软包装制袋常见问题
制袋机操作常见问题
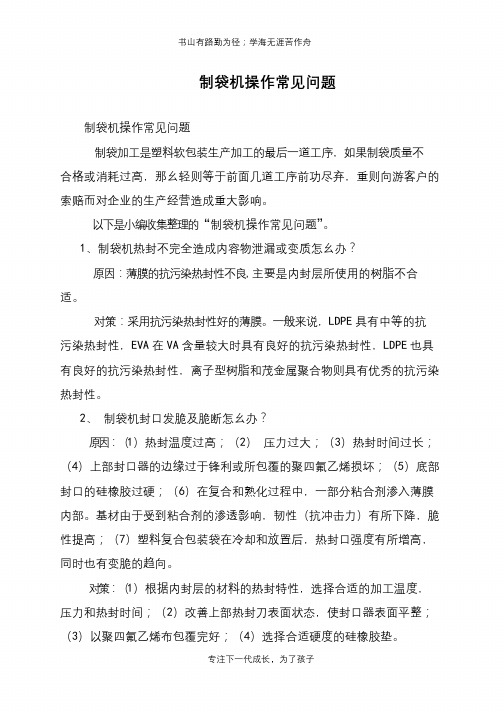
的张力,尽量使相复合的两种基材回缩:(1)冷却时间短;(2)冷却板接触不良;(3)由于硅胶
垫被加热,使得边缘部分熔化;(4)纵向热封力不平横;(5)热封刀的
边缘不整齐、发钝。
对策:(1)调整冷却时间;(2)调整冷却板;(3)更换或调整
(8)控制好复合胶粘合剂中MDI的单体含量。
(9)检查热封面的处理程度。
(10)更换油墨(最好采用两液型油墨)。
(11)改变包装袋的印刷图样,使印有油墨的部分避开热封部位,
或改变热封方法。(特别注意金属油墨不要印在封口处)。
6、热封部位产生气泡或表面不平怎幺办?
原因:(1)在含有尼龙薄膜等吸湿性的材质结构上进行热封时,
专注下一代成长,为了孩子
书山有路勤为径;学海无涯苦作舟
合剂渗到内层表面,影响了基材薄膜表面的摩檫系数,尤其是在薄膜较薄、
电晕处理过度的情况下更容易发生此类问题;(3)薄膜基材本身爽滑性
不良。
对策:(1)严格控制熟化条件(按产品熟化作业指导书);(2)
检查粘合剂的种类或级别;(3)更换基材或使用喷粉。
太小;(3)有些辊转动不平稳。
对策:(1)调整双浮动辊张力;(2)检查并调整有关导辊
(如补偿辊、调偏辊等)。
专注下一代成长,为了孩子
原因:薄膜的抗污染热封性不良,主要是内封层所使用的树脂不合
适。
对策:采用抗污染热封性好的薄膜。一般来说,LDPE具有中等的抗
污染热封性,EVA在VA含量较大时具有良好的抗污染热封性,LDPE也具
有良好的抗污染热封性,离子型树脂和茂金属聚合物则具有优秀的抗污染
热封性。
2、制袋机封口发脆及脆断怎幺办?
史上最全的软包装技术问题汇总下

史上最全的软包装技术问题汇总(下)41、如何解决复合薄膜热封部位的发泡问题?复合薄膜在热封部位出现发泡是由于薄膜中间层为吸水的尼龙薄膜,在进行热封加工时,由吸湿薄膜部开始出现发泡。
解决的方法是在复合薄膜保管中避开湿气。
42、利乐包装材料表面淋膜关键工艺与温控条件?淋膜产品质量控制主要来自四个方面:温度控制、压力控制、冷却系统和电晕处理。
43、如何判断包装袋中的材料(应该是PE、PP、OPP. PET) ?袋子的结构一般是内层为PE或者为CPP,外层为BOPP或者PET。
PE或CPP和BOPP的结构存在剥离强度低的问题,PE或CPP和PET的剥离强度高,所以我们可以通过撕背封的地方加以判断,轻撕后如果撕开的是三角口则表层为BOPP,如果没有分层表层就是PET;然后就是盘算内层,PE在撕开的时候没有声音,而且层的表面没有金属光泽,CPP撕开的时候有声音。
如果你可以撕开表层的话也可以根据密度来区分,BOPP的密度小于水,扔水里漂在水面上, 如果是BOPP则沉底。
还有,也可以把整个取样(带PE或CPP)的仍入水里,如果整个袋子的厚度是在7丝以下的话,沉底的是外表PET,飘起来的是B0PP。
44、有什么好的方法解决蒸煮袋开口性差吗?我们厂是从事凹印的,主要生产蒸煮袋,基材是PET/PE,不知道什么原因,生产出来的成品袋开口性极差,用手搓开后匝在一起的话会粘在一起,一只手很难打开,是不是PE的问题?根本原因在PE上,解决重点放在预防上,PE中的开口剂要保证,在原料检验时注意;如果在复合后、制袋前发现,可以通过喷粉解决;PE膜的问题,在熟化时温度不要太高,另外PE选料时要注意粒子本身的爽滑剂的含量和类型,使用析出缓慢的爽滑剂,并在PE中多加爽滑剂。
45、我公司在复合PE时经常出现复合强度不好,初步确定是PE料的问题,不知怎样在复合前检查PE是否合格?复合强度不好有多种原因:A:原料的处理是否合格,一般采用38达因的处理液测试;B:印刷膜采用的油墨问题,如PET或NY,经常易出现复合强度不牢,可稍微多加些固化剂或提高上胶量;C:PE料配方问题,PE料内含有爽滑剂等助剂成分,会析出表面影响剥离强度;D:胶水选用是否得当,如果PE较厚,在6丝以上,则需要选用适合的胶黏剂,我们一般采用聚酸型的,常温熟化,但是这类胶水会影响摩擦系数。
制袋常见问题及处理方法
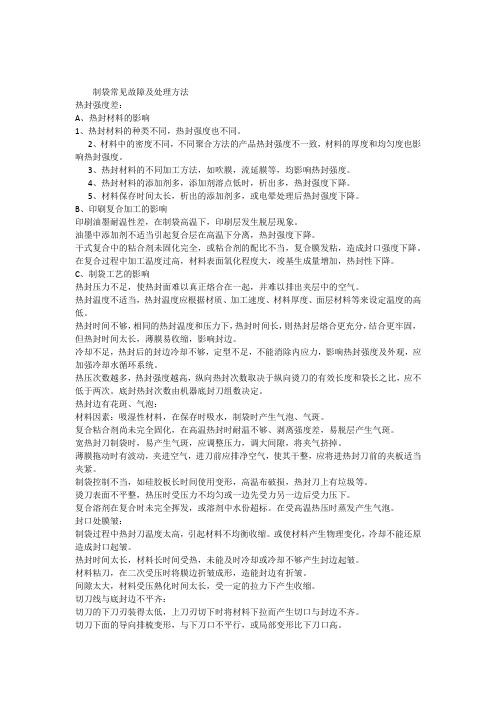
制袋常见故障及处理方法热封强度差:A、热封材料的影响1、热封材料的种类不同,热封强度也不同。
2、材料中的密度不同,不同聚合方法的产品热封强度不一致,材料的厚度和均匀度也影响热封强度。
3、热封材料的不同加工方法,如吹膜,流延膜等,均影响热封强度。
4、热封材料的添加剂多,添加剂溶点低时,析出多,热封强度下降。
5、材料保存时间太长,析出的添加剂多,或电晕处理后热封强度下降。
B、印刷复合加工的影响印刷油墨耐温性差,在制袋高温下,印刷层发生脱层现象。
油墨中添加剂不适当引起复合层在高温下分离,热封强度下降。
干式复合中的粘合剂未固化完全,或粘合剂的配比不当,复合膜发粘,造成封口强度下降。
在复合过程中加工温度过高,材料表面氧化程度大,竣基生成量增加,热封性下降。
C、制袋工艺的影响热封压力不足,使热封面难以真正熔合在一起,并难以排出夹层中的空气。
热封温度不适当,热封温度应根据材质、加工速度、材料厚度、面层材料等来设定温度的高低。
热封时间不够,相同的热封温度和压力下,热封时间长,则热封层熔合更充分,结合更牢固,但热封时间太长,薄膜易收缩,影响封边。
冷却不足,热封后的封边冷却不够,定型不足,不能消除内应力,影响热封强度及外观,应加强冷却水循环系统。
热压次数越多,热封强度越高,纵向热封次数取决于纵向烫刀的有效长度和袋长之比,应不低于两次。
底封热封次数由机器底封刀组数决定。
热封边有花斑、气泡:材料因素:吸湿性材料,在保存时吸水,制袋时产生气泡、气斑。
复合粘合剂尚未完全固化,在高温热封时耐温不够、剥离强度差,易脱层产生气斑。
宽热封刀制袋时,易产生气斑,应调整压力,调大间隙,将夹气挤掉。
薄膜拖动时有波动,夹进空气,进刀前应排净空气,使其干整,应将进热封刀前的夹板适当夹紧。
制袋控制不当,如硅胶板长时间使用变形,高温布破损,热封刀上有垃圾等。
烫刀表面不平整,热压时受压力不均匀或一边先受力另一边后受力压下。
复合溶剂在复合时未完全挥发,或溶剂中水份超标。
软包装制袋顶封不够宽预防措施
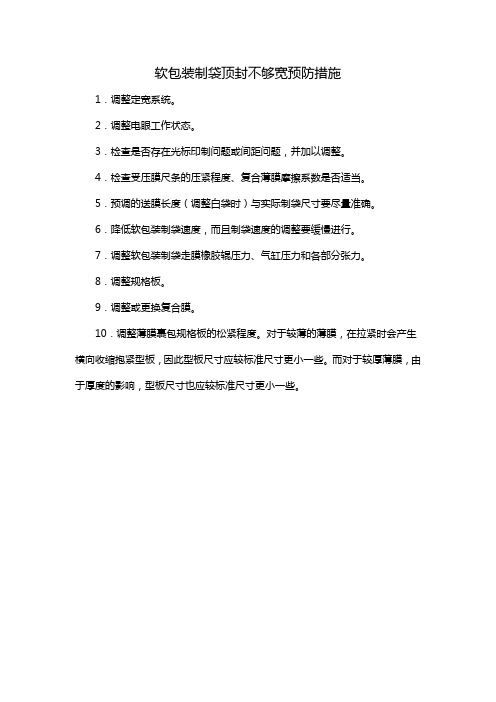
软包装制袋顶封不够宽预防措施
1.调整定宽系统。
2.调整电眼工作状态。
3.检查是否存在光标印制问题或间距问题,并加以调整。
4.检查受压膜尺条的压紧程度、复合薄膜摩擦系数是否适当。
5.预调的送膜长度(调整白袋时)与实际制袋尺寸要尽量准确。
6.降低软包装制袋速度,而且制袋速度的调整要缓慢进行。
7.调整软包装制袋走膜橡胶辊压力、气缸压力和各部分张力。
8.调整规格板。
9.调整或更换复合膜。
10.调整薄膜裹包规格板的松紧程度。
对于较薄的薄膜,在拉紧时会产生横向收缩抱紧型板,因此型板尺寸应较标准尺寸更小一些。
而对于较厚薄膜,由于厚度的影响,型板尺寸也应较标准尺寸更小一些。
好文!软包装三种质量故障实例分析

好文!软包装三种质量故障实例分析【摘要】文章列出三种包装袋遇到质量问题时的原因分析和解决方案,有案例,通俗易懂,建议收藏学习。
【正文】一、立式袋离层折痕1、现象描述结构为PET12/VMPET12/PE80的立式奶粉袋,在超市使用半年,出现PET与VMPET之间发生非油墨层分层现象。
2、原因分析立式袋包装的是小袋装奶粉,因此包装内容物的化学性质不会影响包装袋的质量,但由于包装内容物克重为450g,在超市摆放过程中,立式袋起皱的地方就容易出现离层现象。
查生产记录,发现该袋表层使用的是上一单剩余的脆性高的快干性胶进行复合,脆性胶不耐折,因此需要选用软硬合适的复合胶。
二、复合膜复合强度低1、现象描述结构为BOPP28/VMCPP25结构的退热贴包装袋,双色印刷,无满版白墨托底,复合后剥离强度低,复合离层。
2、原因分析在红墨区和绿墨区剥离强度都很低,原因是在油墨中,原黄墨表现为略带正极性,原红墨为负极性,原蓝墨为负极性,因此由原黄和原蓝配成的绿色墨极性是中性的,其复合强度就比较低,但红墨在这里表现出剥离强度低主要是因为油墨供应商的红色蜡料加入量太大,析出影响复合强度,因此建议选用正规厂家的油墨或印刷面(油墨面)进行电晕一次,并在8小时内进行复合。
三、复合气泡现象1、现象描述结构为PET12/AL17/NY15/MIPE60电子产品包装袋。
在生产过程中,第一天复合PET和AL,没有出现气泡现象;第二天连续复合NY及MIPE,也没出现气泡问题了生产完在车间常温放置2天,未观察到质量问题;然后将其送入熟化室熟化48小时,第6天进行制袋时发现复合膜表面呈带状的起泡现象,并且气泡发生在尼龙和纯铝之间。
2、原因分析通过查生产记录,复合膜PET/AL与NY之间采用的是未变质的胶水,排除了使用过期胶水引起的胶水变质而产生气泡的情况。
再仔细分析气泡的分布情况,无周期性规律,也排除因网辊网孔堵塞产生气泡的情况。
通过与胶水供应商沟通,该胶水的初黏力较低,建议复合后马上进入熟化室。
薄膜复合制袋中常见皱褶问题分析

薄膜复合制袋中常见皱褶问题分析复合薄膜的表面皱褶是复合软包装材料加工及应用过程中常见的问题。
人们通常会说:表面皱褶问题常常会有胶水不干现象相伴随,即将有表面皱褶问题的复合膜剥开时,常常会发现复合膜的胶层有不同程度的“发粘”现象。
因此,人们得出结论:复合薄膜的表面皱褶问题是由于胶水不干问题所引发的!复合薄膜的表面皱褶问题可以出现在复合薄膜的生产及应用的不同阶段:1. 复合薄膜下机时;2. 复合薄膜经过熟化处理后;3. 制袋加工完成时及放置一段时间后;4. 水煮处理完成时及放置一段时间后;5. 蒸煮处理完成时及放置一段时间后。
下图是制袋加工后的表面皱褶的案例之一。
所谓表面皱褶问题的表现是:表层的薄膜向上凸起;内层的薄膜向下凹陷。
上图的表面皱褶即属于“表层薄膜向上凸起”类的。
迄今为止,尚未发现在一张复合薄膜或一个复合膜袋上“表层的薄膜向上凸起”和“内层的薄膜向下凹陷”现象同时发生的现象。
在复合薄膜下机时所出现的表面皱褶,过去俗称为“隧道”,很多人都将其归因为胶水的“初粘力”不足。
伴随着无溶剂型干法复合加工技术的逐步普及,现在已很少有人投诉“胶水初粘力不足”了,因为大家都已清楚地知道:复合膜下机时的隧道问题的原因是放卷张力控制不良!由于放卷的张力控制(设定)不良,使得两个复合基材在复合加工过程中处于不同的延伸率状态,例如PET/CPP的复合薄膜,可能PET膜被拉长了千分之二,CPP膜被拉长了千分之四,当复合过程结束时(即复合膜下机了),由于外加的张力已去掉了,因此,PET膜就会“试图”回缩千分之二,CPP膜也会“试图”回缩千分之四。
如果此时的胶层的初粘力足够大,则两个复合基材都不能回缩到其初始的长度,所以,下机的复合膜就会呈现向CPP层方向卷曲的状态;如果此时的胶层的初粘力不够大,则PET膜就有可能完全恢复到其初始状态,CPP膜也将最大程度地恢复到接近其初始状态的状态。
此时,在两层复合膜间就出现了长度的差异,即在单位长度上,PET膜比CPP 膜长了将近千分之二!其结果就是出现了隧道问题--CPP膜平直、PET膜向上凸起的隧道!隧道问题的严重程度(单位长度上隧道的数量、隧道的长度以及隧道凸起的高度)是与两层基材膜间长度的差异成正比的!从以上的描述中不难发现:对于刚下机的复合薄膜而言,是否会产生隧道问题的原因是在无外加张力的条件下复合薄膜间是否存在长度上的差异,以及胶层的初粘力或剥离力是否足够大!由此可以推断:此种状态下所出现的隧道问题与胶层是否完全固化(即是否发粘)完全没有关系!据此,可以推而广之。
塑料软包装制袋加工的常见问题

塑料软包装制袋加工的常见问题1.跌落试验,包装袋破损的原因?原因:包装袋有时在热封温度较低的情况下,热封强度虽然较低,但也能满足顾客要求,但在进行跌落试验时包装袋不破损。
而在热封温度较高的情况下,热封强度虽然较高,但在进行跌落试验时包装袋破损。
这一现象说明,热封温度较高时,在热封刀压力的作用下,承载热封功能的内层PE薄膜经高温熔融、挤压而变薄、发脆,导致跌落试验时发生破损。
解决办法:在进行制袋工艺时,要调节适当热封温度、压力。
才能生产出综合性能优异的产品。
2.封口发脆及脆断怎么办?原因:(1)热封温度过高。
(2)压力过大。
(3)热封时间过长。
(4)上部封口器的边缘过于锋利或所包覆的聚四氟乙烯损坏。
(5)底部封口的硅橡胶过硬。
(6)在复合和熟化过程中,一部分粘合剂渗入薄膜内部。
基材由于受到粘合剂的渗透影响,韧性(抗冲击力)有所下降,脆性提高。
(7)塑料复合包装袋在冷却和放置后,热封口强度有所增高,同时也有变脆的趋向。
解决方法:(1)根据内封层的材料的热封特性,选择合适的加工温度,压力和热封时间。
(2)改善上部热封刀表面状态,使封口器表面平整。
(3)以聚四氟乙烯布包覆完好。
(4)选择合适硬度的硅橡胶垫。
3.封口处有静电怎么办解决办法:二次加工时,可在内层PE薄膜中加入3%的卫生级抗静电剂,避免此类问题的发生。
所以,软包装企业在接顾客定单时,要充分了解顾客的产品特性与自动灌装生产线特点,才能有的放矢,更好地满足顾客要求。
4.热封后袋子翘曲怎么办?原因:(1)复合膜的厚度不一致。
(2)热封温度过高或热封时间过长。
(3)在纵向热封刀部分,复合膜的运行轨迹不平直。
(4)冷却不充分。
(5)熟化时间不够。
(6)表层基材薄膜耐热性较差。
(7)复合过程中复合基材的张力匹配控制不当,导致其熟化定型后仍有残余的应力,尤其是复合膜厚度较薄时更容易发生此类故障。
解决方法:(1)调整浮动辊张力。
(2)选用具有低温热封性的内封基材。
分切、制袋工序中常见质量问题及解决方法
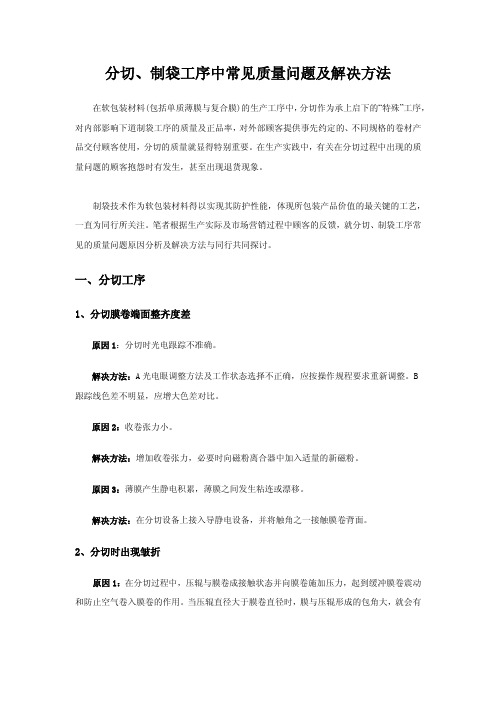
分切、制袋工序中常见质量问题及解决方法在软包装材料(包括单质薄膜与复合膜)的生产工序中,分切作为承上启下的“特殊”工序,对内部影响下道制袋工序的质量及正品率,对外部顾客提供事先约定的、不同规格的卷材产品交付顾客使用,分切的质量就显得特别重要。
在生产实践中,有关在分切过程中出现的质量问题的顾客抱怨时有发生,甚至出现退货现象。
制袋技术作为软包装材料得以实现其防护性能,体现所包装产品价值的最关键的工艺,一直为同行所关注。
笔者根据生产实际及市场营销过程中顾客的反馈,就分切、制袋工序常见的质量问题原因分析及解决方法与同行共同探讨。
一、分切工序1、分切膜卷端面整齐度差原因1:分切时光电跟踪不准确。
解决方法:A光电眼调整方法及工作状态选择不正确,应按操作规程要求重新调整。
B跟踪线色差不明显,应增大色差对比。
原因2:收卷张力小。
解决方法:增加收卷张力,必要时向磁粉离合器中加入适量的新磁粉。
原因3:薄膜产生静电积累,薄膜之间发生粘连或漂移。
解决方法:在分切设备上接入导静电设备,并将触角之一接触膜卷背面。
2、分切时出现皱折原因1:在分切过程中,压辊与膜卷成接触状态并向膜卷施加压力,起到缓冲膜卷震动和防止空气卷入膜卷的作用。
当压辊直径大于膜卷直径时,膜与压辊形成的包角大,就会有空气卷入膜卷而产生纵向皱折;随着膜卷直径的增加,当压辊直径小于膜卷直径时,膜与压辊形成的包角变小,卷入的空气就少,膜卷较为整齐。
解决方法:选用直径大的纸芯,减小压辊直径。
原因2:压辊作用于膜卷的压力由气缸压力产生,并随着膜卷直径和分切线速度的增加而增加。
由于压辊压力的增加,容易造成膜卷“内松外紧”现象,皱折由此而产生。
解决方法:随着膜卷直径和分切线速度的增加,适当调小压辊压力。
原因3:在分切过程中,张力设置过大,膜卷收卷时横向受力分配不均匀,膜卷平整度较差,极易产生皱折。
若张力设置太小,膜卷收卷时容易发生跑边、膜卷松动。
解决方法:适当设置收卷张力;且随着膜卷直径的增大,逐步减小收卷张力。
- 1、下载文档前请自行甄别文档内容的完整性,平台不提供额外的编辑、内容补充、找答案等附加服务。
- 2、"仅部分预览"的文档,不可在线预览部分如存在完整性等问题,可反馈申请退款(可完整预览的文档不适用该条件!)。
- 3、如文档侵犯您的权益,请联系客服反馈,我们会尽快为您处理(人工客服工作时间:9:00-18:30)。
软包装制袋常见问题
蒸煮袋是用来包装蒸煮食品的塑料软包装,根据耐温性能不同而分为耐水
煮袋(≤100℃)、耐蒸煮袋(121-125℃)和耐高温蒸煮袋(≥135℃)。
经过约30
分钟高温杀菌后,蒸煮袋能大大延长食品的保质期,因而蒸煮袋的生产获得了
迅速发展。
蒸煮袋脱层是指装入食品蒸煮后发生的脱层现象。
该问题具有一定
的潜伏性,印刷、复合、熟化时就已埋下隐患,但问题一般发生在食品企业使
用蒸煮袋时,因而往往给企业造成重大损失。
蒸煮袋的结构一般为:(内层)CPP等薄膜/胶水/油墨/尼龙等薄膜(外层),
脱层可能发生在上述任何两种材料的界面之间,共有三个界面,即内层薄膜/胶水、胶水/油墨、油墨/外层薄膜。
脱层现象轻微时表现为在包装的受力部位呈
条纹状脱离,或用手很容易剥离撕开,严重时则在蒸煮后自然呈大面积脱离。
造成蒸煮袋脱层的原因有如下几个方面:
1、油墨或胶水的耐湿热粘接强度不够。
蒸煮袋所用的油墨或胶水不管是双组分或单组分,一般是采用聚氨酯树脂制造而成,油墨或胶水的耐湿热性能主
要由聚氨酯树脂的耐湿热性能决定。
就聚氨酯树脂本身的特性来说,由于聚氨
酯树脂中的酯键、氨脂键等基团有较强的极性,湿热条件下易受到湿气的进攻,发生水解,且聚氨酯树脂与基材表面形成的氢键易受湿热而被破坏,从而使粘
接强度降低,甚至胶粘层脱落。
油墨或胶水生产厂家应该从技术上通过改变聚
氨酯树脂的化学结构以及采用添加剂来提高蒸煮油墨在经过高温蒸煮后的附着
强度。
2、软包装生产企业对油墨或胶水的使用操作存在问题。
主要有以下几点:一是固化剂用量不符合要求。
按要求既不能用少,也不能用多,若用量少了,
则固化剂与树脂的交联程度不够,墨层的粘附强度、耐热性、耐水解性就会降低;若用量多了,则会发生过度的交联,影响高分子间的结晶和微观相分离,
从而可能会损害胶层的内聚强度,内应力增加,墨层过分收缩,引起脱层。
二
是熟化时间达不到要求,时间短则交联不充分,墨层耐温、耐水解性降低。
三
是油墨或胶水活性不够,或掺多了过期失效剩余物。
在未印刷或复合前若油墨
或胶水活性不够,则可用来连接基材的基团数量少,因而附着力不强。
3、油墨、胶水及薄膜间的配伍性不符。
根据粘附理论,当胶粘剂与被粘物
表面张力相等且极性相同时,界面张力最小,粘附强度最高。
因此,油墨、胶
水固化成膜后的表面以及薄膜表面的状况就有可能随不同厂家的产品情况而异,由于各种表面的基团不能很好地发生吸引形成分子间力或者发生化学反应形成
化学键,即使在低温时有一定的作用而形成附着力,但在高温情况下,表面基
团微弱的连接可能受到破坏而发生脱层。
4、薄膜问题。
表现在如下两个方面:一是薄膜处理度达不到要求,或根本
就未处理。
操作人员往往并未发现这个问题,以至于在印刷后、复合后、熟化
后附着牢度都不高,在蒸煮后脱层才发现这个问题。
在生产实践中,我已发现
过好几起这类事例。
二是薄膜内的某些添加剂在高温时加快游离到表面,可能
会造成附着力下降。
如塑料薄膜中添加的开口剂、抗静电剂、爽滑剂等。
蒸煮袋发生蒸煮脱层事故后,企业首先要仔细辨别脱层发生在哪个界面间,弄清与哪两个材料有关,并检查生产工序上是否按照要求操作,同时可调换材
料作对比试验,以查出脱层的真正原因。
为了防止出现蒸煮袋脱层事故,企业
应做好如下工作:
1、食品企业使用蒸煮袋时应严格控制温度在蒸煮袋生产企业所保证的范围
之内。
因为即使是超出几度,但由于这时制作蒸煮袋的各类材料往往已达到所
能承受的极限,这超出的几度对蒸煮袋的性能是否能保证就非常关键。
2、食品企业应做好对批量使用蒸煮袋前蒸煮袋性能的确认。
这种确认也就
是在特定工艺条件下蒸煮袋可否使用的工艺条件试验。
因为内包装物的理化特性,以及在高温下因可能发生的理化变化而产生的新物质等都有可能在蒸煮袋
层内渗透从而引起蒸煮袋包装性能的下降,如造成脱层。
即使是蒸煮袋内的真
空度也可能引起蒸煮袋各层之间应力的差异,而引起粘附力较差的薄膜层间脱离。
3、蒸煮袋生产企业应加强管理工作,做好各工序的工艺指标检测和控制,
特别是要把好蒸煮袋出厂前盛物试验的最后一关。
一是要注意薄膜的处理度是
否达到要求,这对印刷牢度和复合牢度至关重要。
二是要注意熟化时间,让双
组分的油墨或胶水充分起交联固化反应。
三是要注意双组分油墨或胶水在使用
时的失活程度,掺入失活油墨或失活胶水的量一定要控制在一定范围内。
四是
要严格按照材料厂家提供的产品说明书使用,特别是油墨及胶水的固化剂量一定要按要求使用。
五是要模拟食品企业使用的工艺条件来检测成品袋的性能,并督促食品企业对蒸煮袋使用性能的确认,防止出现更大损失。
4、蒸煮袋生产企业要做好各类包装印刷材料的配伍性使用试验。
因为各类产品的使用范围都有一定的局限性和特殊性,无法控制或照顾到各类用户后处理加工及进一步深加工和使用的方方面面,对下游产品的加工处理及后续产品的使用要求也不一定了解很全面。
配伍性试验要注意如下几点:一是要注意试验应贯穿在全生产工序,不可仅停留在印刷阶段。
二是要注意耐高温情况,特别注意高温下薄膜内各种添加剂渗出而引起附着力下降或脱层的问题。
三是要注意更换不同厂家材料,甚至是使用同厂家但不同批号的材料时,也要做好配伍性使用试验。
5、油墨、胶水、薄膜等包装材料生产企业要扎扎实实地提高和稳定产品质量。
一是要提高油墨、胶水的耐温性能。
实际耐温性能要有一定幅度地超出所保证的耐温性能。
二是薄膜生产企业要注意某些添加剂对高温蒸煮后附着力的影响。
三是注意工艺参数的控制,确保产品质量的稳定性,特别是在换用新材料情况下。
四是尽可能全面了解用户及下游用户的使用条件。