前处理烧毛工艺
棉织物前处理—棉织物烧毛

气体烧毛机 特点:设备结构简单、操作方便、劳动强度较低、热能利
用充分、品种适用性强、烧毛质量较好。但对低级棉织物及粗 厚织物的烧毛效果不及铜板烧毛机。
烧毛装置:主要由火口、气体和空气混合器组成。
火口是气体烧毛机的主要部件,火口的性能直接影响到可燃性
气体的燃烧情况、烧毛的效率和质量。一个优良的火口,火口
刷毛装置:主要由4~8只鬃毛或尼龙刷辊组成 作用:刷去织物表面的纱头、尘埃和杂物,防止浮在织物表面的纱头等在
烧毛时使织物产生破洞;并使绒毛竖立以利烧毛
气体烧毛工艺 工艺流程:进布 →刷毛 →烧毛 →灭火 →出布 工艺条件:
火焰温度: 800~900℃ 车 速: 稀薄织物100~150m/min
一般织物80~100m/min 厚重织物60~80m/min
烧毛面: 一般平布、府绸等织物正反面烧毛次 数相同,如二正二反 斜纹、卡其等有正反面之分的织物, 以烧正面为主,如三正一反 稀薄织物一般采用一正一反
织物与还原焰距离: 稀薄织物1~1.2cm 一般织物0.8~1.0cm 厚重织物0.5~1.8cm
烧毛次数: 一正一反、二正二反、 三正一反
前处理工艺实施与管理
烧毛
烧毛加工
定义:利用高温将布面上的绒毛烧去量; 提高服用性能。
原理:将织物迅速通过烧毛机的火焰或擦过赤热的金 属表面,利用织物上的绒毛与织物主体升温的快慢不 同,从而达到只烧去绒毛而又不损伤织物的目的。
烧毛方式:接触式烧毛——铜板烧毛、圆筒烧毛 非接触式烧毛——气体烧毛
喷射速度应快,火焰温度应高而均匀;火口结构要简单,且不
易变形,维修方便;同时耗用燃料省,热能利用率高。
狭缝式火口 1-火口缝隙 2-可燃性气管 3-
染整概论

3、染色牢度:
染色牢度是指染色制品在使用或在染后的加工 过程中,染料(或颜料)在各种外界因素的影 响下,保持原来色泽的能力。
(1)日晒牢度 染色织物与规定标样间褪色相同即为该级。为1~8级。 1级最差,相当于在太阳光下曝晒3小时开始褪色, 8级相当于曝晒384小时开始褪色。 (2)皂洗牢度: 染色织物在规定条件下在肥皂液中皂洗后褪色的程度, 它包括原样褪色与白布沾色。溶液的温度分40℃、 60℃、95℃三种。分5级9档。1级最差,褪色、沾 色最严重;5级最好,不沾色。 (3)摩擦牢度: 分干摩与湿摩二种。观察白布沾色情况。湿摩为用含 水100%的白布。分5级9档。1级最差,沾色最严重; 5级最好。
布铗丝光机
1.透风架、 2.3轧车、 4.绷布辊、 5.布铗伸幅淋吸去碱、 6.去碱蒸箱、 7.水洗槽
直辊丝光机
3.直辊浸轧碱液
高速丝光机
2.3.5三台轧车
4、丝光效果检测及常见疵点
(1)丝光效果常用丝光钡值来测定。一般 大于130。 (2)皱条,去碱蒸箱导布辊不平整,张力 太小。 (3)纬斜,导布辊不平,轧辊左右压力不 匀。 (4)拉破,织物扩幅过大,布铗处去碱不 净。
3、煮练用剂: 烧碱、表面活性剂、硅酸钠、亚硫酸钠、磷酸三 钠
4、煮练工艺
工艺流程
轧碱 汽蒸 水洗 薄30~40 g/L 厚40~50 g/L 薄 3~5 g/L 厚 5~8 g/L 0~5 g/L 0~1 g/L
工艺处方
NaOH 渗透剂 亚硫酸氢钠 磷酸三钠
工艺Байду номын сангаас件
浸轧温度 轧余率 汽蒸温度 汽蒸时间 85~90 ℃ 80~90 % 100~102 ℃ 薄45~60min 厚60~90min
蜡染布生产工艺流程
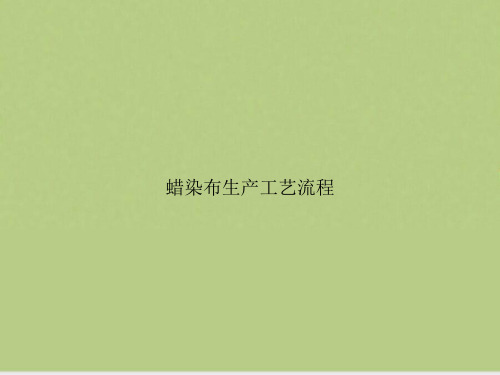
2、仿靛蓝的染色工艺流程 )至少达到140以上,布面平整无皱褶,幅宽113-115cm以上,丝光落布ph值7-8,丝光碱浓度220-240g/L,淡碱浓度40-60g/L 甩蜡时根据蜡纹的粗细、疏密情况,控制给水量,选择合适的旋转数。 采用正反旋转的甩蜡机正反转数一般选择偶数,以保证蜡纹的均匀、织物在开幅时不缠绕,同时起到保护蜡面的作用。 打底—显色—水洗(冷绳洗、热绳洗)—检验拼花—皂洗—拉幅、上浆、定型、烘干—干落布 丝光:将织物在经纬向施加一定张力的状态下浸轧浓碱的加工工序。 同时,蜡印辅助工序还包括化蜡、回收、新旧蜡 比例的调和、花网制作等。 圆网上方有保温罩,保证圆网表面温度在135℃以上,开动蜡印机,A、B网同时压向织物便可进行印蜡。
一、前 ❖处理经过翻、缝、烧,退、煮、漂等前处理加工后的白
前处理工艺布: 即是所谓的半成品。白布打卷是为后工序印蜡做 ● ●翻退、、准缝煮、、备烧漂 。要求:布要拉直、无纬斜,边、中、前、后
●丝光
退浆●的白同布时松打还卷能紧去除整一部分齐天然要杂质一和其他致杂质,。 布卷要干,落布幅宽尺寸要稳定 在118+0.2mm 冷绳洗:冷绳洗退蜡是机械退蜡。
❖ 工艺流程:轧碱—扩幅—水洗(热水洗、冷水洗) —落布— 烘干—拉幅定型—白布打卷
要求:布要拉直、无纬斜,边、中、前、后松紧整齐要一致,布卷要干,落布幅宽尺寸要稳定在118+0. 丝光后的织物要求钡值(钡值:丝光棉纤维吸附氢氧化钡的百分数。 花布打卷:退蜡以后的棉布门幅不一,或与花网幅宽不符,或出现纬斜情况,均不能直接用于印花。 同时,蜡印辅助工序还包括化蜡、回收、新旧蜡 比例的调和、花网制作等。 显色液处方:GBC、HCL、NaNO 2、 缝头:把每车每匹拉出的布头缝接好,缝头要做到:平、直、劳、齐。
全棉布前处理工艺

第一章前处理未经染整加工的织物统称为原布或坯布,其中仅少量供应市场,绝大多数原布尚需在印染厂进一步加工成漂布、色布或花布供消费者使用。
坯布中常含有相当数量的杂质,其中有棉纤维伴生物及杂质、织造时经纱上浆料、化纤上油剂以及在纺织过程中沾附的油污等。
这些杂质污物如不除去,不但影响织物色泽、手感,而且影响织物吸湿性能,使织物上色不均匀,色泽不鲜艳,还影响染色牢度。
前处理的目的就是在使坯布受损很小的条件下,除去织物上的各类杂质,使坯织物成为洁白、柔软并有良好润湿性能的染印半制品。
前处理是印染加工的准备工序,也称为练漂,对于棉及棉型织物的前处理有准备、烧毛、退浆、煮练、漂白、丝光等工序,但对不同品种的织物,对前处理要求不一致,各地区工厂的生产条件也不相同,因而织物在前处理车间所经受的加工过程次序(工序)和工艺条件也常不同。
第一节前处理用水与主要助剂一、前处理用水(一)水质要求印染厂是用蒸汽、水量较大的企业,而前处理工序用水量在整个印染过程中所占比例又较大,据统计,印染厂每生产1km棉印染织物,耗水量近20t,其中前处理用水约占50%。
水的质量不仅对前处理及其它工序制品质量影响很大,而且还影响到染化料、助剂的消耗。
虽然水质可以通过各种方法加以改善,但由于印染厂用水量很大,无论用哪种方法改善水质,都将占用设备、场地,并且耗用能源、化学药剂,导致成本增加。
因而印染厂应建立在水源充足,水质良好,并有污水排放条件的地点。
印染厂水质质量要求如下:透明度>30色度≤10(铂钴度)pH值6.5~8.5含铁量≤0.1mg/L含锰量≤0.1mg/L总硬度:染液、皂洗用水< 0.36mg当量/L,一般洗涤用水3.6mg当量/L(二)硬水及其软化方法通常将含有钙、镁盐类的水称为硬水(硬水中钙镁盐类含量用硬度表示),钙镁盐类含量低的水称为软水。
天然水的软水、硬水区分标准大致如下:软水 0~57ppm略硬水 57~l00ppm硬水 100~280ppm极硬水〉280ppm硬水中的钙镁盐类对印染加工大都不利,如与肥皂作用生成难溶的钙镁肥皂,沉淀在织物上,在碱性溶液中还会生成难溶的水垢,附着在前处理设备上(如机槽内壁、阀门、导辊),妨碍生产正常进行。
毛巾染整工艺流程

毛巾染整工艺流程一、坯布准备。
咱先得有坯布呀。
这坯布就像是我们的画布,是染整的基础。
坯布从织布机上下来,可能会有些小瑕疵,像小线头、小疙瘩之类的。
这时候就得仔细检查检查,把那些看着不顺眼的东西处理掉。
就好像给小脸蛋儿洗脸,得把脏东西都弄掉,才能进行下一步。
这坯布的质量也很关键哦,如果坯布本身就不好,那后面染整出来的毛巾可能就会有问题。
二、前处理。
1. 烧毛。
烧毛这个环节就像是给毛巾来个小火苗的洗礼。
你想啊,坯布表面有那些小绒毛,就像人脸上的小汗毛一样。
用火焰把这些小绒毛烧掉,毛巾的表面就会变得更光滑。
不过这火候可得掌握好,火大了就把毛巾烧坏啦,那可就成悲剧了。
就像烤棉花糖,火小了烤不熟,火大了就焦了,得刚刚好才行。
2. 退浆。
坯布在织布的时候会上浆,这就像是给布穿了一层硬邦邦的盔甲。
退浆就是把这层盔甲去掉,让布变得柔软。
这退浆的过程就像给紧绷着的肌肉做个按摩,让布放松下来。
要是退浆不彻底,那后面染颜色的时候就不均匀,就像脸上擦粉擦得一块白一块黄的,可难看了。
3. 煮练。
煮练就像是给毛巾来个大温泉浴。
把毛巾放到煮练液里煮一煮,把里面的杂质、油脂什么的都煮出来。
这煮练液就像神奇的温泉水,把毛巾里的脏东西都溶解掉。
煮练完的毛巾就像洗了个超级干净的澡,清清爽爽的。
4. 漂白。
漂白这一步可重要啦。
它能让毛巾变得白白净净的,就像给毛巾打了美白针一样。
不过漂白剂的用量得控制好,用多了会把毛巾弄得太脆弱,就像过度美白会伤害皮肤一样。
漂白后的毛巾就像雪一样白,看着就舒服。
三、染色。
染色就是给毛巾穿上漂亮衣服的时候啦。
可以选择各种各样的颜色,就像给毛巾做时尚造型。
染色的时候要注意染料的选择,就像选衣服要选适合自己的风格一样。
不同的染料染出来的效果不一样,颜色的牢度也不一样。
而且染色的温度、时间也很关键,就像烤蛋糕,时间和温度不对,蛋糕就烤不好。
如果染色的条件没控制好,染出来的颜色可能就会掉色,那毛巾用着用着就变成花脸猫了,多难看呀。
提高纺织品色牢度的措施

提高纺织品色牢度的措施提高纺织品色牢度的主要措施有以下一些:1.前处理工艺(1)烧毛烧毛是烧去织物表面茸毛,以增加织物表而的光洁度和平滑度,减少摩擦系数,提高摩擦色牢度.(2)煮漂煮练要煮透,漂白的白度要达到要求,去除浆料和棉籽壳后,织物的吸水性提高,毛效达到8.lOcm/30s以上,可以提高染色时染料的透染性,匀染性,上染率和固色率,染料浮在织物表面的浮色越少,摩擦色牢度和水洗色牢度越好. (3)丝光丝光使织物表面更加平整,提高织物表面的光泽和滑爽度,提高摩擦色牢度和皂洗色牢度,丝光必须严格控制好碱浓度,光的效果.2.染色工艺(1)染料的选用达到充分丝摩擦色牢度提高0.5~1.0级.它是改进日晒色牢度的主要措施,其要点有:(1)染料的选择染料应选用扩散性好的染料,易扩散到纤维IAJ部,上色率和固色率高,配伍性好,易洗净和浮色少的染料.避免选用直接性高扩散性差的染料,造成表而浮色多,其水解染料不易洗除,使摩擦色牢度和皂洗色牢度下降.(2)染色工艺染色应采用浸染法染色,使织物有充分的时问与染料发生反应,达到染料与纤维充分上染和固着,具有较高的固色率,较好的而耐摩擦色牢度和皂洗色牢度.染色时,温度太高,时间太长,浴比太小及pH值太高,都将导致染料水解,染料浮色增加,导致摩擦色牢度和皂洗色牢度的下降,故而控制染色工艺是必需的.3.后处理(1)水洗皂洗处理处理是将染色后的织物内部和表而浮色染料,残余碱剂和电解质等杂质去除,使染色织物达到最佳麾擦色牢度和皂洗色牢度,日晒色牢度.后处理方法是通过水洗,皂洗和机械外力作用,去除染料浮色,其中皂洗所用助剂必须具有良好的渗透功能,而与染料亲和并形成胶束,降低染料和纤维的亲和力,形成内核为染料的胶束后稳定地分散在水中,可选用具有渗透和分散功能的阴离子型和非离子型表面活性剂复配而成,达不到彻底洗除浮色的效果,洗涤后期和洗后织物的pH 值应接近或保持中性,防止在洗涤过程中或洗后存放时染料发生断键,色牢度下降.后处理过程中的水质硬度高,将使浮色染料的水溶性基团形成难溶于水的色淀,严熏影响浮色染料的去除.(2)后整理在后整理上采用固色剂,以提高印染后的织物色牢度,专用固色剂可使活性染料深浓色渝因染料褪色的过程主要是由于染料的发色基团如偶氨键等发生了光致氧化反应或者光致还原反应,以及这两种反应同时作用所导致的,故要提高染色织物的日晒牢度,染料的选择是关键.应首先选用同晒牢度高的染料,在黄色色谱中,日晒牢度高的黄色染料多为吡唑啉酮和以吡啶酮为偶合组分或以2.氨基.3.6.8.萘三磺酸为熏氨组分的单偶氮染料,由于它们的偶氮基邻位都引入了吸电子基,使偶氮基上氦原子的电子云密度降低,不利于生成氧化偶氮化物,从而阻止或降低光氧化反应的发生,因此这些染料的日晒牢度较好,日晒色牢度都能达到5级以上,如C.I.活性黄2(K型,6.7级)等;蓝色色谱同晒牢度高的染料多以蒽醌型和酞菁型结构,如C.I.活性蓝2(6.7级)等;红色色谱活性染料的同晒牢度普遍较低,特别是浅色,只有一些偶氨基两个相邻位置含有配位能力的羟基与铜形成稳定的螫合环,可以提高日晒牢度,如C.I.活性红23(7级)等.(2)染料昀拼色在染色拼色时,选用日晒牢度水平相当的组分染料.拼色组分中含量相对较少的染料可选择同晒牢度等级较高的染料,从而保证织物色牢度的日晒等级.(3)固色剂固色剂对染料的同晒牢度有着紧密的关系,固色剂大致有三种:阳离子表而活性剂固色剂,非表面活性季铵盐型固色剂和反应性固色剂.大多数阳离子表而活性剂固色剂是季铵盐,锍盐或磷盐.此类固色剂与染料在纤维上生成色淀,虽水洗牢度很好,但往往会降低染料原有的日晒牢度,所以当日晒牢度要求高时,尽量避免选用这类固色剂.非表而活性季铵盐型固色剂,该固色剂既不属于合成树脂,本身又不具有表面活性,一般含有两个或多个季铵基团,此类固色剂和铜盐混合使用也能提高活性染料的日晒牢度,例如固色剂NFC是一种阳离子型多胺缩合体和特殊金属盐的混合物,应用时色变小,不影响染色的色光牢度,并有很好的皂洗牢度.反应型固色剂,活性染料染色以染料一纤维共价键结合,具有优良的湿处理牢度,但部分染料染色后会发生断键,水解,针对这种情况,反应型固色剂既具有与纤维结合的活性基团,又具有能与染料阴离子结合的阳离子基团,具有这种交联作用的固色剂,牢度更好.这类固色剂如LTG-8080,不影响色光,且同晒牢度佳,另外用在真丝织物上的LTF-S6F固色剂,提高皂洗,摩擦等牢度的同时不影响手感,色光和日晒牢度.其它的如上海大祥化学工业有限公司的固色剂3A粉,上海助剂厂的固色剂DS等,这类固色剂使用后,织物的色变小,只晒牢度不下降.。
涤棉混纺织物的前处理工艺

涤棉混纺织物的前处理工艺聚酯纤维与棉纤维的理化性质不相同,在染整加工时,两者应兼顾,纤维混纺比例不同时应有相应的工艺。
由于目前涤棉混纺织物是在棉织物染整工艺基础上进行,工艺流程及设备安装路线也大体相似,因此带来一些不便之处,分述于下。
1.原布准备2.烧毛棉织物前处理工艺是先烧毛后退浆、煮练。
涤/棉织物虽然也将烧毛列在退煮之前,但可能带来不利之点,如聚酯纤维没有来得及烧掉,受高热形成小溶珠散布在织物表面,在用某些分散染料染色时会因此产生色点;涤/棉织物常用PVA 浆料上浆,经烧毛高温作用后退浆时PVA 较难退掉,织物上油污也将会固着,影响织物白度。
但由于坯布烧毛的工序顺当,管理方便,烧毛机的清洁要求不高,除了个别漂白涤/棉品种在练漂后烧毛,及个别深色卡其在染后烧毛外,坯布烧毛仍是切实可行的。
烧毛时布身温度要求低于180℃,温度过高,则布幅收缩过大,手感发硬粗糙,强力下降甚至脆损。
对稀薄、网眼、提花织物更应引起注意。
烧毛设备仍以气体烧毛机为好,用于涤/棉织物的烧毛机火口上方有冷流水辊筒,烧毛时织物在辊筒上包绕,可吸去布身热量,降低布身温度。
火口还可转动,针对不同织物采取不同的火口角度,如切线烧毛、透烧、直烧等。
烧毛后落布时布身温度应在50℃以下,可用冷风或绕经大冷水辊降温或喷雾降温。
干落布应加装静电消除器以免落布上齐,或者织物被卷绕到落布架上。
3.碱缩涤棉的碱缩工艺与纯棉相似区别在于处理条件缓和,由于涤纶的耐碱性较棉差,特别是在高温碱性条件下,涤纶容易发生水解,所以涤棉针织氢氧化钠浓度一般为90-160g/l 需要注意的是严格控制在60—70℃,因为温度较高易造成水解。
• 90—160g/lNaOH •室温浸湿5-20min。
4.退浆涤棉混纺织物多用PVA 及其混合浆料上桨,退浆时可采用碱退浆。
碱退浆工艺用烧碱5~1Og/L,润湿剂适量,80℃轧碱后堆置0.5~1h,热水(80~85℃)冲洗,冷水洗。
棉织物的前处理工艺及设备

棉织物的前处理工艺及设备棉织物前处理须经烧毛、退浆、煮练、漂白、丝光等工序,工艺流程较长,使用的设备也多。
经过这些加工过程,可以除去棉纤维中的天然杂质及纺织过程中带来的浆料污物,获得纯净的棉织物,为后续印、染工序提供合格的半制品。
在棉织物加工中,烧毛与丝光必须以平幅状态进行,其它过程用平幅或绳状均可,但厚织物及涤棉混纺织物仍以平幅加工为宜,以兔生成折皱,影响染色加工。
各工序加工要求及有关设备分述于下。
1.坯布准备与烧毛(1)坯布准备包括坯布检验、翻布(分批、分箱、打印)、缝头。
坯布准备工作在原布间进行,经分箱缝头后的坯布送往烧毛间。
坯布检验率一般在10%左右,也可根据工厂具体条件增减。
检验内容为物理指标和外观疵点,物理指标如匹长、幅宽、重量、经纬纱密度和强度等;外观疵点如缺经、断纬、斑渊、油污、破损等。
经检验查出的疵点可修整者应及时处理。
严重的外观疵点除影响印染产品质量外,还可能引起生产事故,如织入的铜、铁等坚硬物质可能损坏染整设备的轧辊,并由此轧破织物,产生连续性破洞。
对于漂白、染色、印花用坯布,应根据原坯布疵点情况妥善安排。
翻布时将织厂送来的布包(或散布)拆开,人工将每匹布翻平摆在堆布板上,把每匹布的两端拉出以便缝头。
布头上可漏拉,摆布时注意正反面一致,也不能颠倒翻摆。
翻布的同时进行分批、分箱。
此时将加工工艺相同、规格相同的坯布划为一类,每批数量根据设备加工方式而定,如采用煮布锅煮练,则以煮布锅的容布量为一批;采用绳状连续练漂时,则以堆布池容量分批;采用平幅连续练漂时,通常以十箱布为一批。
目前国内印染厂布匹运输仍使用堆布车(布箱),每箱布的多少可根据堆布车容量为准。
由于绳状练漂是双头加工,分箱成双数。
每箱布上附一张分箱卡片,标明批号、箱号、原布品种、日期等,以便管理检查。
每箱布的两头距布头10~20cm 处打上印章,打印油必须具有快干性,并能耐酸、碱、氧化剂及蒸煮。
打印油都用碳黑与红车油自行调制。
- 1、下载文档前请自行甄别文档内容的完整性,平台不提供额外的编辑、内容补充、找答案等附加服务。
- 2、"仅部分预览"的文档,不可在线预览部分如存在完整性等问题,可反馈申请退款(可完整预览的文档不适用该条件!)。
- 3、如文档侵犯您的权益,请联系客服反馈,我们会尽快为您处理(人工客服工作时间:9:00-18:30)。
前处理烧毛工艺一、烧毛机的功用纺织厂织好的织物,在坯布表面和经纬纱之间存在许多绒毛,在印染加工会产生好多问题:1、织物易吸尘沾污,影响光洁和美观。
2、染色时易沾在滚筒上,使色泽不易均匀。
3、绒毛落入染化料溶液或浆液中影响加工质量。
4、织物有绒毛存在,很难印制清晰的花纹,特别是精细的花纹。
5、绦棉混纺织物上存在绒毛,因穿着磨擦易起球等由以上可见,对绦纶、维纶、腈纶等混纺织物,其烧毛更为重要。
二、烧毛机的种类:根据烧毛的方法和采用的热源不同,分类如下:1、热板烧毛机,按热板的形状和性质不同,可分为铜板烧毛机、圆筒烧毛机、电热板烧毛机等。
2、气体烧毛机,按热源的不同,可分为煤气烧毛机、石油气烧毛机等;按火口的排列形式不同,可分为立式烧毛机、卧式气烧毛机等。
三、工艺程序(烘干)——刷毛——烧毛——灭火(可惜无法附图)四、注意事项1)、为提高烧毛效率,织物在烧毛前进行均匀烘干,使含水率在5%以下,但如烘干不匀或烘干效果不好,会影响烧毛效果。
2)、除稀薄和提花织物外,在烧毛前应刷毛。
3)、刷毛辊要定期清洁,防止纱头等缠附表面,影响刷毛效果。
4)、织物入机,应不使左右歪斜、卷边、折皱,防止产生烧毛不匀疵病。
5)、使用气体烧毛机烧毛,应经常检查火焰色泽,遇火焰跳动摇晃或色泽不正常,说明空气和可燃性气体比例不当,应调节两者比例。
6)、经常检查出布质量,主要是织物烧毛效果;也要注意局部或连续性疵病,如烧毛不匀,破洞等。
涤纶混纺布更应注意织物落布温度、手感和布幅收缩情况。
如烧毛过度,一般会发生手感发硬,布幅收缩过大,断裂强度特别是撕破强度显著下降。
五、疵病现象产生原因克服方法一)、烧毛不净1.内焰与布距离过大,铜板或圆筒温度不够解决办法:调节内焰高度或提高铜板、圆筒温度2. 车速过快解决办法:减慢车速3.烘燥、刷毛装置未发挥作用解决办法:清洁毛刷与金刚砂辊,调整与织物的接触面提高烘燥效果(二)、烧毛过度(烧焦,涤纶变硬或熔化,或布幅收缩过多)1. 烧毛时温度过高或织物稀薄,火口多解决办法:调节火焰温度,调整烧毛面次数2.涤纶、维纶混纺布烧毛时,织物温度过高解决办法:加强火口间的吹风冷却3. 车速太慢解决办法:加快车速(三)、烧毛不匀(烧毛条花或左右不匀)1.火口阴塞或变形,铜板、圆筒表面不平解决办法:疏通火口或校正火口隙缝,或刨平火口两侧铁板2. 铜板、圆筒两端温度不一致解决办法:锉平铜板或车平圆筒3. 布折皱解决办法:改进操作调节进布张力导辊,保持吸边器灵活(四)、烧毛破洞或豁边1.拖纱、边纱、棉结等燃烧后及时熄灭解决办法:缩短火口与灭火距离2.火星落在布面上,未及时熄灭解决办法:调换雾化喷头或提高气化温度,汽油气化不良,有油滴喷至布面解决办法:3.车速太慢解决办法:加快车速六、烧毛联合机主要单元机1、刷毛箱2、气体烧毛机3、灭火箱4、轧车退浆简介去除织物上浆料的工艺过程。
棉、粘胶以及合成纤维等织物的经纱,在织造前大都先经过浆纱。
浆料在染整过程中会影响织物的润湿性,并阻碍化学品对纤维接触。
因此织物一般都先经退浆。
棉织物退浆兼有去除纤维中部分杂质的作用;合成纤维织物有时可在精练过程中同时退浆。
•编辑本段退浆方法各类织物退浆的方法随浆纱所用的浆料而不同,常用的有下列四种方法。
•热水退浆法织物浸轧热水后,在退浆池内保温堆置十多小时,使浆料溶胀而易于用水洗去。
这种方法对于用水溶性的海藻酸钠、纤维素衍生物等为浆料的织物,有良好的退浆效果。
对于用淀粉上浆的织物,在25~40 C下堆置较长时间,任其自然发酵、降解,也可获得退浆效果。
.碱液退浆法淀粉在氢氧化钠(烧碱)溶液作用下能发生溶胀,聚丙烯酸聚合物在碱液中较易溶解,可利用精练或丝光过程中的废氢氧化钠溶液作退浆剂,浓度通常为10~20克/升。
织物浸轧碱液后,在60~80 C堆置6~12小时;棉织物还可应用碱、酸退浆,其方法是先经碱液退浆,水洗后再浸轧浓度为4~6克/升的稀硫酸堆置数小时,进一步促使淀粉水解,有洗除棉纤维中无机盐类杂质的作用。
•酶退浆法主要用于分解织物上的淀粉浆料,退浆效率较高。
淀粉酶是一种生物化学催化剂,常用的有胰淀粉酶和细菌淀粉酶。
这两种酶主要组成都是a淀粉酶,能促使淀粉长链分子的甙键断裂,生成糊精和麦芽糖而极易从织物上洗除。
淀粉酶退浆液以近中性为宜,在使用中常加入氯化钠、氯化钙等作为激活剂以提高酶的活力。
织物浸轧淀粉酶液后,在40~50 C堆置1~2小时可使淀粉充分水解。
细菌淀粉酶较胰淀粉酶耐热,因此在织物浸轧酶液以后,也可采用汽蒸3~5分钟的快速工艺,为连续退浆工艺创造条件。
•氧化剂退浆法有多种氧化剂可以适用。
将织物在浓度为3~5克/升的过氧化氢碱性溶液中浸轧,再经汽蒸2~3分钟,可促使淀粉、聚乙烯醇降解,同时对织物有一定的漂白效果。
用亚溴酸钠退浆时,织物以pH为9.5~10.5、有效溴浓度为0.5~1.5 克/升的亚溴酸钠溶液浸轧,在常温下堆置20分钟左右,对羧甲基纤维素、淀粉或聚乙烯醇上浆的织物有良好的退浆效果。
过硫酸铵盐或钾盐也有良好的退浆作用,但易使纤维素纤维脆损。
1、退浆退浆是织物练漂前的重要过程,它不仅可去除织物上的浆料,而且可除去棉纤维上的部份杂质。
退浆应根据织物上浆料组成成分和产品特点选择,以提高退浆效果。
织物经退浆后,一般要求退浆率在80%以上,或织物上残浆量少于1%。
2、煮练煮练能去除棉籽壳和纤维素的共生物及布上残留的浆料,使棉布获得良好的外观和吸水性,以利后加工。
粘纤、富纤布由于纤维在制造过程中已经过烧碱和漂白处理,天然杂质较少,一般在加工时仅需进行退浆、漂白,去除织物上浆料和沾污物,进一步提高白度,不需煮练。
而维纶、涤纶、腈纶本身不需煮练,它们与粘纤、富纤的混纺布或涤腈混纺布也不需煮练,但与棉的混纺布,由于棉纤维含杂多,需煮练。
但维纶在高温浓碱作用下,经过长时间处理要泛黄变硬;涤纶在高温浓碱中纤维表面会发生不同程度浸蚀作用。
经过煮练后棉半制品,毛细管效应要求在8 cm/30min以上。
3、漂白棉布经过煮练后,一般还残留天然色素及部分杂质,影响成品白度和色泽鲜艳度,因此除部分染深色产品外,均需漂白。
漂白既能去除色素,又在不同程度上去除棉籽壳和含氮物质等杂质。
漂白后的半制品白度,一般要求达到85% (以BaSO4 作100%)以上。
、常用工艺方法的品种适应性及优缺点1、常用退浆方法的品种适应性及优缺点1.1酶退浆1.1.1酶退浆用于以淀粉上浆及以淀粉为主与其它浆料混合上浆的各类织物,特别适用于以淀粉为主上浆的粘纤、富纤布以及用于染色苯胺黑棉布的退浆厂1.1.2酶退浆优缺点1.1.2.1去除淀粉浆料效果较佳1.1.2.2. 时间短1.1.2.3. 天然杂质去除较少1.2酶酸退浆1.2.1酶酸退浆用于上浆率较大,退浆要求较高的淀粉上浆及以淀粉为主与其它浆料混合上浆的棉布、粘纤、富纤布等织物退浆1.2.2酶退浆优缺点1.2.2.1去除淀粉浆料较净1.2.2.2.酸退浆时,如工艺条件控制不当,会造成织物损伤1.3碱退浆1.3.1碱退浆碱退浆用于以化学浆料(如PVA等)上浆以及化学浆料为主与其它浆料混用上浆的各类织物,用于以淀粉或淀粉为主、上浆率较低的织物1.3.2碱退浆优缺点1.3.2.1酶酸退浆烧碱可利用煮练或丝光废碱,成本低1.3.2.2.可除去棉纤维上的部份杂质1.3.2.3. 用淀粉上浆织物碱退浆的效果不如酶退浆1.4碱酸退浆1.4.1碱酸退浆用于淀粉及淀粉为主与其它浆料混合上浆的棉布,用于含杂较多的棉布,如低级棉布等;用于对渗透要求较高的紧密织物,如府绸等1.4.2碱酸退浆优缺点1.4.2.1.去除棉纤维杂质及矿物质效率较高,并能提高半制品白度和吸水性1.4.2.2. 半制品周转时间较长]1.4.2.3. 适宜于绳状加工1.5氧化剂退浆________________________________1.5.1氧化剂退浆适用于以PVA以及PVA为主与其它浆料混合上浆的合纤纯纺及混纺织物1.521.退浆迅速且效果好,并有部分漂白作用1.5.2.2. 双氧水-烧碱退浆法对纤维素纤维有部分损伤1.5.23用料多,成本高2.1、煮布锅煮练2.1.1工艺程序:轧碱--进锅--煮练--水洗2.1.2注意事项2.1.2.1轧碱前布含水率力求减少,以免冲淡碱液2.1.2.2煮练用水硬度超过120ppm时,应先用磷酸三钠软化后使用2.1.2.3 ]练液应定量加入,不宜过多,在蒸汽供应不足时更需注意。
2.1.2.4加压煮练起压前,锅内空气必须排尽,以免产生氧化纤维素。
2.1.2.5煮练染色坯布,特别是厚重织物,练后排液不能过急,必要时锅壁宜衬布,以防擦伤织物。
2.1.2.6维纶维的皮层,在加工过程中,容易被摩擦而损伤,所以绳状穿布路线应避免小转弯。
2.2、平幅轧卷汽蒸煮练2.2.1、工艺流程:轧碱--汽蒸打卷--保温汽蒸--退卷--水洗2.2.2注意事项 .2.2.1轧碱宜用多浸多轧,增加碱液渗透,最后一道轧车压力要松,增加织物上带液率, 以利于提高煮练效果,但以控制打卷时无碱液挤出为度J ——2.2.2.2织物上卷和保温过程中,要开启汽蒸箱的直接蒸汽,使箱内温度保持汽蒸温度。
但棉维、涤棉混纺布采用保温法工艺时,可不开蒸汽。
打卷时严防起皱,如造成皱条,后工序很难消除。
2.2.2.4打卷时,布卷要整齐,布卷不齐,易产生边皱或局部风干。
3.1、次氯酸盐漂白:3.1.1、主要包括NaCIO和Ca(CIO)2 (漂白粉),但用漂白粉,织物易产生钙斑疵品,一般都用NaCIO。
具有成本低,操作方便,设备简单特点,但工艺控制应严格。
3.1.2、工艺程序:水洗一一浸轧漂液一一堆置一一水洗一一酸洗一一堆置一-水洗——(脱氯——水洗)3.1.3注意事项3.131、漂白织物丝光后复漂,漂液浓度应较初漂时降低有效氯30-40%。
3.132、常压轧碱汽蒸及低压煮布锅煮练的织物漂白时,漂液浓度应根据煮练效果适当增加。
3.1.3.3、一般织物漂白酸洗后,可不再用大苏打脱氯。
粘维、棉维混纺布由于维纶吸氯后不易洗去,因此漂白后,宜用大苏打脱氯,以防织物带氯烘干造成泛黄现象。
但如酸洗后未洗净,就用大苏打脱氯,则大苏打在酸作用下,析出硫磺,使布带淡黄色,难以洗净,影响产品质量,因此必须充分洗净,或改用亚硫酸钠。
3.1.3.3、次氯酸盐漂白时,漂液PH值如控制不当,结纤维不比纤维损伤较大,以PH为7时最严重,通常情况下,漂液本身PH为11左右,一般漂白时的PH 值可以达到工艺要求。
如煮练后漂白前经过酸洗的织物漂白时,必须把酸洗净,必要时可加烧碱或纯碱调节次氯酸盐供应液的碱度,以免脆损织物。
3.1.3.4、漂液温度的高低对漂白作用有较大影响,温度低,漂白作用缓慢;温度升高,作用加快,超过35度时,作用剧烈,纤维素纤维聚合度显著下降,故夏季宜采用降温或降低漂液有效氯浓度,并控制漂前织物的温度,冬季宜在漂液中用耐腐蚀不锈钢管通蒸汽入漂槽中加温或增加漂液有效氯浓度。