染整工艺与原理重点
染整工艺与原理——前处理
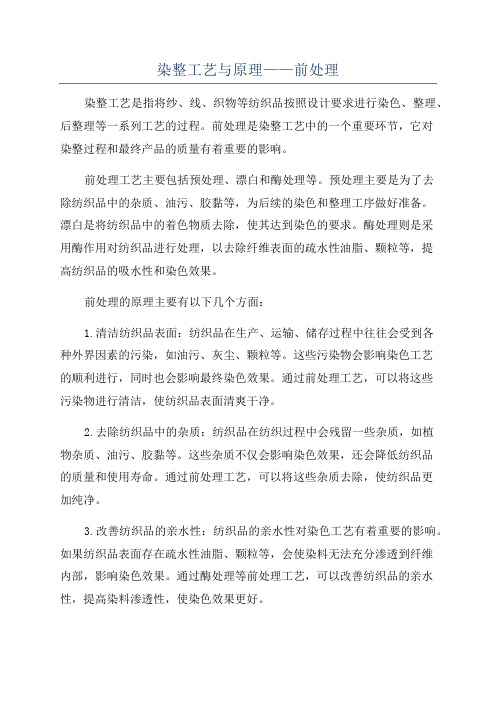
染整工艺与原理——前处理染整工艺是指将纱、线、织物等纺织品按照设计要求进行染色、整理、后整理等一系列工艺的过程。
前处理是染整工艺中的一个重要环节,它对染整过程和最终产品的质量有着重要的影响。
前处理工艺主要包括预处理、漂白和酶处理等。
预处理主要是为了去除纺织品中的杂质、油污、胶黏等,为后续的染色和整理工序做好准备。
漂白是将纺织品中的着色物质去除,使其达到染色的要求。
酶处理则是采用酶作用对纺织品进行处理,以去除纤维表面的疏水性油脂、颗粒等,提高纺织品的吸水性和染色效果。
前处理的原理主要有以下几个方面:1.清洁纺织品表面:纺织品在生产、运输、储存过程中往往会受到各种外界因素的污染,如油污、灰尘、颗粒等。
这些污染物会影响染色工艺的顺利进行,同时也会影响最终染色效果。
通过前处理工艺,可以将这些污染物进行清洁,使纺织品表面清爽干净。
2.去除纺织品中的杂质:纺织品在纺织过程中会残留一些杂质,如植物杂质、油污、胶黏等。
这些杂质不仅会影响染色效果,还会降低纺织品的质量和使用寿命。
通过前处理工艺,可以将这些杂质去除,使纺织品更加纯净。
3.改善纺织品的亲水性:纺织品的亲水性对染色工艺有着重要的影响。
如果纺织品表面存在疏水性油脂、颗粒等,会使染料无法充分渗透到纤维内部,影响染色效果。
通过酶处理等前处理工艺,可以改善纺织品的亲水性,提高染料渗透性,使染色效果更好。
4.去除纺织品中的着色物质:在染色之前,需要将纺织品中的着色物质去除,以达到染色的要求。
漂白是一种常用的去除着色物质的前处理方法。
通过化学物质的作用,将纺织品中的颜色分子氧化或还原,达到去除着色物质的目的。
前处理工艺的质量好坏直接影响到染整工艺的顺利进行和最终产品的质量。
合理选择前处理工艺和方法,严格控制处理参数,是确保染整工艺顺利进行的关键。
同时,还需要根据不同的纺织品材质和要求,合理选择和应用适当的前处理剂,以在最大程度上保证染整工艺的效果和产品的质量。
染整工艺与原理重点
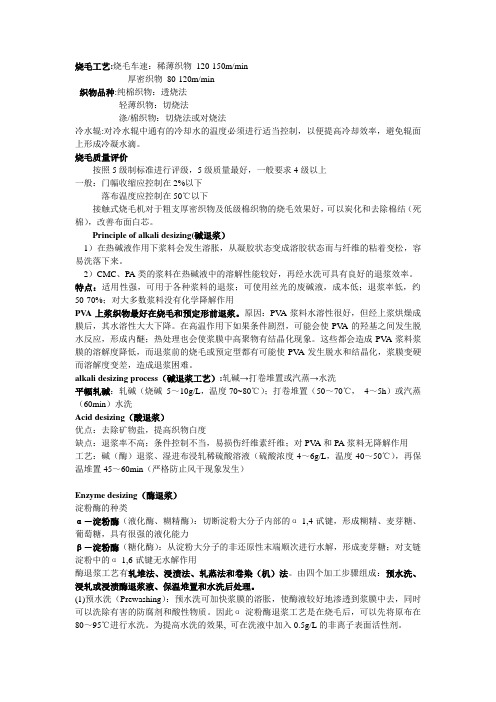
烧毛工艺:烧毛车速:稀薄织物120-150m/min厚密织物80-120m/min织物品种:纯棉织物:透烧法轻薄织物:切烧法涤/棉织物:切烧法或对烧法冷水辊:对冷水辊中通有的冷却水的温度必须进行适当控制,以便提高冷却效率,避免辊面上形成冷凝水滴。
烧毛质量评价按照5级制标准进行评级,5级质量最好,一般要求4级以上一般:门幅收缩应控制在2%以下落布温度应控制在50℃以下接触式烧毛机对于粗支厚密织物及低级棉织物的烧毛效果好,可以炭化和去除棉结(死棉),改善布面白芯。
Principle of alkali desizing(碱退浆)1)在热碱液作用下浆料会发生溶胀,从凝胶状态变成溶胶状态而与纤维的粘着变松,容易洗落下来。
2)CMC、PA类的浆料在热碱液中的溶解性能较好,再经水洗可具有良好的退浆效率。
特点:适用性强,可用于各种浆料的退浆;可使用丝光的废碱液,成本低;退浆率低,约50-70%;对大多数浆料没有化学降解作用PV A上浆织物最好在烧毛和预定形前退浆。
原因:PV A浆料水溶性很好,但经上浆烘燥成膜后,其水溶性大大下降。
在高温作用下如果条件剧烈,可能会使PV A的羟基之间发生脱水反应,形成内醚;热处理也会使浆膜中高聚物有结晶化现象。
这些都会造成PV A浆料浆膜的溶解度降低,而退浆前的烧毛或预定型都有可能使PV A发生脱水和结晶化,浆膜变硬而溶解度变差,造成退浆困难。
alkali desizing process(碱退浆工艺):轧碱→打卷堆置或汽蒸→水洗平幅轧碱:轧碱(烧碱5~10g/L,温度70~80℃);打卷堆置(50~70℃,4~5h)或汽蒸(60min)水洗Acid desizing(酸退浆)优点:去除矿物盐,提高织物白度缺点:退浆率不高;条件控制不当,易损伤纤维素纤维;对PV A和PA浆料无降解作用工艺:碱(酶)退浆、湿进布浸轧稀硫酸溶液(硫酸浓度4~6g/L,温度40~50℃),再保温堆置45~60min(严格防止风干现象发生)Enzyme desizing(酶退浆)淀粉酶的种类α-淀粉酶(液化酶、糊精酶):切断淀粉大分子内部的α-1,4-甙键,形成糊精、麦芽糖、葡萄糖,具有很强的液化能力β-淀粉酶(糖化酶):从淀粉大分子的非还原性末端顺次进行水解,形成麦芽糖;对支链淀粉中的α-1,6-甙键无水解作用酶退浆工艺有轧堆法、浸渍法、轧蒸法和卷染(机)法。
染整工艺与原理赵涛

染整工艺与原理赵涛染整工艺是指对纺织品进行染色和整理处理的一系列工艺流程。
染整工艺主要包括染料选择、配方设计、浸染、固色、洗净、整理等环节。
以下是对染整工艺原理的详细阐述:1. 染料选择:染料是染整工艺的核心,其选择应根据纺织品材质、色彩效果要求、成本等因素进行考虑。
染料可以分为直接染料、酸性染料、还原性染料、活性染料、分散染料等多种类型,每种染料都有不同的适用范围和染色效果。
2. 配方设计:染料的选择和配方的设计是染整工艺中的关键环节。
配方设计需要考虑染色效果、染色工艺参数、纺织品材质等因素。
其中,染色效果包括色相、明度、饱和度等,染色工艺参数包括浸染时间、浓度、温度等。
配方设计要通过试验和经验总结,找到最佳的染色工艺。
3. 浸染:浸染是将染料和纺织品进行接触和相互渗透的过程。
浸染一般采用浴比、液浴比和浸渍时间等参数来控制。
浸染时间越长,染色越均匀,但浸染速度较慢;浸染液的浓度越高,染色越重,但易产生局部浓染和渗透不均匀现象。
4. 固色:固色是使染料与纺织品发生化学反应,使染料牢固结合于纤维上的过程。
固色一般采用温度、时间和pH值等工艺参数进行控制。
不同类型的染料需要不同的固色剂,例如,还原性染料需要使用还原剂进行固色。
5. 洗净:洗净是去除纺织品上的游离染料和杂质的过程。
洗净过程包括清水漂洗、酸洗、碱洗、漂白等环节。
洗净的目的是提高染色的牢度,减少染后分离和脱色现象。
6. 整理:整理是对染色后的纺织品进行加工,使其具有所需的手感和外观效果。
整理可以包括压光、软光、丝光、罗纹、绒毛等各种加工处理。
整理的目的是优化纺织品的表现效果,提高产品附加值。
染整工艺的原理是基于染料与纤维之间的物理和化学相互作用。
在染色过程中,染料分子穿透纤维结构并与纤维分子发生相互吸附或相互作用,从而实现染色目的。
不同类型的染料与纤维之间的作用机制有所不同,例如,直接染料通过离子键与纤维结合;酸性染料通过酸碱反应与纤维结合;活性染料通过共价键与纤维结合。
染整工艺与原理第1章复21

第一章----水和表面活性剂
1、什么叫硬度和碱度?并简述硬水对染整加工有何影响?
2、什么叫ppm?根据其值的大小怎样来划分水的级别?
3、何为化化法?试说明工厂常用的三种软化剂的软化原理及特点。
4、什么叫S.A.A?并简述其结构特征及溶液性质。
5、说明一般情况下雨水、地表水、浅地下水和深地下水中杂质的组成及其来源。
6、为什么通常见到的液滴都是类似球状的?粉状固体(如面粉)长期储存为什么会有结块现象?
7、如果进行下列
①在肥皂稀水溶液的表面用刀片飞快地刮下一薄层溶液;
②在上述肥皂溶液中通入空气后形成泡沫;
③将上述薄层溶液收集,并将泡沫收集待其破裂后形成另一溶液。
对上述两溶液进行浓度测试,所测得的浓度值与肥皂溶液本体浓度之间应当有什么不同?说明不同的原因。
8、在实际测定液体在固体表面上的接触角时为什么要确保固体表面的洁净?
9、采用一些特殊手段在纤维(如聚醋纤维)表面形成微小的刻蚀后为什么可以提高水对该纤维的润湿性能?
10、以油/水型乳状液体系为例,论述混合表面活性剂的应用对体系稳定性的作用及影响。
染整工艺与原理

染整工艺与原理染整工艺是指将纺织品通过染色、印花等工艺,使其获得所需颜色和图案的过程。
而染整工艺的原理则是指在染色和印花过程中所运用的化学、物理原理,以及工艺技术。
下面将就染整工艺与原理进行详细介绍。
首先,染色工艺是指将染料溶液渗透到纤维内部,使其获得所需颜色的过程。
染料分子通过与纤维分子之间的作用力,将染料固定在纤维上,从而实现染色。
在染色工艺中,染料的选择、染色剂的使用、染色条件的控制等都是非常重要的。
染料的选择需要考虑其与纤维的亲和力,染色剂的使用需要考虑其对环境的影响,染色条件的控制需要考虑温度、时间、pH值等因素的影响。
其次,印花工艺是指将染料或浆料通过模板印刷到纺织品上,形成所需图案的过程。
印花工艺的原理是利用染料或浆料与纤维之间的化学或物理作用力,将染料或浆料固定在纤维上,从而实现印花。
在印花工艺中,模板的设计、染料或浆料的选择、印花条件的控制等都是非常重要的。
模板的设计需要考虑图案的复杂度和精细度,染料或浆料的选择需要考虑其对纤维的亲和力,印花条件的控制需要考虑温度、压力、速度等因素的影响。
除了染色和印花工艺,染整工艺还包括漂洗、定型、整理等环节。
漂洗是指将染色或印花后的纺织品进行清洗,去除多余的染料或浆料,使其获得所需的颜色和图案。
定型是指将染色或印花后的纺织品进行加热或加压处理,使染料或浆料固定在纤维上,增强其耐洗、耐摩擦等性能。
整理是指将染色或印花后的纺织品进行整理,使其获得所需的手感和外观。
总之,染整工艺的原理是在染色和印花过程中运用化学、物理原理,以及工艺技术,使纺织品获得所需的颜色和图案。
染整工艺的发展离不开对化学、物理原理的深入研究,以及对工艺技术的不断创新。
希望本文的介绍能够为染整工艺的学习和研究提供一定的帮助。
染整工艺原理重点

染整工艺原理纺织基础知识纺织基础知识染整工艺原理绪言第一章染整用水及表面活性剂第二章棉及棉型织物的退浆和精第三章蚕丝和真丝绸的精练第四章漂白(Bleaching)第五章丝光第六章热定形(Heat Setting)第七章毛织物的湿整理第八章一般整理(Finshing)第九章防缩整理Finishing)第十章防皱整理(Resin Finishing)第十一章特种整理一、纺织加工以后的加工工艺。
它是织物在一定的工艺条件下,通过染料、药剂和助剂在专用设备上进行的化学和物理加工过程。
1.特点(1)属加工工业(在纺织工业中担任承上启下的重要角色);(2)一种化妆术;(3)综合的工艺技术,涉及面广;(4)能耗大(水、热、电),有污染(废水、气、渣)需重视节能和环保。
2.目的改善织物的服用性能(舒适、保暖、抗皱等),赋予功能性(防霉、防蛀、拒水、阻燃、抗菌等),提高身价。
(1)去除杂质;(2)提高白度;(3)染着颜色;(4)改善风格。
二、染整加工的主要内容: 漂、染、印、整。
三、本课程的任务和要求1.掌握纺织品的练漂、整理加工的基本原理和方法。
2.能根据纺织品的特性和练漂、整理加工要求,合理制订加工工艺过程及条件;初步具备解决练漂及整理工艺问题的能力。
3.了解练漂、整理加工的质量检验方法。
4.了解练漂及整理加工技术进展和发展前沿。
5.查阅染整专业的有关文献。
第二章棉及棉型织物的退浆和精练一、练漂的目的1.去除杂质,使染整加工顺利进行。
杂质:①天然杂质:棉上的蜡状物,含氮物,果胶等②加工时沾上的二次杂质:整经用浆,合纤纺纱上油,尘埃,锈迹等 2.改善品质,提高服用性能,如丝光,热定形,多在染前进行,也归为练漂。
二、主要工序因品种而异(棉):原布准备→烧毛→退浆→精练→漂白(深色布可免,漂布须复漂)→开轧烘→丝光→烘干→染色(印花)(涤/棉):准备→烧毛→退浆→精练(亚漂可免)→热定形(兼漂布涤加白)→丝光→氧漂(兼漂布棉加白)→烘干三、加工形式①烧毛、丝光、热定形、烘干以平幅进行。
染整工艺原理后整理
染整工艺原理后整理染整工艺是指对纺织品进行染色和整理加工的方法和过程。
染整工艺的原理主要包括染色原理和整理原理,下面对其进行详细介绍。
一、染色原理:染色是指将染料溶解在一个溶液中,使染料分子进入纤维内部或与纤维表面发生反应,从而在纤维上形成一层彩色薄膜或彩色纤维的过程。
1.染料的选择:染料是染色的核心材料,其选择需要考虑颜色的稳定性、亮度、鲜艳度等因素。
常见的染料有酸性染料、阳离子染料、活性染料等。
2.染料的吸附和扩散:染料在纤维上的吸附和扩散是染色的关键步骤。
纤维内部的吸附表现为分子间的物质转移,这要求染料分子要小且易溶于纤维内部;纤维表面的吸附需要染料与纤维表面发生化学反应,如酸性染料与羟基纤维表面形成氢键,阳离子染料与阴离子纤维表面形成离子键。
3.温度和浸泡时间:温度和浸泡时间对染色的效果有重要影响。
提高温度可增加染料分子的动力学能量,加快扩散速率;延长浸泡时间则有助于染料分子均匀地吸附到纤维上。
4.盐的作用:染色过程中加入盐可提高染料的吸附率和色牢度。
这是因为盐能增加纤维表面的离子浓度,促进染料与纤维表面的离子反应,从而加强染料的固着力。
二、整理原理:整理是指对染色后的纺织品进行物理或化学处理,使其具有良好的外观、手感和性能。
整理过程中可以采用物理力学、化学处理、聚合技术等方法。
1.物理处理:物理处理是指通过拉伸、压缩、压光等手段改变纤维的结构和形态,改变纺织品的手感和外观。
例如,通过水洗、拉直、烘干等处理,可以使纺织品获得柔软、平整的效果。
2.化学处理:化学处理是指通过化学药剂作用改变纤维或织物表面的性质。
例如,通过应用涂覆剂、膨润土和硅油等处理,可以提高纺织品的防水性、防尘性和耐洗性。
3.聚合技术:聚合技术是指通过聚合物的形成或加入增韧剂等手段改变纤维的性能。
例如,通过在纺织品中加入增韧剂,可以增强纤维的拉伸强度和耐磨性。
4.效果检测:整理后的纺织品需要进行效果检测,以确保染色和整理效果符合要求。
染整工艺与原理
染整工艺与原理涂装工艺:1. 制备:(1)表面处理:进行除锈、打磨、抛光、刻纹等表面处理,确保待涂装表面清洁,光滑,无污垢和灰尘,并吸收一部分底漆,准备好涂装的基面。
(2)喷溶剂:利用喷枪分散轻质溶剂,使其逆流覆盖全表面。
2. 底漆涂装:(1)施工环境控制:室内温度控制在20~25℃之间,湿度控制在30%~60%范围内,避免有油渍、灰尘及大量积水。
(2)施工准备:分漆桶内的涂料搅拌均匀,粗梳筛通后,倒入涂料杯内。
2. 中涂装:(1)施工前的准备:中涂面层的着色以及固化剂的添加工作,混合均匀后将涂料放入涂料杯内,再次搅拌均匀,并经梳筛通道筛网。
(2)喷枪调整:各调节开关改为实际用料相应状态,并调整喷嘴直径与施工压力,最后做好喷枪压力与噪声试验,保证效果达到要求。
3. 面漆涂装:(1)施工前准备:搅拌均匀涂料,检查面漆涂装效果,经梳筛通道筛网,保证涂料细腻不凝块。
(2)喷枪调整:确定喷枪和涂料的压力,调整喷枪的噪音、速度和喷头的大小,可保证良好的喷涂效果。
4. 固化:(1)烘烤:添加固化剂的涂件,进行人工烘烤,以提高涂件固化效果。
(2)自然固化:不加固化剂的涂件,可而采用自然固化的方法,让涂件自行固化。
5. 检查:(1)瞬时笺检查:观察涂装平整度、固定性以及釉色深浅和色调均匀性。
(2)持久笺检查:检查涂件的耐用性、耐磨性、耐腐蚀等抗性。
涂装工艺原理:1. 涂料喷射原理:涂料喷射原理是利用压缩空气将油漆或者其他涂料喷射到物体表面,形成坚固保护膜。
2. 溶剂清洗原理:涂装前,通过溶剂清洗原理,使涂装表面彻底清洁,清除表面污垢、抹平表面瑕疵对表面流平性进行修整。
3. 压力控制原理:控制压力,控制涂料,使涂料均匀、分散,避免涂层太厚或太薄,提高涂层的效果。
4. 温度控制原理:控制施工环境的温度和湿度,以保证涂料的正常使用和固化过程。
5.烘烤原理:通过控制烘烤炉温度和湿度,来改变基体物质的形态和物性,使其产生反应、形成合金或固化反应来达到涂料固化的效果。
染整实验考试重点(上) 染整工艺原理
染整实验考试重点(上)染整工艺原理染整实验考试重点(上)染整工艺原理1.棉的阻燃机理:隔绝氧气;分解不可燃气体;吸热反应;改变纤维素纤维分解途径,减太少可燃性气体。
除了横向冷却法,除了那些织物阻燃性能够测试方法?(1)氧指数法,它是指在规定的实验条件下,在氧气、氮气混合气体中,材料刚好能保持冷却状态所须要最高氧浓度,用loi则表示,loi=vo2/(vo2+vn2)*100%(2)45度倾斜燃烧法:采用微型燃烧器,燃烧时火焰高度调节到4.5cm,燃烧起边缘至电极距离0.3cm,冷却时间为1min,操作步骤与横向冷却法相同,根据余燃、阴燃性能好坏。
(3)水平燃烧法:对水平放置的试样点火,测定火焰在试样上的蔓延距离及时间,用燃火烧速度去表观织物阻燃性。
2.横向冷却法和氧指数法这两种测试方法与织物的实际应用领域存有什么关系?分别适用于于什么用途材料的阻燃性能测测试?垂直燃烧法测试较适用于开放空间使用的材料阻燃性能测试。
氧指数法测试较适用于在封闭空间中使用的材料阻燃性能测试。
3.拒水整理剂:减少临界表面张力,构成欲水性薄层,风道与织物接触角减小,较太少水对纤维的粘附能力。
涂层加工:表面均匀地敷一层或多层高分子成膜材料,抗风防水。
4.常用的拒水剂有哪几类?比较分析它们拒水的优缺点。
石蜡-铝皂(棉麻织物)拒水效果较好,不耐水洗或工业用,也不耐摩擦。
吡啶季铵盐(棉织物)拒水性较为耐久,织物上会残留吡啶、甲醛等物质。
羟甲基三聚氰胺衍生物(纤维素纤维织物)良好且较耐洗。
硬脂酸铬络合物(深色织物)良好且耐洗。
常用的涂层剂:共聚丙烯酸酯(pa)类、聚氨酯(pu)类、聚氯乙烯(pvc)5.棉织物丝光是指棉织物在施加一定张力状态下,用浓naoh溶液处理的加工过程。
棉织物在丝光过程中,纤维在浓碱促进作用下能出现不可逆热裂,纤维分子链段出现重排,晶型转型,结晶度上升。
处置后织物表明出来更好的性能,例如尺寸稳定性提升,溶解染化料能力减小布面光泽念提升,强力减少的。
染整工艺与原理一
●1-1.织物的前处理目的是什么?棉织物前处理有哪些工序?答:前处理可以除去织物上面的杂质,从而改善白度、光泽、手感及吸水性,有利于后续加工。
棉织物的前处理:烧毛→退浆→精炼→漂白→丝光●1-2.烧毛机有哪些类型?答:气体烧毛机、圆筒烧毛机、铜板烧毛机●1-3.请说出常用浆料有哪几种,它们的主要性质,可以用什么方法退浆?答:(1)淀粉:难溶于水,对碱稳定,对酸不稳定会水解,可以被淀粉酶催化水解,可以被氧化剂氧化降解,遇碘变蓝紫色;碱退浆,酸退浆,氧化剂退浆,酶退浆。
(2)PVA:水溶性较好,酸、碱不会使它降解但会膨化,能被氧化剂降解,高温下羟基间脱水交联水溶性下降,难以生物降解;碱退浆,氧化剂退浆(3)变性淀粉:改善水溶性,降低粘度,提高使用浓度,提高热粘度稳定性,提高对合纤的粘着性;酸退浆,碱退浆,酶退浆,氧化剂退浆。
(4)CMC:水溶性好,pH=2.5时沉淀,不耐硬水,重金属离子沉淀;碱退浆,热水退浆。
(5)PA:有一定水溶性,在酸碱条件下水溶性进一步提高;碱退浆,氧化剂退浆。
●1-4.BF7658淀粉酶的性质。
答:(1)工作温度为50-80℃,过高过低都会降低效率甚至失活;(2)pH=6左右活性最该,pH﹤5或pH﹥7活性急剧下降;(3)pH=6-9稳定性好,pH﹤6或pH﹥9稳定性急剧下降;(4)含Cl碱金属盐对其有活化作用;(5)重金属离子、离子型表面活性剂对其有阻化作用。
●1-5.棉织物精炼中,天然杂志是如何被除去的?答:(1)果胶类物质:主要以果胶酸、果胶酸甲酯及果胶酸与纤维素上的-COOH以脂键结合;热碱溶液一方面可以使果胶类物质转化为果胶酸钠盐→水溶性↑,另一方面可以降解果胶类物质→聚合度↓→水溶性↑;(2)含氮物质:大部分以蛋白质形式存在,也有以有机物及无机氮化合物形式存在;20%含氮物质可溶于水,蛋白质在热碱溶液中发生肽键水解→聚合度↓→水溶性↑;(3)灰分:主要以碳酸、硅酸、盐酸的钙、镁、钾、钠盐及其金属氧化物形式存在;大部分可以在退浆、精炼、水洗中除去;(4)油蜡物质:主要以高级一元醇、脂肪酸及其酯、液体或固体碳氢化合物形式存在;脂肪酸及其酯可以在热碱溶液中被皂化→水溶性↑,其它油蜡在表面活性剂作用下被乳化、增溶→水溶性↑;(5)棉籽壳:主要成分为木质素,还有纤维素、单宁、蛋白质、油蜡;热碱溶液可以使木质素转化为钠盐→水溶性↑,也可以降解木质素→聚合度↓→水溶性↑。
- 1、下载文档前请自行甄别文档内容的完整性,平台不提供额外的编辑、内容补充、找答案等附加服务。
- 2、"仅部分预览"的文档,不可在线预览部分如存在完整性等问题,可反馈申请退款(可完整预览的文档不适用该条件!)。
- 3、如文档侵犯您的权益,请联系客服反馈,我们会尽快为您处理(人工客服工作时间:9:00-18:30)。
烧毛工艺:烧毛车速:稀薄织物120-150m/min厚密织物80-120m/min织物品种:纯棉织物:透烧法轻薄织物:切烧法涤/棉织物:切烧法或对烧法冷水辊:对冷水辊中通有的冷却水的温度必须进行适当控制,以便提高冷却效率,避免辊面上形成冷凝水滴。
烧毛质量评价按照5级制标准进行评级,5级质量最好,一般要求4级以上一般:门幅收缩应控制在2%以下落布温度应控制在50℃以下接触式烧毛机对于粗支厚密织物及低级棉织物的烧毛效果好,可以炭化和去除棉结(死棉),改善布面白芯。
Principle of alkali desizing(碱退浆)1)在热碱液作用下浆料会发生溶胀,从凝胶状态变成溶胶状态而与纤维的粘着变松,容易洗落下来。
2)CMC、PA类的浆料在热碱液中的溶解性能较好,再经水洗可具有良好的退浆效率。
特点:适用性强,可用于各种浆料的退浆;可使用丝光的废碱液,成本低;退浆率低,约50-70%;对大多数浆料没有化学降解作用PV A上浆织物最好在烧毛和预定形前退浆。
原因:PV A浆料水溶性很好,但经上浆烘燥成膜后,其水溶性大大下降。
在高温作用下如果条件剧烈,可能会使PV A的羟基之间发生脱水反应,形成内醚;热处理也会使浆膜中高聚物有结晶化现象。
这些都会造成PV A浆料浆膜的溶解度降低,而退浆前的烧毛或预定型都有可能使PV A发生脱水和结晶化,浆膜变硬而溶解度变差,造成退浆困难。
alkali desizing process(碱退浆工艺):轧碱→打卷堆置或汽蒸→水洗平幅轧碱:轧碱(烧碱5~10g/L,温度70~80℃);打卷堆置(50~70℃,4~5h)或汽蒸(60min)水洗Acid desizing(酸退浆)优点:去除矿物盐,提高织物白度缺点:退浆率不高;条件控制不当,易损伤纤维素纤维;对PV A和PA浆料无降解作用工艺:碱(酶)退浆、湿进布浸轧稀硫酸溶液(硫酸浓度4~6g/L,温度40~50℃),再保温堆置45~60min(严格防止风干现象发生)Enzyme desizing(酶退浆)淀粉酶的种类α-淀粉酶(液化酶、糊精酶):切断淀粉大分子内部的α-1,4-甙键,形成糊精、麦芽糖、葡萄糖,具有很强的液化能力β-淀粉酶(糖化酶):从淀粉大分子的非还原性末端顺次进行水解,形成麦芽糖;对支链淀粉中的α-1,6-甙键无水解作用酶退浆工艺有轧堆法、浸渍法、轧蒸法和卷染(机)法。
由四个加工步骤组成:预水洗、浸轧或浸渍酶退浆液、保温堆置和水洗后处理。
(1)预水洗(Prewashing):预水洗可加快浆膜的溶胀,使酶液较好地渗透到浆膜中去,同时可以洗除有害的防腐剂和酸性物质。
因此α-淀粉酶退浆工艺是在烧毛后,可以先将原布在80~95℃进行水洗。
为提高水洗的效果, 可在洗液中加入0.5g/L的非离子表面活性剂。
(2)浸轧或浸渍酶退浆液(Impregnation withenzymes):经过预水洗的原布,要尽量去除水分,在70~85℃的温度和微酸性至中性(pH=5.5~7.5)的条件下浸轧、浸渍或喷淋酶溶液。
织物的带液率控制在100%左右,并加入适量的金属离子(钙离子或钠离子)如氯化钙,对酶起活化作用。
(3)保温堆置:保温堆置可以使酶对淀粉进行充分的水解,使浆料易于洗除。
织物在40~50℃堆置需要2~4h,而直接在100~115℃下汽蒸只需要15~120s(高温型酶)。
(4)水洗后处理(After-wash)酶使用条件:兼顾酶的活性、活性稳定性活化剂的作用是提高酶的活性, 阻化剂的作用是降低酶的活性。
Ca2+是活化剂,它对细菌淀粉酶和胰酶有活化作用,可加氯化钙来提高酶的活性,或在退浆时不用软水。
离子型表面活性剂对α-淀粉酶的活性有抑制作用,所以退浆时要用非离子型的表面活性剂作渗透剂或润湿剂。
另外一些重金属离子如铜、铁的盐类,对淀粉酶的活性有阻化作用,使活性减弱,甚至完全丧失。
此外,氧化还原漂白剂都是对酶的有害物质,不宜同浴使用。
Oxidizing agent desizing 氧化剂退浆氧化剂退浆可用于任何天然或合成浆料的退浆氧化型退浆剂主要有过氧化氢、过硫酸盐(过硫酸钠、过硫酸铵和过硫酸钾)和亚溴酸钠。
机理:在碱性条件下,氧化剂可与淀粉和其它天然浆料如羧甲基纤维素中的α-1,4-甙键和α-1,6-甙键反应,使甙键断裂水解,从而发生葡萄糖环的开环、分裂,最终生成二氧化碳和水。
注意事项:在退浆的同时,纤维素纤维也会被氧化,因此退浆的工艺条件须严格控制,以免损伤纤维。
退浆效果的评定:退浆率Scouring (boiling-out)(精炼)目的:经过退浆处理后,棉织物上的大部分浆料、油剂以及小部分的天然杂质被去除,但是大部分天然杂质的存在和浆料、油剂的残留,使织物色泽发黄,吸水性很差,因此必须还要进行精练加工(煮练),使织物获得良好的吸水性和较洁净的外观,以利于后续加工。
精练原理1、煮练中杂质的去除原理在煮练剂烧碱及煮练助剂的作用下,杂质通过溶解、降解、乳化等作用,部分直接溶解在煮练液中,部分由于溶胀和纤维的结合力变小通过水洗从织物上脱落下来,部分通过表面活性剂的乳化作用从织物上剥离下来。
2、煮练液的组成及各组分的主要作用1)烧碱(NaOH)煮练剂a)果胶→果胶酸→果胶酸钠盐b)脂肪酸→脂肪酸钠盐c)含氮物质(蛋白质)→分解d)棉籽壳→溶胀→脱落e)灰分(无机盐)→钠盐而溶解2)表面活性剂(S.A.A)如肥皂、红油等煮练助剂a)起润湿作用,有利于煮练剂等迅速进入纤维内;b)通过乳化作用去除油蜡;3)硅酸钠(NaSiO3)a)吸附煮练液中的铁质,防止织物上产生锈斑;b)吸附煮练液中已分解的杂质,防止再次污染;4)亚硫酸氢钠(NaHSO3)a)有利于棉籽壳的去除;木质素→木质素磺酸→木质素磺酸钠b)还原剂,防止棉织物在高温带碱情况下被空气氧化而脆损;5)磷酸三钠(Na3PO4):作为软水剂与碱精练相比,酶精练用水少,处理液中的污染物少;但精练效果如吸水性略差一些,特别是对棉籽壳的去除效果差酶精练原理:果胶酶先与果胶形成一个复合物,然后,又与这个复合物继续反应,使其变成水溶性产物从纤维上溶解下来。
纤维表面层的果胶和蜡状物质是相互附生的,果胶具有将蜡状物质粘附在纤维中的功能。
随着果胶从纤维表面的角皮层和初生胞壁中溶解下来,残留的蜡状物质结构发生松动,很容易与表面活性剂接触而被乳化去除。
酶的精练方式:间歇式、半连续式和连续式果胶酶多为中温型的酶,处理温度在40~65℃之间,最适宜pH值在弱酸性范围4~6.5之间,碱性果胶酶的最适宜pH值在9~10之间煮练效果的评定:毛效毛效:煮练效果的评定一般用毛效指标来判定。
即30分钟内水沿织物向上爬升的高度(CM)。
棉机织物要求毛效在8CM以上;棉针织物要求毛效在12CM以上;第三章漂白的目的是去除天然色素,赋予棉布以必要的白度,同时棉布上残留的其它杂质也可以进一步被去除,使棉布的润湿性能有所提高。
漂白加工的主要对象是棉及棉型织物,合成纤维不含色素,一般不进行漂白,羊毛织物和蚕丝织物,除了漂白产品外,通常也不需要进行专门的漂白处理利用过氧化氢酶能在很短的时间内迅速将H2O2分解成水和氧气,可在漂白完成后的水洗工艺中加入过氧化氢酶,以减少水洗次数、缩短水洗时间和降低洗涤温度。
H2O2漂白原理H2O2 + OH- →HO2- + H2O当pH≥11.5时,过氧化氢的分子大部分以HO2- (过羟基离子)存在。
HO2-可能与色素中的双键发生加成反应,使色素中原有的共轭系统被中断,π电子的移动范围变小,天然色素的发色体系遭到破坏而消色,达到漂白目的。
HO2-不稳定,按下式分解成氢氧根离子和初生态氧:HO2- →OH- + [O]生成的“活性氧”与色素发色团的双键发生反应,产生消色作用:所以HO2- (过羟基离子)是进行漂白的主要成分。
此外,HO2-引发H2O2分解生成的HO2·、HO·等游离基也可以破坏色素的结构而具有漂白作用。
重金属离子能迅速将H2O2分解产生O2, 一方面使H2O2失去漂白作用,增加H2O2消耗;另一方面如果O2渗透到织物内部,在高温强碱条件下,将使纤维素发生严重降解。
因此,铜、铁屑等的存在可能使棉布产生破洞。
在漂液中要加入一定量的稳定剂,稳定剂的作用是阻止重金属离子对H2O2的催化分解,在总的漂白时间内保持较高的氧化能力而进行有效的漂白,不致浪费有效成分和过度损伤纤维。
通常棉纤维漂白常用硅酸钠和其它非硅酸盐稳定剂如无机磷酸盐、有机螯合剂、蛋白质降解产物和有机多元膦酸盐等;对于羊毛等蛋白质纤维,可选用焦磷酸钠做稳定剂。
漂白方式:浸漂淋漂轧卷漂轧蒸漂浸漂淋漂属于间歇式和绳状加工;轧卷漂属于半连续式平幅加工;轧蒸漂是连续加工连续汽蒸漂白法工艺流程:浸轧漂液→汽蒸→水洗工艺处方:双氧水(100%)2~3g/L;硅酸钠4~7g/L烧碱(100%)1~2g/L;润湿剂2~4g/L工艺条件:漂液PH值:10.5~11浸轧温度:室温轧余率:110~130%(绳状)80~90%(平幅)汽蒸温度:95~100℃;汽蒸时间:45~60min轧余率:织物上带的液体重量与织物本身重量的百分比。
准确的说法是经过浆槽带上溶液后,经过轧棍轧过后布面上带的溶液重量和浸轧前原来织物重量的百分比。
综合H2O2漂液pH值对织物白度、纤维强度、纤维聚合度以及H2O2漂液分解率的影响,过氧化氢pH值控制在9~10比较合适。
如果加入稳定剂,漂液的pH值可以适当提高一些,以提高漂白速度。
一般棉布漂白pH 值控制在10~11之间。
为了提高漂白速度,可以采取在高温条件下进行漂白,一般在90~100℃之间进行。
在生产中,若采用冷轧堆漂白工艺,则在20~30℃的温度范围内应堆置在10h以上,一般为16h~24h。
若采用汽蒸工艺,漂白时间只需1h,若人为的再延长时间,反而会使白度下降。
因为棉纤维在高温碱性条件下长时间停留会逐渐泛黄。
一般情况下,双氧水的浓度应为2~6g/L(双氧水以100%计)。
稳定剂的作用主要是阻止催化剂(金属离子)的催化作用,减少双氧水的无效分解,充分利用双氧水,并尽可能减少对纤维的损伤组分Na2O和SiO2有不同的分子比,漂白用1:3.3硅酸钠作用原理:可吸附重金属离子和杂质,使催化剂被屏蔽而失去活性硅酸钠与双氧水用量之比为2∶1pH=10~11由氢氧化钠提供和硅酸钠水解优点:稳定性好,白度佳,使用方便,价格便宜,可调节溶液的PH值缺点:产生污垢,粘附设备,清洁困难;影响手感在使用过程中,硅酸盐会沉积在纤维和设备上,导致织物手感发硬、造成染色和印花的病疵以及设备必须定期清洗等问题。
为避免上述问题的发生,可采用非硅稳定剂。
非硅类稳定剂:稳定作用机理主要是吸附作用和与重金属离子的络合作用,使重金属离子失去催化双氧水的活性Bleaching with sodium hypochlorite(次氯酸钠漂白)次氯酸钠漂白作用比较复杂,笼统地说,HOCl和Cl2是漂白的有效成分,在不同条件下,有效成分细分为:碱性条件下:主要是NaClO 中性条件下:NaClO+HClO弱酸性条件下:主要是HClO 溶液PH<4时:HClO + Cl2次氯酸钠漂白方式及工艺工艺流程:水洗→轧漂→堆置→水洗→酸洗→堆置→水洗→脱氯→水洗工艺条件:次氯酸钠浓度(有效率,g/L):1~2PH:9.5~10.5温度:(℃):20~30时间(min):20~45硫酸浓度(g/L):1~3酸洗时间(min):10~15酸洗温度(℃):小于50碳酸钠浓度(g/L):3~5综合考虑漂液pH值对漂白效果和纤维强力的影响,控制:漂液pH=10左右。