焊线工艺参数规范
常用焊接参数的选择
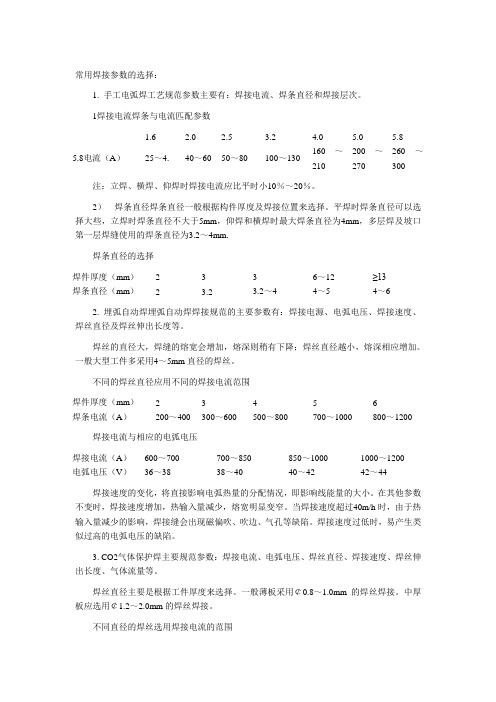
常用焊接参数的选择:1. 手工电弧焊工艺规范参数主要有:焊接电流、焊条直径和焊接层次。
1焊接电流焊条与电流匹配参数· 1.6 2.0 2.5 3.2 4.0 5.0 5.85.8电流(A)25~4.40~60 50~80100~130160~210200~270260~300注:立焊、横焊、仰焊时焊接电流应比平时小10%~20%。
2)焊条直径焊条直径一般根据构件厚度及焊接位置来选择。
平焊时焊条直径可以选择大些,立焊时焊条直径不大于5mm,仰焊和横焊时最大焊条直径为4mm,多层焊及坡口第一层焊缝使用的焊条直径为3.2~4mm.焊条直径的选择焊件厚度(mm)2336~12≥13焊条直径(mm)2 3.2 3.2~44~54~62. 埋弧自动焊埋弧自动焊焊接规范的主要参数有:焊接电源、电弧电压、焊接速度、焊丝直径及焊丝伸出长度等。
焊丝的直径大,焊缝的熔宽会增加,熔深则稍有下降;焊丝直径越小,熔深相应增加。
一般大型工件多采用4~5mm直径的焊丝。
不同的焊丝直径应用不同的焊接电流范围焊件厚度(mm)23456焊条电流(A)200~400 300~600500~800700~1000800~1200焊接电流与相应的电弧电压焊接电流(A)600~700700~850850~10001000~1200电弧电压(V)36~3838~4040~4242~44焊接速度的变化,将直接影响电弧热量的分配情况,即影响线能量的大小。
在其他参数不变时,焊接速度增加,热输入量减少,熔宽明显变窄。
当焊接速度超过40m/h时,由于热输入量减少的影响,焊接缝会出现磁偏吹、吹边、气孔等缺陷。
焊接速度过低时,易产生类似过高的电弧电压的缺陷。
3. CO2气体保护焊主要规范参数:焊接电流、电弧电压、焊丝直径、焊接速度、焊丝伸出长度、气体流量等。
焊丝直径主要是根据工件厚度来选择。
一般薄板采用¢0.8~1.0mm的焊丝焊接。
中厚板应选用¢1.2~2.0mm的焊丝焊接。
导线焊接标准
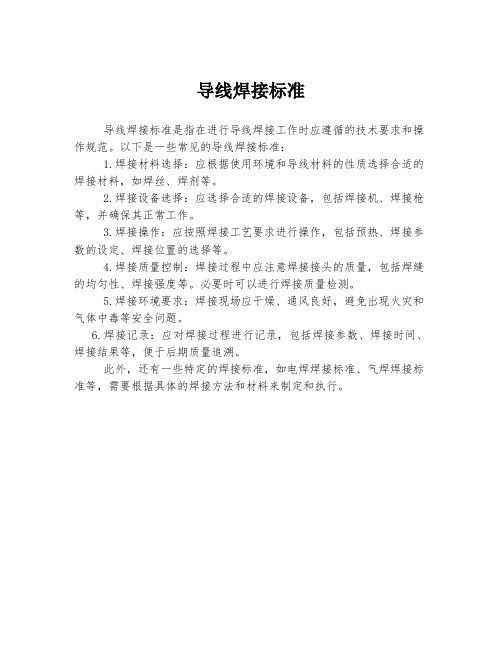
导线焊接标准
导线焊接标准是指在进行导线焊接工作时应遵循的技术要求和操作规范。
以下是一些常见的导线焊接标准:
1.焊接材料选择:应根据使用环境和导线材料的性质选择合适的焊接材料,如焊丝、焊剂等。
2.焊接设备选择:应选择合适的焊接设备,包括焊接机、焊接枪等,并确保其正常工作。
3.焊接操作:应按照焊接工艺要求进行操作,包括预热、焊接参数的设定、焊接位置的选择等。
4.焊接质量控制:焊接过程中应注意焊接接头的质量,包括焊缝的均匀性、焊接强度等。
必要时可以进行焊接质量检测。
5.焊接环境要求:焊接现场应干燥、通风良好,避免出现火灾和气体中毒等安全问题。
6.焊接记录:应对焊接过程进行记录,包括焊接参数、焊接时间、焊接结果等,便于后期质量追溯。
此外,还有一些特定的焊接标准,如电焊焊接标准、气焊焊接标准等,需要根据具体的焊接方法和材料来制定和执行。
焊接工艺规程
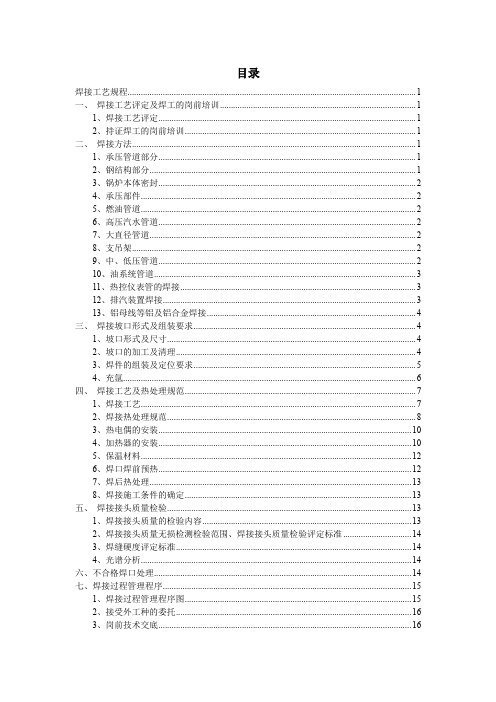
目录焊接工艺规程 (1)一、焊接工艺评定及焊工的岗前培训 (1)1、焊接工艺评定 (1)2、持证焊工的岗前培训 (1)二、焊接方法 (1)1、承压管道部分 (1)2、钢结构部分 (1)3、锅炉本体密封 (2)4、承压部件 (2)5、燃油管道 (2)6、高压汽水管道 (2)7、大直径管道 (2)8、支吊架 (2)9、中、低压管道 (2)10、油系统管道 (3)11、热控仪表管的焊接 (3)12、排汽装置焊接 (3)13、铝母线等铝及铝合金焊接 (4)三、焊接坡口形式及组装要求 (4)1、坡口形式及尺寸 (4)2、坡口的加工及清理 (4)3、焊件的组装及定位要求 (5)4、充氩 (6)四、焊接工艺及热处理规范 (7)1、焊接工艺 (7)2、焊接热处理规范 (8)3、热电偶的安装 (10)4、加热器的安装 (10)5、保温材料 (12)6、焊口焊前预热 (12)7、焊后热处理 (13)8、焊接施工条件的确定 (13)五、焊接接头质量检验 (13)1、焊接接头质量的检验内容 (13)2、焊接接头质量无损检测检验范围、焊接接头质量检验评定标准 (14)3、焊缝硬度评定标准 (14)4、光谱分析 (14)六、不合格焊口处理 (14)七、焊接过程管理程序 (15)1、焊接过程管理程序图 (15)2、接受外工种的委托 (16)3、岗前技术交底 (16)4、焊接施工监督 (16)5、热处理 (16)6、外观检查 (16)7、无损探伤 (16)八、质量检查及验收 (17)1、焊接工程质量检查内容 (17)2、焊接质量验收程序及组织 (17)3*150T/H锅炉安装工程焊接工艺规程************有限公司一、焊接工艺评定及焊工的岗前培训1、焊接工艺评定1.1焊接工艺评定依据以《焊接工艺评定规程》DL/T868-2014为依据,进行焊接工艺评定。
1.2焊接工艺评定要求工艺评定做到满足现场要求,数据准确,保证焊接施工质量。
焊接参数规范
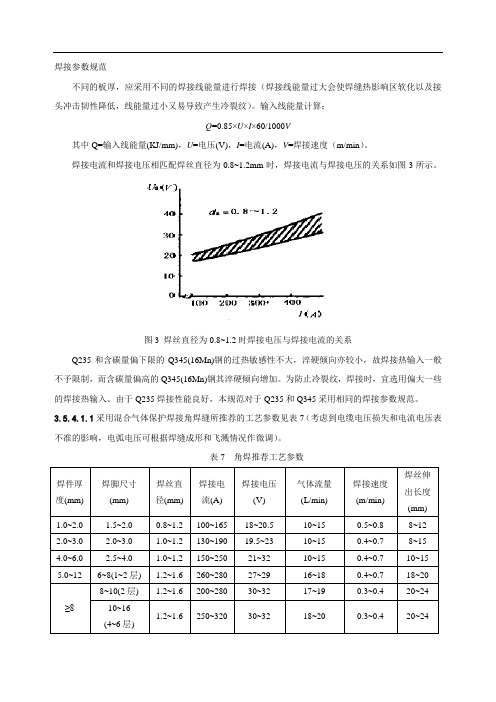
焊接参数规范不同的板厚,应采用不同的焊接线能量进行焊接(焊接线能量过大会使焊缝热影响区软化以及接头冲击韧性降低,线能量过小又易导致产生冷裂纹)。
输入线能量计算:Q=0.85×U×I×60/1000V其中Q=输入线能量(KJ/mm),U=电压(V),I=电流(A),V=焊接速度(m/min)。
所示。
焊接电流和焊接电压相匹配焊丝直径为0.8~1.2mm时,焊接电流与焊接电压的关系如图3Q235和含碳量偏下限的Q345(16Mn)钢的过热敏感性不大,淬硬倾向亦较小,故焊接热输入一般不予限制,而含碳量偏高的Q345(16Mn)钢其淬硬倾向增加。
为防止冷裂纹,焊接时,宜选用偏大一些的焊接热输入。
由于Q235焊接性能良好,本规范对于Q235和Q345采用相同的焊接参数规范。
3.5.4.1.1采用混合气体保护焊接角焊缝所推荐的工艺参数见表7(考虑到电缆电压损失和电流电压表不准的影响,电弧电压可根据焊缝成形和飞溅情况作微调)。
表7 角焊推荐工艺参数3.5.4.1.2对接焊一般应开坡口,采用Ф1.2mm焊丝、混合气体保护焊所推荐的工艺参数见表8(考虑到电缆电压损失和电流电压表不准的影响,电弧电压可根据焊缝成形和飞溅情况作微调)。
表8 不同板厚的对接焊推荐工艺表9 对接焊推荐工艺参数3.6焊接典型接头焊接3.6.1Q235钢及Q345钢典型接头推荐规范:对接焊:对接焊坡口如图5所示,每层不超过4mm,δ≤8的开V型坡口,焊接参数规范参见表10,表10 6mm 板开V 型坡口对接焊规范焊缝层道 电流 (A) 电压 (V) 气体流量(L/min) 焊丝伸出长度(mm) 线能量(KJ/mm) 接头型式打底 190~210 19~20 15~25 15~20 0.6~1.2δ=6坡口角度 40~55°其余180~20020~2215~2515~20表11 12mm 板开X 型坡口对接焊规范焊缝层道 电流(A)电压 (V) 气体流量(L/min) 焊丝伸出长度(mm) 线能量(KJ/mm)焊接层次打底 180~200 20~22 15~25 15~20 1.2~1.5 δ=12 坡口角度 40~60°,3~4道其余 280~300 30~33 15~25 15~20 1.2~1.8 盖面200~240 21~2615~2515~201.2~1.5对接焊,δ>10Habd图5 对接接头K 形坡口表12 12mm 板开K 型坡口对接焊规范焊角>8时,盖面层需多道焊,后道焊缝必须覆盖前道焊缝一半以上,具体层数根据焊角高决定。
焊接工艺规范及焊接通用工艺参数
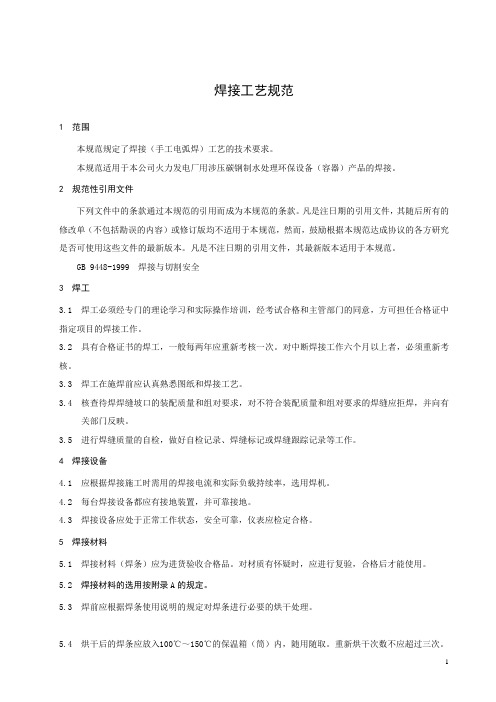
焊接工艺规范1 范围本规范规定了焊接(手工电弧焊)工艺的技术要求。
本规范适用于本公司火力发电厂用涉压碳钢制水处理环保设备(容器)产品的焊接。
2 规范性引用文件下列文件中的条款通过本规范的引用而成为本规范的条款。
凡是注日期的引用文件,其随后所有的修改单(不包括勘误的内容)或修订版均不适用于本规范,然而,鼓励根据本规范达成协议的各方研究是否可使用这些文件的最新版本。
凡是不注日期的引用文件,其最新版本适用于本规范。
GB 9448-1999 焊接与切割安全3 焊工3.1 焊工必须经专门的理论学习和实际操作培训,经考试合格和主管部门的同意,方可担任合格证中指定项目的焊接工作。
3.2 具有合格证书的焊工,一般每两年应重新考核一次。
对中断焊接工作六个月以上者,必须重新考核。
3.3焊工在施焊前应认真熟悉图纸和焊接工艺。
3.4核查待焊焊缝坡口的装配质量和组对要求,对不符合装配质量和组对要求的焊缝应拒焊,并向有关部门反映。
3.5进行焊缝质量的自检,做好自检记录、焊缝标记或焊缝跟踪记录等工作。
4 焊接设备4.1 应根据焊接施工时需用的焊接电流和实际负载持续率,选用焊机。
4.2 每台焊接设备都应有接地装置,并可靠接地。
4.3 焊接设备应处于正常工作状态,安全可靠,仪表应检定合格。
5 焊接材料5.1 焊接材料(焊条)应为进货验收合格品。
对材质有怀疑时,应进行复验,合格后才能使用。
5.2 焊接材料的选用按附录A的规定。
5.3 焊前应根据焊条使用说明的规定对焊条进行必要的烘干处理。
5.4 烘干后的焊条应放入100℃~150℃的保温箱(筒)内,随用随取。
重新烘干次数不应超过三次。
6 焊前准备6.1 坡口加工材料为碳素钢的坡口可采用冷加工或热加工方法制备。
6.2 焊接坡口应符合图样规定。
6.3 焊接坡口应保持平整,不得有裂纹、分层、夹渣等缺陷。
6.4 焊前应将坡口表面及两侧的水、氧化物、油污、锈、熔渣等杂质清除干净。
清理范围为:对接焊缝坡口表面及两侧(距坡口边20mm宽度范围内);角焊缝焊脚尺寸K + 10mm~20mm。
焊接工艺参数
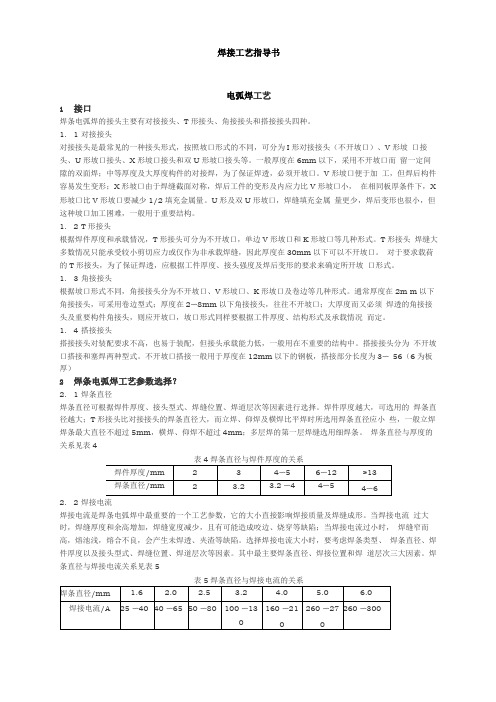
焊接工艺指导书电弧焊工艺1接口焊条电弧焊的接头主要有对接接头、T形接头、角接接头和搭接接头四种。
1. 1 对接接头对接接头是最常见的一种接头形式,按照坡口形式的不同,可分为I形对接接头(不开坡口)、V形坡口接头、U形坡口接头、X形坡口接头和双U形坡口接头等。
一般厚度在6mm以下,采用不开坡口而留一定间隙的双面焊;中等厚度及大厚度构件的对接焊,为了保证焊透,必须开坡口。
V形坡口便于加工,但焊后构件容易发生变形;X形坡口由于焊缝截面对称,焊后工件的变形及内应力比V形坡口小,在相同板厚条件下,X 形坡口比V形坡口要减少1/2填充金属量。
U形及双U形坡口,焊缝填充金属量更少,焊后变形也很小,但这种坡口加工困难,一般用于重要结构。
1. 2 T形接头根据焊件厚度和承载情况,T形接头可分为不开坡口,单边V形坡口和K形坡口等几种形式。
T形接头焊缝大多数情况只能承受较小剪切应力或仅作为非承载焊缝,因此厚度在30mm以下可以不开坡口。
对于要求载荷的T形接头,为了保证焊透,应根据工件厚度、接头强度及焊后变形的要求来确定所开坡口形式。
1. 3 角接接头根据坡口形式不同,角接接头分为不开坡口、V形坡口、K形坡口及卷边等几种形式。
通常厚度在2m m以下角接接头,可采用卷边型式;厚度在2〜8mm以下角接接头,往往不开坡口;大厚度而又必须焊透的角接接头及重要构件角接头,则应开坡口,坡口形式同样要根据工件厚度、结构形式及承载情况而定。
1. 4 搭接接头搭接接头对装配要求不高,也易于装配,但接头承载能力低,一般用在不重要的结构中。
搭接接头分为不开坡口搭接和塞焊两种型式。
不开坡口搭接一般用于厚度在12mm以下的钢板,搭接部分长度为3〜56(6为板厚)2焊条电弧焊工艺参数选择?2. 1 焊条直径焊条直径可根据焊件厚度、接头型式、焊缝位置、焊道层次等因素进行选择。
焊件厚度越大,可选用的焊条直径越大;T形接头比对接接头的焊条直径大,而立焊、仰焊及横焊比平焊时所选用焊条直径应小些,一般立焊焊条最大直径不超过5mm,横焊、仰焊不超过4mm;多层焊的第一层焊缝选用细焊条。
焊接导线的处理工艺

焊接导线的处理工艺焊接导线的处理工艺是指在焊接前对导线进行处理和准备的一系列工艺措施,以确保焊接质量和可靠性。
下面将详细介绍焊接导线的处理工艺。
一、焊接导线的材料选择和准备焊接导线的材料通常是铜或铝,选择合适的材料对焊接的质量和可靠性有着重要影响。
铜导线具有导电性能好、耐腐蚀性能强等优点,因此常被用作焊接导线。
在选择焊接导线材料时,需要考虑导线的直径和长度等因素。
导线的直径应根据焊接的具体要求来确定,一般情况下,导线直径越大,能承受的电流越大,但也会增加焊接工艺的难度。
导线的长度要根据实际需要来确定,过长的导线会增加焊接电阻,影响焊接效果。
在进行焊接前,需要对导线进行清洁处理,以去除表面的油污、氧化物或其他杂质,保证焊接的质量。
清洁处理可以采用化学方法、机械方法或喷砂方法等,具体方法根据导线的材料和污染程度来确定。
二、焊接导线的焊接工艺1. 焊接方法的选择焊接导线的常用方法包括手工弧焊、气体保护焊、电阻焊等。
不同的焊接方法适用于不同的导线材料和焊接要求。
手工弧焊适用于较小粗细的导线,气体保护焊适用于较大粗细的导线,电阻焊适用于高速焊接和大批量焊接。
2. 焊接工艺参数的选择焊接工艺参数的选择是确保焊接质量的关键。
焊接工艺参数包括焊接电流、焊接电压、焊接速度、焊接角度等。
这些参数的选择应根据导线直径、材料、焊接要求和设备性能来确定。
焊接电流和电压的选择要根据导线的直径和材料来确定,焊接速度的选择要根据焊接工艺要求来确定,焊接角度的选择要根据焊接电弧的稳定性来确定。
3. 焊接过程的控制焊接过程中需要严格控制焊接参数,以确保焊接质量。
焊接时要保持焊接电弧的稳定,控制好焊接速度,避免过快或过慢。
焊接完毕后,要对焊接点进行检查,确保焊接质量合格。
三、焊接导线的检测和修复焊接完毕后,需要对焊接质量进行检测和修复。
常用的检测方法包括外观检查、测量电阻和断丝检测等。
外观检查主要是检查焊点的形状和焊剂的均匀性,测量电阻主要是确定焊接点的电阻值是否符合要求,断丝检测主要是检查焊接点的可靠性。
焊线关键参数范围

1.主题内容:规范焊接参数范围2.适用范围:ASM-Eagle60 \ASM-Ihawk3键工艺参数范围:预热温度(Preheat Temperature):150℃-170℃。
焊区温度(Bond Site Temperature):150℃-180℃。
参数:名称1st 2nd Base Parameters1.Contace Time(ms) 超声波时间0-5 0-52. Contace Power(Dac) 超声波功率0-60 0-603. Contace Force(g) 超声波压力50-100 80- 120 BOSB Ball Conrol1. Loop Base /Ball Offset 回拉高度/植球后焊针偏移10-30 -30-102.Ball Thickness (um) 球厚度0-103.Scrub Distace 磨砂距离0-104.Tail Length 线尾长度45-655.Time Base1/2 植球焊接时间10-15 0-56.Power Base1/2 植球焊接功率80-120 35-657.Force Base1/2 植球焊接压力45-85 25-50BOSB wire Contor0.2nd BondPt offset 二焊点偏移补偿35-753.Base Time1/2 植球焊线时间10-15 0-54.Base Power1/2 植球焊线功率90-120 35-655.Base Force1/2 植球焊线压力45-85 25-50EFO Parameters1.Wire Size 线尺寸102.Gap Wide Waring V olt 烧球间隙(华林伏)4500-50003.EFO Current(*0.01) 打火电流3800-50004.EFO Time 打火时间1000-15005.Ball Thickness 球厚度6-8Loop Parameters (Q)Auto LoopLoop Height(mils) 线弧高度7-14Neck/Revers e Angle 颈部/反向ê角度50-80 0-30 LHT Correction/Scale OS 放线补偿/整体放大设定0-10 0-5 Pull Ratio 推动率0-15%核准:审核:制定:。
- 1、下载文档前请自行甄别文档内容的完整性,平台不提供额外的编辑、内容补充、找答案等附加服务。
- 2、"仅部分预览"的文档,不可在线预览部分如存在完整性等问题,可反馈申请退款(可完整预览的文档不适用该条件!)。
- 3、如文档侵犯您的权益,请联系客服反馈,我们会尽快为您处理(人工客服工作时间:9:00-18:30)。
焊线工艺规范1 范围 (2)2 工艺 (2)3 焊接工艺参数范围 (3)4 工艺调试程序 (5)5 工艺制具的选用 (6)6 注意事项 (8)1 范围1.1 主题内容本规范确定了压焊的工艺能力、工艺要求 .工艺参数、工艺调试程序、工艺制具的选用及注意事项。
1.2 适用范围1.2.1 ASM-Eagle60. k&s1488机型。
1.2.2 适用于目前在线加工的所有产品。
2 工艺2.1 工艺能力2.1.1 接垫最小尺寸:45µm×45µm2.1.2 最小接垫节距(相邻两接垫中心间距离):≥60µm2.1.3 最低线弧高度:≥6 mil2.1.4 最大线弧长度:≤7mm2.1.5 最高线弧高度:16mil2.1.6 直径:Eagle60:Ф18—75um , K&S1488: Ф18—50um2.2 工艺要求2.2.1 键合位置2.2.1.1 键合面积不能有1/4以上在芯片压点之外,或触及其他金属体和没有钝化层的划片方格。
2.2.1.2 在同一焊点上进行第二次键合,重叠面积不能大于前键合面积的1/3。
2.2.1.3 引线键合后与相邻的焊点或芯片压点相距不能小于引线直径的1倍。
2.2.2 焊点状态2.2.2.1 键合面积的宽度不能小于引线直径的1倍或大于引线直径的3倍。
2.2.2.2 焊点的长度:键合面积的长度不能小于引线直径的1倍或大于引线直径的4倍。
2.2.2.3 不能因缺尾而造成键合面积减少1/4,丝尾的总长不能超出引线直径的2倍。
2.2.2.4 键合的痕迹不能小于键合面积的2/3,且不能有虚焊和脱焊。
2.2.3 弧度2.2.3.1 引线不能有任何超过引线直径1/4的刻痕、损伤、死弯等。
2.2.3.2 引线不能有任何不自然拱形弯曲,且拱丝高度不小于引线直径的6倍,弯屏后拱丝最高点与屏蔽罩的距离不应小于2倍引线直径。
2.2.3.3 不能使引线下塌在芯片边缘上或其距离小于引线直径的1倍。
2.2.3.4 引线松动而造成相邻两引线间距小于引线直径的1倍或穿过其他引线和压点。
2.2.3.5 焊点与引线之间不能有大于30º的夹角。
2.2.4 芯片外观2.2.4.1 不能因键合而造成芯片的裂纹、伤痕和铜线短路。
2.2.4.2 芯片表面不能有因键合而造成的金属熔渣、断丝和其他不能排除的污染物。
2.2.4.3 芯片压点上不能缺丝、重焊或未按照打线图的规定造成错误键合。
2.2.5 键合强度2.2.5.1 对于25um线径拉力应大于5g,23um线径大于4g,30um铜线大于7g注: 当作破坏性试验时,断点不应发生在焊点上。
2.2.5.2 对于25um线径,要求铜球剪切力大于25g.2.2.6 框架不能有明显的变形,管脚.基岛镀层表面应致密光滑,色泽均匀呈银白色,不允许有沾污.水迹.斑点.异物.发花.起皮.起泡等缺陷.3. 焊接工艺参数3.1 关键工艺参数范围3.1.1 ASM-Eagle60焊线机预热温度(Preheat Temperature):220℃-230℃。
焊区温度(Bond Site Temperature):230℃-240℃。
EFO ParametersK&S1488焊线机预热温度(Preheat Temperature):220℃-230℃焊区温度(Bond Site Temperature)230℃-250℃注:Wire Size根据铜线标称线径设置4 工艺调试程序:4.1 工艺调试员基本职责4.1.1 工艺调试员职责4.1.1.1 以―品质‖和―UPH‖为工作重点。
4.1.1.2 从工艺方面着手逐步消除影响品质和UPH的因素。
4.1.1.3 进行过程监控。
4.1.1.4 协助主管工作。
4.1.1.5 监控当班期间工艺参数的适应性并作适当调整。
4.1.1.6 监控当班期间劈刀状况并更换。
4.1.1.7 夹具更换,调试和维护。
4.1.1.8 填写相关记录。
4.2 工艺监控程序:4.2.1 监控人:工艺调试员,工艺工程师。
4.2.2 监控项目及参数4.2.2.1 第一点时间(T1)。
4.2.2.2 第一点功率(P1)。
4.2.2.3 第一点压力(F1)。
4.2.2.4 第一点功率输出方式。
4.2.2.5 第二点时间(T2)。
4.2.2.6 第二点功率(P2)。
4.2.2.7 第二点压力(F2)。
4.2.2.8 第二点功率输出方式。
4.2.2.9 弧高。
4.2.2.10 反弧。
4.2.2.11 弧度因素。
4.2.2.12 烧球尺寸(BS)。
4.2.2.13 线径尺寸(WS)。
4.2.2.14 预热时间(HT1)。
4.2.2.15 加热时间(HT2)。
4.2.2.16 预热温度。
4.2.2.17 焊区温度。
4.2.2.18 劈刀打线总数。
4.2.2.19 规定的首件检验项目。
4.2.3 监控时机:4.2.3.1 更换型号后。
4.2.3.2 设备重新调试.维修后。
4.2.3.3 交接班后。
4.2.3.4 换劈刀.铜丝后。
4.2.3.5 新材料、新工艺投入生产后。
4.2.4 工艺调试员作业依据4.2.4.1 《压焊作业指导书》。
4.2.4.2 《ASM焊线机使用手册》。
4.2.4.3 本文件中的相关条款。
5. 工艺制具的选用5.1 劈刀选用指导劈刀的选用应综合铜线线径、铝垫尺寸、铝垫间距、相邻弧高等因素来考虑。
5.1.1 根据线径,选用劈刀孔径(H)估算公式为孔径(H)=铜丝线径+经验值(0.5~0.8mil)应用范例:5.1.1.1 采用Φ23-Φ25µm线径产品,选用孔径(H)为30µm劈刀如:UTS-30IE-CM-1/16-XL或UTS-30HE-CM-1/16-XL。
K&S:CU-N8-1224-R35。
5.1.1.2 采用Φ38-Φ42µm铜丝的产品,选用孔径为46-56µm的劈刀如:UTS-46JI-CM-1/16-XL或UTS-56LJ-CM-1/16-XL.5.1.2 根据铝垫尺寸选用内倒角直径(CD)大小估算公式为内倒角直径(CD)=铝垫尺寸-经验值(0.8~0.9mil)5.1.3 根据铝垫间距选用劈刀头部直径(T)的大小估算公式头部直径(T)=2×铝垫间距- 平均金球直径5.1.3.1 铝垫间距>110µm产品可灵活选用UTS或CU―打头‖的劈刀。
5.1.4 根据相邻弧高和相邻间距选用劈刀头部形状5.1.4.1 如果相邻间距≤120µm产品,一般选用CU―打头‖劈刀。
5.1.4.2 如果相邻间距>120µm产品,一般选用UTS ―打头‖劈刀。
5.2 附录 (SPT)1.TIP Stype 劈刀头部类型11.Main Taper Angle(MTA)外端面锥度(外端面夹角)2.Face Angle 头部端面角10.Tool Length 劈刀长度3.Chamfer Angle 内倒角角度9. Tool Diameter 劈刀外圆直径4.Hole Size 内孔直径8. Finish 表面处理状况5.Tip Diameter 劈刀头部直径7. Materiai 材料6.Chamfer Diameter倒角直径1.ip Stype:SBN – Fine Pitch with to deg Slinline Bottleneck(for T≤µm).[细间距,瓶颈端面角为100(T<165µm)]UT –Standard capillary with Face Angle for non-Fine Pitch application.[普通型劈刀不适于细间距焊接使用]CSA–Standard capillary with a 00 Face Angle for nin-Fine Pitchapplication.[普通型劈刀,头部端面角为00,FA=00不适于细间距焊接使用]2.Face Angle:Z-00 F-40 S-80 E-110 [FA--头部端面角]3. Chamfer Angle:Standard-900(no need to specify) [内倒角角度:标准为900 ]4.Hole Size5.Tip Diameter6.Chamfer Diameter25 µm (.0010") W=70 µm (.0028") A=35 µm (.0014")28 µm (.0011") Y=75 µm (.0030") B=41 µm (.0016")30 µm (.0012") Z=80 µm (.0032") C=46 µm (.0018")33 µm (.0013") A=90 µm (.0035") D=51 µm (.0020")35 µm (.0014") B=100 µm (.0039") E=58 µm (.0023")38 µm (.0015") C=110 µm (.0043") F=64 µm (.0025")41 µm (.0016") D=120 µm (.0047") G=68 µm (.0027")43 µm (.0017") E=130 µm (.0051") H=74 µm (.0029")46 µm (.0018") F=140 µm (.0055") I=78 µm (.0031")51 µm (.0020") G=150 µm (.0059") J=86 µm (.0034")56 µm (.0022") H=165 µm (.0065") K=92 µm (.0036")64 µm (.0025") I=180 µm (.0071") L=100 µm (.0039")68 µm (.0027") J=200 µm (.0079) M=114 µm (.0045")75 µm (.0030") K=225 µm (.0089") N=127 µm (.0050")5.4 压焊夹具选用:5.4.1 压焊夹具选用依据5.4.1.1 各机型夹具配置。