微发泡注塑成型技术(下)
微孔泡沫注塑成型

特 别 设 计 的螺杆
,
美 国 T r e x e l 公 司 在 MI T 微 孔发 泡 概念
,
建 材等 领 域
。
发泡 成 型 工 地 分 散 到 熔 融 的塑 料 中
注 入 模 具 中减 压 发 泡
的制品
。
熔料
的基 础 上
将 微 孑 发 泡 注 射成 型 技 术 实 L
,
有 化学 发 泡 法 和 物 理 发 泡 法
。
般采用
。
:
二
氧化
泡 沫微 孔 的 存在 将 不 会 降低 材 料 的
。
碳
、
氮气
、
氯 甲烷 和 戊 烷 等
采 用物 理
强度
( 2 ) 由于 微 孔 的 存在 使 材 料 中原 有
,
量
,
且 制 品 具 有 密度低
,
,
比强 高
,
,
能
发 泡 注 塑 成 型 需 要 用 专 用 的 注 塑机 和 附
属设备
,
性 能和 更 低 的 密度
的情况 下
,
。
在 力学 性 能 不 损 失
~
重 量 可 降低 1 O 名
、
30%
,
而
。
且 可 减 少 制 品 的翘 曲
收缩 及 内应 力
微 孔 泡 沫 塑 料 注 塑 成 型 可 加 工 多种 聚 合
物
,
~I] P P
、
PS
、
P BT
、
PA及 P E E K等 。
L发 微 孑 泡 注 塑 成 型 工 艺过 程 可 分 为
装 置 及 射 嘴 白锁装 置
微发泡注塑成型
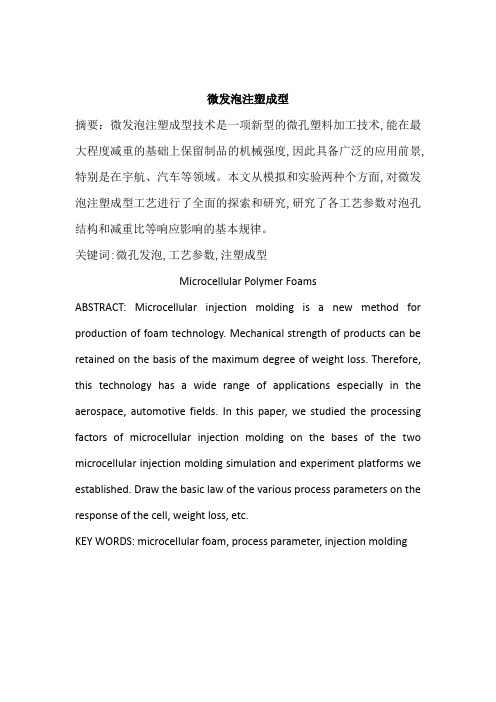
微发泡注塑成型摘要:微发泡注塑成型技术是一项新型的微孔塑料加工技术,能在最大程度减重的基础上保留制品的机械强度,因此具备广泛的应用前景,特别是在宇航、汽车等领域。
本文从模拟和实验两种个方面,对微发泡注塑成型工艺进行了全面的探索和研究,研究了各工艺参数对泡孔结构和减重比等响应影响的基本规律。
关键词:微孔发泡,工艺参数,注塑成型Microcellular Polymer FoamsABSTRACT: Microcellular injection molding is a new method for production of foam technology. Mechanical strength of products can be retained on the basis of the maximum degree of weight loss. Therefore, this technology has a wide range of applications especially in the aerospace, automotive fields. In this paper, we studied the processing factors of microcellular injection molding on the bases of the two microcellular injection molding simulation and experiment platforms we established. Draw the basic law of the various process parameters on the response of the cell, weight loss, etc.KEY WORDS: microcellular foam, process parameter, injection molding1前言微孔发泡技术起源于20世纪80年代美国麻省理工大学,是一项新型的微孔塑料加工技术,其生产制品的最大特点就是泡孔小而密。
高质量低成本的MuCell微发泡注塑成形技术.总结
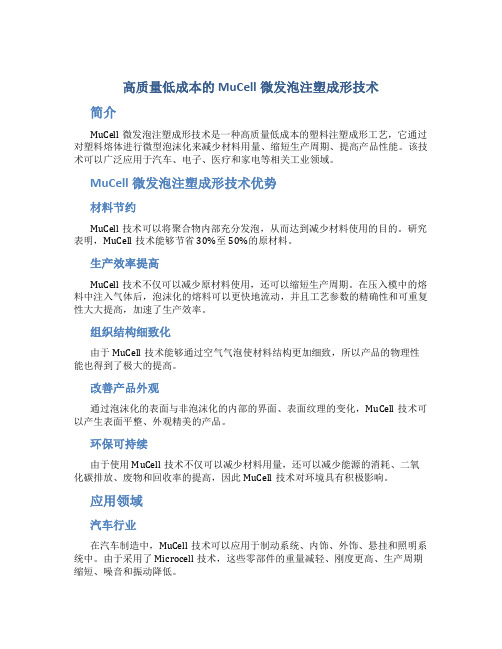
高质量低成本的MuCell微发泡注塑成形技术简介MuCell微发泡注塑成形技术是一种高质量低成本的塑料注塑成形工艺,它通过对塑料熔体进行微型泡沫化来减少材料用量、缩短生产周期、提高产品性能。
该技术可以广泛应用于汽车、电子、医疗和家电等相关工业领域。
MuCell微发泡注塑成形技术优势材料节约MuCell技术可以将聚合物内部充分发泡,从而达到减少材料使用的目的。
研究表明,MuCell技术能够节省30%至50%的原材料。
生产效率提高MuCell技术不仅可以减少原材料使用,还可以缩短生产周期。
在压入模中的熔料中注入气体后,泡沫化的熔料可以更快地流动,并且工艺参数的精确性和可重复性大大提高,加速了生产效率。
组织结构细致化由于MuCell技术能够通过空气气泡使材料结构更加细致,所以产品的物理性能也得到了极大的提高。
改善产品外观通过泡沫化的表面与非泡沫化的内部的界面、表面纹理的变化,MuCell技术可以产生表面平整、外观精美的产品。
环保可持续由于使用MuCell技术不仅可以减少材料用量,还可以减少能源的消耗、二氧化碳排放、废物和回收率的提高,因此MuCell技术对环境具有积极影响。
应用领域汽车行业在汽车制造中,MuCell技术可以应用于制动系统、内饰、外饰、悬挂和照明系统中。
由于采用了Microcell技术,这些零部件的重量减轻、刚度更高、生产周期缩短、噪音和振动降低。
电子和家电行业在电子和家电制造业中,Microcell技术可以用于生产更轻、更细节、更高性能的产品。
例如,通过Microcell技术,可以生产更轻、更细节化的电脑外壳,增加了生产效率和热释放效率。
医疗行业在医疗行业,Microcell技术的应用轻质化各种手术器械、生产更浅薄、更精细的医疗器械等都可以得到很好的应用。
MuCell微发泡注塑成形技术发展趋势目前,该技术的研究和应用一直在不断发展。
在未来,随着人们对环境保护和材料利用率的更高要求,该技术必将得到更广泛和深入的应用。
微发泡注塑成型

微发泡注塑成型工艺目录编辑本段简介微发泡注塑成型工艺,是一种革新的精密注塑技术,微发泡注塑成型工艺突破了传统注塑的诸多局限,可显著减轻制件的重量、缩短成型周期,并极大地改善了制件的翘曲变形和尺寸稳定性。
在生产高质量要求的精密制品上,微发泡注塑成型工艺具有很大的优势。
在注塑成型领域中,Trexel公司的MuCell微发泡成型工艺表现得尤为突出,也是精密成型技术中发展最快、应用最广泛的成型技术之一。
[1]编辑本段技术需求原材料价格不断飙升,对制造相对低廉的亚洲市场带来了巨大的冲击,很多加工商已经开始意识到,即使在中国也不再是廉价制品的产地。
但是另一方面,为了占据有利市场先机,越南、印尼和其他一些国家的供应商却又不得不通过削减价格的方式适应消费者的需求。
然而,随着产品越来越复杂,制件的公差要求和表面外观质量要求也越来越高,采用传统的注塑加工技术生产这些制件,往往会出现多种质量问题,如制品存在较大的内应力、由于收缩不均而导致产品变形等,达不到要求的品质或成本要求。
可以说,塑料加工商遇到了前所未有的挑战,他们迫切需要寻求新的加工技术来改变现在的困境。
精密注塑成型技术越来越受到人们的关注。
微发泡注塑成型工艺,这种技术可以将制件的生产尺寸精度控制在0.01~0.001mm之间,有时甚至能够达到0.001mm以下。
与传统的注塑工艺相比,由该技术生产的制件具有良好的力学性能以及尺寸稳定性,而且制件的尺寸精度和重复精度高,公差范围小。
由于其自身的多种性能优势,加上塑料加工领域的“突变”,为该技术提供了广阔的发展空间。
在对制品规格要求很高的医疗和电子电器领域,精密注塑成型已经发展成为一种非常成熟和完善的注塑工艺。
随着汽车市场的异军突起,司机们在寻找油耗更小的汽车的同时,也更需要配置高精度的汽车配件和修饰件,而这些精密部件的生产同样离不开精密注塑成型工艺。
[2]编辑本段原理图1 MuCell微发泡注塑成型的工艺过程[3]MuCell微发泡成型工艺主要靠气孔的膨胀来填充制品,并在较低且平均的压力下完成制件的成型。
高质量低成本的MuCell微发泡注塑成形技术
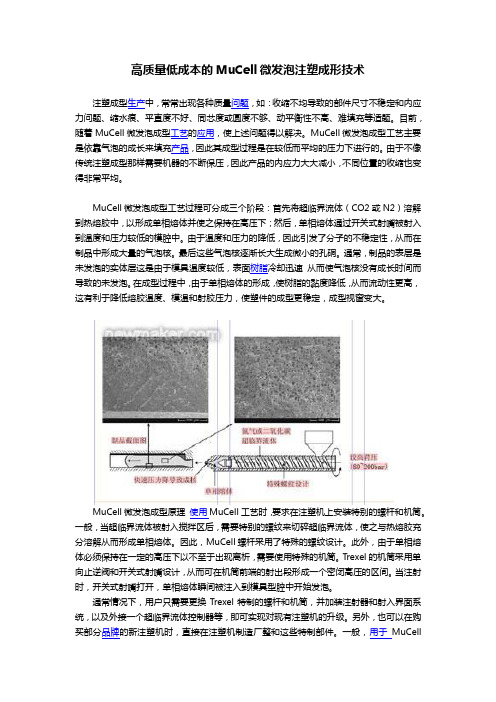
高质量低成本的MuCell微发泡注塑成形技术注塑成型生产中,常常出现各种质量问题,如:收缩不均导致的部件尺寸不稳定和内应力问题、缩水痕、平直度不好、同芯度或圆度不够、动平衡性不高、难填充等适题。
目前,随着MuCell微发泡成型工艺的应用,使上述问题得以解决。
MuCell微发泡成型工艺主要是依靠气泡的成长来填充产品,因此其成型过程是在较低而平均的压力下进行的。
由于不像传统注塑成型那样需要机器的不断保压,因此产品的内应力大大减小,不同位置的收缩也变得非常平均。
MuCell微发泡成型工艺过程可分成三个阶段:首先将超临界流体(CO2或N2)溶解到热熔胶中,以形成单相熔体并使之保持在高压下;然后,单相熔体通过开关式射嘴被射入到温度和压力较低的模腔中。
由于温度和压力的降低,因此引发了分子的不稳定性,从而在制品中形成大量的气泡核。
最后这些气泡核逐渐长大生成微小的孔硐。
通常,制品的表层是未发泡的实体层这是由于模具温度较低,表面树脂冷却迅速从而使气泡核没有成长时间而导致的未发泡。
在成型过程中,由于单相熔体的形成,使树脂的黏度降低,从而流动性更高,这有利于降低熔胶温度、模温和射胶压力,使塑件的成型更稳定,成型视窗变大。
MuCell微发泡成型原理使用MuCell工艺时,要求在注塑机上安装特别的螺杆和机筒。
一般,当超临界流体被射入搅拌区后,需要特别的螺纹来切碎超临界流体,使之与热熔胶充分溶解从而形成单相熔体。
因此,MuCell螺杆采用了特殊的螺纹设计。
此外,由于单相熔体必须保持在一定的高压下以不至于出现离析,需要使用特殊的机筒。
Trexel的机筒采用单向止逆阀和开关式射嘴设计,从而可在机筒前端的射出段形成一个密闭高压的区间。
当注射时,开关式射嘴打开,单相熔体瞬间被注入到模具型腔中开始发泡。
通常情况下,用户只需要更换Trexel特制的螺杆和机筒,并加装注射器和射入界面系统,以及外接一个超临界流体控制器等,即可实现对现有注塑机的升级。
微孔发泡注塑成型技术概述李兵
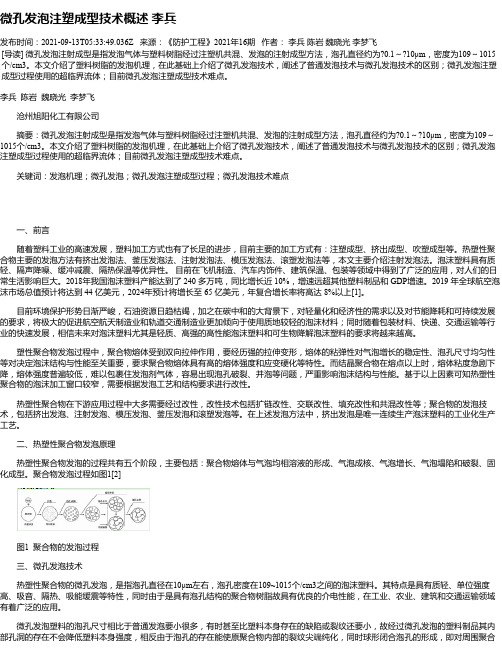
微孔发泡注塑成型技术概述李兵发布时间:2021-09-13T05:33:49.036Z 来源:《防护工程》2021年16期作者:李兵陈岩魏晓光李梦飞[导读] 微孔发泡注射成型是指发泡气体与塑料树脂经过注塑机共混、发泡的注射成型方法,泡孔直径约为?0.1~?10μm,密度为109~1015个/cm3。
本文介绍了塑料树脂的发泡机理,在此基础上介绍了微孔发泡技术,阐述了普通发泡技术与微孔发泡技术的区别;微孔发泡注塑成型过程使用的超临界流体;目前微孔发泡注塑成型技术难点。
李兵陈岩魏晓光李梦飞沧州旭阳化工有限公司摘要:微孔发泡注射成型是指发泡气体与塑料树脂经过注塑机共混、发泡的注射成型方法,泡孔直径约为?0.1~?10μm,密度为109~1015个/cm3。
本文介绍了塑料树脂的发泡机理,在此基础上介绍了微孔发泡技术,阐述了普通发泡技术与微孔发泡技术的区别;微孔发泡注塑成型过程使用的超临界流体;目前微孔发泡注塑成型技术难点。
关键词:发泡机理;微孔发泡;微孔发泡注塑成型过程;微孔发泡技术难点一、前言随着塑料工业的高速发展,塑料加工方式也有了长足的进步,目前主要的加工方式有:注塑成型、挤出成型、吹塑成型等。
热塑性聚合物主要的发泡方法有挤出发泡法、釜压发泡法、注射发泡法、模压发泡法、滚塑发泡法等,本文主要介绍注射发泡法。
泡沫塑料具有质轻、隔声降噪、缓冲减震、隔热保温等优异性。
目前在飞机制造、汽车内饰件、建筑保温、包装等领域中得到了广泛的应用,对人们的日常生活影响巨大。
2018年我国泡沫塑料产能达到了 240 多万吨,同比增长近 10%,增速远超其他塑料制品和 GDP增速。
2019 年全球航空泡沫市场总值预计将达到 44 亿美元,2024年预计将增长至 65 亿美元,年复合增长率将高达 8%以上[1]。
目前环境保护形势日渐严峻,石油资源日趋枯竭,加之在碳中和的大背景下,对轻量化和经济性的需求以及对节能降耗和可持续发展的要求,将极大的促进航空航天制造业和轨道交通制造业更加倾向于使用质地较轻的泡沫材料;同时随着包装材料、快递、交通运输等行业的快速发展,相信未来对泡沫塑料尤其是轻质、高强的高性能泡沫塑料和可生物降解泡沫塑料的要求将越来越高。
微发泡注塑PP及其工艺影响因素
微发泡注塑PP及其工艺影响因素微孔发泡PP是指泡孔分布均匀、泡孔平均直径在1~100m,泡孔密度大约为106~1011个/cm3,材料的密度相比于未发泡削减8~15%的发泡材料,由于微孔发泡PP中的微孔更改了原始聚合物材料中应力的分布以及应力在材料中的传递方式,使得微发泡聚合物表现出有别于其他连续材料的力学特性。
比如具有质轻、比强度高、隔音、冲击强度更高等优点,并且其抗疲乏寿命甚至可以数十倍地提高,同时其绝缘、保温性能等也会大幅度地加添。
因此,微发泡PP特别适用于对材料轻量化要求较高的领域,如汽车、轨道交通,船舶,风机叶片等。
目前,微发泡PP重要有以下几种成型方法:①间歇成型法②连续挤出成型法③注塑成型法。
但是,间歇成型法,生产周期长,不适合应用于大规模工业化;连续挤出成型法虽然可以缩短生产周期,但是连续挤出成型法仅能制造结构简单的制品,限制了其应用范围。
而注塑成型法具有生产周期短,又能制造多而杂结构原件,可在传统注塑机的基础上进行改进,因此是目前工业上重要采纳的方法。
1.微发泡注塑成型技术的工艺与原理注塑成型技术的原理是利用快速更改温度来使聚合物/气体均相体系进行微孔发泡,下图为典型的微孔塑料注塑成型技术的系统结构示意图。
其工艺过程为:聚合物粒料通过料斗加入机筒,通过螺杆的机械摩擦和升温加热器使粒料熔为聚合物熔体,N2或CO2等小分子气体通过计量阀的掌控以肯定的速率注入机筒内的聚合物熔体中(或通过在聚合物中添加化学发泡剂分解产生气体),与聚合物熔体混合均匀,形成聚合物/气体均相体系。
随后,聚合物/气体均相体系由静态混合器进入扩散室,通过分子扩散使体系进一步均化,在这里通过快速升温加热器(例如,在1s内使熔体温度由190℃上升至240℃)使气体在聚合物熔体中的溶解度急剧下降,过饱和气体由熔体中析出形成大量的微小气泡核。
为了抑制扩散室内已形成的气泡核快速生长,扩散室内必需保持高压状态。
在进行注射操作前,模具型腔中充分压缩气体。
物理微发泡注塑成型工艺
物理微发泡注塑成型工艺物理微发泡注塑成型工艺,听起来是不是有点儿高大上?但它就是把塑料变得更轻、更强的一种神奇手法。
想象一下,你手里有一块沉甸甸的塑料,觉得用着可真不方便。
可要是把它做得更轻巧,还不失韧性,简直是个完美的“轻盈战士”!这就是微发泡的魅力所在。
它就像是给塑料打了个气,把它的体积和质量都变得更可爱,更适合各种日常需求。
说到微发泡,这工艺可不是说说而已。
它的原理很简单,利用物理方法在塑料中引入气泡。
就像你喝饮料的时候,看到那些气泡在瓶子里欢快地跳舞,真是让人忍不住想要一口喝下去。
这个过程也类似,塑料在加热的时候,气体被注入,形成许多微小的气泡。
结果呢,塑料的体积变大了,密度却变小了。
就好比是给一个大象穿上了隐形的轻纱,虽然看起来胖乎乎,但实际上轻得很!这些气泡不仅让塑料变得轻巧,还能提升它的强度,真是一举两得,聪明得很!不过,咱们也不能只顾着说好听话,微发泡的过程可没那么简单。
温度的控制是关键。
太高了,塑料会变得过于软,不容易成型;太低了,气泡可能不够均匀,影响最终的产品质量。
就像做饭一样,火候掌握不好,做出来的菜也不会好吃。
除了温度,压力也很重要。
咱们要把气体注入塑料的过程中,得保持一个合适的压力,不能太高,不能太低。
就像给气球充气,充多了就爆,充少了就瘪,这个中间的平衡,真是让人伤透脑筋!再说说原材料的选择。
你知道吗,不同的塑料对微发泡的效果也大相径庭。
有些塑料就像个好学生,容易发泡;有些塑料则像个捣蛋鬼,发泡的效果不好。
为了达到最佳效果,得选对“主角”。
像聚乙烯、聚丙烯这种常见的材料,都是微发泡的“明星”,他们发泡起来可轻松多了,就像一群快乐的小伙伴,一起聚会一样,气氛热烈。
接下来的步骤也是马虎不得,得把这些发泡塑料注入模具里。
这时,模具就像是个变魔术的箱子,把塑料的形状锁定。
咱们的塑料小伙伴们在里面飞快扩张,变得丰满起来。
最终,等到冷却,塑料就被固定住了。
拿出来时,嘿,看看这小家伙,轻巧又结实,真是不得了!一边捏一边乐,这个过程看得人真是心花怒放。
微发泡注塑成型技术
微发泡注塑成型技术发布时间:2022-06-22T07:26:44.031Z 来源:《科技新时代》2022年5期作者:冯逍[导读] 在发泡工艺中,微发泡注塑技术的应用非常广泛。
通过微发泡注塑成型技术可以保证产品基本性能,而且具有更轻的重量,内应力更小,不容易产生表面缺陷,尤其是在一些壁厚有较大差异的产品中表现出很好的技术优越性。
文章对微发泡注塑成型技术进行分析探讨,推动该技术应用水平不断提升。
安徽鲲鹏装备模具制造有限公司1 安徽省装备模具工程技术研究中心2 安徽省滁州市 239000摘要:在发泡工艺中,微发泡注塑技术的应用非常广泛。
通过微发泡注塑成型技术可以保证产品基本性能,而且具有更轻的重量,内应力更小,不容易产生表面缺陷,尤其是在一些壁厚有较大差异的产品中表现出很好的技术优越性。
文章对微发泡注塑成型技术进行分析探讨,推动该技术应用水平不断提升。
关键词:微发泡技术;注塑成型技术;技术原理;技术优势;技术应用1引言在发泡工艺中,微发泡技术的应用越来越广泛。
该技术是一种物理发泡技术,以热塑性材料为基体,在特定的工艺条件下进行发泡,得到密度在十到几十微米范围内的微孔发泡产品。
目前,在全球微发泡技术中,应用最广泛的是美国Trexel公司研发的微发泡专利技术。
2微发泡注塑成型基本原理微发泡注塑成型过程非常复杂,大致可分为四个阶段,聚合物或气体均相体系的形成阶段、气泡孔成核阶段、气泡孔长大阶段、气泡孔成型阶段。
不同的阶段在机理上也不同,主要影响参数也不同。
在微发泡注塑成型技术中,聚合物或气体均相体系的形成阶段非常重要,该阶段的效果直接影响后面阶段,对微发泡的气泡孔成核、长大以及定型关系密切。
气泡孔成核效果的主要衡量指标是气泡孔分布和密度。
气泡孔长大阶段对气泡孔的几何形状和结构影响很大。
气泡孔成型阶段决定着气泡是否长大以及气泡结构是否能维持。
微发泡注塑成型过程中,对各个阶段的技术参数控制有较高要求,必须满足相应的条件参数,才能保证各阶段反应效果,最终得到理想的微发泡产品。
微发泡注塑成型工艺
微发泡注塑成型工艺
微发泡注塑成型工艺是近几年新兴的一种注塑工艺,它是注塑工艺中一种新兴的特殊工艺。
它主要应用于制造微型零件和复杂型号的零件,是实现高性能和高精度的一种重要手段。
本文主要概述了微发泡注塑成型工艺的原理,材料,特点和应用等。
一、微发泡注塑成型工艺的原理
微发泡注塑成型工艺的核心原理是利用微发泡剂的气化热释放,这种物质具有很好的耐热性、耐腐蚀性和可塑性,在高温下分解发泡,其形成的泡沫可填充空隙,使塑料件具有良好的附着力和结构强度。
二、微发泡注塑成型工艺的材料
微发泡注塑成型常使用PE(聚乙烯)、PP(聚丙烯)、PA(聚氨酯)、ABS(丙烯腈-丁二烯-苯乙烯共聚物)、PES(聚氯乙烯)、PC(聚碳酸酯)等塑料。
三、微发泡注塑成型工艺的特点
1、微发泡注塑成型具有型芯强度高、外观无瑕疵等特点。
2、注塑件孔径精度高,可实现孔径小于0.1毫米的微型零件制造。
3、制品具有良好的结合力,表面光滑柔韧,良好的耐化学性和气密性。
四、发泡注塑成型工艺的应用
微发泡注塑成型工艺的应用范围很广,其中包括可穿戴设备、自动化设备零部件、消费类电子、5G移动通讯器件、照明行业元件等,
目前正迅速地发展着,这些都对微发泡注塑成型工艺的发展提出了更高的要求,同时也促进了该工艺的更新换代。
总之,微发泡注塑成型工艺具有速度快、工艺复杂程度低、能够制造微型零件等诸多优势,在各种行业,如建筑、机械、航空航天等领域得到了广泛应用。
未来,随着科技的不断发展,微发泡注塑成型工艺还将发挥更大的作用,使生产更高效,建立更完善的工艺系统,更好地满足我们日常生活的需求。
- 1、下载文档前请自行甄别文档内容的完整性,平台不提供额外的编辑、内容补充、找答案等附加服务。
- 2、"仅部分预览"的文档,不可在线预览部分如存在完整性等问题,可反馈申请退款(可完整预览的文档不适用该条件!)。
- 3、如文档侵犯您的权益,请联系客服反馈,我们会尽快为您处理(人工客服工作时间:9:00-18:30)。
四.技术特点及优势
微发泡成型主要是靠气泡的成长来填充产品,是在较低而平均的压力下进行的,不像传统注塑成型要靠机台的不断保压。
所以产品的内应力大大减小,不同位置的收缩也变得非常平均。
1.降低成本
微发泡成型具有很多的特点:树脂黏度降低令流体的流动性更高,可以降低熔体的温度,模温和注射压力,使塑件稳定,成型视窗变大。
微发泡工艺通过下列途径降低了生产的成本:
1)提高了注塑工艺水平,减少了注塑和装配的不良率;
2)因尺寸更稳定,可减少模具尺寸反复修改,从而降低模具设计和制造成本;
3)降低锁模力40~80%,减少毛边,降低能耗,延长了模具寿命。
可以考虑使用更低吨位的注塑机,或使用多模腔;
4)注塑周期缩短20-30%,增加生产效率,降低能耗,从而降低运营成本;
5)一般减少材料用量8~15%,更可以设计具有薄壁结构的制品来更加降低制品的材料成本。
等等。
2.微发泡解决问题
微发泡技术能解决以下传统注塑常见的问题:部件收缩不均导致尺寸不稳定和内应力问题、缩水痕、平直度不好、同心度或圆度不够、动平衡性不高、难填充等等,采用微发泡注塑技术则可以提高部件质量,下面应用实例:
传统注塑解决部件翘曲通常会靠延长注塑和保压时间来达到,这样大大降低了生产效率。
微发泡使部件不仅在生产时非常平整,而且在热处理后也能保持。
许多
应用表现出了这一优点,比如高精度托盘,打印机过纸架等,例如导纸板在不改动模具的情况下把偏差从0.807mm降低到0.429mm.,提高了47%。
因为射胶压力和熔胶温度较低,微发泡被广泛应用到了模内装饰(IMD)的产品
上,有效地解决了传统注塑易出现的“冲膜”和“渗边“的现象,同时也解决了缩水问题,提高了尺寸的稳定性和平直度的问题,从而大大减少了不良率,锁模
力从250吨降到了75吨.
由于均匀的收缩令产品的尺寸异常稳定。
在模具开发的前阶段, 尺寸的稳定和一致性减少了模具的设计和制作的反复修改。
在生产中Cp和Cpk值非常好,大大减少了不良率。
由于均匀的收缩令微发泡的齿轮的圆度和同心度大大提高,一般可以提升AGMA一到两个级数,大大提升了齿轮的精度。
相同的成型参数下微发泡技术让型腔很容易被填满,因为树脂黏度降低使得流体的流动性更好和气泡在长大的过程中均匀把压力传递到各个部位帮助填充。
流长
比更大,左边产品使用的是Valox 4521(高流动性PBT)4穴,传统注塑需要两个浇口才能充满满,使用微发泡技术后只需要一个浇口。
五.常见应用领域
几乎目前所有的热塑性材料都可以采用微发泡注塑成型技术。
但考虑到经济性和产品品质要求,微发泡制品主要集中在商业设备、汽车及内部装饰材料、电子电器产品等品质要求较高材料较贵的产品上,如打印机复印机,汽车内部件、保险盒、电器开关、薄壁容器等等。
以下列举了一些常用的产品,当然在许多其他行业领域也有很多用户成功应用了这种技术。
商用设备 汽车 电气/电子
打印机内部部件、导纸机构、压纸卷筒、托架和墨辊 发动机罩和动力系下面的部件、进气
管 连接器/插座部件、束
线/芯片
托盘
墨粉盒 电气/电子部件、变速箱、运动部件 封装部件/医用托
盘
复印机 采暖、通风、空调和散热系统部件、风扇护罩、阀门和发动机外壳 开关部件、
接线盒、风
扇/晶片
托架
密封部件、门板、手套式操作箱 嵌件插入
产品 六.微发泡注塑与其他注塑工艺的比较
1. 微发泡注塑与气体辅助注塑
虽然都使用氮气,但成型原理完全不同。
气辅注射于厚壁产品上效果会更加明显,特别是一些中空的部件,它对产品局部有帮助。
它需要在模具上做气道等特殊处理;而微发泡注塑在模具制作上和传统模具并无不同,只是因为注射速度较快需要模具排气较多一些,微发泡注塑理想的流道比传统模具的小20%左右,当然这也节省了不少用料。
它主要应用在薄壁产品上,能对整个产品的不同部位都有帮助。
2. 微发泡注塑与化学发泡成型
化学发泡剂在特定的温度下分解而产生气泡。
不同类型的发泡剂适用于不同温度下分解发泡。
其通常用于厚壁制品成型以消除缩水痕,同时也可以降低制品重量。
对于薄壁制品使用化学发泡剂会使表面质量劣化,同时会显著降低其力学性能。
而且,从经济性角度出发,化学发泡不能够大幅度降低密度。
另外,由于化学发泡剂本质上的热稳定性不佳,因而很难用于加工高温型树脂。
化学发泡剂通常会在树脂中有所残留,或产生副产品。
带有副产品或未分解化学发泡剂的树脂通常会使制品耐老化性能降低,并可能导致模具排气孔堵塞。
而且,回收料很难再次使用。
七.微发泡注塑的限制和新技术发展
微发泡注塑不能用于透明部件上,对于外观要求高的产品也不可直接应用,需要和表面喷涂、模具急冷急热技术、模腔反压技术等结合起来,可以和IMD(模内注塑装饰技术)结合,做出来的产品没有缩水痕,更平直,外观更高的产品。
另外,由于Trexel公司专利授权本地化生产微发泡注塑设备,大大降低了设备
成本,原先难以进入的注塑行业,如白色家电、消费品等,现在都可以将微发泡技术使用在相关产品,因此微发泡技术在国内注塑市场将得到迅速的发展。