高炉配料计算表(可以计算开炉料)
高炉开炉配料计算
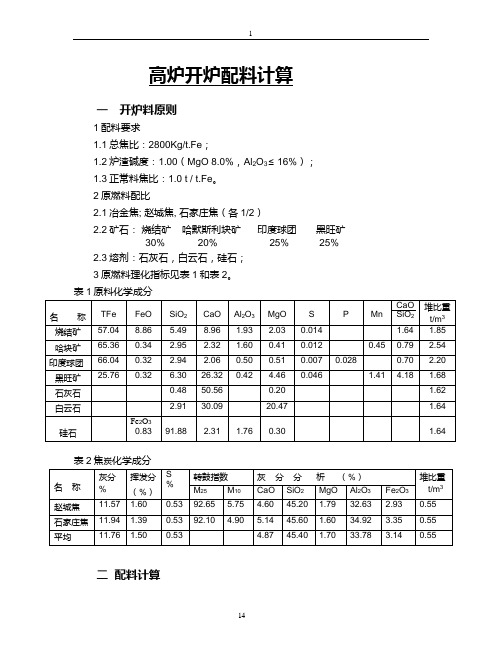
高炉开炉配料计算一开炉料原则1配料要求1.1总焦比:2800Kg/t.Fe;1.2炉渣碱度:1.00(MgO 8.0%,Al2O3≤16%);1.3正常料焦比:1.0 t / t.Fe。
2原燃料配比2.1冶金焦; 赵城焦, 石家庄焦(各1/2)2.2矿石:烧结矿哈默斯利块矿印度球团黑旺矿30% 20% 25% 25%2.3熔剂:石灰石,白云石,硅石;3原燃料理化指标见表1和表2。
二配料计算1、预计生铁成分元素Fe C Si Mn S含量(%) 92.47 4.0 3.0 0.5 0.032 、Fe、Mn回收率Fe回收率: 99.0%;Mn回收率 60.0%; S 分配率:85%进入炉渣,5%进入生铁。
3、以100 Kg混合矿计算:3.1 100 Kg混合矿平均含Fe:30×57.04%+20×65.36%+25×66.04+25×25.76% = 53.134,100 Kg混合矿出铁:100×53.13%×0.99 / 0.9247 = 56.886 Kg。
3.2炉渣成分核算:(1)生铁中Si消耗SiO256.886×3.0%×60 / 28 = 3.657(2)炉渣中FeO量53.134×1.0%×72 / 56 = 0.683(3)入炉料的S负荷30×0.014%+20×0.012%+25×0.007%+25×0.046%+56.886×0.53%=0.321(4)炉渣中的CaS0.321×85%×72 / 32=0.614(5)脱硫消耗CaO0.614×56/72=0.478(6)原燃料成分中进入炉渣的数量(7)炉渣成分调整为使炉渣成分达到要求标准,加白云石和硅石进行调整。
硅石加入量为:x白云石加入量为:y3.927+91.88% x +2.91% y =10.096+2.31% x+30.09% y2.045+0.30% x +20.47% y= 8.0%20.652+96.25% x+53.47% y解方程:x = 7.422 Kg。
高炉开炉配料计算

灰分 0.1313
Fe 57.7 63.9 59.25
10.83
4.13
1.353
0.75 0.25
挥发分 0.0131
SiO2 4.87 6.3 5.23 2.29 11.84 97.67 48.83
5000
Kg
2、则应装净焦的批数为:
二、虚拟矿批及虚拟总批数的计算 矿批=焦批*铁的回收率/(全炉焦比*品位) 1、一批正常料压缩后的体积为: 2、开炉料总批数为:
混合矿的R2=
烧结矿所占的比例:X= 球团矿所占的比例为:1-X=
一、净焦装入的批数(炉缸及炉腹) 1、净焦批重为:
Ⅵ
D3=
Ⅶ
h7=
h"=
料线
正常料焦比 0.86
Mn的回收率 0.5
石灰石 1.6
空料(X) 0.12
料线 1.67
Si 3
渣焦比 0.4
烧结 1.85
正常料(H) 0.12
布料角度 25°×13
h'' D3
Dx5
h7 V7
h6 V6 Dx4
h' Dx3
h5
V5
Dx2 h4 V4
D2 h3 V3
h2
h2-h2' h2'
h-h1 V2
h Dx1
h1
V1
D1 h0
蓝色为人为输入 红色为高炉本身参数 黑色为自动生成
Ⅰ
Ⅱ Ⅲ Ⅳ
D1= h0= h1= Dx1= h=
h-h1= h2= h2’= D2= h3= Dx2=
质量 329.75 142.19 472.16 320.57 448.86
CaO %
煤气发生量计算

一、已知某设计高炉的冶炼条件如下1、原料成分:高炉采用生矿和烧结矿两种矿石进行冶炼,其中矿石、和石灰石的成分经过整理和计算,如表1所示且混合矿是按照烧结矿和生矿比为9:1进行。
表1原料成分表%2、高炉使用的焦炭及喷吹的煤粉成分表如表2和表3所示:表3 喷吹无烟煤成分%3、根据炼钢对生铁的要求,规定生铁成分[Si]=0.7%,[S]=0.03%4、设计焦比为:K=干焦消耗量/合格生铁量=480kg 煤比:M=煤粉耗用量/合格生铁量=70kg5、设计炉渣碱度R=CaO/SiO2=1.106、元素在生铁,炉渣以及煤气中的分配比,如表4所示表4 元素分配率 %7、按照工艺设计规定,我们选取铁的直接还原度γd=0.45,氢利用率为ηH2=35%8、鼓风湿度测定为大约12.8g/m³9、热风温度大约为1100℃10、高炉采用冷烧结矿,炉顶温度为200℃二、配料计算根据上述已知条件,可以对高炉进行配料计算1、吨铁使用矿石量计算如下:燃料带入的铁量Fe.f:Fe.f=480×(0.0043×56/72)+70×0.0121×56/72=2.26 kg由公式A=[1000×﹙95.7-0.73[Si]-[S]﹚-99.7Fe.f]/﹙0.997TFe+0.68P矿+0.515Mn矿﹚可得吨铁矿石用量A=[1000×﹙95.7-0.7×0.73-0.03﹚-99.7×2.26]/﹙52.37+0.68×0.044+0.515×0.1﹚=1812.832、进行生铁成分的计算:[Fe]=(1812.83×0.5327+2.26)×0.997/10=96.51 (%)[Mn]=1812.83×0.001×0.5/10=0.09 ﹙%﹚[P]=﹙1812.83×0.00044+480×0.0001×62/142﹚/10=0.082 ﹙%﹚[C]=100-96.51-0.09-0.082-0.03-0.7=2.59 ﹙%﹚通过上述计算可以得到生铁成分表如下表5所示:表5 生铁成分表%3、石灰石用量矿石和燃料带入CaO的量G CaOG CaO =1812.83×0.1074+480×0.0051+70×0.0020=197.29kg矿石和燃料带入的SiO2的量G SiO2(必须扣除还原消耗的硅)G SiO2=1812.83×0.1027+480×0.0732+70×0.0939-10×0.7×60/28=200.54kg石灰石有效容剂性G SiO2有效=54.11-1.10×0.73=53.31 ﹙%﹚石灰石用量ФФ=﹙200.45×1.10-197.29﹚/0.5531=41.95 kg4、渣量及炉渣成分的计算由炉料带入的各种炉渣组分量∑CaO=197.29+41.95×0.5411=219.99 kg∑SiO2=200.54+41.95×0.073=200.85kg∑MgO=1812.83×0.0341+480×0.0012﹢70×0.0016+41.95×0.0116=62.99 kg∑Al2O3=1812.83×0.0113+480×0.0542+70×0.0582+41.95×0.0013=50.63 kg炉渣中MnO的量=1812.83×0.001×0.5×71/55=1.17 kg炉渣中FeO的量=965.1×0.003/0.997×72/56=3.73 kg一吨生铁炉料带入的硫量∑S=1812.83×0.00041+480×0.0079+70×0.0036+41.95×0.00029=4.80kg进入生铁中的硫量=10×0.03=0.3kg进入煤气中的硫量=4.80×0.05=0.24kg进入渣中的硫量=4.80-0.3-0.24=4.26kg于是得到如表6所示的炉渣组分表表6 炉渣组分表对炉渣进行性能校核:炉渣的实际的碱度为R=219.99/200.85=1.095≈1.10(实际碱度与规定碱度相符)炉渣脱硫的硫的分配系数Ls=2×0.30/0.03=20通过查阅炉渣相图可以得到炉渣的融化温度大约为1350℃由于炉渣在1500℃时,其粘度为2.5泊;当炉渣温度为1400℃时,炉渣粘度为4.0泊,故由炉渣的成分及性能校核,该种炉渣完全符合高炉冶炼的要求。
高炉简易配料计算
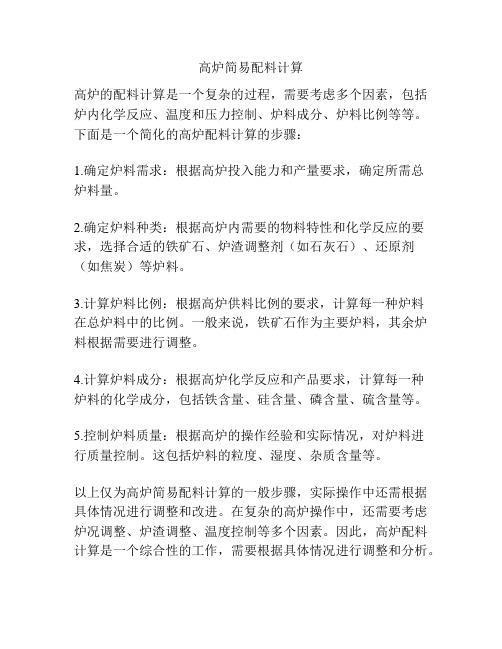
高炉简易配料计算
高炉的配料计算是一个复杂的过程,需要考虑多个因素,包括炉内化学反应、温度和压力控制、炉料成分、炉料比例等等。
下面是一个简化的高炉配料计算的步骤:
1.确定炉料需求:根据高炉投入能力和产量要求,确定所需总
炉料量。
2.确定炉料种类:根据高炉内需要的物料特性和化学反应的要求,选择合适的铁矿石、炉渣调整剂(如石灰石)、还原剂(如焦炭)等炉料。
3.计算炉料比例:根据高炉供料比例的要求,计算每一种炉料
在总炉料中的比例。
一般来说,铁矿石作为主要炉料,其余炉料根据需要进行调整。
4.计算炉料成分:根据高炉化学反应和产品要求,计算每一种
炉料的化学成分,包括铁含量、硅含量、磷含量、硫含量等。
5.控制炉料质量:根据高炉的操作经验和实际情况,对炉料进
行质量控制。
这包括炉料的粒度、湿度、杂质含量等。
以上仅为高炉简易配料计算的一般步骤,实际操作中还需根据具体情况进行调整和改进。
在复杂的高炉操作中,还需要考虑炉况调整、炉渣调整、温度控制等多个因素。
因此,高炉配料计算是一个综合性的工作,需要根据具体情况进行调整和分析。
1高炉配料计算

高炉炼铁主要经济技术指标 选定 (1) 高炉有效容积利用系数(v η)高炉有效容积利用系数即每昼夜生铁的产量与高炉有效容积之比,即每昼夜1m³有效容积的生铁产量。
可用下式表示:有V Pη=v 式中: v η——高炉有效容积利用系数,t /(m 3·d) P ——高炉每昼夜的生铁产量,t /d有V ——高炉有效容积,m 3V η是高炉冶炼的一个重要指标,有效容积利用系数愈大,高炉生产率愈高。
目前,一般大型高炉超过2.3,一些先进高炉可达到2.9。
小型高炉的更高。
本设计中取2.7。
(2) 焦比(K )焦比即 每昼夜焦炭消耗量与每昼夜生铁产量之比,即冶炼每吨生铁消耗焦炭量。
可用下式表示:式中 K ——高炉焦比,kg/tP ——高炉每昼夜的生铁产量,t /dK Q ——高炉每昼夜消耗焦炭量,kg/d焦比可根据设计采用的原燃料、风温、设备、操作等条件与实际生产情况进行全面分析比较和计算确定。
当高炉采用喷吹燃料时,计算焦比必须考虑喷吹物的焦炭置换量。
本设计中取K = 330 kg/t (3) 煤比(Y )冶炼每吨生铁消耗的煤粉为煤比。
本设计中取煤比为180 kg/t . (4) 冶炼强度(I )和燃烧强度(i )高炉冶炼强度是每昼夜31m 有效容积燃烧的焦炭量,即高炉每昼夜焦炭消耗量与有V 的比值, 本设计I =1.1 t/m 3∙d 。
燃烧强度i 既每小时每平方米炉缸截面积所燃烧的焦炭量。
本设计i = 30 t/m 2∙d 。
(5) 生铁合格率化学成分符合国家标准的生铁称为合格生铁,合格生铁占总产生铁量的百分数为生铁合格率。
它是衡量产品质量的指标。
(6) 生铁成本生产一吨合格生铁所消耗的所有原料、燃料、材料、水电、人工等一切费用的总和,单位为 元/t 。
(7) 休风率休风率是指高炉休风时间占高炉规定作业时间的百分数。
先进高炉休风率小于1%。
(8) 高炉一代寿命高炉一代寿命是从点火开炉到停炉大修之间的冶炼时间,或是指高炉相邻两次大修之间的冶炼时间。
高炉开炉方案

1#高炉开炉方案一、开炉方法采用带风装料,全焦炭填充炉缸,钒钛烧结矿+普球+会块开炉。
炉料填充原则:炉缸加上炉腹2/3填充净焦,炉腹1/3、炉腰、炉身下部填充空焦,最上面装入正常料。
当净焦和空焦装完后,开始通过混风阀向高炉送风,热风炉冷、热风阀全部关闭,当料线见影、上料设备运转正常后,转用热风阀向高炉送风,然后根据当时的高炉状况,逐步装料到规定料线。
二、开炉前的准备工作1、高炉所有检修项目结束,烘炉完毕;2、喷吹口装好,送风前开少量风(压力2.5-3kg/cm2),高、低渣口用镂耙堵上,外面固定保证不退出;3、1#、14#风口和铁口烧通。
开炉用8个风口送风,堵5#~10#风口,保证只能捅开不能吹开;4、炉前做好临时撇渣器;5、干渣场清理完毕,保证干渣场无积水,做好放干渣的准备;6、开铁口机角度调至0度;7、热风炉提前8小时烧好两座热风炉,保证送风时风温≥900℃;8、校正溜槽角度;9、上料系统联动试车8小时以上;10、铁水罐按要求配好,尽量用旧罐。
三、开炉原燃料结构1、焦炭: 30%德马焦+20%攀钢焦+50%圣达焦;2、烧结矿70%+普球15%+会块15%;四、开炉配料计算一、开炉参数的确定1、开炉总焦比(干)3.2t/t,正常料焦比(干)1.2t/t2、生铁成分:3、炉渣二元碱度R:1.05~1.14、各段炉容填充容积5、炉料压缩率6、各种料的堆比重(t/m3)7、原燃料化学分析8、焦炭水分:7%㈡配料计算(另出)五、开炉装料1、炉料填充原则:开炉料由净焦、空焦、正常料组成。
各种料的填充原则:炉缸加上炉腹2/3填充净焦、炉腹1/3以上填充空焦、正常料。
装料表如下:注:①、以上焦炭均为干焦,装料时根据当时焦炭的水份折算成湿焦。
②、每批料加萤石100kg,共56×100=5.6吨。
2 装料前准备工作确认装料准备工作和设备状态确认表3.装料操作(1)烘炉温度降至≤400℃,条件具备即开始装料。
高炉配料计算

高炉配料计算冶炼1t 生铁,需要一定数量的矿石、熔刑和燃料(焦炭及喷吹燃料)。
对于炼铁设计的工艺计算,燃料的用量是预先确定的,是已知的量,配料计算的主要任务,就是求出在满足炉渣碱度要求条件下,冶炼规定成分生铁所需要的矿石、熔剂数量。
对于生产高炉的工艺计算,各种原料的用量都是已知的,从整体上说不存在配料计算的问题,但有时需通过配料计算求解矿石的理论出铁量、理论渣量等,有时因冶炼条件变化需要作变料计算。
一、配料计算的目的配料计算的目的,在于根据已知的原料条件和冶炼要求来决定矿石和熔剂的用量,以配制合适的炉渣成分和获得合格的生铁。
二、配料计算时需要确定的已知条件(1)原始资料的收集整理生产中原始资料分析常常不完全,或元素分析和化合物分析不相吻合,加之分析方法不同存在分析误差,以致各种化学组成之和不等于100%。
因此,应该先确定元素在原料存在的形态,然后进行核算,使总和为100%。
换算为100%方法,可以均衡地扩大或缩小各成分的百分比,调整为100%,或者按照分析误差允许的范围,人为的调整为100%。
调整幅度不大时,以调整Al 2O 3或MgO 为宜。
在各种原料中化合物存在的形态和有关换算,按照下述方法处理。
烧结矿分析的S ,P ,Mn 分别以FeS, P 2O 5,MnO 形态存在。
它们的换算为:S──FeS ω(FeS)=ω(S )×3288% P──P 2O 5 ω(P 2O 5) =ω(P )×62142%Mn ──MnO ω(MnO)=ω(Mn )×5571%式中的S ,P ,Mn 等元素皆为分析值(百分含量),当要计算Fe 2O 3时,需要从生铁(TFe )中扣除FeO 和FeS 中的Fe ,再进行换算。
ω(Fe 2O 3)= (112162ω(Fe )-ω(FeO )×7256-ω(FeS )×8856)% 式中的Fe ,FeO 为分析所得烧结矿的全铁和氧化亚铁的百分含量,FeS 为换算所得的硫化亚铁量。
开炉计算
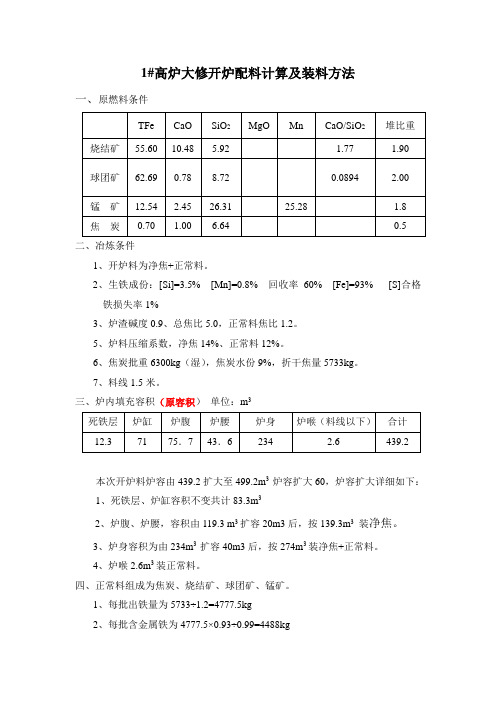
1#高炉大修开炉配料计算及装料方法一、原燃料条件二、冶炼条件1、开炉料为净焦+正常料。
2、生铁成份:[Si]=3.5% [Mn]=0.8% 回收率60% [Fe]=93% [S]合格铁损失率1%3、炉渣碱度0.9、总焦比5.0,正常料焦比1.2。
5、炉料压缩系数,净焦14%、正常料12%。
6、焦炭批重6300kg(湿),焦炭水份9%,折干焦量5733kg。
7、料线1.5米。
三、炉内填充容积(原容积)单位:m3本次开炉料炉容由439.2扩大至499.2m3 炉容扩大60,炉容扩大详细如下:1、死铁层、炉缸容积不变共计83.3m32、炉腹、炉腰,容积由119.3 m3扩容20m3后,按139.3m3装净焦。
3、炉身容积为由234m3 扩容40m3后,按274m3装净焦+正常料。
4、炉喉2.6m3装正常料。
四、正常料组成为焦炭、烧结矿、球团矿、锰矿。
1、每批出铁量为5733÷1.2=4777.5kg2、每批含金属铁为4777.5×0.93÷0.99=4488kg3、需要锰矿量为4777.5×0.8%/60%÷25.28%=252kg 取260kg4、锰矿带入金属铁260×12.54%=32.6kg5、焦炭带入金属铁为5733×0.7%=40kg6、烧结矿、球团矿需带入金属铁应为4488-32.6-40=4415.4kg7、设每批正常料含烧结矿为X,含球团矿为Y,列方程组:0.556X+0.6269Y=4415.40.1048X+0.0078Y+5733×0.01 +260×0.0245 0.90.0592X+0.0872Y+5733×0.0664+260×0.2631-4777.5×0.035×2.14解方程组取X=4500Y=3000即正常料为焦炭6300kg(湿),烧结4500kg,球团3000kg,锰矿260kg,矿石批重7760kg。