再订货点与安全库存-myOM
安全库存-
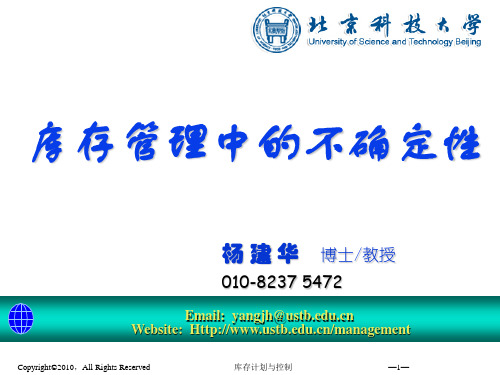
产品可获得能力与利润目标、战略及竞争问 题相联系 如何设立满足率或周期服务水平,确保供应 链上利润最大?
库存计划与控制 —9—
Copyright©2010,All Rights Reserved
补货策略 Replenishment Policies
补货策略: 决定何时再下订单,订单数量? 库存的持续检查 Continuous review: 库存处 于持续监控下,当库存水平达到再订货点(the reorder point) ROP时,下达订单订货批量Q-----定量订货模型 库存的定期检查Periodic review: 以固定周期 检查库存水平,下达订单的订货批量需要达 到一个预先确定的极限水平------定期订货模 型
库存计划与控制 —19—
Copyright©2010,All Rights Reserved
使用安全库存的定量订货模型
不确定提前期、 需求量固定 化工厂每天消耗800吨酸性溶液,来自供应商的交 货期服从正态分布,期望值14天,标准差4天。如果 化工厂希望保证99% 的服务水平,那么再订货点应 是多少?(z=2.33)
库存管理中的不确定性
杨建华
博士/教授 010-8237 5472
Email: yangjh@ Website: /management
Copyright©2010,All Rights Reserved 库存计划与控制 —1—
例 (1)
Copyright©2010,All Rights Reserved
库存计划与控制
—11—
安全库存降低了提前期内缺货风险
Quantity
Maximum probable demand during lead time
会设安全库存,再订货点的计算就很容易

会设安全库存,再订货点的计算就很容易在库存计划领域,除了安全库存,经常打交道的还有再订货点(或者就叫订货点)。
其逻辑是一旦库存降到预设的水位(再订货点,ROP),就启动订货机制,驱动供应链补充一定数量的货(订货量,ROQ);在货来到之前,库存继续下降,直到订的货到达,拉高库存的水位,然后开始下一个循环,如图1[1]。
再订货点法在企业里使用很广,它的几个参数,在此稍作解释。
图1:再订货法示意图先说再订货点。
再订货点由两部分构成:(1)补货周期内的平均需求——这是平均需求预测*补货周期(如果需求相对稳定的话,一般会用过去一段时间的平均需求来代替);(2)安全库存——这是为了应对需求和供应的不确定性,以及提高有货率,我们在前面已经详细探讨过。
这概念其实你在做单身汉的时候就烂熟于胸:你每周买一次菜(这意味着补货周期是7天),每天平均吃半斤小白菜,那你要把小白菜“库存”至少建到3.5斤,那是“补货周期内的平均需求”;有时候斜对门的另一个单身汉来蹭饭,那是“需求的不确定性”,你就得多备点,得了,再加1斤,就是你的“安全库存”。
这样,你的“再订货点”就是4.5斤。
再说订货量。
这是说每当补货时,需要补多少。
你知道,最少也要达到或超过再订货点(取决于不同的计算机系统:在有些系统,库存水位达到再订货点,就触动补货;而在另一些系统,需要低于再订货点)。
但同时,还要考虑补货相关的成本。
在订货量方面,你天生就是专家:(1)订货成本越高,订货量就越大——为了几根葱,就让你跑趟菜市场,你会很愤怒,因为你跑一趟的“订货成本”很高,你当然希望多买些东西,把单位订货成本降下来;(2)需求量越大,订货量就越大——这能解释为什么你一次买50斤米,但不会买50斤盐;(3)库存成本越高,订货量就越小——这就是为什么你不会买半年喝的水,因为占地方没处放;你也不会买一个月吃的小青菜,因为小青菜会坏掉,两种情况下的库存成本都很高。
在经济学上,有个经济订货量(EOQ)的概念,已经研究了一百年了,就是平衡上述订货成本、需求量和库存成本,生产的最小批量,采购的最小订货量也是来源于此[2]。
安全库存设置及管理办法
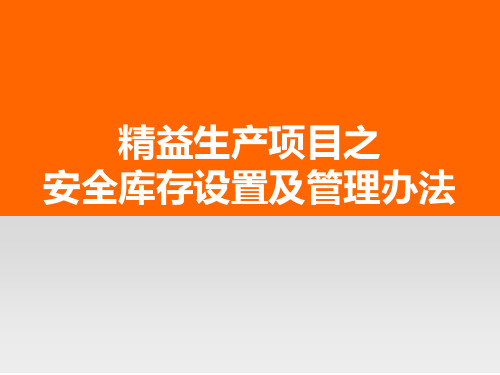
17/150
10、采购对应方式
1、明确同类物料有几家可以供应; 2、每家采购周期明确; 3、定价方式提前约定避免每次报价、核价与竞价延误时间; 4、跟进采购订单手工与ERP; 5、供应商的产能比例(50%、30%、20%)根据交付、品质、成本等调整;
18/150
10、采购对应方式
6、采购跟进管理(物料Hot大报警)。
4、设定出安全库存管理表。
14/150
8、建立“安全库存”步骤
5、正确录入系统,由系统发挥监控,标准化管理。
15/150
9、订货点管理法
数量
最大库存
均衡消费 消费加快
• • 订货点
批 量
增加 订货量
订货点
不变
消费减慢
订货点
•升高
订货量 不变
安全库存量
LT
LT
LT
订货提前期 订货提前期 订货提前期
安全 系数
1 1 1 1 1 1 1 1 1 1 1 1 1 1
使用部门
防一 通用 防一 通用 屏风 防一 防一 屏风 通用 防一 防一 屏风 屏风 防一
量产采 购员 邹蓉萍 邹蓉萍 邹蓉萍 邹蓉萍 邹蓉萍 邹蓉萍 邹蓉萍 邹蓉萍 邹蓉萍 邹蓉萍 邹蓉萍 邹蓉萍 邹蓉萍 邹蓉萍
13/150
8、建立“安全库存”步骤
适中管理, 一般控制
可以做一定的安全库存
C类料
其成本最 整个物料成本 可采用经济定量
少
的10%左右 采购的方式
粗放管理, 稍加控制
不用做安全库存,根据采购 费用和库存维持费用之和的 最低点,订出一次的采购量。
7/150
6、按物料类别设置安全库存
类别区分
区分办法 采购办法 安全库存选定办法 物料种类(举例)
安全库存及重订货点

一、安全库存设置供给:现有库存+接收(采购订单,确认订货建议,生产订单等等)需求:计划独立需求,客户需求,相关需求,物料预留以及预测需求等等以三达现在的设法为例,MRP类型PD,批量为EX,按正常情况下,运行MRP对供给和需求进行平衡后,供给等于需求,如果设置了安全库存,则供给=需求+安全库存。
也就是说安全库存是在需求计划外多备的一部分库存,这部分库存可以在紧急情况下使用,如采购来不及、紧急需要等。
最小安全库存是指系统中一定要备有的数量,这部分数量不能用于发料,建议不要设置。
使用安全库存的优点就是可以满足紧急情况下使用,缺点是因为这部分库存在需求之外,增加了库存成本。
如果某个物料具有采购周期较长、经常采购来不及、使用较频繁、成本较低的特征可以考虑设置安全库存二、人工重订货点设置人工重订货点的MRP类型为VB,在MRP1视图重订货点输入需要重订货的基准数量。
PD与VB的差别在于PD是供给跟需求进行平衡,当供给小于需求时,系统会产生计划订单或采购申请对需求进行平衡,而VB是供给跟重订货点进行平衡,即VB不考虑实际的需求情况。
当供给低于重订货点时,系统根据设置的批量策略来进行补给,如批量设置成HB,最大库存水平为500,则当供给小于100时,运行完MRP系统产生供给(计划订单或采购申请)补充到500。
例:假设当前没有接收(采购订单、生产订单、采购申请等),需求数量为100,当前库存50,运行MRP后,系统产生450的计划订单,即系统不会考虑需求数量为100,而是考虑供给小于100应该触发重新订货,然后重新订货根据批量设置了HB,最大库存水平设置了500,从而将供给补充到500。
人工重订货点主要是根据历史消耗的情况来设置,这种方式不基于当前系统的实际需求数量来计划。
采用重订货点方式需考虑重订货点数量设置多少,以及补给策略,如最大库存水平大小。
再订货点与安全库存
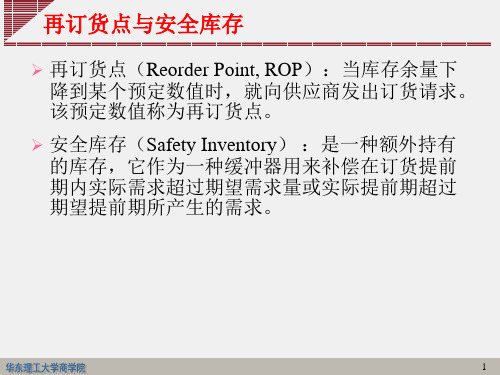
再订货点(Reorder Point, ROP):当库存余量下
降到某个预定数值时,就向供应商发出订货请求。 该预定数值称为再订货点。
安全库存(Safety Inventory) :是一种额外持有
的库存,它作为一种缓冲器用来补偿在订货提前 期内实际需求超过期望需求量或实际提前期超过 期望提前期所产生的需求。
标准正态分 布中的安全 系数
需求服从正 态分布时的 再订货点
平均需求
再订货点
安全 系数
0
Z
6
给定采购补货策略下的服务水平衡量
服务水平(CSL)衡量公式:
CSL=Prob(周期需求≤ROP)
在需求服从正态分布的条件下,上式变为:
CSL=F( ROP,DLT ,σLT )
ROP D LT , 0, 1) =Φ(
缩短供应提前期需要供应商付出努力,而减少的是采购 商的库存,因而需要设计相应的收益分享激励机制。
降低需求的不确定性,即标准差σ 安全库存与标准差保持同比例下降。 方法:采用更好的市场情报系统和更先进的需求预测方法。
对供应链管理来说,要降低需求的不确定性,就必须使各环 节的预测与最终顾客需求的数据相一致,协同预测(CPFR)。
用标准方差
• 库存在不确定性需求下如何处理?
1 2
用批量定货量与平均需求匹配
用一个安全库存来保证变化下的服务水平
安全库存与需求分布的方差有关 安全库存与服务水平有关
5
服务水平与安全库存的关系
服务水平 (无缺货概率) 无缺货概率
安全 库存
在提前期内需求 近似服从正态分 布的情况下,如 果没有安全库存, 缺货的概率可达 50% 。增加安全 库存后,降低了 缺货风险,提高 了服务水平。
订货点采购和库存控制

订货点采购和库存控制引言在供应链管理中,订货点采购和库存控制是重要的概念和工具。
订货点采购是指根据销售预测和库存水平设定的订货点,及时补充库存以满足市场需求。
而库存控制则是确保库存水平合理的管理方法。
本文将详细介绍订货点采购和库存控制的概念、原则以及相关的管理策略。
订货点采购定义订货点采购是供应链管理中的重要环节,它通过设置订货点来实现库存的合理补充。
订货点是指在销售预测和库存水平之间设定的一个触发点,当库存水平低于订货点时,即触发采购行动。
订货点的计算订货点的计算通常基于以下几个因素:1.预测销售量:基于市场需求和过去的销售数据,预测未来的销售量。
2.供货时间:供应商从接收采购订单到交货所需的时间。
3.安全库存:预防延迟交货或销售高峰期对库存的影响,设置的保留库存。
订货点可以通过以下公式计算得出:订货点 = 预测销售量 \* 供货时间 + 安全库存订货点采购的优势和适用场景订货点采购具有以下几个优势和适用场景:1.减少库存成本:订货点采购可以避免库存积压和过剩,减少库存成本。
2.提高交货效率:订货点的设定使得供应商能够在合适的时间内交货,提高交货效率。
3.提升客户满意度:及时补充库存可以满足市场需求,提升客户满意度。
4.适用于稳定销售环境:订货点采购在面对销售需求相对稳定的情况下更为适用。
库存控制定义库存控制是指对库存进行合理管理的方法和策略,旨在实现优化供应链的目标。
库存控制的主要目标包括最小化库存成本、最大化库存周转率和减少库存缺货。
基本原则库存控制的基本原则包括:1.合理的库存目标:根据企业的需求和供应链特点,设定合理的库存水平目标。
2.库存分类:根据产品特性、销售模式等因素,将库存进行分类,以便更好地进行管理。
3.周期检查和盘点:定期进行库存检查和盘点,确保库存数据的准确性和完整性。
4.供应链协同:与供应商和客户建立良好的合作关系,实现供应链的协同管理。
库存控制策略库存控制可以采用以下策略来进行管理:1.JIT(Just-in-Time)库存管理:根据实际需求,及时补充库存,以减少库存积压和浪费。
库存管理的五种方法
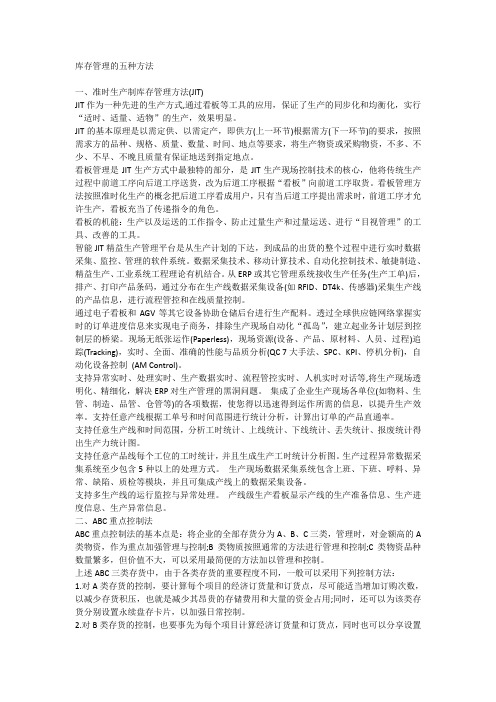
库存管理的五种方法一、准时生产制库存管理方法(JIT)JIT作为一种先进的生产方式,通过看板等工具的应用,保证了生产的同步化和均衡化,实行“适时、适量、适物”的生产,效果明显。
JIT的基本原理是以需定供、以需定产,即供方(上一环节)根据需方(下一环节)的要求,按照需求方的品种、规格、质量、数量、时间、地点等要求,将生产物资或采购物资,不多、不少、不早、不晚且质量有保证地送到指定地点。
看板管理是JIT生产方式中最独特的部分,是JIT生产现场控制技术的核心,他将传统生产过程中前道工序向后道工序送货,改为后道工序根据“看板”向前道工序取货。
看板管理方法按照准时化生产的概念把后道工序看成用户,只有当后道工序提出需求时,前道工序才允许生产,看板充当了传递指令的角色。
看板的机能:生产以及运送的工作指令、防止过量生产和过量运送、进行“目视管理”的工具、改善的工具。
智能JIT精益生产管理平台是从生产计划的下达,到成品的出货的整个过程中进行实时数据采集、监控、管理的软件系统。
数据采集技术、移动计算技术、自动化控制技术、敏捷制造、精益生产、工业系统工程理论有机结合。
从ERP或其它管理系统接收生产任务(生产工单)后,排产、打印产品条码,通过分布在生产线数据采集设备(如RFID、DT4k、传感器)采集生产线的产品信息,进行流程管控和在线质量控制。
通过电子看板和AGV等其它设备协助仓储后台进行生产配料。
透过全球供应链网络掌握实时的订单进度信息来实现电子商务,排除生产现场自动化“孤岛”,建立起业务计划层到控制层的桥梁。
现场无纸张运作(Paperless),现场资源(设备、产品、原材料、人员、过程)追踪(Tracking),实时、全面、准确的性能与品质分析(QC 7大手法、SPC、KPI、停机分析),自动化设备控制(AM Control)。
支持异常实时、处理实时、生产数据实时、流程管控实时、人机实时对话等,将生产现场透明化、精细化,解决ERP对生产管理的黑洞问题。
再订货点与安全库存myOM
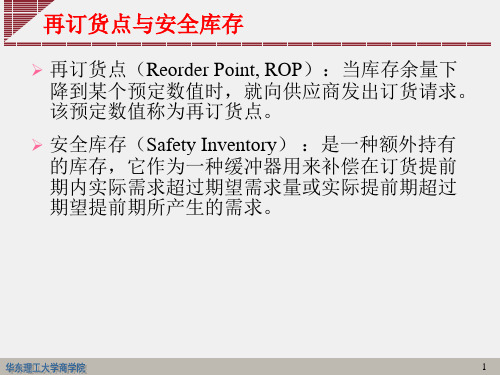
需求和提前期都不确定条件下的再订货点
DLT=d×ALT
σDLT=
LT2d2
2 LT
ROP = DLT+ SI = DLT+ z× σDLT
12
例4中,假设提前期均值为3天,标准差为0.5天。
σDLT= L T2d2L 2T= 332020 20 0.52
=112 .7 SI=1.64×112.69≈185件 ROP=200×3+185=785件
ROPDL
LT
T=Φ-1(
CSL
,
0,
1)
ROP = DLT+Φ-1( CSL , 0, 1)× σLT
SI =Φ-1( CSL , 0, 1)× σLT
安全系数z
转化为标准正 态分布求解
9
例4:某大型服装零售商销售一款服装,每天平 均需求量为200件,标准差为30件,订货提前期 为3天。若该零售希望达到95%的周期服务水平, 则应如何确定安全库存和再订货点?
1
需求与提前期都是常数时的再订货点
在库存持有量能够满足等待订货期间(即提 前期)的需求时下订单。 ➢ 若需求与提前期都是常数,再订货点为:
ROP = d LT 其中: d —— 需求率; LT —— 提前期
Q*=93
ROP=?
2
需求与提前期变化时的再订货点
➢ 一旦需求或提前期发生变化,实际需求就 有可能超过期望需求。因此,为了减少缺 货风险,应持有额外库存即安全库存。这 时,再订货点为: ROP = 提前期内的期望需求 + 安全库存(SI)
再订货点与安全库存
➢ 再订货点(Reorder Point, ROP):当库存余量下 降到某个预定数值时,就向供应商发出订货请求。 该预定数值称为再订货点。
- 1、下载文档前请自行甄别文档内容的完整性,平台不提供额外的编辑、内容补充、找答案等附加服务。
- 2、"仅部分预览"的文档,不可在线预览部分如存在完整性等问题,可反馈申请退款(可完整预览的文档不适用该条件!)。
- 3、如文档侵犯您的权益,请联系客服反馈,我们会尽快为您处理(人工客服工作时间:9:00-18:30)。
LT
=Φ-1( CSL , 0, 1)
转化为标准正 态分布求解
ROP = DLT+Φ-1( CSL , 0, 1)× σLT SI =Φ-1( CSL , 0, 1)× σLT
安全系数z
9
例4:某大型服装零售商销售一款服装,每天平 均需求量为200件,标准差为30件,订货提前期 为3天。若该零售希望达到95%的周期服务水平, 则应如何确定安全库存和再订货点?
(1)整个周期内供货的数量/ 整个周期的需求量 (2)提前期内供货的数量/提前期的需求量 (3)顾客订货得到完全满足的次数/ 订货发生的总次数 (4)不发生缺货的补充周期数/ 总补充周期数 (5)手头有货可供的时间/ 总服务时间
4
如何处理不确定性需求?
σ DLT= LT σ DLT=d×LT
• 如何表示需求变化?
1
需求与提前期都是常数时的再订货点
在库存持有量能够满足等待订货期间(即提 前期)的需求时下订单。
若需求与提前期都是常数,再订货点为:
ROP = d LT 其中: d —— 需求率; LT —— 提前期
Q*=93 ROP=?
2
需求与提前期变化时的再订货点
一旦需求或提前期发生变化,实际需求就
11
需求和提前期都不确定条件下的再订货点
DLT=d×ALT
σDLT= LT d
2 2 2 LT
ROP = DLT+ SI
= DLT+ z× σDLT
12
例4中,假设提前期均值为3天,标准差为0.5天。
2 2 2 2 σDLT= LT 2 d 2 LT = 3 30 200 0.5
14
常见的多级库存渠道
仓库层级
R1
仓库, 提前期,LTW
d1,σ1
S
供应商
W
仓库
R2
d2,σ2
最 终 客 户 需 求
R3
零售商
d3,σ3
15
例6:对于常见的分销系统,零售商根据最终客户的需求预 测零售需求。零售商对各种产品的月需求预测如下表所示。
一月 二月 三月 四月 五月 六月 七月 八月 九月 十月 十一 月 十二 月 平均 标准 差
有可能超过期望需求。因此,为了减少缺 货风险,应持有额外库存即安全库存。这 时,再订货点为: ROP = 提前期内的期望需求 + 安全库存(SI)
3
周期服务水平
服务水平(CSL)是衡量随机型库存系
统的一个重要指标,它反映的是补货周期 内不发生缺货的概率。
CSL=Prob(周期需求≤ROP)
服务水平可用以下指标衡量:
=112 .7 SI=1.64×112.69≈185件 ROP=200×3+185=785件
13
多级库存管理
• 多级库存管理:管理整个渠道的库存而不只是 各自独立的存储点的库存。 • 基本逻辑:渠道中的每一级都按自己的库存水平 加上来自所有下游的库存来进行库存计划。也即, 每一级库存水平 的计划都不是仅仅考虑自己下 一级的需求信息,而是考虑最终客户的需求信息。
DLT
转化为标准正 态分布求解
7
例3:假定联想电脑某款芯片的周需求符合正态分布, 均值为2500,标准差为500。供应商的供货提前期为两 周。目前联想的库存控制策略是连续盘点,当库存芯片 少于6000片时,订货10000片。试分析该芯片库存的均 值,安全库存和库存周转时间;并衡量周期服务水平。 d=2500; σ=500; LT=2周; ROP=6000; Q=10000 SI=ROP-DLT=6000-2500×2=1000 周期平均库存=Q/2+ SI =10000/2+1000=6000 库存周转时间=平均库存/平均周转速度 =6000/2500=2.4周 σDLT= LT σ= 2×500≈707 CSL= Φ(
标准正态分 布中的安全 系数
需求服从正 态分布时的 再订货点
平均需求
再订货点
安全 系数
0
Z
6
给定采购补货策略下的服务水平衡量
服务水平(CSL)衡量公式:
CSL=Prob(周期需求≤ROP)
在需求服从正态分布的条件下,上式变为:
CSL=F( ROP,DLT ,σLT )
ROP D LT , 0, 1) =Φ(
用标准方差
• 库存在不确定性需求下如何处理?
1 2
用批量定货量与平均需求匹配
用一个安全库存来保证变化下的服务水平
安全库存与需求分布的方差有关 安全库存与服务水平有关
5
服务水平与安全库存的关系
服务水平 (无缺货概率) 无缺货概率
安全 库存
在提前期内需求 近似服从正态分 布的情况下,如 果没有安全库存, 缺货的概率可达 50% 。增加安全 库存后,降低了 缺货风险,提高 了服务水平。
首先计算订货提前期内的标准差 σDLT=LT σ = 3 ×30=1.732×30=51.96
查正态分布表得 z(0.95)=1.64
因此安全库存SI=1.64×51.96≈ 85件
再订货点ROP=200×3+85=685件 订货批量可由一般经济订货批量模型确定。
10
降低安全库存的方法
缩短供应提前期 如果提前期缩短到原来的k倍,安全库存则降低为原 来的 k 倍。
6000 5000 )= 707
Φ(1.414) ≈ 0.92
8
给定服务水平下的安全库存及订货点的确定
基本原理:
对方程CSL=Prob(周期需求≤ROP)逆向 求解得ROP,再根据SI = ROP-DLT求安全 库存。
在需求服从正态分布的条件下,则为: ROP =F-1( CSL, DLT , σDLT )
缩短供应提前期需要供应商付出努力,而减少的是采购 商的库存,因而需要设计相应的收益分享激励机制。
降低需求的不确定性,即标准差σ 安全库存与标准差保持同比例下降。 方法:采用更好的市场情报系统和更先进的需求预测方法。
对供应链管理来说,要降低需求的不确定性,就必须使各环 节的预测与最终顾客需求的数据相一致,协同预测(CPFR)。
再订货点与安全库存
再订货点(Reorder Point, ROP):当库存余量下
降到某个预定数值时,就向供应商发出订货请求。 该预定数值称为再订货点。
安全库存(Safety Inventory) :是一种额外持有
的库存,它作为一种缓冲器用来补偿在订货提前 期内实际需求超过期望需求量或实际提前期超过 期望提前期所产生的需求。