810m3高炉开炉料计算
高炉开炉配料计算
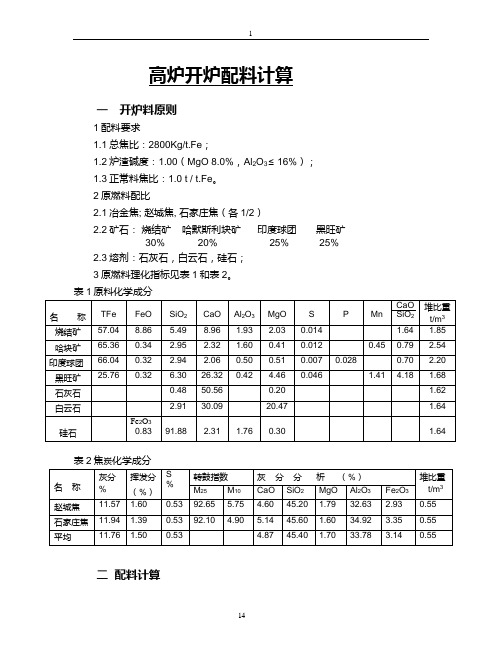
高炉开炉配料计算一开炉料原则1配料要求1.1总焦比:2800Kg/t.Fe;1.2炉渣碱度:1.00(MgO 8.0%,Al2O3≤16%);1.3正常料焦比:1.0 t / t.Fe。
2原燃料配比2.1冶金焦; 赵城焦, 石家庄焦(各1/2)2.2矿石:烧结矿哈默斯利块矿印度球团黑旺矿30% 20% 25% 25%2.3熔剂:石灰石,白云石,硅石;3原燃料理化指标见表1和表2。
二配料计算1、预计生铁成分元素Fe C Si Mn S含量(%) 92.47 4.0 3.0 0.5 0.032 、Fe、Mn回收率Fe回收率: 99.0%;Mn回收率 60.0%; S 分配率:85%进入炉渣,5%进入生铁。
3、以100 Kg混合矿计算:3.1 100 Kg混合矿平均含Fe:30×57.04%+20×65.36%+25×66.04+25×25.76% = 53.134,100 Kg混合矿出铁:100×53.13%×0.99 / 0.9247 = 56.886 Kg。
3.2炉渣成分核算:(1)生铁中Si消耗SiO256.886×3.0%×60 / 28 = 3.657(2)炉渣中FeO量53.134×1.0%×72 / 56 = 0.683(3)入炉料的S负荷30×0.014%+20×0.012%+25×0.007%+25×0.046%+56.886×0.53%=0.321(4)炉渣中的CaS0.321×85%×72 / 32=0.614(5)脱硫消耗CaO0.614×56/72=0.478(6)原燃料成分中进入炉渣的数量(7)炉渣成分调整为使炉渣成分达到要求标准,加白云石和硅石进行调整。
硅石加入量为:x白云石加入量为:y3.927+91.88% x +2.91% y =10.096+2.31% x+30.09% y2.045+0.30% x +20.47% y= 8.0%20.652+96.25% x+53.47% y解方程:x = 7.422 Kg。
高炉开炉配料计算

灰分 0.1313
Fe 57.7 63.9 59.25
10.83
4.13
1.353
0.75 0.25
挥发分 0.0131
SiO2 4.87 6.3 5.23 2.29 11.84 97.67 48.83
5000
Kg
2、则应装净焦的批数为:
二、虚拟矿批及虚拟总批数的计算 矿批=焦批*铁的回收率/(全炉焦比*品位) 1、一批正常料压缩后的体积为: 2、开炉料总批数为:
混合矿的R2=
烧结矿所占的比例:X= 球团矿所占的比例为:1-X=
一、净焦装入的批数(炉缸及炉腹) 1、净焦批重为:
Ⅵ
D3=
Ⅶ
h7=
h"=
料线
正常料焦比 0.86
Mn的回收率 0.5
石灰石 1.6
空料(X) 0.12
料线 1.67
Si 3
渣焦比 0.4
烧结 1.85
正常料(H) 0.12
布料角度 25°×13
h'' D3
Dx5
h7 V7
h6 V6 Dx4
h' Dx3
h5
V5
Dx2 h4 V4
D2 h3 V3
h2
h2-h2' h2'
h-h1 V2
h Dx1
h1
V1
D1 h0
蓝色为人为输入 红色为高炉本身参数 黑色为自动生成
Ⅰ
Ⅱ Ⅲ Ⅳ
D1= h0= h1= Dx1= h=
h-h1= h2= h2’= D2= h3= Dx2=
质量 329.75 142.19 472.16 320.57 448.86
CaO %
810m3高炉开炉料计算

810m3高炉开炉料计算810m高炉开炉料计算开炉工作有两个方面的要求:一是安全顺利地完成开炉工作,即做到炉温适中,铁口易开,下料顺畅,并且无人身、设备事故:二是在开炉后能较快平稳地过渡到正常生产,以获得较好的经济效益。
为此开炉时应该使炉内各区域适时地达到所需要的温度,故开炉料的选择,开炉焦比的确定,以及炉段的安排至关重要。
36.1 开炉焦比的选择所谓开炉焦比(总焦比是指开炉料的总焦量与理论出铁量之比。
开炉时由于高炉炉衬温度、料柱的温度都很低,炉料未经充分的预热和还原直接到炉缸,直接还原增多,渣量打,需要消耗的热量也多,所以开炉焦比要比正常焦比高几倍。
具体数值应该根据高炉容积大小,原燃料条件、风温高低、设备状况及技术操作水平等因素进行选择。
一般情况见表6-1:表6-1 开炉焦比的选择炉容/m 焦比/t?t铁?13100以下 >4100-500 3-4500-1000 2.5-31000以上 <2.6选择合适的开炉焦比对开炉进程有决定性的影响。
焦比选择过高,既不经济,又可能导致炉况不顺,即导致高温区上移,在炉身中上部容易产生炉墙结厚现象,更严重的是延长了开炉时间;焦比选择过低,会导致炉缸温度不足,出渣出铁困难,渣铁流动不畅,严重时会造成炉缸冻结。
一般要求开炉前几次含硅量为3%-3.5%。
6.2 开炉造渣制度的选择为了改善渣铁流动性能,冶炼合格生铁,加热炉缸,稀释渣中的Al2O3(Al2O3含量大于18%时,开炉配料中需增加低Al2O3的造渣剂),开炉时渣量要大一些,渣铁比一般为0.4-0.5.如渣量小,可加干渣调节。
开炉时炉渣碱度SiO2?0.90-1.05。
控制生铁含?Mn?0.8%,为了改善炉渣流动性,可提高渣中的MgO含量,使之维持在8%-10%左右,也可适当加些萤石来稀释炉渣。
小高炉在用全天然矿冷风开炉时,焦比特高,可在空料(即焦炭+石灰石)段加些硅石来调整炉渣成分。
不用干渣,既可以节约焦炭,而且铁口见渣较晚,可以延长喷吹铁口时间,有利于加热炉缸。
1高炉配料计算

高炉炼铁主要经济技术指标 选定 (1) 高炉有效容积利用系数(v η)高炉有效容积利用系数即每昼夜生铁的产量与高炉有效容积之比,即每昼夜1m³有效容积的生铁产量。
可用下式表示:有V Pη=v 式中: v η——高炉有效容积利用系数,t /(m 3·d) P ——高炉每昼夜的生铁产量,t /d有V ——高炉有效容积,m 3V η是高炉冶炼的一个重要指标,有效容积利用系数愈大,高炉生产率愈高。
目前,一般大型高炉超过2.3,一些先进高炉可达到2.9。
小型高炉的更高。
本设计中取2.7。
(2) 焦比(K )焦比即 每昼夜焦炭消耗量与每昼夜生铁产量之比,即冶炼每吨生铁消耗焦炭量。
可用下式表示:式中 K ——高炉焦比,kg/tP ——高炉每昼夜的生铁产量,t /dK Q ——高炉每昼夜消耗焦炭量,kg/d焦比可根据设计采用的原燃料、风温、设备、操作等条件与实际生产情况进行全面分析比较和计算确定。
当高炉采用喷吹燃料时,计算焦比必须考虑喷吹物的焦炭置换量。
本设计中取K = 330 kg/t (3) 煤比(Y )冶炼每吨生铁消耗的煤粉为煤比。
本设计中取煤比为180 kg/t . (4) 冶炼强度(I )和燃烧强度(i )高炉冶炼强度是每昼夜31m 有效容积燃烧的焦炭量,即高炉每昼夜焦炭消耗量与有V 的比值, 本设计I =1.1 t/m 3∙d 。
燃烧强度i 既每小时每平方米炉缸截面积所燃烧的焦炭量。
本设计i = 30 t/m 2∙d 。
(5) 生铁合格率化学成分符合国家标准的生铁称为合格生铁,合格生铁占总产生铁量的百分数为生铁合格率。
它是衡量产品质量的指标。
(6) 生铁成本生产一吨合格生铁所消耗的所有原料、燃料、材料、水电、人工等一切费用的总和,单位为 元/t 。
(7) 休风率休风率是指高炉休风时间占高炉规定作业时间的百分数。
先进高炉休风率小于1%。
(8) 高炉一代寿命高炉一代寿命是从点火开炉到停炉大修之间的冶炼时间,或是指高炉相邻两次大修之间的冶炼时间。
高炉一般计算

高炉一般计算第一篇:高炉一般计算工作总结在繁忙的工作中不知不觉又迎来了新的季度,回顾前几个月的工作历程,在部门领导和同事们的关心与帮助下圆满的完成了生产任务,并在前辈师傅的授受中努力提高高炉冶炼理论知识,学习他们在工作中积累的丰富经验,为了更好地做好以后的工作,现将上季度学到的专业知识做如下总结:冶炼周期可以估计改变装料制度(如变料等)后渣铁成分、温度、流动性等发生变化的时间,从而及时注意观察、分析判断、掌握炉况变化动向;当高炉计划休风或停炉时,根据冶炼周期可以推测休风料到达时间,以便掌握休风或停炉的时机。
(1)用时间表示:t=24V有PV'(1-C)P=V有hη有t=24hη有V'(1-C)式中t——冶炼周期,h;V有——高炉有效容积,m3;P——高炉日产量,t/d;V’——1t铁的炉料体积,m3/t;C——炉料在炉内的压缩系数,大中型高炉C≈12%,小高炉C≈10%。
(2)用料批表示:生产中常采用由料线平面到达风口平面时的下料批数,作为冶炼周期的表达方法。
如果知道这一料批数,又知每小时下料的批数,同样可求出下料所需的时间。
VN=批(V矿+V焦)(1-C)式中N批——由料线平面到风口平面曲的炉料批数;V——风口以上的工作容积,m3;V矿——每批料中矿石料的体积(包括熔剂的),m3; V焦——每批料中焦炭的体积,m3。
通常矿石的堆积密度取2.0~2.2t/m3,烧结矿为1.6t/m3,焦炭为0.55t/m3,冶炼周期是评价冶炼强化程度的指标之一。
冶炼周期越短,利用系数越高,意味着生产越强化。
风口以上高炉工作容积的计算公式:V=V效—n/4(D²*H+d²*h)式中 V效——高炉有效容积,m³;D——炉缸直径,m H——铁口中心线至风口中心线的距离,m d——炉喉直径mh——高炉料线,m 理论出铁量的计算通过计算出铁量,可以检查放铁的好坏和铁损的情况,如发现差距较大时,应及时找出产生原因,尽快解决P理论出铁量=G矿石消耗量×Fe矿石品位×0.997/0.945 理论出渣量的计算渣量批=QcaO批//CaO渣安全容铁量计算安全容铁量=0.6×ρ铁×1/4πd2h h取低渣口中心线到铁口中线间距离,m ρ铁——铁水密度,7t/m3; d——炉缸直径,m 全焦冶炼实际入炉风量计算VB =0.933C焦×CΦ×K×P/﹙0.21+0.29f﹚×1440 式中VB——入炉实际风量,m³/min0.933——1kgC燃烧需要的氧量,m³/kg(0.21+0.29f﹚——湿空气含氧量,其中f为鼓风量湿分,%C焦——综合燃料含碳量,%CΦ——风口前燃烧的碳量占入炉量的比率,一般去65-75%,中小高炉取较小值K——综合燃料比,kg/tP——昼夜产铁量,t 根据碳平衡计算入炉风量(V风,m3)(1)风口前燃烧的碳量(C风,kg):由碳平衡得:C风=C焦+C煤+C料+C碎-C铁-C尘-C甲烷-Cd1224126012Fe还⋅rd+Si铁+Mn铁+P铁+bCO2⋅CO2熔5628556244bCO2——熔剂中CO2被还原的系数,本例为0.4。
高炉简易配料计算
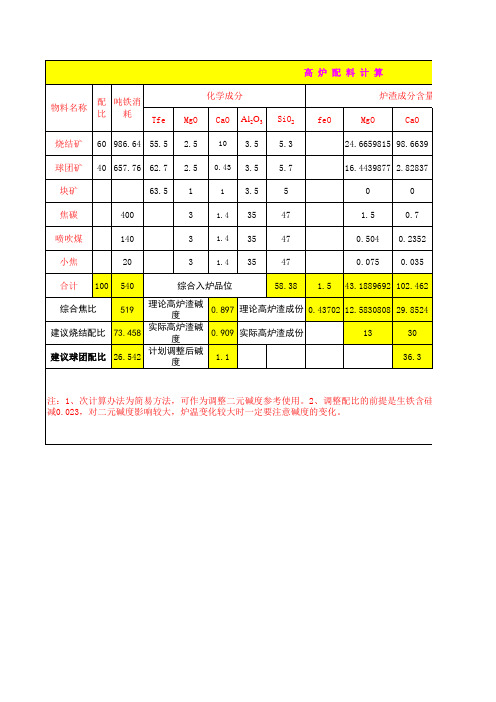
Al2O0 986.64 55.5 40 657.76 62.7 63.5
24.6659815 98.6639 16.4439877 2.82837 0 1.5 0.504 0.075 0 0.7 0.2352 0.035
综合入炉品位
43.1889692 102.462
高 炉 配 料 计 算 吨铁消 物料名称 配比 耗 烧结矿 球团矿 块矿 焦碳 喷吹煤 小焦 合计 100 400 140 20 540 519 化学成分 Tfe MgO 2.5 2.5 1 3 3 3 CaO
10 0.43 1 1.4 1.4 1.4
炉渣成分含量 SiO2 5.3 5.7 5 47 47 47 58.38 1.5 feO MgO CaO
炉渣成分含量 Al2O3 SiO2
吨铁渣 量
灰分
原料带 吨铁耗 入铁量 矿 547.585 412.415 0
34.5324 52.2919 23.0216 37.4923 0 17.5 5.88 0.875 81.809 0 23.5 7.896 1.175 114.27 343.23 生铁含硅量 12.5 12 12.5
综合焦比
理论高炉渣碱度 0.897 理论高炉渣成份 0.43702 12.5830808 29.8524 13 30 36.3
建议烧结配比 73.458 实际高炉渣碱度 0.909 实际高炉渣成份 建议球团配比 26.542 计划调整后碱度 1.1
注:1、次计算办法为简易方法,可作为调整二元碱度参考使用。2、调整配比的前提是生铁含硅不变 减0.023,对二元碱度影响较大,炉温变化较大时一定要注意碱度的变化。
1.6444
960 0.38
23.835 33.2925 20 33
高炉开炉配料自动计算表(专利)

7.30 20
0.00 0.00 0.87 7.30
45 45 45 45
总铁量 总渣量 渣铁比 正常料负荷 硫负荷 全炉焦比 226.8957 168.1047097 740.8899 2.164383562 3.658487 2.863431
渣碱度 及成分
212.18736 211.1264232 1.0609368 R2 0.886529628
MgO 批含量 0.000% 0 0.000% 0 3.000% 0.02616 1.470% 0.013532 0.039692
S 0.000% 0.000% 0.150% 0.820%
批含量
0 0 0.001308 0.007548346 0.008856346 (CaO+MgO)/(SiO2+Al2O3) 0.741313276 MgO 3.150% 1.630% 0.000% 0.000% 0.000% 批含量 0.3528 0 0.07009 0 0 0 0
45
586.112
22
447.503
汇 总 配 料 表
名称 烧结 矿烧 球团 澳矿 锰矿 海南矿 硅石 萤石 石灰石 焦炭 合计 入铁 入渣 参数计算
批重
批重
空焦 批数
24 24 24 24 24 24
Tfe 54.200% 0.000% 63.180% 0.000% 18.000% 0.000%
总重 145.6896 0 65.20176 0 1.296 0
8.84114 8.796934 0.044206 批铁量 渣量 渣铁比 参数计算 9.453986 4.02181317 425.4092
炉料分类 净焦
空焦 料 批 计 算 正常料
高炉开炉配料计算
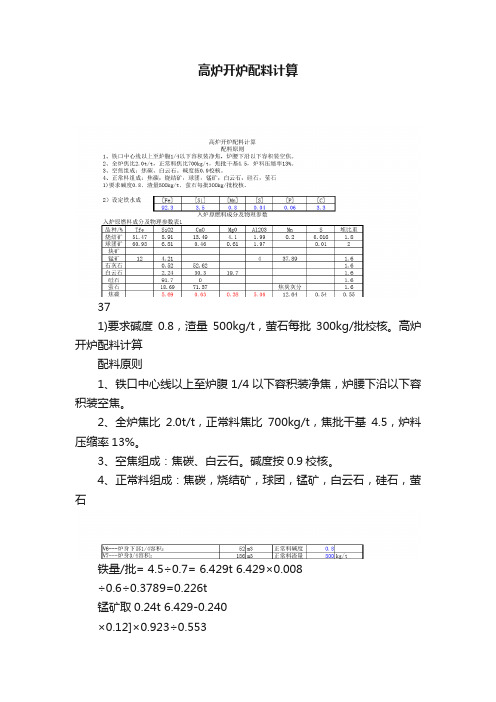
高炉开炉配料计算371)要求碱度0.8,渣量500kg/t,萤石每批300kg/批校核。
高炉开炉配料计算配料原则1、铁口中心线以上至炉腹1/4以下容积装净焦,炉腰下沿以下容积装空焦。
2、全炉焦比2.0t/t,正常料焦比700kg/t,焦批干基4.5,炉料压缩率13%。
3、空焦组成:焦碳、白云石。
碱度按0.9校核。
4、正常料组成:焦碳,烧结矿,球团,锰矿,白云石,硅石,萤石铁量/批= 4.5÷0.7= 6.429t 6.429×0.008÷0.6÷0.3789=0.226t锰矿取0.24t 6.429-0.240×0.12]×0.923÷0.553=10.691t混合矿取11t 焦炭: 4.5t 烧结矿: 6.6t 球团: 4.4t 锰矿:0.2t6.429×500= 3.214t锰矿量/批=混合矿量/批=[根据计算正常料批组成:上述计算的正常料炉渣成分校对见表2一批正常料需配渣量=配渣前炉渣成分表2配渣调整炉渣成分变化见表3硅石量=[ 2.239×(0.2369×0.8-0.4194)]÷0.917÷0.8=-0.702t0.702t 3.214- 2.883=0.332t 0.332×0.4073÷0.917=0.147t 0.147×0.917×0.8÷(0.5262-0.0052×0.8)=0.207t0.207×1×52.62÷30.300=0.359t 0.207×0.000=0.000t0.702+0.147=0.849t硅石取0.849t 石灰石取0t 白云石取0.359t焦炭:4.5t烧结矿: 6.6t配平碱度硅石量取需要配渣量=需配硅石量=需配石灰石量=正常料配硅石=配渣后的正常料组成:石灰石100%换成白云石=石灰石00%量=球团: 4.4t 锰矿:0.240t硅石:0.849t 石灰石:0t 萤石:0.3t 白云石:0.359t 6.6÷ 1.8+(0.240+0.849+0+0.3+0.359)÷1.6+ 4.4÷2+ 4.5÷0.55]×0.87=13.17m3/批R31.090.632)÷(30.3- 2.24×0.9)=0.714t0.714×0.5×30.3÷52.62=0.206t正常料体积=[正常料炉渣成分校对见表4空焦白云石0%换成石灰石=0.714×0.5=0.357t 白云石取0.714t 石灰石取0t 焦炭: 4.5t白云石:0.714t 石灰石:0t 4.5÷0.55+(0.714+0)÷1.6)×0.87=7.506m3=7.12m3/批空焦=7.506m3/批正常料=13.17m3/批69+41=110m3110÷7.118182=15.45批净焦取16.00批7.506X+13.17Y =3114.5×16+ 4.5×(X+Y)÷( 6.429×Y)=213.173Y+7.51X=311(3)开炉料组成空焦白云石100%量=空焦组成:空焦体积计算=((1)净焦批数:净焦容积为炉腹1/4以下容积;净焦容积=V3+1/4V4=净焦批数=(2)空焦与正常料设X——空焦 Y——正常料列方程为:整理方程得:8.357143Y - 4.5X =72110.0858Y +62.73222X =2599.071110.0858Y-59.27696X =948.4313X=13.53批正常料取16批Y=15.90批空焦取13批61.5m3加空焦=61.5÷7.506=8.19批取8.00批3OC+Cn 3OC+Cn 3OC+Cn 7OC+2cn死铁层+16C +8Cn ++++7OC+2cn202.5÷( 6.429×16)= 1.97t/t7.118182×16+7.506×13+13.17×16=422.237m3422.2369÷421=100.29%全炉开炉料按排:3OC+Cn解方程:空焦与正常料按排:炉腹3/4容积3/4V4=其余炉身和炉喉的容积炉料按排:3OC+Cn 3OC+Cn 其中:C——为净焦;Cn——为空焦;OC——正常料。
- 1、下载文档前请自行甄别文档内容的完整性,平台不提供额外的编辑、内容补充、找答案等附加服务。
- 2、"仅部分预览"的文档,不可在线预览部分如存在完整性等问题,可反馈申请退款(可完整预览的文档不适用该条件!)。
- 3、如文档侵犯您的权益,请联系客服反馈,我们会尽快为您处理(人工客服工作时间:9:00-18:30)。
810m3高炉开炉料计算810m高炉开炉料计算开炉工作有两个方面的要求:一是安全顺利地完成开炉工作,即做到炉温适中,铁口易开,下料顺畅,并且无人身、设备事故:二是在开炉后能较快平稳地过渡到正常生产,以获得较好的经济效益。
为此开炉时应该使炉内各区域适时地达到所需要的温度,故开炉料的选择,开炉焦比的确定,以及炉段的安排至关重要。
36.1 开炉焦比的选择所谓开炉焦比(总焦比是指开炉料的总焦量与理论出铁量之比。
开炉时由于高炉炉衬温度、料柱的温度都很低,炉料未经充分的预热和还原直接到炉缸,直接还原增多,渣量打,需要消耗的热量也多,所以开炉焦比要比正常焦比高几倍。
具体数值应该根据高炉容积大小,原燃料条件、风温高低、设备状况及技术操作水平等因素进行选择。
一般情况见表6-1:表6-1 开炉焦比的选择炉容/m 焦比/t?t铁?13100以下 >4100-500 3-4500-1000 2.5-31000以上 <2.6选择合适的开炉焦比对开炉进程有决定性的影响。
焦比选择过高,既不经济,又可能导致炉况不顺,即导致高温区上移,在炉身中上部容易产生炉墙结厚现象,更严重的是延长了开炉时间;焦比选择过低,会导致炉缸温度不足,出渣出铁困难,渣铁流动不畅,严重时会造成炉缸冻结。
一般要求开炉前几次含硅量为3%-3.5%。
6.2 开炉造渣制度的选择为了改善渣铁流动性能,冶炼合格生铁,加热炉缸,稀释渣中的Al2O3(Al2O3含量大于18%时,开炉配料中需增加低Al2O3的造渣剂),开炉时渣量要大一些,渣铁比一般为0.4-0.5.如渣量小,可加干渣调节。
开炉时炉渣碱度SiO2?0.90-1.05。
控制生铁含?Mn?0.8%,为了改善炉渣流动性,可提高渣中的MgO含量,使之维持在8%-10%左右,也可适当加些萤石来稀释炉渣。
小高炉在用全天然矿冷风开炉时,焦比特高,可在空料(即焦炭+石灰石)段加些硅石来调整炉渣成分。
不用干渣,既可以节约焦炭,而且铁口见渣较晚,可以延长喷吹铁口时间,有利于加热炉缸。
开炉焦比高,硫负荷就会随之增大,此时炉渣碱度(CaOSiO2)不宜低于正常时的下限,同时还可以选用含硫较低的开炉料。
6.3 开炉配料计算6.3.1计算条件(1)高炉各部位的容积(2)开炉使用的原料、燃料、熔剂等的化学成分、体积密度。
(3)选定开炉焦比与正常料焦比。
(4)确定炉缸的填充方法。
(5)选定铁、锰、硫等元素在渣铁、煤气中的分配率。
(6)选定生铁成分与炉渣碱度,一般要求渣中Al2O3含量不大于18%。
(7)确定开炉料使用料种之间的比例。
(8)选定焦炭或矿石的批重。
6.3.2选定数据全焦填充,炉缸装净焦(C),炉腹以上装空料(x),炉腰上部1/3容积开始过渡至装正常聊(N)。
料线1.75m。
炉料压缩率15%(炉缸净焦19%,炉腹空料16%,其余13%)。
填充容积(已扣除料线以上空间及铁口泥包):表5-1 填充容积部位炉喉 36炉身 447炉腰 75炉腹 135炉缸 112死铁 48.6合计 853.6开炉料成分及其它数据:表5-2 开炉料成分(%)FeSiO2CaOMgOMnAl2O3SP堆密度t/m3烧结矿锰矿石灰石焦炭52.55 16.9 0.6111.04 19.21 1.02 6.3211.09 0.55 51.08 0.681.09 0.322.82 0.190.16 25.240.95 2.01 0.03 4.730.03 0.17 0.630.01 0.42 0.01 0.0051.6 1.9 1.52 0.45焦炭工业分析:灰分14.18%,挥发分0.94%,硫0.63%,水分4.4% 焦炭强度:M4078%, M108% 预订生铁成分,表5-3预定生铁成分,%Fe Si Mn P S 92.67 2.5 0.5 0.04 0.05铁的回收率 99.6%,锰的回收率60%焦炭批重9000Kg/批,总焦比2.5,正常焦比0.9 (每批出铁10000Kg)炉渣碱度CaO/SiO2=1.0C 4.01)以铁和猛的平衡列方程解出正常料的烧结矿和锰矿的批重:设:x—―烧结矿批重,Kg;y—―锰矿批重,Kg;Fe烧、Fe锰、Fe焦—―分别为烧结矿、锰矿、焦炭的含铁量,%; Mn烧、Mn锰—―分别为烧结矿、锰矿的含锰量,%。
列方程(x·Fe + y·Fe锰 + 焦炭批重×Fe焦)×铁的回收率=每批出铁量生铁含Fe(x·Mn烧 + y·Mn锰)×锰的回收率=每批出铁量×生铁含Mn (145)99.6??(0.5255x?0.169y?9000?0.0061)??10000即 ? 92.67??0.6?10000?0.005?(0.0016x?0.2524y)解方程得 x=17543 y=218.8取烧结矿批重为17500kg,锰矿批重为220kg。
2)每批正常料的石灰石用量:已知原燃料带入 SiO2,,kg CaO,kg烧结矿带入 17500×0.1104=1932 17500×0.1109=1940.8 (146)锰矿带入 220×0.1921=42.3 220×0.0055=1.2 焦炭带入 9000×0.0632=568.8 9000×0.0068=61.2 合计 2543.1kg 2003.2kg生铁含Si消耗SiO2 10000×0.025×60=535.7kg (147) 进入渣中28的SiO2 2543.1-535.7=2007.4kg (148)渣碱度 1.0,尚需CaO 2007.4-2003.2=4.2kg (149) 石灰石有效CaO 51.08-1.02=50.06% (150) 每批正常料需要的石灰石量 4.2÷0.5006=8.4kg (151)为取料方便,每6批正常料取石灰石1次,每次量50kg。
3)每批石灰石用量:取值1000kg/批568.8?61.2=1014kg (152)0.50064)每批净焦、空料、正常料的体积:9000×0.81=16.2m3/批 (153) 45090001000?)?0.84=17.353m3/批 (154) 空料Ⅰ(炉腹) (450152090001000?)?0.87=17.972m3/批 (155) 空料Ⅱ(炉腰上部以上) (45015209000175002208.4???)?0.87=27.021m3/批 (156) 正常料 (450160019001520净焦(炉缸)5)炉缸(包括死铁层空间)填充用净焦批数:48.6?112?=9.9取10批 (157)16.26)炉腹及炉腰下部2/3容积装空料批数;(135?75?)?17.353=10.7 取11批 (158)237)按照总焦比和炉腰上部以上至料线的容积来计算空料和正常料的批数:设:x1—正常料批数;13y1—空料批数。
列方程 x1×正常料体积+y1×空料体积=炉吼+炉身+1 32焦炭批重?(炉缸?炉腹?炉腰等空间已填充批数)?焦炭批重?(x1?y1)3 x1?每批正常料出铁量=总焦比1?27.021x?17.972y?36?447??7511??3即 ? (159)(910?11)?(9x1?y1)?2.5??10x1?解方程得 x1=15.01 y1=5.6取值:正常料为15批空料为6批其分配为:①炉腰上部1及炉身下部装空料4批及正常料4批,本段计算焦比为2.087 t焦/t铁;3加上其下的空料11批空料,计算焦比为4.21t焦/t铁。
②炉身中部装空料2批及正常料11批,本段计算焦比为1.348 t焦/t铁。
③炉身上部及炉喉装正常料装料制度COOC↓至料线1.75m为止。
为使炉缸热量充沛,且经高炉解剖研究证实,正常生产时炉腰以下几乎全被焦炭填充,不应有未还原矿石,所以开炉装料时含有矿石的正常料应装在炉腰以上。
9)校核:根据以上计算列出校核表如表8-7. 序号装料部位内容体积m1死铁层及炉缸10C 11X3(2x+n)+6(x+n)=12X+9N8(x+2n)=8X+16N10N 11C+31X+35N=97 41x+35N=76 160.6 1853炉料构成,t焦炭石灰石烧结矿锰矿 189 234 26出铁量 t焦比 t焦/t铁1.244 1.5402 炉腹及2/3炉腰1/3炉腰及炉身下部炉身中部3 174 162 9.076 157.5 1.98 90.377 2.0874 149 185 853.6198 90 873 6846.314 0.084 41.474 41.474280.0 175.0 612.5 612.53.52 2.20 7.70 7.70160.081 99.829 353.06 351.881.348 0.9022.473 1.9695 炉身上部及炉喉6 7合计不计净焦表8-7 开炉料计算校核(续表)序号 1进入生铁,t Si,折成SiO2S 0.045 0.080 0.050 0.175P 0.012 0.035 0.062 0.031 0.140SiO2 12.669 24.985 36.740 20.083 94.477 CaO进入炉渣,t MgOAl2O3 9.372MnOS 1.247 1.221 1.371 0.573 4.412渣碱度Cao/SiO2 0.993 0.998 0.999 0.999 0.998渣量 t 38.869 64.247 92.149 49.213 242.6582 0.0693 4.5814 8.5825 5.348 67 18.8512.584 0.99724.931 2.423 10.479 0.388 36.695 3.703 12.950 0.690 20.074 2.0885.9640.43194.284 9.211 38.765 1.509注:1.不计净焦的渣铁比:242.658/351.88=0.690;2.硫负荷:(0.175+4.412)/351.88=13.03kg/t铁;炉渣含硫:(4.412/242.658)×100=1.82% 3.生铁含磷:(0.14/351.88)×100=0.04% 4.炉渣含Al2O3:(38.765/242.658)×100=15.98% 5.总开炉焦比2.473,正常料焦比0.902高炉内型参数序号 1 2 3 4 5 6 7 8 9 10 11 12 13 14 15 16项目有效容积Vu/m 炉缸直径d/mm 炉腰直径D/mm 炉喉直径d1/mm 死铁层深度h0/mm 炉缸高度h1/mm 炉腹高度h2/mm 炉腰高度h3/mm 炉身高度h4/mm 炉喉高度h5/mm 有效高度Hu/mm 炉腹角α炉身角β Hu/D铁口数/个风口数/个3数值 800 6900 8000 5600 13003500 3100 1500 12200 1500 27000 80° 84.4° 2.725 1(夹角90°) 16。