3.4液相法制备陶瓷粉体
液相法制备超细粉体的原理及特点
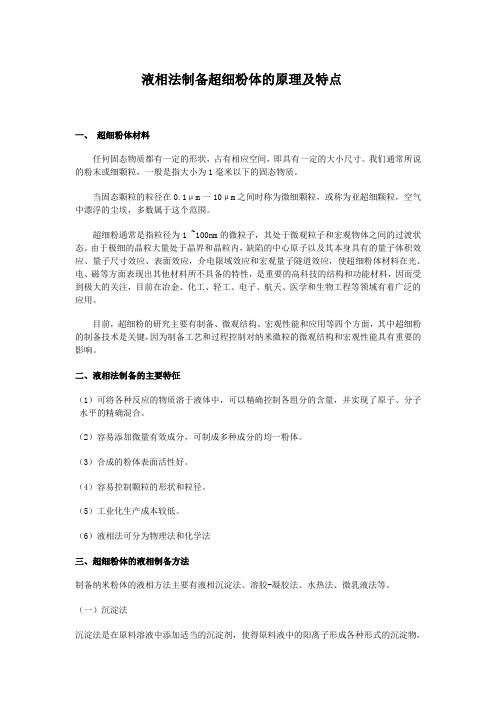
液相法制备超细粉体的原理及特点一、超细粉体材料任何固态物质都有一定的形状,占有相应空间,即具有一定的大小尺寸。
我们通常所说的粉末或细颗粒,一般是指大小为1毫米以下的固态物质。
当固态颗粒的粒径在0.1μm一10μm之间时称为微细颗粒,或称为亚超细颗粒,空气中漂浮的尘埃,多数属于这个范围。
超细粉通常是指粒径为1 ~100nm的微粒子,其处于微观粒子和宏观物体之间的过渡状态。
由于极细的晶粒大量处于晶界和晶粒内,缺陷的中心原子以及其本身具有的量子体积效应、量子尺寸效应、表面效应,介电限域效应和宏观量子隧道效应,使超细粉体材料在光、电、磁等方面表现出其他材料所不具备的特性,是重要的高科技的结构和功能材料,因而受到极大的关注,目前在冶金、化工、轻工、电子、航天、医学和生物工程等领域有着广泛的应用。
目前,超细粉的研究主要有制备、微观结构、宏观性能和应用等四个方面,其中超细粉的制备技术是关键,因为制备工艺和过程控制对纳米微粒的微观结构和宏观性能具有重要的影响。
二、液相法制备的主要特征(1)可将各种反应的物质溶于液体中,可以精确控制各组分的含量,并实现了原子、分子水平的精确混合。
(2)容易添加微量有效成分,可制成多种成分的均一粉体。
(3)合成的粉体表面活性好。
(4)容易控制颗粒的形状和粒径。
(5)工业化生产成本较低。
(6)液相法可分为物理法和化学法三、超细粉体的液相制备方法制备纳米粉体的液相方法主要有液相沉淀法、溶胶-凝胶法、水热法、微乳液法等。
(一)沉淀法沉淀法是在原料溶液中添加适当的沉淀剂,使得原料液中的阳离子形成各种形式的沉淀物,然后再经过虑、洗涤、干燥,有时还需加热分解等工艺过程制得纳米粉体的方法。
沉淀法具有设备简单、工艺过程易控制、易于商业化等优点,能制取数十纳米的超细粉。
沉淀法可分为共沉淀法、直接沉淀法、均匀沉淀法和水解法等。
1、共沉淀法在混合的金属盐溶液中加入合适的沉淀剂,由于解离的离子是以均一相存在于溶液中,经反应后可以得到各种成分具有均一相的沉淀,再进行热分解得到高纯超细粉体。
陶瓷粉体基础表征

高温陶瓷材料在高温环境下表现出良 好的抗氧化性、抗蠕变性和高温强度, 使其成为高温环境下应用的理想材料。
高温陶瓷材料的制备通常需要经过复 杂的合成和烧结过程,以确保其具有 优良的力学性能、化学稳定性和高温 稳定性。
电子陶瓷材料
电子陶瓷材料是指具有优良电性 能的陶瓷材料,广泛应用于电子 元器件、集成电路、传感器等领
针对不同应用领域,研究具有 特定性能需求的陶瓷粉体,拓 展其在能源、环境、生物医学 等领域的应用。
加强跨学科合作,将陶瓷粉体 科学与材料科学、物理学、化 学等学科进行有机结合,推动 陶瓷粉体科学的发展。
感谢您的观看
THANKS
多孔陶瓷材料的孔径、孔隙率、比表面积等参数对其性能和应用具有重要影响,需 要根据具体应用需求进行优化设计。
06 结论与展望
研究结论
陶瓷粉体的形貌、粒径、化学 组成等基础性质对陶瓷材料的
性能具有重要影响。
通过先进的表征技术,如X射线 衍射、扫描电子显微镜、透射 电子显微镜等,可以深入了解 陶瓷粉体的结构和性质。
总结词
液相法是一种通过溶液中的化学反应来制备陶瓷粉体的方法。
详细描述
液相法通常是将原料溶解在溶剂中,然后通过控制溶液的浓度、温度和pH值等参数,使原料在溶液中 发生化学反应并析出晶体,最终得到所需的陶瓷粉体。该方法制备的粉体具有较窄的粒度分布和较好 的形貌控制,但制备过程中需要去除溶剂并进行高温煅烧,成本较高且易引入杂质。
详细描述
扫描电子显微镜利用电子束扫描陶瓷 粉体表面,通过收集和分析二次电子、 背散射电子等信号,形成高分辨率的 图像,能够观察陶瓷粉体的形貌和粒 度分布。
透射电子显微镜观察
总结词
透射电子显微镜观察可以观察陶瓷粉体的内 部结构和晶体生长情况。
陶瓷粉体
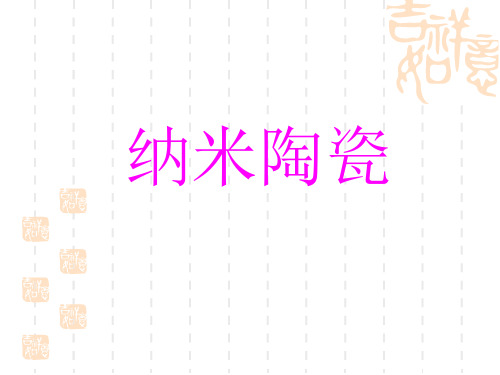
纳米陶瓷: 指显微结构中的物相(包括晶粒尺 寸、晶界宽度、第二相分布、气孔与尺 寸缺陷等)都在纳米量级的水平上的陶 瓷材料。
现有陶瓷材料的晶粒尺寸一般是在微 米级的水平。当其晶粒尺寸变小到纳米级 的范围时,晶粒的表面积和晶界的体积会 以相应的倍数增加,晶粒的表面能亦随之 剧增。 由于颗粒的线度减少而引起表面效应 和体积效应,使得材料的物理、化学性质 发生一系列变化,而且甚至出现许多特殊 的物理与化学性质。
纳米材料的制备: 纳米粉体的合成 素坯的成型 产品的烧结
粉体合成按合成条件分类: 1、气相法:气相法是直接利用气体,或 者通过各种手段将物质转变为气体,使之 在气体状态下发生物理变化或者化学反应, 最后在冷却过程中凝聚长大形成纳米粒子 的方法。 优点:制得的纳米陶瓷粉体的纯度较 高,团聚较少,烧结性能较好 缺点:产量低,设备昂贵
2、应用于提高陶瓷材料的超塑性 只有陶瓷粉体的粒度小到一定程度 才能在陶瓷材料中产生超塑性行为,其 原因是晶粒的纳米化有助于晶粒间产生 相对滑移,使材料具有塑性行为。
3、应用于制备电子(功能)陶瓷 纳米陶瓷粉体之所以广泛地用于 制备电子陶瓷,原因在于陶瓷粉体晶粒 的纳米化会造成晶界数量的大大增加, 当陶瓷中的晶粒尺寸减小一个数量级, 则晶粒的表面积及晶界的体积亦以相 应的倍数增加
3、固相法:指纳米粉体是由固相原 料制得,按其加工的工艺特点可分 为机械粉碎法和固相反应法两 类。 优点:所用设备较简单,方便操作 缺点:纯度较形状、
体积和强度的坯体的过程,素坯的相对 密 度和显微结构的均匀性对陶瓷在烧结过 程 中的致密化有极大的影响
纳米陶瓷的性能:
1、高强度: 纳米陶瓷材料在压制、烧结后,其强度比 普通陶瓷材料高出4-5倍,如在 100度下,纳米 TiO2陶瓷的显微硬度为13000KN/mm2,而普通 TiO2陶瓷的显微硬度低于2000KN/mm2。日本 的新原皓一制备了纳米陶瓷复合材料,并测定 了其相关的力学性能,研究表明纳米陶瓷复合 材料在韧性和强度上都比原来基体单相材料均 有较大程度的改善,对 Al2O3/SiC 系统来说, 纳米复合材料的强陶度比单相氧化铝的强度提 高了3-4倍。
实验三 液相法粉体材料的制备
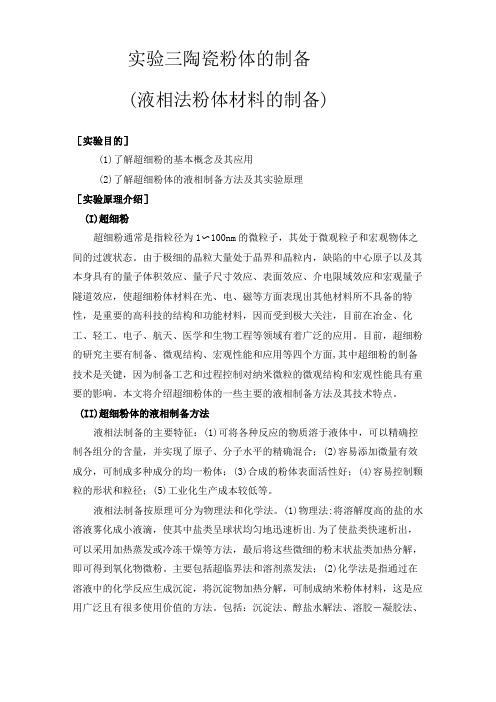
实验三陶瓷粉体的制备(液相法粉体材料的制备)[实验目的](1)了解超细粉的基本概念及其应用(2)了解超细粉体的液相制备方法及其实验原理[实验原理介绍](I)超细粉超细粉通常是指粒径为1〜100nm的微粒子,其处于微观粒子和宏观物体之间的过渡状态。
由于极细的晶粒大量处于晶界和晶粒内,缺陷的中心原子以及其本身具有的量子体积效应、量子尺寸效应、表面效应、介电限域效应和宏观量子隧道效应,使超细粉体材料在光、电、磁等方面表现出其他材料所不具备的特性,是重要的高科技的结构和功能材料,因而受到极大关注,目前在冶金、化工、轻工、电子、航天、医学和生物工程等领域有着广泛的应用。
目前,超细粉的研究主要有制备、微观结构、宏观性能和应用等四个方面,其中超细粉的制备技术是关键,因为制备工艺和过程控制对纳米微粒的微观结构和宏观性能具有重要的影响。
本文将介绍超细粉体的一些主要的液相制备方法及其技术特点。
(II)超细粉体的液相制备方法液相法制备的主要特征:(1)可将各种反应的物质溶于液体中,可以精确控制各组分的含量,并实现了原子、分子水平的精确混合;(2)容易添加微量有效成分,可制成多种成分的均一粉体;(3)合成的粉体表面活性好;(4)容易控制颗粒的形状和粒径;(5)工业化生产成本较低等。
液相法制备按原理可分为物理法和化学法。
(1)物理法:将溶解度高的盐的水溶液雾化成小液滴,使其中盐类呈球状均匀地迅速析出.为了使盐类快速析出,可以采用加热蒸发或冷冻干燥等方法,最后将这些微细的粉末状盐类加热分解,即可得到氧化物微粉。
主要包括超临界法和溶剂蒸发法;(2)化学法是指通过在溶液中的化学反应生成沉淀,将沉淀物加热分解,可制成纳米粉体材料,这是应用广泛且有很多使用价值的方法。
包括:沉淀法、醇盐水解法、溶胶-凝胶法、水热合成法、非水乳液法、微乳液法等。
下面对对其中几种技术的特点进行介绍:(一)沉淀法沉淀法是在原料溶液中添加适当的沉淀剂,使得原料液中的阳离子形成各种形式的沉淀物,然后再经过滤、洗涤、干燥,有时还需加热分解等工艺过程制得纳米粉体的方法。
液相法制备超细粉体材料
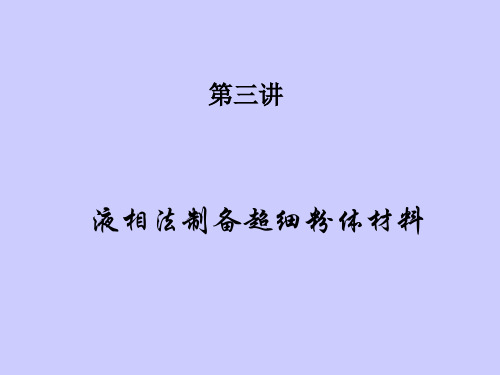
4 3 g G r r 2 3 V 2V 临界晶核大小: rc RT ln S
成核过程可以看作是激活过程,成核所需的活化能为:
Ec Gmax 1
ln S
2
提高溶液的过饱和度S,可以大大降低ΔGmax,使rc 减小,因此溶液的过饱和度是超细颗粒成核的必要 条件。
• 物理法:将溶解度高的盐的水溶液雾化成小液 滴,使其中盐类呈球状均匀地迅速析出.为了 使盐类快速析出,可以采用加热蒸发或冷冻干 燥等方法,最后将这些微细的粉末状盐类加热 分解,即可得到氧化物微粉。主要包括超临界 法和溶剂蒸发法 • 化学法是指通过在溶液中的化学反应生成沉淀, 将沉淀物加热分解,可制成纳米粉体材料,这 是应用广泛且有很多使用价值的方法。包括: 沉淀法、醇盐水解法、溶胶-凝胶法、水热合 成法、非水乳液法、微乳液法等。
有一系列突出的优点:①能在溶液状态下获得组分的均匀 混合,适合于微量元素的添加。②制得的超细粉体粒径一 般在1~50μm范围内,表面活性好,比表面积高。③操作 简单,特别有利于高纯陶瓷材料的制备。
沉淀法反应器设计原则及其特点
对于用沉淀法制备粒度分布窄化,晶型可控的超细粉 体,混合对其粒度分布和颗粒形貌有重要影响,混合包括 发生在大尺度上的宏观混合过程和发生在分子尺度上的微 观混合过程。通过宏观混合,各组分可达反应器尺度上的 宏观浓度分布均匀,通过微观混合则使局部小区域内各组 分浓度分布达到分子尺度上的均匀化。对晶粒的成核,微 观混合起十分重要的关键作用。对于晶体生长,微观混合 对其无影响,只要考虑容器尺度的宏观混合即可,宏观混 合均匀则晶核即可在浓度均匀的生长环境中长大成尺寸分 布均匀和形状一致的晶粒。 沉淀法制备高品质超细粉体的反应器的设计和选型原 则是(1)反应成核区和晶体生长区分开;(2)反应成核 区臵于高度强化的微观混合区;(3)晶体生长区臵于完 全宏观混合区;(4)反应成核区宏观流动设计为平推流、 无返混。
液相沉淀法制备云母玻璃陶瓷粉体的品化行为
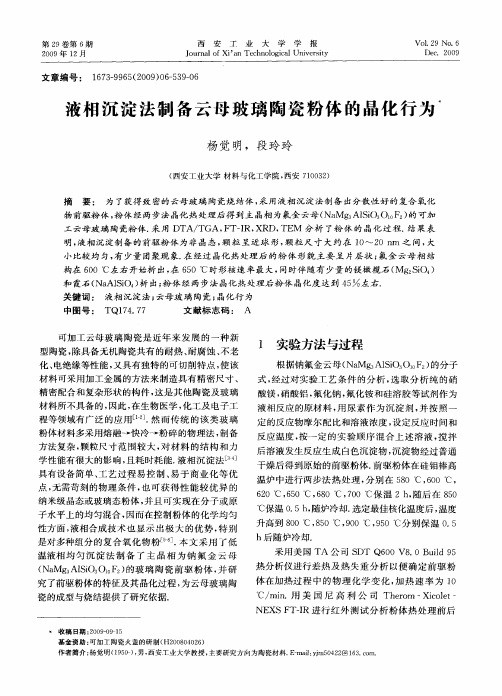
( MgA1i3 F ) Na 。 SO O。 z的玻 璃 陶瓷 前 驱 粉 体 , 研 并 究 了前驱 粉体 的特征 及其 晶化过 程 , 云母 玻 璃 陶 为 瓷 的成 型与烧结 提供 了研究 依据 .
热分 析仪 进行 差热 及 热失 重 分 析 以便 确 定 前 驱粉 体在 加热 过程 中 的 物理 化 学 变化 , 热 速 率 为 1 加 O
小 比较 均 匀, 少量 团聚现 象. 经过 晶化 热处理 后 的粉 体 形貌 主要 呈 片层 状 ; 有 在 氟金 云母 相 结 构在 6 0。 右开 始析 出 , 6 0。 0 C左 在 5 C时形核速 率 最大 , 同时伴随有 少量 的镁 橄榄 石 ( z i 4 Mg S0 )
和 霞石 ( A1i 4 析 出 ; 体经 两 步法 晶化 热处理后 粉 体 晶化度达 到 4 %左 右. Na S0 ) 粉 5
。 C保温 05h随炉 冷却. . , 选定最佳 核化温度 后 , 温度
升 高到 80℃,5 C,0 C,5 0 8 0。 9 0。 9 0℃分别 保 温 0 5 . h后 随 炉冷却 .
采用 美 国 T 公 司 S T Q6 oV8 oB i 5 A D o 。 ul 9 d
材料 所不具 备 的 , 因此 , 在生 物 医学 , 工及 电子 工 化
1 实验方法与过程
根据 钠氟 金云母 ( Mg A1i O 2 的分 子 Na 。 SO。 。 ) F 式, 经过对 实验 工 艺 条 件 的分 析 , 取 分 析 纯 的硝 选 酸镁 , 硝酸 铝 , 氟化钠 , 化铵 和硅 溶胶 等试剂 作为 氟 液 相反 应 的原材 料 , 尿 素 作 为 沉 淀 剂 , 用 并按 照 一
定 的反 应物 摩尔 配 比和溶 液浓 度 , 定反 应时 间和 设
第一章特种陶瓷粉体的物理性能及其制备

Ao =A / V, 单位 m2/m3 或m-1 。
2、粉体颗粒的吸附与凝聚
粉体所以区别于一般固体而呈独立物态,是因为:一方 面它是细化了的固体;另一方面,在接触点上与其它粒 子间有相互作用力存在。此外,颗粒之间也相互附着而 形成团聚体。 附着:一个颗粒依附于其它物体表面上的现象。 附着力(force of adhesion):存在于异种固体表面的引力。 凝聚:颗粒间在各种引力作用下的团聚。 凝聚力(agglomerative force) :存在于同种固体表面间的 引力。
积、可压缩性、流动性和工艺性能有重要影响。
特种陶瓷的制备,实际上是将特种陶瓷的粉体原
料经过成型、热处理,最终成为制品的过程。因 此,学习和掌握好特种陶瓷粉体的特性,并在此 基础上有目的地进行粉体制备和粉体性能调控、 处理,是获得优良特种陶瓷制品的重要前提。粉
体的制备方法一般可分为粉碎法和合成法两种。
3) 氧化还原法
非氧化物特种陶瓷的原料粉末多采用氧化物还原方法制备。 或者还原碳化,或者还原氮化。如SiC、Si3N4等粉末的制备。 SiC粉末的制备:将SiO2与碳粉混合,在1460~1600℃的加 热条件下,逐步还原碳化。其大致历程 如下: SiO2 + C → SiO+CO SiO + 2C → SiC+CO SiO + C → Si+CO Si + C → SiC Si3N4粉末的制备:在N2条件下,通过SiO2与C的还原-氮化。 反应温度在1600℃附近。其基本反应如下: 3SiO2+6C+2N2 → Si3N4 +6CO
2) 化合反应法
两种或两种以上的固体粉末,经混合后在一定的热力学条件 和气氛下反应而成为复合物粉末,有时也伴随气体逸出。化 合反应的基本形式: A(s)+B(s)→C(s)+D(g) 钛酸钡粉末、尖晶石粉末、莫来石粉末的合成都是化学反应 法: BaCO3+TiO2→BaTiO3+CO2 Al2O3+MgO→MgAlO4 3Al2O3+2SiO2→3Al2O3· 2SiO2
陶瓷粉体制备ppt课件
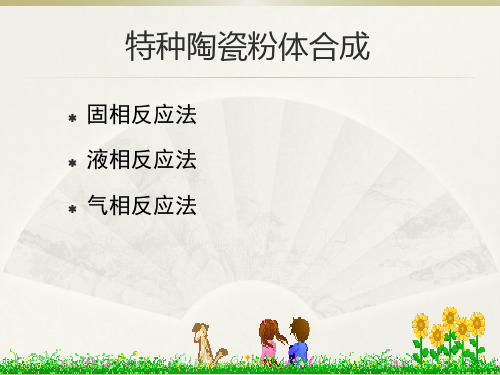
解速度有利于溶胶凝胶形成。 湿度。一般<50% 温度。提高温度促进水解、缩聚反应,缩短
凝胶时间
20
醇盐分解法
采用金属醇盐M(OR)n为先驱体,以无水乙醇为溶 剂,遇水后很容易水解形成氧化物或其水合物。
控制水解条件可以获得粒径几纳米到几十纳米的超 细粉。
2. 在适当的高温下煅烧合成 3. 将合成的熟料块体粉碎研磨至所需细度
主要用于合成复合氧化物(如BaTiO3等)
BaCO3 TiO2 BaTiO3 CO2
3Al2O3 2SiO2 3Al2O3 2SiO2
3
碳热还原反应法
非氧化物的合成
碳化物
TiO2 C ArTiC CO2 SiO2 3C Ar SiC 2CO
R O
R O
Si
H2O
O R
O R
H O
OH
Si
HO
O H
21
水热法
在密闭反应釜(高压釜)内,采用水溶液为反应介质,对 反应釜加热,溶剂蒸发形成高温高压,使通常条件下难溶 或不溶的物质发生溶解析出传质,得到晶体颗粒。
优点:
晶粒发育完整、细小、均匀; 无(或少)团聚; 无煅烧及粉碎等加工过程。
这两种力的合力状态决定了颗粒的团聚 与分散(DLVO理论)。 影响分散的因素:
pH、电解质溶液中离子强度 分散剂
25
干燥过程
干燥过程中的团聚主要是由颗粒间液体 的表面张力产生的。
P 2 LV cos
R
• 乙醇的表面张力比水小,因此,通过乙 醇清洗后再干燥,可减少干燥中的团聚 程度。
- 1、下载文档前请自行甄别文档内容的完整性,平台不提供额外的编辑、内容补充、找答案等附加服务。
- 2、"仅部分预览"的文档,不可在线预览部分如存在完整性等问题,可反馈申请退款(可完整预览的文档不适用该条件!)。
- 3、如文档侵犯您的权益,请联系客服反馈,我们会尽快为您处理(人工客服工作时间:9:00-18:30)。
• 是利用某一化学反应,使溶液中的构成产物的阴离子(或阳离 子)在溶液中缓慢地、均匀地产生出来,从而形成沉淀的方法。
• 生成沉淀的途径主要有:
1)沉淀剂缓慢的化学反应,导致H+(OH-)离子变化,溶液pH 值变化,使产物溶解度逐渐下降而析出沉淀 H2NCONH2 + 3H2O CO2 + NH4+ + OH- (90C) 2) 沉淀剂缓慢的化学反应,释放出沉淀离子,达到沉淀离子的沉 淀浓度而析出沉淀 NH2HSO3 + H2O SO4+ + NH4+ + H+ 3)混合作用 H2NCONH2 + H2O CO2 + NH3 (90C) NH3 + HC2O4C2O42- + NH4+ 最常用的沉淀剂有尿素(CO(NH2)2)和六甲基四胺((CH2)6N4), 其反应机理如下:
试剂浓度与粒子尺寸
[urea] 4.0M 2.0M 2.0M 1.0M 1.0M 1.0M
粒子尺寸(nm)
8.6 9.2 9.6 11 12 8.6
(TEM) ~10 ~10 ~60 40~50 ~50 ~50
② 反应物配比
当反应物浓度一定时,尿素/反应物(摩尔比) 越大,溶液中的OH-浓度越大,过饱和度增加,有利 于生成小粒径粒子沉淀。同时,过量的尿素还能保证 在一定反应时间内与反应物充分反应,提高了产物产 率。
①
过饱和度
均相沉淀法Sm掺杂的氧化铈(SDC)
Sm(NO3)3 Ce(NO3)3 尿 素
85oC恒温 沉淀
粉体
焙烧
干燥
洗涤
过滤
①
[M4+] a b c d e f 0.4M 0.2M 0.05M 0.1M 0.01M 0.005M
过饱和度
晶粒尺寸(nm)
(谢乐公式计算)
如何计算? 最低过饱和度Cmin
当晶粒的生成速率小于生长速率时,有利 于生成大而少的粗粒子;当生成速率大于生长 速率时,有利于纳米颗粒的形成。因此,为了 获得纳米粒子须保证晶粒的生成速率大于生长 速率。 通常通过使反应在较大的过冷度或高的过 饱和度下进行来达到成核速率大于生长速率。
五、 影响粉体制备的因素
1、过饱和度 2、反应物配比
这样在溶液内部生成沉淀剂NH4OH。若溶液中存在金属离子将NH4OH消耗掉,不致 产生局部过浓现象。当NH4OH被消耗后, (NH2)2CO继续水解,产生NH4OH。 因为尿素的水解是由温度控制的,故只要控制好升温速度,就能控制尿素的水解速度, 这样可以均匀地产生沉淀剂,从而使沉淀在整个溶液中均匀析出。
四、 均匀沉淀法理论基础-沉淀过程动力学模型amer model)
为了从液相中析出 大小均一的固相颗粒,必 须使成核和生长这两个过 程分开。
I无晶核生成 II成核阶段 III生长阶段
为使成核与生长尽 可能分开,必须使成核速 率尽可能高而生长速率适 当的慢,应尽可能压缩阶 段II。在阶段III必须使浓度 低于最低过饱和浓度,以 免生成新核。
溶胶-凝胶法等
液相合成技术特点
可以精确控制化学组成; 易添加微量有效成份,制备多成份均一微粉; 粉体表面活性好; 颗粒形状和粒径易控;
沉淀法分类
(1)均相沉淀法
沉淀剂慢慢地生成
(i)单相共沉淀 (2)共沉淀法
(ⅱ)混合物共沉淀
(3)水解沉淀法
3.4.1 均相沉淀法
一、均匀沉淀法原理:
3、反应温度
4、反应时间 5、煅烧温度和时间 6、表面活性剂
①
过饱和度
过饱和度越大,生成(成核)速率越快。 加快成核速率,降低生长速率,有利于生成粒 径细小的晶粒。实际上过饱和度增加的同时也 有利于晶核的生长,但随着过饱和度的进一步 提高,生成速率增长不占优势,因此,在溶液 中析出的纳米氧化物粒径就会小。
3.4 液相法制备陶瓷粉体
粉体的粒度(particle size)
由于细颗粒的团聚作用,粉体一般是大量颗粒的聚合体。 习惯上也把聚合体称为颗粒。
按ISO3252定义,晶粒 (A)、颗粒(B)、聚合 体(C)的区别如 右图所示。
气相法:蒸发法 固相法:粉碎法 (磁控,激光)溅射法 固相反应法 等离子体喷涂法 自蔓延法, 化学气相淀积(CVD)法 低温燃烧合成 气溶胶法 凝胶浇注法 化学喷雾热解法 液相法:沉淀法(共沉淀、均相沉淀法) 水热合成法 燃烧
四、 均匀沉淀法理论基础
根据化学反应动力学理论,晶核的生成速率为:
3 2 16 M N K exp 3 3 2 3R T (ln S )
σ——液固界面张力
M——溶质的分子质量 ρ——溶质颗粒的密度 S——溶液的过饱和度 K——反应速率常数
由上式可以看出,晶粒的生成速率对过饱和度S十分敏 感,S愈大,界面张力σ愈小,所需活化能愈低,生成速率愈 大。
2、 六甲基四胺作沉淀剂(制备ZnO)
(CH 2 ) 6 N 4 10 H 2O 6 HCHO 4 NH 3 H 2O
Zn 2 2 NH 3 H 2O Zn(OH ) 2 2 NH 4
Zn(OH ) 2 ZnO2 H 2O
三、均匀沉淀法特点
1)加入溶液的沉淀剂不立即与沉淀成分反应,而是通 过化学反应 在溶液中合均匀释放构晶离子 2)避免沉淀剂局部过浓的不均匀现象,使过饱和度控 制在适当的范围内,从而控制沉淀粒子的生长速度, 能获得粒度均匀、纯度高的超细粒子。 3) 用于粒子表面改性:均匀、可控的过饱和度,使可 在粒子表面非均相成核,通过粒子表面的其他材料复 合或外延生长而使粒子改性。 如:CoFe2O4 包覆的 rFe2O3
四、 均匀沉淀法理论基础
另一过程是核的生长过程,即在过饱和 溶液中形成晶粒以后,溶质在晶粒上不断地 沉积,使晶粒不断长大。晶粒线性生长速率 的普遍式为:
B/T R AGv exp
式中A、B——与系统性质有关的常数
ΔGv——固态分子的自由能变化
Gv VRT ln S
四、 均匀沉淀法理论基础
1 、尿素作沉淀剂(制备iO2)
常温下,该溶液体系无明显变化,当加热至70C以上时,尿素就发生如下水解反应:
CO ( NH 2 ) 3H 2O CO2 2 NH 3 H 2O TiOSO4 2 NH 3 H 2O TiO (OH ) 2 ( NH 4 ) 2 SO4 TiO (OH ) 2 TiO2 H 2O