汽轮机转子输出端和联轴器的设计探讨 李光磊
汽轮发电机带有交替径向风道的转子流体与传热耦合分析
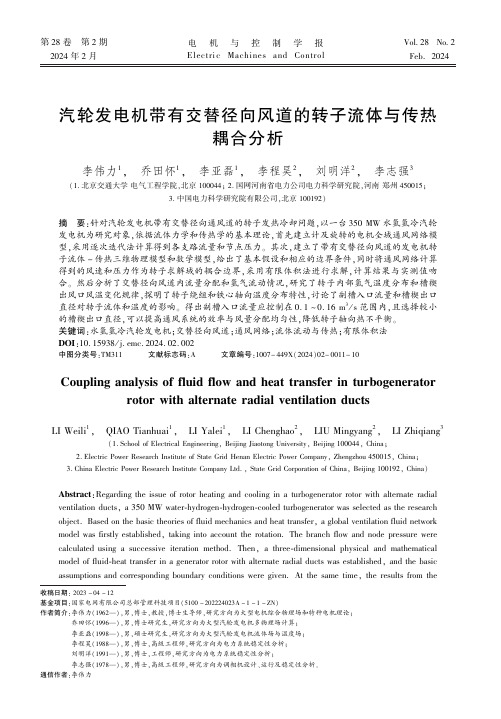
第28卷㊀第2期2024年2月㊀电㊀机㊀与㊀控㊀制㊀学㊀报Electri c ㊀Machines ㊀and ㊀Control㊀Vol.28No.2Feb.2024㊀㊀㊀㊀㊀㊀汽轮发电机带有交替径向风道的转子流体与传热耦合分析李伟力1,㊀乔田怀1,㊀李亚磊1,㊀李程昊2,㊀刘明洋2,㊀李志强3(1.北京交通大学电气工程学院,北京100044;2.国网河南省电力公司电力科学研究院,河南郑州450015;3.中国电力科学研究院有限公司,北京100192)摘㊀要:针对汽轮发电机带有交替径向通风道的转子发热冷却问题,以一台350MW 水氢氢冷汽轮发电机为研究对象,依据流体力学和传热学的基本理论,首先建立计及旋转的电机全域通风网络模型,采用逐次迭代法计算得到各支路流量和节点压力㊂其次,建立了带有交替径向风道的发电机转子流体-传热三维物理模型和数学模型,给出了基本假设和相应的边界条件,同时将通风网络计算得到的风速和压力作为转子求解域的耦合边界,采用有限体积法进行求解,计算结果与实测值吻合㊂然后分析了交替径向风道内流量分配和氢气流动情况,研究了转子内部氢气温度分布和槽楔出风口风温变化规律,探明了转子绕组和铁心轴向温度分布特性,讨论了副槽入口流量和槽楔出口直径对转子流体和温度的影响㊂得出副槽入口流量应控制在0.1~0.16m 3/s 范围内,且选择较小的槽楔出口直径,可以提高通风系统的效率与风量分配均匀性,降低转子轴向热不平衡㊂关键词:水氢氢冷汽轮发电机;交替径向风道;通风网络;流体流动与传热;有限体积法DOI :10.15938/j.emc.2024.02.002中图分类号:TM311文献标志码:A文章编号:1007-449X(2024)02-0011-10㊀㊀㊀㊀㊀㊀㊀㊀㊀㊀㊀㊀㊀㊀㊀㊀㊀㊀㊀㊀㊀㊀㊀㊀㊀㊀㊀㊀㊀㊀㊀㊀㊀㊀㊀㊀㊀㊀㊀㊀㊀㊀㊀㊀㊀㊀㊀㊀㊀㊀㊀㊀㊀㊀㊀㊀㊀㊀㊀㊀㊀㊀㊀㊀㊀㊀㊀㊀㊀㊀㊀㊀㊀㊀㊀㊀㊀㊀㊀㊀㊀㊀㊀㊀㊀㊀㊀㊀㊀㊀㊀㊀㊀㊀㊀㊀㊀㊀㊀㊀㊀㊀㊀㊀㊀㊀㊀㊀㊀㊀㊀㊀㊀㊀㊀㊀收稿日期:2023-04-12基金项目:国家电网有限公司总部管理科技项目(5100-202224023A -1-1-ZN )作者简介:李伟力(1962 ),男,博士,教授,博士生导师,研究方向为大型电机综合物理场和特种电机理论;乔田怀(1996 ),男,博士研究生,研究方向为大型汽轮发电机多物理场计算;李亚磊(1998 ),男,硕士研究生,研究方向为大型汽轮发电机流体场与温度场;李程昊(1988 ),男,博士,高级工程师,研究方向为电力系统稳定性分析;刘明洋(1991 ),男,博士,工程师,研究方向为电力系统稳定性分析;李志强(1978 ),男,博士,高级工程师,研究方向为调相机设计㊁运行及稳定性分析㊂通信作者:李伟力Coupling analysis of fluid flow and heat transfer in turbogeneratorrotor with alternate radial ventilation ductsLI Weili 1,㊀QIAO Tianhuai 1,㊀LI Yalei 1,㊀LI Chenghao 2,㊀LIU Mingyang 2,㊀LI Zhiqiang 3(1.School of Electrical Engineering,Beijing Jiaotong University,Beijing 100044,China;2.Electric Power Research Institute of State Grid Henan Electric Power Company,Zhengzhou 450015,China;3.China Electric Power Research Institute Company Ltd.,State Grid Corporation of China,Beijing 100192,China)Abstract :Regarding the issue of rotor heating and cooling in a turbogenerator rotor with alternate radial ventilation ducts,a 350MW water-hydrogen-hydrogen-cooled turbogenerator was selected as the research object.Based on the basic theories of fluid mechanics and heat transfer,a global ventilation fluid network model was firstly established,taking into account the rotation.The branch flow and node pressure were calculated using a successive iteration method.Then,a three-dimensional physical and mathematical model of fluid-heat transfer in a generator rotor with alternate radial ducts was established,and the basic assumptions and corresponding boundary conditions were given.At the same time,the results from theventilation network were used as the coupling boundary of the rotor solution domain,and the finite volume method was used for coupling calculation.The calculated results match well with the measured values. Then,the flow distribution and hydrogen flow in the alternate radial ducts were analyzed,and the hydro-gen temperature distribution inside the rotor and the temperature variation at the slot wedge outlet were studied.The axial temperature distribution characteristics of the rotor winding and iron core were ex-plored.Furthermore,the effects of the inlet flow rate of the sub-slot and the outlet diameter on the rotor fluid and temperature were discussed.The inlet flow rate of the sub-slot should be controlled within the range of0.1m3/s-0.16m3/s,and a smaller slot wedge outlet diameter should be selected to improve the efficiency of the ventilation system and the uniformity of air volume distribution,and reduce the axial thermal imbalance.Keywords:water-hydrogen-hydrogen-cooled turbogenerator;alternate radial ducts;ventilation fluid net-work;fluid flow and heat transfer;finite volume method0㊀引㊀言大型汽轮发电机在运行中由于转子匝间发生绝缘故障引起发电机转子匝间短路问题时有发生,危及电机运行安全[1-2]㊂转子通风系统作为发电机重要通风系统组成部分,它的风路设计的合理性以及氢气流动规律是设计和运维人员非常关心的问题之一㊂同时,转子内部氢气流动状态不仅影响转子体温度分布,而且影响轴向转子铜排的热应力分布㊂转子铜排和匝间绝缘因热膨胀系数的不同,会导致绝缘在热应力的作用下失效,导致发电机出现故障㊂因此,研究发电机转子温度分布,是非常重要的㊂国内外专家学者对大型汽轮发电机的通风系统和定㊁转子温度场进行了许多研究㊂国外M.Fuku-shima等[3]根据流体相似理论对一台300MW空冷汽轮发电机的风路进行建模与计算,得到了各节点压力值和各支路流量值㊂G.Traxler-Samerk等[4]利用通风网络和等效热网络耦合的方法对一台315MW发电机关键构件温度进行了计算㊂国内李伟力教授等[5]采用流体网络法对一台330MW水氢氢冷汽轮发电机的通风系统模型进行了计算,分析了各支路流量分布情况㊂以上基于 路 的方法具有计算速度快㊁参数可变的优点,其精度依赖于节点数量㊂为了提高计算准确度,学者们普遍采用有限体积法对汽轮发电机的定㊁转子温度场进行研究㊂文献[6-7]采用有限体积法分别研究了空冷汽轮发电机定子径向通风沟和定子端部的空气流动状态和温度分布规律㊂李俊卿等采用一种混合单元的网格划分[8],研究了水路堵塞对定子流体场和温度场的影响[9-10]㊂路义萍等人对双径向直风道的空冷汽轮发电机转子流体场和温度场进行了全面的研究,采用有限体积法计算了转子的二维温度场[11];分析了变结构和副槽入口风速变化等对内部风道流量分配的影响[12];探明了副槽形状变化㊁槽楔出口直径变化㊁通风沟数量变化对转子内部传热的影响机制[13]㊂以上基于 场 的计算方法可以获得较高的精度,但计算时间相对较长㊂目前大部分文献主要对水氢氢冷汽轮发电机定子温度场和空冷汽轮发电机带有双径向直风道的转子流体-温度场进行了较多的研究,而对水氢氢冷汽轮发电机的转子流体-传热耦合计算研究较少,尤其是对一种交替径向风道的转子热计算更是鲜有报道㊂此外,目前汽轮发电机转子流体-传热耦合计算大多采用场算的方法,其边界条件(如入口速度)的给定大多依赖于实测值,而这显然不是一种通用的方式㊂而且在发电机风路计算中,转子的旋转效应很少被考虑,这容易带来计算误差㊂针对上述问题,本文以一台350MW水氢氢冷汽轮发电机为研究对象,将场算与路算方式有机结合,提出以计及转子旋转的全域风路作为前置边界的发电机转子三维流体与传热场路耦合计算方法,对具有新型交替径向风道的转子进行流体-传热研究,旨在揭示转子内部氢气流动状态和关键部件温度分布规律㊂首先,根据电机通风系统特点与结构参数,建立计及旋转的全域通风流体网络,基于流体力学基本理论对其求解,结果作为转子计算模型的边界条件㊂其次,采用有限体积法对带有交替径向风道的转子模型进行流体-传热耦合计算,研究内部风道流量分配规律与流体速度分布情况,总结转子内部流体与固体关键截面温度变化,揭示副槽入21电㊀机㊀与㊀控㊀制㊀学㊀报㊀㊀㊀㊀㊀㊀㊀㊀㊀㊀㊀㊀㊀第28卷㊀口流量和槽楔出口直径变化对转子内流量分配和结构件温度的影响㊂最后,得出一些有益的结论,为该类型汽轮发电机转子结构设计与准确计算提供参考㊂1㊀计及旋转的汽轮发电机全域通风流体网络1.1㊀电机结构参数与通风系统本文所研究的350MW 水氢氢冷汽轮发电机主要结构参数如表1所示㊂采用密闭式定子全径向单路通风和转子副槽通风的冷却方式,由于发电机本体沿轴向呈对称结构,因此仅对轴向半个电机进行研究㊂其通风系统如图1所示,电机关键部件以及流体路径已重点标出㊂表1㊀350MW 水氢氢冷发电机主要结构参数Table 1㊀Parameters of a 350MW water-hydrogen-hydro-gen cooled turbo-generator㊀㊀发电机参数数值额定功率/MW 350额定电压/V 24000额定电流/A 9905.5额定频率/Hz 50额定励磁电流/A 2600定子内径/mm 1300铁心长度/mm 4600转子外径/mm 1100额定转速/(r /min)3000图1㊀350MW 水氢氢冷汽轮发电机通风系统示意图Fig.1㊀Ventilation system of a 350MW water-hydro-gen-hydrogen cooled turbo-generator冷却氢气经轴流式风扇加压后,分为三路进入发电机:1)一路流经发电机定子绕组端部区域,冷却发电机端部绕组和压指㊁压板㊁铜屏蔽等,进入发电机轭背部;2)一路进入发电机转子护环下通风道,一部分冷却转子端部绕组,另一部分进入转子副槽,经由转子绕组内部的径向通风沟对绕组进行冷却后,从转子槽楔的出风口流入气隙;3)一路直接进入气隙,与转子槽楔出来的氢气汇合,进入定子径向通风沟,流向定子轭背部,与定子端部区域的冷却氢气会合后共同进入氢冷却器,最后通过机壳通风道进入轴流式风扇,实现冷却氢气的流动循环㊂1.2㊀计及旋转的发电机全域通风网络为了简化计算,根据电机通风系统的特点,做出如下假设:1)发电机关于轴中心是对称的,因此仅建立半个电机的通风网络模型;2)认为电机内的冷却氢气处于连续㊁稳定的循环流动状态,流量和压力连续变化;3)认为电机内冷却氢气为不可压缩气体,忽略温度变化对氢气密度的影响,忽略氢气的重力㊂冷却气体在流经通风道时受到沿程阻力或局部阻力会产生压力损失,其表达式[5]为ΔH =ζ12ρv 2H =ζ(12ρQ 2S 2)=(ζρ2S2)Q 2=ZQ 2㊂(1)式中:ρ为冷却氢气密度;Q 为各支路的流量;S 为风道特征截面的面积;v H 为冷却氢气流速;Z 为各支路风阻;ζ为阻力系数㊂根据质量守恒定律,流入和流出通风网络中任一横截面的冷却氢气的流量应相同㊂因此对于网络中任何一个节点都应有ðQ m=0㊂(2)其中Q m 为与该节点相连各支路的冷却氢气流量㊂根据伯努利方程和能量守恒定律,对于通风网络中任一闭合回路,冷却氢气的流动压力变化总和为0,即ðH n=0㊂(3)其中H n 为第n 条闭合回路的冷却氢气压降㊂结合上述基本假设与流体力学基本理论,所建立的计及转子旋转的汽轮发电机(半个电机)通风网络模型如图2所示㊂通风网络模型中的风阻Z 1㊁Z 2㊁ ㊁Z 26与图1中的数字1㊁2㊁ ㊁26一一对应㊂Z 0㊁Z 1㊁Z 2为风扇前端的风阻;Z 3为轴流式风扇到护环前的风阻;Z 4为护环到气隙入口前的风阻;Z 5为气隙入口风阻;Z 6为气隙内沿程风阻;Z 7~Z 10为定子径向通风沟风阻;Z 11~Z 14为定子端部绕组风阻;Z 15~Z 17为定子压指间及压板风阻;Z 18~31第2期李伟力等:汽轮发电机带有交替径向风道的转子流体与传热耦合分析Z 20为定子铜屏蔽风阻;Z 21为风扇到转子护环下方风阻;Z 22为转子副槽入口风阻;Z 23~Z 24为转子径向通风沟风阻;Z 25为转子端部绕组风阻;Z 26为氢冷却器风阻㊂轴流式风扇旋转产生的压力用P f 来表示㊂转子旋转产生的离心压力也是冷却氢气流动的压力源之一,本文考虑了转子旋转带来的离心压升P r ,其表达式[14]为P r =12ρω2(R 22-R 21)㊂(4)其中:ω为电机转子角速度;R 2为转子外表面半径;R 1为转子径向通风沟底部半径㊂图2㊀汽轮发电机通风网络模型(半个电机)Fig.2㊀Ventilation network model of half a turbo-generator1.3㊀发电机通风网络计算结果根据式(1)~式(3),采用逐次迭代法对通风网络模型进行求解,得到了发电机内部关键区域流量分布,如表2所示㊂表2㊀汽轮发电机通风网络计算结果(半个电机)Table 2㊀Calculation results of ventilation network in ahalf turbo-generator单位:m 3/s㊀支路计算值总流量㊀18.986定子端部 2.817压指㊀㊀ 1.325铜屏蔽㊀ 1.492气隙入口11.68副槽入口 3.955转子端部绕组0.534从表2中可以看出,半个轴向段电机通风系统总体积风量为18.986m 3/s,实测值为18m 3/s,误差为5.47%,证明通风网络计算的准确性㊂定子端部支路流量占总流量的14.8%,其中压指和铜屏蔽的流量比较接近,这保证了电机端部结构件良好的通风以及风量分配的均匀性㊂气隙支路流量占总流量的61.5%,副槽支路流量占总流量的20.8%,转子端部绕组支路流量占总流量的2.8%㊂从整体来看,各支路风量分配较为合理㊂电机通风系统关键位置风压:风扇工作点压力P f 为15204Pa,转子旋转产生的离心压力P r 为3456Pa,转子槽楔出口压力为8028Pa㊂由副槽入口流量除以副槽截面积可以得到副槽入口的平均风速为107.5m /s,这将作为转子计算模型的边界条件㊂2㊀带有交替径向风道的转子流体流动与传热的物理模型和数学描述2.1㊀物理模型由于发电机转子通风系统关于轴向中心对称,因此为减少计算负担,仅对半轴长转子进行研究㊂汽轮发电机转子求解域如图3所示,为双半齿㊁一个整槽㊁半个轴向段的物理模型㊂转子的求解域分为固体域和流体域㊂固体域主要包括转子铁心㊁转子绕组㊁槽楔㊁楔下垫条㊁槽底垫条㊂流体域主要包括副槽通风道㊁槽底垫条通风道㊁转子绕组交替径向通风道㊁楔下垫条通风道和槽楔通风道㊂求解域边界包括转子副槽入口和52个转子槽楔出口(出口编号如图3所示)㊂图3㊀转子求解域物理模型Fig.3㊀Physical model of rotor solution domain与传统的转子双径向通风道结构不同,本文所研究的转子通风道为单径向风道与双径向风道交替排列的,称之为交替径向风道㊂由于采用了变支路数的结构,可以利用不稳定的热边界条件,提高匝导体对氢气的表面散热系数,增强转子匝导体的散热能力㊂2.2㊀数学模型由于转子交替径向通风道内的氢气随发电机作旋转运动,具有径向加速效果㊂本文采用以角速度Ω旋转的相对坐标系来代替静止的直角坐标系㊂在相对坐标系下,旋转的固体及其边界处于相对静止状态,转速为0㊂氢气的绝对速度矢量用u 表示,相41电㊀机㊀与㊀控㊀制㊀学㊀报㊀㊀㊀㊀㊀㊀㊀㊀㊀㊀㊀㊀㊀第28卷㊀对速度矢量用u r 表示㊂针对稳态流动,在相对坐标系中,列出质量守恒方程㊁动量守恒方程㊁能量守恒方程[15-17]分别为:▽(ρu r )=0;(5)▽(ρu r u r )+ρ(2Ωˑu r +ΩˑΩˑr )=-▽p +▽τ+F ;(6)▽(ρu T )=▽(Γgrad T )+S T ㊂(7)其中:▽表示散度,即▽(ρu r )=div(ρu r );Ω为旋转角速度矢量;r 为转动坐标系微元体的位置矢量;p 为作用于微元体上的静压力;τ为微元体表面的粘性应力;F 表示微元体上的体积力;ρ(2Ωˑu r +ΩˑΩˑr )为科里奥里力;Γ表示扩散系数㊂本文采用RNG k -ε模型模拟流体运动状态,可以更好地处理氢气流动高应变率及流线弯曲程度较大的流动,有利于提高运算精度㊂2.3㊀基本假设和边界条件计算过程中做出如下基本假设与设置:1)转子内氢气雷诺数较大(Re >2300),通风道内氢气处于湍流状态,因此用湍流模型进行计算;2)转子内氢气流速小于声速,即马赫数很小,故将氢气看作不可压缩气体;3)由于压力源较大,忽略电机内热氢气的浮力和重力对流体流动的影响;4)转子求解域内,转子绕组是主要的发热部件,转子绕组内热密为1751830W /m 3,计算过程中考虑了转子表面附加电场热损耗㊂经计算,电磁透入深度为5.6mm,热密值为1298787W /m 3;5)在计算过程中,认为材料物性参数不随温度变化㊂其中:匝间绝缘㊁主绝缘与楔下垫条㊁槽底垫条均为绝缘材料;槽楔材料为铝;绕组材料为铜㊂此处转子绕组匝间绝缘和绕组看作一体,采用等效导热系数进行等效处理㊂由于主绝缘厚度较小,对其建立物理模型会导致网格数量急剧增加,且计算难度变大㊂此处采用等效壁面的方式,忽略主绝缘的物理结构,保留其传热特性㊂下面求解域边界条件设置㊂在模型中,固体与固体㊁固体与流体的接触面均满足三维传热方程[18],即1r r λr r T r ()+1r 2rλθ T θ()+ r λz T z ()=-q +ρcTt㊂(8)式中:λr ㊁λθ㊁λz 分别为r ㊁θ㊁z 方向导热系数;q 为单位时间内单位体积发热量㊂由图3所示的求解域,可以确定如下边界条件:1)散热面㊂S 1为转子的一个端面,S 2为转子外表面,受到转子旋转或气隙内氢气运动的作用,S 1和S 2为散热面,满足:-λT nS 1,S 2=α(T -T f )㊂(9)式中:n 为边界法向量;λ为导热系数;α为散热系数;T f 为氢气温度㊂2)绝热面㊂S 5为转子铁心内圆表面,其与转轴之间的传热很小可被忽略,因此对其施加绝热边界条件为T nS 5=0㊂(10)3)周期性边界和对称边界㊂S 3和S 4为转子齿中心切面,根据周向结构周期对称性,设置为周期性边界;S 6为转子结构轴中心切面,根据轴向风路对称性,S 6设置为对称边界㊂4)与通风网络模型的耦合边界条件㊂发电机转子求解域的副槽入口为速度入口,槽楔出口设置为压力出口,对应速度值和压力值从通风网络模型计算所得,入口氢气温度设置为45ħ㊂3㊀计算结果与分析3.1㊀转子径向通风道内流量分布与速度分布沿着轴向从转子端部至转子中心处对径向通风道进行编号,分别为1,2,3, ,52㊂交替径向风道与传统双径向风道结构下各风道内质量流量分布结果如图4所示㊂图4㊀交替径向风道与传统双径向风道的质量流量分布Fig.4㊀Mass flow distribution in alternating radial ducts and traditional double radial ducts可以看出,对于交替径向风道,转子内部前3个51第2期李伟力等:汽轮发电机带有交替径向风道的转子流体与传热耦合分析径向风道的风量较大,且流量几乎相等,这主要是因为前3个风道的尺寸较大,进风量大㊂4号通风沟内流量急剧下降,从4号通风沟开始,沿轴向从端部区域到中心区域开始缓慢增加,且最大风量在靠近转子中心区域的径向风道内㊂这主要是因为4号通风沟通风面积小,且其对应位置的副槽风道内氢气流速较高,静压较小,导致进入风道内的流量较小,而后随着副槽内氢气流速的逐渐降低,各通风道内流量逐渐增加㊂此外,传统双径向风道的流量分布规律与交替径向风道基本一致,但是后者整体流量分布趋势更加平缓,这主要得益于变支路数的交替径向风道结构㊂为了分析交替径向风道内部氢气速度分布,选取1号㊁26号㊁52号通风道进行研究㊂采样截面以及3条通风道截面处x ㊁y ㊁z 三向速度分量分布如图5所示,其中:x 为周向;y 为轴向;z 为径向㊂图5㊀交替径向风道关键截面xyz 三向氢气速度分布Fig.5㊀Distribution of velocity components in key sections of hydrogen in alternating radial ducts61电㊀机㊀与㊀控㊀制㊀学㊀报㊀㊀㊀㊀㊀㊀㊀㊀㊀㊀㊀㊀㊀第28卷㊀㊀㊀在计算时考虑了转子旋转,随着氢气所在位置直径的增大,其旋转的线速度越大㊂由x 速度分布可知,随着径向高度的不断增加,v x 值不断增大,在转子槽楔出口处达到最大值,约为170m /s㊂由y 速度分布可知,靠近副槽入口处v y 值较大,约为100m /s,随着轴向长度的增加,v y 值逐渐减小㊂在交替径向风道内,v y 值均很小㊂由z 速度分布可知,由于转子高速旋转,在1号风道内左右两支路氢气速度分布不对称,在右侧支路出现v z 值小于0的情况,说明此处有氢气回流,而左侧支路回流现象不明显㊂在槽楔通风道内v z 值剧增,出口处v z 值约为75m /s㊂同时,转子的旋转也导致了副槽内氢气速度的不均匀分布,靠近风道左侧v z 值较大,右侧v z 值很小㊂综合上述分析可知,在副槽通风道内,v x 和v z 变化不大,v y 为主要变化量;在交替径向通风道内,v x 和v z 为主要变化量,v y 变化不大,其中受转子风道结构和旋转的影响,v z 在风道内分布不均匀,且有不同程度的回流现象,转子交替径向风道内氢气流动状态较为复杂㊂3.2㊀转子内部流体温度分布与出口风温变化仍然选取1号㊁26号㊁52号通风道,对其内部氢气温度分布进行研究㊂采样截面以及3条通风道截面处温度如图6所示㊂图6㊀交替径向风道内氢气关键截面温度分布Fig.6㊀Distribution of temperature in key sections of hydrogen in alternating radial ducts㊀㊀可以看出,随着径向高度的增加,3条通风道内氢气温度不断上升㊂这是因为冷氢气流经转子匝导体,不断吸热,导致气体温度升高㊂同时如图中虚线所示,1号交替径向风道下部的左㊁右支路氢气温度略有差异,这是由于转子高速旋转导致左右两支路氢气径向速度不同㊂而26号和52号交替径向风道内左右支路的氢气温度分布比较均匀㊂由于副槽内氢气不断流向转子中间位置,其与槽底垫条之间也有热交换,导致52号通风道副槽位置温度略高㊂图7为交替径向风道转子52个槽楔出口氢气的温度变化㊂可以看出,靠近端部的前3个风道出口的氢气温度较高,且由图4可知其出口流量也较大㊂这说明前3个风道内的冷却氢气带走了较多的热量,对于端部的散热有利㊂从4号至40号风道,出口风温缓慢下降,从70ħ降至65ħ,此时风道内流量的逐渐增加(见图4)是导致风温降低的主要因71第2期李伟力等:汽轮发电机带有交替径向风道的转子流体与传热耦合分析素㊂从41号至52号风道,出口风温又逐渐升高,从65ħ升至67.5ħ,虽然风道内流量还在缓慢增加,但是副槽内氢气在流动过程中不断吸热,自身温度逐渐升高,氢气风温成为主要因素,热交换变差,导致出口温度增大㊂图7㊀交替径向风道转子出风温度Fig.7㊀Hydrogen temperature of outlet in alternatingradial ducts3.3㊀转子绕组和铁心轴向温度分布图8所示为发电机转子绕组偏右侧截面A -Aᶄ和转子齿部截面B -Bᶄ的温度分布情况㊂可以看出,转子绕组靠近端部顶匝区域的温度较高,最热点温度约为120ħ㊂这是由于冷却氢气流经转子匝导体,不断吸热,在顶匝区域气体温度升高,导致热交换变差㊂除端部区域以外的转子绕组和转子铁心在轴向上温度分布比较均匀,各部分温差较小,这主要是由于交替径向风道结构使得各通风沟内流量分配相对均匀㊂在径向方向的转子绕组和铁心的温度梯度较大,尤其是靠近端部区域的温差较大,跨度分别为96~120ħ㊁46~90ħ㊂由于考虑了转子主绝缘的传热,主绝缘有一定的温度降,转子铁心截面温度低于转子绕组㊂转子绕组平均温升计算值为51.3ħ,在额定状态下采用电阻法得到的实测值为48ħ,误差约为6.8%,满足工程精度要求,也验证了计算方法与结果的准确性㊂图8㊀转子绕组与转子铁心关键截面温度分布Fig.8㊀Temperature distribution of key sections of rotor winding and rotor core3.4㊀不同副槽入口流量对转子流体和温度的影响副槽入口流量的大小对于发电机转子内流体运动㊁各部件温度分布有着重要的影响㊂因此,本节主要研究不同副槽入口流量对转子内部风量分配和温度的影响规律,此处流量为体积流量,流量值从0.04m 3/s 至0.2m 3/s 变化,步长为0.02m 3/s㊂图9为不同副槽入口流量下各径向通风沟内流量分布㊂可以看出,沿着轴向从转子端部至转子中心处,流量分配的变化趋势与图4中基本一致㊂随着副槽入口流量的不断增加,转子径向通风沟内流量分布逐渐变得陡峭,即流量分布逐渐不均匀,这可能会导致转子绕组轴向热不平衡系数的增大㊂图9㊀不同副槽入口流量下转子通风沟内流量分配Fig.9㊀Flow distribution in rotor ventilation ducts un-der different inlet flow rates of the sub-slot不同副槽入口流量下转子铁心和转子绕组的平81电㊀机㊀与㊀控㊀制㊀学㊀报㊀㊀㊀㊀㊀㊀㊀㊀㊀㊀㊀㊀㊀第28卷㊀均温度和最高温度列于表3中㊂可以看出,转子铁心和转子绕组的平均温度和最高温度随着入口流量的增加而显著减小,当流量大于0.16m3/s以后,平均温度和最高温度的降低效果变弱㊂当入口流量为0.04m3/s时,转子绕组的最高温度超过155ħ,超过了B级绝缘的最大耐受温度㊂入口流量为0.08m3/s时,转子绕组和铁心的最高和平均温度均不超过135ħ,这一温度是F级绝缘㊁B级考核的标准㊂因此,通过上述的研究方案,发现转子副槽入口流量不能低于0.08m3/s,也尽量不高于0.16m3/s㊂这样在能保证发电机正常运行的情况下优化汽轮发电机的风扇和转子通风系统的利用率,以实现更好的冷却效果㊂表3㊀不同入口流量下转子铁心和转子绕组的温度Table3㊀Temperature of rotor core and rotor winding un-der different inlet flow rates转子副槽入口流量/(m3/s)转子绕组转子铁心平均温度/ħ最高温度/ħ平均温度/ħ最高温度/ħ0.04127.6161.695.8122.2 0.06112.814488.0110.1 0.08104.9134.283.7103.6 0.1099.9127.880.899.3 0.1296.3123.178.896.2 0.1493.5119.477.093.6 0.1691.4116.775.891.8 0.1889.6114.374.790.1 0.2088.0112.273.788.6 3.5㊀不同槽楔出口直径对转子流体和温度的影响为了研究槽楔出口直径的大小对转子通风道内流量分配以及结构件温度分布的影响,本节将槽楔出口直径从2mm至10mm变化,步长为2mm㊂图10为不同槽楔出口直径下各径向通风沟内流量分布㊂可以看出,随着槽楔出口直径的减小,径向通风沟内流量分布的均匀性逐渐增强㊂当出口直径为2mm时,流量分布最为均匀,这有利于降低绕组的轴向热不平衡㊂此外,对于每一种方案,通风沟内流量最大位置均位于端部位置和转子中心位置㊂不同槽楔出口直径下转子铁心和转子绕组的平均温度和最高温度列于表4中㊂可以看出,转子铁心和转子绕组的平均温度和最高温度随着出口直径的减小而逐渐降低㊂但当出口直径过小(即2mm)时,绕组和铁心的平均温度和最高温度反而升高,不利于转子的散热㊂因此,应当在保证结构件温度不高的情况下,尽可能选择较小的出口直径㊂图10㊀不同槽楔出口直径下转子通风沟内流量分配Fig.10㊀Flow distribution in rotor ventilation ducts un-der different outlet diameter表4㊀不同槽楔出口直径转子铁心和转子绕组的温度Table4㊀Temperature of rotor core and rotor winding un-der different outlet diameter槽楔出口直径/mm转子绕组转子铁心平均温度/ħ最高温度/ħ平均温度/ħ最高温度/ħ296.5124.279.297.6 495.8120.578.394.3 696.0121.878.595.0 896.3123.078.896.2 1096.4124.179.097.44㊀结㊀论1)求解350MW水氢氢冷汽轮发电机通风网络模型,得到总体积流量(半个电机)为18.986m3/s,与实测值相比误差较小,验证了通风网络模型计算的准确性㊂电机内部各区域风量分布较为合理,计算出的流量和压力值作为转子流-热计算的耦合边界条件㊂2)在交替径向通风道内,氢气速度的周向和径向分量为主要变化量㊂随着径向高度的不断增加,周向分量值几乎呈线性增大㊂受转子旋转和风道结构的影响,副槽和径向风道内氢气径向速度分布呈不均匀性㊂尤其1号风道底部左右两支路氢气径向速度分布差异较大,右侧支路有较大回流,这也导致两侧氢气温度略有差异㊂3)交替径向风道结构相比于传统双径向直风道,其内部氢气流量分布更加均匀,这使得转子绕组和铁心在轴向上温差较小㊂端部前3个风道较大的通风面积导致其流量大,有利于端部的散热;从4号91第2期李伟力等:汽轮发电机带有交替径向风道的转子流体与传热耦合分析。
汽轮发电机组轴系找中及联接研究

汽轮发电机组轴系找中及联接研究摘要:汽轮发电机组轴系找中和联接是汽轮发电机组本体安装工作中极其重要的一个环节,也是安装过程中较繁琐和困难的一项工序。
轴系的找中和联接的质量不满足要求将会给整个机组的运行带来不可估量的后果,严重威胁机组的安全运行。
本论文通过对运行中影响中心的主要因素、转子按靠背轮找中和调整的方法及靠背轮的联接进行分析研究,为后续机组汽轮发电机组的找中及联接提供借鉴。
关键词:汽轮发电机;轴系;找中;联接1概述随着国家对发电企业节能减排、大力发展大型机组的趋势要求,近年各地发电企业均上马百万机组。
机组的安装工艺也不断创新,其中汽轮发电机组安装的轴系找中心环节,是汽轮发电机组安装中最为重要环节之一,它工艺质量的好坏将直接影响到机组的安全可靠运行及经济性。
转子按靠背轮找中心的目的是使汽轮发电机组各转子的中心线能通过靠背轮连接为一根连续的曲线,为此,转子连接时必须使两个靠背轮的外圆同心并使端面保持平行,避免因对中不良或邻近轴承上负荷分配不良引起的弯曲应力。
根据不同的机组,有不同的汽缸支撑方式、轴瓦型式、联轴器形式、找中要求等,针对不同的机组要选择合适的找中、铰孔和联轴方法及施工逻辑,并提高测量精度,以求提高安装质量,实现机组安全可靠运行。
2 运行状态下对转子轴线的影响转子找中心是在冷态下进行的,当汽轮机处于运行状态时,由于各种因素的影响,均会使在冷态下已找好的中心发生变化,这种状态下影响转子中心位置的因素大致有以下几点:2.1 轴承座垂直方向的热膨胀汽轮机在运行状态时,各轴承座的温度各不相同,热膨胀也不同,因此转子各轴颈的升高也不一样。
实践表明,轴承座的这种不均匀膨胀的结果,使中轴承座太高,即中轴承座的负荷加重了。
为了避免这种现象发生,安装时应将两靠背轮预留某一下张口值。
2.2 油膜厚度的影响转子静止时,轴颈沉于轴瓦底部,此时轴颈的中心o1在轴瓦洼窝中心o的正下方,轴颈两侧形成楔形油室。
转子刚开始转动时,由于转速较低,油膜还不能形成,随着转子的转动,楔形油室中的油受挤压从而压力升高,压力改到一定程度,就可以把轴颈托起,使转子浮在油膜上转动。
汽轮机转子输出端和联轴器的设计探讨 李光磊

汽轮机转子输出端和联轴器的设计探讨李光磊摘要:不同于通流部位的转子,输出端的转子位于汽轮机轴承箱内,该部位转子不承受高温高压蒸汽的影响,故其强度设计不同于通流部分转子的强度设计。
转子输出端最主要的作用是传递叶片上气流力产生的扭矩。
根据舒本柯-舒宾等人的研究,汽轮机转子最薄弱的部位通常位于输出端轴颈和联轴器处。
因此,保证汽轮机转子输出端的安全运行是转子设计的重要任务之一。
基于此,本文主要对汽轮机转子输出端和联轴器的设计进行分析探讨。
关键词:汽轮机转子;输出端;联轴器;设计探讨前言工业汽轮机转子是直接参与热能转换成机械能的过程,并将这种能量通过联轴器传递输出到被驱动设备上的关键转动部件。
汽轮机中所有转动零部件的组合体,称为转子。
包括主轴(或称为转鼓)、动叶片以及汽封、平衡活塞、油封环、推力盘、盘车棘轮、联轴器,还有驱动调节系统的传动装置和主油泵等。
1、转子输出端的设计1.1转子的积木块设计思想在转子设计中,通常将主轴的毛坯锻件图、成品图和转子总成图分开。
将主轴的毛坯图分成3个区段,即前区段、通流段和后区段,形成积木块系列。
根据用户的要求和设计准则的规定,很快就能够设计生成主轴毛坯锻件图,并且最大程度地包容各种可能的因素于这种机型中,形成通用的毛坯图;当然也有少量特殊的个性化主轴毛坯图。
将转子的总成图分成5个区段,即前区段的轴段I和轴段Ⅱ、通流段(或者称轴段Ⅲ)和后区段的轴段Ⅳ和轴段Ⅴ;其中前区段的轴段Ⅱ和后区段的轴段Ⅳ,已形成系列的、标准的和通用的轴段图纸,基本上与汽轮机的外汽封、径向轴承、推力轴承和油封环等积木块系列部套有关和匹配。
而通流段(或者称轴段Ⅲ)则根据热力和强度计算确定,本研究不作叙述。
因此转子结构设计的主要内容就是与用户要求有关联的轴段I和轴段Ⅴ,尤其是转子输出端的设计。
1.2转子输出端的设计流程转子输出端的设计,是整个转子设计过程中,非常重要的一个环节。
对于双输出轴转子或者特殊要求的敏感转子,就可能是一个关键的环节。
重型燃气轮机斜向转子支撑结构分析

在重型燃气轮机中 ,由于其 转子高速旋转的特性 ,转子的 同轴度 误差对机组的运行质量影响较大 ,严重时影响各轴瓦的载荷分配 ,并 产生较大的振动 。转子支撑的变形是 影响转 子同轴度—个重要的直接 因素 。本文主要 借助A S S F N Y X对转 子支撑工况进行数值模拟 ,求 C 解 不同结构 支撑 的变形 情况 ,从 中选取较 为优 化的交撑结 构。同时 , 由于影响燃气轮机效 率的核心 参数是气体 的初温和压缩 比 ,映射 到 转 子支撑工 况上就 是燃 气的温度 、压强和轴重载的变化 ,因此 , 中 文 还对在具有 不同气 体的温度和轴重载的工况条件下 的转子 支撑变形进 行分 析,为 以后汽轮发 电机技术 的研 究和发 展提供一定的依据。
重 型 燃 气 轮 机 斜 向转 子 支 撑 结构 分 析
张 艳 彪 孙 文 磊
( 疆 大学北校 区 ) 新 摘 要 本文针 对重 型燃气轮机 转子支撑结构 ,采用流一 固耦 合和热一 固耦 合求解 方法 。应 用A s s F 程 序对其 工况进行数值 NY X C 模 拟 。通过分析斜 向转子 支撑 结构 变形情 况,并进 一步分析斜向 支撑在 不同工况务件下 变形规律 ,以支持热 态 自 应对 中动压滑动轴 适 承工作机理 和动力特 性表 征方法 的研 究,并最终将研 究成果扩展应 用于轴 系动 力稳 定性 的研 究。
位 ,并建立统一的参考体系 。
( )固体 模型的建立 。首先按 实际尺寸建 立部件完全模型 ,实 1 现每—个细节 , 部件模 型有一个 对
完全系统的认识 ,各部件完全模 型 如图l 所示。其中外缸 、轴承座、 支撑是焊接 在—起 的 , 称支撑 结 合 构。 为了减 小计算 量,提 高分析效 率,对模型进行简化 。简化时 保留 主要结构尺寸 ,保 留加强筋等影响 结构力学和热力学性能的重要部分
汽轮发电机转子联轴器对组用销孔加工工艺改进

孑 L , 通过销孑 L 装入联接螺栓将发 电机转子与汽轮机转子对组 、 把合 。 为 保 证 发 电机 转 子 和 汽 轮机 转 子 的顺 利 、 精确 地 组 装 , 对 销 孔 的 尺 寸公差 、 位 置 度 及 表 面 粗 糙 度 都 做 了 严格 的要 求 , 该 组 销 孔 的 直 径 公差一般在± 0 . 0 5 a r m以 内, 位置度在 0 . 0 5 — 0 . 1 0 m m以内 , 表 面 粗 糙
度R a 1 . 6以上 。
为保证销孔 的加工精度 , 过去一直采用专用工具 钻模 的传统加 工工 艺 。近 年来 , 各 发 电机 制造 厂 家 需 要在 短 期 内不 断 开发 出不 同 规格 的新 产 品 , 以适 应 市 场 需要 。新 产 品 的转 子 联 轴 器销 孑 L 尺 寸 各 不相 同, 如采用传统工艺则需要提制不同尺寸的钻模。因钻模制造 周期长 , 且制造费用较高 , 势必要占用发 电机产品整体制造周期 , 且 提 高 产 品 制造 成 本 , 特 别 是 对 于某 些 工 期 紧急 的产 品 , 钻模 的设 计 及 制造 甚 至 会成 为制 约 生产 进 度 的一 个 不 利 因素 。 2 工 艺 改进 针对此问题 , 我公 司近年来改进联轴器销孔的加工工艺 , 利用 数控镗床完成销孑 L 的加_ 『 二 。此方法不需要使用钻模 , 大大缩短产品 整体 制 造 工 期 ( 每种 产 品 至 少缩 短 2个 月 的制 造 时 间 ) , 且 节 省 了 生 产 钻模 的费 用 ,降 低 了产 品制 造成 本 ( 一 般钻 模 的制 造 成 本 约为 1 万 元, 件1 。 还 因减 少 了工 具 的种 类 和 数量 , 减 轻 了工具 保 管 人员 的工 作量 , 收 到较 好 的 效果 。 3工 艺 要点 及 适 用性 使 用 数 控镗 床 加 工联 轴 器 销孑 L , 普 遍采 用 的工 序 如下 : 粗镗 、 半 精镗 、 位 置度 测 量 、 修 正 坐标 、 精镗 、 位 置度 检 查 。 使 用 工 具 为微 调 刀杆 。 在 加 工过 程 中采 用 修 正 坐标 的 方法 克 服 了国内电机制造厂家普遍存在的 , 因机床长期超负荷使用且保养不 好而造成 的精度不足的不利 因素。位置度测量方法简单而实用 , 仅 用精 密 卡 尺 、 内径 千分 尺 即可 完 成 测量 。 因此 , 此 工艺 方 法尽 管 采 用 的是 数 控 镗 床 , 但 对 于 数 控 镗 床 的 精 度 没有 做 过 严 格 要 求 , 操 作 方 法 简 单实 用 , 适 合 一般 企 业 , 具 有推 广 价值 。 4 实 例 拿一 台 1 0 0 0 MW 超 超 临 界 汽 轮 发 电 机 为 例 。 其联 轴 器 销 孑 L 为
汽轮机转子输出端和联轴器的设计探讨
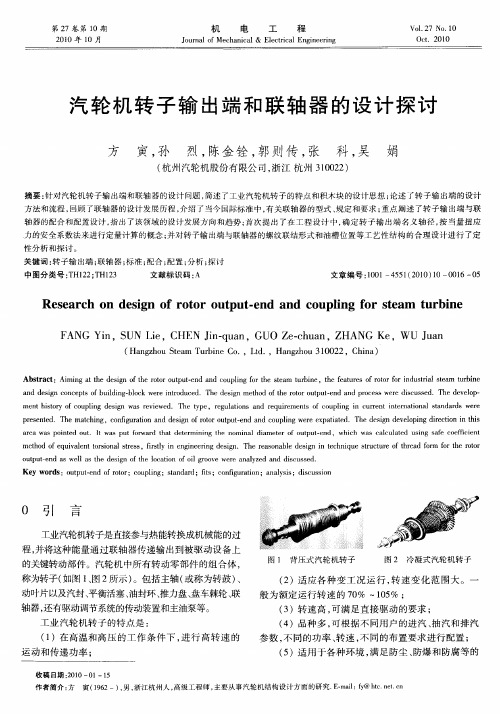
第2 7卷 第 1 0期
2 0年 1 01 0月
机
电
工
程
Vo . 7 1 2 No. 0 1 0c .201 t 0
J u n l fMe h n c l& E e t c lE gn ei g o r a c a ia o lc r a n i e r i n
汽 轮 机 转 子 输 出 和 轴 器 的 设 计 探 讨 端 联
a d de in c n e s o ui n — lc r nto u e n sg o c pt fb l g bo k wee i r d c d.Th e in meh d o her tro t u — n n r c s r ic s d.Th e eo — di e d sg t o ft oo u p te d a d p o e swe e ds use e d v lp me thitr fc u i g d sg s r ve d Th y e, rg ain a d r q ie n s o o p i n u rnti e n t na sa d r s we e n so y o o pln e in wa e iwe . etp e ult s n e u rme t fc u lng i c re ntr ai l tn a d r o o
219492874_汽轮机轴系支撑方案探讨

DOI:10.13808/ki.issn1674-9987.2023.02.001汽轮机轴系支撑方案探讨第一作者简介:张健(1975-),男,工程硕士,高级工程师,毕业于哈尔滨工业大学热力发动机专业,主要从事汽轮机设计工作。
张健袁廖上斌(东方电气集团东方汽轮机有限公司,四川德阳,618000)摘要:为提高经济性,现代汽轮机多采用多缸多转子结构,轴系由多个滑动轴承水平支撑,转子的自重和扰力由滑动轴承的油膜力平衡抵消。
多转子轴系分为双支撑和三支撑两种支撑方式,因三支撑方案具有结构紧凑、支持轴承标高变化对轴系稳定性影响小的优点,得到越来越多设计人员的青睐。
但三支撑方式也有一定的局限性,文章对三支撑轴系的局限性和轴系特点进行探讨,希望在新机型开发时,能够根据机组的特点和使用环境,合理选择机组轴系的支撑方案。
关键词:轴系,三支撑,响应,振动中图分类号:TK262文献标识码:B文章编号:1674-9987(2023)02-0001-05 Discussion on Steam Turbine Shafting Support SchemeZHANG Jian,LIAO Shangbin(Dongfang Turbine Co.,Ltd.,Deyang Sichuan,618000)Abstract:In order to improve the economy,modern steam turbines mostly use multi-cylinder and multi-rotor structure.The shaft system is supported horizontally by multiple sliding bearings.The weight and disturbance force of the rotor are offset by the balance of oil film force of sliding bearings.Multi-rotor shafting can be divided into two supporting modes:double span-three fulcrum and double span four fulcrum.The three fulcrum schemes are favored by more and more designers because of their advantages of compact structure and small influence of bearing elevation changes on shafting stability.However,the three fulcrum method also has some limitations.This paper discusses the limitations and characteristics of the double span-three fulcrum shafting.It is hoped that readers can reasonably choose the support scheme of the unit shafting according to the characteristics and operating environment of the unit when developing new models.Key words:shaft system,double span-three fulcrum,response,vibration1引言对经济性的不断追求促使现代大型汽轮机采用多汽缸多转子结构,汽轮机各转子及汽轮机与被驱动设备转子之间通过联轴器连接构成轴系。
1000MW机组雷击事件对汽轮机轴承振动影响及分析

1000MW机组雷击事件对汽轮机轴承振动影响及分析发布时间:2021-11-16T03:56:02.357Z 来源:《科学与技术》2021年第8月23期作者:李磊张守文刘博阳郭进文雷鹏李德浩[导读] 雷击事件大部分是由出线线路问题导致了较大的负序电流,从而导致发电机李磊张守文刘博阳郭进文雷鹏李德浩华能国际电力股份有限公司玉环电厂浙江省台州市 317604摘要:雷击事件大部分是由出线线路问题导致了较大的负序电流,从而导致发电机、励磁机电磁场变化,作用在定子和转子上的电磁力瞬时变化,导致6、7、8号瓦轴振、瓦振均有变化且此时轴振、瓦振为真实振动。
由于6、7号瓦测点安装在发电机大端盖上,6、7号瓦瓦振反应的是发电机定子的瞬时振动情况,根据轴振的变化情况及6、7号瓦轴瓦间隙可以判断。
通过分析负序电流对汽轮机轴承振动产生的影响,可查漏补缺,发现不足并制定后续处理和检查方案,为机组的安全稳定运行保驾护航。
关键词:1000MW;超超临界;汽轮机轴承振动;雷击事件;监测系统VM600 1 背景概述华能玉环分公司2021年6月11日15:38、6月18日19:46、6月27日14:12,曾发生雷击天气,导致机组振动变化突变情况。
三次线路故障或雷击影响了我厂四台机组主机轴系振动,主要表现在6、7、8号轴承和瓦振。
现场检查四台机组6、7、8号瓦情况,听音无异常。
查看TDM系统,检查各台机组8号瓦间隙电压无明显变化。
检查8号瓦频谱均是工频为主,存在少量的2倍频。
检查6月11日15:38和6月27日14:12两次电气线路故障,存在较大的负序电流,导致6、7、8号瓦轴振、瓦振均发生较大的突变。
6月18日19:46雷击事件存在微弱的负序电流,只引起了轴振突变,瓦振无明显变化。
2 雷击后现场检查及分析2.1 6月11日雷击事件检查情况6月11日15时38分45秒#3机组负荷电流21560A。
500kV 系统发生A相接地故障,A相残压约70%Un,持续时间约47ms。
- 1、下载文档前请自行甄别文档内容的完整性,平台不提供额外的编辑、内容补充、找答案等附加服务。
- 2、"仅部分预览"的文档,不可在线预览部分如存在完整性等问题,可反馈申请退款(可完整预览的文档不适用该条件!)。
- 3、如文档侵犯您的权益,请联系客服反馈,我们会尽快为您处理(人工客服工作时间:9:00-18:30)。
汽轮机转子输出端和联轴器的设计探讨李光磊
发表时间:2019-03-27T10:47:42.287Z 来源:《电力设备》2018年第29期作者:李光磊[导读] 摘要:不同于通流部位的转子,输出端的转子位于汽轮机轴承箱内,该部位转子不承受高温高压蒸汽的影响,故其强度设计不同于通流部分转子的强度设计。
(哈尔滨汽轮机厂有限责任公司哈尔滨 150046)
摘要:不同于通流部位的转子,输出端的转子位于汽轮机轴承箱内,该部位转子不承受高温高压蒸汽的影响,故其强度设计不同于通流部分转子的强度设计。
转子输出端最主要的作用是传递叶片上气流力产生的扭矩。
根据舒本柯-舒宾等人的研究,汽轮机转子最薄弱的部位通常位于输出端轴颈和联轴器处。
因此,保证汽轮机转子输出端的安全运行是转子设计的重要任务之一。
基于此,本文主要对汽轮机转子输出端和联轴器的设计进行分析探讨。
关键词:汽轮机转子;输出端;联轴器;设计探讨
前言
工业汽轮机转子是直接参与热能转换成机械能的过程,并将这种能量通过联轴器传递输出到被驱动设备上的关键转动部件。
汽轮机中所有转动零部件的组合体,称为转子。
包括主轴(或称为转鼓)、动叶片以及汽封、平衡活塞、油封环、推力盘、盘车棘轮、联轴器,还有驱动调节系统的传动装置和主油泵等。
1、转子输出端的设计
1.1转子的积木块设计思想
在转子设计中,通常将主轴的毛坯锻件图、成品图和转子总成图分开。
将主轴的毛坯图分成3个区段,即前区段、通流段和后区段,形成积木块系列。
根据用户的要求和设计准则的规定,很快就能够设计生成主轴毛坯锻件图,并且最大程度地包容各种可能的因素于这种机型中,形成通用的毛坯图;当然也有少量特殊的个性化主轴毛坯图。
将转子的总成图分成5个区段,即前区段的轴段I和轴段Ⅱ、通流段(或者称轴段Ⅲ)和后区段的轴段Ⅳ和轴段Ⅴ;其中前区段的轴段Ⅱ和后区段的轴段Ⅳ,已形成系列的、标准的和通用的轴段图纸,基本上与汽轮机的外汽封、径向轴承、推力轴承和油封环等积木块系列部套有关和匹配。
而通流段(或者称轴段Ⅲ)则根据热力和强度计算确定,本研究不作叙述。
因此转子结构设计的主要内容就是与用户要求有关联的轴段I 和轴段Ⅴ,尤其是转子输出端的设计。
1.2转子输出端的设计流程
转子输出端的设计,是整个转子设计过程中,非常重要的一个环节。
对于双输出轴转子或者特殊要求的敏感转子,就可能是一个关键的环节。
一般情况下,转子输出端的设计流程,是根据已知传递功率、转速范围等参数和已确定机型的相关结构尺寸,依据准则或者大致估算转子输出端的轴径、半联轴器的重量和重心位置;设计一张与被驱动设备的轴头连接图,然后依据最终确定的联轴器重量和重心位置,再进行详细的振动计算,最终设计确定转子各轴段图和总成图等技术文件。
通过这样的积木块设计思想、方法和流程,能够很好地融合工业汽轮机品种多、范围广和单台小批量的特点;解决了不同布置要求和转子制造加工周期长之间的矛盾。
2、联轴器的型式和标准的规定
2.1转子输出端和联轴器的型式
上世纪80年代,世界各国的工业汽轮机制造厂家对于工业汽轮机转子输出端和联轴器的型式,一般采用喷油润滑的齿式联轴器。
随着工业汽轮机单机功率不断递增,联轴器专业厂家的制造水平不断成熟,现在已经广泛地应用膜盘和膜片式联轴器。
工业汽轮机转子输出端与联轴器配合型式的发展,一方面是需要符合国际上公认的API612]和ISO14661标准的规定和要求;另一方面也改变了传统工业汽轮机制造厂家,由原来制造齿式联轴器发展为向联轴器专业厂家采购配套的方式转变。
2.2联轴器标准的规定和要求
对于转子输出端的联轴器,国际上公认的API612和ISO14661标准中有单独的章节给予阐述和要求,标准明确规定联轴器应该符合API671或ISO10441。
对于联轴器的布置,应设计成不拆除被驱动机器、齿轮装置和汽轮机缸体时就能接近两个半联轴器,并且汽轮机应能带着联轴器而脱开被驱动机器进行试验。
对于联轴器的配合,要求半联轴器应通过带键或者不带键的圆柱面和锥面与转子输出端紧配合;可以用液压套装或者红套的工艺方法,安装符合API671或ISO10441标准的联轴器质量模拟器(商定的力矩模拟器)或者单独的空转接套,以便能够在装运出厂前,对汽轮机转子进行正确的试验。
3、转子输出端与联轴器的配合和配置
3.1转子输出端与联轴器的配合
工业汽轮机转子最终是通过联轴器将能量传递输出到被驱动设备上的,即通过转子输出端与联轴器轴毂的紧配合(过盈配合)来承担全部扭矩。
并且紧配合(过盈配合)的值与输出端和联轴器轴毂的形式紧密关联。
一般情况下,转子输出端轴径与联轴器轴毂内孔配合的过盈量设计,按不同的配合方式进行选择。
以下4种配合方式,其过盈量设计范围为名义轴径的0.5‰~2.5‰:
(1)带双键的圆柱形配合;
(2)不带键的圆柱形配合;
(3)带双键的圆锥形配合;
(4)不带键的圆锥形配合。
3.2转子输出端与联轴器的配置
一般就不带键的圆锥形配合这一类,对于转子输出端与半联轴器的配置型式有两种:
(1)转子输出端的轴为内螺纹形式的(如图7所示);
(2)转子输出端的轴为外螺纹形式的(如图8所示)。
以上两种配置型式都需要用液压套装工具来安装半联轴器。
图1 输出端的轴为内螺纹形式的液压套装工具图2 输出端的轴为外螺纹形式的液压套装工具 4、转子输出端与联轴器的设计
目前世界各国的工业汽轮机制造厂家 ,使用不带键的圆锥形配合形式越来越普遍和广泛 ,并已经发展成为一种趋势:
(1)一般情况下,转子输出端与联轴器圆锥形配合的锥度采用1∶20和1∶24居多, 圆锥形配合接触面积≥85%。
(2),转子输出端与联轴器配合采用基轴制 ;不带键的圆锥形配合,其过盈量为名义轴径 (圆锥大端 )的 2.5‰。
(3)从图1和图2中可以看到 , 转子输出端的轴无论是内螺纹形式的还是外螺纹形式的 ,一般油槽的位置是开在轴上的, 极少数是将油槽开在半联轴器上的。
(4)对于按照 API612标准设计的工业汽轮机转子而言 ,转子输出端与联轴器安装后 ,就必须进行转子动平衡。
因此其转子输出端设计时, 就要有与动平衡设备连接的工艺孔。
极少数是将连接的工艺孔开在半联轴器或者空转接套上。
5、转子输出端与联轴器的分析和探讨
5.1转子输出端螺纹形式
转子输出端内、外螺纹形式的采用,其目的是将半联轴器或者空转接套安装到转子输出端上 (1)转子振动特性的影响。
对于双支点的工业汽轮机转子而言,转子输出端的重量大小对转子振动特性的影响很大,尤其对双出轴转子是很敏感的;在转子输出端直径、外伸长度和联轴器型式同等的条件下,采用内、外螺纹形式的判断依据就是重量;内螺纹形式要优于外螺纹形式。
(2)转子动平衡工艺孔的影响。
外螺纹形式的转子输出端由于受到锁紧螺母和外螺纹尺寸的原因,其设计较困难;个别转子甚至要将动平衡工艺孔开到半联轴器或者空转接套上。
所以从设计转子动平衡工艺孔角度而言,内螺纹形式要优于外螺纹形式。
5.2转子输出端油槽位置
转子输出端油槽位置的合理设计,其目的是将半联轴器或者空转接套顺利地安装到转子输出端上。
转子输出端油槽位置的设计确定,要考虑联轴器的结构。
半联轴器凸缘在不同位置时,锥面受液压力作用下的位移变形如图11~图13所示。
合理的油槽位置是尽可能接近半联轴器的重心位置;对实际情况来说,还要注意工程上的可能性和可操作性。
6、结束语
综上所述,在工业汽轮机转子的设计过程中,要充分考虑转子输出端和联轴器的结构设计对转子的影响因素。
加强与被驱动设备制造厂家的沟通和技术协调,合理地设计和确定转子输出端轴头的尺寸、联轴器的配合和配置型式,注重输出端油槽位置和动平衡工艺孔等结构的细节设计,以满足液压套装工具的方便使用和转子动平衡等试验的顺利进行,从而确保设计的工业汽轮机转子安全可靠的运行。
参考文献:
[1]顾煜烔.汽轮机发电机组扭振安全性分析与应用[M].北京:科学出版社,2013.
[2]丁有宇.汽轮机强度计算手册[M].北京:中国电力出版社,2010.。