板料冲压成形及回弹有限元模拟分析
回弹分析

汽车覆盖件成形仿真中的回弹分析0引言薄板冲压成形作为一种塑性加工方法,广泛应用于汽车、航空航天、电器、造船、仪表等工业领域,它在汽车制造中尤为重要。
据统计,汽车上有60%~70%的零件是采用冲压工艺生产出来的。
汽车冲压件成形质量的好坏不仅影响到整车的装配、汽车外观,更影响到汽车的制造成本以及新车型开发的周期。
薄板冲压成形包含多种复杂物理现象,主要有:接触碰撞现象;摩擦磨损现象;大位移、大转动和大变形现象。
这种复杂性使得对的设计和控制非常的困难,从而造成成形过程中产生许多缺陷,并且难以纠正。
起皱、破裂和回弹是薄板成形中的三种主要缺陷,其中回弹是最难控制的,因为涉及到对回弹量的准确预测,而不同材料、不同形状的冲压件的回弹规律差别很大。
回弹问题的存在会影响冲压件的形状尺寸精度和表面质量。
冲压件的最终形状取决于成形后的回弹量,当回弹量冲过允许容差后,就成为成形缺陷,进而影响整车装配。
由于目前对轿车装配质量的要求日益提高,综合装配误差严格控制在较小的数值范围内,这无形中增加了对冲压件成形精度的要求。
回弹不仅是工业生产中的一个实际问题,同样也是学术界长期以来关注的热点。
从NUMISHEET93’(第二届板料成形三维数值模拟国际会议)开始,每届会议都有关于回弹预测的标准考题(BENCHMARK),在NUMISHEET’99上,专门有一个关于回弹预测和回弹误差控制的会议专题,其中文章达到10篇,约占全部会议文章的11%。
有限元数值模拟技术的引入,为推动回弹问题的解决提供了有利的工具。
因此,利用数值模拟技术对轿车冲压成形后的回弹变形进行准确预测,在此基础上,研究回弹控制方法以提高成形精度,对于降低轿车冲压件制造成本、保障整车装配质量、缩短新产品开发周期有着重要的意义。
1薄板冲压成形仿真系统随着理论和技术上的日臻完善,冲压成形有限元仿真分析在汽车工业中的应用日益受到重视。
覆盖件冲压成形仿真分析在多方面对企业的冲压生产提供有利的支持:在设计工作的早期阶段评价覆盖件及其模具设计、工艺设计的可行性;在试模阶段进行故障分析,解决问题;在批量生产阶段用于缺陷分析,改善覆盖件生产质量,同时可用来调整材料等级,降低成本。
板料冲压成形的弹塑性有限元仿真分析方法

( . h o fM e ha r n c Eng n e i g,Ch n c u i e s t fTe h o o y,Ch n c u 3 0 2,Ch n 1 Sc o lo c t o i i e rn a g h n Un v r i y o c n l g a g h n1 0 1 ia 2 Sc o lo sc Sce e . h o fBa i inc ,Cha gc u n h n Uni e s t fTe h o o ,Ch n c u 3 0 2,Ch n ) v r iy o c n l gy a g h n1 0 1 ia
g ! !堕 ! !曼 璺 i ! ! 2 ! 2
!: ! !
板 料 冲 压 成 形 的 弹 塑 性 有 限元 仿 真 分 析 方 法
厉 呈 臣 潘 晓 辉 韩 秀 清 , ,
( . 春 工业 大 学 机 电 工程 学 院 ,吉 林 长 春 1 0 1 ;2 长 春 工 业 大 学 基 础 科 学 学 院 , 林 长 春 1 0 1) 1长 302 . 吉 3 0 2
O 引 言
板 料 成 形 是 利 用 模 具 对 金 属 板 料 的 冲 压 加 工, 获得质 量轻 、 面光 滑 、 型美观 的冲压 件 , 表 造 具
现 使这 些 问 题 有 了 巨大 的改 善 。板 料 成 形 C AE
分 析 软件 , 以在 产 品原 型 设 计 阶 段进 行 工 件 坯 可 料 形状 预示 、 品可成 形性 分析 , 产 以及工 艺方 案优 化 , 而有 效地 缩短 模具 设 计周 期 , 从 大大 减少 试模
板料冲压成形回弹补偿修正方法及其验证_李延平

H=
F 2( F 2(
$d ) $p )
=
F 2( d 2) - F 2( d 1) F 2( p 2) - F 2( p 1)
( 4)
可见, 如果已知两组相近的模具形状数据和对
应的冲压件形状数据, 即可计算出模具 - 冲压件偏 差频域传递函数 H 。
如果对模具 Ñ 进行补偿修正( 修正后新模具的
形状测量数据为 d * ) , 使其对应的冲压件为给出的
例系数为 H 。
# 488 #
汽车工程
2005 年 ( 第 27 卷) 第 4 期
如果设模具 Ñ 形状测量数据为 d 1、对应的冲压 件 Ñ 形状测量数据为 p 1, 模具 Ò 形状测量数据为 d 2、对应的冲压件 Ò 形状测量数据为 p 2, 在线性小
量回弹情况下, $d = d 2 - d1; $p = p 2 - p 1, 那么 由式( 3) 得
数值模拟效率高费用低由于计算模型与实际工况有差距导致计算精度较可靠性较差优化结果难以满足工程实际需要以线性闭环控制系统空间fourier变换和频域传递函数为理论基础基于模具实验迭代建立了模具回弹补偿修正算法板料冲压成形回弹补偿修正算法211回弹补偿修正系统工作原理板料冲压成形模具回弹补偿修正系统工作原理如图首先应用cad系统设计初始模具通过经国家863项目2001aa421270和十五国家科技攻关项目2001ba205b1001资助原稿收到日期为2004修改稿收到日期为2004验知识和ca仿真使模具初始设计尽量满足成形要求不存在起皱开裂等缺陷系统制作模具原型采用快速模具弧喷涂等快速制造模具在冲压机上进行样件试冲压调整工艺参数使样件没有起皱开裂等缺陷保持工艺参数稳定对试冲压样件进行三维激光扫描测量评价其尺寸误差若样件尺寸误差满足要求模具即为最终设计模具否则在保证冲压成形性能前提下按合适的模具修正方法进行模具型面修正根据模具型面修正数据制造新模具在原冲压工艺参数下进行新的样件试冲压激光扫描测量和尺寸误差评价若新样件尺寸误差满足要求新模具即为最终设计模具否则重复以上迭代过程直至满足要求为止是高度非线性的所以整个系统也是非线性的必须对其进行线性化处理才能用简单的算法实现回弹补偿
基于ANSYS的钢板的冲压回弹分析

基于ANSYS的钢板的冲压回弹分析1 引言在汽车、航空、家电等工业部门,许多构件是用板料冲压成形生产的。
板料成形过程牵涉到几何非线性、材料非线性和边界条件非线性的复杂的力学问题。
在多数动态金属成形工序中,高度非线性过程导致在坯料中产生大量的弹性应变能,存储的弹性能在成形压力消失后释放,使坯料向着原有几何构形变形。
因此,在板金属成形过程中最后的形状不仅仅取决于模具的轮廓形状,也取决于坯料在塑性变形时存储的弹性能总量。
因为在变形部分存储的弹性能总量是许多过程参数 (如材料性质,二表面间的载荷 )的函数,在成形时期预测回弹是特别复杂的。
金属板料冲压成型是利用金属塑性变形的特点,通过对金属板料施加压力,使其产生塑性变形从而获得所需要的形状。
由于板料冲压成型过程包含大位移、大变形等十分复杂的物理现象,使得对其成型控制非常困难,以前更多的是通过反复试验的方法制造出合乎要求的产品,其过程需要花费大量的时间和经费。
随着有限元模拟技术的迅速发展,利用有限元软件模拟金属板料冲压成型过程及分析其回弹量已成为可能,本文介绍了利用有限元软件Ansys对金属板料冲压成型过程进行模拟和回弹分析的方法。
2 模型的建立及计算讨论如图1所示,钢板冲压模型由两部分组成,分别是被冲压件钢板和冲压的刚性模具。
在计算中采用刚-柔接触计算模型分析。
把钢板假设为柔性件,模具为刚性件不考虑其变形。
计算中钢板采用双线性等向强化模型,来考虑冲压过程中的弹塑性变形。
其计算参数如表1所示。
表1 计算中主要的参数本文冲压模拟分为两个阶段,第一个阶段为刚性模具进行冲压阶段,第二阶段为回弹计算,计算中假设整个过程为准静态。
在计算回弹时采用微量卸载来保证数值计算的稳定性。
其个阶段的计算结果如下:图3到图8给出了冲压不同阶段的钢板的等效应力。
由以上各图可以看出冲压初始阶段压力较大处主要集中于中间的上下表面,然后最大应力从中间钢板的上下表面向钢板内部发展;同时应力从钢板中间向两边传播。
板料冲压及回弹分析过程的动态模拟
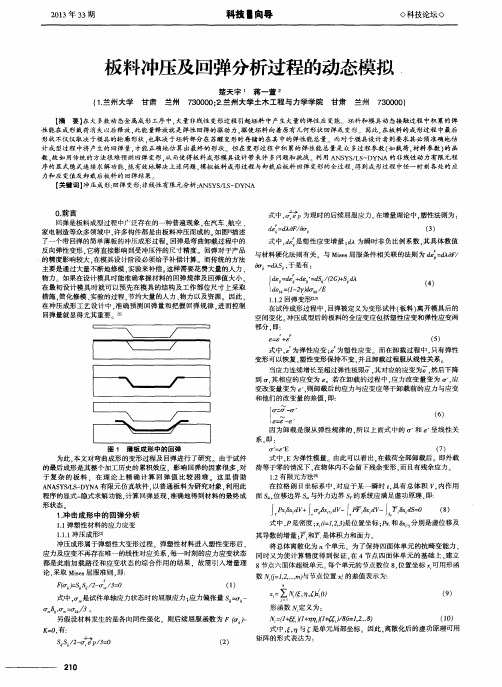
科技 I向导
◇ 科技论坛◇
板 料冲压及 回弹分析 过程的动态模 拟
( 1 . 兰州大学 甘肃 楚天字 , 蒋一萱 2 兰州 7 3 0 0 0 0 ; 2 . 兰州大学土木工程与力学学院 甘肃 兰州 7 3 0 0 0 0 )
【 摘 要】 在 大多数动 态金属成形工序 中, 大量非线性 变形过程引起 坯料中产生大量的弹性 应变能。坯料 和模具 动态接触过程 中积 累的弹 性能在成形载荷 消失 以后释放 , 此能量释放 就是弹性回弹的驱动力 , 驱使 坯料 向着原有几何 形状 回弹或 变形 因此 . 在板料 的成形过程 中最后 形状 不仅仅取 决于模具的轮廓形状 . 也取决于坯料部分在 苏醒变形时存储 的在其中的弹性 能总量 而对于模具设计 者则要 求其必 须准确 地估 计成型过程 中将产 生的 回弹量 , 才能正确地估 算 出最终的形状 但在 变形过程 中积 累的弹性能 总量是 众多过程 参数( 如栽荷 。 材料参数 ) 的函 数. 故如 用传统 的方法很难预测回弹 变形 . 从而使得板料成形模具设计带来许多问题 和挑 战 利 用 A NS YS / L S — DYNA的非线性动力有限元程 序 的显式 隐式连 续求解功 能. 能有效地解决上述 问题 。 模拟板料成形过程与卸载后板料回弹变形的全过 程. 得 到成 形过程 中任一 时刻各处的应
1 . 冲 击 成 形 中 的 回 弹分 析
J P x 6 x d V + J
, j d V — J & d V — J r 瓯 0 ( 8 )
1 . 1弹塑性 材料 的应力应 变 1 . 1 . 1冲压 成形[ 其导数 的增量 : 和 是体积力和面力 。 冲压成形属于弹塑性大变形过程 弹塑性 材料进入塑性变形后 . 将总体离散化为 n 个单元 . 为 了保持 四面体 单元的抗畸变能力 , 应力及应 变不再 存在唯一的线性 对应关 系. 每一 时刻的应力应变状态 同时又为使计算 精度得到保证 . 在4 节点 四面体单元 的基 础上 建立
板料冲压成型过程的仿真分析

板料冲压成型过程的仿真分析板料冲压成型过程的仿真分析冲压成型是一种广泛应用于制造业的加工方法,可以用于生产各种类型的零件和产品。
在冲压成型过程中,板料被放置在冲床上,然后通过冲压头施加压力,将板料变形成所需形状。
为了进行冲压成型过程的仿真分析,我们可以按照以下步骤进行思考:第一步:确定冲压件的设计和材料参数。
在仿真分析之前,需要明确冲压件的设计要求,包括形状、尺寸和材料参数等。
这些参数将用于后续的仿真模型建立和分析。
第二步:建立冲压过程的仿真模型。
基于冲压件的设计参数,可以使用一些专业的仿真软件,如AutoForm、PAM-STAMP等,建立冲压过程的仿真模型。
在建立模型时,需要考虑板料的材料特性、冲床的结构参数以及冲压头的运动规律等。
第三步:进行冲压过程的仿真分析。
在建立好仿真模型后,可以进行冲压过程的仿真分析。
通过对模型施加适当的载荷和边界条件,可以模拟真实的冲压过程,并得到冲压件的变形情况、应力分布以及可能出现的缺陷等信息。
第四步:优化冲压过程的参数。
根据仿真分析的结果,可以对冲压过程的参数进行优化。
例如,调整冲压头的运动速度、改变冲压件的厚度或减小冲床的压力等,以达到更好的成形效果和减少缺陷的目的。
第五步:验证仿真结果的准确性。
为了验证仿真结果的准确性,可以将仿真得到的冲压件与实际生产的样品进行对比。
通过比较冲压件的尺寸、形状以及可能存在的缺陷等,可以评估仿真结果的可靠性,并进行必要的修正和改进。
最后,冲压成型过程的仿真分析可以帮助设计师和工程师更好地理解冲压过程的工艺特性,优化冲压工艺参数,提高产品质量和生产效率。
同时,通过仿真分析,还能更早地发现潜在的问题和缺陷,减少实际生产中的试错成本和风险。
因此,冲压成型过程的仿真分析在现代制造业中具有重要的应用价值。
泡沫铝材料的制备与有限元模拟
泡沫铝材料的制备与有限元模拟泡沫铝材料是一种轻质、高强、具有良好吸声和隔热性能的新型功能材料。
由于其独特的优点,泡沫铝材料在许多领域都具有广泛的应用前景,如汽车、航空航天、建筑和国防等。
因此,研究泡沫铝材料的制备技术与有限元模拟对其性能的影响具有重要意义。
泡沫铝材料的制备方法主要有物理发泡法、化学发泡法和机械搅拌法等。
其中,物理发泡法是最常用的方法,其工艺流程如下:将混合物放入模具中,置于一定温度和压力条件下;发泡剂分解产生气体,导致混合物膨胀,形成泡沫铝材料;通过观察泡沫铝材料的泡孔结构,发现泡孔大小、分布和密度等因素对其性能有较大影响。
同时,泡沫铝材料的力学性能也表现出明显的各向异性,其中沿垂直于泡孔方向的性能较好。
有限元模拟是一种常用的数值分析方法,可以用来预测泡沫铝材料的性能。
在有限元模拟过程中,需要选择合适的材料模型、边界条件和有限元软件。
其中,材料模型需要考虑泡沫铝材料的弹性模量、泊松比和密度等参数;边界条件需要考虑材料的受力情况;有限元软件可选择ANSYS、SolidWorks等。
通过有限元模拟,可以得出泡沫铝材料的应力、应变和疲劳寿命等性能指标。
在应力分析中,发泡剂的加入使得泡沫铝材料的应力水平显著降低;在应变分析中,泡沫铝材料的应变主要发生在泡孔内,并且沿泡孔方向的应变最大;在疲劳寿命分析中,泡沫铝材料的疲劳寿命随着泡孔密度的增加而降低。
通过对泡沫铝材料的制备与有限元模拟研究,发现制备过程中的发泡工艺对泡沫铝材料的性能具有重要影响。
同时,有限元模拟结果表明,泡沫铝材料的应力、应变和疲劳寿命等性能指标受到泡孔结构、密度等因素的影响。
然而,目前的研究还存在一些不足之处,如制备过程中工艺参数的控制、有限元模拟中材料模型的精度等问题需要进一步探讨。
为了更好地应用泡沫铝材料,未来的研究方向可以从以下几个方面展开:优化制备工艺:进一步研究发泡工艺中的关键参数,如发泡剂类型、温度和压力等对泡沫铝材料性能的影响,为实现制备过程的优化提供依据。
板材成型回弹
板材冲压成形模拟回弹预示刘军华 柳玉起 胡 平 李运兴(吉林工业大学力学系 130025)摘要 基于弹塑性大变形有限元数值方法,在自行开发研究的汽车覆盖件板材成形分析软件基础上研究了板材冲压成形后脱模卸载和切边后的回弹现象,给出预示它们回弹量大小的数值方法。
研究了典型的U 型件拉深弯曲回弹,与实验结果进行了比较。
然后又预示了卫星天线反射面拉深成形的脱模卸载回弹量和切边后的回弹量,并与实际冲压件进行了回弹量比较,两种回弹都得到了较满意的结果。
回弹严重影响汽车覆盖件的成形质量和尺寸精度,也是实际工艺中很难有效克服的成形缺陷之一,它的精确预示是实际工程技术人员非常关心的问题。
回弹包括冲压件的脱模回弹和切边后回弹两方面,根据实际冲压件结构和实际工艺的不同,两种回弹都可能产生很大的作用,所以在有限元数值模拟时,两种回弹必须都能有效预示。
它是计算固体力学与金属塑性加工学科相互交叉的前沿性研究课题。
由于大型冲压件形状复杂,难于事先预示其成形性和成形后的产品质量,致使模具调试时间长,加工质量低,制模成本高,严重制约了我国模具及汽车工业的自主发展,尚失了国内国际市场的竞争力。
因此,板材成形回弹问题的研究不仅具有重要的理论价值,而且具有十分广阔的应用前景和重大的经济效益。
1 有限元基本理论及回弹处理方法1.1 单元模型采用DKT 平板单元[1]和薄膜三角形单元的组合[2]来模拟空间大变形大应变板材冲压成形问题。
在局部随体正交坐标系z x ox 21下,即z 轴垂直于单元平面,1x 轴通过单元1,2结点,2x 轴由1x 轴和z 轴按右手规则确定。
在z x ox 21坐标系下考虑Kirchhoff 直法线假设,单元内任意点()z x p i , ()2,1=i 的速度可假定为()()()()()i i i j i j i j x w z x w x z x u z x u &&&&&=+=,,β )2,1,(=j i (1)式中,i u &和w &分别表示p 点在中面上相对应点()0,i x 沿i x 和z 方向的速度;iβ&表示单元法线转角速度。
汽车覆盖件冲压成形回弹及模面优化研究
汽车覆盖件冲压成形回弹及模面优化研究摘要:回弹是汽车覆盖件冲压成形时产生的主要质量缺陷之一,直接影响到产品的尺寸精度和最终形状。
本文以某汽车背门内板为例,利用板料成形仿真软件Autoform研究了零件的冲压成形及回弹过程,预测了实际板料冲压成形后可能出现的回弹量,通过优化模具型面来控制回弹,并与实际零件对比,验证了优化方案的合理性。
关键词:汽车覆盖件;冲压成形;回弹;模面优化板料冲压成形中的回弹问题一直是冲压成形领域关注的热点问题[1]。
随着汽车工业的不断发展,特别是近年来高强度钢板和铝合金板的大量使用,汽车覆盖件冲压成形中的回弹问题变得越来越棘手。
冲压件的最终形状取决于成形后的回弹量,回弹量超过允许的差值,就成为成形缺陷,进而影响整车的外观和装配。
为了更好的控制冲压件的回弹,提高其成形质量和成形精度,必须对回弹量做出准确地预测。
有限元仿真技术成为研究回弹问题的强有力工具[2]。
本文以某汽车背门内板为例,材质为高强度钢,利用板料成形仿真软件Autoform对其冲压成形和回弹过程进行模拟,对零件实际生产过程中可能出现的回弹量进行预测,为优化模具型面来控制回弹提供有益的指导。
1 成形过程仿真与结果分析1.1有限元建模及参数设置将UG中建立好的背门内板模型通过标准的IGES格式导入到Autoform中,如图1所示,设置拉延工具:凹模、凸模、压边圈的数模;拉延类型选择单动拉延,调整各工具的拉延运动模式,如方向、速度、行程等;摩擦力设置为0.15,压边力设置为1800kN,压边圈行程设置为180mm。
Autoform计算采用等效拉延筋,即将拉延筋复杂的几何形状抽象为一条能承受一定力的附着在模具表面的拉延筋线,在表示拉延筋的线上施加阻力来代替实际拉延筋[3]。
图1 模具和板料的有限元模型板料所选用的材料为高强度钢板DX56D,厚度为1.2mm,其材料参数如表1所示。
表1 高强度钢板DX56D的材料参数1.2 成形仿真结果分析有限元建模和参数设置完毕后提交运算,得到结果。
板材多点成形回弹的有限元分析
作 者 简 介 : 怀 焱 ( 94) 男 , 士 生 。 袁 18 一, 硕 研 究 方 向 : 船 自动 化 与设 备 。 造
E- i: u n u ia 2)8 1 3 C 1 maly a h ay n ()@ 6 . O I ( T
形方法成形 质量差 、 生产 效率 低 , 而且 劳动 强度 极 大 。应用数控技 术进行 自动化弯板 , 仅可大 幅度 不
理想 弹塑性 的 ; 中性 面 固定 在板 的几何 中面 上 , ②
且 中性 面上 没有应 力 ; ③板 内任 一 点 的应 变 的大
小正 比于该 点到 中性 面的距 离l 。 _ 1 ]
显式算 法模 拟成 形 过 程 , 网格 细 化 将 使 时 间步 长
正确理解 加工过程 中出现 的各种 问题 , 确定有关 工
艺参数 , 提高 加工 质量 。因此 , 虑采 用有 限元 分 考
析 软件 AN YSL - Y S / SD NA, 以球 面钢 板 为研 究 对
象, 通过显式算 法模 拟动 态成 形 过程 , 将变 形后 的 几何 形状 和应力输 入 AN Y S S隐式 分析 中 , 过给 通
定合适 的边 界条 件来模拟线性 回弹变形 , 用不 同 的 板料厚度 对 回弹的影响进行分析 和 比较 。
减小 , 长 C U 时 间 。 其 最 大 时 问 步 长 t 延 P 由
C uat o rn 条件 确定 :
≤ KL C /
1 在冷 弯加工 过程 中存在 回弹现 象 。这 是 由于板料 在弯 曲过 程 中 , 料 中不 但 存在 塑 性 变 材 形, 也存 在 弹性 变 形 , 因此 卸 载之 后 , 的弯 曲半 板 径 较卸 载前增 大 , 曲角则较 卸载 前减小 , 弯 即产 生 回弹 。回弹造 成构 件 的 成形 精 度 差 , 加 了成 形 增 后 的校形 工作 量 , 在 生 产 实 际 中迫 切需 要 有 效 故
- 1、下载文档前请自行甄别文档内容的完整性,平台不提供额外的编辑、内容补充、找答案等附加服务。
- 2、"仅部分预览"的文档,不可在线预览部分如存在完整性等问题,可反馈申请退款(可完整预览的文档不适用该条件!)。
- 3、如文档侵犯您的权益,请联系客服反馈,我们会尽快为您处理(人工客服工作时间:9:00-18:30)。
Ku=F
式中K为总刚度矩阵;u为位移向量;F为节点载荷向量。
在隐式算法中,对于第i个给定的加载增量,用Newton-Raphson迭代法,需要求解下面的方程:
板料冲压成形及回弹有限元模拟分析
摘要
回弹是板材冲压成形过程中不可避免的普遍现象,直接影响到冲压件的尺寸精度和零件最终形状。本文利用ANSYS/LS-DYNA有限元软件中的非线性动力的显式、隐式连续求解功能,模拟了板料冲压成形过程与卸载后板料回弹变形的全过程,得到了成形过程中任一时刻各处Von-Mises应力云图和应变值及卸载后板料的回弹结果,帮助我们更好的认识分析板料冲压成形以及回弹过程中物质内部的变化。
ANSYS/LS-DYNA是一个通用的显示非线性动力分析有限元程序,近年来开发的板料冲压成形数值模拟新功能,取得了很大成功。通过计算,可以观察板料冲压成形过程中的变形状态、应力状态和壁厚变化,了解可能出现的起皱和开裂现象。此外,ANSYS/LS-DYNA程序具有显式、隐式求解功能,用显式求解模拟动态成形过程,然后用隐式求解模拟线性回弹变形。这不仅能够模拟材料变形过程,而且也能较好地计算回弹现象,比较准确地得到材料最终成形状态。
关键词:板材冲压,回弹,非线性有限元分析,数值模拟
Sheet metal stamping and rebound finite element simulation analysis
Abstract
The rebound is inevitable common phenomenon in sheet metal forming process, a direct impact on the final shape to the dimensional accuracy of the stampings and parts. In this paper, the nonlinear dynamic finite element software ANSYS / LS-DYNA explicit, implicit sequential solution function to simulate thespringbackdeformation of the sheet after sheet metal stamping process and uninstall the whole process, forming process at any time throughout the Von-Misesstress cloud and strain and after unloading sheetspringbackresults, help us to a better understanding analysis sheet metal stamping and rebound process material internal changes.
2.2 有限元法
在拉格朗日坐标系中,对应于某一瞬时t,具有总体积V,内作用面 ,位移边界 与外力边界 的相互作用系统应满足虚功原理,即
式中 是密度; 是位置坐标; 是加速度; 和 分别为虚位移及其导数的增量; 和 是体积力与面力。
将体积离散化为n个单元,为了保持4面体单元的抗畸变能力,同时又使计算精度得以保证在4节点4面体单元的基础上,建立了8节点6面体超级单元。每个单元的节点数为8,位置坐标 可用形函数 与节点位置 的插值表示为
4.1 板料变形分析
图4-1板料变形图和图4-2位移矢量的等值线图为时间t=0.01s板料的变形程度,从图中可以清楚的知道在冲压过程结束后,板料的下部变形程度最大。
在板料上可能与模具曲率变化较大的区域相接触的部位也应细化板料网格。则板料网格划分中存在网格密度分布问题。在板料冲压成形及回弹过程中,板料会发生大位移、大转动和大变形,在冲压成形前预先确定扳料上的网格密度分布情况是非常困难的。目前有限元软件中采用自适应网格划分技术解决此问题。所谓自适应网格划分。是指板料在接触过程中遇到变形较剧烈的部位自动进行局部区域的网格细化,以提高有限元在这些部位的计算准确度.网格划分如图3-4所示。
式中 为当前的切向刚度矩阵; 为位移纠正向量; 为外力向量; 为内力向量。
经Newton-Raphson迭代计算后的位移增越为:
算法中的要点如下:
l)对于每一个加载增量都要进行迭代,直至收敛为止。
2)每一节点都要达到力平衡和力矩平衡。
3)每一节点都要满足接触条件。
4)相对于位移增量来说,位移校正量是很小的。
图3-2SHELL163 单元几何图示
SOLID164是用于3维的显式结构实体单元,如图3-3所示,有8节点构成。节点在x、y、z方向的平移、速度和加速度的自由度。这个单元只用在动力显式分析,它支持所有的许可的非线性特性。
图3-3SOLID164 实体单元几何特征
3.3 网格划分
有限元网格的划分是数值模拟技术中的重要环节,网格划分是否合理在一定程度上会影响到计算精度和计算时间。在网格划分过程中,网格的形状、尺寸和位置都是需要考虑的问题。对于板料冲压成形回弹问题,坯料是典型的大变形构件,又是成形分析过程中的从接触面,因此必须采用比摸具单元较精细的网格模型,单元的形状尽量采用四边形或者六面体。而对于模具,因在分析过程中认为是刚性体,若形状较简单,可不划分单元直接采用其解析刚性面进行分析,若模具形状较为复杂,因对其进行网格划分,在模具圆角及形状变化较大的区域采用较密的网格,以保证精确的描述模具型面的几何形状.
2 基本原理
2.1 弹塑性材料的应力应变关系
板料冲压成形属于弹塑性大变形行为,弹塑性材料进入塑性后应力应变不再存在唯一的线性对应关系每一时刻的应力~应变状态都是此前的加载路径和应变状态综合作用的结果应引入增量理论。本文采用Mises屈服准则即
式中 是材料单轴应力状态时的屈服应力; 是应力偏张量, 。假设材料发生的是各向同性强化后续屈服函数应为 ,即
形函数 定义为
式中 , 与 是单元局部坐标,t是时间变量。
完整的回弹数值模拟分为2步:冲头落下板料成形的过程模拟和去除冲头等工具板料回弹的过程模拟。前1步计算是回弹过程模拟的基础,为其提供应力、应变等数据,该步计算的准确与否将直接影响回弹计算的精度,2步计算可分别采用不同的算法。
数值模拟主要有2种算法:静力隐式算法和动力显式算法。2种算法的区别在于静力隐式算法需要构造和求解刚度矩阵,每一步迭代都要进行接触判断,往往会出现迭代不收敛的情况,计算速度慢,但计算精度高;而动力显示算法不需要构造和求解刚度矩阵,因此该算法的最大优势是计算速度快。实践证明:动力显式算法计算的应力是不准确的,而残余应力恰恰是造成回弹现象的关键所在,因此认为在回弹模拟的第1步采用动力显式算法是不合适的。虽然动力显式算法在计算以接触为主的问题时速度相当快,但是当用于不存在接触并且以低频率方式变形的柔性结构时(最典型的是回弹模拟的第2步计算),为保证算法的稳定性,分析时间常常比模拟成形过程所要的时间还要长。质量加大技术虽然可以加速成形模拟过程,但它对回弹第2步计算是毫无帮助的,因为加大质量的同时也加大了达到静平衡的时间。为预测回弹后零件的形状,大部分学者建议采用静力隐式方法。
本次分析选用单元类型是:板料模型采用显式壳单元SHELL163,且使用能容忍弯曲能力的Belytschko-Wong-Chiang算法;凸、凹摸则采用SOLID164体单元。
SHELL163 是一个4节点显示结构薄壳单元,如图3-2所示,有弯曲和膜特征。可加平面和法向载荷。单元在每个节点上有12个自由度: 在节点x,y,和z方向的平动,加速度,速度和绕x,y,和z轴的转动。该单元只用于显示动力学分析所有非线性特性.
Keywords: sheet metal stamping, rebound, nonlinear finite element analysis, numerical simulation
1 引言
金属板料冲压成形是压力加工的重要组成部分,薄板金属在压力作用下由模具引导成形的过程是一个十分复杂的物理过程,由于模具几何结构尺寸、接触摩擦和压边力等因素的影响,在金属的成形过程中常发生起皱现象。为了得到高质量的钣金产品,必须克服和抑制成形过程中起皱的发生和发展。过去人们常常采用试错的方法,但这种单凭设计人员经验的方法在很大程度上带有盲目性,在面对复杂零件或新产品时往往无法解决。
图 3-4网格划分
3.4施加边界条件
凸模和凹模与板材的接触都采用面—面接触方式,并选择自动接触类型,摩擦系数取0.1。 有限元数值模拟时要尽量反映成型过程中的真实工艺情况,有了真实有效的工艺参数才能保证数值模拟结果的正确,按照实际加工时的参数来设定凸模的速度,求解时间为0.01秒,输出步数为100。
应力连续增长到超过弹性极限 ,其相应的应变为 ,然后下降到 ,其相应的应变为 。如在卸载的过程中,应力改变为 ,应变改变量为 ,则卸载后的应力与应变应等于卸载前的应力与应变分别减去它们的改变量,即
因为卸载是服从弹性规律的,所以上面式中的 和 是呈线性关系的,即 。式中,E为弹性模量。由此可以看出,在全部卸载后,即外载荷等于零的情况下,在物体内不仅会留下残余变形,而且有残余应力。
式中 为现时的后续屈服应力。增量理论中,塑性流动法则为
式中 是塑性应变增量; 为瞬时的非负比例系数,具体数值与材料硬化法则有关,与Mises屈服条件相关联的流动法则为 ,于是有
在金属成形过程中,回弹被定义为变形部件(板料)离开模具后的空间变化。板料冲压成形后的全应变包括弹性应变和塑性应变两部分,即
式中, 为弹性应变; 为塑性应变。在卸载过程中,只有弹性变形得到恢复,而塑性变形保持不变,并且卸载过程服从线性关系。
4 数值模拟结果与分析
计算完成后通过ANSYS后处理器POST1与POST26对结果进行后处理。首先先检验结果的有效性,一般来说,沙漏能量(hourglass energy)不超过内能(internal energy)的10%即被认为是可以接受的分析结果。本次分析的沙漏能为零,因此数值模拟分析的过程是可靠的。