磨削温度对磨削效果的影响
机械制造中的磨削工艺工作原理
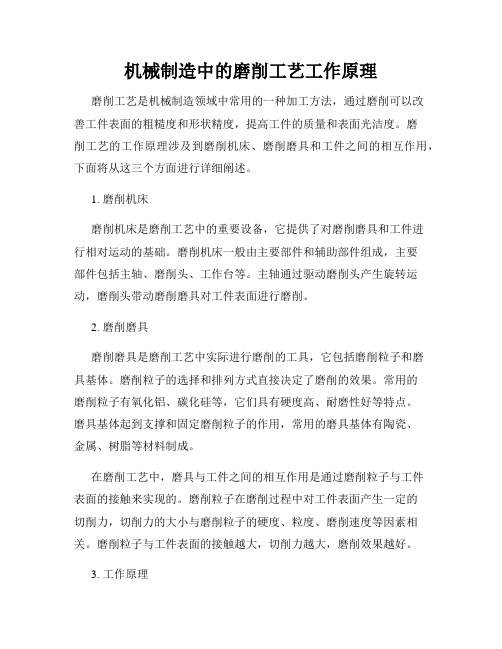
机械制造中的磨削工艺工作原理磨削工艺是机械制造领域中常用的一种加工方法,通过磨削可以改善工件表面的粗糙度和形状精度,提高工件的质量和表面光洁度。
磨削工艺的工作原理涉及到磨削机床、磨削磨具和工件之间的相互作用,下面将从这三个方面进行详细阐述。
1. 磨削机床磨削机床是磨削工艺中的重要设备,它提供了对磨削磨具和工件进行相对运动的基础。
磨削机床一般由主要部件和辅助部件组成,主要部件包括主轴、磨削头、工作台等。
主轴通过驱动磨削头产生旋转运动,磨削头带动磨削磨具对工件表面进行磨削。
2. 磨削磨具磨削磨具是磨削工艺中实际进行磨削的工具,它包括磨削粒子和磨具基体。
磨削粒子的选择和排列方式直接决定了磨削的效果。
常用的磨削粒子有氧化铝、碳化硅等,它们具有硬度高、耐磨性好等特点。
磨具基体起到支撑和固定磨削粒子的作用,常用的磨具基体有陶瓷、金属、树脂等材料制成。
在磨削工艺中,磨具与工件之间的相互作用是通过磨削粒子与工件表面的接触来实现的。
磨削粒子在磨削过程中对工件表面产生一定的切削力,切削力的大小与磨削粒子的硬度、粒度、磨削速度等因素相关。
磨削粒子与工件表面的接触越大,切削力越大,磨削效果越好。
3. 工作原理磨削工艺的工作原理可以概括为磨削磨具与工件表面的相互研磨作用。
当磨削工艺开始时,磨削磨具接触到工件表面,磨削粒子通过切削力对工件表面进行破坏和剥离,同时产生磨渣和切削热。
磨渣被磨削磨具和工作台带走,切削热则通过磨削磨具和冷却液排出。
磨削工艺的工作原理中还存在磨削力和磨削温度的问题。
在磨削过程中,磨削力对工件表面产生一定的切削和热变形,而磨削温度则会影响磨削粒子与工件表面的接触。
过高的磨削力和磨削温度会导致工件表面的质量下降和工具的损坏。
为了提高磨削工艺的效果,需要采取适当的磨削参数和技术手段。
磨削参数包括磨削速度、进给量等,它们的选择需要考虑到工件材料、磨削粒度和切削力等因素。
技术手段包括冷却液的使用、磨削液的选用等,它们可以有效降低磨削温度和防止损伤。
磨削工艺系数(常用)
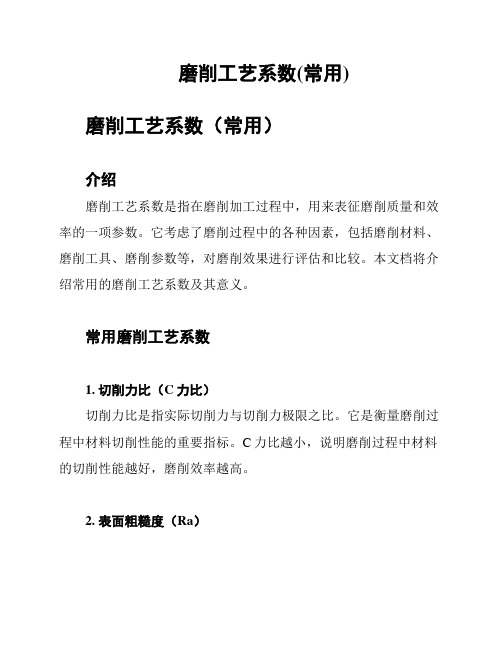
磨削工艺系数(常用)
磨削工艺系数(常用)
介绍
磨削工艺系数是指在磨削加工过程中,用来表征磨削质量和效率的一项参数。
它考虑了磨削过程中的各种因素,包括磨削材料、磨削工具、磨削参数等,对磨削效果进行评估和比较。
本文档将介绍常用的磨削工艺系数及其意义。
常用磨削工艺系数
1. 切削力比(C力比)
切削力比是指实际切削力与切削力极限之比。
它是衡量磨削过程中材料切削性能的重要指标。
C力比越小,说明磨削过程中材料的切削性能越好,磨削效率越高。
2. 表面粗糙度(Ra)
表面粗糙度是指工件表面在磨削加工后的表面质量。
它反映了磨削加工过程中的磨料和工件之间的相互作用情况。
Ra值越小,表面质量越好,磨削效果越理想。
3. 磨削温度(T)
磨削温度是指在磨削过程中磨削区域的温度。
磨削温度对磨削效果和工件表面质量有很大影响。
一般来说,磨削温度越低,磨削效果越好,工件表面质量越高。
4. 磨损量(W)
磨损量是指磨削过程中磨削工具的磨损情况。
磨削工具的磨损量越小,说明磨削过程中磨料的消耗越少,磨削效率越高。
结论
磨削工艺系数是评价磨削过程中材料切削性能、工件表面质量和磨削效果的重要指标。
切削力比、表面粗糙度、磨削温度和磨损量是常用的磨削工艺系数。
通过合理控制这些参数,可以提高磨削效率,优化磨削工艺。
以上是对磨削工艺系数(常用)的简要介绍。
如需深入了解,请参考相关资料。
磨削烧伤的小常识
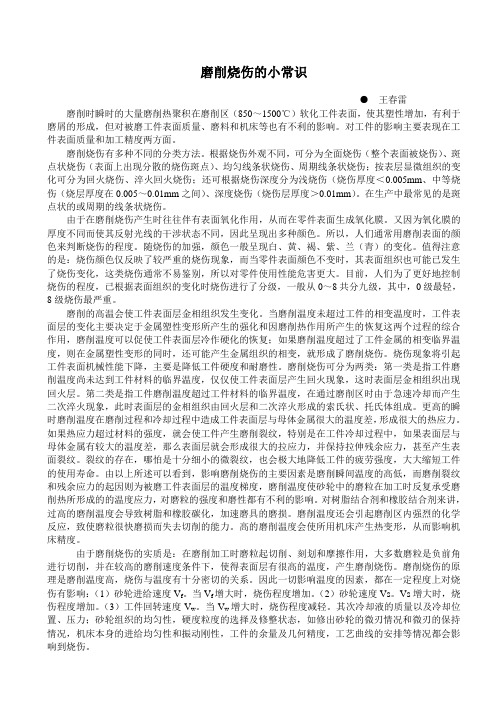
磨削烧伤的小常识●王春雷磨削时瞬时的大量磨削热聚积在磨削区(850~1500℃)软化工件表面,使其塑性增加,有利于磨屑的形成,但对被磨工件表面质量、磨料和机床等也有不利的影响。
对工件的影响主要表现在工件表面质量和加工精度两方面。
磨削烧伤有多种不同的分类方法。
根据烧伤外观不同,可分为全面烧伤(整个表面被烧伤)、斑点状烧伤(表面上出现分散的烧伤斑点)、均匀线条状烧伤、周期线条状烧伤;按表层显微组织的变化可分为回火烧伤、淬火回火烧伤;还可根据烧伤深度分为浅烧伤(烧伤厚度<0.005mm、中等烧伤(烧层厚度在0.005~0.01mm之间)、深度烧伤(烧伤层厚度>0.01mm)。
在生产中最常见的是斑点状的或周期的线条状烧伤。
由于在磨削烧伤产生时往往伴有表面氧化作用,从而在零件表面生成氧化膜。
又因为氧化膜的厚度不同而使其反射光线的干涉状态不同,因此呈现出多种颜色。
所以,人们通常用磨削表面的颜色来判断烧伤的程度。
随烧伤的加强,颜色一般呈现白、黄、褐、紫、兰(青)的变化。
值得注意的是:烧伤颜色仅反映了较严重的烧伤现象,而当零件表面颜色不变时,其表面组织也可能已发生了烧伤变化,这类烧伤通常不易鉴别,所以对零件使用性能危害更大。
目前,人们为了更好地控制烧伤的程度,已根据表面组织的变化时烧伤进行了分级,一般从0~8共分九级,其中,0级最轻,8级烧伤最严重。
磨削的高温会使工件表面层金相组织发生变化。
当磨削温度未超过工件的相变温度时,工件表面层的变化主要决定于金属塑性变形所产生的强化和因磨削热作用所产生的恢复这两个过程的综合作用,磨削温度可以促使工件表面层冷作硬化的恢复;如果磨削温度超过了工件金属的相变临界温度,则在金属塑性变形的同时,还可能产生金属组织的相变,就形成了磨削烧伤。
烧伤现象将引起工件表面机械性能下降,主要是降低工件硬度和耐磨性。
磨削烧伤可分为两类:第一类是指工件磨削温度尚未达到工件材料的临界温度,仅仅使工件表面层产生回火现象,这时表面层金相组织出现回火层。
磨削加工参数对工件表面粗糙度的影响
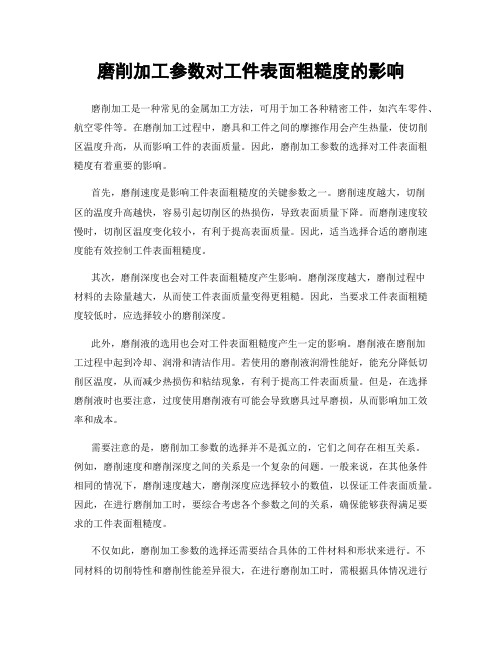
磨削加工参数对工件表面粗糙度的影响磨削加工是一种常见的金属加工方法,可用于加工各种精密工件,如汽车零件、航空零件等。
在磨削加工过程中,磨具和工件之间的摩擦作用会产生热量,使切削区温度升高,从而影响工件的表面质量。
因此,磨削加工参数的选择对工件表面粗糙度有着重要的影响。
首先,磨削速度是影响工件表面粗糙度的关键参数之一。
磨削速度越大,切削区的温度升高越快,容易引起切削区的热损伤,导致表面质量下降。
而磨削速度较慢时,切削区温度变化较小,有利于提高表面质量。
因此,适当选择合适的磨削速度能有效控制工件表面粗糙度。
其次,磨削深度也会对工件表面粗糙度产生影响。
磨削深度越大,磨削过程中材料的去除量越大,从而使工件表面质量变得更粗糙。
因此,当要求工件表面粗糙度较低时,应选择较小的磨削深度。
此外,磨削液的选用也会对工件表面粗糙度产生一定的影响。
磨削液在磨削加工过程中起到冷却、润滑和清洁作用。
若使用的磨削液润滑性能好,能充分降低切削区温度,从而减少热损伤和粘结现象,有利于提高工件表面质量。
但是,在选择磨削液时也要注意,过度使用磨削液有可能会导致磨具过早磨损,从而影响加工效率和成本。
需要注意的是,磨削加工参数的选择并不是孤立的,它们之间存在相互关系。
例如,磨削速度和磨削深度之间的关系是一个复杂的问题。
一般来说,在其他条件相同的情况下,磨削速度越大,磨削深度应选择较小的数值,以保证工件表面质量。
因此,在进行磨削加工时,要综合考虑各个参数之间的关系,确保能够获得满足要求的工件表面粗糙度。
不仅如此,磨削加工参数的选择还需要结合具体的工件材料和形状来进行。
不同材料的切削特性和磨削性能差异很大,在进行磨削加工时,需根据具体情况进行参数调整。
同时,工件的形状也会对磨削加工参数的选择产生影响。
例如,对于大面积的平面磨削,一般可以采用较高的磨削速度和较大的磨削深度,以提高加工效率。
而对于曲面磨削,应适当调整磨削速度和磨削深度,以保证工件表面粗糙度。
轧辊磨床磨削参数的选择
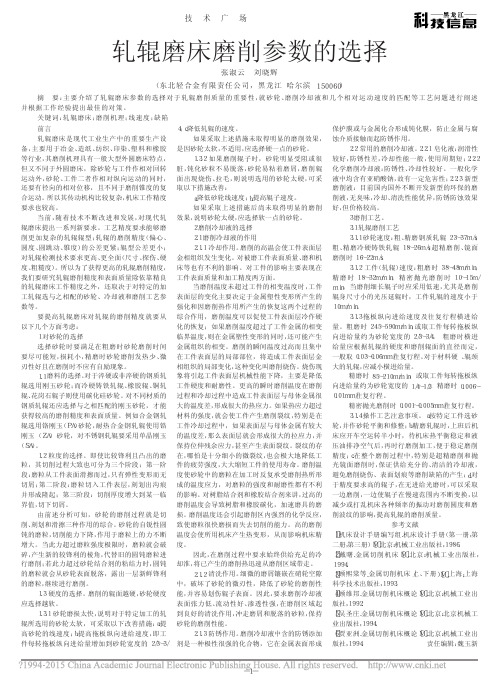
关键词: 轧辊磨床; 磨削机理; 线速度; 缺陷
前言
4; c.降低轧辊的速度。
保护膜或与金属化合形成钝化膜, 防止金属与腐
轧辊磨床是现代工业生产中的重要生产设
如果采取上述措施未取得明显的磨削效果, 蚀介质接触而起防锈作用。
备, 主要用于冶金、造纸、纺织、印染、塑料和橡胶 是因砂轮太软, 不适用, 应选择硬一点的砂轮。
的磨粒, 继续进行磨削。
中, 破坏了砂轮的微刃性, 降低了砂轮的磨削性 科学技术出版社,1993.
1.3硬度的选择。磨削的辊面越硬, 砂轮硬度 能, 并容易划伤辊子表面。因此, 要求磨削冷却液 [4]顾维邦.金属切削机床概论[M].北京:机械工业出
应选择越软。
表面张力低、流动性好、渗透性强, 在磨削区域起 版社,1992.
1.3.1 砂轮磨损太快, 说明对于特定加工的轧 到良好的清洗作用, 冲走磨屑和脱落的砂粒, 保持 [5]吴圣庄.金属切削机床概论[M].北京:北京机械工
辊所选用的砂轮太软, 可采取以下改善措施: a.提 砂轮的磨削性能。
业出版社,1994.
高砂轮的线速度; b.提高拖板纵向进给速度, 即工
2.1.3 防锈作用。磨削冷却液中含的防锈添加 [6]贾亚洲.金属切削机床概论[M].北京:机械工业出
2.2 常用的磨削冷却液。2.2.1 皂化液: 润滑性
等行业, 其磨削机理具有一般大型外圆磨床特点,
1.3.2 如果磨削辊子时, 砂轮明显受阻或很 较好, 防锈性差, 冷却性能一般, 使用周期短; 2.2.2
但又不同于外圆磨床, 除砂轮与工件作相对回转 脏, 钝化砂粒不易脱落, 砂轮易粘着磨屑, 磨削辊 化学磨削冷却液: 防锈性、冷却性较好。一般化学
件每转拖板纵向进给量增加到砂轮宽度的 2/3~3/ 剂是一种极性很强的化合物, 它在金属表面形成 版社,1994.
丝杠磨削过程中的温度场和热变形分析
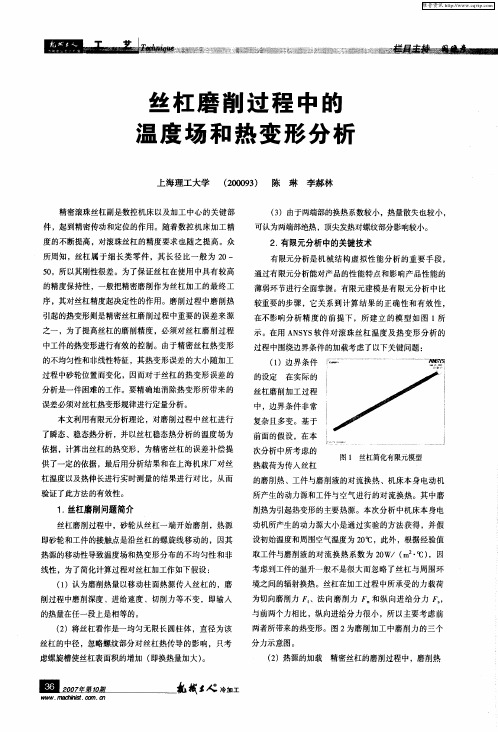
丝杠磨削加工 过程
中, 边界条件 非常
复杂且多 变。基 于 前面 的假设 ,在本
t | …
本文利用有限元分析理论 ,对磨削过程 中丝杠进行 了瞬态 、稳态热分析 ,并以丝杠稳态热分析 的温度场为 依据 ,计算出丝杠 的热变形 ,为精密丝杠 的误差 补偿提 供 了一定 的依据 ,最后用分析结 果和在上海机床 厂对丝 杠温度以及热伸长进行 实时测 量的结果进行对 比, 而 从
误差必须对丝杠热变形规律进行定量分析 。
()由于两端部的换热系数较小 , 3 热量散失也较小, 可认 为两端部绝热,顶尖发热对螺纹部分影响较小 。
2 有限元分析中的关键技术 .
有限元分析是机械 结构 虚拟性 能分析 的重要 手段 ,
通过有 限元分析能对产 品的性能特点 和影 响产品性能 的 薄弱环节进行全面掌握 。有限元建模是有 限元 分析 中比
维普资讯
丝 杠 磨 削 过 程 中 的 温度 场 和 热 变 形分 析
上海理工大学 (o o 3 陈 琳 2o9 ) 李郝林
精密滚珠丝杠副是数控 机床以及加工 中心 的关键 部 件 , 到精密传动和定位的作用。随着数 控机床加工 精 起 度的不 断提高 ,对滚珠丝杠 的精度要求也随之提 高。众 所周知 , 丝杠 属于细 长类 零件 ,其 长径 比一般 为 2 0~ 5 , 以其刚性很差 。为了保证丝杠在使用 中具有较高 0 所 的精度保持性 ,一般把精密磨削作为丝杠加 工的最终工 序 ,其对丝杠精度起决定性 的作用 。磨削过程 中磨削热 引起的热变形则是精密丝杠磨削过程 中重要 的误差 来源 之一 ,为了提高丝杠的磨削精度 ,必须对丝杠磨 削过程 中工件的热变形进行有效的控制 。由于精密丝杠热 变形 的不均匀性和非线性特征 , 其热 变形 误差的大小 随加工 过程中砂 轮位置而变化 ,因而对 于丝杠 的热变形误差 的 分析是一件 困难的工作 。要精确地消 除热 变形 所带来 的
磨削加工中的磨削温度监测
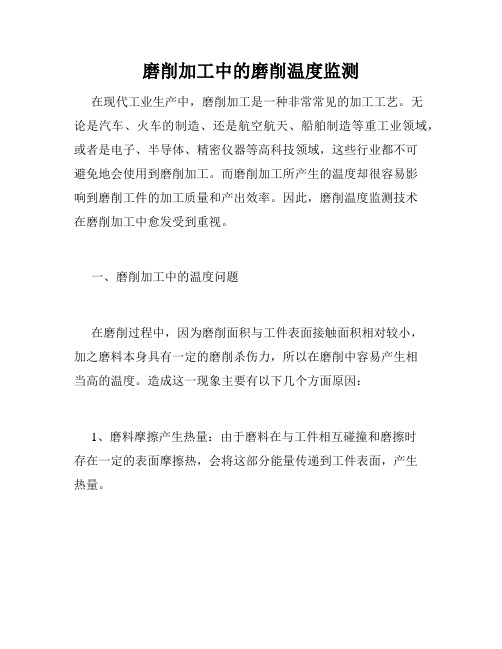
磨削加工中的磨削温度监测在现代工业生产中,磨削加工是一种非常常见的加工工艺。
无论是汽车、火车的制造、还是航空航天、船舶制造等重工业领域,或者是电子、半导体、精密仪器等高科技领域,这些行业都不可避免地会使用到磨削加工。
而磨削加工所产生的温度却很容易影响到磨削工件的加工质量和产出效率。
因此,磨削温度监测技术在磨削加工中愈发受到重视。
一、磨削加工中的温度问题在磨削过程中,因为磨削面积与工件表面接触面积相对较小,加之磨料本身具有一定的磨削杀伤力,所以在磨削中容易产生相当高的温度。
造成这一现象主要有以下几个方面原因:1、磨料摩擦产生热量:由于磨料在与工件相互碰撞和磨擦时存在一定的表面摩擦热,会将这部分能量传递到工件表面,产生热量。
2、变形能转化为热能:在磨削过程中,磨料与工件在弹性变形和塑性变形过程中会将变形能转化为热能,并将这部分热能传递到工件表面中,导致加工温度升高。
3、摩擦热分布不均匀:磨削中由于磨料与工件表面的相对位置不断地改变,摩擦热分布不均匀会导致磨削温度在工件表面的分布不一致。
二、磨削温度监测的必要性由于磨削中的高温会对工件的质量产生较大的影响,而常规的磨削温度监测方法主要基于磨屑或刀具温度表面检测法。
但这些方法都容易受到磨料与工件接触的影响,而且通常需要间接测量状态的方法,所以并不是很准确。
因此,为了提高磨削加工的质量和效率,需要采用更为准确的磨削温度监测技术。
三、磨削温度监测技术的发展1、基于视觉图像处理技术的磨削温度监测系统:这种技术通过摄像机对加工区域进行实时图像监测,抓取磨削过程中加工区域的温度变化信息,并通过数字图像处理技术对温度信息进行分析,得出磨削机构所产生的温度变化规律。
然而,由于受工艺和磨削加工环境、光线等诸多因素的影响,这种技术容易产生误差。
2、基于光纤传感和红外线辐射技术的磨削温度监测系统:这种技术主要通过红外线辐射实时监测加工区域的温度,采用光电转换器将温度信号转换为电信号,进而分析温度信号。
不锈钢的平面磨床磨削方法
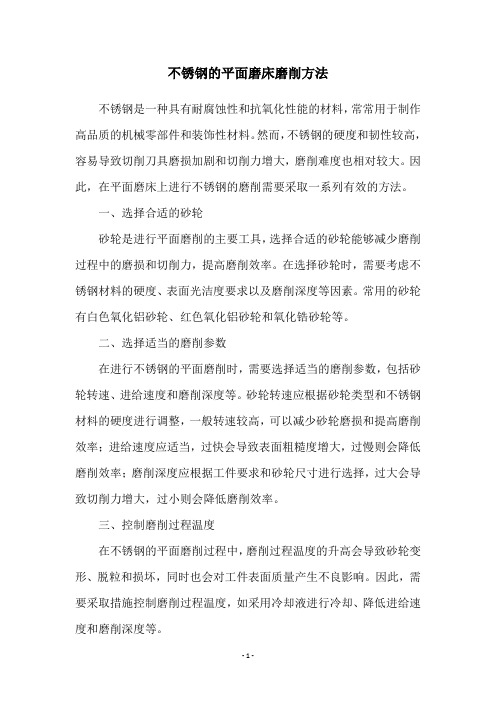
不锈钢的平面磨床磨削方法
不锈钢是一种具有耐腐蚀性和抗氧化性能的材料,常常用于制作高品质的机械零部件和装饰性材料。
然而,不锈钢的硬度和韧性较高,容易导致切削刀具磨损加剧和切削力增大,磨削难度也相对较大。
因此,在平面磨床上进行不锈钢的磨削需要采取一系列有效的方法。
一、选择合适的砂轮
砂轮是进行平面磨削的主要工具,选择合适的砂轮能够减少磨削过程中的磨损和切削力,提高磨削效率。
在选择砂轮时,需要考虑不锈钢材料的硬度、表面光洁度要求以及磨削深度等因素。
常用的砂轮有白色氧化铝砂轮、红色氧化铝砂轮和氧化锆砂轮等。
二、选择适当的磨削参数
在进行不锈钢的平面磨削时,需要选择适当的磨削参数,包括砂轮转速、进给速度和磨削深度等。
砂轮转速应根据砂轮类型和不锈钢材料的硬度进行调整,一般转速较高,可以减少砂轮磨损和提高磨削效率;进给速度应适当,过快会导致表面粗糙度增大,过慢则会降低磨削效率;磨削深度应根据工件要求和砂轮尺寸进行选择,过大会导致切削力增大,过小则会降低磨削效率。
三、控制磨削过程温度
在不锈钢的平面磨削过程中,磨削过程温度的升高会导致砂轮变形、脱粒和损坏,同时也会对工件表面质量产生不良影响。
因此,需要采取措施控制磨削过程温度,如采用冷却液进行冷却、降低进给速度和磨削深度等。
四、定期更换砂轮
砂轮的磨损程度会影响磨削效率和工件表面质量,因此需要定期更换砂轮,以保证磨削效率和磨削质量。
同时,在更换砂轮时也需要注意选择合适的砂轮规格和类型。
不锈钢的平面磨床磨削方法需要综合考虑多种因素,采取有效的措施进行控制和调整,方可达到理想的磨削效果和工件表面质量。
- 1、下载文档前请自行甄别文档内容的完整性,平台不提供额外的编辑、内容补充、找答案等附加服务。
- 2、"仅部分预览"的文档,不可在线预览部分如存在完整性等问题,可反馈申请退款(可完整预览的文档不适用该条件!)。
- 3、如文档侵犯您的权益,请联系客服反馈,我们会尽快为您处理(人工客服工作时间:9:00-18:30)。
磨削温度对磨削效果的影响
磨削温度对磨削效果的影响
大量的磨削热将会软化工件表面,使其塑性增加,有利于磨屑的形成。
但对被磨工件表面质量、磨和机床等也有不利的影响。
对工件的影响主要表现在工件表面质量和加工精度两
方面。
磨削的高温会使工件表面层金相组织发生变化。
当磨削温度未超过工件的相变温度时,工件表面层的变化主要决定于金属塑性变形所产生的强化和因磨削热作用所产生的恢复这两个过程的综合作用,磨削温度可以促使工件表面层冷作硬化的恢复;如果磨削温度超过了工件金属的相变临界温度,则在金属塑性变形的同时,还可能产生金属组织的相变。
磨削的瞬间温度过高而且集中在工件表面层的局部部位,将造成工件表面层金相组织的局部变化,这种变化叫磨削烧伤。
烧伤现象将引起工件表面层机械性能下降,主要是降低工件硬度和耐磨性。
磨削烧伤可分为两类:第一类是指工件磨削温度尚未达到工件材料的临界温度,仅仅使工件表面层产生回火现象,这时表面层金相组织出现回火层。
第二类是指工件磨削温度超过工件材料的临界温度,在通过磨削区时由于急速冷却而产生二次淬火现象,此时表面层的金组织由回火层和二次淬火形成的索氏状、托氏体组成。
更高的瞬时磨削温度在磨削过程和冷却过程中造成工件表面层与母体金属很大的温度差,形成很大的热应力。
如果热应力超过材料的强度,就会使工件产生磨削裂纹,特别是在工件冷却过程中,如果表面层与母体金属有较大的温度差,那么表面层就会形成很大的拉应力,并保持位伸残余应力,甚至产生表面裂纹。
裂纹的存在,哪怕是十分细小的微裂纹,也会极大地降低工件的疲劳强度,大大缩短工件的使用寿命。
由以上所述可以看到,影响磨削烧伤的主要因素是磨削瞬间时的高低,而磨削裂纹和残余应力的起因则为被磨工件表面层的温度梯度,这一点在磨削那些导热系数的抗拉强度低的材料时更应特别注意。
有时在磨削导热性差的材料时,为了减少温度梯度,可以用加热被磨工件的方法来降低磨削温度的梯度,防止产生磨削裂纹。
磨削温度使砂轮中的磨粒在加工时反复承受磨削热所形成的温度应力,对磨粒的强度和耐磨性都有不利的影响。
对树脂结合剂和橡胶结合剂来讲,过高的磨削温度会导致树脂和橡胶碳化,加速磨具的磨损。
磨削温度还会引起磨削区内强烈的化学反应,致使磨粒很快磨损而失去切削的能力。
高的磨削温度会使所用机床产生热变形,从而影响机床
精度。