连铸坯表面质量
连铸坯质量缺陷

连铸坯的质量缺陷及控制摘要连铸坯质量决定着最终产品的质量。
从广义来说所谓连铸坯质量是得到合格产品所允许的连铸坯缺陷的严重程度,连铸坯存在的缺陷在允许范围以内,叫合格产品。
连铸坯质量是从以下几个方面进行评价的:(1)连铸坯的纯净度:指钢中夹杂物的含量,形态和分布。
(2)连铸坯的表面质量:主要是指连铸坯表面是否存在裂纹、夹渣及皮下气泡等缺陷。
连铸坯这些表面缺陷主要是钢液在结晶器内坯壳形成生长过程中产生的,与浇注温度、拉坯速度、保护渣性能、浸入式水口的设计,结晶式的内腔形状、水缝均匀情况,结晶器振动以及结晶器液面的稳定因素有关。
(3)连铸坯的内部质量:是指连铸坯是否具有正确的凝固结构,以及裂纹、偏析、疏松等缺陷程度。
二冷区冷却水的合理分配、支撑系统的严格对中是保证铸坯质量的关键。
(4)连铸坯的外观形状:是指连铸坯的几何尺寸是否符合规定的要求。
与结晶器内腔尺寸和表面状态及冷却的均匀程度有关。
下面从以上四个方面对实际生产中连铸坯的质量控制采取的措施进行说明。
关键词:连铸坯;质量;控制1 纯净度与质量的关系纯净度是指钢中非金属夹杂物的数量、形态和分布。
夹杂物的存在破坏了钢基体的连续性和致密性。
夹杂物的大小、形态和分布对钢质量的影响也不同,如果夹杂物细小,呈球形,弥散分布,对钢质量的影响比集中存在要小些;当夹杂物大,呈偶然性分布,数量虽少对钢质量的危害也较大。
此外,夹杂物的尺寸和数量对钢质量的影响还与铸坯的比表面积有关。
一般板坯和方坯单位长度的表面积(S)与体积(V)之比在0.2~0.8。
随着薄板与薄带技术的发展,S/V可达10~50,若在钢中的夹杂物含量相同情况下,对薄板薄带钢而言,就意味着夹杂物更接近铸坯表面,对生产薄板材质量的危害也越大。
所以降低钢中夹杂物就更为重要了。
提高钢的纯净度就应在钢液进入结晶器之前,从各工序着手尽量减少对钢液的污染,并最大限度促使夹杂物从钢液中排除。
为此应采取以下措施:⑴无渣出钢。
连铸坯表面质量浅析
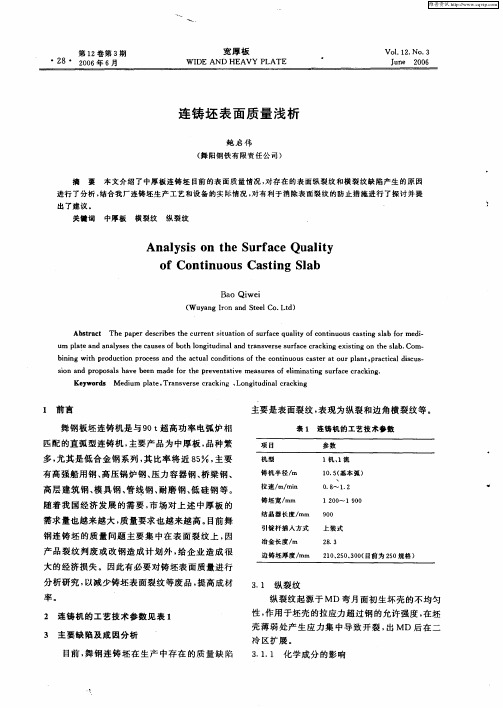
舞 钢 的连 铸 钢 种 中, O 8 %的 钢 种 都 属 于包 晶 钢范围, 即C含 量在 0 1 .2  ̄ o o 1 %之 间 , 时 坯 .6 此 壳 厚 度的 不均匀 性最 严重 , 最易 引起 纵裂 , 图 也 见 1 。若钢 中S、 P含量 高 , 的高温 强度 和 塑性 明显 钢 降低 , 得发生 纵 裂 的趋 向增 大 。 使
主要 是 表面裂 纹 , 表现 为纵 裂和边 角 横裂纹 等 。
表 1 连 铸 机 的 工 艺 技 术参 数
项目
机 型
参 数
1机 、 流 1 1.( 本 弧) 0 5基
、
铸机半径/ m
拉 速 / mi m/ n
0 8 12 . ~ . 12 ~ 19 0 00 0
率。
上 装 式
2 . 3 8
边 铸坯 厚 度/ mm
2 0 2 0 3 0 目前 为 2 0规 格 ) 1 、5 、 0 ( 5
3 1 纵 裂纹 .
纵 裂纹起 源 于 MD弯 月面初 生坏 壳 的不 均匀 性, 作用 于坯 壳 的拉应力 超 过钢 的允 许强 度 , 坯 在 壳 薄弱 处 产 生应 力 集 中 导致 开 裂 , MD后 在 二 出
An lsso h u f c aiy ay i n t eS r a eQu l t
o ntnu usCa tn l b f Co i o s i g S a
Ba we o Qi i
( u a g Io n t e o L d) W y n r n a d S e lC . t
1 前 言 舞钢 板坯 连铸 机是 与 9 超 高功 率 电弧炉 相 Ot 匹配 的直 弧型 连铸 机 , 主要产 品 为 中厚 板 , 品种 繁 多 , 其是 低合 金 钢 系列 , 比率 将 近 8 , 尤 其 5 主要 有 高强船 用 钢 、 压锅 炉钢 、 高 压力 容器 钢 、 桥梁 钢 、 高层建筑钢、 具钢、 模 管线 钢 、 磨 钢 、 硅 钢 等 。 耐 低 随着 我 国经 济 发展 的需 要 , 场对 上 述 中 厚板 的 市
连铸坯的缺陷及控制

二冷段和末端区的电磁搅拌可有效抑制枝晶搭桥形成封闭 的液窝。
连铸主要工艺参数
① 拉坯速度及其控制 ② 铸坯的冷却(结晶器冷却、二次冷却)
连铸坯的内部凝固是在出结晶器后进行的,后继的二次水冷、 弯曲矫直等直接影响内部质量。
连铸坯的缺陷及控制
提高连铸坯内部质量的工艺措施:
① 控制二冷段的传热,使铸坯均匀凝固,提高等轴晶率; 偏析、缩孔、缩松
② 降低浇钢的过热度; ③ 使用性能好的保护渣,防止钢水二次氧化和污染; ④ 控制拉速,保证连铸机正常运行; ⑤ 电磁搅拌(二冷段和末端区)。 偏析、缩孔、缩松
连铸坯的缺陷及控制
提高连铸坯表面质量的工艺措施:
① 控制结晶器的传热,使初凝固壳均匀; 裂纹、凹陷
② 控制结晶器的振动;
振痕、横裂纹
③ 使用性能好的保护渣;
气孔、夹杂
④ 优化结晶器结构;
倒锥角度,弧形壁
⑤ 电磁搅拌;
气孔、夹杂
⑥ 软接触电磁连铸。
振痕、裂纹
电磁搅拌的部位:
结晶器电磁搅拌:
(1)借助旋转电磁场使连铸 机结晶器内的金属液产生平 面旋转,去除杂质、气体。
结晶器电磁搅拌:
(2)扩大等轴晶区改善宏观 偏析,减少粗大柱状晶区 。
软接触电磁连铸:
软接触电磁连铸:
(1)减轻结晶器振动对弯月 面的影响,液态渣膜连续均 匀。
软接触电磁连铸:
(2)减小初凝壳对结晶器的 连铸坯的内部缺陷
裂纹 气孔 夹杂 缩孔、缩松 成分偏析
连铸坯的缺陷及控制
连铸坯的缺陷及控制
1. 连铸坯的表面缺陷
裂纹 气孔 夹杂 振痕、凹陷 成分偏析
连铸坯的缺陷及控制
1. 连铸坯的表面缺陷
连铸坯质量及控制
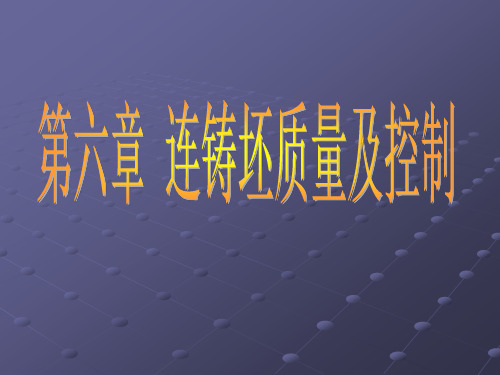
用酸浸或硫印法所显示的组织结构属于宏 观结构——连铸坯和金属材料检验中最为 常用的检验技术。
连铸坯自表面至中心都是由边缘等轴晶区 (激冷区)、柱状晶区和中心等轴晶区三 部分组成。
温度梯度较大时,固液两相区小,有利于 柱状晶的生长,而凝固速度较快,则易于 生成枝晶间距小的铸造组织,所以连铸坯 具有较发达的柱状晶组织,并具有较小的 枝晶间距。
连铸坯宏观组织的好坏可以用等轴晶所占 的比例多少来衡量。
连铸坯凝固过程的一般特征:从连铸坯的 侧面优先凝固,其温度梯度高,凝固速度 快,连铸坯内部结晶体成长是不规则的, 局部优先生长使内部晶体产生“搭桥”等 现象,造成因钢水补充不足而出现中心缩 孔等缺陷。
铸坯凝固特征:
1)冷却过程为强制冷却过程; 2)在凝固过程中形成了很长的液相穴; 3)铸坯的凝固是分阶段的凝固过程; 4)除头尾外,铸坯在长度方向上的结构较 为一致。
增加能生成等轴晶具体措施: 1)低温浇铸或实现所谓“零”过热度浇注; 2)加孕育剂; 3)电磁搅拌; 4)调整二冷水量。
浇注条件(铸温、钢种、拉速、冷却强度 等)、铸机的形式、铸坯断面等。
1.浇铸条件: 低温浇注有利于等轴晶率的提高。
铸温(过热度)↗,拉速↗,二冷强度↗, →柱状晶区的发展,其中铸温影响最大。
碳偏析 含量较低,而后凝固部分溶质含量较高,这种成分不均匀的现象称偏析。
凹坑 由于坯壳和结晶器壁间周期性接触和收缩而产生的皱纹,严重的如山谷状的凹 重皮 陷,称为凹坑。钢水在凹陷部位渗漏出来,再在结晶器壁重新凝固,称重皮。
切割断 面缺陷
连铸坯端部的切斜不得大于20mm,因剪切造成的宽展不得大于边长的10%。
连铸坯质量
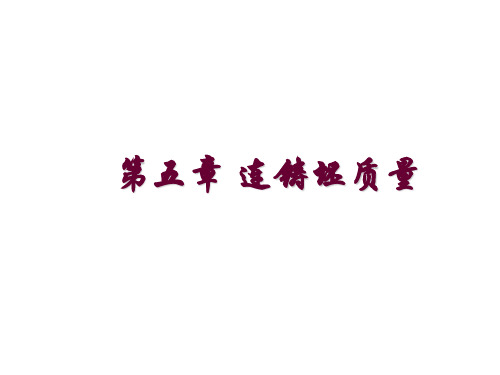
侧固液相界面捕捉,在内弧侧距表
面约10mm处,有一夹杂物集聚带。 大型夹杂物多集中于内弧侧
1/5~1/4厚度处。
直结晶器+2~3m垂直段:注流冲击 是对称的,液相内夹杂物得到上浮, 同时夹杂物分布也比较均匀。见右 图和下页图
1 弧形连铸机 2 直结晶器的弧形连铸机 3 立式连铸机
连铸机机型对大型夹杂物的影响
30 30
CaO- SiO2-Al2O3
Al2O3 ,Al2O3〃SiO2 Al2O3-MnO-CaO,Al2O3
⑵ 如何分析夹杂物对产品质量的影响
应从以下几个方面着手分析: ①夹杂物的形态和组成。塑性夹杂和球形不变形夹杂对钢性能的影响 不同,沿轧制方向伸长的塑性夹杂使钢横向力学性能恶化。MnS夹杂 能变形,FeO和MnO夹杂能稍变形,SiO2 和Al2O3 夹杂不变形。FeS、 FeO熔点低使钢产生热脆,MnS熔点高改善钢的热脆。 ②夹杂物的大小和聚集状态。夹杂物会使钢材产生分层,夹杂物越大, 影响越大。但即使存在着小的夹杂物聚集,也可能使钢材分层。
③ 预防及消除方法: — 结晶器铜板表面最好镀铬或 镀镍,减少铜的渗透; — 适当控制钢中残余元素,如 ω[Cu] <0.20%; — 降低钢中硫含量,并控制合 适的[Mn]/[S]比大于40; — 控制钢中Al、N含量,选择合 适的二冷制度。
⑸ 皮下气泡与气孔
① 缺陷特征:在铸坯皮下存在的直径约1mm,长约10mm,沿柱状晶生 长方向分布的气泡称为皮下气泡。若裸露于铸坯表面的气泡称为表面气 泡;小而密集的小孔叫皮下针孔。
①连铸时钢液凝固速度快,夹杂物集聚长大机会少→尺寸较小,不易从 钢液中上浮。
②连铸过程中多了中间包装臵,钢液与大气、熔渣、耐材接触时间长易
钢锭连铸坯验收标准

钢锭连铸坯验收标准
1、连铸坯的化学成份应符合有关标准的规定;
2、尺寸允许偏差;
尺寸130×130、200×200、φ130、φ200边长允许偏差(mm)±4.0±6.0 对角线长度之差(mm)≤6.0≤9.0 允许偏差(mm)±3.0±4.0椭圆度(mm)不大于直径公差的0.75倍;
3、外形:
3.1、方坯弯曲度每米不大于20 mm,总弯曲度不大于总长度的1.5%;
3.2、圆坯弯曲度每米不大于15 mm,总弯曲度不大于总长度的1.0%;
3.3不得有明显的扭转,端部切斜不得大于10 mm;
4、表面质量□不得有肉眼可见的裂纹、重叠、结疤、夹渣、夹杂、气孔、深度(高度)大于3mm的滑痕、划伤、皱纹、凸块。
如有上述缺陷存在则必须清除,清除深、宽、长比不得小于1:6:8;
5、保证连铸坯的质量,头坯、尾坯的切除量规定如下:
头坯:不得少于700mm;
尾坯:不得少于1000 mm 如头坯切除量达不到上述要求,则判第一条坯为利用品;
尾坯切除量达不到上述要求,则判最后一条坯为利用品;
6、班组质量员对连铸坯进行逐支检查,写上炉号和钢号,注明利用品,按炉做好原始记录;
7、质检部质检员每天对表面质量进行检查,合格品盖上“检”字章,做好抽查记录。
连铸坯质量的控制

连铸坯的质量控制系统专业:班级:姓名:XXX目录1连铸坯纯净度与产品质量 (1)1.1纯净度与质量的关系 (1)1。
2提高纯净度的措施 (2)2连铸坯质量............................................................ 错误!未定义书签。
2.1 连铸坯的几何形状质量 (3)2。
1.1 铸坯形状缺陷类型 (4)2。
1。
2 铸坯形状缺陷产生原因及防止措施 (4)2.1.3 铸坯鼓肚 (4)2.1.4 铸坯菱变 (4)2。
1。
5 铸坯变成梯形坯 (5)2.2 连铸坯表面质量 (5)2。
2。
1 连铸坯表面振痕 (5)2。
2。
2 振痕形成机理 (5)2。
2.3 振痕对铸坯质量的影响 (6)2。
2。
4 影响振痕深度的因素 (6)2.2.5 减少振痕深度的措施 (7)2。
2.6 铸坯表面裂纹 (7)2。
2。
7 表面纵裂纹 (8)2。
2.8 铸坯角部纵裂纹 (11)2。
2。
9 表面横裂纹 (12)2。
2.10 角部横裂纹 (14)2.2。
11 铸坯表面星状和网状裂纹 (15)2。
2.12 铸坯表面夹渣(杂) (16)2.2。
13 铸坯气孔和气泡 (17)2。
2.14 铸坯表面凹陷 (17)2。
2.15 铸坯表面增碳和偏析 (18)2。
2.16 重皮和重结及结疤 (19)2.3 连铸坯内部质量 (19)2。
3。
1 铸坯内部裂纹 (19)2。
3.2 皮下裂纹 (20)2.3.3 中间裂纹 (20)2.3.4 矫直裂纹 (21)2。
3。
5 压下裂纹 (22)2.3。
6 断面裂纹-——-中心线裂纹 (22)2。
3。
7三角区裂纹 (24)2。
3.8角部附近的裂纹 (25)2.3。
9白点及发纹 (25)2。
3。
10铸坯中心偏析、疏松和缩孔 (25)2.3。
11铸坯内部夹渣(杂) (26)3连铸坯星状缺陷 (27)3.1 鼓肚变形 (27)3。
2 菱形变形 (28)3.3 圆铸坯变形 (28)致谢 (29)摘要连铸坯质量决定着最终产品的质量。
连铸坯的质量控制概述

提高铸坯洁净度的措施: (1)无渣出钢 (2)选择合适的精炼处理方式 (3)采用无氧化浇铸技术 (4)充分发挥中间包冶金净化的作用 (5)选用优质耐火材料 (6)充分发挥结晶器的作用 (7)采用电磁搅拌技术,控制铸流运动
三、铸坯表面质量及控制
控制表面质量的必要性 表面缺陷的形成 表面裂纹的主要种类 液面结壳 凹坑和重皮
4.3.2 内部纵向裂纹
包括中心线裂纹、三角区裂纹和角部裂纹 形成原因:液相穴末端板坯鼓肚;
板坯宽面、窄面鼓肚 主要影响因素:
1、浇铸速度过快; 2、浇铸温度过高; 3、钢水含硫量过大; 4、结晶器锥度太小; 5、铸流不对正。
减少内部裂纹的措施
采用多点矫直技术以弥补单点矫直的 不足
二冷区采用合适的夹辊辊距,支撑辊 准确对弧
对弧,并确保二冷区的均匀冷却
5.2 圆柱坯变形
定义:圆坯变形成椭圆形或不规则多边 形。圆坯直径越大,变成随圆的倾向越 严重。
椭圆变形原因: (1)圆形结晶器内腔变形 (2)二冷区冷却不均匀 (3)连铸机下部对弧不准 (4)拉矫辊的夹紧力调整不当,过分压下
应对圆柱坯变形的措施: (1)及时更换变形的结晶器 (2)连铸机要严格对弧 (3)二冷区均匀冷却 (4)可适当降低拉速
3.5 深振痕
结晶器上下振动时,在铸坯表面形成 周期性的和拉坯方向垂直的振动痕迹。 较深(大于0.5mm)时,振痕谷部会 形成缺陷,危害成品质量。
振痕深度与振动参数、含碳量、保护 渣性能及结晶器液面波动状态等因素 有关。
3.6 表面气泡(和皮下气泡)
形成原因:凝固过程中,钢中氧、氢、氮 和碳等元素在凝固界面富集,当其生成的 CO、H2、N2等气体的总压力大于钢水静 压力和大气压力之和时,即有气泡产生。