机床铣削加工时的工作模态分析方法
基于ANSYS的平面端铣模态及切削响应分析

基于ANSYS的平面端铣模态及切削响应分析平面端铣是一种基本的切削工艺,广泛应用于制造业中。
在切削过程中,铣刀振动会产生切削响应,这可能会影响机床和工件的质量和精度。
因此,模态分析和切削响应分析对于研究铣削过程中振动的影响非常重要。
ANSYS是一种广泛使用的有限元分析软件,可以用于模拟和分析各种机械系统的性能。
在本文中,我们将使用ANSYS进行平面端铣的模态和切削响应分析。
模型建立首先,需要建立平面端铣刀的三维CAD模型。
在ANSYS中,我们可以将该模型导入为STEP或IGES格式。
导入后,还需要将其划分为有限元网格,以便进行有限元分析。
网格划分的质量和密度会直接影响分析结果的准确性和效率。
其次,还需要建立工件和夹紧装置的CAD模型。
这些模型也需导入并进行网格划分,以便进行分析。
在本文中,我们假设工件为一个铝合金矩形块,并将其放置在夹紧装置上。
模态分析在进行切削响应分析之前,需要进行模态分析,以确定系统固有频率和振型。
模态分析可以通过改变系统结构的一些特性,如材料、刚度和几何尺寸,来寻找最优的结构设计。
在进行模态分析时,需要考虑模型的各种边界条件和所涉及的材料的弹性及刚度参数。
在ANSYS中,可以通过设置模型的替代质量等参数,来控制模态分析中的计算精度和速度。
模态分析的结果可以显示出系统的自然频率和相应的振型。
这些信息可以帮助设计者调整结构,以避免共振和过度振动,从而提高整体性能。
切削响应分析一旦完成了模态分析,就可以进行切削响应分析。
这是进一步研究平面端铣刀振动的关键步骤。
在切削过程中,铣刀振动会产生一定的切削力和切削振幅,这可能会导致刀具磨损、加工精度下降或工件损坏等问题。
在ANSYS中,可以通过定义切削场景、工件材料和夹紧装置等参数,来模拟铣削过程中刀具和工件的动态相互作用。
切削响应分析的输出包括刀具和工件的应力、变形和振动等信息,可以用于优化铣削参数和改进铣削系统的设计。
结论本文介绍了基于ANSYS的平面端铣模态和切削响应分析方法。
数控铣床床身结构的模态分析及优化

型,这是进行有限元分析的基础。本文利用比较流行 的三维软件Pro/E创建三维模型,并把Pro/E三维模型 导入到有限元分析软件Workbench中。
(2) 材料属性和边界条件。床身材料为 HT250,密度为7.28 x 103kg/m3,泊松比为0.156,弹 性模量为1.38xl05MPa,
图1 V形床身网格划分
76 竺煦第7顎 www.mwl950. com
余爲於》工®冷加工
图2矩形床身网格划分
身一阶振型为床身中间上半部分上下摆动,固有频
率为170.26Hz,在该振型下V形床身的最大振幅为
92.607 gm,此时的最大变形为2.372 2mm;床身
二阶振型为床身中间下半部分上下摆动,固有频
参考文献: [1] 倪晓宇,易红,汤文成,等.机床床身结构的有限元分
析与优化[J].制造技术与机床,2005⑵:47-50. [2] 郝文化,肖新标,等.ANSYS 7.0实例分析与应用
400.00
800.00 (mm)
200.00
600.00
图3 V形床身第一阶振型
B: Modal Figure Type: Total Deformation Frequency: 190.71 Hz Unit: mm 2018/10/1 19:24
4.392 3.843 3.294 2.745 2.196 1.647 1.098 0.549 0 min
最大变形/mm 2.372 2 4.9410 1.458 5 5.116 9 2.047 3
阶次 1 2 3 4 5
表2矩形床身模态分析结果
固有频率/Hz 169.75 196.53 236.45 250.45 286.65
数控机床铣削切削力的模拟与实测方法

数控机床铣削切削力的模拟与实测方法摘要:数控机床在现代制造业中发挥着重要作用,铣削切削力的模拟与实测是数控机床加工研究的关键问题之一。
本文将介绍数控机床铣削切削力的模拟与实测方法,包括力学模型的建立、数值仿真和实验测试等方面的内容,以期为相关研究提供参考。
一、引言数控机床作为现代制造业的重要工具,其高精度、高效率的特点受到广泛关注。
而铣削切削力在数控铣床加工过程中起着决定性作用,对加工质量和机床性能具有重要影响。
因此,模拟和实测数控机床铣削切削力成为加工研究的重要内容之一。
二、模拟方法1. 力学模型的建立铣削切削力的模拟首先要建立合适的力学模型。
常用的力学模型包括切削力系数模型和有限元模型两种。
切削力系数模型是通过实验获得相关参数后,根据经验公式计算切削力。
有限元模型则是将加工过程建模为一系列有限元素,通过数值分析计算切削力的分布和大小。
2. 数值仿真数值仿真是利用计算机软件模拟数控机床加工过程和切削力的计算。
常用的仿真软件有Deform、ABAQUS等。
数值仿真可以通过调整刀具几何参数、切削条件和材料性质等因素,预测不同情况下的切削力大小和分布情况,为工艺优化提供指导。
三、实测方法1. 切削力测量设备实测切削力是了解加工过程中切削力的真实情况的重要手段。
常用的切削力测量设备包括力传感器、力加载装置和数据采集系统。
力传感器可以精确测量切削力大小,力加载装置则提供切削力测量所需的切削环境。
数据采集系统可以记录和分析切削力的变化规律。
2. 实验测试方法实验测试是通过具体的切削加工试验获取切削力的实际数值。
实验测试中需要准确控制切削条件,包括切削速度、进给速度和切削深度等。
通过实验测试可以获得不同切削条件下的切削力数值,用于验证模拟结果的准确性。
四、研究进展与展望随着数控机床技术的不断发展,数控机床铣削切削力的模拟与实测方法也在不断改进和完善。
当前的研究重点主要集中在提高模拟精度和实验测试的准确性,并进一步优化数控机床的切削性能。
数控铣床振动模态分析
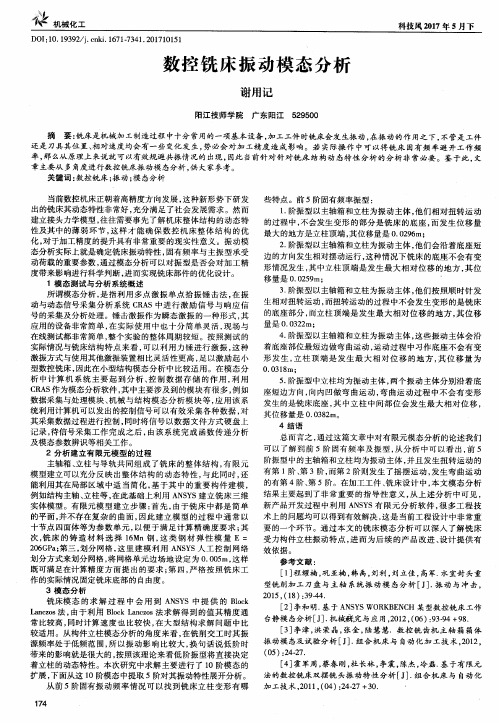
而扭转运动 的过程 中不会发生 变形 的是 铣床 动与动态信号采 集分 析系统 C R A S中进 行激 励信 号 与响应 信 生相对扭转运 动 , 的底座部 分 , 而立柱 顶端是 发生 最大相 对位 移 的地 方 , 其位 移 号 的采集及分析处 理。锤击 激振 作为 瞬态 激振 的一 种形式 , 其 量 是 0 . 0 3 2 2 m: 应用 的设备非 常简 单 , 在实 际使用 中也 十分 简单灵 活 , 现 场与 4 . 阶振型 以主轴箱 和立 柱为振动主体 , 这些振 动主体会 沿 在线测试都非 常简单 , 整个实验 的整体周期 较短 。按照测 试的 着底座部位最短边做 弯曲运 动 , 运动过 程 中习作 底座不会 有变 实际情况 与铣床结 构特 点来看 , 可以利 用力锤 进行 激振 , 这 种 激振方式与使用其他激振装 置相 比灵活性 更高 , 足 以激励 起小 形发 生 , 立柱 顶 端 是发 生 最大 相 对位 移 的 地方 , 其位 移 量 为 型数控铣床 , 因此在小型结构模态 分析 中比较 适用 。在模 态分 0. 031 8 m; 析 中计 算机 系统 主要 起 到 分析 、 控制 数 据存 储 的作用 , 利 用 5 . 阶振型 中立柱均 为振 动主体 , 两个 振动主体 分别沿 着底 C R A S作为模态分析软件 , 其 中主要涉及到的模块有很 多 , 例如 座短边方 向 , 向内凹做 弯 曲运动 , 弯 曲运 动过程 中不会 有变 形 数据采集与处理模 块 、 机械 与结构 模态 分析模 块 等 , 应 用该 系 发生 的是铣床底 座 , 其 中立柱 中间部位 会发 生最 大相对 位移 , 统利用计算机可 以发 出的控 制信 号可 以有效 采集各种 数据 , 对 其位移量是 0 . 0 3 8 2 m。 其采集数据过程进行控制 , 同时将信号 以数据文 件方式硬 盘上 4 结 语 记录 , 待 信号采集工作 完成 之后 , 由该 系统 完成 函数传 递分 析 总而 言之 , 通过 这篇文章 中对有 限元模态分析 的论 述我们 及模态参数辨识等相关工作 。 可 以了解 到前 5阶 固有频率 及振 型 , 从分 析 中可 以看 出 , 前5 2 分 析 建 立 有 限元 模 型 的过 程 阶振型 中的主轴箱 和立柱均为振动主体 , 并且发 生扭转运 动的 主轴箱 、 立柱与导轨 共 同组成 了铣床 的整 体结 构 , 有 限元 阶、 第 3阶 , 而第 2阶则发生 了摇摆运 动 , 发 生弯 曲运动 模型建立可 以充分 反映 出整体 结构 的动 态特性 , 与此 同时 , 还 有第 1 的有第 4阶、 第 5阶。在加工工件 、 铣 床设计 中 , 本 文模态 分析 能利用其在局部 区域 中适 当简 化 , 基 于其 中的重要 构件 建模 , 结果 主要起到 了非 常重 要 的指导性 意义 , 从 上述 分析 中可见 , 例如结构主轴 、 立柱等 , 在此基 础上利 用 A N S Y S建立 铣床 三维 新 产 品开 发 过 程 中 利 用 A N S Y S有 限 元 分 析 软 件 , 很 多 工 程 技 实体模型 。有 限元 模型 建立步 骤 : 首先 , 由于铣床 中都 是简 单 的平面 , 并不存在复杂 的 曲面 , 因此建 立模 型 的过程 中通 常以 术上 的问题均 可以得到有效解决 , 这是 当前工程 设计 中非 常重 十节点 四面体等为 参数 单元 , 以便 于满 足计算 精确 度要 求 ; 其 要 的一个环节 。通 过本 文 的铣 床模 态分 析可 以深入 了解 铣床 次, 铣 床 的铸 造 材 料 选 择 1 6 Mn钢 , 这类 钢材 弹 性模 量 E= 受力构件立柱振动 特点 , 进 而为 后续 的产 品改进 、 设 计提 供有 2 0 6 G P a ; 第三 , 划分 网格 , 这 里建 模利 用 A N S Y S人工 控 制 网络 效依据 。 划分方式来划分 网格 , 将 网格单元 边场地设 定为 0 . 0 0 5 m, 这样 参 考 文献 : 既可满足在计算精 度方 面提 出的要 求 ; 第 四, 严 格按 照铣床 工 [ 1 ] 程耀楠 , 巩亚楠 , 韩 禹, 刘利 , 刘立佳 , 高军. 水室封头 重 作的实际情况 固定铣床底部 的 自由度 。 型铣 削加 工刀盘 与主 轴 系统振 动模 态分析 [ J ] . 振 动 与 冲击 ,
关于数控机床模态分析的综述

关于数控机床模态分析的综述数控机床模态分析是指通过对数控机床进行模态分析,研究其结构、特性和运动方式的方法。
数控机床模态分析是数控机床设计与研究中的重要内容,可以帮助人们更好地理解和掌握数控机床的工作原理和运动规律。
在数控机床模态分析中,常用的方法主要有理论分析法和实验测量法。
理论分析法是通过对数控机床进行力学和动力学建模,采用理论推导和计算求解的方法,得到数控机床的模态参数。
实验测量法则是通过在实际数控机床上进行测量和实验,获取其振动信号、频率响应等数据,从而得到数控机床的模态参数。
这两种方法互为补充,可以更全面地了解数控机床的特性和性能。
数控机床模态分析的目的主要有两个:一是为了研究和分析数控机床的结构特性和运动规律,为数控机床的设计和改进提供参考;二是为了评估数控机床的性能和稳定性,为数控机床的使用和维护提供依据。
在数控机床模态分析中,常涉及到的内容有模态参数、模态振型、固有频率和阻尼等。
模态参数是数控机床模态分析的重要指标,主要包括质量参数、刚度参数和阻尼参数。
质量参数表示数控机床结构的质量分布和集中程度,刚度参数表示数控机床结构的硬度和刚性程度,阻尼参数表示数控机床的能量损耗和振动衰减。
模态振型是数控机床模态分析中的另一个重要概念。
模态振型描述了数控机床结构在不同模态下的运动方式和振动形态。
通过分析和解释模态振型,可以更好地了解数控机床的结构和运动规律。
固有频率是数控机床的固有性能和特性之一、固有频率表示了数控机床在不同模态下的自然频率,是数控机床结构和振动特性的重要指标。
通过研究和分析固有频率,可以评估数控机床的性能和稳定性。
阻尼是数控机床模态分析中的一个重要概念。
阻尼表示数控机床在振动过程中的能量损耗和振动衰减程度。
阻尼对于数控机床的稳定性和振动性能有着重要的影响。
通过研究和控制阻尼,可以提高数控机床的性能和稳定性。
总之,数控机床模态分析是研究数控机床结构特性和运动方式的重要方法,对于数控机床的设计、改进和使用都具有重要意义。
床身铣床的振动模态分析与控制
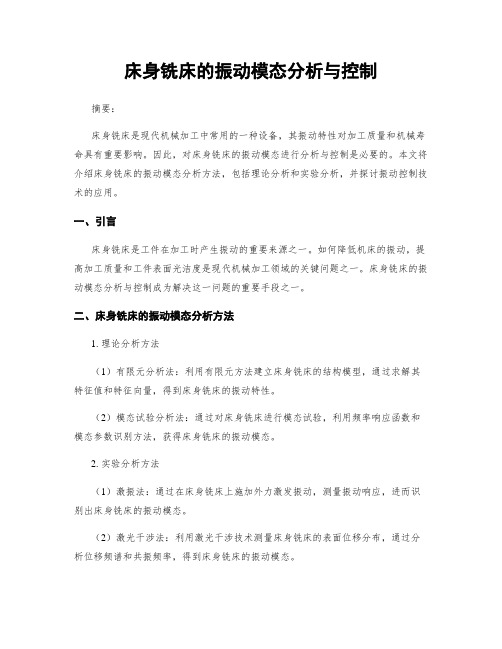
床身铣床的振动模态分析与控制摘要:床身铣床是现代机械加工中常用的一种设备,其振动特性对加工质量和机械寿命具有重要影响。
因此,对床身铣床的振动模态进行分析与控制是必要的。
本文将介绍床身铣床的振动模态分析方法,包括理论分析和实验分析,并探讨振动控制技术的应用。
一、引言床身铣床是工件在加工时产生振动的重要来源之一。
如何降低机床的振动,提高加工质量和工件表面光洁度是现代机械加工领域的关键问题之一。
床身铣床的振动模态分析与控制成为解决这一问题的重要手段之一。
二、床身铣床的振动模态分析方法1. 理论分析方法(1)有限元分析法:利用有限元方法建立床身铣床的结构模型,通过求解其特征值和特征向量,得到床身铣床的振动特性。
(2)模态试验分析法:通过对床身铣床进行模态试验,利用频率响应函数和模态参数识别方法,获得床身铣床的振动模态。
2. 实验分析方法(1)激振法:通过在床身铣床上施加外力激发振动,测量振动响应,进而识别出床身铣床的振动模态。
(2)激光干涉法:利用激光干涉技术测量床身铣床的表面位移分布,通过分析位移频谱和共振频率,得到床身铣床的振动模态。
三、床身铣床的振动控制技术1. 主动控制主动振动控制是通过在床身铣床上施加控制力对振动进行控制。
常见的主动振动控制方法包括:伺服驱动控制、力矩控制、电液伺服控制等。
这些方法能够实时感知床身铣床的振动状态,通过反馈控制技术对振动进行抑制。
2. 被动控制被动振动控制是通过改变床身铣床的结构或增加振动吸收材料等 passively 来降低振动。
常见的被动振动控制方法包括:隔振控制、阻尼控制、能量吸收控制等。
这些方法通过改变床身铣床的传递特性,减少振动的传播和能量损失。
3. 半主动控制半主动振动控制是主动控制和被动控制的结合,利用主动控制技术和被动控制技术相结合来实现振动控制。
常见的半主动振动控制方法包括:阻尼控制、智能材料控制等。
这些方法通过智能调节材料的特性或控制方式,实现对床身铣床振动的实时调控。
利用模态分析方法改善高速机床刚度与稳定性
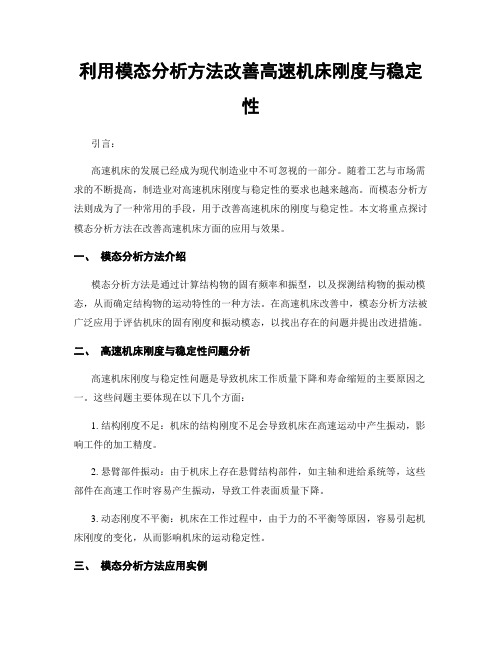
利用模态分析方法改善高速机床刚度与稳定性引言:高速机床的发展已经成为现代制造业中不可忽视的一部分。
随着工艺与市场需求的不断提高,制造业对高速机床刚度与稳定性的要求也越来越高。
而模态分析方法则成为了一种常用的手段,用于改善高速机床的刚度与稳定性。
本文将重点探讨模态分析方法在改善高速机床方面的应用与效果。
一、模态分析方法介绍模态分析方法是通过计算结构物的固有频率和振型,以及探测结构物的振动模态,从而确定结构物的运动特性的一种方法。
在高速机床改善中,模态分析方法被广泛应用于评估机床的固有刚度和振动模态,以找出存在的问题并提出改进措施。
二、高速机床刚度与稳定性问题分析高速机床刚度与稳定性问题是导致机床工作质量下降和寿命缩短的主要原因之一。
这些问题主要体现在以下几个方面:1. 结构刚度不足:机床的结构刚度不足会导致机床在高速运动中产生振动,影响工件的加工精度。
2. 悬臂部件振动:由于机床上存在悬臂结构部件,如主轴和进给系统等,这些部件在高速工作时容易产生振动,导致工件表面质量下降。
3. 动态刚度不平衡:机床在工作过程中,由于力的不平衡等原因,容易引起机床刚度的变化,从而影响机床的运动稳定性。
三、模态分析方法应用实例1. 结构刚度分析:通过模态分析方法,对机床结构的固有频率和振型进行计算和预测,从而确定机床刚度的问题所在。
通过针对性的改进,如增加结构材料的厚度或使用更高强度的材料,可以提高机床的刚度,并减少振动。
2. 悬臂部件优化设计:通过模态分析方法,可以确定悬臂部件的振动模态和固有频率。
结合结构优化设计,如加强悬臂部件的支撑结构或改变其材料,可以减少悬臂部件的振动,提高机床的稳定性。
3. 动态刚度平衡调整:通过模态分析方法,可以获取机床在不同工况下的刚度变化规律,并通过适当的调整机床结构或增加动态平衡装置,实现机床刚度的平衡,从而提高机床的稳定性。
四、模态分析方法的优势与限制尽管模态分析方法在改善高速机床刚度与稳定性方面具有明显优势,但也存在一定的限制:1. 只适用于线性振动系统:模态分析方法主要适用于线性振动系统,对于非线性振动系统的分析能力有限。
数控铣床振动模态分析

万方数据·190·机床与液压第37卷过研究无阻尼的自由振动来求解。
由式(1)变形可得腑(t)+Kx(f)=0(2)它的解可以假设为以下形式:戈=q'sinto(t—to)(3)咖是Ⅳ阶向量,∞是向量振动频率,t是时间变量,t。
是由初始条件确定的时间常数。
将式(3)代入式(2),可得到一个广义特征值方程,即脚一∞2肘咖=O图3铣床有限元模型求解以上方程可以确定西和fit),得到n个特征3模态分析解(∞;,1),(∞;,2),(∞;,3),…,(∞:,妒。
)。
对已建立的有限元模型,在ANSYS中用Block其中特征值∞t,∞:,…,∞。
代表固有频率,特征向l_anc功s法求解铣床的模态。
BlockLanczos法计算精量1,2,3,…,多。
代表固有振型。
度高,计算速度快,适用于大型结构求解问题。
下面该铣床在铣削加工时振源频率属低频范围,因此主要针对铣床的主要受力构件立柱进行模态分析。
铣下面主要针对前5阶振动固有频率和振型做分析研床在铣削加工时振源频率属低频范围,因此低阶固有笼。
振型要比高阶固有振型对立柱的振动影响大,越是低2有限元模型的建立阶影响就越大,因此低阶振型对立柱的动态特性起决2.1利用ANSYS建立铣床三维实体模型定作用,作者求解时共扩展了lo阶模态,现取前5铣床主要由立柱、主轴箱、导轨组成。
建模过程阶模态进行振动特性的分析。
中在如实反映铣床结构动态特性的前提下,对结构局经计算铣床的前5阶固有频率如图4所示。
部区域做了一些简化,主要建立重要结构部件立柱及相关结构主轴箱和底座。
铣床三维实体模型如图1所示,铣床的立柱剖面图如图2所示。
图1铣床三维实体模型图2立柱剖面三维实体模型2.2建立有限元模型(1)单元类型的选择由于该铣床无复杂曲面,可采用十节点四面体等参数单元(Solid92)即可满足计算精度的需要。
图4铣床前10阶固有振动频率(单位:Hz)(2)定义材料属性铣床的铸造材料为16Mn钢,其弹性模量E=由图4得前5阶固有振动频率为70·854Hz,206GPa,泊松比肛=0.29,P=7850kg/m3。
- 1、下载文档前请自行甄别文档内容的完整性,平台不提供额外的编辑、内容补充、找答案等附加服务。
- 2、"仅部分预览"的文档,不可在线预览部分如存在完整性等问题,可反馈申请退款(可完整预览的文档不适用该条件!)。
- 3、如文档侵犯您的权益,请联系客服反馈,我们会尽快为您处理(人工客服工作时间:9:00-18:30)。
机床铣削加工时的工作模态分析方法
摘要:模态分析是近年结构健康监测领域的热点之一,其获取的结构模态参
数在既有结构的动力特性评价、结构损伤诊断、结构振动控制等领域具有重要应用。
工作模态分析只需测量结构在环境激励下的响应信号便可进行模态参数识别,具有操作简单可行、试验经济等特点,因而在程领域中得到了广泛应用。
近年来,很多学者分别在时域内和频域内提出了各种工作模态分析方法。
基于此,本篇文
章对机床铣削加工时的工作模态分析方法进行研究,以供参考。
关键词:机床铣削加工;工作模态;分析方法
引言
工作模态分析可仅利用结构输出的振动位移响应信号识别结构的工作模态参
数(模态振型、固有频率和阻尼比),进而应用于结构损伤检测、结构设计等。
目前,为识别时不变结构的工作模态参数,提出利用PCA和Isomap算法识别结
构的工作模态参数。
利用了LLE算法识别出复杂三维连续体结构的工作模态参数。
当前,针对线性慢时变结构的工作模态参数识别问题,主要有时域法和频域法。
线性慢时变结构的振动响应信号往往是不能一次性获取完整的,需要通过随着时
间的推移,不断进行采样得到。
因此,基于“短时时不变”理论的滑动窗方法能
很好应用于线性慢时变结构工作模态参数识别中。
目前,滑动窗方法已应用在一
些算法上做线性慢时变结构的工作模态参数识别。
将滑动窗与主元分析相结合,
有效的识别了多自由度系统的工作模态参数。
基于滑动窗变步长EASI算法识别
了线性慢时变系统的工作模态参数。
1现有铣削参数确定的情况
现代工业产品中涉及到大量复杂曲面,导致铣削处理技术的要求标准较高。
如何保障加工效率及品质,逐渐成为数控加工研究的热点。
影响铣削精度的因素
主要有切削参数、产品设计、制作材料和刀具等,其中切削参数最重要。
目前,
国内数控加工运用潜力和优势尚未完全突显。
如果选择运用传统处理经验确定参
数,会引发诸多问题。
因此,需探究铣削加工的参数,保障此工序的落实成效。
若参数设置不当,会影响机组运转效率和零件成品质量。
第一,空走刀频率增加,零件的有效加工时间短,使得制造时间长。
第二,机床及刀具会发生严重振动,
导致零件成品表面精度低。
第三,零件转角位置容易拉刀,从而造成过切的问题。
第四,刀具容易受损,出现磨损明显、刀具使用寿命缩短等问题。
第五,工时设
定不准确,无法提升零件制作管理效果。
2选定加工参数
在选定加工参数的过程中,需要确定刀具和检验规则等参数。
其中:刀具参
数包括直径和材料,需要根据具体情况进行选择;检验参数的设置需要满足机床
与刀具的工作需求,注重安全值与制造精度标准。
首先,计算切削力。
此参数在
切削期间会出现变化,在参数优化中通常表示最大的切削力值。
其次,确定切削
温度。
切削作业中,变形及摩擦耗用的功绝大部分会变成热能。
在确定温度参数时,需计算剪切温升和摩擦面温升得到温升均值。
再次,选择耐用性合适的刀具。
该参数表示从刀具开始使用直至摩钝的时长,与切削速度、切削材料及进给量有关。
最后,估算粗糙度。
一般曲面加工包含粗加工、半精加工以及精加工。
成品
粗糙度参数与刀具轨迹相关,需按照走刀方式确定估算思路。
例如,环形走刀会
形成横纵两个方向的粗糙度,其中纵向粗糙度难以预测且影响不大,实际优化中
可仅考虑横向参数。
3周期铣削激励下模态分析方法验证
在数控机床切削试验中,切削力需保证足够大的能量激励力才能辨识得到准
确模态参数。
因此加工参数设置如下:主轴转速为1200r/min,进给速度为600mm,切宽为8mm,切深为1.5mm,被切削工件为45钢。
图1为切削试验的现场布置图。
机床切削过程中,图2为主轴测点的原始加速度信号,其中包含明显的周期
成分。
图1切削试验现场
图2原始加速度信号
为了抑制信号中周期成分对辨识模态参数的干扰,对原始振动信号进行倒频谱编辑处理。
经过倒频谱编辑处理后,原始自功率谱与倒频谱编辑后信号的自功率谱对比见图3。
由图可知,原始信号的谐频及倍频在倒频谱编辑后被去除,周期成分得到了有效的去除。
剩余信号部分保留了原始自功率谱的大体轮廓,可用于工作模态分析。
图3原始信号与倒频编辑后信号的自功率谱对比
采用LMS.TestLab软件中的Op.PolyMAX算法对倒频谱编辑后的剩余信号进行模态参数辨识。
为了与传统试验模态分析保持一致,辨识过程中的模态阶数和分析频带参数的设置与PolyMAX分析过程相同。
图4为倒频谱编辑后信号的模
态稳态图。
根据稳态图中自功率谱和极点队列的分布可知,各阶模态均得到了有
效辨识。
图4倒频谱编辑后的主轴信号的稳态图
由静止与铣削状态下得到的固有频率和阻尼比对比可知(见表1和表2):①不
同状态下,同阶模态频率均有偏差,但偏差均不超过±5%;②当模态阶数增加时,不同状态下、同阶次固有频率的差异百分比逐渐减小;③各阶模态阻尼比差异较大。
机床固有频率和阻尼比在不同状态下存在差异的可能原因如下:①两种方法
的激励方式和频带不同,试验模态分析中的锤击力可近似为宽频脉冲信号,但工
作模态分析中的激励力频带较小,不能充分激发所有的模态;②与静止状态相比,机床的边界条件发生变化,机床运行状态下的物理特性(质量矩阵、刚度矩阵和
阻尼矩阵)不同,所以动力学特性也会存在差异。
4加强机床铣削加工精度的路径探索
4.1合理设计工艺支撑
机床外形相对不规则,外加机床自身特性影响导致其极易在铣削加工过程中
出现形变问题而影响到铣削加工精度,因此在实际机床加工过程中要合理设置科学、标准、规范的铣削加工工艺技术,以有效保障机床铣削加工精度。
选用不同
的薄壁件进行加工时,要充分考虑工件加工受热和应力的影响程度,再结合薄壁
件加工目标和要求合理设计、采用有效的工艺支撑,以最大限度保障机床在受外
界应力的作用下不会发生明显变形;实际机床在进行加工时需要多次变换固定位置,这就需要人们在进行机床加工前有效结合远技术坐标,以科学计算并合理设
置工件的固定位置,然后严格控制加工顺序和流程,以消除残余应力对工件形变
的影响。
4.2正确选择使用工具
在以往的机床铣削加工过程中采用的夹具通常为自定心三爪和四爪卡盘式,
而不同夹具在使用过程中的夹紧方向不同、夹紧应力和拉应力也不同,这时工件
会在夹紧力的作用下达到预期目标,因此要根据实际机床特性科学选择最佳的夹
具和施加的夹紧力,选择合适、有效的装夹方式,在降低工件变形程度的基础上,降低专用夹具的制造成本;根据刀具直径、螺旋角以及机床的加工要求科学选择
刀具参数,确保工件内腔精加工时刀具的直径要小于拐角处的圆角半径,以避免
由于刀具与零件的接触面变大而产生振动现象,从而增加工件表面振纹。
结束语
综上所述,本文基于铣削加工过程中路径的变化,建立了工作模态分析模型。
分析如下:(1)切削点越靠近薄壁件中心,固有频率越高,工件变形越小。
(2)根据实验数据拟合结果发现,工作模态分析即可对切削点的动态特性进行较好的
评估。
参考文献
[1]李春辉,宋志强,张博,苏一鸣.机床铣削加工时的工作模态分析方法[J].
工具技术,2019,55(10):78-81.
[2]孙启梦.大型弱刚性零件加工工艺优化及数控加工过程监测方法研究[D].东华大学,2019.
[3]侯鹏荣.铝合金LF21微铣削表面形貌仿真研究[D].大连理工大学,2019.
[4]刘斌.立卧加工中心关键零部件静动态特性分析及优化设计[D].山东大学,2019.
[5]王晨.高速高精加工中心的切削稳定性研究[D].兰州理工大学,2019.。