转向操纵机构设计报告
机械设计创新报告——小型机器人转向机构
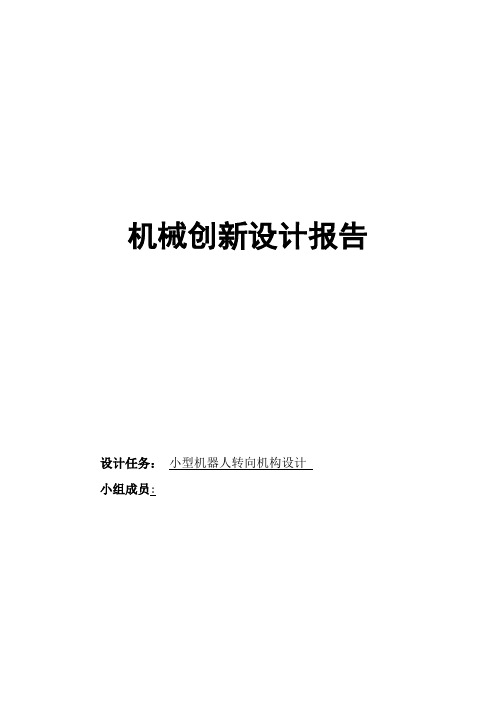
机械创新设计报告设计任务:小型机器人转向机构设计小组成员:初期设计构思:xx:1、简单的左右轮驱动:两个轮子分别由两只马达控制,需要转弯时,RCX控制一个马达转动,另一个马达停止或反方向转动即可。
转弯角度是通过程序控制马达运动和停止的时间来控制的。
2、前轮驱动的三轮装置,三轮装置由一个用于驱动和转弯的前轮及两个保持稳定的独立后轮组成。
3、舵轮结构,利用一个电机通过差速器驱动小车行进,小车后面使用一个舵轮装置,构成了一个“主动舵”,舵轮轴向随动,径向作主动运动时,又可以带动小车转动以改变方向。
XX:1、用两个锥齿轮实现机器人原地转向。
2、用棘轮间歇机构实现小型机器人的间歇转动。
3、用升降马达和带动丝杠组成轮式转向机构。
XX:1、两排轮子,用电机分别控制,两排轮子转速不一样时可转弯。
2、转弯时机器人底部伸出一个支撑座,使得带有轮子的主体转过后,轮子着地,底座收起继续前行。
3、将轮子做成充气式,通过改变轮子的充其量改变轮子的直径,达到转向的目的。
XX:1、用五个轮子,其中四个为驱动轮,第五个为辅助轮,采用辅助轮转向;2、后轮驱动前轮拉杆转向;3、转向单边驱动另一边抱死。
XX1、利用连杆机构实现两个前轮的转向,将转向驱动力直接传输到两个前轮;2、利用锥齿轮等齿轮实现两个前轮的转向;3、使用三轮结构,然后对单前轮实现转动。
功能结构图:工作原理和工艺动作过程简图:图1图2图31.车轮2.主销3.连杆4.拉杆5.车架6.转向节车轮1由主销2固定在连杆3上,连杆上转向节6两端经轴承(图1中轴承未画出)和车架5固定在一起,转向节两端可以安置两个劲度系数相同的弹簧,从而实现避震效果(图2中弹簧未画出),并且可以自由转动,连杆上圆柱和拉杆4配合在一起,可以相对转动。
当需要转动时,利用拉杆4可以将电动机的转动变为其自身左右的摆动,从而带动连杆3和转向节6的摆动,前轴的两端和转向节6由主销2铰接在一起,转向节6和连杆3上连有横向拉杆4,当拉杆4带动一个转向节转动时,另一个转向节也随着变位,在后轮驱动轮的驱动下,就可以实现使机器人转向。
实例_转向系统设计计算报告

目录1.概述 (1)1.1任务来源 (1)1.2转向系统基本介绍 (1)1.3转向系统结构简图 (1)2.转向系统相关参数 (1)3.最小转弯半径 (2)4.转向系传动比的计算 (3)5.转向系载荷的确定 (3)M (3)5.1原地转向阻力矩r5.2车轮回正阻力矩Ms (3)F (3)5.3作用在转向盘上的力k6.转向管柱布置的校核 (4)6.1转向管柱布置角度的测量 (4)6.2转向管柱角速度及力矩波动计算 (4)6.3转向管柱固有频率要求 (7)7.结论 (7)参考文献.................................................... 错误!未定义书签。
1.概述1.1任务来源根据007车型设计开发协议书, 007项目是一款全新开发的车型,需对转向系统进行设计计算。
1.2转向系统基本介绍转向管柱为角度不可调式管柱,转向机采用结构简单、布置容易的齿轮齿条式转向机。
转向盘采用软发泡三辐式,轮辐中间有一块大盖板,打开时可拆装调整转向盘。
1.3转向系统结构简图2.转向系统相关参数轮胎规格为185R14LT ,层级为8。
轮辋偏置距为+45mm ,负荷下静半径为304㎜,滚动半径约317mm ,满载下前胎充气压力240KPa 。
3.最小转弯半径汽车的最小转弯半径是汽车在转向轮处于最大转角条件下以低速转弯时前外轮中心与地面接触点的轨迹构成圆周半径,它在汽车转向角达到最大时取得。
转弯半径越小,则汽车转向所需场地就愈小,汽车的机动性就越好。
为了避免在汽车转向时产生的路面对汽车行驶的附加阻力和轮胎过快磨损,要求转向系能保证在汽车转向时,所有车轮应绕瞬时转向中心作纯滚动。
此时,内转向轮偏转角β应大于外转向轮偏转角α,在车轮为绝对刚体的假设条件下,角α与β的理想关系式应是:L ctg ctg K+=βα式中:K —两侧主销轴线与地面相交点之间的距离; L —轴距。
3.1按外轮最大转角C LR +=αsin 1 =5194.9(mm ) 3.2按内轮最大转角C KL K L R +++=21222]tan 2)sin [(ββ=5912.3(mm )取221min R R R +==5553.6mm 所以最小转弯半径约为5.6m 。
转向系统设计计算报告
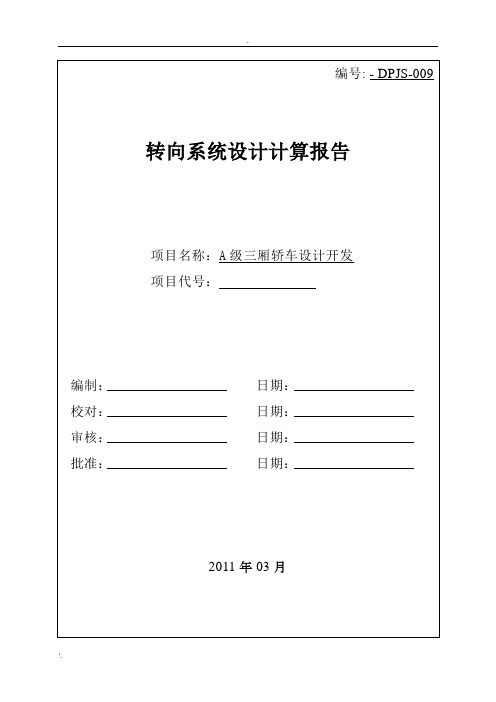
目录1.系统概述 (1)1.1系统设计说明 (1)1.2系统结构及组成 (1)1.3系统设计原理及规范 (2)2.输入条件 (2)2.1标杆车基本参数 (2)2.2LF7133确定的整车参数 (3)3.系统计算及验证 (4)3.1方向盘转动圈数 (4)3.2齿轮齿条式转向系的角传动比 (4)3.3车轮实际最大转角 (5)3.4静态原地转向阻力矩 (5)3.5静态原地转向时作用于转向盘的力 (5)3.6最小转弯半径的校核 (6)4.总结 (8)参考文献 (8)1.系统概述1.1系统设计说明LF7133是在标杆车的基础上开发设计的一款全新车型,其转向系统是在标杆车转向系统为依托的前提下,根据总布置设计任务书而开发设计的。
根据项目要求,需要对转向系统各参数进行计算与较核,以确保转向系统的正常使用,使系统中各零部件之间参数匹配合理,并且确保其满足国家相关法律法规的要求。
1.2系统结构及组成LF7133转向系统是在标杆车的基础上,根据驾驶室和发动机舱的布置,对转向管柱、方向盘和转向器等作相应调整与优化设计。
为提高汽车行驶的安全性,转向系必须转向轻便、灵活,以减轻司机的疲劳。
LF7133电动助力转向系统中转向器采用齿轮齿条式转向器、电动助力转向管柱的结构方式。
该结构紧凑,布置方便,降低油耗,工作可靠,维修方便,并且满足了整车的各项指标。
1).转向系统的结构简图32图1 转向系统结构简图1、转向器2、电动助力转向管柱3、转向盘2).转向系统的转向梯形示意简图由于LF7133转向系结构与布置情况参照标杆车设计,所以LF7133与标杆车转向梯形示意图一致,如下图2所示。
1.3系统设计原理及规范对于液压动力转向系的设计,在保证系统拥有正常助力功用的情况下,还应满足如下的技术要求:1).根据GB17675-1999 汽车转向系基本要求的规定,同样要求在不带助力转向时转向力应小于254N。
2).对于乘用车来说,还要求转向盘转动在总圈数一般不超过4圈。
转向梯形机构设计报告
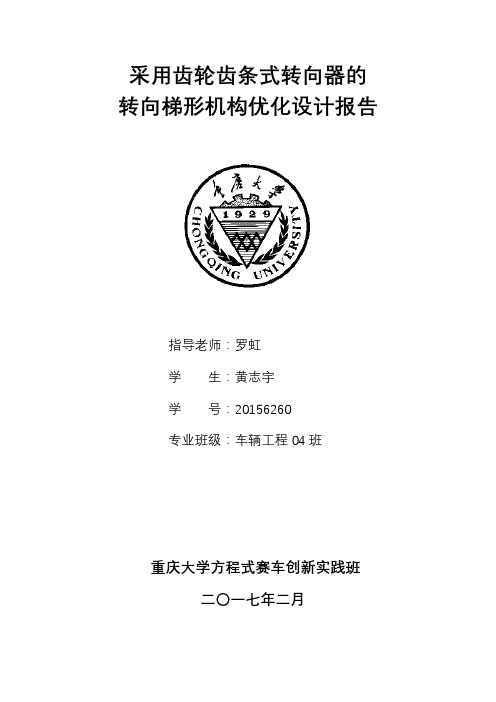
采用齿轮齿条式转向器的转向梯形机构优化设计报告指导老师:***学生:黄志宇学号:********专业班级:车辆工程04班重庆大学方程式赛车创新实践班二〇一七年二月赛车转向系统是关系到赛车性能的主要系统,它是用来改变或恢复汽车行驶方向的系统的总称,通常,车手通过转向系统使转向轮偏转一定角度实现行驶方向改变。
赛车转向系统一股由方向盘、快拆、转向轴、转向柱、万向节、转向器、转向拉杆、梯形臂等部分组成。
其中,方向盘用于输入转向角度,快拆用于快速分离方向盘与转向柱,转向柱、转向轴、万向节共同将方向盘输入角度传递到转向器,转向器通过内部传动副机构将旋转运动转化为转向拉杆的直线运动,转向拉杆与梯形臂作用于转向节,实现车轮转向。
图1展示了转向系梯形结构,图2展示了赛车转向系统构成。
图1转向梯形机构图2赛车转向系统构成由于大赛组委会规则里面明确规定不允许使用线控或者电动转向,考虑到在赛车转向系统布置空间有限,且有严格的成本限制,以及轻量化的赛车设计目标,将赛车转向器范围限定机械式转向器。
目前,国内外的大多数方程式赛车采用齿轮齿条式转向器和断开式转向梯形结构。
●齿轮齿条式转向器齿轮齿条式转向器的传动副为齿轮齿条,其中,齿轮多与转向柱做成一体,齿条多与转向横拉杆直接连接,连接点即为断开点位置。
根据输出位置不同,分为两端输出式和中间输出式。
其主要优点是:结构简单,体积小,易于设计制作;转向器可选材料多样,壳体可选用招合金,质量轻;传动效率较高;容易实现调隙,当齿轮齿条或者齿条与壳体之间产生间隙时,可以通过安装在齿条背部的挤压力可调的弹簧来消除间隙;转向角度大,制造成本低。
其主要缺点是:传动副釆用齿轮齿条,正效率非常髙的同时,逆效率非常高,可以到达当汽车在颠簸路面上行驶时,路感反馈强烈,来自路面的反冲力很容易传递到方向盘;转向力矩大,驾驶员操纵费力,对方向盘的反冲容易造成驾驶员精神紧张,过度疲劳。
●断开式转向梯形结构根据转向器和梯形的布置位置的不同,断开式转向梯形又分为四类,分别为:转向器前置梯形前置,转向器后置梯形后置,转向器前置梯形后置,转向节后置梯形前置。
FSAE转向组设计报告

FSAE转向组设计报告作者:吴帅2012/4/11前言汽车产品的质量检测具有重大的社会意义。
转向器作为汽车的一个重要部件,对其综合性能进行检测直接关系到人民的生命财产安全。
根据汽车安全性统计,,全世界每年因交通事故死亡的人数超过20万,加之几倍于死者的受伤者以及物质上的损失,其直接或间接的危害是难以估计的。
在我国,由于交通管理技术落后、路况差、车辆性能差,加之各类车辆混合行驶,交通事故时有发生。
近年来,我国交通事故死亡人数居世界前几位,每万辆车平均事故居大国中第一位。
交通事故己成为一个严重的社会问题。
概括交通事故的原因,不外乎人、汽车和环境三个因素。
显而易见,提高汽车的安全性能是减少交通事故的关键措施之一,因此,汽车工业发达的国家都非常重视汽车安全性的研究。
目前汽车工业己成为我国的支柱产业之一,所以,为了提高汽车的质量,保证行驶的安全性,在大力发展我国的汽车工业的同时,这就要求生产厂家对每一批产品必须进行质量检测,而其中转向器是汽车维持驾驶员给定方向稳定行驶能力(即操纵稳定性)的基本保障,所以汽车转向器综合性能试验成了汽车性能测试中的一个重要项目。
由于汽车转向器属于汽车系统中的关键部件,它在汽车系统中占有重要位置,因而它的发展同时也反映了汽车工业的发展,它的规模和质量也成为了衡量汽车工业发展水平的重要标志之一。
近年来随着我过汽车工业的迅猛发展,作为汽车的重要安全部件—汽车转向器的生产水平也有了很大的提高。
在汽车转向器生产行业里,70年代推广循环球转向器,80年代开发和推广了循环球变传动比转向器,到了90年代,驾驶员对汽车转向器性能的要求有了进一步的提高,要求转向更轻便,操纵更灵敏。
随着汽车的高速比和超低压扁轮胎的通用化,过去的采用循环球转向器和循环球变传比转向器只能相对的解决转向轻便性和操纵灵敏性问题,现在虽然转向器以向动力转向发展,但大部分汽车还应用机械型转向器,如何改进转向器的设计,使之更加适合驾驶者,是最重要的,因此还需不断改进。
汽车转向系 报告

西安航空职业技术学院毕 业 设 计 开 题 报 告系 别: 航空维修工程系 专 业: 汽车运用技术 班级学号: 08506211 学生姓名: 周伟指导教师: 孟志坚西安航空职业技术学院制2010 年 12 月 20日毕业设计开题报告(3)主要技术指标:采用特制成型管材,承载能力强;.高耐磨新型尼龙螺母作为主要传动件,整机性能达到国际先进水平;选用优质限位开关控制上、下行程,并配有同步保险急停装置;丝杆螺母传动,在任意位置均能自锁,双螺母机械保险,确保安全、可靠,选用优质三角带,使用寿命长,采用特种材料制造滑块导向,举升平稳;托臂在其活动范围内任意角度自锁,托盘橡胶耐磨并易于更换。
(4)设计思路根据我国设备使用的发展现状,以及汽车行业和新材料的应用情况,确定以双柱举升机为设计对象和代表。
双柱举升机设备的设计思路如下:首先设计出举升设备的整体尺寸,达到适应各种轿车的使用水平在举升设备基座上标明各个部件的安装位置设计举升装置及强度计算与校核所需举升力的大小及作用点位置设计支撑结构、限位并强度计算与校核按要求选配相应的液压部件(5)进度计划时间安排序号毕业设计阶段性工作及成果1收集资料确定设计方案1---2周2调研、实验、初步设计3---4周3设计、绘图、台架制作5---6周7周4校对图纸、初步完成毕业设计5完成毕业设计8周(6)参考文献参考文献[1] 王忠志主编.精密研磨[M].北京:中国计量出版社,1989.[2] 李虹.砂带磨削[OL].中国机床网,2006-9-16.[3] 唐金松主编.简明机械设计手册(第二版)[M].上海:上海科学技术出版社,2002.[4] 徐薄滋等编.带传动[M].北京:高等教育出版社,1988.[5] 李虹.细长轴砂带磨抛工艺研究[OL].中国机床网,2006-9-16.[6] 黄云 朱派龙编.砂带磨削原理及应用[M].重庆:重庆大学出版社,1993.[7] 李伯民.实用磨削技术[M].北京:高等教育出版社,1995.[8] 李虹.砂带磨抛细长轴精度研究[OL].中国机床网,2006-9-16.[9] 李虹.细长轴砂带磨抛表面粗糙度研究[OL].中国机床网,2006-9-16.[10] Abrasives Market - UK ,2006-9-16.[11] 王天成.砂带磨削发展[OL].中国研磨网,2006-9-16.[12] Mohawk Lifts Car Lifts, Truck Lifts, Vehicle Hoists, Home Auto Lifts, Garage Lifts [W]. [13] Mohawk Lifts HR6 [W]. [14] Mohawk Lifts USL-6000[W]. [15] 杨黎明等主编.机械零件设计手册[M].北京:国防工业出版社,1987.[16] 黄贤武.传感器原理与应用[M]. 西安:电子科技大学出版社,1999.[5] 杨渝钦.控制电机[M]. 北京:机械工业出版社,1998.[17] ALI ALCTV-1998, AUTOMOTIVE LIFTS-SAFETY REQUIREMENTS FOR CONSTRUCTION, TESTING AND VALIDATION [S].[18] 国内举升机市场2005年度调查报告[W]. [19] 举升机的结构特点介绍[W]. [20] 广西大学编写.实用机械零件手册[M].南宁:广西人民出版社,1987.[21] 电机工程手册编辑会主编.机械工程手册[M].北京:机械工业出版社,1981.[22] 张英会主编.弹簧[M].北京:机械工业出版社,1982.[23] 汪曾祥 魏光英主编.弹簧设计手册[M].上海:上海科学文献技术出版社,1994.[24] 施高义等主编.连轴器[M].北京:机械工业出版社,1988.[25] 胡寿松主编.自动控制原理[M].北京:国防工业出版社,1994.[26]《齿轮手册》编委会主编.齿轮手册[M]:上册.北京:机械工业出版社,1998.[27] 浦炎主编.机械传动装置设计手册[M]:上册.北京:机械工业出版社,1999.[28] 顾永泉著.机械密封实用技术[M].北京:机械工业出版社,2001.[29] 邹惠君编著.机械系统设计原理[M].北京:科学出版社,2003.[30] C.H柯热夫尼夫等.机构[M]:上下册.北京:机械工业出版社,1999.指导教师意见:课题难度适中,工作量较饱满,进度安排合理,工作条件具备,同意开题。
转向系统设计说明书

转向系统设计说明书转向系统设计说明书一、需求分析1.1系统简介本转向系统设计是为汽车制造企业设计的一款新型转向系统,包括方向盘、转向齿轮、转向杆等组件,用于汽车转向操作。
1.2系统功能本系统主要实现以下功能:(1)实现车辆转向操作;(2)提供灵敏度和舒适性,使驾驶员可以轻松驾驶;(3)确保车辆转向时的安全性。
1.3使用环境本系统主要用于汽车行驶时的转向操作,适用于各类车辆,包括小汽车、大型客车、货车、越野车等。
1.4系统需求(1)具有可靠性和耐用性;(2)转向灵敏度高,操控舒适;(3)保证转向操作安全;(4)可适应各种驾驶员的需求。
二、系统设计2.1系统架构本转向系统采用传统的齿轮传动转向系统。
主要包括方向盘、转向齿轮、转向杆等组件,在行驶过程中通过变换转向齿轮的位置,控制车轮的转向。
2.2系统组成本转向系统包括以下组件:(1)方向盘:由驾驶员操控,控制转向的方向。
(2)转向齿轮:连接车轮的转向轴,通过旋转控制车轮角度,实现左右转向操作。
(3)转向杆:将方向盘的旋转运动转换成转向齿轮的轴向运动。
(4)轴承:用于支撑转向齿轮,使其顺畅运转。
2.3系统工作原理当驾驶员通过方向盘控制转向时,方向盘传递力量到转向齿轮上,通过转向齿轮转动和转向杆的传动作用,使车轮转向。
其中,转向齿轮是通过齿轮副传动,将方向盘的旋转运动转换成轴向运动,控制车轮的转向角度。
2.4系统性能(1)灵敏度:驾驶员控制方向盘时,系统应能快速反应,确保车辆转向灵敏。
(2)舒适性:转向时不应有任何异响或抖动感,使驾驶员的操控更加舒适。
(3)可靠性:系统应具有较高的可靠性和耐久性,确保在各种路况下的转向操作安全。
三、结论本转向系统是一种新型的汽车转向系统,采用传统的齿轮传动技术,实现车辆转向操作。
系统整体性能较强,灵敏度高、舒适性好、可靠性强。
同时,本系统还具有可扩展性,在不断的设计应用和技术进步中,可为用户提供更多更好的服务。
转向梯形机构设计报告
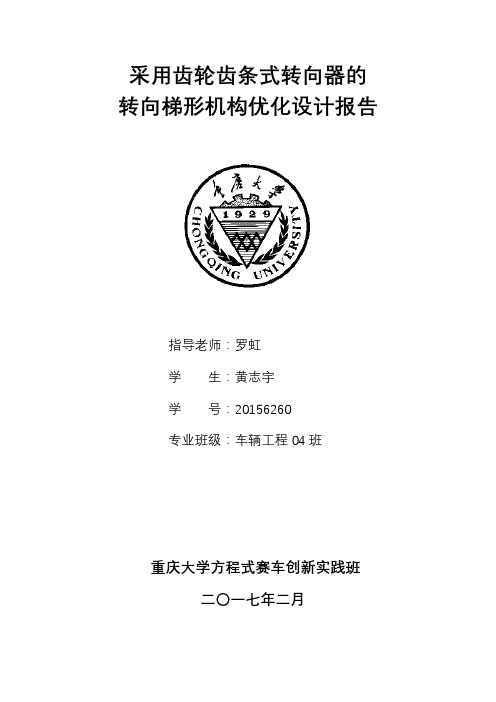
采用齿轮齿条式转向器的转向梯形机构优化设计报告指导老师:***学生:黄志宇学号:********专业班级:车辆工程04班重庆大学方程式赛车创新实践班二〇一七年二月赛车转向系统是关系到赛车性能的主要系统,它是用来改变或恢复汽车行驶方向的系统的总称,通常,车手通过转向系统使转向轮偏转一定角度实现行驶方向改变。
赛车转向系统一股由方向盘、快拆、转向轴、转向柱、万向节、转向器、转向拉杆、梯形臂等部分组成。
其中,方向盘用于输入转向角度,快拆用于快速分离方向盘与转向柱,转向柱、转向轴、万向节共同将方向盘输入角度传递到转向器,转向器通过内部传动副机构将旋转运动转化为转向拉杆的直线运动,转向拉杆与梯形臂作用于转向节,实现车轮转向。
图1展示了转向系梯形结构,图2展示了赛车转向系统构成。
图1转向梯形机构图2赛车转向系统构成由于大赛组委会规则里面明确规定不允许使用线控或者电动转向,考虑到在赛车转向系统布置空间有限,且有严格的成本限制,以及轻量化的赛车设计目标,将赛车转向器范围限定机械式转向器。
目前,国内外的大多数方程式赛车采用齿轮齿条式转向器和断开式转向梯形结构。
●齿轮齿条式转向器齿轮齿条式转向器的传动副为齿轮齿条,其中,齿轮多与转向柱做成一体,齿条多与转向横拉杆直接连接,连接点即为断开点位置。
根据输出位置不同,分为两端输出式和中间输出式。
其主要优点是:结构简单,体积小,易于设计制作;转向器可选材料多样,壳体可选用招合金,质量轻;传动效率较高;容易实现调隙,当齿轮齿条或者齿条与壳体之间产生间隙时,可以通过安装在齿条背部的挤压力可调的弹簧来消除间隙;转向角度大,制造成本低。
其主要缺点是:传动副釆用齿轮齿条,正效率非常髙的同时,逆效率非常高,可以到达当汽车在颠簸路面上行驶时,路感反馈强烈,来自路面的反冲力很容易传递到方向盘;转向力矩大,驾驶员操纵费力,对方向盘的反冲容易造成驾驶员精神紧张,过度疲劳。
●断开式转向梯形结构根据转向器和梯形的布置位置的不同,断开式转向梯形又分为四类,分别为:转向器前置梯形前置,转向器后置梯形后置,转向器前置梯形后置,转向节后置梯形前置。
- 1、下载文档前请自行甄别文档内容的完整性,平台不提供额外的编辑、内容补充、找答案等附加服务。
- 2、"仅部分预览"的文档,不可在线预览部分如存在完整性等问题,可反馈申请退款(可完整预览的文档不适用该条件!)。
- 3、如文档侵犯您的权益,请联系客服反馈,我们会尽快为您处理(人工客服工作时间:9:00-18:30)。
实验一:可分离式汽车转向操作机构设计与三维CAD建模分析实验报告一、实验过程说明1、引言随着社会经济和汽车工业的发展,汽车变得越来越普及。
汽车转向管柱作为驾驶员操控汽车的重要部件,其安全性和可靠性显得尤为重要。
在汽车行驶的过程中,任何来自转向管柱的异响、卡滞和变形过大都会给驾驶员造成很大的心理压力,影响行车安全。
转向管柱主要包括转向轴总成、上柱管、管柱支架、紧定螺栓、拉脱锁、下柱管、下支架、旋铆销轴、锁定手柄等。
转向轴总成通常是上端加工有连接花键,用来安装方向盘;下端焊接有万向节总成,与转向器连接,实现转向扭矩的传递。
上、下柱管装配在一起,通过管柱支架和下支架安装在车架上。
拉脱锁与管柱支架通过注塑装配在一起。
它的作用是将驾驶员转动转向盘的操纵力传给转向器。
同时装有转向柱管安全装置和方向盘位置调节装置,分别是用于当转向轴受到巨大的冲击时产生轴向位移,使支架或支撑塑性变形来吸收冲击能量,防止驾驶人员因转向机构原因而受伤;以及因驾驶员身高不同,把握方向盘时要调整方向盘的高度来达到安全舒适的状态。
转向操作机构是汽车上不可或缺的一部分,其工作可靠性直接影响行驶安全。
本实验是根据机械原理,参考大众新桑塔纳转向操作机构参数,设计了转向操作机构的传动机构和动力机构。
并运用本课程所学的知识,基于UG建模软件对转向操作机构的机构零件进行结构设计和优化,然后运用ADAMS运动学仿真软件对转向操作机构进行仿真分析以及动画制作,对相关的参数进行分析,终完成本转向操作机构的简易设计。
2、可分离式机构设计方案与参数计算(1)设计方案根据网上查找的资料,转向吸能装置的设计方案一般有如下几种:①可分离式机构简图如图2.1所示。
此类转向操纵机构的转向管柱分为上下两段,当发生撞车时,上下两段相互分离或相互滑动,从而有效地防止转向盘对驾驶员的伤害,但转向机构本身并不包含吸能装置。
②网格管、波纹管变形吸能式机构简图如图2.2所示。
其转向操纵机构的转向轴和转向管柱都分成两段,上转向轴和下转向轴之间通过细花键结合并传递转向力矩,同时它们二者之间可以作轴向伸缩滑动。
在下转向轴的外边装有波纹管,它在受到压缩时能轴向收缩变形并消耗冲击能量。
它的下转向管柱的上端套在上转向管柱里面,但二者不直接连接,而是通过管柱压圈和限位块分别对它们进行定位。
当汽车撞车时,下转向管柱向上移动,在第一次冲击力的作用下限位块首先被剪断并消耗能量,与此同时转向管柱和转向轴都作轴向收缩。
当受到第二次冲击时,上转向轴下移,压缩波纹管使之收缩变形并消耗冲击能量。
③钢球滚压变形式机构简图如图2.3所示。
其结构分为转向管柱上下两段,上转向管柱比下转向管柱稍细,可套在下转向管柱的内孔里,二者之间压入带有塑料隔圈的钢球。
隔圈圈起钢球保持架的作用,钢球与上下转向管柱压紧并使之结合在一起。
在撞车时,上下管柱在轴向相对移动,这时钢球边转动边在上下转向管柱的壁上压出沟槽,从而消耗了冲击能量。
④支架变形缓冲式机构简图如图2.4所示。
发生碰撞时,转向器向后移动,下转向传动轴插入上转向传动轴的孔中,上转向传动轴被压扁,吸收了冲击能量。
此外,转向管柱通过支架和U形金属板固定在仪表板上。
当驾驶员身体撞击转向盘后,转向管柱和支架将从仪表板上脱离下来向前移动。
这时,一端固定在仪表板上而另一端固定在支架上的U形金属板就会产生扭曲变形并吸收冲击能量。
图2.1图2.2图2.3 图2.4(2)设计要求根据汽车驾驶的要求,汽车转向操作机构有如下设计要求:①操纵轻便,转向系应有能使驾驶员免遭或减轻伤害的防伤装置。
②转向盘转动方向与汽车行驶方向的改变相一致。
③按照《防止汽车转向机构对驾驶员伤害的规定》的试验程序,人体模块以24.1km/h—25.3km/h的相对速度撞击转向操纵装置时,转向操纵装置作用在人体模块上的水平力不得超过11123N。
④转向操纵装置面向驾驶员侧能被直径为165mm球体接触的部分应平滑,尖角或凸起部位的圆角半径不得小于2.5mm。
⑤压缩行程:转向柱及中间轴的可压缩行程150mm以上;⑥转向柱系统烦人最小临界压力:1.1—2.5kN;⑦转向柱断开联接盒分离力:联接盒每个注塑销的破坏力为500N,转向柱上每个可断裂联接盒一般有2—4个注塑销;⑧除了保证规定的轴向压缩力外,还要足够的抗弯强度,以提高轴向吸能效果;⑨压缩吸能部分上下端有一定的强度和刚度差异,保证压缩吸能力的传递根据设计要求,综合考虑其他因素,参考上诉第一种设计方案进行设计。
把汽车转向操作机构机构主要分成三部分:一部分机构为方向盘机构,主要由骨架等组成,通过矩形细花键与转向轴上端相连,并用螺母轴向固定限位;另一部分的机构为上转向轴,从转向管柱中穿过并通过支撑轴承和上端轴承支撑在转向管柱中,转向轴上下端用弹性挡圈轴向限位;另一部分为转向柱管,用支架固定在驾驶室的前围板上,转向柱管上装有组合开关、点火开关等部件。
本次设计中传动机构使用可分离式缓冲吸能机构,动力机构参照实际汽车的转向操纵机构为动力部分,简化为传动机构得到汽车转向操作机构完整的机构简图如图2.5所示:图2.5 汽车转向操作机构机构运动简图该机构的参数如下:Dab=385mm,Lcd=836mm,Lef=457mm,Lgh=319mm。
此机构中传动机构处于极位,且同时处于死点锁死位置;动力机构(即方向盘机构AB)是转向动力机构,且传动过程中无死点。
计算机构的自由度:F=3*6-2*8-1=1。
方向盘为主动件时,已知自由度为1,所以,该机构具有确定的相对运动。
3、可分离式机构运动学设计与仿真验证将装配好的转向操作机构模型从UG中导出为.xmt格式,之后将其导入到Adams软件中进行运动学仿真。
添加好各项运动副,将方向盘分别设置为驱动,辅以STEP(TIME......)时间函数,实现转向操作机构运动方向盘调节动作。
图3.1 导入UG中导出的.xmt文件图3.2 加载约束模型图3.3 模型自由度验证模型4、可分离式机构三维CAD建模设计与分析(1)传动机构的设计起初设计为波纹管式转向操作机构,之后不易对其进行仿真,所以改为可分离式转向操作机构。
传动机构为上下两轴的连接传动,其中上转向轴长度为823mm,下转向轴长度为460mm,且满足转向轴条件。
转向轴主要的尺寸为直径为35mm,转向管柱最大直径为95mm。
图4.1为传动机构的结构三维模型图。
图4.1 传动机构三维模型(2)动力机构的设计动力机构为方向盘机构及手柄的调节装置,其中方向盘最大直径为385mm,方向盘调节装置的滑槽长度为80mm,可以对方向盘进行伸缩调节,手柄的调节角度为30°。
方向盘与转向轴连接成转动副。
动力机构的结构如图4.2所示。
转向操作机构整体结构图如图4.3和图4.4所示。
图4.2 动力机构三维建模图4.3 波纹管式转向机构三维建模图4.4 可分离式转向操作机构三维建模5、可分离式机构动力学分析与仿真(1)运动分析将转向操作机构的三维模型导入ADAMS软件中,对各个构件进行约束,然后动画仿真分析,仿真结果分别如图5.2、5.3和5.4所示.图5.1 转向操作机构前后调节图5.2 转向操作机构前后调节图5.3 分离式缓冲吸能该机构的主动件为方向盘,通过给方向盘施加一个与水平面成30°角的力,在动力机构中产生传递,作用于传动机构,使转向操作机构上下转向轴进行分离。
由之前的方案确定知道该转向操作机构的各个参数设计,现在对该转向操作机构进行运动学仿真分析。
在方向盘与地面之间添加单向力为11000N,设置的仿真时间为5s,仿真过程中上转向轴的位移、速度、加速度分别如图5.4、图5.5、图5.6所示。
图5.4 上转向轴位移图5.5 上转向轴速度图5.6 上转向轴加速度由图5.4、图5.5和图5.6可知,上转向轴下滑动,位移为H=135mm,且加速度突变,减少了对人体的刚性冲击。
该机构从动件为下转向轴,下转向轴的速度如图5.7所示。
图5.7 下转向轴位移从动件下转向轴的速度如图5.8所示。
图5.8 下转向轴速度曲线由图5.7、图5.8可知,从动件下转向轴向下运动,且加速度无突变,为上转向轴的滑动提供了空间。
(2)静力分析(不计重力)汽车共有1个转向操作机构,查资料知中型汽车对人体的冲击力不能超过11123N,上下转向轴之间阻力不得超过500N。
在ADAMS中对各个构件进行修改,将重力设置为0。
将初始给方向盘的力为11000N施加在方向盘质心上,运动仿真得传动件上转向轴的动能如图5.9所示.图5.9 传动件上转向轴的动能上下转向轴之间连接螺栓的摩擦曲线如图5.10所示:图5.10 连接处的摩擦上下转向轴之间连接处的轴套力如图5.11所示:图5.11 连接处的力曲线由上述仿真图可知构件上转向轴做向下滑动吸收冲击的能量,符合转向操作机构防伤功能,且从动件受较大的力,但是主动件需要施加的力合理,才能有利于控制;固定连接处的螺栓受到的力有集中突变,在结构设计的时候需要加以注意。
(3)吸能检验把汽车转向操作机构的上转向轴加入平移驱动,上下转向轴之间连接处摩擦,所有约束加载以后测量转向操作机构在冲击力作用吸收能量的曲线。
利用ADAMS软件进行测量,结果如图5.12所示:图5.12 转向轴吸能能量吸收式转向柱除了要保证汽车正常行驶时的传递转向扭矩外,当汽车发生正面碰撞,碰撞力达到一定值时,转向轴可以伸长、压缩、弯曲或断开以消除转向齿轮的后移影响,达到隔绝首次碰撞影响的目的,满足传动条件。
6、可分离式机构主要零件加工工艺与建模方法分析上转向轴、下转向轴的三维模型图分别如图6.1、6.2所示。
图6.1 上转向轴图6.2 下转向轴图6.3 转向轴装配图1.主要加工工艺(1)尺寸精度轴颈是轴类零件的主要表面,它影响轴的回转精度及工作状态。
轴颈的直径精度根据其使用要求通常为IT6~9,精密轴颈可达IT5。
(2)几何形状精度轴颈的几何形状精度(圆度、圆柱度),一般应限制在直径公差点范围内。
对几何形状精度要求较高时,可在零件图上另行规定其允许的公差。
(3)位置精度主要是指装配传动件的配合轴颈相对于装配轴承的支承轴颈的同轴度,通常是用配合轴颈对支承轴颈的径向圆跳动来表示的;根据使用要求,规定高精度轴为0.001~0.005mm,而一般精度轴为0.01~0.03mm。
此外还有内外圆柱面的同轴度和轴向定位端面与轴心线的垂直度要求等。
(4)表面粗糙度根据零件的表面工作部位的不同,可有不同的表面粗糙度值,例如普通机床主轴支承轴颈的表面粗糙度为Ra0.16~0.63um,配合轴颈的表面粗糙度为Ra0.63~2.5um,随着机器运转速度的增大和精密程度的提高,轴类零件表面粗糙度值要求也将越来越小。