1高炉配料计算
高炉开炉配料计算
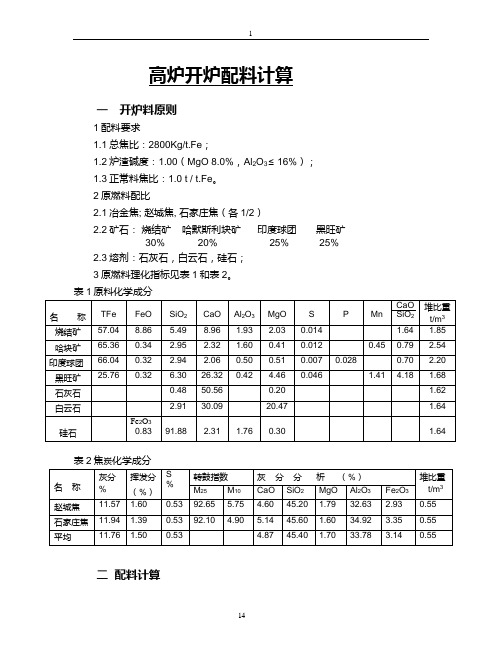
高炉开炉配料计算一开炉料原则1配料要求1.1总焦比:2800Kg/t.Fe;1.2炉渣碱度:1.00(MgO 8.0%,Al2O3≤16%);1.3正常料焦比:1.0 t / t.Fe。
2原燃料配比2.1冶金焦; 赵城焦, 石家庄焦(各1/2)2.2矿石:烧结矿哈默斯利块矿印度球团黑旺矿30% 20% 25% 25%2.3熔剂:石灰石,白云石,硅石;3原燃料理化指标见表1和表2。
二配料计算1、预计生铁成分元素Fe C Si Mn S含量(%) 92.47 4.0 3.0 0.5 0.032 、Fe、Mn回收率Fe回收率: 99.0%;Mn回收率 60.0%; S 分配率:85%进入炉渣,5%进入生铁。
3、以100 Kg混合矿计算:3.1 100 Kg混合矿平均含Fe:30×57.04%+20×65.36%+25×66.04+25×25.76% = 53.134,100 Kg混合矿出铁:100×53.13%×0.99 / 0.9247 = 56.886 Kg。
3.2炉渣成分核算:(1)生铁中Si消耗SiO256.886×3.0%×60 / 28 = 3.657(2)炉渣中FeO量53.134×1.0%×72 / 56 = 0.683(3)入炉料的S负荷30×0.014%+20×0.012%+25×0.007%+25×0.046%+56.886×0.53%=0.321(4)炉渣中的CaS0.321×85%×72 / 32=0.614(5)脱硫消耗CaO0.614×56/72=0.478(6)原燃料成分中进入炉渣的数量(7)炉渣成分调整为使炉渣成分达到要求标准,加白云石和硅石进行调整。
硅石加入量为:x白云石加入量为:y3.927+91.88% x +2.91% y =10.096+2.31% x+30.09% y2.045+0.30% x +20.47% y= 8.0%20.652+96.25% x+53.47% y解方程:x = 7.422 Kg。
高炉炼铁原材料配比及用量计算

高炉炼铁原材料配比及用量计算
设计中采用高炉炼铁工艺,有效容积为200M³的高炉两座,有效容积为100M³的高炉一座。
选取炉高炉有效容积利用系数ηv=2.2 t/(m3.d),由公式:P Q=M×T ×ηv×V v
式中:P Q——高炉车间年生铁产量,吨;
M——高炉座数;
T——年平均工作日,高炉一代炉役中,扣除大、中、小修时间后每年平均实际生产天数一般为330~350天。
此处采用350天。
所以,有效容积为200M³的高炉年产量为
PQ200M³=M×T ×ηv×Vv=2×350 ×2.2×200=308000t
PQ100M³=M×T ×ηv×Vv=1×350 ×2.2×100=77000t
PQ= PQ200M³+PQ100M³=308000+77000=385000t
根据高炉冶炼原理,生产1吨生铁,需要1.5-2.0吨铁矿石、0.4-0.6吨焦炭以及0.2-0.4吨熔剂。
本次设计采用生产1吨生铁,需要2.0吨铁矿石、0.5吨焦炭以及0.3吨熔剂。
所以经计算可知:
需要铁矿石的量为385000t×2=770000t
焦炭的量为385000t×0.5=192500t
熔剂的量为385000t×0.3=115500t。
高炉简易配料计算

高炉简易配料计算摘要:一、高炉配料计算的概述二、高炉配料计算的方法三、高炉配料计算的实例四、高炉配料计算的注意事项正文:一、高炉配料计算的概述高炉配料计算是高炉生产中非常重要的一个环节,它的主要目的是为了保证高炉的稳定生产和优化生产效果。
高炉配料计算主要包括矿石、燃料和熔剂的配比计算,通过合理的配料计算,可以使高炉在生产过程中达到最佳的熔化条件和最高的生产效率。
二、高炉配料计算的方法高炉配料计算的方法主要有经验法、理论法和模型法三种。
经验法是基于历史数据和操作经验进行的配料计算,这种方法简单易行,但准确性较低,适用于小型高炉和生产条件相对稳定的高炉。
理论法是根据高炉的熔化条件和物料的物理化学性质进行的配料计算,这种方法的准确性较高,但计算过程较为复杂,需要专业的技术人员进行。
模型法是利用计算机模拟高炉的熔化过程,根据模拟结果进行的配料计算,这种方法的准确性最高,但需要先进的计算机设备和专业的技术支持。
三、高炉配料计算的实例以某大型高炉为例,其生产过程中需要配比的物料主要有铁矿石、焦炭和石灰石。
根据高炉的熔化条件和物料的物理化学性质,我们可以通过理论法或模型法计算出铁矿石、焦炭和石灰石的最佳配比。
例如,假设高炉的熔化条件为:矿石熔化温度1500℃,燃料燃烧温度1200℃,熔剂加入温度1300℃。
铁矿石的含铁量55%,焦炭的热值8000kcal/kg,石灰石的含氧化钙量95%。
根据这些条件,我们可以计算出铁矿石、焦炭和石灰石的最佳配比为:铁矿石1000kg,焦炭800kg,石灰石500kg。
四、高炉配料计算的注意事项在进行高炉配料计算时,需要注意以下几点:1.确保计算的准确性。
配料计算的准确性直接影响到高炉的生产效果,因此在进行配料计算时,应尽可能的提高计算的准确性。
2.考虑物料的物理化学性质。
不同的物料在高炉中的作用不同,因此在进行配料计算时,应充分考虑物料的物理化学性质。
3.考虑生产条件的变化。
高炉开炉配料计算

灰分 0.1313
Fe 57.7 63.9 59.25
10.83
4.13
1.353
0.75 0.25
挥发分 0.0131
SiO2 4.87 6.3 5.23 2.29 11.84 97.67 48.83
5000
Kg
2、则应装净焦的批数为:
二、虚拟矿批及虚拟总批数的计算 矿批=焦批*铁的回收率/(全炉焦比*品位) 1、一批正常料压缩后的体积为: 2、开炉料总批数为:
混合矿的R2=
烧结矿所占的比例:X= 球团矿所占的比例为:1-X=
一、净焦装入的批数(炉缸及炉腹) 1、净焦批重为:
Ⅵ
D3=
Ⅶ
h7=
h"=
料线
正常料焦比 0.86
Mn的回收率 0.5
石灰石 1.6
空料(X) 0.12
料线 1.67
Si 3
渣焦比 0.4
烧结 1.85
正常料(H) 0.12
布料角度 25°×13
h'' D3
Dx5
h7 V7
h6 V6 Dx4
h' Dx3
h5
V5
Dx2 h4 V4
D2 h3 V3
h2
h2-h2' h2'
h-h1 V2
h Dx1
h1
V1
D1 h0
蓝色为人为输入 红色为高炉本身参数 黑色为自动生成
Ⅰ
Ⅱ Ⅲ Ⅳ
D1= h0= h1= Dx1= h=
h-h1= h2= h2’= D2= h3= Dx2=
质量 329.75 142.19 472.16 320.57 448.86
CaO %
高炉简易配料计算
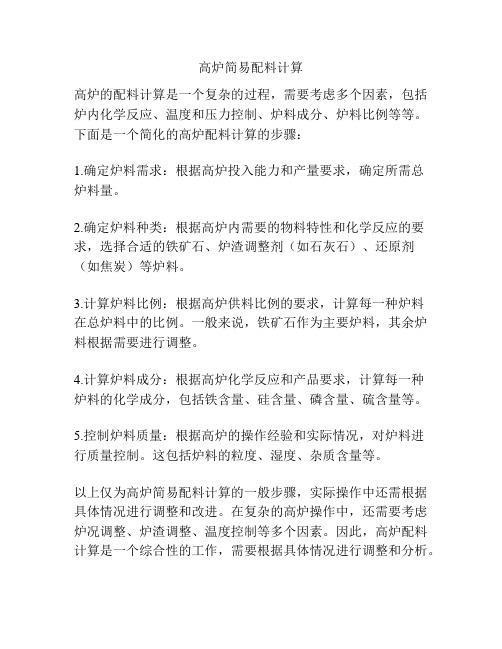
高炉简易配料计算
高炉的配料计算是一个复杂的过程,需要考虑多个因素,包括炉内化学反应、温度和压力控制、炉料成分、炉料比例等等。
下面是一个简化的高炉配料计算的步骤:
1.确定炉料需求:根据高炉投入能力和产量要求,确定所需总
炉料量。
2.确定炉料种类:根据高炉内需要的物料特性和化学反应的要求,选择合适的铁矿石、炉渣调整剂(如石灰石)、还原剂(如焦炭)等炉料。
3.计算炉料比例:根据高炉供料比例的要求,计算每一种炉料
在总炉料中的比例。
一般来说,铁矿石作为主要炉料,其余炉料根据需要进行调整。
4.计算炉料成分:根据高炉化学反应和产品要求,计算每一种
炉料的化学成分,包括铁含量、硅含量、磷含量、硫含量等。
5.控制炉料质量:根据高炉的操作经验和实际情况,对炉料进
行质量控制。
这包括炉料的粒度、湿度、杂质含量等。
以上仅为高炉简易配料计算的一般步骤,实际操作中还需根据具体情况进行调整和改进。
在复杂的高炉操作中,还需要考虑炉况调整、炉渣调整、温度控制等多个因素。
因此,高炉配料计算是一个综合性的工作,需要根据具体情况进行调整和分析。
开炉配料方案
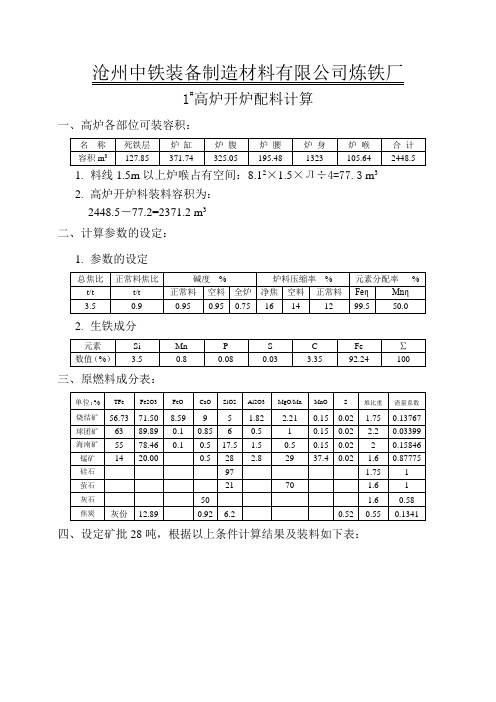
沧州中铁装备制造材料有限公司炼铁厂
1#高炉开炉配料计算
一、高炉各部位可装容积:
1.料线1.5m以上炉喉占有空间:8.12×1.5×Л÷4=77.3 m3
2.高炉开炉料装料容积为:
2448.5-77.2=2371.2 m3
二、计算参数的设定:
1.参数的设定
2.生铁成分
三、原燃料成分表:
四、设定矿批28吨,根据以上条件计算结果及装料如下表:
#
装料误差:0.608% 枕木区的空余体积189 参与造渣的焦炭总量844.7 净焦参与造渣的数量13.4
注: 1、表中H——Kg↓J↓,K-机烧+球团+海南矿+锰矿;J—焦炭;g—萤石;h—灰石;
2、料批组成的焦炭为干焦,装料时注意应该转化为湿焦,焦炭水分为:4%,则实际焦炭批重:13.38kg/批;
3、空焦上完规定料批后实测料线,超过料线继续按装料计划上料,如果低于计划料线则补加空焦到达料线后再装下段料;
4、点火送风2小时如无异常后焦比减到750kg/t,8小时后如无异常焦比减到700kg/t,出完第一次铁后无异常焦比减到650kg/t。
高炉开炉方案
1#高炉开炉方案一、开炉方法采用带风装料,全焦炭填充炉缸,钒钛烧结矿+普球+会块开炉。
炉料填充原则:炉缸加上炉腹2/3填充净焦,炉腹1/3、炉腰、炉身下部填充空焦,最上面装入正常料。
当净焦和空焦装完后,开始通过混风阀向高炉送风,热风炉冷、热风阀全部关闭,当料线见影、上料设备运转正常后,转用热风阀向高炉送风,然后根据当时的高炉状况,逐步装料到规定料线。
二、开炉前的准备工作1、高炉所有检修项目结束,烘炉完毕;2、喷吹口装好,送风前开少量风(压力2.5-3kg/cm2),高、低渣口用镂耙堵上,外面固定保证不退出;3、1#、14#风口和铁口烧通。
开炉用8个风口送风,堵5#~10#风口,保证只能捅开不能吹开;4、炉前做好临时撇渣器;5、干渣场清理完毕,保证干渣场无积水,做好放干渣的准备;6、开铁口机角度调至0度;7、热风炉提前8小时烧好两座热风炉,保证送风时风温≥900℃;8、校正溜槽角度;9、上料系统联动试车8小时以上;10、铁水罐按要求配好,尽量用旧罐。
三、开炉原燃料结构1、焦炭: 30%德马焦+20%攀钢焦+50%圣达焦;2、烧结矿70%+普球15%+会块15%;四、开炉配料计算一、开炉参数的确定1、开炉总焦比(干)3.2t/t,正常料焦比(干)1.2t/t2、生铁成分:3、炉渣二元碱度R:1.05~1.14、各段炉容填充容积5、炉料压缩率6、各种料的堆比重(t/m3)7、原燃料化学分析8、焦炭水分:7%㈡配料计算(另出)五、开炉装料1、炉料填充原则:开炉料由净焦、空焦、正常料组成。
各种料的填充原则:炉缸加上炉腹2/3填充净焦、炉腹1/3以上填充空焦、正常料。
装料表如下:注:①、以上焦炭均为干焦,装料时根据当时焦炭的水份折算成湿焦。
②、每批料加萤石100kg,共56×100=5.6吨。
2 装料前准备工作确认装料准备工作和设备状态确认表3.装料操作(1)烘炉温度降至≤400℃,条件具备即开始装料。
1高炉配料计算
高炉炼铁主要经济技术指标 选定(1) 高炉有效容积利用系数(v η)高炉有效容积利用系数即每昼夜生铁的产量与高炉有效容积之比,即每昼夜1m³有效容积的生铁产量。
可用下式表示:有V Pη=v 式中: v η——高炉有效容积利用系数,t /(m 3·d) P ——高炉每昼夜的生铁产量,t /d有V ——高炉有效容积,m 3V η是高炉冶炼的一个重要指标,有效容积利用系数愈大,高炉生产率愈高。
目前,一般大型高炉超过2.3,一些先进高炉可达到2.9。
小型高炉的更高。
本设计中取2.7。
(2) 焦比(K )焦比即 每昼夜焦炭消耗量与每昼夜生铁产量之比,即冶炼每吨生铁消耗焦炭量。
可用下式表示:式中 K ——高炉焦比,kg/t——高炉每昼夜的生铁产量,t /dK Q ——高炉每昼夜消耗焦炭量,kg/d焦比可根据设计采用的原燃料、风温、设备、操作等条件与实际生产情况进行全面分析比较和计算确定。
当高炉采用喷吹燃料时,计算焦比必须考虑喷吹物的焦炭置换量。
本设计中取K = 330 kg/t (3) 煤比(Y )冶炼每吨生铁消耗的煤粉为煤比。
本设计中取煤比为180 kg/t .(4) 冶炼强度(I )和燃烧强度(i )高炉冶炼强度是每昼夜31m 有效容积燃烧的焦炭量,即高炉每昼夜焦炭消耗量与有V 的比值, 本设计I =1.1 t/m 3∙d 。
燃烧强度i 既每小时每平方米炉缸截面积所燃烧的焦炭量。
本设计i = 30 t/m 2∙d 。
(5) 生铁合格率化学成分符合国家标准的生铁称为合格生铁,合格生铁占总产生铁量的百分数为生铁合格率。
它是衡量产品质量的指标。
(6) 生铁成本生产一吨合格生铁所消耗的所有原料、燃料、材料、水电、人工等一切费用的总和,单位为 元/t 。
(7) 休风率休风率是指高炉休风时间占高炉规定作业时间的百分数。
先进高炉休风率小于1%。
(8) 高炉一代寿命高炉一代寿命是从点火开炉到停炉大修之间的冶炼时间,或是指高炉相邻两次大修之间的冶炼时间。
高炉常用计算公式
炼铁用计算公式1、根据焦炭负荷求焦比焦比=1000/(负荷×综合品位)=矿批/(负荷×理论焦比)2有效容积利用系数=每昼夜生铁产量/高炉有有效容积3焦比=每昼夜消耗的湿焦量×(1-水分)/每昼夜的生铁产量4理论出铁量=(矿批×综合焦比)/=矿批×综合品位×不考虑进去渣中的铁量因为焦炭也带入部分铁5富氧率=-×富氧量/60×风量=×富氧量/风量6煤比=每昼夜消耗的煤量/每昼夜的生铁含量7 综合焦比=焦比+煤比×8 综合燃料比=焦比+煤比+小块焦比9 冶炼强度=每昼夜消耗的干焦量/高炉有效容积10 矿比=每昼夜加入的矿的总量/每昼夜的出铁量11 风速=风量(1-漏风率)/风口总面积漏风率20%12 冶炼周期=(V有 -V炉缸内风口以下的体积)/(V球+V烧+V矿)×88%=(V球+V烧+V矿)×88%13 综合品位=(m烧×烧结品位+m球×球品位+m矿×矿品位)/每昼夜加入的矿的总量14 安全容铁量=×ρ铁×1/4πd2hh取风口中心线到铁口中线间高度的一半15 圆台表面积=π/2(D+d)体积=π/12×h×(D2+d2+Dd)16 正方角锥台表面积S=a2 +b2 +4( a+b/2)h V=h/3(a2+b2+ab)=h/3(S1+S2+√S1S)17、圆锥侧面积M=πrl=πr√r2+h2体积V=1/3πr2h18、球S=4πr2=πd2V=4/3πr3=π/6d319、风口前燃烧1kg碳素所需风量(不富氧时)V风=24×1/+ f为鼓风湿度20、吨焦耗风量V风=(+)×1000×85%f为鼓风湿度 85%为焦炭含碳量21、鼓风动能(1)E=(764I2-3010I+3350)dE-鼓风动能 I-冶炼强度(2)E=1/2mv2=1/2×Q×r风/(60gn)v风实2Q-风量 r 风-风的密度 g= n-风口数目22、石灰的有效容剂性 CaO 有效=CaO 熔-SiO 2×R23、洗炉墙时,渣中CaF 2含量控制在2%-3%,洗炉缸时可掌控在5%左右,一般控制在%每批料萤石加入量X=P 矿×TFe ×Q ×(CaF 2)/([Fe]×N) P 矿-矿批重 TFe-综合品位 [Fe]-生铁中含铁量 Q-吨铁渣量 (CaF 2)-渣中CaF 2含量 N-萤石中CaF 2含量24、风口前燃烧1kg 碳素的炉缸煤气量 V 煤气=(+)/(+)××C 风 C 风-风口前燃烧的碳素量,kg25、理论出渣量 渣量批=QCaO 批/CaO 渣渣量批-每批炉料的理论渣量,t QCaO 批-每批料带入的CaO 量,t CaO 渣-炉渣中CaO 的含量,%25、喷吹煤粉热滞后时间 t=V 总/(V 批×n )V 总-H 2参加反应区起点处平面(炉身温度1100℃~1200℃处)至风口平面间的容积,m ³V 批-每批料的体积,m ³ n-平均每小时的下料批数,批/h26、高炉某部位需要由冷却水带走的热量称为热负荷,单位表面积炉衬或炉壳的热负荷称为冷却强度Q=CM(t-t)×103Q-热负荷 kJ/hM-冷却水消耗量,t/hC-水的比热容,kJ/(kg.℃) t-冷却水出水温度℃-冷水进水温度,℃t。
高炉配料计算
高炉配料计算冶炼1t 生铁,需要一定数量的矿石、熔刑和燃料(焦炭及喷吹燃料)。
对于炼铁设计的工艺计算,燃料的用量是预先确定的,是已知的量,配料计算的主要任务,就是求出在满足炉渣碱度要求条件下,冶炼规定成分生铁所需要的矿石、熔剂数量。
对于生产高炉的工艺计算,各种原料的用量都是已知的,从整体上说不存在配料计算的问题,但有时需通过配料计算求解矿石的理论出铁量、理论渣量等,有时因冶炼条件变化需要作变料计算。
一、配料计算的目的配料计算的目的,在于根据已知的原料条件和冶炼要求来决定矿石和熔剂的用量,以配制合适的炉渣成分和获得合格的生铁。
二、配料计算时需要确定的已知条件(1)原始资料的收集整理生产中原始资料分析常常不完全,或元素分析和化合物分析不相吻合,加之分析方法不同存在分析误差,以致各种化学组成之和不等于100%。
因此,应该先确定元素在原料存在的形态,然后进行核算,使总和为100%。
换算为100%方法,可以均衡地扩大或缩小各成分的百分比,调整为100%,或者按照分析误差允许的范围,人为的调整为100%。
调整幅度不大时,以调整Al 2O 3或MgO 为宜。
在各种原料中化合物存在的形态和有关换算,按照下述方法处理。
烧结矿分析的S ,P ,Mn 分别以FeS, P 2O 5,MnO 形态存在。
它们的换算为:S──FeS ω(FeS)=ω(S )×3288% P──P 2O 5 ω(P 2O 5) =ω(P )×62142%Mn ──MnO ω(MnO)=ω(Mn )×5571%式中的S ,P ,Mn 等元素皆为分析值(百分含量),当要计算Fe 2O 3时,需要从生铁(TFe )中扣除FeO 和FeS 中的Fe ,再进行换算。
ω(Fe 2O 3)= (112162ω(Fe )-ω(FeO )×7256-ω(FeS )×8856)% 式中的Fe ,FeO 为分析所得烧结矿的全铁和氧化亚铁的百分含量,FeS 为换算所得的硫化亚铁量。
- 1、下载文档前请自行甄别文档内容的完整性,平台不提供额外的编辑、内容补充、找答案等附加服务。
- 2、"仅部分预览"的文档,不可在线预览部分如存在完整性等问题,可反馈申请退款(可完整预览的文档不适用该条件!)。
- 3、如文档侵犯您的权益,请联系客服反馈,我们会尽快为您处理(人工客服工作时间:9:00-18:30)。
高炉炼铁主要经济技术指标 选定 (1) 高炉有效容积利用系数(v η)高炉有效容积利用系数即每昼夜生铁的产量与高炉有效容积之比,即每昼夜1m³有效容积的生铁产量。
可用下式表示:有V Pη=v 式中: v η——高炉有效容积利用系数,t /(m 3·d) P ——高炉每昼夜的生铁产量,t /d有V ——高炉有效容积,m 3V η是高炉冶炼的一个重要指标,有效容积利用系数愈大,高炉生产率愈高。
目前,一般大型高炉超过2.3,一些先进高炉可达到2.9。
小型高炉的更高。
本设计中取2.7。
(2) 焦比(K )焦比即 每昼夜焦炭消耗量与每昼夜生铁产量之比,即冶炼每吨生铁消耗焦炭量。
可用下式表示:式中 K ——高炉焦比,kg/tP ——高炉每昼夜的生铁产量,t /dK Q ——高炉每昼夜消耗焦炭量,kg/d焦比可根据设计采用的原燃料、风温、设备、操作等条件与实际生产情况进行全面分析比较和计算确定。
当高炉采用喷吹燃料时,计算焦比必须考虑喷吹物的焦炭置换量。
本设计中取K = 330 kg/t (3) 煤比(Y )冶炼每吨生铁消耗的煤粉为煤比。
本设计中取煤比为180 kg/t . (4) 冶炼强度(I )和燃烧强度(i )高炉冶炼强度是每昼夜31m 有效容积燃烧的焦炭量,即高炉每昼夜焦炭消耗量与有V 的比值, 本设计I =1.1 t/m 3∙d 。
燃烧强度i 既每小时每平方米炉缸截面积所燃烧的焦炭量。
本设计i = 30 t/m 2∙d 。
(5) 生铁合格率化学成分符合国家标准的生铁称为合格生铁,合格生铁占总产生铁量的百分数为生铁合格率。
它是衡量产品质量的指标。
(6) 生铁成本生产一吨合格生铁所消耗的所有原料、燃料、材料、水电、人工等一切费用的总和,单位为 元/t 。
(7) 休风率休风率是指高炉休风时间占高炉规定作业时间的百分数。
先进高炉休风率小于1%。
(8) 高炉一代寿命高炉一代寿命是从点火开炉到停炉大修之间的冶炼时间,或是指高炉相邻两次大修之间的冶炼时间。
大型高炉一代寿命为10~15年。
烧结矿、球团矿、块矿用矿比例(炉料结构):63:27:10高炉炼铁综合计算高炉炼铁需要的矿石、熔剂和燃料(焦炭及喷吹燃料)的量是有一定规律的,根据原料成分、产品质量要求和冶炼条件不同可以设计出所需的工艺条件。
对于炼铁设计的工艺计算,燃料的用量是预先确定的,是已知的量,配料计算的主要任务,就是计算在满足炉渣碱度要求条件下,冶炼预定成分生铁所需要的矿石、熔剂数量。
对于生产高炉的工艺计算,各种原料的用量都是已知的,从整体上说不存在配料计算的问题,但有时需通过配料计算求解矿石的理论出铁量、理论渣量等,有时因冶炼条件变化需要作变料计算 [1]。
4.1 高炉配料计算配料计算的目的,在于根据已知的原料条件和冶炼要求来决定矿石和熔剂的用量,以配制合适的炉渣成分和获得合格的生铁。
有V Q I K4.1.1已知条件4.1.1.1 原始数据整理生产中原始资料分析常常不完全,或元素分析和化合物分析不相吻合,加之分析方法不同存在分析误差,以致各种化学组成之和不等于100%。
因此,应该先确定元素在原料存在的形态,然后进行核算,使总和为100%。
换算为100%方法,可以均衡地扩大或缩小各成分的百分比,调整为100%,或者按照分析误差允许的范围,人为的调整为100%。
调整幅度不大时,以调整Al 2O 3或MgO 为宜。
在各种原料中化合物存在的形态和有关换算,按照下述方法处理。
烧结矿分析的S ,P ,Mn 分别以FeS , P 2O 5,MnO 形态存在。
它们的换算为:S 存在形式为FeS ,换算关系为: w (FeS)=w (S)×3288%P 存在形式为P 2O 5,换算关系为: w (P 2O 5) =w (P)×62142%Mn 存在形式为MnO ,换算关系为: w (MnO)=w (Mn)×5571%式中的S ,P ,Mn 等元素皆为分析值(百分含量),当要计算Fe 2O 3时,需要从生铁(TFe )中扣除FeO 和FeS 中的Fe ,再进行换算。
w (Fe 2O 3)= 160/112*(w (Fe)-w (FeO)×7256-w (FeS)×8856)% 式中的Fe ,FeO 为分析所得烧结矿的全铁和氧化亚铁的百分含量,FeS 为换算所得的硫化亚铁量。
若天然矿石中的S 以FeS 2形态存在,换算式如下:w (FeS 2)=w (S)×64120%,式中S 为分析所得的百分含量。
4.1.1.2 矿石选配在使用混合矿石冶炼时,应根据矿石供应量及炉渣成分适当配比选取。
此时,需要注意以下几点:(1) 矿石含P 量不应该超过生铁允许含P 量,因考虑P 全部进入生铁,故需要依据矿石含量事先预算,若某种矿石冶炼含P 超标,此种情况下,只能搭配含P 更低的矿石冶炼。
(2) 冶炼铸造铁时,应该核算生铁含锰量是否满足要求。
w [Mn]=Mn ×w (Mn)矿×m (Fe)铁/w (Fe)矿式中: w [Mn]—生铁含锰量,%;w (Mn)矿——混合矿含锰量,%;Mn η—锰的回收率,一般为0.5~0.6;m (Fe)铁—矿石带入的生铁的铁量,kg/t 铁; w (Fe)矿—混合矿含铁量,%。
(3) 冶炼锰铁时,为保证其含锰量,须检查矿石含铁量是否大于允许范围。
w (Fe) 矿=(100-w [Mn]-w [C]-w [Si]-w [P])/100×(w [Mn]/w Mn矿×Mn η)式中:w [Mn],w [Si],w [C],w [P]表示锰铁中该元素含量,%;w (Mn)矿—锰矿含锰量,%; w (Fe)矿—锰矿允许含铁量,%;Mn η—锰回收率,通常为0.7~0.82。
(4)适当控制碱金属[2]。
4.1.1.3 冶炼条件确定(1)根据原料条件,国家标准和行业标准等确定生铁成分。
C ,P 元素一般操作不能控制,而Si,Mn,S 等元素可以改变操作条件加以控制。
(2)各种元素在铁,渣和煤气中的分配比例。
按照经验和实际生产数据选取。
一般可参考表4-1选。
表4-1 常见元素分配率钒钛磁铁时,还应该考虑炉渣抑制硅钛还原和利于矾的回收能力,在正常炉钢温度下,要保证流动性和稳定性,因此除了考虑二元碱度外,还需要有适宜的MgO 含量,若炉料含碱金属还应该兼顾炉渣排碱要求。
本设计中取炉渣碱度R =1.1。
(4)燃料使用量确定。
确定燃料比应该依据冶炼铁种,原料条件,风温水平和生产经验等全面衡定,在有喷吹条件下,力争多喷燃料。
本设计假定(1)焦比为330 kg/t ,(2)煤粉喷吹量为180 kg/t ,(3)炉渣碱度1.1SiO CaO2=,(4)冶炼强度I =1.1 t/m3∙d ,(5)热风温度为1250℃,鼓风相对湿度为1% ,(6)炉顶煤气温度为400℃,(7)炉尘吹出量为8 kg/t ,(8)直接还原度为 0.45,(9)焦炭与喷吹燃料中总碳量的1.2% 与2H 生成CH 4。
(5)原燃料成分分析,入炉原料成分见表4-2。
表 4-2 入炉原料成分(%)4-2其中,烧结矿、球团矿、块矿的比例(炉料结构):63:27:10。
石灰石成分如下表。
炉尘成分如下表。
(6)焦炭成分分析见表4-3。
表4-3 焦炭成分(%)(7)喷吹物 煤粉的成分见表4-4。
表4-4 喷吹物成分(%)4.1.2 计算方法与过程为精确配料,现根据设计的生产要求,先根据生铁成分,然后用理论方法进行配料比计算,然后以配出的矿石为基础对矿石用量、生铁中铁量、渣量及炉渣进行计算,最后进行炉渣性能、生铁成分进行校核。
4.1.2.1 生铁成分本计算假定为炼钢生铁,其含硅量为0.4%,含硫量根据生铁规格和冶炼条件假定为0.03%。
预定的生铁成分如表4-5。
表4-5 生铁成分(%)4.1.2.2 计算混合矿量根据以上已知条件,先以1t 生铁作为计算单位进行计算,确定矿石配比。
则: 焦炭带入Fe 量:0 kg ; 煤粉带入Fe 量:0kg ;进入生铁中Fe 量:946.3 kg ;进入渣中Fe 量:847.2997.0003.03.946=⨯ kg ;进入炉尘中Fe 量: 8 ×0.432=3.456 kg ;故需要混合矿量:00.1641805.50456.347.826.394=++kg 。
4.1.2.3 根据碱度平衡计算石灰石用量: 假设石灰石加入量为X kg /t ,则:混合矿带入CaO 量:1641×6.946%=113.98 kg 焦炭带入CaO 量:330×0.855%=2.82 kg 煤粉带入CaO 量 :180×0.567%=1.02 kg 石灰石带入CaO 量 :X ×52.57%=0.5257X kg 炉尘带走的CaO 量:8*8.3%=0.664 kg共带入CaO 量:113.98+2.82+1.02+0.5257X-0.664=117.82+0.5257X kg混合矿带入SiO 2 量:1641×5.421%=88.96 kg 焦炭带入SiO 2 量:330×6.311%=20.83 kg 煤粉带入SiO 2 量:180×9.438%=16.99 kg 石灰石带入SiO 2量 :X ×1.70%=0.017X kg 炉尘带走的SiO 2量:8*13.8%=1.104 kg 还原硅所消耗的SiO 2量:4*60/28=8.571 kg共带入SiO 2 量:88.96+20.83+46.99+0.017X -1.104-8.571=117.105+0.017X kg 由于设计的炉渣碱度:1.1SiO CaO2=,则解得 石灰石加入量为23.00 kg/t 。
则总CaO 量为129.91kg/t ,总SiO 2量为117.49kg/t 。
原料消耗总表如表4-6。
表4-6 冶炼每吨炼钢生铁原料消耗表(kg )4.1.2.4 终渣成分及渣量计算 (1) 终渣S 含量炉料全部含S 量:1641×0.247%+330×0.631%+180×0.303%=6.68kg 进入生铁的S 量: 1000×0.03%=0.3kg 炉尘带走的S 量:8×0.485%=0.0388 kg 煤气带走的S 量:6.68×0.05=0.334 kg故进入炉渣的S 量: 6.68-0.3-0.0388-0.334=6.0072 kg(2) 终渣的FeO 量:5672×997.0003.0946.3=3.66kg (3) 终渣的MnO 量:1641×0.105%×0.5=0.86kg(4) 终渣的SiO 2量: =117.49kg (5) 终渣的CaO 量: =129.91kg (6) 终渣的Al 2O 3量:1641×1.762%+330×5.242%+180×5.686%+23.00*1.85%-8*1.31% =56.77kg(7) 终渣的MgO 量:1641×1.579%+330×0.224%+180×0.137%+23.00×2.21%-8×1.99%=27.25kg终渣成分见表4-7。