板料弯曲回弹及工艺控制
板料弯曲回弹调节试验模型的建立
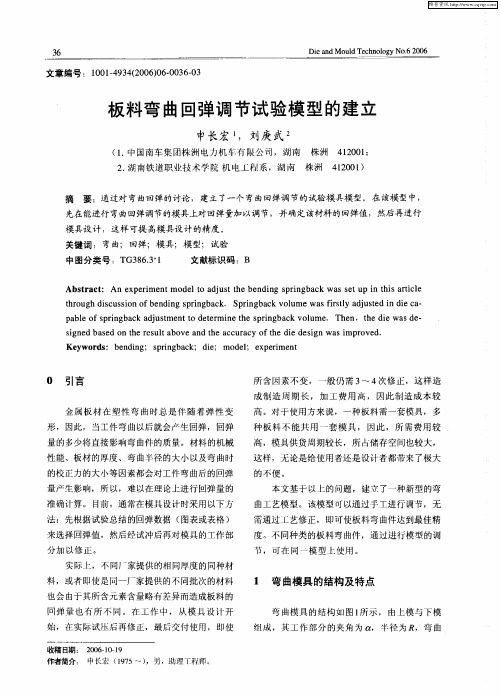
始 ,在实 际试 后 再修 正 ,最后 交付 使用 ,即使
收稿 日期: 2 0 —01 0 61—9 作者简介: 申长宏 ( 9 5~ ) 17 , ,助理 T程师 。
Ke wor y ds: be d ng; s i g c ni prn ba k; di ; mo l e e i nt e de ; xp rme
0 引言
金 属 板 材 在 塑 性 弯 曲时 总 是 伴 随 着 弹 性 变
形 ,因此 , 当工件 弯 曲以后就 会产 生 回弹 , 回弹
维普资讯
3 6
Di n o l c n lg . 0 6 ea dM udTe h oo yNo62 0
0 14 3 (0 60 — 0 60 文章编号 1 0 9 42 0 ) 60 3 — 3
板 料弯 曲回弹调 节试 验模 型 的建 立
pbe f pig akajs e todt m n e pig ak ou e h n h i w s e a l o r bc ut n t e r ie h r b c lm .T e ,t de a — s n d m e t s n v e d
sg e a e n ter s l a o ea d t ea c r c f h i e i nwa mp o e . i n d b s do h e u t b v n h c u a y o ed ed sg si r v d t
来选择回弹值 ,然后经试冲后再对模具的工作部
分加 以修 正 。
实 际上 ,不 同厂家 提供 的相 同厚 度 的 同种 材
料,或者即使是同一厂家提供 的不同批次的材料
板料弯曲回弹分析与控制

Ana l y s i s a nd Co n t r o l o f Be S he e t Me t a l s
校正板料弯曲回弹量分析

2 9 1 6
2 80 . 8
2 16 .9
2 80 . 8
20 7 .9
2? 8 .4
回弹后弯曲角 ;
p。 —— 回弹后 中性层 曲率半径 。
从 附表可看出 :
姗弹 角△
。 =一 (
= 占 +
( ) 当 r£ 1 / 一定时 ,△ 随 P 增大而减小。 ( ) 当P 一定时,△ 2 , 随 r£ 大而增大 。 /增
屈服条件 :
f 一f = p , , 。 。
() 2
伴随弹性变形 ,因此卸载 后必将 引起板料 回弹 ,使 工件
的曲率 半径和弯 曲角发生变化。
式中 o ——变形 区切 向应力 ; r
— —
。
变形 区径 向应力 ;
目前 ,国内外许多文献资 料 已指 出 回弹量 随校 正力
参磊 工热 工 整 墼 堕 呈!r 笪! 0.com 加 WWW.met ki 塑 _ 壁 al ng 7 wo 95
●■I 星 le ■■ I1t ■一 _ a ■ ■ Ml
— —
n g
u
将 式 ( ) 代入 式 ( ) 中司 得 : 4 2
小驯 一
由此式可看出,回弹角 △ 与单 位校 正力 P 及相 对 . 弯 曲半径 r£ 问的量化关系。 /之
Po=
4 .工业性试 验
采用厚度为 1 mm的 2 0钢板料 ,在 不 同单位校 正力
如果板厚减薄不计 ,R= + ,则 rt
=
/ { ) 一÷ +卜 一 ÷ P. ( r[ )÷ +) 及相应弯曲半径 r 条件下 ,取 得 回弹角 △ 的数值如 ÷ (
防止回弹的措施
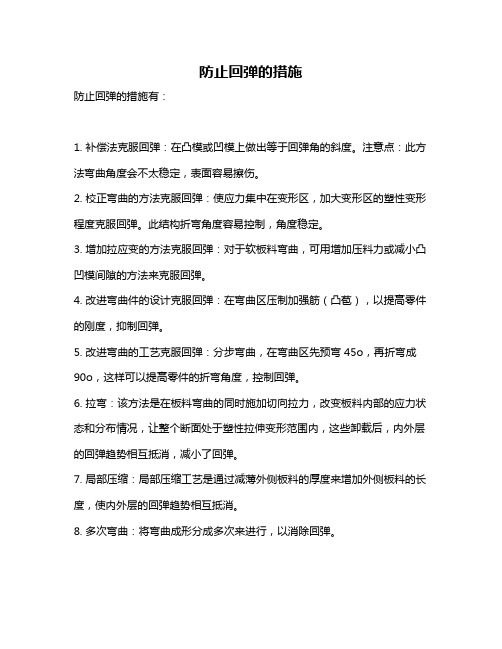
防止回弹的措施
防止回弹的措施有:
1. 补偿法克服回弹:在凸模或凹模上做出等于回弹角的斜度。
注意点:此方法弯曲角度会不太稳定,表面容易擦伤。
2. 校正弯曲的方法克服回弹:使应力集中在变形区,加大变形区的塑性变形程度克服回弹。
此结构折弯角度容易控制,角度稳定。
3. 增加拉应变的方法克服回弹:对于软板料弯曲,可用增加压料力或减小凸凹模间隙的方法来克服回弹。
4. 改进弯曲件的设计克服回弹:在弯曲区压制加强筋(凸苞),以提高零件的刚度,抑制回弹。
5. 改进弯曲的工艺克服回弹:分步弯曲,在弯曲区先预弯45o,再折弯成90o,这样可以提高零件的折弯角度,控制回弹。
6. 拉弯:该方法是在板料弯曲的同时施加切向拉力,改变板料内部的应力状态和分布情况,让整个断面处于塑性拉伸变形范围内,这些卸载后,内外层的回弹趋势相互抵消,减小了回弹。
7. 局部压缩:局部压缩工艺是通过减薄外侧板料的厚度来增加外侧板料的长度,使内外层的回弹趋势相互抵消。
8. 多次弯曲:将弯曲成形分成多次来进行,以消除回弹。
9. 内侧圆角钝化:从弯曲部位的内侧进行压缩,以消除回弹。
当板形U形弯曲时,由于两侧对称弯曲,采用这种方法效果比较好。
10. 变整体拉延成为部分弯曲成形:将零件一部分采用弯曲成形后再通过拉延成形以减少回弹。
这种方法对二维形状简单的产品有效。
11. 控制残余应力:拉延时在工具的表面增加局部的凸包形状,在后道工序时再消除增加的形状,使材料内的残余应力平衡发生变化,以消除回弹。
12. 负回弹:在加工工具表面时,设法使板料产生负向回弹。
上模返回后,制件通过回弹而达到要求的形状。
弯曲回弹的影响因素及其克服措施
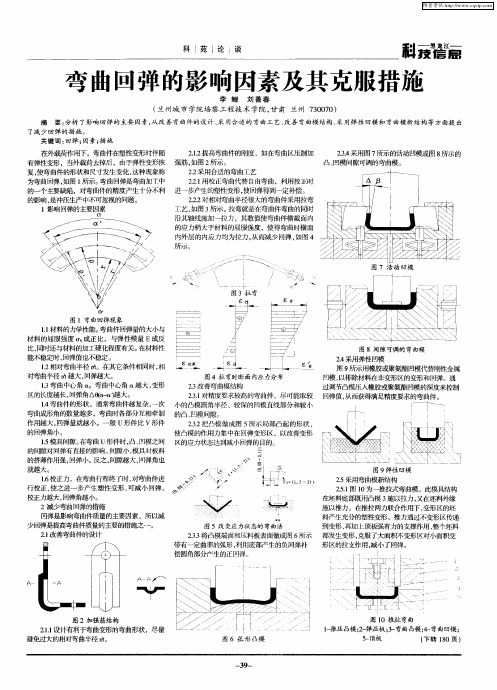
一
、
{
、
l
图1 0榭 主 弯曲 l椎压 凸模 ;_ — 2 弹压板 ;- 曲凸模 ;- 3弯 _ 4 弯曲 凹模 ;
5 顶板 一 ( 下转 10页 ) 8
2 .设计有利于弯曲变形的弯曲 1 1 形状 , 尽量 避免过大的相对弯曲半径 。
图 6 弧 形 凸模
一
39 一
/ 0 0 ,: 1 一 /_ / 1} I
一 /
图 8间 隙可调的 弯 曲模
一
一
—
—
l J
—
一
y
r
一
‘
一
『 l 一 一 一 _l _' — _
I
h
- —
.—
—
…
/
—
2 . 4采用弹性凹模 L L …. 堡 图9 所示用橡胶或聚氨酯凹模代替刚性金属 图 4 拉 弯时断 面 内应 力 分布 凹模 , 以排除材料在非变形区的变形和回弹。通 2 . 3改善弯 曲模结构 过调节凸模 压^ 橡胶或聚氨酯凹模的深度来控制 2 .对精度要求较高的弯曲件 ,尽可能取较 回弹值, .1 3 从而获得满足精度要求的弯曲 件。 小的凸模圆角半径 、较深的凹模直线部分和较小 的凸 、 凹模间隙。 2. .2把凸模做成图 5 3 所示局部凸起的形状 , 使凸模的作用力集中在 回弹变形 区,以改善变形 区的应 力状 态达 到减 小 回弹的 目的 。
维普资讯
科赫
唐 鹏
市政 与路 桥 ll l l
赵 金 龙
关于鸡讷公路松花江大桥冬季施工方案的介绍
( 龙建路桥 股份有 限公 司第一工程处 , 黑龙江 哈 尔滨 10 0 ) 50 0
U形冲压件弯曲回弹的控制与消除

弯 曲件 的 回弹量是 变形 区 和非变形 区 两部分 回
弹的综合效应 , 它与弯曲方式和模具结构有关 , 以 难 通过 分析 计算 用精确数 学公式 进行 明确 表达 。一 般 在设计模具时 , 回弹值的取得是按表格查 出经验数 值, 或者按计算方法求得 回弹值后 , 再在试模 中修 正 。但 目前 各类 冷 冲压 设计 手 册 、 料 基 本 上都 介 资
5 8
甘
肃
科
技
第2 6卷
能压 出合 格 的制件 。 即“ ” U 形制件 再 弯 曲的 回弹公
式为 :
有好 处 的。 2 14 设计合 理 的工件形状 ..
r= 0 ( + t / h z r 1 3 sO E ) / rr 式中: 为“ ” h u 形制件高度。
() 2
问题 。
的高 度 。r 值 愈 小 , 圆 角 区变 形 程度 愈 大 。其 /t 则
他条件相同时 , 回弹角随 r 值的增大而增大。 /t
I13 校整 程度 一般 来 说 , 整 力愈 大 , .. 校 回弹 角愈 、
12 “ ” . U 形制件再 弯 曲的 回弹经 验公 式
金 属 板材 在 塑性 弯 曲时 总是 伴 随着 弹性 变形 , 因此 当工 件弯 曲 以后 就 会 产 生 弹复 , 件不 仅 角 度 工
到 图纸要求 , 图 1 示 。经验公 式 为 : 如 所 r= ,/( +3r r/E ) t ( 1 t ) t ) s( () 1 式 中 :) , 为工 件 的圆 角半 径 ; 为 凸 模 的 圆角 半 径 ; ( r t E为材料 的弹性模 数 ;s c 为材 料 的 屈服 点 ; 为工 件 r t 材料厚 度 。
弯曲工艺与弯曲质量分析实验
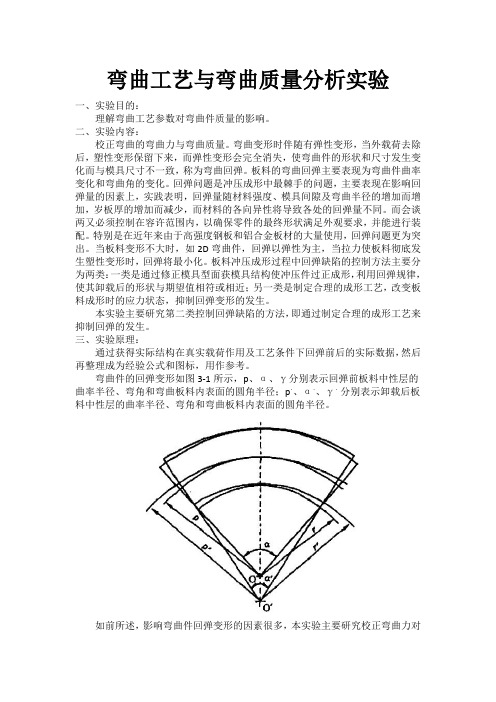
弯曲工艺与弯曲质量分析实验一、实验目的:理解弯曲工艺参数对弯曲件质量的影响。
二、实验内容:校正弯曲的弯曲力与弯曲质量。
弯曲变形时伴随有弹性变形,当外载荷去除后,塑性变形保留下来,而弹性变形会完全消失,使弯曲件的形状和尺寸发生变化而与模具尺寸不一致,称为弯曲回弹。
板料的弯曲回弹主要表现为弯曲件曲率变化和弯曲角的变化。
回弹问题是冲压成形中最棘手的问题,主要表现在影响回弹量的因素上,实践表明,回弹量随材料强度、模具间隙及弯曲半径的增加而增加,岁板厚的增加而减少,而材料的各向异性将导致各处的回弹量不同。
而会谈两又必须控制在容许范围内,以确保零件的最终形状满足外观要求,并能进行装配。
特别是在近年来由于高强度钢板和铝合金板材的大量使用,回弹问题更为突出。
当板料变形不大时,如2D弯曲件,回弹以弹性为主,当拉力使板料彻底发生塑性变形时,回弹将最小化。
板料冲压成形过程中回弹缺陷的控制方法主要分为两类:一类是通过修正模具型面获模具结构使冲压件过正成形,利用回弹规律,使其卸载后的形状与期望值相符或相近;另一类是制定合理的成形工艺,改变板料成形时的应力状态,抑制回弹变形的发生。
本实验主要研究第二类控制回弹缺陷的方法,即通过制定合理的成形工艺来抑制回弹的发生。
三、实验原理:通过获得实际结构在真实载荷作用及工艺条件下回弹前后的实际数据,然后再整理成为经验公式和图标,用作参考。
弯曲件的回弹变形如图3-1所示,p、α、γ分别表示回弹前板料中性层的曲率半径、弯角和弯曲板料内表面的圆角半径;p、、α、、γ、分别表示卸载后板料中性层的曲率半径、弯角和弯曲板料内表面的圆角半径。
如前所述,影响弯曲件回弹变形的因素很多,本实验主要研究校正弯曲力对回弹变形的影响。
板料的弯曲过程分为两种情况:一是自由弯曲过程;一是校正弯曲过程(如图3-2和3-3所示)。
图3-2 自由弯曲过程图3-3校正弯曲过程自由弯曲时,由于弯曲件的成形部分在冲压过程中不受模具的校正影响,所以卸载后回弹量较大,故在实际生产中较少使用;而校正弯曲是在板材自由弯曲的终了阶段,凸模继续下行将弯曲件压靠在凹模上,对弯曲件的圆角和直边进行精压,减少了回弹的影响,所以在实际中较为常见。
板料的弯曲现象及其原因
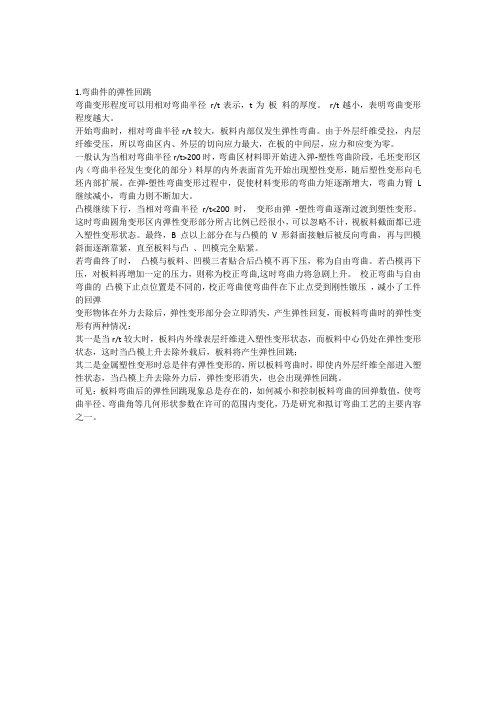
1.弯曲件的弹性回跳弯曲变形程度可以用相对弯曲半径r/t表示,t为板料的厚度。
r/t越小,表明弯曲变形程度越大。
开始弯曲时,相对弯曲半径r/t较大,板料内部仅发生弹性弯曲。
由于外层纤维受拉,内层纤维受压,所以弯曲区内、外层的切向应力最大,在板的中间层,应力和应变为零。
一般认为当相对弯曲半径r/t>200时,弯曲区材料即开始进入弹-塑性弯曲阶段,毛坯变形区内(弯曲半径发生变化的部分)料厚的内外表面首先开始出现塑性变形,随后塑性变形向毛坯内部扩展。
在弹-塑性弯曲变形过程中,促使材料变形的弯曲力矩逐渐增大,弯曲力臂L 继续减小,弯曲力则不断加大。
凸模继续下行,当相对弯曲半径r/t<200时,变形由弹-塑性弯曲逐渐过渡到塑性变形。
这时弯曲圆角变形区内弹性变形部分所占比例已经很小,可以忽略不计,视板料截面都已进入塑性变形状态。
最终,B 点以上部分在与凸模的V形斜面接触后被反向弯曲,再与凹模斜面逐渐靠紧,直至板料与凸、凹模完全贴紧。
若弯曲终了时,凸模与板料、凹模三者贴合后凸模不再下压,称为自由弯曲。
若凸模再下压,对板料再增加一定的压力,则称为校正弯曲,这时弯曲力将急剧上升。
校正弯曲与自由弯曲的凸模下止点位置是不同的,校正弯曲使弯曲件在下止点受到刚性镦压,减小了工件的回弹变形物体在外力去除后,弹性变形部分会立即消失,产生弹性回复,而板料弯曲时的弹性变形有两种情况:其一是当r/t较大时,板料内外缘表层纤维进入塑性变形状态,而板料中心仍处在弹性变形状态,这时当凸模上升去除外载后,板料将产生弹性回跳;其二是金属塑性变形时总是伴有弹性变形的,所以板料弯曲时,即使内外层纤维全部进入塑性状态,当凸模上升去除外力后,弹性变形消失,也会出现弹性回跳。
可见:板料弯曲后的弹性回跳现象总是存在的,如何减小和控制板料弯曲的回弹数值,使弯曲半径、弯曲角等几何形状参数在许可的范围内变化,乃是研究和拟订弯曲工艺的主要内容之一。
- 1、下载文档前请自行甄别文档内容的完整性,平台不提供额外的编辑、内容补充、找答案等附加服务。
- 2、"仅部分预览"的文档,不可在线预览部分如存在完整性等问题,可反馈申请退款(可完整预览的文档不适用该条件!)。
- 3、如文档侵犯您的权益,请联系客服反馈,我们会尽快为您处理(人工客服工作时间:9:00-18:30)。
板料弯曲回弹及工艺控制
板料在弯曲过程中,产生塑性变形的同时会产生弹性变形。
当工件弯曲后去除外力时,会立即发生弹性变形的恢复,结果使弯曲件的角度和弯曲半径发生变化,与模具相应形状不一致,即产生回弹。
回弹是弯曲成形过程的主要缺陷,它的存在造成零件的成形精度差,显著地增加了试、修模工作量和成形后的校正工作量,故在冲压生产中,掌握回弹规律非常重要。
如果在设计模具前,能准确掌握材料的回弹规律及回弹值大小,设计模具时可预先在模具结构及工作部分尺寸上采取措施,试冲后即使尺寸精度有所差异,其修正工作量也不会太大,这不仅可以缩短模具制造周期,而且有利于模具成本的降低及弯曲件精度的提高。
1 弯曲回弹的表现形式
弯曲回弹的表现形式有下列二个方面(如图1所示):
(a) 弯曲半径增加:卸载前板料的内半径r (与凸模的半径吻合),在卸载后增加至r0,半径的增量为△r二r0一r
(b) 弯曲件角度增大:卸荷前板料的弯曲角为α(与凸模的顶角吻合),在卸荷后增大到α0,角度增量为△α=α0一α
图1 回弹导致弯曲角和弯曲半径变化
2 弯曲回弹产生的原因
弯曲回弹的主要原因是由于材料弹性变形所引起的。
板料弯曲时,内层受压应力,外层受拉应力。
弹塑性弯曲时,这两种应力尽管超过屈服应力,但实际上从拉应力过渡到压应力时,中间
总会有一段应力小于屈服应力的弹性变形区。
由于弹性变形区的存在,弯曲卸载后工件必然产生回弹。
在相对弯曲半径较大时,弹性变形区占的比重大,回弹尤其显著。
回弹是由于在板厚方向应力或应变分布不均匀而引起的。
这种应力和应变的不均匀分布是弯曲的特点,对于只施加弯矩的弯曲方式,要有效减少回弹是困难的。
为了使回弹减小,应尽量使板厚断面内的应力和应变分布均匀,为此可采取在纵向纤维方向对板料进行拉伸或压缩的方法,也可采用在板厚方向施加强压的方法。
在沿板的长度方向单纯拉伸变形的场合,除去外力后,由于在整个板厚断面内变形的恢复是均匀的,所以不会发生形状的变化。
3 影响弯曲回弹的因素
(1)材料的机械性能材料的屈服点σs越高,弹性模量E越小,回弹越大。
(2)相对弯曲半径R/t 弯曲半径R越大,材料厚度t越小,即相对弯曲半径R/t值越大,回弹越大。
(3)弯曲处校正力的大小校正力越大,回弹越小。
(4)凸凹模间隙间隙越大,回弹越大。
间隙小于材料厚度时,有可能出现负回弹。
(5)弯曲件的形状弯曲件直边过短时,回弹较大。
V型弯曲件的回弹比U型弯曲件的回弹大。
(6)凹模形状及尺寸凹模深度过小时,回弹很大。
4 控制弯曲回弹的方法与措施
减小回弹常用方法有补偿法、校正法、改变应力状态、改进工件设计等。
影响弯曲回弹的因素很多,对于不同的影响因素,应采用不同的措施,也可综合运用几种方法,来减少回弹。
4.1 补偿法减少弯曲回弹
补偿法是按预先估算或试验所得的回弹量,在模具工作部分相应的形状和尺寸中予以“扣除”,从而使出模后的弯曲件获得要求的形状和尺寸。
(l) V型弯曲,如图2a所示。
可在凸模和凹模上同时减小一个回弹角,使工件回弹后恰好等于所要求的角度,这种方法适用于相对弯曲半径较大,回弹较大的工件。
(2) L型弯曲,如图2b所示。
凹模向内倾斜一角度△α,并同时缩小凸、凹模的间隙,单面间隙取小于材料厚度,促使工件贴住凹模。
出模后工件回弹,直边恢复垂直。
图2c所示,采用硬橡胶促使工件贴住凹模,补偿工件回弹。
图 2 补偿法减小回弹
(3) U型弯曲,如图2d,2e,2f。
图1d中将凸模的两侧壁制成向内倾斜一角度△,并同时缩小凸、凹模的间隙,单面间隙取小于材料厚度,促使工件贴住凸模。
出模后工件回弹,两边恢复垂直。
图2e中采用弧形顶板,并且凸模底部也相应做成弧形面。
工件出模后由于其底部曲面回弹伸直,补偿了两边的回弹,使两边恢复垂直。
图2f中采用硬橡胶促使工件贴住凸模,凸模的两侧壁制成向内倾斜一角度△α,补偿工件回弹。
(4) z形弯曲,如图2g所示。
Z形弯曲两个弯角回弹值不同,易导致平行部位不平行,为了避免这种现象,凸模和凹模应分别向外倾斜一角度△α,对板厚在lmm以内的冷轧板弯曲,倾斜角取2º一3º较为合适。
(5)∏形弯曲,采用如图2h所示模具结构时,为避免回弹导致法兰边与底不平行,凸模和凹模应分别倾斜一角度△α,对板厚在lmm以内的冷轧板弯曲,倾斜角取2º-3º较为合适。
图2i 所示模具,弯曲时,活动凹模沿着斜面向下运动的同时向内夹紧工件,使工件贴紧凸模,凸模两侧和肩部都做出斜度,从而补偿工件回弹。
4.2 校正法减少弯曲回弹
校正法是在模具结构上采取措施,使校正力集中在弯曲处,通过加大弯曲处的应力,增大变形区的塑性变形成份,改善应力状态分布,从而减少弹性变形,减少回弹,如图3所示。
图3 校正法减小回弹
(1) v型弯曲,如图3a,3b,3c所示。
可将凸模角度减小2º ~3º或使凸模的尖角稍稍突起
0.2~0.3mm,以便把校正压力集中在这部分上,提高单位面积的受力,从而消除回弹。
也可采用图3c所示结构,加大凹模圆角半径R,取R= r+(1.2~1.25)t,使工件圆角部分材料变薄,达到消除回弹的目的。
(2) L型弯曲,如图3d所示。
凹模圆角处向上稍稍突出一条筋,以便最后整形时把校正压力集中在这部分上,提高单位面积的受力,从而消除回弹。
(3) U型弯曲,如图3e、3f所示。
图3e中凸模圆角处稍稍突起0. 1~0. 3mm的筋,以便把校正压力集中在这部分上,提高单位面积的受力,从而消除回弹。
图3f中加大凹模圆角半径R,取R= r+(1.2~1.25)t,使工件圆角部分材料变薄,达到消除回弹的目的。
(4) ∏形弯曲,如图3g所示。
凸模圆角处向上突出二条筋,以便最后整形时把校正压力集中在这部分上,提高单位面积的受力,从而消除回弹。
∏形弯曲的肩部后压弯部分几乎不产生回弹,甚至产生轻微的负回弹。
4.3 调整模具间隙的方法减少弯曲回弹
缩小模具间隙,有利于减少弯曲回弹。
当弯曲模具单面间隙小于材料厚度时,回弹已变得很小,甚至产生轻微的负回弹,模具单面弯曲间隙应比板厚小0.02~0.05mm为宜,一般取0. 03mm。
过小的间隙会引起材料变薄,工件表面划伤,同时会降低模具寿命。
4.4 采取工艺措施的方法减少弯曲回弹
(1) 采用校正弯曲代替自由弯曲,采用弹性顶板压紧材料弯曲,并施加较大的背压力。
(2) 凸模圆角半径尽量取最小弯曲半径,凹模深度一般不小于10倍的料厚。
(3) 当工件弯曲高度过小时,可先增加弯曲高度,弯曲后在后续工序切去多余材料。
(4) 对精度要求高的弯曲件,可采用弯曲后整形。
(5) 在条件允许的情况下,采用加热后弯曲。
4.5 改变应力状态的方法减少弯曲回弹
采用拉弯工艺或采用附加拉应力的方法改变板料断面的应力状态,对减少回弹极为有效。
加拉力的方式有三种:可在给了拉力之后的状态下进行弯曲,或在进行弯曲变形的同时加上拉力以及给予弯曲变形之后再拉伸的三种方式。
三种方式中,以在弯曲后加拉力的方案其回弹最小。
拉弯适合于相对弯曲半径很大的工件。
图4a所示,采用先强力压紧材料后弯曲成形,通过摩擦力对板料产生附加拉力来减少回弹,适合于带法兰边的工件。
采用弯曲后在板料长度方向施加压力的方法改变板料断面的应力状态,对克服回弹极为有效。
图4b中,板料先通过橡胶传力弯曲成形,随后通过压缩橡胶对工件高度方向施加压力,使工件高度压缩3%左右,工件在整个长度上产生微量塑性变形,工件壁厚增厚0.03 ~0.06mm(工件两端增厚多,中间增厚少)。
卸载后,工件与模具内腔形状、尺寸一致,不产生回弹。
图4 改变应力状态减小回弹
4.6 改进工件设计减少弯曲回弹
在弯曲区压制加强筋,不仅可以提高工件刚度,也有利于减少回弹。
在满足使用的条件下,选用弹性模量大、屈服点低、硬度低、塑性好的材料,以减少回弹。
5 结论
弯曲回弹较为复杂,在实际工作中,完全消除弯曲回弹是很困难的,在一定范围内采取预防措施,尽量减少弯曲回弹带来的不良影响,是我们工作的目标。
实践中应根据具体情况灵活运用不同的控制回弹的方法。
必要时,可将几种减小弯曲回弹的方法综合使用,效果可能更好。