铸造模具在砂型铸造中的重要性
砂型铸造模具设计及制造分析
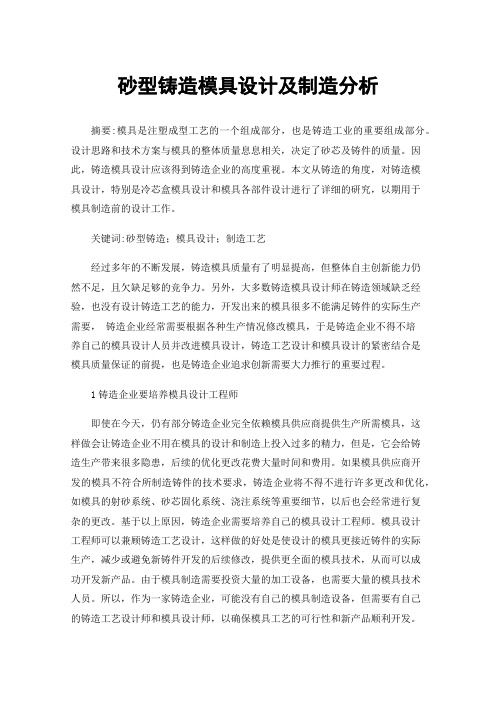
砂型铸造模具设计及制造分析摘要:模具是注塑成型工艺的一个组成部分,也是铸造工业的重要组成部分。
设计思路和技术方案与模具的整体质量息息相关,决定了砂芯及铸件的质量。
因此,铸造模具设计应该得到铸造企业的高度重视。
本文从铸造的角度,对铸造模具设计,特别是冷芯盒模具设计和模具各部件设计进行了详细的研究,以期用于模具制造前的设计工作。
关键词:砂型铸造;模具设计;制造工艺经过多年的不断发展,铸造模具质量有了明显提高,但整体自主创新能力仍然不足,且欠缺足够的竞争力。
另外,大多数铸造模具设计师在铸造领域缺乏经验,也没有设计铸造工艺的能力,开发出来的模具很多不能满足铸件的实际生产需要,铸造企业经常需要根据各种生产情况修改模具,于是铸造企业不得不培养自己的模具设计人员并改进模具设计,铸造工艺设计和模具设计的紧密结合是模具质量保证的前提,也是铸造企业追求创新需要大力推行的重要过程。
1铸造企业要培养模具设计工程师即使在今天,仍有部分铸造企业完全依赖模具供应商提供生产所需模具,这样做会让铸造企业不用在模具的设计和制造上投入过多的精力,但是,它会给铸造生产带来很多隐患,后续的优化更改花费大量时间和费用。
如果模具供应商开发的模具不符合所制造铸件的技术要求,铸造企业将不得不进行许多更改和优化,如模具的射砂系统、砂芯固化系统、浇注系统等重要细节,以后也会经常进行复杂的更改。
基于以上原因,铸造企业需要培养自己的模具设计工程师。
模具设计工程师可以兼顾铸造工艺设计,这样做的好处是使设计的模具更接近铸件的实际生产,减少或避免新铸件开发的后续修改,提供更全面的模具技术,从而可以成功开发新产品。
由于模具制造需要投资大量的加工设备,也需要大量的模具技术人员。
所以,作为一家铸造企业,可能没有自己的模具制造设备,但需要有自己的铸造工艺设计师和模具设计师,以确保模具工艺的可行性和新产品顺利开发。
2铸造工艺设计2.1分型面的选择在砂型铸造中,分型面选择合理可以简化组芯、造型操作,提高生产率,在选择分型面时一般需要考虑以下几个方面:为便于起模,一般分型面应选择在铸件最大截面处,一个截面无法起模时,局部阻碍起模的形状可做成活块,尽可能减少分型面和活块数量。
铸造模具方法
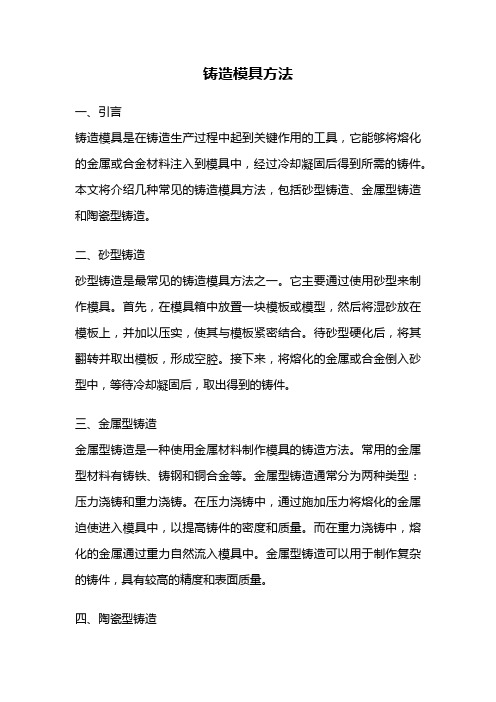
铸造模具方法一、引言铸造模具是在铸造生产过程中起到关键作用的工具,它能够将熔化的金属或合金材料注入到模具中,经过冷却凝固后得到所需的铸件。
本文将介绍几种常见的铸造模具方法,包括砂型铸造、金属型铸造和陶瓷型铸造。
二、砂型铸造砂型铸造是最常见的铸造模具方法之一。
它主要通过使用砂型来制作模具。
首先,在模具箱中放置一块模板或模型,然后将湿砂放在模板上,并加以压实,使其与模板紧密结合。
待砂型硬化后,将其翻转并取出模板,形成空腔。
接下来,将熔化的金属或合金倒入砂型中,等待冷却凝固后,取出得到的铸件。
三、金属型铸造金属型铸造是一种使用金属材料制作模具的铸造方法。
常用的金属型材料有铸铁、铸钢和铜合金等。
金属型铸造通常分为两种类型:压力浇铸和重力浇铸。
在压力浇铸中,通过施加压力将熔化的金属迫使进入模具中,以提高铸件的密度和质量。
而在重力浇铸中,熔化的金属通过重力自然流入模具中。
金属型铸造可以用于制作复杂的铸件,具有较高的精度和表面质量。
四、陶瓷型铸造陶瓷型铸造是一种使用陶瓷材料制作模具的铸造方法。
它通常用于高温合金的铸造,如钨合金、钼合金等。
陶瓷型铸造的制造过程相对复杂,需要经过多道工序。
首先,制作陶瓷型芯。
然后,在陶瓷型芯的周围制作陶瓷型壳。
接下来,将熔化的金属或合金注入陶瓷型芯中,待冷却凝固后,取出得到的铸件。
陶瓷型铸造可以制作出高精度、高温下使用的铸件。
五、其他铸造模具方法除了上述三种常见的铸造模具方法,还有一些其他的方法。
例如,失蜡铸造是一种使用蜡型制作模具的铸造方法,适用于制作复杂的铸件。
再如,凝胶铸造是一种使用凝胶模具制作模具的铸造方法,适用于制作高精度的铸件。
六、总结铸造模具方法的选择取决于铸件的形状、尺寸、材料以及生产需求等因素。
砂型铸造、金属型铸造和陶瓷型铸造是常见的几种方法,它们各自具有优势和适用范围。
了解不同的铸造模具方法可以帮助我们选择适合的方法来满足生产需求,提高铸件的质量和效率。
砂型铸造流程
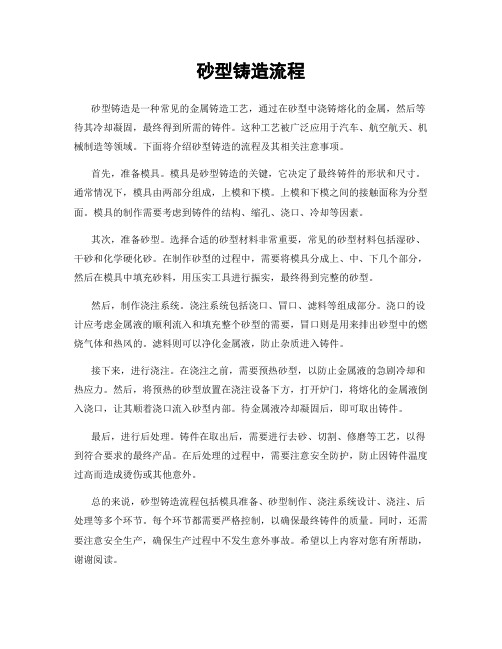
砂型铸造流程砂型铸造是一种常见的金属铸造工艺,通过在砂型中浇铸熔化的金属,然后等待其冷却凝固,最终得到所需的铸件。
这种工艺被广泛应用于汽车、航空航天、机械制造等领域。
下面将介绍砂型铸造的流程及其相关注意事项。
首先,准备模具。
模具是砂型铸造的关键,它决定了最终铸件的形状和尺寸。
通常情况下,模具由两部分组成,上模和下模。
上模和下模之间的接触面称为分型面。
模具的制作需要考虑到铸件的结构、缩孔、浇口、冷却等因素。
其次,准备砂型。
选择合适的砂型材料非常重要,常见的砂型材料包括湿砂、干砂和化学硬化砂。
在制作砂型的过程中,需要将模具分成上、中、下几个部分,然后在模具中填充砂料,用压实工具进行振实,最终得到完整的砂型。
然后,制作浇注系统。
浇注系统包括浇口、冒口、滤料等组成部分。
浇口的设计应考虑金属液的顺利流入和填充整个砂型的需要,冒口则是用来排出砂型中的燃烧气体和热风的。
滤料则可以净化金属液,防止杂质进入铸件。
接下来,进行浇注。
在浇注之前,需要预热砂型,以防止金属液的急剧冷却和热应力。
然后,将预热的砂型放置在浇注设备下方,打开炉门,将熔化的金属液倒入浇口,让其顺着浇口流入砂型内部。
待金属液冷却凝固后,即可取出铸件。
最后,进行后处理。
铸件在取出后,需要进行去砂、切割、修磨等工艺,以得到符合要求的最终产品。
在后处理的过程中,需要注意安全防护,防止因铸件温度过高而造成烫伤或其他意外。
总的来说,砂型铸造流程包括模具准备、砂型制作、浇注系统设计、浇注、后处理等多个环节。
每个环节都需要严格控制,以确保最终铸件的质量。
同时,还需要注意安全生产,确保生产过程中不发生意外事故。
希望以上内容对您有所帮助,谢谢阅读。
砂型铸造的概念

砂型铸造的概念
砂型铸造是一种常见的金属铸造方法,它通过使用砂型来制造各种复杂形状的金属件。
砂型铸造是铸造工艺中最古老和最常用的方法之一。
在砂型铸造中,首先需要制造一个砂型。
砂型通常由特殊的砂料和粘结剂组成,以确保其在铸造过程中能够保持稳定的形状。
制作砂型的过程称为模具制造。
模具制造通常涉及将模具分成两个或更多的部分,以便能够容易地脱模并取出铸件。
制作好的砂型将具有所需的空腔形状,以便于金属的浇注和凝固。
在铸造过程中,金属通常以液态形式注入砂型中。
一旦金属充满整个砂型腔体,它将开始冷却和凝固。
当金属完全凝固后,砂型可以被拆除,从而获得所需的金属件。
这个过程被称为脱模。
砂型铸造具有许多优点。
首先,它相对简单,成本相对较低。
砂型可以根据需要定制,因此可以制造出各种形状和尺寸的铸件。
此外,砂型铸造适用于几乎所有的金属材料,包括铁、铝、铜、镁等。
然而,砂型铸造也有一些限制。
首先,由于砂型的使用,表面质量相对较差,需要进行后续加工。
此外,砂型的使用寿命有限,通常只能用于少量的铸件。
较复杂的形状可能需要制造更复杂的砂型,这可能
会增加制造成本和时间。
总之,砂型铸造是一种常用的金属铸造方法,它通过使用砂型制造各种形状的金属件。
尽管存在一些限制,但砂型铸造仍然是一种广泛应用的铸造方法,适用于许多不同类型的铸件制造。
翻砂铸造知识(铸造木模、金属铝模)

金属模是用金属做的模子,翻砂模是翻砂用的模型,即造型用的模型,包括木模、金属模、树脂模,塑料模。
金属模又包括铝模、铁模、钢模等等。
铸件模具主要分为金属模、塑料模、木模具、泡沫模四大类,这是按照使用寿命排列的顺序,价格也是依次降低。
砂型铸造,如果零件表面要求高,批量大,一般会采用金属模具进行造型,其次会选用塑料模(树脂模具)造型,这两种模具成本较高,但零件尺寸能的以有效保证;假如零件表面要求不是很高,或属于小批量单件生产的,一般采用木模具造型,成本低!泡沫模主要用于消失模铸造,尺寸精度很高,但是一次性投入较大,泡沫不能回用。
而对于复杂铸件内腔来说,如柴油机缸盖水腔、排气管等等,一般的金属模是无法保证的,这个要根据工艺特点制作特殊的用于热(冷)芯盒生产的专用金属模具。
翻砂是将熔化的金属浇灌入铸型空腔中,冷却凝固后而获得产品的生产方法。
在汽车制造过程中,采用铸铁制成毛坯的零件很多,约占全车重量的60%左右,如气缸体、变速器箱体、转向器壳体、后桥壳体、制动鼓、各种支架等。
制造铸铁件通常采用砂型。
砂型的原料以砂子为主,并与粘结剂、水等混合而成。
砂型材料必须具有一定的粘合强度,以便被塑成所需的形状并能抵御高温铁水的冲刷而不会崩塌。
为了使砂型内塑成与铸件形状相符的空腔,必须先用木材制成模型,称为木模。
炽热的铁水冷却后体积会缩小,因此,木模的尺寸需要在铸件原尺寸的基础上按收缩率加大,需要切削加工的表面相应加厚。
空心的铸件需要制成砂芯子和相应的芯子木模(芯盒)。
有了木模,就可以翻制空腔砂型。
在制造砂型时,要考虑上下砂箱怎样分开才能把木模取出,还要考虑铁水从什么地方流入,怎样灌满空腔以便得到优质的铸件。
砂型制成后,就可以浇注,也就是将铁水灌入砂型的空腔中。
浇注时,铁水温度在1250—1350度,熔炼时温度更高。
然后还要经过除砂、修复、打磨等过程,才能够成为一件合格铸件。
铸造砂铸造砂铸造生产中用来配制型砂和芯砂的一种颗粒状耐火材料。
砂型铸造工艺流程

砂型铸造工艺流程一、砂型铸造简介砂型铸造是一种常用的铸造方法,通过使用砂模来制造金属铸件。
砂型铸造工艺流程包括模具制备、砂型制备、浇铸、冷却、脱模和后处理等步骤。
本文将详细介绍砂型铸造的工艺流程及每个步骤的具体操作。
二、模具制备在砂型铸造中,模具是制作砂型的重要工具。
首先需要准备好铸造所需的模子。
模子可以使用木模、金属模或者其他材料制作而成。
模具制备的具体步骤如下:1.设计模具结构–根据所需铸件的结构和尺寸,设计模具的内外形状和结构。
–考虑到铸件的收缩率和热胀冷缩等因素,在设计模具时需要留出相应的缩孔和浇口。
2.制作模具–根据设计图纸,选择合适的模具材料进行制作。
–使用机械加工或者手工加工的方式,按照设计图纸的要求制作模具的内外形状。
3.组装模具–将制作好的模具组装在一起,确保模具内外表面的高度一致,以保证最终铸件的尺寸精度。
–使用螺栓或者其他连接方式将模具牢固地固定在一起。
三、砂型制备砂型是铸造的关键步骤之一,其质量直接影响到最终铸件的质量。
砂型制备的具体步骤如下:1.选择砂料–根据铸件的性质和金属的种类,选择适合的砂料。
–砂料应具有良好的塑性和耐高温的特性,以便能够更好地填充模具。
2.调配砂料–将砂料和适量的粘结剂混合,用水使其充分搅拌均匀。
–确保砂料的湿度适中,既能够起到黏合作用,又不会因过度湿润而影响成型效果。
3.成型砂型–将调配好的砂料倒入模具中,使用工具进行压实,确保砂料填充整个模具空间。
–模具中的芯子应根据需要放置在合适的位置,以形成中空的铸件结构。
4.敲击模具–使用锤子等工具敲击模具的四周和底部,以去除空气泡并提高砂型的密实度。
–确保模具表面平整光滑,以便于浇铸过程中金属的流动。
5.脱模–等待砂型充分硬化后,将模具分离并轻轻敲击,使铸件和砂型分离。
–检查铸件和砂型的质量,并进行必要的修整和清理。
四、浇铸浇铸是将熔融金属倒入砂型中的过程。
在浇铸之前,需要进行一系列准备工作:1.预热砂型–在浇铸之前,将砂型预热以提高砂型的温度稳定性。
砂型铸造通用技术规范最新版
砂型铸造通用技术规范最新版砂型铸造是一种常见的铸造工艺,通过在模具中填充砂子并将其固化,然后在固化的砂型中倒入熔融金属,待金属冷却凝固后取出,得到所需产品。
为了确保砂型铸造的质量和效率,制定了一系列的砂型铸造通用技术规范。
一、砂型铸造材料规范1. 砂型铸造用砂应选用合适的砂子,具有良好的耐热性和粘结性,保证铸件的表面质量和尺寸精度;2. 砂型铸造砂子的组成和比例应符合工艺要求,避免因过多的添加剂对铸件质量造成不良影响;3. 砂型铸造砂子的处理要求,如筛选、干燥等,保证砂子的质量和适用性。
二、砂型铸造模具设计规范1. 砂型铸造模型应根据铸件的形状、尺寸和结构特点合理设计,保证铸件的准确度和外观质量;2. 砂型铸造模具应采用适当的材料,具有足够的强度和刚度,可靠地承受铸造过程中的挤压力和热应力;3. 砂型铸造模具的结构应合理,易于脱模,减少破损和报废率。
三、砂型铸造工艺规范1. 砂型铸造工艺中,要控制铸造温度、浇注速度和金属的液态时长,保证铸件的质量和性能;2. 砂型铸造时,要注意金属液流动的方向和填充的均匀性,避免产生气孔、缩松等缺陷;3. 砂型铸造后,要进行适当的铸件清理和修整工作,如修边、抛光等,使其达到要求的外观质量。
四、砂型铸造检测规范1. 砂型铸造铸件的检测主要包括外观检验、尺寸测量和性能试验等;2. 外观检验要求铸件表面光滑,无缺陷和毛刺;3. 尺寸测量要求按照设计要求进行,对于特殊要求的铸件要进行形状测量;4. 砂型铸造铸件的性能试验包括强度、硬度、耐磨性等试验,保证铸件的使用性能。
以上为砂型铸造通用技术规范的主要内容,对于砂型铸造工艺的实施具有指导作用。
不同的铸造企业可以根据自身的实际情况进行相应的调整和补充,以确保铸造的质量和效率。
五种常见的铸造工艺及其在铸造行业中的应用案例
五种常见的铸造工艺及其在铸造行业中的应用案例铸造工艺是一种常见的制造工艺,用于生产各种金属制品和零部件。
本文将介绍五种常见的铸造工艺,并通过应用案例来展示它们在铸造行业中的实际运用。
一、砂型铸造工艺砂型铸造是最常见和传统的铸造工艺之一。
它使用砂型作为铸型材料,将液态金属倒入模具中,待金属凝固后,砂型被破碎以得到铸件。
这种工艺广泛应用于生产大型铸件,如发动机缸盖和机床床身等。
案例一:汽车制造业中的缸体铸造在汽车制造业中,发动机的缸体通常是用砂型铸造工艺生产的。
砂型可以灵活地制作出各种复杂形状和内腔结构,满足汽车发动机缸体的要求。
二、金属型铸造工艺金属型铸造是一种使用金属模具的铸造工艺。
金属模具可以重复使用,提高了生产效率和产品质量。
这种工艺适用于生产高精度和大批量的铸件。
案例二:飞机引擎叶片的制造飞机引擎叶片是需要具备高精度和高强度的金属部件。
金属型铸造工艺可以制造出符合要求的叶片,有助于提高飞机引擎的性能。
三、压铸工艺压铸是一种将液态金属注入高压模具中,通过施加压力使金属充填模腔的铸造工艺。
压铸可用于生产精密度高、尺寸复杂的铸件。
案例三:手机外壳的生产手机外壳通常由铝合金或镁合金制成,具有精密的尺寸和复杂的结构。
压铸工艺能够满足手机外壳的质量和生产效率要求。
四、连续铸造工艺连续铸造是一种将液态金属连续倒入模具中,通过连续冷却和切割得到连续条状铸坯的工艺。
它适用于生产长条状铸件,如铁路轨道和钢板等。
案例四:钢铁工业中的连铸连铸广泛应用于钢铁工业,以生产各种规格和长度的钢坯。
通过连续铸造工艺,可以提高钢坯的质量和生产效率。
五、精密铸造工艺精密铸造是一种生产高精度和复杂形状铸件的工艺。
它通常结合了其他铸造工艺,如石膏型铸造和失蜡铸造等。
案例五:航空航天领域中的精密铸造在航空航天领域,精密铸造被广泛应用于生产航空发动机的复杂部件,如叶轮、涡轮等。
精密铸造工艺的使用可以确保零部件的高精度和性能要求。
总结:通过对五种常见铸造工艺的介绍和应用案例的展示,可以看出在铸造行业中这些工艺的重要性和广泛运用。
砂型铸造工艺及工装设计
砂型铸造工艺及工装设计一、工艺流程设计砂型铸造的工艺流程设计是整个工艺的基础,包括以下步骤:设计铸造模具:根据产品需求和工艺要求,设计铸造模具的结构和尺寸。
制作砂型:根据模具和产品需求,制作符合要求的砂型。
浇注:将熔融的金属液体注入砂型,填充模具的型腔。
冷却:让金属液体冷却凝固,形成铸件。
脱模:将凝固的铸件从砂型中脱出,完成整个铸造过程。
二、铸造模具设计铸造模具的设计是整个工艺的核心,直接影响产品的质量和工艺的效率。
设计时需考虑以下几点:模具材料选择:根据产品需求和工艺要求,选择合适的模具材料。
模具结构确定:根据产品形状和尺寸,设计模具的结构和形状。
模具尺寸精度:根据产品要求和工艺条件,确定模具的尺寸精度。
浇口设计:浇口是金属液体注入模具的通道,设计时需考虑浇口的尺寸、位置和形式。
排气口设计:排气口是排除模具内的空气和挥发物的通道,设计时需考虑排气口的位置和大小。
三、砂型制作工艺设计砂型制作是整个工艺的重要环节,其质量直接影响产品的质量和工艺的效率。
设计时需考虑以下几点:砂型材料选择:选择符合要求的砂型材料,如黄沙、石英砂等。
砂型紧实度控制:控制砂型的紧实度,以保证砂型的强度和稳定性。
砂型透气性控制:控制砂型的透气性,以保证浇注过程中金属液体能够顺利填充模具的型腔。
砂型表面处理:对砂型的表面进行处理,以提高产品的表面质量。
四、浇注系统设计浇注系统是金属液体注入模具的通道,其设计直接影响到金属液体的流动和填充效果。
设计时需考虑以下几点:浇注系统结构形式:根据产品要求和工艺条件,选择合适的浇注系统结构形式。
浇注系统尺寸精度:根据产品要求和工艺条件,确定浇注系统的尺寸精度。
浇注速度控制:控制浇注速度,以保证金属液体能够平稳、充足地填充模具的型腔。
浇口位置选择:根据产品形状和模具结构,选择合适的浇口位置。
溢流槽设计:溢流槽是收集多余金属液体的结构,设计时需考虑溢流槽的位置和大小。
过滤网设置:过滤网是过滤金属液体中的杂质和气泡的结构,设计时需考虑过滤网的形式和材料。
砂型铸造工艺
砂型铸造工艺砂型铸造工艺是一种常见的金属铸造工艺,也是最古老的铸造方法之一。
它通过将熔化的金属注入制作好的砂型中,经过冷却凝固后得到所需的铸件。
砂型铸造工艺具有成本低、适用范围广、生产周期短等优点,在工业生产中被广泛应用。
砂型铸造的工艺流程可以分为模具制作、铸造操作和铸件处理三个主要步骤。
首先是模具制作。
模具是铸造过程中的重要工具,用于制作铸件的外形和内部结构。
模具制作的首要任务是根据产品的图纸和要求设计出合适的模具形状,并选择适当的砂型材料。
常用的砂型材料有石英砂、石膏砂、水玻璃砂等。
制作模具时需要根据产品的形状和尺寸进行精确的加工和装配,以确保铸件的质量和尺寸精度。
其次是铸造操作。
在进行铸造前,需要先预热模具,以避免热应力对模具的影响。
接下来,将砂型放置在铸造设备中,然后通过加热炉将金属熔化。
一旦金属达到适当的温度,就会倒入模具中。
在倒入金属之前,还需要在砂型中放置冷铁、通道、浇口等辅助构件,以便于金属在砂型中流动和凝固。
倒入金属后,需要等待一段时间,让金属冷却凝固,形成铸件。
最后是铸件处理。
铸件冷却后,需要将其从砂型中取出,并进行后续处理。
这包括切割、修磨、清理等工序,以去除铸件表面的砂粒和气孔,使其达到所需的光洁度和精度。
随后,可以对铸件进行热处理、表面处理等工艺,以提高其力学性能和外观质量。
最后,对铸件进行检验,确保其符合产品要求。
砂型铸造工艺具有许多优点。
首先,它适用于各种复杂形状和尺寸的铸件制造,可以满足不同行业的需求。
其次,砂型铸造成本低廉,模具制作相对简单,不需要复杂的设备和工艺。
此外,砂型铸造还具有生产周期短的优势,可以快速得到所需的铸件。
因此,砂型铸造广泛应用于汽车、航空航天、机械制造等领域。
然而,砂型铸造工艺也存在一些局限性。
首先,砂型铸造对金属材料的要求较高,一些高温和腐蚀性金属难以进行砂型铸造。
其次,在砂型铸造过程中,砂型会因为高温和金属的冲击而破裂,导致模具寿命较短。
- 1、下载文档前请自行甄别文档内容的完整性,平台不提供额外的编辑、内容补充、找答案等附加服务。
- 2、"仅部分预览"的文档,不可在线预览部分如存在完整性等问题,可反馈申请退款(可完整预览的文档不适用该条件!)。
- 3、如文档侵犯您的权益,请联系客服反馈,我们会尽快为您处理(人工客服工作时间:9:00-18:30)。
铸造模具在砂型铸造中的重要性工厂将铸造模具称之为“铸造之母”,此话可谓是对铸造模具在铸造生产中作用和地位的一个高度的概括。
称之为“母”,其一是因为在工厂里,所有铸件都是用铸模制成砂型然后得到的,无铸造模具即无铸件;其二是铸件总是带有铸造模具的“遗传性”;铸件的尺寸精度、表面粗糙度乃至某些铸造缺陷无一不与铸造模具质量有直接关系。
铸件依模而作,模的尺寸误差无一例外地会在铸件上反映出来。
尤其是一些复杂铸件,由于采用多个铸模(外模和芯盒),其累积误差更会严重影响到铸件尺寸精度。
表面光洁的铸模不仅改善起模性,从而减少型(芯)废,提高生产率,而且能得到光洁的型腔(或砂芯),有利于得到光洁的铸件。
一部分铸件缺陷可能由铸造模具质量不佳所造成,如铸模表面存在倒料度、凹凸不平,将导致起模性不好,破坏铸型表面甚至造成砂眼;模具安装偏差或定位销(套)磨损造成错型、挤型、砂眼;浇注系统的随意制作或安装导致金属渣流动偏离工艺设计要求,因而可能造成气孔、缩松等缺陷,等等。
铸造模具用材料铸造模具用材料十分广泛,根据铸件产量的不同即铸造模具使用次数的不同,可分别选用木材、塑料、铝合金、铸铁及钢材等。
木模目前仍广泛应用于手工造型或单件小批量生产中,但随着环境保护要求日益加严,木材使用将日益受到限制,代之而起的将是实型铸造。
实型铸造以泡沫塑料板材为材料,裁剪粘接而成模样,然后浇注而成铸件。
该方法较之用木模,不但节省了木材,而且使铸件有更高的尺寸精度和更好的表面粗糙度,塑料模应用呈上升趋势,尤其是可加工塑料的推向市场和塑料模寿命的提高,更使得塑料模应用日益广泛。
铝合金模由于重量轻、尺寸精度又较高,固此应用仍较广泛。
但近来应用已有减少趋势,部分范围已分别为塑料模(当铸件批量较小时)或铸铁模(当铸件批量较大时)所取代。
铸铁模仍是大批量铸造生产的首选,并被大量使用,它具有强度高、硬度高、耐磨、加工性好、成本低廉、使用寿命长等优点。
近几年来,由于铸造水平的提高,已有越来越多的模样、模底板、型板框等采用强度和耐磨性更高的球铁或低稀土合金灰铸铁制作,而耐热疲劳性能更好的蠕墨铸铁也被用于芯盒材料。
钢材以往主要用于铸模上的标准件、耐磨镶块或内衬,较少用于制作铸造模具本体,因为碳钢使用寿命并不高于球铁或低合金灰铁,而合金钢价格又十分昂贵。
但随着模具加工技术的提高及对铸造模具尺寸稳定性要求的提高,模具钢、铬钼台金钢也用于制作铸造模具。
某厂从法国引进的轿车缸体模具,其模样及芯盒本体均采用40CMD8(法国标准)铬钼台金钢,其使用寿命为:模样100万次,芯盒50万次。
此外,已有越来越多的钢材用于制作模底板、芯盒框架等工装件上。
铸造模具的维护保养工厂应建立铸造工艺装备的维护保养制度,其范围应包括型板(含模样)、模板框、芯盒、砂箱、夹具等,内容则应包括预防性维护和修复性维护。
预防性维护一般只需通过外观检查或测量检查,采用专用或简易工具,即可使工装保持或恢复良好技术状态。
它包括保养和点检。
1、保养保养一般由操作工实施,分为日常保养和定期保养。
日常保养在每天停机后进行,定期保养则一般利用节假日和停产检修期间开展。
清除模样、模板工作表面的积砂、杂物、污垢;清除模样上标识符号表面沾敷的积砂和污垢,检查浇注系统、通气片的固定螺钉“封皮”是否脱落,铸造模具表面是否有磕碰伤,通气针(片)、字牌是否松动、脱落,定位销是否凸起或凹缩等。
清除芯盒分盒面、芯腔内表面及销套上的积砂污垢,清除通气塞、排气槽内的污垢垫砂,检查各部位紧固件是否牢固,有无缺损,检查芯盒滑块、镶块、定位块等是否有松动或位移。
在清除干净后的型板和芯盒表面喷涂分型剂。
检查砂箱的销、套是否有磨损、松动、弯曲、断裂、清除砂箱和定位销、套配合面上沾敷的积砂和污垢以及小铁块、残渣、铁屑等。
检查夹具的各部件是否完整,定位、夹紧机构是否松动,并对各润滑点进行加油润滑。
2、点检点检一般由维修工实施,也分为日常点检和定期检查。
日常点检在每次模具生产使用前进行,内容与保养差不多。
定期检查则是模具使用一定次数后,送模具部门进行划线检查,内容有:1) 检查上、下(或前、后)模型和上、下(或动、静)芯盒的外形错边偏差;2) 检查铸造模具和芯盒芯头位置的准确及尺寸精度;3) 检查铸造模具和芯盒工作面和分型面磨损程度;4) 检查铸造模具和芯盒工作面的几何形状和尺寸精度;5) 检查铸造模具定位点、定位面的位置准确度和尺寸精度;6) 检查芯盒、型板(框)销、套的磨损程度及型板(框)、芯盒本体的变形程度;7) 检查各紧固件、定位销、套是否松动、缺件、下沉;8) 检查通气塞是否有破损或下机现象:9) 检查通气针(片)是否弯曲、橙动、缺件:10) 其他部件如抽块、导轨、斜杠、滚轮等件是否完好;11) 检查备件是否齐全,外观有无缺陷、标志牌是否清晰。
铸造模具的清洗技术树脂砂芯盒的结垢与清洗是我国许多企业多年来一直未能有效解决的难题。
芯盒的结垢不仅造成铸造模具表面粗糙。
严重影响砂芯的外观质量,导致铸件粘砂、尺寸精度降低、严重时则会造成铸件批量废品和铸造模具报废。
树脂砂芯盒中垢物的形成机理,主要是由于芯砂表面的树脂在射砂过程中受到射砂气流的冲击,部分树脂破裂,少量的树脂被挤压粘附于芯盒表面,日积月累逐渐在芯盒表面形成一层坚硬、致密的硬化树脂垢。
因此,射砂压力过大,树脂质量差,芯砂中树脂加入量过高,脱模剂与所用树脂不匹配;芯盒表面粗糙都将促使芯盒结垢。
目前国内外企业在芯盒清洗方面使用了多种清洗方法。
1) 利用化学清洗剂清洗。
2) 利用液体或固体喷砂机喷砂清洗。
3) 采用干球喷射法清洗芯盘。
下面对上述部分清理方法分别作以下介绍:1、液体喷砂机清洗芯盒1) 工作原理以磨液泵和压缩空气为动力,通过喷枪将磨液高速喷射到模具表面,达到光饰铸造模具的目的。
磨液是用对模具有保护作用的载液与一定粒度的磨料(白刚玉砂,玻璃丸等人造磨料)按一定配比混合而成,放置在机体下部的贮箱中。
工作时磨液泵将贮箱中的磨液以一定压力和流量通过磨液管路输入喷枪。
此时,还有一磨液旁路经装置在其中的搅拌喷嘴高速喷出,从而使贮箱中的磨料和载液搅拌均匀;另外压缩空气由外接气源经过(溢)减压阀、电磁阀进入喷枪。
喷枪是直接执行液体喷吵工作的主要部件。
它与磨液、压缩空气管路系统相连接,设置在机体上部密闭的工作舱内。
喷射出的磨液对铸造模具表面冲击磨削后,从圆盘工作台流下,经网孔板返回贮箱,如此循环便完成了对铸造模具的喷射清洗。
2) 清洗工艺根据芯盒不同的工艺要求,有两种工作方式可供选择:①不加压缩空气,只靠磨液泵供给磨液,通过喷嘴加速射向被清洗铸造模具。
适用于定期对芯盒进行一般性清洗保养。
②磨液系统和压缩空气系统同时启动,向喷枪同时提供磨液和压缩空气,使其在喷枪内混合后,经喷嘴向铸造模具表面高速喷射气、磨液流。
由于有气、泵兼施的工作方式,使得喷出的气、磨液流具有更大压力,被载液包裹着的磨液质点动能加大,有效提高了芯盒的清洗能力(主要适用于芯盒表面树脂结垢的清洗)。
3) 工艺方法及参数使用液体喷砂机,压缩空气压力为0.5~0.7MPa,喷射距离为10~120mm左右。
清洗介质选用粒度为90um的玻璃丸或0.125mm(120目)的白刚玉砂对芯盒进行清洗保养(或清除结垢),一般情况下芯盒定期清洗保养时间≤1—2min,而对于表面有树脂结垢的芯盒清洗时间,视芯盒的大小、结垢厚度、形状复杂程度不同而定,通常在5—20min范围内可将芯盒垢物清除干净,而喷射时间对芯盒的尺寸精度和表面粗糙度基本没有影响。
4) 生产效率和经济效益比较①使用液体喷砂机和玻璃丸清洗芯盒的工艺基本上能够将芯盒表面较厚的树脂结垢清理干净,但对于较长时间没有清洗积垢很厚的沟槽处,却难于清除干净。
金属铸造模具的技术要求金属模样绝大多数是由铸造毛坯加工而成的。
因此在进行铸造模具设计时,应根据铸造模具的材料特性、制造条件和使用要求,对铸造模具毛坯和制品提出各方面的要求,才能更好地保证铸造模具的使用质量和合理的制造费用。
1) 铸造模具毛坯的材质性能应符合各项相应标准的要求。
加工后的铸造模具表面不允许有任何铸造缺陷。
为保证铸造模具尺寸的稳定,坯件特别是铸铁铸钢件一般应进行人工时效处理,较大的复杂坯件应进行二次人工时效处理。
2) 对铸造模具制品的要求如下:① 金属铸造模具表面粗糙度。
② 工作形体与加工定位基准的位置极限偏差为±0.05mm。
③ 工作表面的形状尺寸极限偏差是:凸体为0mm,凹体为-0mm,应在技术条件中说明。
④ 铸造模具转接圆弧半径极限偏差:R≤15mm,极限偏差为0.5mm;R>15mm,极限偏差为1.0mm。
⑤ 中小型铸造模具基面(分型面)平面度为0.05mm。
中、大型铸造模具基面平面度为0.1mm。
⑥ 芯头起定位和固定砂芯的作用。
在大量流水生产中,对芯头尺寸精度的要球甚至比对形状尺寸精度的要求更高。
对于手工下芯和水平分型的机械下芯。
铸造模具芯头尺寸≤100mm的尺寸极限偏差一般为0mm,而尺寸>100mm的铸造模具芯头尺寸极限偏差一般为0mm。
砂芯芯头与芯座为间隙配合;对于垂直分型的无箱挤压造型采用下芯框(芯罩)机械下芯时,则砂芯苍头与芯座之间为过盈配合,过盈量一般为0.1~0.4mm。
⑦铸件上的所有铸造圆角都必须在铸造模具上标注清楚。
除产品和铸造工艺要求的圆角在铸造模具上注明以外,应在技术条件中说明未注的铸造内圆角和外圆角的半径数值。
⑧起模斜度。
为了提高工作敛率,少换刀具(数控加工除外),同一铸造模具的起模斜度数值种类越少越好。
除图形中注明者外,未注明的起模斜度数值应在技木条件中说明。
⑨ 铸造模具上的标识。
为了满足现代化管理和铸件质量问题可追溯的需要,产品图和铸造工艺设计者,往往要求在铸造模具上的指定位置做出各种各样的标识,如:零件号、产品商标、生产厂商代号、铸造模具序号、铸件生产时间(生产日期、班次等),以及表示方向的箭头等具有特殊用途的标识。
这些标识,大部分结构比较复杂而小巧,均有特定的标准与规定,且要求铸出后清晰、美观、容易辨认。
因此,应该采用精细加工手段,如电火花加工等来制作这些标识。
有些不需要更换的标识,可以直接在铸造模具本件上做出。
但是,大多数标识是先做成标准件,然后再镶嵌在模铸造模具本体上。
机械造型用金属铸造模具的结构设计为了发挥机械造型的高教率,机械造型用铸造模具不采用活块结构,而采用砂芯或砂胎的结构形式。
铸造模具外形结构决定于产品结构、铸造工艺和制模方法。
铸造模具的内部结构,是在保证模样强度和刚度的前提下进行适当的“挖空”,以减轻铸造模具重量。
机械造型用铸造模具都是与模底板一起使用的。
设计时应根据铸造模具和底板的具体结构。
设计定位准确、牢固可靠的定位固紧结构,以确保铸造模具和模底板之间有准确牢固的定位和锁紧。