PE管材对接焊操作规程
PE管道焊接操作方法规程
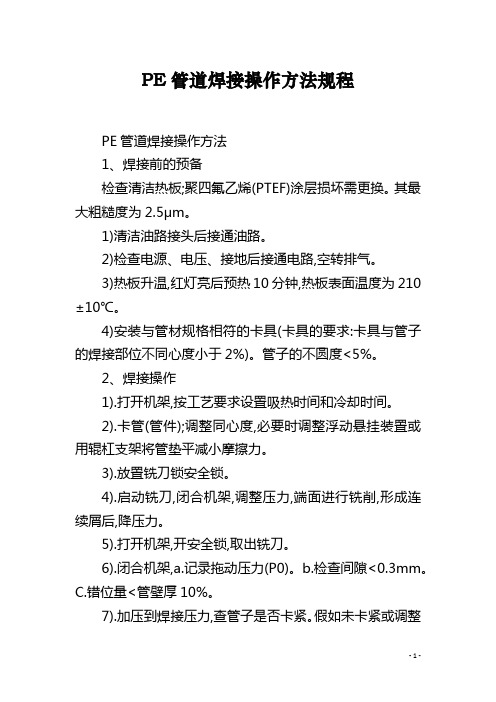
PE管道焊接操作方法规程PE管道焊接操作方法1、焊接前的预备检查清洁热板;聚四氟乙烯(PTEF)涂层损坏需更换。
其最大粗糙度为2.5μm。
1)清洁油路接头后接通油路。
2)检查电源、电压、接地后接通电路,空转排气。
3)热板升温,红灯亮后预热10分钟,热板表面温度为210±10℃。
4)安装与管材规格相符的卡具(卡具的要求:卡具与管子的焊接部位不同心度小于2%)。
管子的不圆度<5%。
2、焊接操作1).打开机架,按工艺要求设置吸热时间和冷却时间。
2).卡管(管件);调整同心度,必要时调整浮动悬挂装置或用辊杠支架将管垫平减小摩擦力。
3).放置铣刀锁安全锁。
4).启动铣刀,闭合机架,调整压力,端面进行铣削,形成连续屑后,降压力。
5).打开机架,开安全锁,取出铣刀。
6).闭合机架,a.记录拖动压力(P0)。
b.检查间隙<0.3mm。
C.错位量<管壁厚10%。
7).加压到焊接压力,查管子是否卡紧。
假如未卡紧或调整管子位置,需重复3)的过程。
8).打开机架,放加热板(焊接端面有灰尘需清洁)。
9).闭合机架加压到焊接压力(P1)=拖动压力(P0)+接缝压力(P2)。
10).观看管端凸起高度,降压至拖动压力(P0),同时按吸热计时按钮,计时开始。
11).蜂鸣器响吸热结束,打开机架,快速取出热板,马上闭合机架,调整压力到焊接压力(P1),同时按冷却计时按钮。
12.蜂鸣器响,冷却时间到,降压力,松开卡具螺丝取管,进行下一循环。
b)焊接留意事项:1).必需测量电网、发电机电压,保证电压220V,防机毁。
2).必需测量加负载后的电压、机器外壳接地,保证人身安全。
3).与焊接端面接触的全部物件必需清洁,保证焊接质量。
4).加热板温度指示灯必需亮(红色),保证焊接温度。
5).卡管必需留有足够的距离,保证焊接端面有效接触。
6).铣削时铣刀安全锁必需锁死,防止铣刀飞出伤人。
7).铣屑必需是连续的长屑,保证焊接端面有效接触。
PE管热熔焊接操作规程

PE管热熔焊接操作规程一、目的与范围为了保证PE管热熔焊接的质量和安全,制定本操作规程。
本规程适用于PE管热熔焊接过程中的工艺控制和操作规范。
二、设备和材料2.1焊接机:应选用具有稳定焊接电流和精确控温功能的热熔焊接机,同时要保证熔炉体的热效应良好。
2.2PE管:应选择优质的聚乙烯管材,确保管材质量符合相关标准要求。
2.3PE管接头:应选择与PE管匹配的合适接头,确保连接牢固、密封性良好。
2.4PE管切刀:应选用具有锋利切削刀片的管切刀,确保切口平整。
2.5温度计:应选用精确度高的温度计,用于测量焊接机的工作温度。
三、操作流程3.1准备工作3.1.1检查焊接机、温度计等设备是否完好,确认焊接机的电源稳定。
3.1.2清洁管材和接头的外表面,确保没有污染物和杂质。
3.1.3根据管材规格调整熔炉和切刀的位置和尺寸,确保与管材匹配。
3.1.4根据管材和接头尺寸,调整焊接机的温度和压力。
3.2管材切割3.2.1将PE管放置在切刀上,调整切刀位置,使切口平整。
3.2.2切口应垂直于管材轴线,在切口处避免刮伤和变形。
3.3管材热熔3.3.1通过对焊接机控制温度和时间,将熔炉预热到适宜的工作温度。
3.3.2将切割好的管材和接头放在熔炉中,确保其与熔炉接触均匀。
3.3.3确认管材和接头熔融后的外观和颜色,避免过热或不充分熔融。
3.4管材连接3.4.1将熔融的管材和接头从熔炉中取出,快速将管材和接头连接起来。
3.4.2在连接过程中,保持管材与接头的位置不动,直到冷却固化。
3.5焊缝检验3.5.1用手轻轻拉扯已连接好的管材,检查焊接处是否牢固。
3.5.2视觉检查管材和接头连接处是否平整、无明显缺陷。
3.5.3用测温仪检测管材和接头焊接处的温度是否正常。
四、安全注意事项4.1操作人员应穿戴好防护用品,包括工作服、安全帽、防护眼镜、防静电手套等。
4.2操作人员应熟悉设备和工艺规程,遵守操作规范,不得擅自改变焊接参数。
4.3焊接现场应通风良好,避免烟雾和有害气体的积聚。
PE热熔对焊机安全操作规程
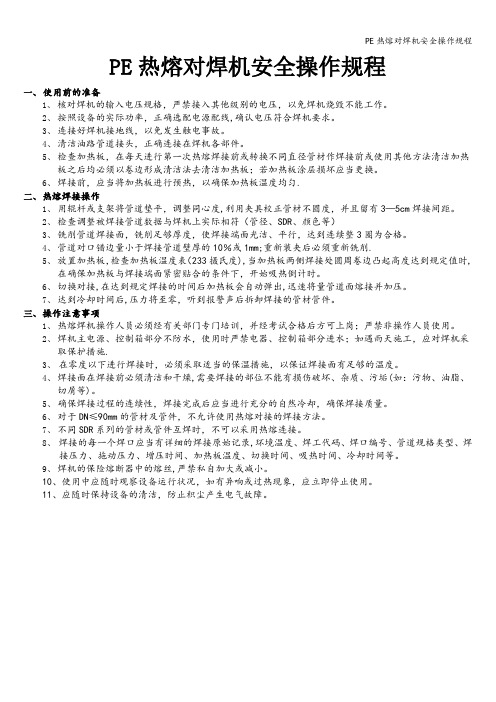
PE热熔对焊机安全操作规程PE热熔对焊机安全操作规程一、使用前的准备1、核对焊机的输入电压规格,严禁接入其他级别的电压,以免焊机烧毁不能工作。
2、按照设备的实际功率,正确选配电源配线,确认电压符合焊机要求。
3、连接好焊机接地线,以免发生触电事故。
4、清洁油路管道接头,正确连接在焊机各部件。
5、检查加热板,在每天进行第一次热熔焊接前或转换不同直径管材作焊接前或使用其他方法清洁加热板之后均必须以卷边形成清洁法去清洁加热板;若加热板涂层损坏应当更换。
6、焊接前,应当将加热板进行预热,以确保加热板温度均匀.二、热熔焊接操作1、用辊杆或支架将管道垫平,调整同心度,利用夹具校正管材不圆度,并且留有3—5cm焊接间距。
2、检查调整被焊接管道数据与焊机上实际相符(管径、SDR、颜色等)3、铣削管道焊接面,铣削足够厚度,使焊接端面光洁、平行,达到连续整3圈为合格。
4、管道对口错边量小于焊接管道壁厚的10%或1mm;重新装夹后必须重新铣削.5、放置加热板,检查加热板温度表(233摄氏度),当加热板两侧焊接处圆周卷边凸起高度达到规定值时,在确保加热板与焊接端面紧密贴合的条件下,开始吸热倒计时。
6、切换对接,在达到规定焊接的时间后加热板会自动弹出,迅速将量管道面熔接并加压。
7、达到冷却时间后,压力将至零,听到报警声后拆卸焊接的管材管件。
三、操作注意事项1、热熔焊机操作人员必须经有关部门专门培训,并经考试合格后方可上岗;严禁非操作人员使用。
2、焊机主电源、控制箱部分不防水,使用时严禁电器、控制箱部分进水;如遇雨天施工,应对焊机采取保护措施.3、在零度以下进行焊接时,必须采取适当的保温措施,以保证焊接面有足够的温度。
4、焊接面在焊接前必须清洁和干燥,需要焊接的部位不能有损伤破坏、杂质、污垢(如:污物、油脂、切屑等)。
5、确保焊接过程的连续性,焊接完成后应当进行充分的自然冷却,确保焊接质量。
6、对于DN≤90mm的管材及管件,不允许使用热熔对接的焊接方法。
PE热熔对焊机操作规程模版
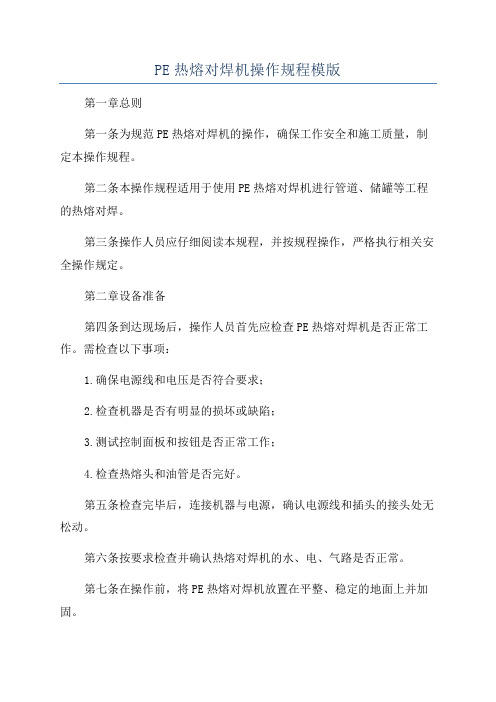
PE热熔对焊机操作规程模版第一章总则第一条为规范PE热熔对焊机的操作,确保工作安全和施工质量,制定本操作规程。
第二条本操作规程适用于使用PE热熔对焊机进行管道、储罐等工程的热熔对焊。
第三条操作人员应仔细阅读本规程,并按规程操作,严格执行相关安全操作规定。
第二章设备准备第四条到达现场后,操作人员首先应检查PE热熔对焊机是否正常工作。
需检查以下事项:1.确保电源线和电压是否符合要求;2.检查机器是否有明显的损坏或缺陷;3.测试控制面板和按钮是否正常工作;4.检查热熔头和油管是否完好。
第五条检查完毕后,连接机器与电源,确认电源线和插头的接头处无松动。
第六条按要求检查并确认热熔对焊机的水、电、气路是否正常。
第七条在操作前,将PE热熔对焊机放置在平整、稳定的地面上并加固。
第三章操作流程第八条操作人员应佩戴符合要求的个人防护装备,如安全帽、防护眼镜、防护服、防护手套、防护鞋等。
第九条操作人员应仔细查看并拆开PE管道的保护布,确保管道表面光滑干净。
第十条操作人员应根据需要调整PE热熔对焊机的工作温度和时间,以保证热熔的效果。
第十一条在对焊前,先将PE管道两端与热熔头相连接,同时按下操作按钮,预热热熔头。
第十二条当预热时间到达要求后,操作人员将热熔头抬起,保持合适的角度,使其于管道齐平。
第十三条按下操作按钮,使得PE热熔对焊机的热熔头与管道接触,并均匀施加一定的压力。
第十四条按下计时按钮开始计时,并保持一定的压力,直至计时结束。
第十五条计时结束后,抬起热熔头,停止供料,将热熔头移开并观察焊缝。
第十六条检查焊接效果,焊缝应整齐紧密、无水泡或其它缺陷。
第十七条若焊缝出现问题,应及时停机并查找原因。
在确认问题解决后,方可进行下一步操作。
第四章设备维护保养第十八条每日结束操作后,操作人员应对PE热熔对焊机进行清洁,包括清除机身内外的污垢、热熔头残留物等。
第十九条定期对PE热熔对焊机进行保养,包括对润滑、冷却系统进行检查和维修。
PE管道焊接操作规程

PE管道焊接操作规程PE管线具有易施工,速度快,耐腐蚀,无污染,使用寿命长等特点。
PE管道连接主要有两种方法:热熔连接和电熔连接。
目前主管道主要采用热熔连接。
热熔连接原理是将两根PE 管道的配合面紧贴在加热工具上来加热其平整的端面直至熔融,移走加热工具后,将两个熔融的端面紧靠在一起,在压力的作用下保持到接头冷却,使之成为一个整体。
一、焊接准备。
热熔焊接施工准备工作如下:①将与管材规格一致的卡瓦装入机架;②准备足够的支撑物,保证待焊接管材可与机架中心线处于同一高度,并能方便移动;③设定加热板温度200~230℃(本数据以杭州东雷机械厂供应的焊机为参考,具体温度以厂家提供的数据为准);④接通焊机电源,打开加热板、铣刀和油泵开关并试运行。
二、焊接。
焊接工艺流程如下:检查管材并清理管端→紧固管材→铣刀铣削管端→检查管端错位和间隙→加热管材并观察最小卷边高度→管材熔接并冷却至规定时间→取出管材。
在焊接过程中,操作人员应参照焊接工艺卡各项参数进行操作,而且在必要时,应根据天气、环境温度等变化对其进行适当调整:①核对欲焊接管材规格、压力等级是否正确,检查其表面是否有磕、碰、划伤,如伤痕深度超过管材壁厚的10% ,应进行局部切除后方可使用;②用软纸或布蘸酒精清除两管端的油污或异物;③将欲焊接的管材置于机架卡瓦内,使两端伸出的长度相当(在不影响铣削和加热的情况下尽可能短,宜保持20~30mm),管材机架以外的部分用支撑物托起,使管材轴线与机架中心线处于同一高度,然后用卡瓦紧固好;④置入铣刀,先打开铣刀电源开关,然后再合拢管材两端,并加以适当的压力,直到两端有连续的切屑出现后(切屑厚度为0.5~10mm,通过调节铣刀片的高度可调节切屑厚度),撤掉压力,略等片刻,再退开活动架,关闭铣刀电源;⑤取出铣刀,合拢两管端,检查两端对齐情况(管材两端的错位量不能超过壁厚的10% ,通过调整管材直线度和松紧卡瓦予以改善;管材两端面间的间隙也不能超过0.3mm(de225mm 以下)、0.5mm(de225mm~400mm)、1mm(de400mm以上),如不满足要求,应在此铣削,直到满足要求。
PE管热熔对接焊机操作指导书
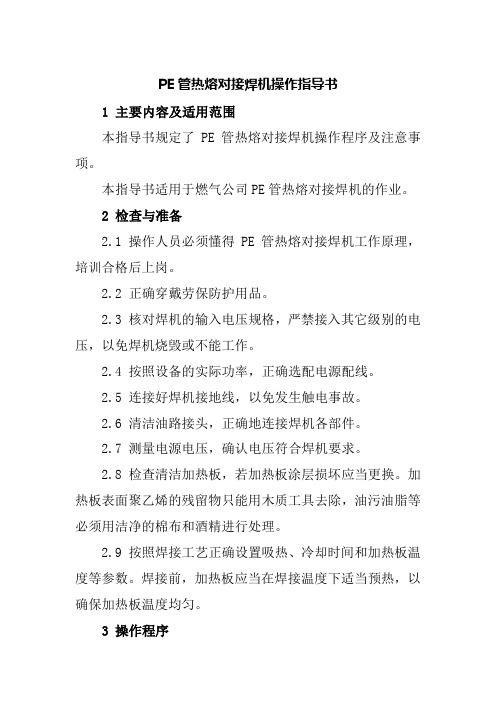
PE管热熔对接焊机操作指导书1 主要内容及适用范围本指导书规定了PE管热熔对接焊机操作程序及注意事项。
本指导书适用于燃气公司PE管热熔对接焊机的作业。
2 检查与准备2.1 操作人员必须懂得PE管热熔对接焊机工作原理,培训合格后上岗。
2.2 正确穿戴劳保防护用品。
2.3 核对焊机的输入电压规格,严禁接入其它级别的电压,以免焊机烧毁或不能工作。
2.4 按照设备的实际功率,正确选配电源配线。
2.5 连接好焊机接地线,以免发生触电事故。
2.6 清洁油路接头,正确地连接焊机各部件。
2.7 测量电源电压,确认电压符合焊机要求。
2.8 检查清洁加热板,若加热板涂层损坏应当更换。
加热板表面聚乙烯的残留物只能用木质工具去除,油污油脂等必须用洁净的棉布和酒精进行处理。
2.9 按照焊接工艺正确设置吸热、冷却时间和加热板温度等参数。
焊接前,加热板应当在焊接温度下适当预热,以确保加热板温度均匀。
3 操作程序3.1 将管垫平,调整同心度,利用夹具校正管材不圆度,并且留有足够的焊接距离。
3.2 铣削焊接面,铣削足够厚度,使焊接端面光洁、平行,确保对接端面间隙小于0.3mm;错边量小于焊接处壁厚的10%。
重新装夹时必须重新铣削。
3.3 测量并且记录拖动压力(P拖)。
3.4 放置加热板,调整焊接压力(P1)=拖动压力(P拖)+焊接规定压力(P2)。
当加热板两侧焊接处圆周卷边凸起高度达到规定值时,降压至拖动压力(P拖)或者在确保加热板与焊接端面紧密贴合的条件下,开始吸热计时。
3.5到达吸热时间(蜂鸣器将发出蜂鸣声),迅速打开夹具,取出加热板,并快速检查加热后的管材端面,确认取出加热板过程中未损伤熔融端面后,迅速闭合夹具,在规定时间内迅速将压力升到P3(P3= P拖冷却压力),同时按下冷却时间按钮,开始记录冷却时间。
3.6 达到冷却时间后,将压力降至零,拆卸完成焊接的焊机元件。
4 注意事项4.1 铣削完毕闭合夹具,此时液压缸不应达到最大行程,以保证焊接质量要求。
PE100给水管实壁管对接焊接工艺

PE实壁管对接焊接
①目测管材是否有破损,以及液压油量是否在规定之内(不可低于警戒值作业)
②接通电源,将两根管道放置于焊架上,预留铣刀铣边距离(每个管材预留50mm 左右即可),固定好管材,确使两端对接误差不高于管材壁厚1/10③放置铣刀,启动电源,用铣刀清洗两端管口不平整的地方,并目测两端口对接误差不高于管材壁厚1/10④卸下铣刀,小压力移动管材,当两端面闭合时,记出该拖动的最小压力值,如0.6MPa,移除管材⑤(管子面积/油缸面积)+最小拖动压力=热熔对接压力(实际焊接压力=对接压力+拖动压力P=P1+P2)❀注:一个液压阀6.3,两个液压阀12.6,算得热熔压力为1.6MPa+0.6MPa=2.2MPa⑥用酒精清洁热熔管材端面。
将加热板(220±10℃)放置于两管材中间,加压至2.2MPa,待其卷料在壁厚1.5mm后(壁厚的1/10),然后泄压至0.6MPa,再加热约150秒(时间取壁厚10倍/秒)⑦迅速取出加热板,且及时将两管材对接重合(压力会自动升至预先设置的2.2MPa),冷却约15分钟即可(时间取壁厚1倍/分钟)。
PE管道热熔连接操作规程

PE管道热熔连接操作规程1、目的为规范热熔连接操作程序,提高管道操作的可靠性,保证焊接质量,特指定本规程. 2、焊接准备焊接准备是焊接前必须进行的步骤,操作人员必须予以充分的重视。
2.1 设备应置于平整、干燥、并有足够操作空间的场地,否则,应采取相应的措施。
2。
2 检查整个机具各个部位的紧固件有无脱落或松动,并予以必要的处理。
2。
3 检查整机电器线路有无损坏,并予以必要的处理。
2。
4 检查液压箱内液压油是否充足.2。
5 确认电源与机具输入要求是否匹配。
2.6 将与规格一致的卡瓦装入机架。
2.7 准备足够的支撑物,以保证待焊接管材可与机架中心线处于同一高度,并能方便移动。
2.8 将焊机各部件按照要求插装连接好并检查无误。
2。
9 设定加热板温度在200~220℃。
2。
10 接通焊机电源,打开加热板、铣刀和油泵开关并试运行,检查各自工作是否正常。
3、焊接在焊接过程中,操作人员一般应参照焊接工艺卡各项参数进行操作.单必要时应根据天气、环境温度等变化对其做适当调整。
3.1 核对欲焊接的管材规格、压力等级是否准确,检查其表面是否有磕、碰、划伤,如伤痕深度超过管材壁厚的10%,应予以局部切除后方可使用。
3.2 用干净的布清除两管端的油污或异物。
3。
3 将欲焊接的管材置于机架卡瓦内,使两端伸出的长度相当(在不影响铣削和加热的情况下应尽可能短),机架以外的管材用支撑物托起,使管材轴线与机架中心线处于同一高度,然后用卡瓦紧固好。
3。
4 置入铣刀,先打开铣刀电源开关,然后再合拢管材两端并加以适当的压力(铣削压力高于拖动力P0 0。
2到0。
3MPa即可),直到两端均有连续的切屑出现后,撤掉压力,略等片刻,让铣刀在无压力的状态下空转几圈,再退开活动架,关掉铣刀电源。
切屑厚度在0。
5mm左右为最佳,通过调节铣刀片的高度可调节切屑厚度。
3.5 取出铣刀,合拢两管端,检查两端对齐情况。
管材两端的错位量不应超过壁厚的10%,通过调整管材的直线度和松紧卡瓦可予以改善;管材两端面间的局部间隙也不应超过壁厚的10%,否则应再次铣削,直到满足上述要求。
- 1、下载文档前请自行甄别文档内容的完整性,平台不提供额外的编辑、内容补充、找答案等附加服务。
- 2、"仅部分预览"的文档,不可在线预览部分如存在完整性等问题,可反馈申请退款(可完整预览的文档不适用该条件!)。
- 3、如文档侵犯您的权益,请联系客服反馈,我们会尽快为您处理(人工客服工作时间:9:00-18:30)。
PE管材对接焊操作规程
一.总体技术要求
1. 用于对接焊的管材、管件应由相同牌号的材料制成,对于由不同材料制成的管材,应由生产厂有出具两种材料相熔的证明。
2. 用于对接焊的管材必须是经检验合格的合格产品,且管材外径、壁厚相同。
3. 聚乙烯管道对接焊操作人员必须经过专业培训,持证上岗。
4. 焊接机具必须处于完好正常状态。
5. 环境温度低于-5℃时或下雨、刮风、太阳暴晒等恶劣天气下,必须采取防护措施。
二.工艺流程
管材准备-夹紧定位-铣端面-系统拖动力确定-端面-熔接-冷却定型
1. 管材准备:准备需要对接焊的管材
2. 夹紧定位:根据管材的规格,配备相应的夹模,将焊机的两夹具放在最大张开位置,将管材固定在两夹具内,使相对管端面伸出夹具拖板约50mm,移动夹具到两端面接触,校正使两端面完全重合。
3. 铣端面:张开两夹具,将铣刀盘放置在夹具中间,开动铣刀盘,缓慢地移动夹具,使两端面压紧铣刀盘,将两对接焊端面铣平整。
切屑厚度不应超过0.2mm。
移动待焊管段使两个端面贴合,两平面之间的最大缝隙不应超过
0.5mm,同时两管边的错位也不能超过壁厚的10%。
否则,应校正后再次重复上面的处理。
铣削后的端面不能被污染,应立即开始熔接。
4. 系统拖动力确定(P0):将两夹具移动到最大张开位置,然后将压力调节开关放置最小,操纵夹具移动手柄使夹具闭合,同时调整压力调节旋钮,使压力逐渐增大,观察夹具的移动速度,确定一个适宜的值,保持压力旋钮不变,使两夹具移动几次,观察系统压力P0的变化,最终将较准确的P0值记录在工艺原始记录卡上。
5. 设备系统对接压力确定(P2):
P2=P×π×e×(D-e)/s+ P0
P: 单位对接面积应施加的力为0.18-0.22N/mm2
e: 壁厚
D: 外径
S: 焊接机具液压系统执行缸活塞总有效面积
6. 端面熔接:设定加热板的温度,控制在规定的范围内。
通过秒表设定时间参数。
熔接过程压力-时间的关系曲线及各种规格管材的有关熔接参数表的示。
将达到熔接温度的加热板放在两待焊面中间,操作动夹具端面在对接压力P2的作用下,双面紧贴到加热板面上,观察待焊面在加热的两边逐渐溢出熔融
料(称为预热卷边),当卷边的高度达到参数表的值时,通过减压按键将吸热压力降至P1,吸热时间达到后,将动卡具移开,迅速撤出加热板,使两个待焊端面熔接,线性加压至P2,使两个端面完全贴合,同时溢出的熔融物料在熔缝区周围形成两道均匀的焊环。
7. 为使焊接面不被污染,每次焊接前必须用洁净的绵织物将加热材擦净(或用无水酒精擦拭)。
8. 当遇到大风天气时,管材的另一端应封堵,避免管内通风冷却。
9. 冷却定型:熔接完成后,按下秒表开始计时,冷却时间到后,管件焊接完成。
冷却过程中不应受到任何外力的影响。
禁止任何形式的人工加速冷却方式。
10. 焊接参数记录:焊接完成后,记录操作者、焊机型号、天气、环境温度、拖动压力、焊接压力、焊接温度、焊接时间、吸热时间、操作时间等参数。
三.管件熔接压力-时间关系曲线
P1:吸热压力
P2:预热及焊接压力
t1:预热时间(卷边凸起达到预定高度的时间)
t2:吸热时间
t3:转换时间
t4:加压时间
t5:冷却时间
焊接参数的确定:
-焊接温度:230±5℃
-压力P1:低
-压力P2: P2=P×π ×e×(D-e)/s+ P0
P: 单位对接面积应施加的力为0.18-0.22N/mm2
e: 壁厚(mm)
D: 外径(mm)
S: 焊接机具液压系统执行缸活塞总有效面积
t1:卷边凸起达到0.5+0.1e(mm)高度的时间
t2:18e(s)
t3:最大3+0.01D(s)
t4:最大3+0.03D(s)
t5:15+0.5e(min)。