发泡模具工艺流程
发泡成型模具

顶出机构的设计
顶出面积应尽量大,以减少单位面积上的顶 出力,否则会使塑件凹入变形。推杆直径要 比普通注塑模的推杆大20%~30%。
冷却系统的设计
为了冷却均匀,应使冷却水先流经浇口附近, 由最终充填处排出,以免产生发泡不均匀的 缺陷。
排气槽的设计
由于发泡剂分解产生较多的气体,如果不及 时排气,会影响塑料熔体流动,造成填充不 足。 排气槽一般设在分型面上。
浇注系统的设计
(1)主流道 ) 由于发泡材料的冷却速度较慢,故在主流道 外部一般要设置冷却水道。
(2)分流道 注射时要尽量使熔融塑料在注入型腔前不发 泡,所以分流道应尽量短,断面尺寸要比普 通注塑模大。断面形状一般为圆形,大型塑 件分流道直径可选6~10mm,小型塑件直径 可选4~6mm。
流道设计
2.2 注塑成型模具
1 发泡注射成型模具基本结构 注塑成型模具主要由凹模,凸模,成型芯, 导柱,导套等组成。其内部结构(浇注系统) 可分为模腔,流道,分流道,浇口,排气 口,冷料井等。
低发泡注射成型模的基本结构与普通注射成型模具 基本相同,其设计方法也与注射成型模具极为类似。 由于发泡材料的物理性质与非发泡料材有所不同, 因此在个别部位的设计上有其特殊要求。 (1)浇注系统 (2)型腔排气 (3)冷却系统 (4)脱模机构 (5)型腔数
发泡塑料的注塑成型模具
1 概述
泡沫塑料的加工方法和普通塑料加工方法基 本相同,所有设备和普通塑料加工设备基本 相同。可以用挤出法,模压法,注塑法,压 延法等。
2.注塑成型
注塑成型为一次性成型方法,生产效率高, 制品质量好,适用于形状复杂,尺寸要求较 严格的泡沫塑料制品。
2.1 注塑成型过程
将物料及发泡剂加入料斗内,通过螺杆的旋 转和外部加热作用,使其受热熔化至流动状 态。熔融塑料通过喷嘴射出,注入一个温度 较低的闭合模具中,经冷却硬化,即可保持 模具型腔所赋予的型样,开启模具即得到制 品。
发泡模与搪塑模的制备讲诉

二、发泡模结构及分类 – 产品特点2
2、产品特点要求:
L
切割 位置 充气密 封条
骨架:足够的工艺边用于密封 充气密封条工艺边 L>20mm 一般密封条工艺边L>15mm 硬密封L>5mm
有充气密封条过渡的凸圆角>R11;凹>R6
★ 硬密封常用于闭模浇注 ★ 充气密封条直径一般为10mm & 8mm ★ 普通密封条可使用D6或矩形 ★ 硬密封一般两种形式,a、骨架上增加凸筋, 与表皮0.2mm过 盈配合;b、模具上增加凸台
定位槽和凸台
模具公司
Tool Shop
二、发泡模结构及分类 – 零件类
4、汽车内饰常用发泡零件 仪表板
门板嵌饰板
扶手 方向盘 座椅 ……
模具公司
Tool Shop
二、发泡模结构及分类 – 发泡模分类
5、按浇注类型分类 开模浇注
闭模浇注
按表皮分类 搪塑表皮 真空吸附成型表皮 无表皮发泡,真皮包袱 按发泡区域分类 整体发泡
模具公司
Tool Shop
三、发泡模制造过程简述– 铝模翻砂
由于发泡模单件生产地性 质,铸铝模型一般用聚苯 乙烯泡沫制成(白泡), 泡沫密度越高越好。 采用重力浇注等常规浇注 方案,应将水管布局所占 区域在泡沫上加工出来; 常用水管为内径12mm,外 径14mm不锈钢钢管,泡沫 预留28mm凸起,能满足水 管铸造空间完全被包裹3 采用消失模铸造,水管弯 折在泡沫模型上,并用泡 沫碎末混合胶水包覆水管, 该方法难度较高 翻砂制成件 红色为环氧层
滑块 环氧层
密封条放置槽 加热水管
镶块
上模
滑块
气缸
下模
气缸
发泡模与搪塑模的制备
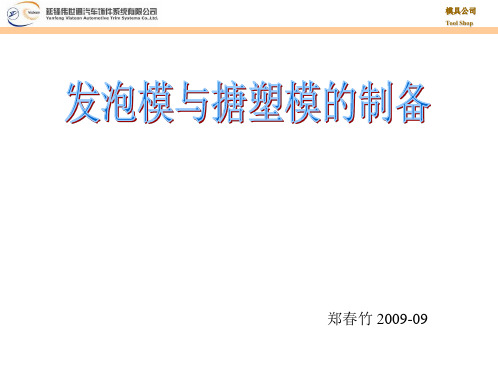
滑块、抽芯、镶块 等结构分型边界均 应放置在圆角上
模具公司
Tool Shop
用分析工具找出倒勾面,确定 脱模结构,方法同设计注塑模
模具公司
Tool Shop
二、发泡模结构及分类
–
型腔系统2
表皮真空抽气槽 充气密封条
滑块环氧层
6、发泡模型腔系统
表皮
②环氧层厚度5-8mm;
铸铝厚度15-20mm;
③在表皮不易紧密吸附
采用消失模铸造,水管弯 折在泡沫模型上,并用泡 沫碎末混合胶水包覆水管, 该方法难度较高
模具公司
Tool Shop
红色为环氧层
翻砂制成件
三、发泡模制造过程简述– 铝模翻砂
模具公司
Tool Shop
铸造技术提高:
真空铸造技术的应用,能 提高铸件的密度和强度, 减少铸造缺陷
铝模采用真空铸造是发泡 模制造的趋势
模具公司
Tool Shop
二、发泡模结构及分类 – 产品特点2
2、产品特点要求: 骨架:足够的工艺边用于密封
充气密封条工艺边 L>20mm
L
切割 位置
一般密封条工艺边L>15mm 硬密封L>5mm
充气密 封条
有充气密封条过渡的凸圆角>R11;凹>R6
R
★ 硬密封常用于闭模浇注 ★ 充气密封条直径一般为10mm & 8mm ★ 普通密封条可使用D6或矩形 ★ 硬密封一般两种形式,a、骨架上增加凸筋,
般先抽有定位凸台和定位槽区域, 其余区域轻微真空,待表皮铺设 准确,再全力抽真空
⑤上模吸盘推荐使用3.5褶皱 的硅胶吸盘,根据骨架形状可采 用伸缩气缸辅助吸附
带伸缩气缸 的吸盘
发泡模与搪塑模的制备解读

⑤上模吸盘推荐使用3.5褶皱 的硅胶吸盘,根据骨架形状可采 用伸缩气缸辅助吸附
带伸缩气缸 的吸盘 普通吸盘
模具公司
Tool Shop
Φ10 &Φ8 二、发泡模结构及分类 – 密封系统
6、密封系统 ①PU料密封:a、根据排气和 工艺需要,采用分段充气密封策 略,侧壁或陡峭斜面推荐采用充 气密封条;b、平坦区域可采用一 般密封条密封;c、密封边界狭窄 区域采用硬密封。 ②滑块之间、滑块与本体之间 均需要严格密封,形成封闭的真 空缝隙;(为了防止密封条在运 动中磨损,设法放置在垂直碰面 上,至少保证斜面45°
模具公司
Tool Shop
一、发泡模生产流程
开模浇注生产流程: ①顶出机构、滑块复位→②铺设表皮(自动感应抽真空吸附) →③ 上模放置骨架(自动感应,吸盘或真空吸附) →④模架旋转(合适 的浇注位置) →⑤浇注→⑥合模→⑦锁模→⑧气垫顶出(加锁模力) →⑨充气密封条充气(根据排气情况分段充气密封) →⑩气垫下降 或充气密封条放气排气(上模真空或吸盘断)→ ⑾合紧模熟化→⑿ 模架旋转至取件状态→⒀开锁、气垫下降(断真空)→⒁开模→⒂ 开模→⒃滑块、抽芯依次打开→⒄顶块将产品顶出→⒅取件……. (切割) 闭模模浇注生产流程: …… → ⑤放置在⑩前;其它过程相似
15~25mm
充气密封 条截面
60 ° 充气密封条进 气接头方式
滑块、本体之间密 封条形状(4*6)
Tool Shop
二、发泡模结构及分类 – 产品特点2
2、产品特点要求:
L
切割 位置 充气密 封条
骨架:足够的工艺边用于密封 充气密封条工艺边 L>20mm 一般密封条工艺边L>15mm 硬密封L>5mm
pu海棉发泡模具方法

pu海棉发泡模具方法
pu海棉发泡模具方法是一种常用的模具制作技术,它采用了聚氨酯材料的优点,具有高强度、优异的耐磨性、耐化学腐蚀性等特点。
下面是pu海棉发泡模具制作的方法:
1. 准备材料:聚氨酯材料、模具结构材料、发泡剂等。
2. 制作模具结构:根据所需的模具形状和尺寸,选择合适的模具结构材料,如木板、铁板等,制作出模具的骨架。
3. 涂刷隔离层:将隔离层涂刷在模具骨架的表面,以防止聚氨酯泡沫粘附在模具骨架上。
4. 喷涂聚氨酯材料:将聚氨酯材料和发泡剂混合后,通过喷涂方式均匀地喷在模具骨架表面,注意聚氨酯材料不要过度喷涂,以免影响模具的质量。
5. 发泡:将喷涂后的模具放置在恰当的环境中进行发泡,一般需要等待几个小时至24小时左右,直到聚氨酯材料完全发泡成型。
6. 去除模具:发泡结束后,将模具从聚氨酯材料中取出,并进行必要的修整和拼接,最终得到所需的pu海棉发泡模具。
以上是pu海棉发泡模具制作的基本步骤,制作过程需要注意安全,避免液体聚氨酯接触皮肤和眼睛,同时还需要控制好聚氨酯材料的喷涂量和发泡时间,以确保模具的质量。
- 1 -。
发泡操作工艺规范
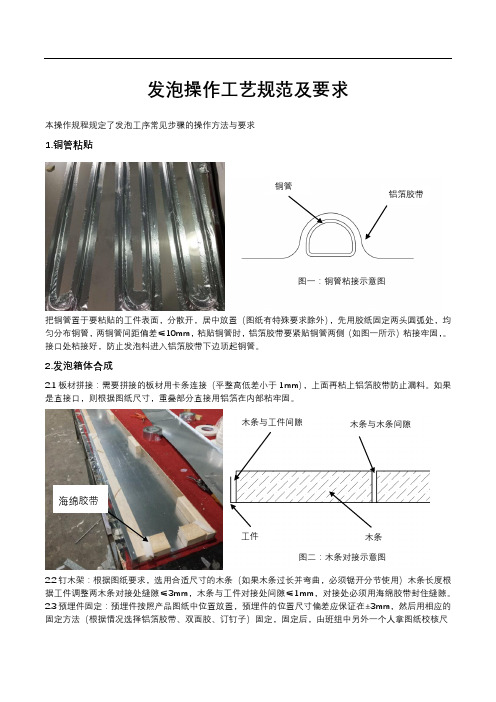
发泡操作工艺规范及要求本操作规程规定了发泡工序常见步骤的操作方法与要求1.铜管粘贴把铜管置于要粘贴的工件表面,分散开,居中放置(图纸有特殊要求除外),先用胶纸固定两头圆弧处,均匀分布铜管,两铜管间距偏差≤10mm ,粘贴铜管时,铝箔胶带要紧贴铜管两侧(如图一所示)粘接牢固,。
接口处粘接好,防止发泡料进入铝箔胶带下边顶起铜管。
2.发泡箱体合成2.1板材拼接:需要拼接的板材用卡条连接(平整高低差小于1mm ),上面再粘上铝箔胶带防止漏料。
如果是直接口,则根据图纸尺寸,重叠部分直接用铝箔在内部粘牢固。
2.2钉木架:根据图纸要求,选用合适尺寸的木条(如果木条过长并弯曲,必须锯开分节使用)木条长度根据工件调整两木条对接处缝隙≤3mm ,木条与工件对接处间隙≤1mm ,对接处必须用海绵胶带封住缝隙。
2.3预埋件固定:预埋件按照产品图纸中位置放置,预埋件的位置尺寸偏差应保证在±3mm ,然后用相应的固定方法(根据情况选择铝箔胶带、双面胶、订钉子)固定,固定后,由班组中另外一个人拿图纸校核尺图一:铜管粘接示意图铝箔胶带铜管 图二:木条对接示意图木条与工件间隙 木条与木条间隙工件 木条海绵胶带寸及件数,防止出现位置不对,漏埋等不良现象。
2.4刷胶:对于不锈钢砂板材质的表面在室温低于20℃时表面必须刷胶,刷胶后放置30min后方可注料。
2.5订钉子:钉子之间的间隙为100mm±10mm,要求:钉子均匀平整。
2.6尺寸校核:工件完全订好后,对照图纸对尺寸校核未注线性公差按照(尺寸1mm∽1500mm 之间为±1mm尺寸1501mm∽4000mm 之间为±2mm)操作,角度未注公差为±1˚。
注:校核尺寸必须量对角。
3.装模(适用于非整体模具)打开模具后,清理干净模具中遗留的发泡料,把工件放入模具中,工件不靠模具侧壁的面要用挡条挡住,模具侧壁工件位置挡板顶杆图三:平板模与直角模具俯视图然后用顶杆顶住(挡条和顶杆可用材料为木条、方管、矩形管等),挡条的长度为被挡的“工件面长度-100mm”厚度为“工件发泡层厚度0-1mm”。
注塑发泡工艺(3篇)

第1篇一、引言注塑发泡工艺是一种广泛应用于塑料制品生产中的成型技术。
它通过在注塑过程中引入发泡剂,使塑料在熔融状态下产生气泡,形成多孔结构,从而降低塑料制品的密度,提高其性能。
本文将详细介绍注塑发泡工艺的原理、流程、设备、应用及优缺点。
二、注塑发泡工艺原理注塑发泡工艺的原理是在塑料熔融状态下,将发泡剂均匀地分布在熔体中,通过化学反应或物理变化,使熔体产生气泡。
这些气泡在注塑过程中逐渐长大,最终形成多孔结构的塑料制品。
发泡剂主要有以下几种类型:1. 气体发泡剂:如二氧化碳、氮气、氩气等,通过化学反应或物理变化产生气泡。
2. 液体发泡剂:如水、醇类等,通过蒸发产生气泡。
3. 固体发泡剂:如碳酸氢钠、碳酸钠等,通过加热分解产生气泡。
4. 混合发泡剂:将多种发泡剂按一定比例混合使用。
三、注塑发泡工艺流程1. 原料准备:选择合适的塑料原料和发泡剂,确保原料质量符合生产要求。
2. 熔融混合:将塑料原料和发泡剂送入注塑机料筒,在高温、高压条件下进行熔融混合。
3. 注塑成型:将熔融混合物注入模具,通过模具冷却、固化,形成多孔结构的塑料制品。
4. 后处理:对注塑成型的塑料制品进行脱模、修整、检验等工序。
5. 包装:将合格的产品进行包装,储存或销售。
四、注塑发泡工艺设备1. 注塑机:用于将塑料原料和发泡剂熔融混合,并注入模具。
2. 模具:用于成型多孔结构的塑料制品。
3. 冷却系统:用于冷却模具,提高生产效率。
4. 辅助设备:如料斗、输送带、自动脱模机等。
五、注塑发泡工艺应用注塑发泡工艺广泛应用于以下领域:1. 家用电器:如冰箱、洗衣机、空调等家电的隔热层、隔音层等。
2. 建筑材料:如保温板、隔音板等。
3. 交通工具:如汽车、船舶、飞机等内饰件。
4. 包装材料:如泡沫塑料托盘、缓冲材料等。
5. 纺织品:如泡沫填充物、运动鞋等。
六、注塑发泡工艺优缺点1. 优点:(1)降低塑料制品密度,减轻产品重量。
(2)提高塑料制品的隔热、隔音性能。
发泡模具设计详解

发泡模具设计详解发泡模具设计详解2016发泡成型的模具就是塑料发泡模具。
将发泡性树脂直接填入模具内,使其受热熔融,形成气液饱和溶液,通过成核作用,形成大量微小泡核,泡核增长,制成泡沫塑件。
常用的发泡方法有三种:物理发泡法,化学发泡法和机械发泡法。
下面一起来看看发泡的模具设计原理,希望对大家的学习有所帮助!一、发泡模成型机的原理1、发泡原材料的种类:EPS,EPP,EPE,EPO等。
2、成型原理:合模,加料,利用蒸汽加热成型,再冷却,脱模。
二、 EPS模具总体结构根据客户机型的种类来设计模具,与客户机台配套。
1、水箱(汽室):三片式模具,客户有标准水箱。
台湾机、方圆机、等机台没有标准水箱,必须根据产品的排模来定水箱,又叫一体模。
2、三片式模具,都具有三片板,分别叫凸模板、凹模板、枪板,凸模板来固定连接凸模型腔,凹模板用来固定连接凹模型腔,枪板也叫做后封板、背板、主要装顶杆套和料枪。
3、压料:为凸模与凹模配合,方便预开加料成型而设计的一种结构,起到预开加料时不跑料。
根据水箱的合模台阶、模板来计算,压料有离空和没有离空两种,没有离空的,凹凸模的压料相同,有离空的,凹模压料加离空等于凸模压料,凹模压料不少于10 mm。
4、法兰边:也就是凹模与凹模板连接处的.空间,方便安装螺丝钉,根据水箱合模台阶和模板来定,一般做到15 mm左右为宜,不能少于10mm,还有一种,从模板下面往上面套,叫反托,反托高度根据模板的厚度来定,如库尔特机型,一般采用反托式,日本机型一般采用正面安装,有法兰边。
5、壁厚:EPP模具的壁厚一般在15 mm左右,EPS模具、EPO 模具的壁厚在8~10 mm之间,EPE模具的壁厚一般在15 mm,除客户特别说明要求。
6、缩水:一般的发泡模具EPS材料的缩水为0.3%(国内)国外0.4%,倍率低的客户要求提供0.25%、0.2%等,EPO材料一般在0.9%~1.0%之间;EPP、EPE材料根据倍率的不同,缩水也不同;EPP、EPE材料又分JSP原料、卡内卡原料等,缩水又不同,所以EPP、EPE 等材料的缩水是客户提供,也可以叫生产原材料厂家提供,如国内两家原料公司,JSP、卡内卡;7、气芯:气芯∮4、∮6、∮8、∮10、∮12等规格,有条型和针孔两种类型,还有一种叫无孔气芯,闷气芯;根据要求分一般气芯,特殊气芯,如条型的,条型直缝为0.25mm~0.4mm的为特殊气芯,一般用线切割加工制作;普通的条型直缝为0.8 mm ~0.7mm;EPS原材料模具,采用针孔气芯比较多,EPP、EPE等原材料模具采用条型气芯比较多,指平面、侧面一般用针孔;气芯按材质分,有铝气芯,铜气芯、不锈钢气芯,常用的是铝气芯,其它根据客户要求来定。
- 1、下载文档前请自行甄别文档内容的完整性,平台不提供额外的编辑、内容补充、找答案等附加服务。
- 2、"仅部分预览"的文档,不可在线预览部分如存在完整性等问题,可反馈申请退款(可完整预览的文档不适用该条件!)。
- 3、如文档侵犯您的权益,请联系客服反馈,我们会尽快为您处理(人工客服工作时间:9:00-18:30)。
发泡模具工艺流程
发泡模具工艺流程是制作发泡模具的一种常见工艺流程,它的主要目的是通过
加热和冷却的过程来使原材料膨胀成为所需形状的模具。
下面将详细介绍发泡模具工艺流程的步骤和注意事项。
第一步:原材料准备
在进行发泡模具工艺流程之前,首先需要准备好适宜的原材料。
常用的原材料
有聚氨酯、聚苯乙烯等。
根据实际需要选择合适的原材料,并确保其质量符合要求。
原材料通常以颗粒或块状形式存在。
第二步:模具准备
在开始制作发泡模具之前,需要准备好模具。
模具的制作可以使用不同材料,
如铝、钢等。
根据实际需要选择合适的模具材料,并进行相关的加工和处理。
模具的设计和制造需要考虑到产品的形状和尺寸,以保证发泡模具的质量和精度。
第三步:注塑
在进行注塑之前,需要将原材料加热至一定的温度。
加热的方式可以是直接加
热或间接加热。
加热后的原材料会变得粘稠,可以通过注射机将其注入到已经准备好的模具中。
注塑过程需要控制注射时间、注射速度等参数,以确保注入的原材料均匀分布并填充整个模具。
第四步:发泡
注塑完成后,需要对模具中的原材料进行发泡处理。
发泡的过程中需要控制好
温度和时间,确保原材料可以膨胀成为所需的模具形状。
温度的控制可以通过加热或冷却来实现,时间的控制可以根据原材料的特性和制品的要求来确定。
经过发泡处理后,原材料会膨胀成为模具的形状。
第五步:冷却
发泡完成后,需要对模具中的制品进行冷却。
冷却的方式可以是自然冷却或强
制冷却。
冷却时间的长短取决于材料的类型和厚度,一般较薄的制品冷却时间较短,而较厚的制品冷却需要较长的时间。
通过冷却,制品可以固化和形成稳定的结构。
第六步:脱模与修整
在冷却完成后,就可以将制品从模具中取出。
脱模需要注意不要造成模具和制
品的损坏。
取出后,可以对制品进行修整和加工,以使其达到最终的要求和标准。
修整的方式包括切割、打磨、修边等。
根据制品的具体要求,选择适当的修整方法,使制品的表面光滑、边缘整齐。
总结:
发泡模具工艺流程是一种常见的制作模具的工艺流程。
其主要步骤包括原材料
准备、模具准备、注塑、发泡、冷却和脱模与修整。
在进行该工艺流程时,需严格控制各个环节的参数,并根据具体要求对制品进行相应的修整。
通过合理操作和严格控制,可以制作出符合要求的发泡模具。