集成电路制造工艺流程之详细解答
集成电路制造工艺流程
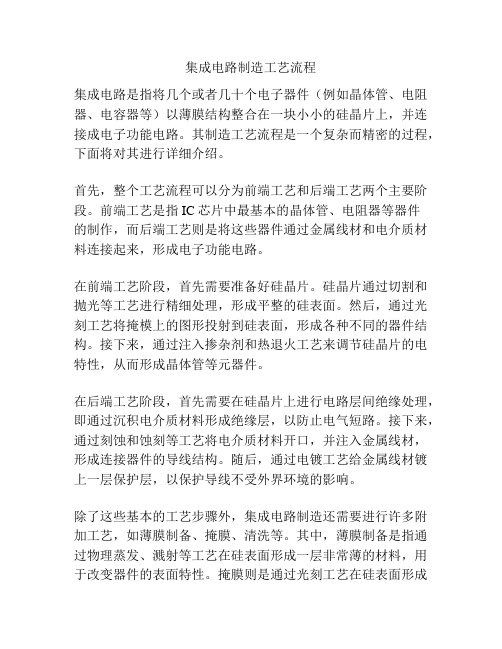
集成电路制造工艺流程集成电路是指将几个或者几十个电子器件(例如晶体管、电阻器、电容器等)以薄膜结构整合在一块小小的硅晶片上,并连接成电子功能电路。
其制造工艺流程是一个复杂而精密的过程,下面将对其进行详细介绍。
首先,整个工艺流程可以分为前端工艺和后端工艺两个主要阶段。
前端工艺是指IC芯片中最基本的晶体管、电阻器等器件的制作,而后端工艺则是将这些器件通过金属线材和电介质材料连接起来,形成电子功能电路。
在前端工艺阶段,首先需要准备好硅晶片。
硅晶片通过切割和抛光等工艺进行精细处理,形成平整的硅表面。
然后,通过光刻工艺将掩模上的图形投射到硅表面,形成各种不同的器件结构。
接下来,通过注入掺杂剂和热退火工艺来调节硅晶片的电特性,从而形成晶体管等元器件。
在后端工艺阶段,首先需要在硅晶片上进行电路层间绝缘处理,即通过沉积电介质材料形成绝缘层,以防止电气短路。
接下来,通过刻蚀和蚀刻等工艺将电介质材料开口,并注入金属线材,形成连接器件的导线结构。
随后,通过电镀工艺给金属线材镀上一层保护层,以保护导线不受外界环境的影响。
除了这些基本的工艺步骤外,集成电路制造还需要进行许多附加工艺,如薄膜制备、掩膜、清洗等。
其中,薄膜制备是指通过物理蒸发、溅射等工艺在硅表面形成一层非常薄的材料,用于改变器件的表面特性。
掩膜则是通过光刻工艺在硅表面形成一层光刻胶,以便进行后续的刻蚀工艺。
清洗则是在集成电路制造过程中,通过溶液等方法将硅表面的杂质去除,以保证器件的电特性。
在整个制造工艺的过程中,需要严格控制各个工艺步骤的条件和参数,以确保最终制得的集成电路具有良好的性能和稳定性。
诸如工艺参数、工艺流程等的微小变化都可能影响到整个工艺的成功与否。
综上所述,集成电路的制造工艺流程是一个复杂而精密的过程,涉及到多个工艺步骤和参数的控制。
通过前端工艺和后端工艺的协同作用,可以将晶体管、电阻器等元器件整合在一片硅晶片上,并形成电子功能电路。
这些制备出的集成电路,被广泛应用于计算机、通信、嵌入式等各个领域,推动了现代科技的发展。
集成电路的制造工艺流程

集成电路的制造工艺流程集成电路制造工艺流程是指将电子器件的元件和电路按照一定的规则和方法集成在半导体晶片上的过程。
制造工艺流程涉及到多个环节,如晶圆加工、电路图形绘制、光刻、腐蚀、沉积、复合、切割等。
下面将详细介绍集成电路的制造工艺流程。
首先,制造集成电路的第一步是选择合适的基片材料。
常用的基片材料有硅、蓝宝石和石英等。
其中,硅基片是最常用的基片材料,因为硅具有良好的热导性能和机械性能,同时也便于进行光刻和腐蚀等工艺步骤。
接下来,对基片进行晶圆加工。
晶圆加工是指将基片切割成薄片,并对其进行去杂质处理。
这一步骤非常关键,因为只有获得高质量的基片才能保证电路的性能和可靠性。
然后,根据电路设计图纸,使用光刻技术将电路图形绘制在基片上。
光刻技术是一种重要的制造工艺,主要利用分光光源、透镜和光刻胶等材料来实现。
通过光刻,可以将电路的结构图案转移到基片表面,形成精确的电路结构。
接着,进行腐蚀处理。
腐蚀是将未被光刻阻挡住的区域去除,使得电路结果清晰可见。
常用的腐蚀液有氟化氢、硝酸等。
腐蚀过程中需要严格控制时间和温度,以防止过腐蚀或不足腐蚀。
接下来,进行沉积工艺。
沉积是指利用化学反应或物理过程将金属、氧化物等材料沉积在基片表面。
沉积技术包括物理气相沉积(PVD)和化学气相沉积(CVD)等。
沉积工艺可以形成导体、绝缘体和介质等层,以实现电路的功能。
在进行复合工艺之前,还需要对电路进行电性能测试。
通过测试,可以检测电路是否存在故障和缺陷,并对其进行修复或更换。
最后一步是切割。
切割是将晶片切割成小片,以供后续封装和测试使用。
常用的切割工艺有晶圆锯切和激光切割等。
综上所述,集成电路的制造工艺流程包括基片材料选择、晶圆加工、电路图形绘制、光刻、腐蚀、沉积、复合和切割等环节。
每个环节都非常关键,需要严格控制各项参数和步骤,以保证最终产品的质量和性能。
集成电路制造的五个步骤

集成电路制造的五个步骤一、晶圆制备晶圆制备是集成电路制造的第一步,也是最基础的一步。
晶圆是以硅或其他半导体材料为基底的圆片,其表面经过一系列的加工和处理后,成为集成电路的基础。
晶圆制备包括以下几个步骤:1. 材料选择:选择合适的半导体材料,如硅、砷化镓等,并进行纯化处理,以确保材料的纯度达到要求。
2. 晶体生长:将纯化后的材料以一定的温度和压力条件下,通过化学气相沉积或其他方法生长成大尺寸的晶体。
3. 切割晶圆:将生长好的晶体切割成薄片,即晶圆,并对其进行抛光,以达到一定的表面光洁度。
4. 清洗处理:对切割好的晶圆进行酸洗、去胶等处理,以去除表面的杂质和污染物。
二、光罩制作光罩制作是指根据集成电路设计图纸制作光罩,光罩是将电路图案投射到晶圆上的工具。
光罩制作包括以下几个步骤:1. 设计电路图:根据集成电路的功能需求,设计电路图,包括电路结构、电路元件等。
2. 布图:将设计好的电路图进行布图,确定电路中各个元件的位置和连线方式。
3. 制作掩膜:根据布图结果,将电路图案绘制到光罩上,形成掩膜。
4. 检验和修复:对制作好的光罩进行检验,确保电路图案的准确性和完整性;如有问题,需要进行修复。
三、曝光和刻蚀曝光和刻蚀是将光罩上的电路图案投射到晶圆上的关键步骤,也是制造集成电路中最核心的步骤之一。
曝光和刻蚀包括以下几个步骤:1. 涂覆光刻胶:将晶圆表面涂覆一层光刻胶,以形成感光层。
2. 曝光:将光罩上的电路图案通过曝光机投射到涂覆有光刻胶的晶圆上,形成图案的暴露区域。
3. 显影:将曝光后的晶圆放入显影液中,使光刻胶在暴露区域溶解,形成图案。
4. 刻蚀:将显影后的晶圆放入刻蚀机中,去除暴露区域的材料,形成电路图案。
四、沉积和蚀刻沉积和蚀刻是集成电路制造中的关键步骤之一,用于在晶圆上沉积或去除特定材料,以形成电路的结构和连接。
沉积和蚀刻包括以下几个步骤:1. 沉积:通过化学气相沉积或物理气相沉积等方法,在晶圆表面沉积一层薄膜,如金属、氧化物等。
集成电路制造过程

集成电路制造过程一、概述集成电路(Integrated Circuit,简称 IC)是一种由多个电子元件组成的小型微电子元件,它是将大量的电子元件(如晶体管、电阻、电容、二极管等)封装在单片封装形式上,从而有效地提高了电子元件的封装密度和可靠性,并把它们结合成一个可以用来miniaturizes 电路和功能的多元件半导体器件。
集成电路的整体制造过程,从原材料的提取、加工、晶圆制作、晶圆处理、晶圆分选、集成线路设计、封装测试、封装装配到晶圆复位等,涉及到多个工艺步骤,现将制作过程做如下总结:二、集成电路制作过程1、原材料采集集成电路的制作是从半导体材料的采集开始的,原始材料包括硅,金,铝等元素,经过精细的加工处理,最后采用特定的化学反应生成的硅锗晶体母材就可以用来制造集成电路了。
2、晶圆制作晶圆制作是整个生产过程中最重要的一步,在这一步骤的基础上,包括最小的元件下至最复杂的微电子电路元件的制作都是围绕着晶圆进行的。
晶圆制作的具体流程,是将晶圆母材经过一系列的工艺处理,如:分割、表面腐蚀、去除表面缺陷、晶圆发光检测、表面抛光,最终形成一块晶圆,然后将线路图输入到光刻机中,通过光刻机将线路图转换成晶圆表面上的线路模式,然后将晶圆放置到硅片上,最后形成规则分布的晶圆硅片即基板,用以制作集成电路。
3、晶圆处理晶圆处理是基于晶圆制作的基础上,通过金属化学气相沉积(MOCVD)、光刻、固定,将硅表面上形成的线路模式变成真正可以工作的三极管、晶体管、门电路、电容、电阻等微电子电路元件,最终得到一块上好的整体晶圆。
4、晶圆分选晶圆分选是整个集成电路制造过程中十分重要的一步。
在这一步中,用一系列的测试工具和测试设备,对晶圆表面上的电路元件进行功能测试,根据测试结果将其分类,最终将全部优良的晶圆留存,不合格的晶圆经过改正调整或归类报废。
5、集成线路设计集成线路设计是一个较为复杂的工作。
在这一过程中,经过一系列的数据分析、理论计算,以及原型示波器实验,最终将集成电路的线路结构设计好,并存储到计算机中,用以验证工程师的设计思路正确性和可行性。
集成电路制造工艺流程
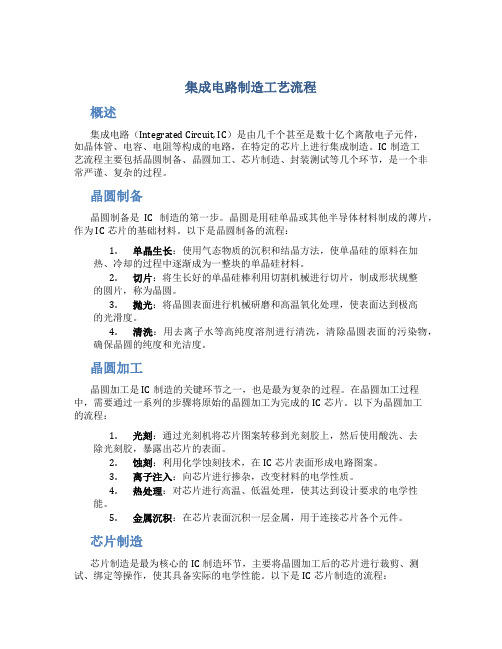
集成电路制造工艺流程概述集成电路(Integrated Circuit, IC)是由几千个甚至是数十亿个离散电子元件,如晶体管、电容、电阻等构成的电路,在特定的芯片上进行集成制造。
IC制造工艺流程主要包括晶圆制备、晶圆加工、芯片制造、封装测试等几个环节,是一个非常严谨、复杂的过程。
晶圆制备晶圆制备是IC制造的第一步。
晶圆是用硅单晶或其他半导体材料制成的薄片,作为IC芯片的基础材料。
以下是晶圆制备的流程:1.单晶生长:使用气态物质的沉积和结晶方法,使单晶硅的原料在加热、冷却的过程中逐渐成为一整块的单晶硅材料。
2.切片:将生长好的单晶硅棒利用切割机械进行切片,制成形状规整的圆片,称为晶圆。
3.抛光:将晶圆表面进行机械研磨和高温氧化处理,使表面达到极高的光滑度。
4.清洗:用去离子水等高纯度溶剂进行清洗,清除晶圆表面的污染物,确保晶圆的纯度和光洁度。
晶圆加工晶圆加工是IC制造的关键环节之一,也是最为复杂的过程。
在晶圆加工过程中,需要通过一系列的步骤将原始的晶圆加工为完成的IC芯片。
以下为晶圆加工的流程:1.光刻:通过光刻机将芯片图案转移到光刻胶上,然后使用酸洗、去除光刻胶,暴露出芯片的表面。
2.蚀刻:利用化学蚀刻技术,在IC芯片表面形成电路图案。
3.离子注入:向芯片进行掺杂,改变材料的电学性质。
4.热处理:对芯片进行高温、低温处理,使其达到设计要求的电学性能。
5.金属沉积:在芯片表面沉积一层金属,用于连接芯片各个元件。
芯片制造芯片制造是最为核心的IC制造环节,主要将晶圆加工后的芯片进行裁剪、测试、绑定等操作,使其具备实际的电学性能。
以下是IC芯片制造的流程:1.芯片测试:对芯片的性能进行测试,找出不合格的芯片并予以淘汰。
2.芯片切割:将晶圆上的芯片根据需求进行切割。
3.接线:在芯片表面安装金线,用于连接各个器件。
4.包装:将芯片放入封装盒中,并与引线焊接,形成成品IC芯片。
封装测试封装测试是IC制造的最后一步。
集成电路制造工艺流程介绍

集成电路制造工艺流程介绍1. 晶圆生长:制造过程的第一步是晶圆生长。
晶圆通常是由硅材料制成,通过化学气相沉积(CVD)或单晶硅引入熔融法来生长。
2. 晶圆清洗:晶圆表面需要进行清洗,以去除可能存在的污染物和杂质,以确保后续工艺步骤的成功进行。
3. 光刻:光刻是制造过程中非常关键的一步。
在光刻过程中,先将一层光刻胶涂覆在晶圆表面,然后使用光刻机将芯片的设计图案投影在晶圆上。
接着,进行光刻胶显影,将未受光的部分去除,留下所需的图案。
4. 沉积:接下来是沉积步骤,通过CVD或物理气相沉积(PVD)将金属、氧化物或多晶硅等材料沉积在晶圆表面上,以形成导线、电极或其他部件。
5. 刻蚀:对沉积的材料进行刻蚀,将不需要的部分去除,只留下所需的图案。
6. 接触孔开孔:在晶圆上钻孔,形成电极和导线之间的接触孔,以便进行电连接。
7. 清洗和检验:最后,对晶圆进行再次清洗,以去除可能残留的污染物。
同时进行严格的检验和测试,确保芯片质量符合要求。
以上是一个典型的集成电路制造工艺流程的简要介绍,实际的制造过程可能还包括许多其他细节和步骤,但总的来说,集成电路制造是一个综合了多种工艺和技术的高精度制造过程。
集成电路(Integrated Circuit,IC)制造是一项非常复杂的工艺,涉及到材料科学、化学、物理、工程学和电子学等多个领域的知识。
在这个过程中,每一个步骤都至关重要,任何一个环节出错都可能导致整个芯片的质量不达标甚至无法正常工作。
以下将深入介绍集成电路的制造工艺流程及相关的技术细节。
8. 电镀:在一些特定的工艺步骤中,需要使用电镀技术来给芯片的表面涂覆一层导电材料,如金、铜或锡等。
这些导电层对于芯片的整体性能和稳定性非常重要。
9. 封装:制造芯片后,需要封装芯片,以保护芯片不受外部环境的影响。
封装通常包括把芯片封装在塑料、陶瓷或金属外壳内,并且接上金线用以连接外部电路。
10. 测试:芯片制造完成后,需要进行严格的测试。
集成电路的制造工艺与特点

集成电路的制造工艺与特点集成电路(Integrated Circuit,简称IC)是现代电子技术的核心和基础,广泛应用于各个领域。
制造一颗集成电路需要经历多道复杂的工艺流程,下面将详细介绍集成电路的制造工艺与特点。
一、制造工艺步骤:1.掺杂:首先,将硅片(制造IC的基础材料)通过掺杂工艺,添加特定的杂质元素,如硼、磷等。
掺杂过程中,杂质元素会改变硅片的电学性质,形成P型或N 型半导体材料。
2.沉积:接下来,将制造IC所需的氧化层或其他特殊材料沉积在硅片表面。
这些材料可以保护芯片,也可以作为电气隔离层或其他功能层。
3.光刻:在硅片上涂上光刻胶,并通过光刻机器曝光、显影、清洗等步骤,将设计好的电路图案转移到光刻胶上。
然后,根据光刻胶的图案,在硅片上进行蚀刻或沉积等处理。
4.蚀刻:利用蚀刻工艺,在未被光刻胶保护的区域上去除多余的材料。
蚀刻可以采用化学腐蚀或物理蚀刻等方法。
5.离子注入:通过离子注入工艺,将特定的杂质元素注入硅片中,以改变硅片的电学性质。
这个过程可以形成导线、二极管、晶体管等功能器件。
6.金属化:在硅片上涂上金属层,以形成电路的金属导线。
经过一系列的金属化工艺,如光刻、蚀刻等,可以形成复杂的电路连接。
7.封装:将完成的芯片连接到封装基板上,通过线缆与外部器件连接。
封装的目的是保护芯片,并提供外部电路与芯片之间的连接。
8.测试:对制造完成的芯片进行测试,以确保其性能和质量符合设计要求。
测试可以包括功能测试、可靠性测试等多个方面。
二、制造工艺特点:1.微小化:集成电路的制造工艺趋向于微小化,即将电路的尺寸缩小到纳米级别。
微小化可以提高电路的集成度,减小体积,提高性能,并降低功耗和成本。
2.精密性:制造集成电路需要高度精密的设备和工艺。
尺寸误差、浓度误差等都可能影响电路的功能和性能。
因此,工艺步骤需要严格控制,以确保芯片的准确性和一致性。
3.多工艺组合:集成电路的制造通常需要多种不同的工艺组合。
集成电路制造工艺流程介绍

集成电路制造工艺流程介绍引言集成电路制造是一项复杂且精细的工艺,它涉及到多个步骤和环节。
本文将介绍集成电路制造的工艺流程,从设计原型到最终产品的制造过程。
设计与验证在制造集成电路之前,首先需要进行电路的设计和验证。
1.电路设计:电路设计包括功能分析、电路拓扑设计、布局设计和布线设计等阶段。
这些设计阶段要求工程师使用专业的电路设计工具,如Cadence、Mentor Graphics等软件。
2.电路验证:电路设计完成后,需要通过电路仿真等方法进行验证。
这样可以确保电路在实际运行中的性能符合预期。
掩膜制作在完成电路设计和验证之后,需要开始制作掩膜。
掩膜制作是整个集成电路制造过程中的核心环节。
1.光刻:在掩膜制作中,首先需要使用光刻机将电路设计图案投射到硅片上。
这一步骤利用了光刻胶和硅片上的光刻层,形成了电路的图案。
2.蚀刻:蚀刻是将暴露在硅片表面的图案转移到硅片内部的过程。
通常使用等离子体蚀刻机进行蚀刻,该机器能够在硅片表面进行高精度的刻蚀,以形成电路的结构。
清洗与电镀掩膜制作完成后,需要对硅片进行清洗和电镀。
这些步骤旨在去除掉不需要的物质并增加必要的层。
1.清洗:清洗是将硅片表面的杂质和残留物去除的过程。
清洗通常使用化学溶液和超声波浴进行,以保证硅片的纯洁度。
2.电镀:电镀是给硅片表面增加一层金属的过程,以提供导电性和保护性。
常用的电镀材料包括铜、银和金等。
封装与测试在集成电路制造的最后阶段,需要将芯片进行封装,并进行测试。
1.芯片封装:芯片封装是将芯片与封装材料进行结合的过程,以提供保护和连接功能。
芯片封装通常使用塑料封装、金线封装或球栅阵列封装等技术。
2.芯片测试:芯片测试是在封装完成后对芯片进行功能和性能测试的过程。
测试通常包括逻辑测试、功能测试和可靠性测试等。
结论整个集成电路制造工艺流程涵盖了电路设计、验证、掩膜制作、清洗与电镀、封装与测试等多个环节。
每个环节都需要精细的操作和严格的控制,以确保最终产品的质量和性能。
- 1、下载文档前请自行甄别文档内容的完整性,平台不提供额外的编辑、内容补充、找答案等附加服务。
- 2、"仅部分预览"的文档,不可在线预览部分如存在完整性等问题,可反馈申请退款(可完整预览的文档不适用该条件!)。
- 3、如文档侵犯您的权益,请联系客服反馈,我们会尽快为您处理(人工客服工作时间:9:00-18:30)。
集成电路制造工艺流程之详细解答
1.晶圆制造( 晶体生长-切片-边缘研磨-抛光-包裹-运输 )
晶体生长(Crystal Growth)
晶体生长需要高精度的自动化拉晶系统。
将石英矿石经由电弧炉提炼,盐酸氯化,并经蒸馏后,制成了高纯度的多晶硅,其纯度高达0.99999999999。
采用精炼石英矿而获得的多晶硅,加入少量的电活性“掺杂剂”,如砷、硼、磷或锑,一同放入位于高温炉中融解。
多晶硅块及掺杂剂融化以后,用一根长晶线缆作为籽晶,插入到融化的多晶硅中直至底部。
然后,旋转线缆并慢慢拉出,最后,再将其冷却结晶,就形成圆柱状的单晶硅晶棒,即硅棒。
此过程称为“长晶”。
硅棒一般长3英尺,直径有6英寸、8英寸、12英寸等不同尺寸。
硅晶棒再经过研磨、抛光和切片后,即成为制造集成电路的基本原料——晶圆。
切片(Slicing) /边缘研磨(Edge Grinding)/抛光(Surface Polishing)
切片是利用特殊的内圆刀片,将硅棒切成具有精确几何尺寸的薄晶圆。
然后,对晶圆表面和边缘进行抛光、研磨并清洗,将刚切割的晶圆的锐利边缘整成圆弧形,去除粗糙的划痕和杂质,就获得近乎完美的硅晶圆。
包裹(Wrapping)/运输(Shipping)
晶圆制造完成以后,还需要专业的设备对这些近乎完美的硅晶圆进行包裹和运输。
晶圆输送载体可为半导体制造商提供快速一致和可靠的晶圆取放,并提高生产力。
2.沉积
外延沉积 Epitaxial Deposition
在晶圆使用过程中,外延层是在半导体晶圆上沉积的第一层。
现代大多数外延生长沉积是在硅底层上利用低压化学气相沉积(LPCVD)方法生长硅薄膜。
外延层由超纯硅形成,是作为缓冲层阻止有害杂质进入硅衬底的。
采用。
9.晶圆检查Wafer Inspection (Particles)
在晶圆制造过程中很多步骤需要进行晶圆的污染微粒检查。
如裸晶圆检查、设备监控(利用工艺设备控制沉积到晶圆上的微粒尺寸),以及在CMP、CVD及离子注入之后的检查,通常这样的检查是在晶圆应用之前,或在一个涂光刻胶的层曝光之前,称之为无图形检查。
2.沉积
化学气相沉积 Chemical Vapor Deposition
化学气相沉积 (CVD) 是在晶圆表面通过分解气体分子沉积混合物的技术。
CVD会产生很多非等离子热中间物,一个共性的方面是这些中间物或先驱物都是气体。
有很多种CVD技术,如热CVD、等离子CVD、非等离子CVD、大气CVD、LPCVD、HDPCVD、LDPCVD、PECVD等,应用于半导体制造的不同方面。
3.光刻(Photolithography)
光刻是在晶圆上印制芯片电路图形的工艺,是集成电路制造的最关键步骤,在整个芯片的制造过程中约占据了整体制造成本的35%。
光刻也是决定了集成电路按照摩尔定律发展的一个重要原因,如果没有光刻技术的进步,集成电路就不可能从微米进入深亚微米再进入纳米时代。
光刻工艺将掩膜图形转移到晶片表面的光刻胶上,首先光刻胶处理设备把光刻胶旋涂到晶圆表面,再经过分步重复曝光和显影处理之后,在晶圆上形成需要的图形。
通常以一个制程所需要经过掩膜数量来表示这个制程的难易。
根据曝光方式不同,光刻可分为接触式、接近式和投影式;
根据光刻面数的不同,有单面对准光刻和双面对准光刻;
根据光刻胶类型不同,有薄胶光刻和厚胶光刻。
一般的光刻流程包括前处理、匀胶、前烘、对准曝光、显影、后烘,
可以根据实际情况调整流程中的操作。
4.刻蚀(Etching)
然后把此图形精确地转移到抗蚀剂下面的介质薄膜(如氧化硅、氮化硅、多晶硅)或金属薄膜上去,制造出所需的薄层图案。
刻蚀就是用化学的、物理的或同时使用化学和物理的方法,有选择地把没有被抗蚀剂掩蔽的那一部分薄膜层除去,从而在薄膜上得到和抗蚀剂膜上完全一致的图形。
等离子刻蚀(plasma etch)是在特定的条件下将反应气体电离形成等离子体,等离子体选择性地从晶圆上除去物质,剩下的物质在晶圆上形成芯片图形。
5.离子注入 Ion Implantation
晶圆衬底是纯硅材料,不导电或导电性极弱。
为了在芯片内具有导电性,必须在晶圆里掺入微量的不纯物质,通常是砷、硼、磷。
掺杂可以在扩散炉中进行,也可以采用离子注入实现。
一些先进的应用都是采用离子注入掺杂的。
离子注入有中电流离子注入、大电流/低能量离子注入、高能量离子注入三种,适于不同的应用需求。
6.热处理Thermal Processing
利用热能将物体内产生内应力的一些缺陷加以消除。
所施加的能量将增加晶格原子及缺陷在物体内的振动及扩散,使得原子的排列得以重整。
热处理是沉积制造工序后的一个工序,用来改变沉积薄膜的机械性能。
目前,热处理技术主要有两项应用:
一个使用超低k绝缘体来提升多孔薄膜的硬度,
另一个使用高强度氮化物来增加沉积薄膜的韧性抗张力,以提升器件性能。
在紫外热处理反应器里,等离子增强化学气相沉积薄膜经过光和热的联合作用改变了膜的性能。
高强度氮化薄膜中紫外热处理工艺使连接重排,空间接触更好,产生出了提高器件性能所需的高强度水平。
2.沉积(蒸发、溅射)
物理气相沉积 Physical Vapor Deposition
晶圆上最常见的金属互连材料是Al,通常应用物理气相沉积(PVD)法制备金属材料薄膜。
PVD方法也用于沉积阻挡层和籽晶层,以及用于双嵌式互连的铜薄膜。
7.化学机械研磨 CMP
推动芯片技术向前发展的关键之一是每个芯片的层数在增加,一个芯片上堆叠的层数越来越多,而各层的平坦不均会增加光刻精细电路图像的困难。
CMP 系统是使用抛光垫和化学研磨剂选择性抛光沉积层使其平坦化。
CMP包括多晶硅金属介质(PMD) 平坦化、层间绝缘膜(ILD) 平坦化和钨平坦化。
CMP是铜镶嵌互连工艺中的关键技术。
8.晶圆检测 Wafer Metrology
在芯片制造过程中,为了保证晶圆按照预定的设计要求被加工必须进行大量的检测和量测,包括芯片上线宽度的测量、各层厚度的测量、各层表面形貌测量,以及各个层的一些电子性能的测量。
随着半导体工艺和制造技术的不断发展,这些检测已经成为提高量产和良率的不可缺少的部分。
在铜互连工艺中,由于采用更精细的线宽技术和低k介电材料,需要开发更精密的测试设备和新的测试方法。
检测主要包括三类:光学检测、薄膜检测、关键尺寸扫描电子检测(CD-SEM)。
晶圆检测的一个重要发展趋势是将多种测量方法融合于一个工艺设备中。
9.晶圆检查Wafer Inspection (Particles)
在晶圆制造过程中很多步骤需要进行晶圆的污染微粒检查。
如裸晶圆检查、设备监控(利用工艺设备控制沉积到晶圆上的微粒尺寸),以及在CMP、CVD及离子注入之后的检查,通常这样的检查是在晶圆应用之前,或在一个涂光刻胶的层曝光之前,称之为无图形检查。
10.晶圆探针测试(Wafer Probe Test)
晶圆探针测试是对制造完成的晶圆上的每个芯片(Die)进行针测,测试时,晶圆被固定在真空吸力的卡盘上,并与很薄的探针电测器对准,细如毛发的探针与芯片的每一个焊接点相接触。
在测试过程中,每一个芯片的电性能和电路机能都被检测到,不合格的晶粒会被标上记号,而后当芯片切割成独立的芯片颗粒时,标有记号的不合格芯片颗粒会被淘汰。
探针检测的相关数据,现在已经可以用来对晶圆制造中的良率提升提供帮助。
14.封装(Assembly & Packaging)
封装技术这几年发展非常快,这主要是因为(a)芯片的复杂程度越来越高:芯片中所含晶体管数量急剧增多,管脚也越来越多。
需要新的封装技术满足这些需求。
(b)电子产品小型化:现在的电子产品要求体积小,功能强大,功耗低,这也意味着对于丝焊要求更高,封装形式要适应这些变化。
晶圆上的芯片在这里被切割成单个芯片,然后进行封装,这样才能使芯片最终安放在PCB 板上。
这里需要用的设备包括晶圆切割机,粘片机(将芯片封装到引线框架中)、线焊机(负责将芯片和引线框架的连接,如金丝焊和铜丝焊)等。
在引线键合工艺中使用不同类型的引线:金(Au)、铝(Al)、铜(Cu),每一种材料都有其优点和缺点,通过不同的方法来键合。
随着多层封装乃至3D封装的应用的出现,超薄晶圆的需求也在不断增强。
15.成品检测(Final Test)
因为最终的芯片良率不可能达到100%,芯片的检测就变得尤为重要。
如何检测出性能高的芯片,如何快速进行检测,考虑到每片芯片都要进行检测,晶圆厂就必须全盘平衡成本,这催生了检测功能更为强大、成本更为低廉、检测速度更快的新一代检测设备。
11111111111111111111111111111111111111111111111111111111111111111111111111111 1111111111111111111111111111111111111111111111
1111111111111111111111111111111111111111111111
111111111111111111111111111111111
111111111111111111111111111111111
1111111111111111111111111111111。