铜渣的处理与资源化
铜矿废弃物资源化利用技术研究

研究挑战:铜矿废弃物资 源化利用技术需要解决一 系列技术难题,如废弃物 成分复杂、处理成本高等。
03
铜矿废弃物资源化利用技术的方法和原理
铜矿废弃物资源化利用的主要方法
生物浸出法:利用微生物将铜矿废弃物中的铜元素转化为可溶性铜离子
化学浸出法:使用酸、碱等化学试剂将铜矿废弃物中的铜元素溶解出来
电化学浸出法:利用电化学反应将铜矿废弃物中的铜元素提取出来
政策建议和社会参与
政府出台相关政策,鼓励企业采用铜矿废弃物资源化利用技术
建立铜矿废弃物资源化利用技术研发中心,推动技术创新和成果转化
加强社会宣传,提高公众对铜矿废弃物资源化利用技术的认识和接受度
鼓励企业与高校、科研机构合作,共同推进铜矿废弃物资源化利用技术的研技术实施过程中的问题和解决方案
添加标题
问题:废弃物成分 复杂,处理难度大
添加标题
解决方案:采用先 进的分离技术和设 备,提高处理效率
添加标题
问题:废弃物中含 有有害物质,对环 境造成污染
添加标题
解决方案:采用环 保技术,减少有害 物质的排放
添加标题
问题:废弃物资源 化利用成本高
添加标题
解决方案:优化工 艺流程,降低生产 成本
添加标题
问题:废弃物资源 化利用技术推广难 度大
添加标题
解决方案:加强政 策支持和宣传推广, 提高社会认知度
技术应用的优缺点和经济效益分析
优点:减少环 境污染,提高 资源利用率, 降低生产成本
缺点:技术难 度大,投资成 本高,回收率
低
经济效益分析: 回收铜矿废弃物 可以带来一定的 经济效益,但需 要综合考虑技术 难度和投资成本
铜矿废弃物的产生和危害
铜矿开采过程中产生的废石、废渣等废弃物 铜矿冶炼过程中产生的废气、废水、废渣等废弃物 铜矿废弃物对环境的危害:污染土壤、水源、空气,影响生态环境和人类健康 铜矿废弃物对资源的浪费:大量有价值的金属元素未被充分利用,造成资源浪费
铜渣处置现状分析报告

铜渣处置现状分析报告1. 引言1.1 概述铜渣是在铜冶炼过程中产生的一种废弃物,其处理方式直接影响着环境保护和资源利用的效率。
本报告旨在分析当前铜渣的处理现状,探讨铜渣处理方法的优劣以及对铜渣处理效果进行评估。
通过对铜渣产生情况、处理方法和效果进行全面调研和分析,旨在为相关冶炼企业提供科学、可行的处理对策和建议,实现对铜渣资源的高效利用和环境保护的双赢局面。
1.2 文章结构文章结构部分的内容:本报告主要分为三个部分,包括引言、正文和结论。
引言部分主要概述了铜渣处理的背景和重要性,介绍了本报告的结构和目的,为读者提供了对报告整体内容的预览。
正文部分包括铜渣产生情况、铜渣处理方法和铜渣处理效果评估三个重要内容,通过对现有情况的调研和分析,展现了铜渣处理的现状和问题。
结论部分对正文部分进行了综合分析,总结了目前铜渣处理的现状,并提出了对策建议,为进一步改善铜渣处理提供了指导和参考。
1.3 目的目的部分的内容可以包括对本报告的写作目的和目标的详细描述。
目的是为了分析当前铜渣处置的现状,并评估其处理效果,从而找出存在的问题和不足之处。
同时也为了提出合理的对策建议,以改善铜渣处理方法,提高铜渣处理效果,并推动铜渣处置行业的可持续发展。
通过本报告,希望为相关部门和企业提供参考,促进铜渣处置行业的规范化和升级。
2. 正文2.1 铜渣产生情况铜渣是指在冶炼、熔炼和精炼铜过程中产生的固体废渣,主要包括氧化铜、硫化铜、铁、砷、锑等金属成分,以及一定量的非金属氧化物、硅酸盐、硼酸盐和钠钾盐等。
铜渣的产生与铜冶炼的规模和生产工艺有关,通常来自铜矿的选矿、浮选、冶炼等过程,同时也包括电解和铸造等环节。
随着铜冶炼产能的不断扩大和技术的不断进步,铜渣的产生量也在不断增加。
据统计,中国每年产生的铜渣数量巨大,尤其是在重化工业基地和铜冶炼中心地区,铜渣的产生量相当可观,给环境保护和资源综合利用带来了一定的压力。
因此,对铜渣产生情况的深入了解和分析,有利于科学合理地处理和利用铜渣,减少对环境的影响,实现资源的循环利用。
铜冶金固体废物的综合利用

铜冶金固体废物的综合利用冶金行业的铜渣主要来自于火法炼铜的过程,包括采矿过程中废石、冶炼过程中的废渣和尾矿渣。
其他的铜渣则是炼锌、炼铅过程中的副产物。
铜渣含有铜、锌等重金属和金、银等贵金属。
目前,我国的粗铜年产量为52万吨左右,产出的炉渣约为150万吨,再加上副产废铜渣,数量巨大。
这些固体废物大量堆积,不仅侵占了土地、污染了环境,而且这些废渣含有的大量的有用物质没有被充分利用。
目前,铜渣的利用方法很多,利用率也较高,主要包括提取有价金属、生产化工产品和建筑材料等。
1.化学组成铜渣由于炼铜原料的产地、成分以及冶炼的方法的不同,其组成具有较大的差异性。
表13-5所示为铜渣的化学组成。
由表13-5中数据可知,铜渣中铁的含量很高,还含有Cu、Pb、Zn、Cd等金属,具有回收金属元素的价值,铜渣中的主要矿物包括硅酸铁、硅酸钙、少量的硫化物和金属元素等。
在提取有价金属后,可以作为水泥的原料。
2.粒度组成水淬铜渣颗粒形状不规则,尺寸也不同。
有个别滤渣状多孔颗粒和细针状颗粒。
粒径组成略大于普通沙的一级配区。
如表13-6。
一、含铜废渣中回收铜根据美国国家地质调查局(USGS)发布的NERAL COMMODITY UMMARIES 2012显示:截至2011年年底,全球铜储量为6.9亿吨,智利以1.9亿吨的铜储量居于全球首位,中国以3000万吨位居全球第五。
但我国主要以贫矿为主,且开发程度不高。
而我国铜消耗量在逐年增长,精炼铜和矿山铜(精矿)多年来供不应求。
自给率仅为65%左右,长期靠进口弥补。
因此,一些低品位矿、尾矿、表外矿及含铜矿渣等难以开采和洗选矿脉的开发利用,不仅能满足铜的需求,还能减少废渣对环境造成的危害,能产生巨大的社会和环境效益。
为了回收铜渣中的铜,研究人员将难选的氧化铜矿类矿渣经过氨浸、蒸馏、酸化和结晶等工艺流程后得到五水硫酸铜产品。
在实验中探讨了氨浸的机制,研究了铜浸出率的主要影响因素,确定了最佳的浸出液配比,得出了氨浸、蒸氨、酸化、浓缩和结晶过程中的工艺条件,为难选氧化铜类矿石及其废渣中回收铜提供了有效的方法和基本工艺参数。
铜渣综合回收利用研究进展
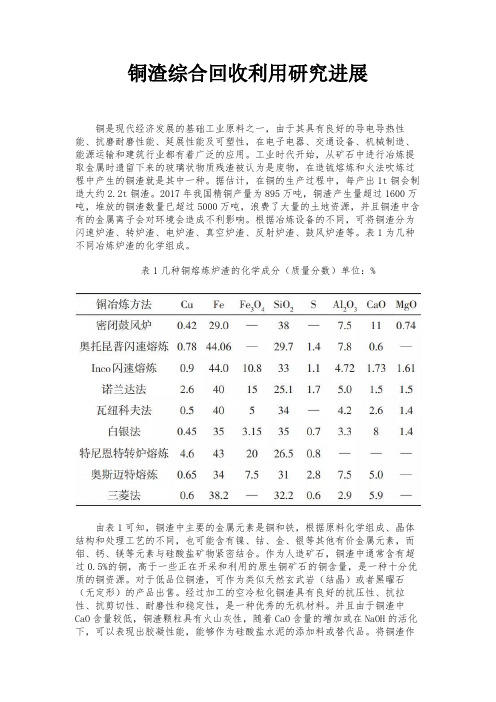
铜渣综合回收利用研究进展铜是现代经济发展的基础工业原料之一,由于其具有良好的导电导热性能、抗磨耐磨性能、延展性能及可塑性,在电子电器、交通设备、机械制造、能源运输和建筑行业都有着广泛的应用。
工业时代开始,从矿石中进行冶炼提取金属时遗留下来的玻璃状物质残渣被认为是废物,在造锍熔炼和火法吹炼过程中产生的铜渣就是其中一种。
据估计,在铜的生产过程中,每产出1t铜会制造大约2.2t铜渣。
2017年我国精铜产量为895万吨,铜渣产生量超过1600万吨,堆放的铜渣数量已超过5000万吨,浪费了大量的土地资源,并且铜渣中含有的金属离子会对环境会造成不利影响。
根据冶炼设备的不同,可将铜渣分为闪速炉渣、转炉渣、电炉渣、真空炉渣、反射炉渣、鼓风炉渣等。
表1为几种不同冶炼炉渣的化学组成。
表1几种铜熔炼炉渣的化学成分(质量分数)单位:%由表1可知,铜渣中主要的金属元素是铜和铁,根据原料化学组成、晶体结构和处理工艺的不同,也可能含有镍、钴、金、银等其他有价金属元素,而铝、钙、镁等元素与硅酸盐矿物紧密结合。
作为人造矿石,铜渣中通常含有超过0.5%的铜,高于一些正在开采和利用的原生铜矿石的铜含量,是一种十分优质的铜资源。
对于低品位铜渣,可作为类似天然玄武岩(结晶)或者黑曜石(无定形)的产品出售。
经过加工的空冷粒化铜渣具有良好的抗压性、抗拉性、抗剪切性、耐磨性和稳定性,是一种优秀的无机材料。
并且由于铜渣中CaO含量较低,铜渣颗粒具有火山灰性,随着CaO含量的增加或在NaOH的活化下,可以表现出胶凝性能,能够作为硅酸盐水泥的添加料或替代品。
将铜渣作为一种材料进行资源化利用,可以降低材料生产成本。
倾倒或堆放这些炉渣会造成金属价值的浪费,并导致环境问题。
这些炉渣可以充分利用其物理化学性质进行资源化利用,而不是随意堆放或者丢弃。
因此,一些研究者对铜渣的资源化进行了探索,开发出了多种利用方式,如回收有价金属、生产水泥、砂浆、填料、道砟、磨料、骨料、玻璃、瓷砖等。
金属冶炼副产物的综合利用与资源化
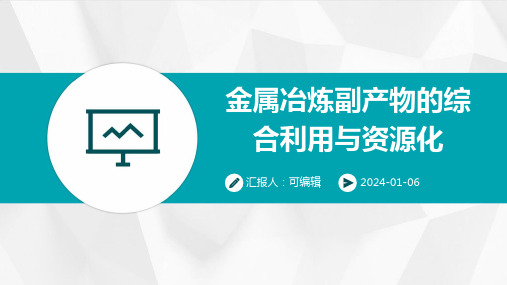
副产物的材料化利用
制备建筑材料
一些金属冶炼副产物可以经过加工处理后,用于制备建筑材料,如水泥、砖瓦等 。这些建筑材料具有较好的耐久性和稳定性,能够满足各种建筑需求。
制作复合材料
通过将金属冶炼副产物与其他材料复合,可以制备出性能优异的复合材料。这些 复合材料具有轻质、高强、耐腐蚀等优点,广泛应用于航空、汽车、化工等领域 。
案例二:某铜冶炼企业副产物的资源化利用
• 总结词:该铜冶炼企业通过技术升级和改造,实现了副产物的资源化利 用,提高了企业的经济效益和环保水平。
• 详细描述:该铜冶炼企业在生产过程中产生了大量的铜渣等副产物。为了充分利用这些副产物,该企业进行了一系列的 技术升级和改造。首先,他们采用先进的浮选和重选技术,从铜渣中回收了大量的铜和铁元素,并制成高附加值的铜铁 合金和阳极铜等产品。其次,他们将部分铜渣进行高温熔炼处理,提取出有价值的元素,如锌、铅等,并制成相应的金 属制品或合金材料。此外,该企业还通过其他方式对副产物进行资源化利用,如将部分铜渣用作建筑材料、生产水泥等 。
案例三:某铝冶炼企业副产物的能源化利用
• 总结词:该铝冶炼企业通过将副产物进行高温焚烧处理,转化为具有高能值的燃料或气体,实现了资源的有效 利用和能源的节约。
• 详细描述:该铝冶炼企业在生产过程中产生了大量的铝灰等副产物。为了充分利用这些副产物,该企业将其进行高温焚烧处理,转化为具有高能值的燃料或气体。这些燃料或气体可以 用于企业的热力供应或进一步转化为电能,为企业提供可观的能源供应。同时,该企业还将部分铝灰进行回收和再利用,从中提取出有价值的元素,如铁、硅等,并制成相应的金属制 品或非金属材料。通过这种能源化利用方式,该企业不仅实现了资源的有效利用和能源的节约,还降低了对环境的影响。
重金属冶炼废渣的处理与资源化利用

破碎法
将废渣破碎成小块或粉末,以便于 后续处理。
筛分法
根据废渣中不同粒度的颗粒进行分 类,分离出不同粒度的物质。
化学处理法
酸处理法
利用酸溶解废渣中的重金属,将 其从废渣中分离出来。
氧化还原法
通过氧化或还原反应将废渣中的 重金属转化为稳定或无害的形态
。
沉淀法
向废渣中加入沉淀剂,使重金属 离子转化为沉淀物,分离出重金
国际案例
介绍了美国、欧洲等发达国家在重金属废渣处理与资源化利用方面的成功案例,如某著名 钢铁企业的废渣处理项目、某知名科研机构的资源化利用研究成果等。
经验总结
总结了国际上在重金属废渣处理与资源化利用方面的成功经验,包括政策支持、技术创新 、产业链合作等方面。同时,也指出了我国在这一领域存在的差距和不足之处。
制作有机肥料
将废渣堆肥处理后制成有机肥料,提供植物所需的营养元素。
降低农业污染
合理利用废渣,减少化肥和农药的使用量,降低农业面源污染。
05 重金属冶炼废渣 处理与资源化利 用的挑战与前景
当前面临的主要挑战
处理难度大
重金属冶炼废渣含有多 种有毒有害物质,处理 过程复杂,技术难度高
。
环境风险高
废渣中重金属易溶出, 对土壤、水源和生态系
重金属冶炼废渣的处理与资 源化利用
contents
目录
• 引言 • 重金属冶炼废渣的来源与特性 • 重金属冶炼废渣的处理技术 • 重金属冶炼废渣的资源化利用 • 重金属冶炼废渣处理与资源化利用的挑
战与前景 • 案例研究
01 引言
研究背景
工业发展导致重金属 冶炼废渣大量产生
资源化利用是解决废 渣问题的有效途径
废渣的环境影响
铜冶炼渣的资源化利用
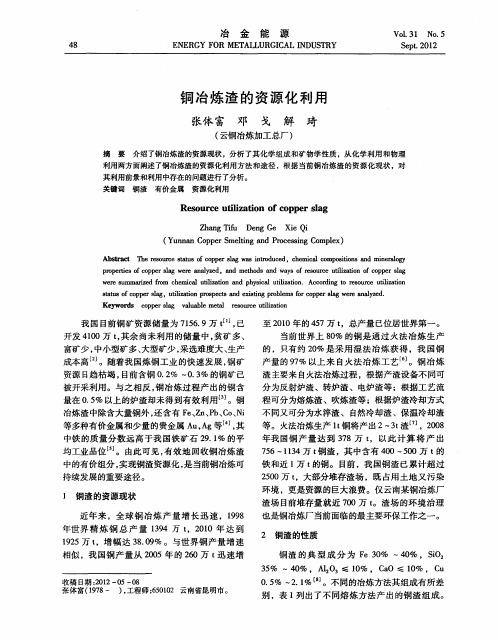
Z agTf D n e X eQ hn i e gG i i h
( u n nC p e me iga dPoes gC m l ) Y n a op rS ln n rcsi o pe t n x
Ab ta t Th e o r e sau fc p e 1g wa n r d c d,c e c l c mp st n n n r o y sr c e rs u c tt s o o p r s s i t u e a o h mia o o i o s a d mi e a g i l p o r e fc p rsa r n y e rp t s o o p lg wee a a z d,a d me h d n a s o s u c t z f n o o p r sa e i e l n t o s a d w y f r o re u H a o c p lg e i i f e
5 %降低到 03 % 以下。王学文等¨ 人在真空条 .5 训
件 下研究 了真空 度 、温度 、处理 时间 、渣型 及添
z 等 用 “ a 氧化浸出 一 萃取”法从铜渣 中回收
有价金属 ,在常压下用 H s . H O 混合溶液 2O 和 2 2 对铜渣进行氧化浸 出,再用萃取剂分步萃取浸 出 液 得到有 价 金 属 ,C 、C Z u O n回收 率 分 别 达 到 8 %、9 %、9 %。蒋镜宇等人采用碳铵 一 0 0 0 氨水 体系浸取黄铜熔 炼渣 ,黄铜熔炼渣经稀碱洗 涤 后 ,在碳铵 一 氨水体系中浸出,铜、锌的浸出率
形玻璃体 引,其 中铜主要 以辉铜矿 ( uS 、金 C:)
表 1 典型熔炼炉渣的化 学成分
3 铜渣 的资源 化利 用
间 2 , 属铜 的 回收率 达到 8 % 以上 。 h金 5
铜渣综合利用的研究情况与难点及新技术论文
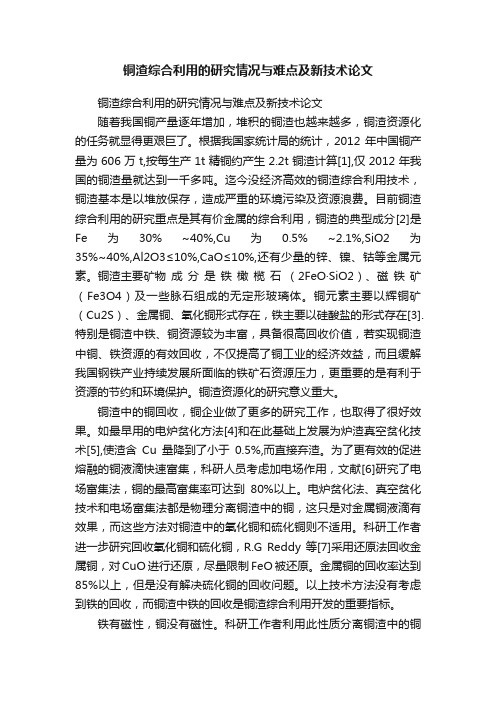
铜渣综合利用的研究情况与难点及新技术论文铜渣综合利用的研究情况与难点及新技术论文随着我国铜产量逐年增加,堆积的铜渣也越来越多,铜渣资源化的任务就显得更艰巨了。
根据我国家统计局的统计,2012年中国铜产量为606万t,按每生产1t精铜约产生2.2t铜渣计算[1],仅2012年我国的铜渣量就达到一千多吨。
迄今没经济高效的铜渣综合利用技术,铜渣基本是以堆放保存,造成严重的环境污染及资源浪费。
目前铜渣综合利用的研究重点是其有价金属的综合利用,铜渣的典型成分[2]是Fe为30% ~40%,Cu为0.5% ~2.1%,SiO2为35%~40%,Al2O3≤10%,CaO≤10%,还有少量的锌、镍、钴等金属元素。
铜渣主要矿物成分是铁橄榄石(2FeO·SiO2)、磁铁矿(Fe3O4)及一些脉石组成的无定形玻璃体。
铜元素主要以辉铜矿(Cu2S)、金属铜、氧化铜形式存在,铁主要以硅酸盐的形式存在[3].特别是铜渣中铁、铜资源较为丰富,具备很高回收价值,若实现铜渣中铜、铁资源的有效回收,不仅提高了铜工业的经济效益,而且缓解我国钢铁产业持续发展所面临的铁矿石资源压力,更重要的是有利于资源的节约和环境保护。
铜渣资源化的研究意义重大。
铜渣中的铜回收,铜企业做了更多的研究工作,也取得了很好效果。
如最早用的电炉贫化方法[4]和在此基础上发展为炉渣真空贫化技术[5],使渣含Cu量降到了小于0.5%,而直接弃渣。
为了更有效的促进熔融的铜液滴快速富集,科研人员考虑加电场作用,文献[6]研究了电场富集法,铜的最高富集率可达到80%以上。
电炉贫化法、真空贫化技术和电场富集法都是物理分离铜渣中的铜,这只是对金属铜液滴有效果,而这些方法对铜渣中的氧化铜和硫化铜则不适用。
科研工作者进一步研究回收氧化铜和硫化铜,R.G Reddy等[7]采用还原法回收金属铜,对CuO进行还原,尽量限制FeO被还原。
金属铜的回收率达到85%以上,但是没有解决硫化铜的回收问题。
- 1、下载文档前请自行甄别文档内容的完整性,平台不提供额外的编辑、内容补充、找答案等附加服务。
- 2、"仅部分预览"的文档,不可在线预览部分如存在完整性等问题,可反馈申请退款(可完整预览的文档不适用该条件!)。
- 3、如文档侵犯您的权益,请联系客服反馈,我们会尽快为您处理(人工客服工作时间:9:00-18:30)。
铜渣的处理与资源化
1、铜渣中含有大量的可利用的资源
现代炼铜工艺侧重于提高生产效率,渣中的残余铜含量增加,回收这部分铜资源是现阶段处理铜冶炼渣的主要目的。
当然,渣中的大部分贵金属是与铜共生的,回收铜的同时也能回收大部分的贵金属。
渣中的主要矿物为含铁矿物,铁的品位一般超过40%,远大于铁矿石29.1%的平均工业品位。
铁主要分布在橄榄石相和磁性氧化铁矿物中,可以用磁选的方法得到铁精矿。
显然,针对铜渣的特点,开展有价组分分离的基础理论研究,开发出能实现有价组分再资源化的分离技术,为含铜炉渣再资源产业化提供技术依据,对国民经济和科技发展具有重要的现实意义。
2、铜渣的工艺矿物学特征
随着铜冶金技术的不断发展,传统的炼铜技术包括鼓风炉熔炼,反射炉熔炼和电炉熔炼正在逐渐被闪速熔炼取代,与此同时,与上述二次熔炼的方法不同的所谓一步熔炼出粗铜的熔池熔炼方法,如诺兰达法、瓦纽科夫法、艾萨法也逐步受到人们的重视。
冶炼厂转炉、闪速熔炼等含铜较高的炉渣(尤其是含砷等有害元素较高的炉渣),返回处理困难,这些物料往往需要开路处理。
炼铜炉渣主要成分是铁硅酸盐和磁性氧化铁.铁橄榄石(2FeO ·SiO2)、磁铁矿(Fe3O4)及一些脉石组成的无定形玻璃体。
机械夹带和物理化学溶解是金属在渣中的两种损失形态。
一般而言,铜在渣中的损失随炉渣的氧势、锍品位、渣Fe/SiO2比增大而增大。
熔炼渣中的铜主要以冰铜或单纯的辉铜矿(Cu2S)状态存在.几乎不含金属铜.多见铜的硫化物呈细小珠滴形态不连续分布在铁橄榄石和玻璃相间。
而吹炼渣中存在少量金属铜.在含铜高的炉渣中,Cu,S含量也随之增大。
机械夹带损失的有价金属皆因冶炼过程中大量生成Fe3O4,致使炉渣粘度提高,渣锍比重差别减小.使渣锍无法有效分离。
3、铜渣的火法贫化
返回重熔和还原造锍是铜渣火法贫化的主要方式。
炉渣返回重熔
是回收铜的传统方法,产生的冰铜返主流程。
针对炉渣的钴、镍回收,采取在主流程之外的单独还原造锍。
炉渣贫化方法很多,选择哪一种方法取决于现场条件,如资金、场地、副产品、杂质等。
显然,熔炼工艺是确定炉渣贫化工艺技术的主要因素,因为炉渣的特性取决于熔炼技术。
随着技术的进步,一些新的贫化方式也不断出现。
(1)反射炉贫化炼铜渣
反射炉是过去长时间使用的炉渣贫化法,炉顶采用氧/燃喷嘴的反射筒形反应器来贫化炉渣。
将含铜和磁性氧化铁矿物高的炉渣分批装入反应器内。
第一步是通过风口喷粉煤、油或天然气进入熔池,还原磁性氧化铁矿物,使渣中磁性氧化铁矿物含量降低到10%。
这一步与火法精炼铜的还原阶段相似,降低了炉渣的粘度。
第二步停止喷吹,让熔融渣中冰铜和渣分离。
这种方法至今仍在日本小名浜冶炼厂、智利的卡列托勒斯炼铜厂应用。
(2)电炉法
用电炉贫化可以提高熔体温度,使渣中铜的含量降到很低,有利于还原熔融渣中氧化铜、回收熔渣中细颗粒的铜粒子。
电炉贫化不仅可处理各种成分的炉渣,而且可以处理各种返料。
熔体中电能在电极间的流动产生搅拌作用,促使渣中的铜粒子凝聚长大。
(3)真空贫化法
杜清枝等开发炉渣真空贫化技术,使诺兰达富氧熔池炉渣1/2—2/3的渣层含铜量从5%降到0.5%以下。
真空贫化的优点在于:迅速消除或减少Fe 0 的含量,降低渣的熔点、粘度和密度,提高渣一锍间的界面张力,促进渣—锍的分离。
真空有利于迅速脱除渣中的SO:气泡,由于气泡的迅速长大、上浮,对熔渣起着强烈的搅拌作用,增大了锍滴碰撞合并的几率。
主要存在问题是成本较高,操作比较复杂。
(4)渣桶法¨
用渣桶作为额外的沉淀池,这是通用的降低废渣含铜的一种最简便的方法。
此法关键是用一个大的渣桶保持桶内炉渣的温度,回收桶底富集的部分渣或渣皮再处理。
渣桶法主要利用渣的潜热来实现铜滴的沉降和晶体的粗化。
(5)熔盐提取
熔盐提取法是基于铜在渣中与铜锍中的分配系数的差异,利用液态的铜锍作为提取相,使其与含铜炉渣充分接触,从而有效提取溶解和夹杂在渣中的铜。
S.Vaisburd等对这种方法进行了深入的研究,并将其用于处理哈萨克斯坦的瓦纽科夫法产生的炉渣。
另外,火法贫化研究还有直流电极还原,电泳富集等方式。
4 炉渣选矿法
依据有价金属赋存相表面亲水、亲油性质及磁学性质的差别,通过磁选和浮选分离富集。
渣的粘度大,阻碍铜相晶粒的迁移聚集,晶粒细小,铜相中硫化铜的含量下降,铜浮选难度大。
弱磁性的铁橄榄石所占比例越大,磁选时精矿降硅就越困难。
炉渣中晶粒的大小、自形程度、相互关系及主要元素在各相中的分配与炉渣的冷却方式有着密切的关系。
缓冷过程中,炉渣熔体的初析微晶可通过溶解一沉淀形式成长,形成结晶良好的自形晶或半自形晶,聚集并长大成相对集中的独立相。
(1)浮选法
从富氧熔炼渣(如闪速炉渣)和转炉渣中浮选回收铜在炼铜工业上已得到广泛应用。
浮选法除铜收率高,能耗低(较电炉贫化)外,与炉渣返回熔炼对比,可以将Fe 0及一些杂质从流程中除去,吹炼过程的石英用量将大为减少。
铜浮选回收率一般在90%以上,所得精矿大于20%,尾渣含铜在0.3% ~0.5%。
(2)磁选法
渣中强磁成份有铁(合金)和磁铁矿。
钴、镍在铁磁矿物中相对集中,铜在非磁相,因而磨细结晶良好的炉渣可作为预富集的一种手段。
由于有用金属矿物在渣中分布复杂,常有连生交代,且弱磁性铁橄榄石在渣中占的比例较大,因而磁选效果不尽人意。
目前,世界上有多家铜冶炼厂用选矿方法对转炉渣中的铜金属进行回收,由此也产生了大量的选矿尾矿。
贵溪冶炼厂选矿车间以转炉渣作为原料进行选别作业,回收其中的铜金属,渣尾矿中除SiO2的含量超标外,完全符合铁精矿要求。
5 湿法浸出
湿法过程可以克服火法贫化过程的高能耗以及产生废气污染的缺点,其分离的良好选择性更适合于处理低品位炼铜炉渣?。
(1)湿法直接浸出
炼铜炉渣中的Cu、Ni、Co、zn等金属的矿物(硫化物,金属及结合氧化物)在加压条件下可经氧气氧化而溶于(稀硫酸为例)介质中。
另外,也有文献报道用HCI和HNO,及KCN直接进行湿法浸出,但由于这些试剂费用较高,腐蚀性大,有毒等,因此在工业上用于铜渣提取金属的前景不明。
浸出液在滤清之后,滤液用含提取剂的溶出液处理。
目前工业应用较好的是汉高公司生产的LIX系列和英国Avecia公司生产的Acorge M系列萃取剂。
(2)间接浸出
适当的预处理可以将铜渣中的有价金属赋存相进行改性,使之更易于回收及分离。
氯化焙烧和硫酸化焙烧就是典型例子,焙烧产物直接水浸,金属收率主要取决于预处理效果;用酸性FeCI 浸出经还原焙烧的闪速炉渣及转炉渣,镍钴浸出率可提高到95%和8O%。
(3)细菌浸出
细菌浸出由于能够浸溶硫化铜,并具有一系列优点,故发展很快。
但细菌浸出的最大缺点是反应速度慢,浸出周期长。
最近的研究有加入某些金属(如Co、Ag)催化加快细菌氧化反应的速率,其机理在于上述金属阳离子取代了矿物表面硫化矿晶格中原有的Cu2+、Fe3+等金属离子,增加了硫化矿的导电性,所以加快了硫化矿的电化学氧化反应速率。
6 用于水泥工业建筑行业
炼铜炉渣水淬后是一种黑色、致密、坚硬、耐磨的玻璃相。
密度3.3—4.5g/cm3,孑L隙率50%左右,细度模数3.37—4.52,属粗砂型渣。
8 铜渣综合利用前景和存在的问题
铜渣综合利用大致可分为二类:一是利用铜渣的物理性质,二是利用铜渣中某些组分。
随着环境保护要求的提高和矿产资源的日益枯
竭,铜渣有很好的综合利用前景,选矿及贫化、浮选过程没有采矿成本,可充分回收铜及其中有Au、Ag等贵金属资源,尾矿含铁40%左右,经磁选富集可获得铁精矿。
炼铜炉渣的综合利用存在的问题主要是炉渣的理论研究工作不够深入,尤其是热力学和动力学方面的研究还很少。
目前,炼铜炉渣的综合利用虽然得到了较广泛的研究,但是形成工业生产规模的方法还不多。
综合利用铜渣对经济、社会和环境效益都非常重要,本文所提到的选择性处理铜渣就是一种很有前途的方式。