漆膜病态及解决方法
涂装病态原因分析与解决措施
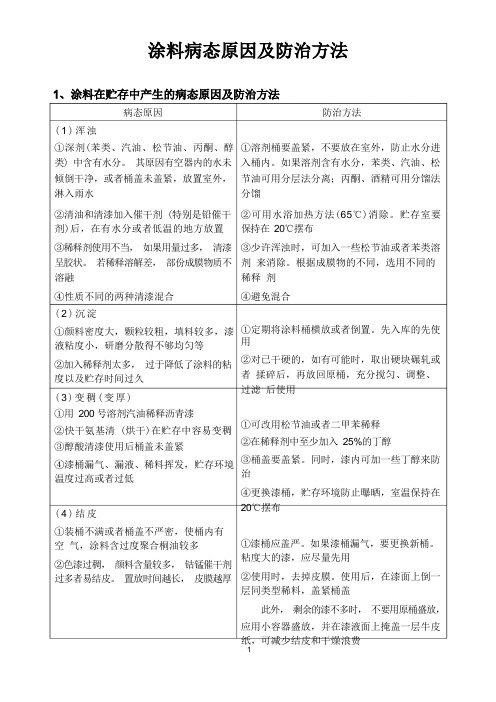
病态原因(1)浑浊①深剂(苯类、汽油、松节油、丙酮、醇类) 中含有水分。
其原因有空器内的水未倾倒干净,或者桶盖未盖紧,放置室外,淋入雨水②清油和清漆加入催干剂 (特别是铅催干剂)后,在有水分或者低温的地方放置③稀释剂使用不当,如果用量过多,清漆呈胶状。
若稀释溶解差,部份成膜物质不溶融④性质不同的两种清漆混合(2)沉淀①颜料密度大,颗粒较粗,填料较多,漆液粘度小,研磨分散得不够均匀等②加入稀释剂太多,过于降低了涂料的粘度以及贮存时间过久(3)变稠(变厚)①用200 号溶剂汽油稀释沥青漆②快干氨基清 (烘干)在贮存中容易变稠③醇酸清漆使用后桶盖未盖紧④漆桶漏气、漏液、稀料挥发,贮存环境温度过高或者过低(4)结皮①装桶不满或者桶盖不严密,使桶内有空气,涂料含过度聚合桐油较多②色漆过稠,颜料含量较多,钴锰催干剂过多者易结皮。
置放时间越长,皮膜越厚防治方法①溶剂桶要盖紧,不要放在室外,防止水分进入桶内。
如果溶剂含有水分,苯类、汽油、松节油可用分层法分离;丙酮、酒精可用分馏法分馏②可用水浴加热方法(65℃)消除。
贮存室要保持在20℃摆布③少许浑浊时,可加入一些松节油或者苯类溶剂来消除。
根据成膜物的不同,选用不同的稀释剂④避免混合①定期将涂料桶横放或者倒置。
先入库的先使用②对已干硬的,如有可能时,取出硬块碾轧或者揉碎后,再放回原桶,充分搅匀、调整、过滤后使用①可改用松节油或者二甲苯稀释②在稀释剂中至少加入25%的丁醇③桶盖要盖紧。
同时,漆内可加一些丁醇来防治④更换漆桶,贮存环境防止曝晒,室温保持在20℃摆布①漆桶应盖严。
如果漆桶漏气,要更换新桶。
粘度大的漆,应尽量先用②使用时,去掉皮膜。
使用后,在漆面上倒一层同类型稀料,盖紧桶盖此外,剩余的漆不多时,不要用原桶盛放,应用小容器盛放,并在漆液面上掩盖一层牛皮纸,可减少结皮和干燥浪费(5)变色①虫胶清漆在马口铁桶中颜色会变深, 贮 存赵久色泽赵深, 且带黑色, 干性也不好 ②金粉、 银粉与清漆会发生作用 (酸蚀作 用)以致失去明艳光泽,色泽变绿、变暗 ③复色漆中颜料密度不同, 密度大的颜料 下沉,轻的浮在上面 (6)发胀①肝化:是氧化物(如红丹)与酸价高的 天然树脂漆料作用而产生 ②胶凝: 是油料聚合过度, 其中含有聚合 胶体, 粘度增高或者结成冻胶, 如着色颜料 (铁兰等) 遇到聚合度很高的涂料, 会凝 聚成固体 ③假厚:也稀触变。
漆膜常见问题及解决办法
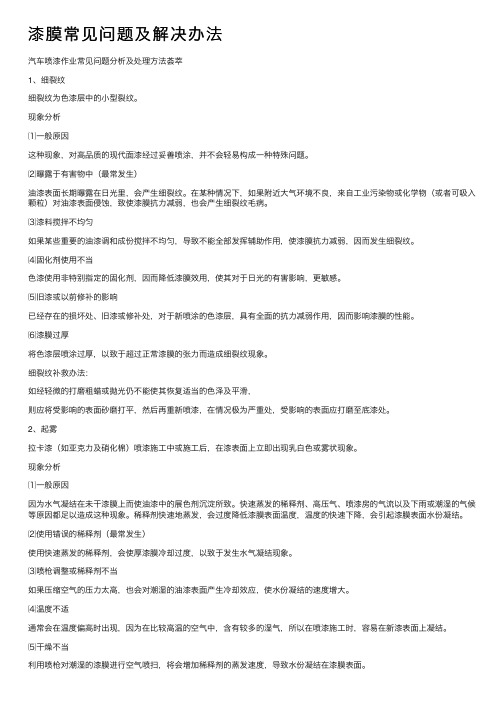
漆膜常见问题及解决办法汽车喷漆作业常见问题分析及处理⽅法荟萃1、细裂纹细裂纹为⾊漆层中的⼩型裂纹。
现象分析⑴⼀般原因这种现象,对⾼品质的现代⾯漆经过妥善喷涂,并不会轻易构成⼀种特殊问题。
⑵曝露于有害物中(最常发⽣)油漆表⾯长期曝露在⽇光⾥,会产⽣细裂纹。
在某种情况下,如果附近⼤⽓环境不良,来⾃⼯业污染物或化学物(或者可吸⼊颗粒)对油漆表⾯侵蚀,致使漆膜抗⼒减弱,也会产⽣细裂纹⽑病。
⑶漆料搅拌不均匀如果某些重要的油漆调和成份搅拌不均匀,导致不能全部发挥辅助作⽤,使漆膜抗⼒减弱,因⽽发⽣细裂纹。
⑷固化剂使⽤不当⾊漆使⽤⾮特别指定的固化剂,因⽽降低漆膜效⽤,使其对于⽇光的有害影响,更敏感。
⑸旧漆或以前修补的影响已经存在的损坏处、旧漆或修补处,对于新喷涂的⾊漆层,具有全⾯的抗⼒减弱作⽤,因⽽影响漆膜的性能。
⑹漆膜过厚将⾊漆层喷涂过厚,以致于超过正常漆膜的张⼒⽽造成细裂纹现象。
细裂纹补救办法:如经轻微的打磨粗蜡或抛光仍不能使其恢复适当的⾊泽及平滑,则应将受影响的表⾯砂磨打平,然后再重新喷漆,在情况极为严重处,受影响的表⾯应打磨⾄底漆处。
2、起雾拉卡漆(如亚克⼒及硝化棉)喷漆施⼯中或施⼯后,在漆表⾯上⽴即出现乳⽩⾊或雾状现象。
现象分析⑴⼀般原因因为⽔⽓凝结在未⼲漆膜上⽽使油漆中的展⾊剂沉淀所致。
快速蒸发的稀释剂、⾼压⽓、喷漆房的⽓流以及下⾬或潮湿的⽓候等原因都⾜以造成这种现象。
稀释剂快速地蒸发,会过度降低漆膜表⾯温度,温度的快速下降,会引起漆膜表⾯⽔份凝结。
⑵使⽤错误的稀释剂(最常发⽣)使⽤快速蒸发的稀释剂,会使厚漆膜冷却过度,以致于发⽣⽔⽓凝结现象。
⑶喷枪调整或稀释剂不当如果压缩空⽓的压⼒太⾼,也会对潮湿的油漆表⾯产⽣冷却效应,使⽔份凝结的速度增⼤。
⑷温度不适通常会在温度偏⾼时出现,因为在⽐较⾼温的空⽓中,含有较多的湿⽓,所以在喷漆施⼯时,容易在新漆表⾯上凝结。
⑸⼲燥不当利⽤喷枪对潮湿的漆膜进⾏空⽓喷扫,将会增加稀释剂的蒸发速度,导致⽔份凝结在漆膜表⾯。
建筑涂料的常见病态及其防治方法

建筑涂料已成为建筑物内外墙装饰用的首选材料,但是不少建筑涂料经过一段时间使用后,会出现起皮、脱落等现象。
建筑涂料的上述病态,可能在涂料施工前产生,也可能在施工时或施工后产生。
清楚了解涂料产生病态的原因,有助于有的放矢地采取相应的预防措施,以保证涂料的最终装饰效果。
施工前的常见病态及其防治∙增稠:涂料在贮存期内粘度增大,变得难以施工的现象称为增稠。
∙原因及防治:漆料的酸价太高,与碱性颜料发生皂化;涂料包装桶漏气,溶剂挥发;包装桶内混入水分或颜料含水贮存温度过高,使漆料加速聚集;贮存温度过低,涂料的粘度增大,造成施工困难。
补救办法视具体情况可加入相应的溶剂,搅匀调整粘度后使用;也可移入暖房贮存2~3 天,让其恢复原来的粘度。
∙沉淀结块:色漆中的颜料沉淀于桶底,甚至结成硬块的现象称为沉淀结块。
∙原因及防治:贮存时间过久;颜料,特别是红丹、铬黄的比重大;颜料粒子过粗;漆料的粘度过低;砂磨分散不均匀等。
防治方法是在贮存期间包装桶要密封好,定期倒放或横放;使用前搅拌均匀,必要时搅拌后过滤除去沉淀物。
∙结皮涂料:开罐出现一层油皮的现象称为桶内结皮。
∙原因及防治:涂料装桶不满或桶盖不严;漆料中桐油量大,或聚合过度;催化剂用量太大。
结皮必须揭去或过滤后方可使用可加入防结皮剂等予以防治。
∙流挂:施工时的常见病态及其防治流挂在垂直表面施工时,漆液向下流淌,使漆膜厚薄不均,似流泪或挂幕的现象称为流挂。
∙原因及防治:漆料的粘度太小,或兑水过多;涂料的干性差涂料中重质颜料过多或分散不匀;涂料对物面附着力差漆刷蘸漆过多;涂料施涂过厚施工环境的湿度过大或温度太低或喷涂距离过近等。
一般情况下可酌情提高施工粘度,使涂料的粘度适中,一般涂一遍粘度25s以上;控制施涂厚度,一般控制膜厚20~25 u为宜;施工环境的温度应保持在10℃以上,湿度应小于85;调整喷涂压力和适当增大喷距等,以防止和减少流挂。
∙慢干和返粘:涂料施工后,涂膜在规定的时间内不干或成膜后粘指的现象称为慢干和返粘。
涂膜病态原因分析及其防治方法

涂膜病态原因分析及其防治方法一、简述涂膜表面出现针孔的原因和防治方法。
针孔和发笑有时会被混淆,针孔是涂层表面出现圆形小圈,小的似注射针孔,大的似麻点,主要见于干燥快的涂料磨层。
原因分析:低沸点溶剂用量过多,使涂料中溶剂挥发太快;基体与施工环境有温差;环境温度高、相对湿度大;工件加热太快、温度太高,工件进入烘房太快;工件表面有油污或灰尘等杂质;喷涂时压缩空气气体压力过高;压缩空气未经过滤有油污和水。
防治方法:使用配套稀释剂或在稀释剂中增加高沸点溶剂,碱缓溶剂的挥发速度;调整环境温度或将工件在施工环境中停放一段时间,使工件与环境温度相同后再涂漆,有条件的可以将工件送烘房预热后再涂漆;要避开在高温、高湿或有雾的环境条件下施工,有空调条件的使室内相对温度控制在70%以下;烘烤温度要按烘烤条件进行,升温要缓和,也可分阶段升温烘烤,喷涂完的工件应放置4-5min后再进入烘房烘烤;涂漆前工件要彻底除净油等污染物,压缩空气必须通过油水分离器净化、气体压力不宜过高,一般应控制在0.3-0.4MPa。
二、简述涂膜表面透视出底层漆砂纸磨痕的原因和防治方法。
原因分析:主要是打磨时底层未干透,磨出砂纸道;选用的砂纸太粗,磨出砂纸道;冬天水磨时,水温过热,使漆层发软,磨出砂纸道;第二道漆粘度小固体含量太低,盖不住砂纸道。
防治方法:要待漆膜完全干透涂层有一定硬度后再打磨;不要单纯追求速度而选用较粗的砂纸,一般打磨面漆的水砂纸应选用400-500号为宜;冬天打磨用热水温度不宜太高,一般宜在20-30°C,绝对不要超过40°C;经打磨后1喷涂的首道面漆粘度不宜过低,一般不应低于20s、以20-35s为好(涂-4杯)。
三、简述涂膜生产流挂的原因和防治方法。
原因分析:刷漆刷子蘸漆过多,漆刷得太厚;喷涂时涂料粘度太低,漆喷得过厚;稀料沸点高,挥发太慢,或加入量过多;工件形状复杂,或有较多深孔,使孔周围积漆流挂;喷枪距离太近,移动速度太慢,或移动轨迹呈弧形,使漆膜有厚有薄;喷枪喷嘴直径太大,光照不好,看不清。
漆膜缺陷原因和防治措施
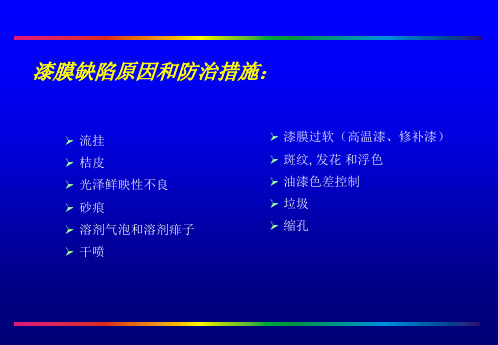
材料
Paints(油漆) Greases(润滑油)
Purge Solvents清洗溶剂
人
Antiperspirants 防汗剂 Hand Lotions 润肤液
环境
Water/DIW 水 Sandpaper 砂纸
Perfumes 香水 Solvents 溶剂 Coveralls 工作服 Sealers 密封垫
漆膜缺陷原因和防治措施:
干喷
稀释剂挥发速率太快
黏度太低
空气压力太大 漆膜太薄 枪距太远 底漆或基材表面太粗糙
漆膜缺陷原因和防治措施:
干喷 :干喷的结果是造成漆膜表面粗糙、失光、效果颜料排列翘
起,颜色发暗,长短波特大,DOI值大幅下降等弊病。
防治
添加高沸点溶剂,防止雾化漆液溶剂过分挥发,使湿膜具有一定的 润湿性流平性 其次可采用降低雾化压力,增加吐漆量,缩短同漆道间闪干时间等 辅助措施。
漆膜缺陷原因和防治措施:
砂 痕- 漆膜光泽度低并且反映出低层涂层的瑕疵。
涂膜太薄 打磨用砂纸太粗
固化不完全
对砂纸的处理方式 油漆的遮盖力低
防治: 按工艺要求,选用适宜打磨砂纸 涂层干透并冷却至室温后打磨 要求装饰性高的场合,需湿打磨
漆膜缺陷原因和防治措施:
发花斑纹:涂膜颜色不均匀,出现斑印,条纹和色相杂乱的现象,特别是
气泡、气孔: 溶剂或空气水分在漆膜干操过程中,
突破已表干漆膜,逸出时留下的孔穴, 孔穴直径0.1mm左右时为针孔,较大孔穴 为气孔,未破而使漆膜隆起的称之为气
泡。
漆膜缺陷原因和防治措施:
产生原因
E涂料及涂膜产生弊病的原因及防治.

E 涂料及涂膜产生弊病的原因及防治涂料及其涂膜产生的病态,可在涂料施工前产生,也可在施工期间或施工后出现。
因此产生病态的因素很多,主要有以下几点:(1).涂料本身的质量涂料所用基料及其性质、基料与颜、填的比例、颜填料的细度及在基料中的分散状况、助剂的选择及用量是否合适等。
(2).施工基层状况基层材质、施工程序、表面粗糙度、基材的湿度、酸度、保养期及基材处理是否得当、所用腻子质量等。
(3).涂装工艺涂层厚度、施工程序、是否有底漆与面漆配套、重涂间隔等。
(4).施工操作在施工前涂料是否搅拌均匀,是否任意稀释,施工机械质量或运转情况是否正常,操作人员的施工技术是否熟练等。
(5).施工环境施工时的气候条件,施工场所的条件,如温度、湿度、是否刮风下雨,室内通风状况。
是否涂装体系选择不当,所用的漆系统是否配套,所用的稀释剂是否匹配。
及涂刷表面和涂刷工具是否洁净等。
1 涂膜起泡涂膜干结后,局部形成直径不同的球形小泡,内部包有液体或气体,或者发生破裂的状态。
原因:表面处理不彻底(1)残留有油、水、灰尘等(2)在潮湿表面上涂漆预防:∙彻底处理表面,保持干燥、无尘、无油、无水。
∙刚涂刷的物体要避免接触高温和日光直射。
处理:将底材充分打磨至泡的凹陷处,重涂。
建议使用拜迪漆相关产品2 涂膜失光刚涂好的涂膜有光泽,但干燥后,变成无光泽或光泽不足现象原因:∙被涂物面多孔或相当粗糙∙稀释剂过多或选用不当∙湿度太大,80%以上预防方法:∙加强表面处理∙适当稀释∙控制湿度在80%以下处理:表面处理平整后,用软布沾适当稀释剂擦拭后重涂。
建议使用拜迪漆相关产品3 开裂、剥落涂膜干燥后,失去其附着力,使涂膜干裂,导致涂膜小片脱落或成张揭皮现象。
原因:∙被涂物面过分光滑∙残留有水、油、蜡、氧化皮等∙涂层太厚∙中间层有油污、蜡、或修补过腻子预防:∙涂前仔细处理表面∙涂层不宜太厚处理:铲除松动、剥落处,用砂纸将边缘打磨后,用油漆按原道的补上后大面积重涂。
涂料常见问题及解决方法

涂料常见病态及解决方法一、针孔——在漆膜表面出现的一种凹陷透底的针尖细孔现象。
这种针尖状小也就像针刺小孔,孔径在100微米左右。
(一)原因:1、木才表面木眼太深,填充困难,打磨不好;2、边疆喷涂两次间隔时间太短,下涂层干燥不完全,上涂层急速干燥;3、被涂面有灰尘,水分,压缩空气有水、油污;4、油漆配好搅拌后静置时间不够(一般应静放10-15分钟);5、一次性厚涂,表面干燥而底层溶剂继续蒸发而凸起;6、使用不良的涂料稀释剂或错用稀释剂;7、固化剂加入太多,或错用固化剂;8、稀释剂用量太小,涂料粘度过高;9、施工环境温度过高,湿度太大;10、喷涂压力过大或距离太远。
(二)解决方法:1、木材表面应充分填补好,砂光打磨达到要求;2、多次涂装时,延长重涂时间,让下层充分干燥;3、处理好补涂面灰尘和水,打水磨后,应晾置2-3小时以上,净化压缩空气;4、搅拌均匀后静置5-10分钟才能用;5、分两次或多次施工;6、使用配套产品;7、按指定的调漆比例正确调漆,并且充分搅拌均匀;8、增加稀释剂用量,达到施工最佳粘度;9、设法改善作业环境,夏天温度过高,要相应减少固化剂用量,适当选用慢干溶剂(如环已酮、CAC);10、调整好喷涂压力的距离。
二、气泡——漆膜干后出现大小不等的突起圆形泡,也叫鼓泡。
(一)原因:1、木材表面木眼深,填充困难,喷涂漆成膜后,白坯的气体向外膨胀顶起漆膜,引起起泡;2、使用过高粘度的涂料;3、喷涂空气压力过高,涂料混入空气过多;4、加热干燥过于激烈;5、物面含水率高,环境温度太高,湿度太大,通风不行;6、空气压缩机及管道带有水分;7、固化剂加入油漆调匀后,放置时间不够;8、采用含水醇高的不良稀释剂刷涂时,溶剂挥发太快;9、一次涂太厚或边疆喷涂层间间隔时间太短。
(二)解决方法:1、刮透明腻子,充分填补木眼,在喷涂前先刷一遍底得宝封闭缝隙,排出木眼中的空气;2、适当调整涂料粘度;3、调整适当的空气压力,减少空气的混入;4、加热干燥时,待溶剂挥发后进行;5、改善施工环境物面应干燥,被涂面打水磨后晾干2-3小时以上;6、使用油水分离器分离,并定期排水,每半天一次;7、搅拌后应静置5-10分钟;8、选用配套稀释剂;9、可加5-10%慢干溶剂(如CAC,环已酮等);10、分多次施工,多次涂装时,延长干燥时间,让下层充分干燥。
5.3 涂膜病态起因与预防措施

5.3涂膜病态起因与预防措施涂料是一种液体或粉末状态的材料,涂布在物体表面时能干燥成膜,均匀地覆盖和良好地附着在物体表面,达到装饰与保护的功能。
涂料经过涂装工序才能涂布在被涂物表面,再经过干燥固化工序形成具有装饰和保护作用的涂膜。
以下介绍的色漆涂膜的病态和异常现象是在施工中经常出现的,主要是讨论病态产生的原因、理论上的依据以及克服病态的预防措施。
1 .流挂色漆涂饰于垂直物体表面,在涂膜形成过程中湿膜受到重力的影响朝下流动, 形成不均匀的涂膜,称为“流挂”。
湿膜应有某种程度的流动,以求达到满意的流平性,但过度流动就会形成流挂病态。
其产生原因是与涂料本身的流变性能、施工粘度、喷涂厚度、溶剂的挥发速度等因素有关。
施工时既要达到良好的流平性,又要防止流挂的发生,这就要求我们对施工工艺、涂料品质、施工粘度、喷涂厚度、溶剂的挥发速度、流变助剂的添加等要素进行严格的设计、选择、控制和调配,使之达到预定的流平效果。
2.刷痕、滚筒痕涂料采用刷涂或滚涂方法施工时,涂膜表面干燥后产生未能流平的痕迹称为“刷痕”或“滚筒痕”,明显地影响了涂膜的外观。
产生原因是涂料未能充分流平和流平性差、施工时刷涂技术不佳、施工粘度高、涂膜表干过快等,使湿膜的展布不良而导致刷痕。
预防措施是严格控制涂料质量,调整好最佳施工粘度及环境条件,并使用合适工具,正确地进行施工,必要时可酌量添加少量高沸点溶剂。
3.桔皮桔皮是湿膜未能充分流动形成的类似桔皮状的痕迹。
原因一方面跟涂料本身内在的流变性有关;另一方面喷涂施工时,施工粘度较高,喷枪口径大小不适,导致雾化程度不足、喷枪离被涂工件的距离过远、喷漆室的过度通风、烘干前的闪蒸时间不当,稀释剂的质量、底材的温度等,均会影响涂膜桔皮病态的产生。
预防措施主要是一方面严格控制涂料质量;另一方面是添加适量挥发速度较慢的溶剂或流平剂、降低到较为合适的施工粘度,以延长湿膜的流动时间,使之有足够时间使整体表面张力趋向一致。
- 1、下载文档前请自行甄别文档内容的完整性,平台不提供额外的编辑、内容补充、找答案等附加服务。
- 2、"仅部分预览"的文档,不可在线预览部分如存在完整性等问题,可反馈申请退款(可完整预览的文档不适用该条件!)。
- 3、如文档侵犯您的权益,请联系客服反馈,我们会尽快为您处理(人工客服工作时间:9:00-18:30)。
返回
定义:当涂料干燥成膜后,涂膜很容易从底材上剥落下来,若 定义
造成大面积脱落。
产生原因: 产生原因 底材金属表面过分光滑,底材被油料玷污、含有
水分或含有过多的硅烷类流平剂等。
预防措施: 预防措施 涂装以前吧光滑的底材磨粗,用溶剂擦拭干净除
去底材上的油污。
返回
定义: 定义 涂料复涂时,在两层涂膜间出现附着力差的现象,重涂
定义: 定义 涂料成膜后出现大小不等的突起的圆形泡,产生于漆膜
表面和涂膜之间。
产生原因:色漆在使用过程中,由于搅拌、泵料输送或施工 产生原因
中混入空气,不易消散,在施工后的涂膜表面浮着气泡。
预防措施: 预防措施 1、施工前应将稀释剂搅拌后的涂料放置一段时间
后再用;2、加入适量消泡剂。
返回
定义: 定义 当色漆施涂时,在湿膜表面上会出现一种微小的气泡。 产生原因: 产生原因 1、颜料及填料表面所吸附的气体或液体,条件改
硅烷流平剂(如:BYK-310)
返回
定义:涂装后漆膜表面出现不规则块状物的总称。 定义 产生原因: 产生原因 1、颜料分散不良;2、色漆所用漆基中有不溶
的聚合物软颗粒或析出不容的金属盐;3、小块漆皮被分散混 合在漆中。
预防措施: 预防措施 注意涂料的净化及施工场所环境的洁净度
返回
定义: 定义 涂料施工后,湿膜在流平过程中出现回缩,成小圆形的
返回
定义: 定义 涂膜表面上呈现一种铜金的或泛金光的外观。 产生原因: 产生原因 常发生于使用有机红色颜料和铁蓝颜料的色漆中。
大红粉及铁蓝颜料中有一种可溶物,在制备氨基烘漆时,随着烘 烤的进行,由挥发溶剂带出,呈现在涂膜表面。
预防措施: 预防措施 严格控制颜料质量,在颜料制造过程中将这种可
溶物洗净。
施工,可采用施涂预涂底漆及封闭底漆后再涂面漆的办法;2、 提高涂料对底层的粘附能力,可采用在涂料中加入硅烷偶联剂的 办法。
返回
定义: 定义 涂料涂覆在黑色金属底材表面,在涂装后不久,涂膜下
会出现红丝或锈点,个别情况还会出现浮锈。
产生原因:涂层表面处理不好,有时虽经表面处理或磷化处 产生原因
理后,未能及时涂漆,也会产生早期生锈的弊病。
速干燥所致。含干性油的油性漆及醇酸漆,因干燥剂选用不当, 使用钴和锰催干剂过多、锌干料缺少均会引起涂膜起皱。
预防措施: 预防措施 1、用桐油为成膜物时,注意漆基的熬炼程度要适
宜;2、自干漆加温干燥时,应选用少量高沸点溶剂,让湿膜在 常温下风干时间稍长些。
返回
定义: 定义 含有铝粉及珠光颜料的涂料,在施涂后因流平性差出现
的第二道面涂的涂膜变脆,并局部或全部地从已烘干的头道面漆 涂膜上成片地剥落,完全丧失附着力。
产生原因:表面处理不当,底漆配套不良。 产生原因 预防措施: 预防措施 控制涂料的质量,检验层间附着力必须达到规定
要求。建议复涂时采取“湿碰湿”工艺。
返回
定义: 定义 涂膜在使用过程中,因外界机械损伤,涂膜极易被划出
返回
定义: 定义 在色漆施涂时,涂层已足够厚但遮盖能力仍不足而产生
显露底材的毛病。
产生原因: 产生原因 1、色漆贮存期过久,颜料沉底未搅拌均匀;2、
色漆本身颜料量不足或产生絮凝引起的。
预防措施: 预防措施 1、使用前,先进行色漆遮盖力质量指标的检测,
合格后再施工;2、施工时所用的稀释剂必须匹配。
返回
流坠或因湿膜喷涂厚薄不匀使铝粉或珠光颜料不能形成均匀的定 向排列,导致涂膜金属闪光色不匀。
产生原因: 产生原因 1、铝粉的选用、珠光颜料的质量,选用的成膜物
质及助剂结构,所用溶剂的挥发速率均是影响因素;2、喷涂时 的漆雾雾化不良,厚薄不均以及涂膜干燥过慢也会影响金属颜料 的排列。
预防措施: 预防措施 1、选用的金属铝粉必须是浮型的,且贮存期不能
返回
发花: 发花 涂膜的外观有花斑,呈斑点或条斑的现象。施涂后涂膜
中存在多种颜料不均匀分布。
浮色: 浮色 发花的极端状况。某些颜料浮升至表面,虽该膜表面颜
色均匀一致,但明显地不同于刚施涂时的湿膜颜色。
产生原因:颜料粒子大小不同或由于溶剂挥发形成的漆基循 产生原因
环流引起颜料不均匀分离而致
预防措施: 预防措施 1、制漆时不选用含极细颗粒的颜料品种;2、在
喷出时大量溶剂挥发,使漆雾粘度增高所致。
预防措施: 预防措施 选用适宜的溶剂,调整到适宜施工粘度。
返回
定义: 定义 涂膜干燥后,在涂膜表面形成针状小孔,严重时针孔大
小似皮革的毛孔状表面。
产生原因: 产生原因 喷涂施工时,湿膜中溶剂挥发速度快,以及因涂
膜中空气泡溢出,湿膜不能流平,导致涂膜干燥后留下针状小孔。
补漆;2、加入流变助剂提高湿膜的屈服值,阻止湿膜有较长的 流动时间。
返回
定义: 定义 施涂后溶剂迅速挥发过程中出现的一种不透明的白色膜。 产生原因: 产生原因 正在干燥的涂膜邻近的空气冷冻到了露点,致使
水分凝结在涂膜上面的缘故。
预防措施:1、调整好涂料所用溶剂,适量增加高沸点溶剂, 预防措施
减小挥发快的容积用量;2、施工时,控制空气中相对湿度在 65%以下。
变时释放出来;2、因溶解于涂料内的气体随温度升高而释放出 来;3、生产或施工时所引起的气泡;4、多孔底材表面残留空气。
预防措施: 预防措施 1、涂料中要使用湿润分散剂取代颜料表面空气杂
物;2、制造工艺上,适当延长颜料湿润与分散时间;3、在施工 时要控制涂料的湿膜流平性。
返回
定义: 定义 涂料在喷涂时雾化不好,喷涂于底材上的漆雾呈丝状。 产生原因: 产生原因 涂料施工粘度高,稀释剂溶解力差,漆从喷枪中
预防措施: 预防措施 1、适当增加色漆的触变性,2、加入适量的流变
助剂
返回
定义: 定义 施涂后,在底材的边、角处的涂膜回缩,导致该处涂膜
较薄,甚至露底。
产生原因: 产生原因
湿膜的表面张力过高,使体系的表面能趋向最小,
湿膜就从边角处回缩。
预防措施: 预防措施 1、工件尽量设计得没有锐角、锐边,或在边角上
返回
定义: 定义 浅灰、浅蓝体系色漆在涂装后,湿膜表面会呈现出白色
颜料的浮色(不同于黑色、蓝色颜料的浮色)
产生原因: 产生原因 1、与选用的白色颜料的品种有关;2、可能因混
入另一种漆基而引起颜料的絮凝或分离,导致钛白颜料的漂浮。
预防措施: 预防措施 1、严格筛选合适的白色颜料;2、在制漆时尽量
避免选用两种不同漆基。
预防措施: 预防措施 添加适量的流变助剂(有机改性膨润土)
返回
定义: 定义 涂膜表面干燥后产生未能流平的痕迹称为刷痕。 原因: 原因 1、涂料粘度过稠,流平性差,稀释剂挥发速度过
快;2、施工时刷涂技术不佳;3、涂装工具选择不当;4、 被涂物底材吸收性过强,涂料涂刷后即被快速吸收,造成涂 刷困难出现刷痕。
超过半年;2、铝粉颗粒大小应实验搭配;3、珠光颜料的粒度分 布也会影响闪光效应;4、掌握喷涂技术,控制涂膜厚度均匀一 致
返回
定义: 定义 在施涂自干型溶剂漆时,在干燥成膜后的短时间内又会
发现漆膜手感不爽,指触有发粘的现象。
产生原因: 产生原因 1、由于聚合不足的油、沥青或其氧化产物的脱液
收缩作用(即液体从胶体中排出)引起;2、底材处理不当,底材中 的松香、油污、增塑剂等物从漆膜表面渗出而引起;3、在高温 高湿环境中,更容易促使产生此病态。
漆膜病态
1、流坠(流挂) 3、桔皮 5、缩孔 7、厚边 9、泛白 11、浮白 13、咬起 15、气泡 17、拉丝 19、起皱 2、 刷痕 4、起粒 6、抽缩 8、露角 10、泛金光 12、发花和浮色 14、露底 16、微泡 18、针孔 20、金属闪光色不匀
21、回粘 23、剥落 25、耐划痕性差 27、片落 29、玷污、斑点 31、泛碱 33、干燥不良 35、漆膜丰满度差 37、粉化 39、起泡
防治措施: 防治措施 1、选择优质涂料和稀释剂,适当调整涂料
粘度; 2、正确施工; 3、选择适当涂装工具; 4、用封闭 底漆对基材进行封闭,然后再涂刷底漆和面漆。
返回
定义: 定义 湿膜未能充分流动形成的类似桔皮状的痕迹。 产生原因: 产生原因 喷涂施工时,施工粘度较高,喷枪口径大小不适。 预防措施:1、添加适量挥发速度较慢的溶剂;2、加入改性 预防措施
裸露底材或底层。
产生原因: 产生原因 湿膜上下部分表面张力不同。 预防措施: 预防措施 1、改善湿膜流展性能;2、涂料的表面张力要低,
且对底材的润湿性要好;3、加适宜的流变助剂或低表面张力的 溶剂。
返回
定义: 定义 涂料施涂后,湿膜回缩,使较大面积的底材裸露出来,
这种病态称为抽缩。
产生原因: 产生原因 涂料的展布系数为较大的负值。这种病态是由于
预防措施: 预防措施 1、严格选用稀释剂,严格控制施工粘度;2、施
工时防止水分及其他杂物混入,严格检查压缩空气的洁净度及被 涂物表面的污染程度。
返回
定义: 定义 施涂于底层上的涂膜,在干燥过程中,无论是常温干或
烘干,会形成局部或全部的皱纹状涂膜。
产生原因: 产生原因 涂膜施涂过厚、湿膜闪蒸时间不够,骤然高温加
中析出。
预防措施: 预防措施 控制所用配套溶剂和稀释剂的质量,调整好溶剂
的配方。
返回
定义: 定义 涂料施涂在底材上后,出现涂膜局部的剥落。 产生原因: 产生原因 底材处理不好、表面有油污、金属表面光洁度大
或因底层粉化严重,黑色金属底材经磷化处理或轻金属经阳极化 处理后离涂漆的间隔时间过长。
预防措施: 预防措施 1、对底层的处理应严格控制,彻底打磨干净后在
涂膜对底材润湿不良。
预防措施: 预防措施 1、在涂装前对底材表面进行严格的除油处理。2、
采取提高润湿性的措施(如表面改性处理)3、尽量选用表面张 力较低的专用涂料。