀等阀芯是否磨损,是否存在内泄现象。检查溢流阀, 减压阀阻尼孔是否堵塞,对压力的控制是否灵敏、准确。 • 6、每半年检查一次各连接油管接头,油阀的安装螺丝等 是否有松动现象,如有松动要及时紧固,以防泄漏或液压 系统进入空气。
压铸模的结构 模架系统:由结构钢组成的用以支撑、定位、导向的结构;包括动静模 座板、动静模框、支撑板、支撑块、推板、顶杆固定板、复位杆、导柱、 导套、螺栓等。
23
二、压铸的三要素——压铸模
压铸模的结构 抽芯系统:解决铸件垂直于开模方向的凹槽和孔洞成型后出模的机 构;主要包括滑块、导条、锁紧块、限位块、斜导柱(油缸)、螺钉弹 簧等。
压铸工艺基本知识
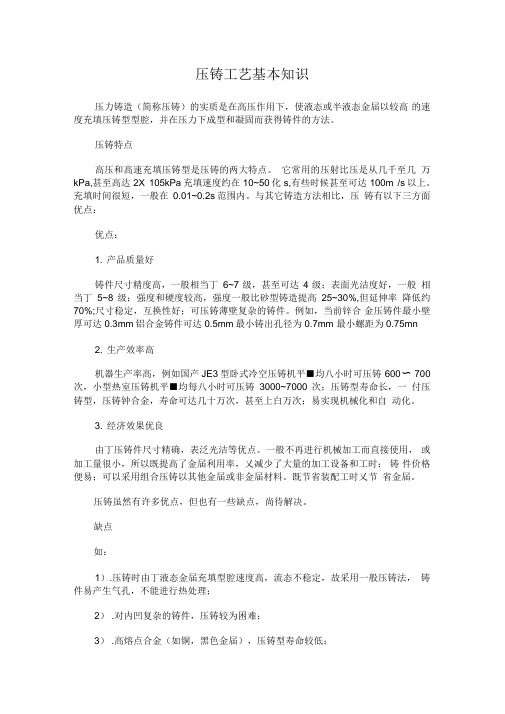
压铸工艺基本知识压力铸造(简称压铸)的实质是在高压作用下,使液态或半液态金届以较高的速度充填压铸型型腔,并在压力下成型和凝固而获得铸件的方法。
压铸特点高压和高速充填压铸型是压铸的两大特点。
它常用的压射比压是从几千至几万kPa,甚至高达2X 105kPa充填速度约在10~50化s,有些时候甚至可达100m /s以上。
充填时间很短,一般在0.01~0.2s范围内。
与其它铸造方法相比,压铸有以下三方面优点:优点:1. 产品质量好铸件尺寸精度高,一般相当丁6~7级,甚至可达4级;表面光洁度好,一般相当丁5~8级;强度和硬度较高,强度一般比砂型铸造提高25~30%,但延伸率降低约70%;尺寸稳定,互换性好;可压铸薄壁复杂的铸件。
例如,当前锌合金压铸件最小壁厚可达0.3mm铝合金铸件可达0.5mm最小铸出孔径为0.7mm 最小螺距为0.75mn2. 生产效率高机器生产率高,例如国产JE3型卧式冷空压铸机平■均八小时可压铸600〜 700次,小型热室压铸机平■均每八小时可压铸3000~7000次;压铸型寿命长,一付压铸型,压铸钟合金,寿命可达几十万次,甚至上白万次;易实现机械化和自动化。
3. 经济效果优良由丁压铸件尺寸精确,表泛光洁等优点。
一般不再进行机械加工而直接使用,或加工量很小,所以既提高了金届利用率,乂减少了大量的加工设备和工时;铸件价格便易;可以采用组合压铸以其他金届或非金届材料。
既节省装配工时乂节省金届。
压铸虽然有许多优点,但也有一些缺点,尚待解决。
缺点如:1).压铸时由丁液态金届充填型腔速度高,流态不稳定,故采用一般压铸法,铸件易产生气孔,不能进行热处理;2) .对内凹复杂的铸件,压铸较为困难;3) .高熔点合金(如铜,黑色金届),压铸型寿命较低;4) .不宜小批量生产,其主要原因是压铸型制造成本高,压铸机生产效率高, 小批量生产不经济。
压铸应用范围及发展趋势压铸是最先进的金届成型方法之一,是实现少切屑,无切屑的有效途径,应用很广,发展很快。
压铸教程
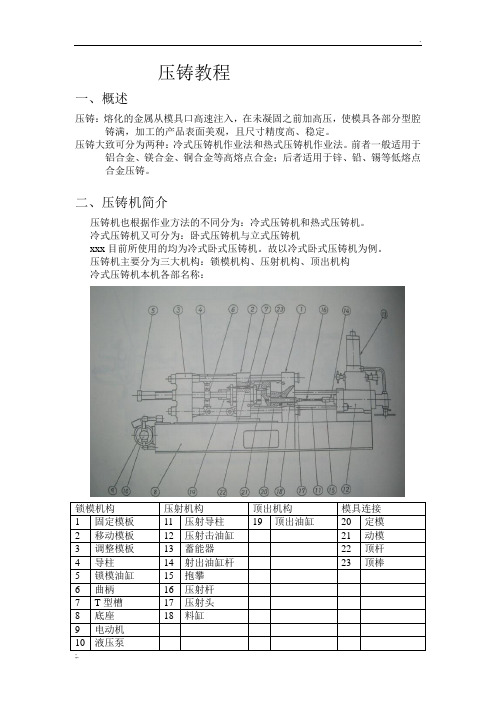
压铸教程一、概述压铸:熔化的金属从模具口高速注入,在未凝固之前加高压,使模具各部分型腔铸满,加工的产品表面美观,且尺寸精度高、稳定。
压铸大致可分为两种:冷式压铸机作业法和热式压铸机作业法。
前者一般适用于铝合金、镁合金、铜合金等高熔点合金;后者适用于锌、铅、锡等低熔点合金压铸。
二、压铸机简介压铸机也根据作业方法的不同分为:冷式压铸机和热式压铸机。
冷式压铸机又可分为:卧式压铸机与立式压铸机xxx目前所使用的均为冷式卧式压铸机。
故以冷式卧式压铸机为例。
压铸机主要分为三大机构:锁模机构、压射机构、顶出机构冷式压铸机本机各部名称:锁模机构压射机构顶出机构模具连接1 固定模板11 压射导柱19 顶出油缸20 定模2 移动模板12 压射击油缸21 动模3 调整模板13 蓄能器22 顶杆4 导柱14 射出油缸杆23 顶棒5 锁模油缸15 抱攀6 曲柄16 压射杆7 T型槽17 压射头8 底座18 料缸9 电动机10 液压泵下面是冷式压铸机各装置的典型布局主要有压铸机本机、给汤机、喷涂机、取出机等组成。
三、压铸安全操作注意事项1、开机作业前,必须确认“安全门”、“非常停止按钮”、“操作电源开关”、的功能是否正常。
2、必须确认开合模、与取出机、喷雾机之间的安全互锁关系是否正常。
3、严禁两人或更多的人同时操作按钮。
当有帮手时(换模),必须在相互确认,高声呼喊,方可下一步动作。
4、压铸作业时,模具分型面前方严禁站人。
下面是铸造作业时发生灾害事故的分析:(数据来源日本)a 模具分型面最容易飞散铝液引起烫伤事故。
43%b 开模时候的料饼裂碎会引起烫伤事故。
7%c 被顶出板夹住引起事故。
6%d 被曲柄夹住引起事故。
2%e 其他的灾害事故42%5、取出机活动范围内严禁站人。
6、清理或修理模具时,必须关闭“操作电源开关”或按下“非常停止”按钮。
7、给汤机勺子作业前要预热、涂钛白粉、烘干,以免造成爆炸。
熔解炉中严禁注水。
严禁站人铸造运行中不要靠近模具的分型面8、压铸机、模具修理时,如有身体一部分要进入动作结构时,必须切断电源开关,以免机械误动造成人身伤害。
压铸培训教程.pptx

r最大= h
R=r+h
压
铸
當h1=h時﹕
模
r≧ h+h1
设
3
计
R=r+ h+h1
2
2020/8/16
K值
鋅﹕1/4 鋁﹕1/2
Macherchen
10
四.成型工艺
(五)孔
鋅:0.8~1.5(最小直径)
鋁:2.0~2.5(最小直径)
(六)文字:凸凹纹﹐直纹
压
铸 例:平行纹(直纹)高0.7MM﹐间距1MM﹐角度60.5。
压 铸 模 设 计
2020/8/16
由喷射﹑喷射流转变为压力流
Macherchen
5
三.压铸制程溶汤的流动方式
(二)压力流
因冲撞,磨擦和气体阻力等(抽象),运动能量耗尽(常发生在加强筋,
凸台,远离浇口之部位),具有接受后继金属液中供给的压力能,从而使金
属液沿着型腔内壁前进的特性.利用这特性,可便以型腔排气.在压力流充
13
五.压铸合金及其性能
压 铸 模 设 计
2020/8/16
鋅合金種類
合 商業習用編號
No.3
金
ASTM
AG40A
代
UNS
Z33251
號
SAE
903
Die Cast Aged
抗拉強度(Kg/mm2) 28.8 24.6
機 降伏強度(Kg/mm2) --
--
伸長率(%)
10
16
械 剪切強率(Kg/mm2) 21.8
铸
模 均匀﹐保证足够强度与刚度的前提)
设
计
2020/8/16
Macherchen
压铸知识培训完整版doc
压铸知识培训完整版doc标题:压铸知识培训完整版一、引言压铸作为一种重要的金属成型工艺,被广泛应用于汽车、摩托车、家电、通讯、航空航天等行业。
为了提高员工的专业技能和综合素质,使企业更好地适应市场需求,我们特举办本次压铸知识培训。
本文档将详细阐述压铸工艺的基本原理、设备、模具、原材料、工艺参数以及常见问题及解决方法等内容,旨在帮助员工全面了解压铸知识,提高实际操作能力。
二、压铸工艺基本原理1. 压铸定义:压铸是一种利用高压将熔融金属迅速注入模具型腔,并在压力作用下凝固成型的金属成型方法。
3. 压铸特点:压铸具有生产效率高、成型精度高、力学性能好、表面质量好、材料利用率高等优点。
三、压铸设备1. 压铸机:压铸机是压铸生产中的关键设备,主要由合模机构、注射机构、液压系统、电气控制系统等组成。
2. 辅助设备:辅助设备包括熔化炉、保温炉、输送系统、模具冷却系统、喷涂料装置等。
四、压铸模具1. 模具结构:压铸模具主要由动模、定模、型腔、浇注系统、冷却系统、顶出系统等组成。
2. 模具材料:模具材料应具备良好的导热性、耐磨性、抗热疲劳性、抗腐蚀性等性能。
3. 模具设计要点:模具设计应考虑产品结构、分型面、浇注系统、冷却系统、顶出系统等因素。
五、压铸原材料1. 常用压铸材料:压铸材料主要包括铝合金、锌合金、镁合金、铜合金等。
2. 材料选择原则:根据产品性能要求、生产成本、工艺特点等因素选择合适的压铸材料。
六、压铸工艺参数1. 压力:压力是压铸过程中的关键参数,包括合模力、注射力、保压力等。
2. 温度:温度控制对压铸产品质量具有重要影响,包括熔融金属温度、模具温度等。
3. 时间:时间参数包括填充时间、保压时间、冷却时间等。
七、压铸常见问题及解决方法1. 缩孔:增加浇注系统截面积、提高模具温度、降低注射速度等方法。
2. 气孔:优化模具设计、提高熔融金属温度、增加注射压力等方法。
3. 疲劳裂纹:选用高强度模具材料、提高模具表面质量、控制模具温度等方法。
压铸生产培训教程
压铸生产培训教程一、引言压铸是一种将熔融金属在高压下注入模具型腔,并在压力作用下快速凝固成型的精密铸造方法。
作为一种先进的金属成型技术,压铸具有高效、精密、复杂等特点,广泛应用于汽车、摩托车、电子、通讯、家电等行业。
本教程旨在为从事压铸生产的技术人员提供系统的培训,使其掌握压铸工艺的基本原理、设备操作、模具设计、质量控制等方面的知识,提高生产技能和产品质量。
二、压铸工艺基本原理1. 压铸过程(1)熔化金属:将金属原料熔化成液态金属,并通过过滤去除杂质。
(2)注入模具:将液态金属在高压下注入模具型腔。
(3)冷却凝固:金属在模具型腔内快速冷却凝固,形成铸件。
(4)开模取出铸件:待铸件完全凝固后,打开模具,取出铸件。
(5)后处理:对铸件进行去毛刺、抛光、热处理等后处理工序。
2. 压铸设备压铸设备主要包括压铸机、熔化炉、模具、冷却系统等。
压铸机是压铸生产的核心设备,根据压铸力大小可分为热室压铸机和冷室压铸机。
3. 压铸模具(1)模具结构:包括型腔、浇注系统、排溢系统、冷却系统等。
(2)模具材料:要求具有良好的导热性、耐磨性和抗热疲劳性能。
(3)模具加工:采用高精度加工设备,确保模具尺寸精度和表面质量。
三、压铸生产操作1. 开机准备(1)检查设备:确保设备正常运行,无异常声响和漏油现象。
(2)检查模具:确认模具完好无损,安装到位。
(3)检查熔化炉:确保熔化炉内金属熔化均匀,温度适中。
2. 压铸操作(1)合模:将模具合拢,确保模具闭合严密。
(2)注射:启动压铸机,将熔融金属注入模具型腔。
(3)保压:在金属凝固过程中保持一定的压力,以防止缩孔、气孔等缺陷。
(4)开模:待铸件完全凝固后,打开模具,取出铸件。
3. 安全注意事项(1)遵守设备操作规程,严禁违章操作。
(2)穿戴好劳动保护用品,防止烫伤、割伤等事故。
(3)保持现场整洁,及时清理废料和油污。
四、压铸质量控制1. 铸件质量检验(1)尺寸精度:通过测量工具检验铸件尺寸是否符合要求。
压铸基础必学知识点
压铸基础必学知识点1. 压铸工艺:压铸是指将加热至熔融状态的金属或合金注入到压铸模具中,在一定压力下冷却固化,从而得到所需的铸件的加工方法。
压铸要素包括铸型、压铸机、模具、压铸合金和工艺参数等。
2. 压铸机:压铸机是用于压铸工艺的专用设备,主要由两个机构组成:锁模机构和压铸机构。
锁模机构用于固定模具,压铸机构用于施加压力和注入金属。
3. 模具:模具是用于压铸过程中形成铸件形状的工具。
模具一般由模座、模芯、顶针等组成。
模具的材料一般选用高硬度、高耐磨的材料,如合金钢等。
4. 压铸合金:压铸合金是指用于压铸工艺的金属或合金材料。
常用的压铸合金有铝合金、镁合金、锌合金等。
这些合金具有良好的流动性和凝固性,适用于压铸工艺。
5. 工艺参数:在压铸过程中,需要调节的一些参数,如压力、温度、注射速度等。
这些参数的选择和调整对于得到满足要求的铸件非常关键。
6. 凝固收缩:在压铸过程中,金属或合金在冷却固化过程中会发生收缩现象。
收缩率的大小对最终铸件的尺寸和形状有很大影响,需要在设计模具时考虑。
7. 缺陷与质量控制:在压铸过程中可能会出现一些缺陷,如气孔、夹杂、缩孔等。
对于这些缺陷的预防和控制需要采取相应的措施,以确保铸件质量达到要求。
8. 表面处理:压铸铸件的表面通常需要进行一些处理,以提高其表面质量和外观。
常见的表面处理方法有喷砂、抛光、喷漆等。
9. 机械加工:有些压铸铸件需要进行机械加工,以达到更高的精度和形状要求。
常见的机械加工方法有铣削、钻孔、车削等。
10. 环保与安全:在进行压铸工艺时,需要注意环保和安全要求。
例如,控制废气和废水的排放,遵守相关安全操作规程,确保工作人员的人身安全。
压铸基础培训资料
①合上模具 → ②将铝液倒入压室
→
③铝液高速的充填模具 型腔,并在高压下凝固
→ ④打开模具 → ⑤取出产品
1.1 铝压铸的特点
1.1.2 铝压铸的4大要素
压力铸造
铝锭材料
合金特性 熔炼工艺
压铸机
压铸机性能 稳定性
模具
产品结构 浇注系统方案
压铸工艺
真空压铸、半固态 压铸、充氧压铸 速度、压力、时间、 高速切换位置
3.经济效益好:相当多的压铸件不需再进行切削加工而直接使用,或加工量很少,提高了金属
利用率,减少了大量的加工设备和工时。
4.强度高质量轻:随着铝合金材料的不断优化,压铸铝合金产品强度也可达到很多机械行业特
别是汽车行业的使用要求,但其质量却只有铸铁(钢)的1/3.
铝压铸产品缺点
1.易产生气孔,气孔内部压力大,一般不能进行热处理; 2.对于口部小,内部大的“内凹”结构的产品,压铸较为困难; 3.不适宜小批量生产,其主要原因是压铸模具制成成本高,生产连续性要求较强。
顶出机构 合模油缸
哥林柱 曲肘 电机 模具
功能作用 安装固定定模 安装固定动模 为动模板移动、曲肘提支撑
顶出产品 推动动模板移动 平衡压铸机“三板”
通过扩大合模油缸力锁紧模具
带动整个液压系统的液压泵 产品成型工具
2.2 压铸机
2.2.2 基本结构—压射机构
储能器
冲头 压射杆
压射机构
压射油缸 增压油缸
第1节 铝压铸的特点和过程
到底有什么 不一样呢?
1.1 铝压铸的特点
1.1.1 铝压铸的概念
什么是压铸?
压力铸造是近代金属加工工艺中发展较快的一种少或者无切削的特种铸造方法。