中心孔加工
中心孔及螺纹加工

XXX制造集团有限公司钻中心孔、钻孔及车螺纹的说明文件编号:受控状态:分发号:编制:日期:审核:日期:批准:日期2012 年04 月06 日发布2011 年04 月06日实施XXX制造集团有限公司发布编制说明一、为了保证产品质量,根据公司实际需要,技术部对本公司的自制件、外购件和外协件的尺寸,形状公差作如下规定:二、本文件由XXX制造集团有限公司技术部根据国家标准,结合我单位产品情况,对钻中心孔、钻孔及车螺纹汇总、整理。
三、除内部使用需要外(包括认证审核需要),未经允许任何人不能以任何形式提供给他人。
报送:技术质量经理、质量保证、技术负责人;发送:技术部、质检部、生产部、各生产车间钻中心孔钻孔及普通螺纹的加工说明一、钻中心孔说明:•在工件安装中,一夹一顶或两顶都要先预制中心孔,在钻孔时为了保证同轴度也往往要先钻中心孔来决定中心位置。
•在车床上钻孔加工也是比较常见的工艺,如齿轮、轴套、带轮、盘盖类等零件的孔,都必须要先进行钻孔加工。
•钻中心孔和钻孔是车工必须要首先掌握的基本技能。
1、钻中心孔(1)中心孔的型式•中心孔是机械设计中常见的结构要素,可用作零件加工和检测的基准。
GB/T145—2001规定中心孔有A、B、C、R四种型式。
•以上四种型式中心孔的圆锥角为60°,重型工件用75°或90°的圆锥角•中心孔通常用中心钻钻出,直径在6.3mm以下的中心孔一般采用钻的加工工艺,较大的中心孔可采用车、锪锥孔等加工方法。
制造中心钻的材料一般为高速钢。
(2)中心钻的几何结构(3)中心孔的作用与结构(4)中心孔的标注意义中心孔表示法(摘自GB/T4459.5 —— 1999 )A 型是普通中心孔,用于 精度要求一般的工件。
B 型是带护锥的中心孔,精度要求较高并需多次使用中心孔的工件,一般都采用B 型中心孔C 型是带螺纹的中心孔, 需要把其他零件轴向 固定在轴上时采用。
R 型中心孔是将A 型中心孔的圆锥母线改为圆弧线,以减少中心孔与顶尖的接触面积,减少摩擦力,和顶针的接触形式为线接触,提高了重复定位的精度 。
加工中心孔加工编程

【深化讨论H】
程序组合与刀具长度补偿(H) ☆刀具长度补偿建立与取消
建立方式:
取消方式: 【参数说明】
G49 (Z____);
G43——刀具长度正补偿/离开工件补偿;
G44——刀具长度负补偿/趋向工件补偿; H——刀具长度偏置寄存器号(H01~H32)
【深化讨论】
☆刀具长度补偿量设置→工件坐标系原点Z0设置 ●方法1:工件坐标系原点Z0设定在工件上表面
固定循环编程法
O0001;(程序名)
G90G80G40;(初始化) G91G28Z0;( 回换刀点) M6T1;(装刀) M03S2000M08;(刀具旋转) G54G90G0Z100;(初始平面) G0X0Y0;(试走)
M9 G0X200;(刀退出) M30;(程序结束)
【注】G80、G01~G03等代码 可以取消固定循环
G73 快速加工深孔 易断屑排屑/冷却,退刀量小
【自学G82】
【附】G82:带停顿的钻孔循环 (锪孔) G98(G99)G82 X_Y_Z_R_ P_ F_
初 始 点B 参 照 点R
G98
初 始 B点 参 照 R点 孔 底 Z点 鍃钻
与G81区别: 孔底暂停P 用于加工沉孔、 盲孔,以提高 孔深精度
G99
孔 底 点Z
加工到底,停顿
【自学G74】
【附】G74:反攻丝循环 G98/G99 G74 X_Y_Z_R_P_F_
初始 B点
左旋 丝锥
参照 R点
G98
初始 B点 参照 R点
主轴 反转 攻丝
孔底 Z点
G99 主轴
正转 退出
与G84区别: 攻左旋螺纹, 主轴反转攻丝, 到孔底时主轴 停止旋转,正 转退回
各种中心孔的优缺点
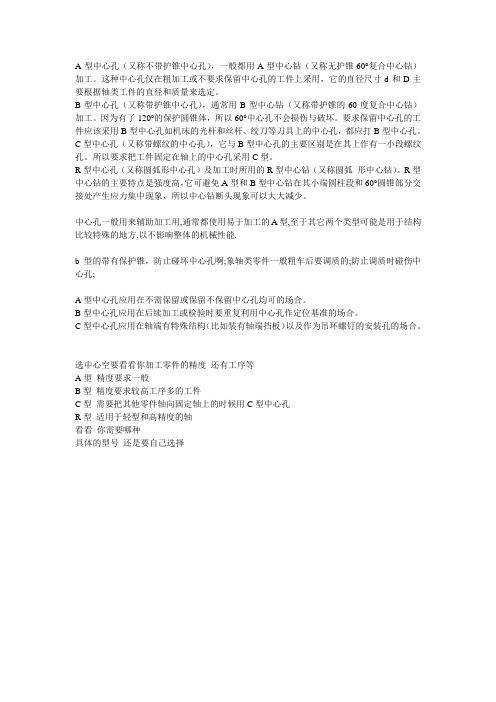
A型中心孔(又称不带护锥中心孔),一般都用A型中心钻(又称无护锥60°复合中心钻)加工。
这种中心孔仅在粗加工或不要求保留中心孔的工件上采用,它的直径尺寸d和D主要根据轴类工件的直径和质量来选定。
B型中心孔(又称带护锥中心孔),通常用B型中心钻(又称带护锥的60度复合中心钻)加工。
因为有了120°的保护圆锥体,所以60°中心孔不会损伤与破坏。
要求保留中心孔的工件应该采用B型中心孔如机床的光杆和丝杆、绞刀等刀具上的中心孔,都应打B型中心孔。
C型中心孔(又称带螺纹的中心孔),它与B型中心孔的主要区别是在其上作有一小段螺纹孔。
所以要求把工件固定在轴上的中心孔采用C型。
R型中心孔(又称圆弧形中心孔)及加工时所用的R型中心钻(又称圆弧形中心钻)。
R型中心钻的主要特点是强度高,它可避免A型和B型中心钻在其小端圆柱段和60°圆锥部分交接处产生应力集中现象,所以中心钻断头现象可以大大减少。
中心孔一般用来辅助加工用,通常都使用易于加工的A型,至于其它两个类型可能是用于结构比较特殊的地方,以不影响整体的机械性能.b型的带有保护锥,防止碰坏中心孔啊;象轴类零件一般粗车后要调质的;防止调质时碰伤中心孔;A型中心孔应用在不需保留或保留不保留中心孔均可的场合。
B型中心孔应用在后续加工或检验时要重复利用中心孔作定位基准的场合。
C型中心孔应用在轴端有特殊结构(比如装有轴端挡板)以及作为吊环螺钉的安装孔的场合。
选中心空要看看你加工零件的精度还有工序等A型精度要求一般B型精度要求较高工序多的工件C型需要把其他零件轴向固定轴上的时候用C型中心孔R型适用于轻型和高精度的轴看看你需要哪种具体的型号还是要自己选择。
中心孔选用标准

中心孔选用标准全文共四篇示例,供读者参考第一篇示例:中心孔是工件上用来固定、定位和传动力矩的孔,是加工中最基本的定位孔。
在机械加工中,中心孔的选用标准对于加工精度、效率和质量起着至关重要的作用。
合理选择中心孔标准,能够确保工件的加工精度、能耗、生产效率和质量,提高生产效率,降低成本,是加工中不可忽视的重要环节。
中心孔的选用标准应符合工件的实际要求。
在进行中心孔选用时,需根据工件的形状、尺寸、材质、加工量等因素来选择合适的中心孔标准。
通常情况下,标准中心孔有A、B、C、D四种类型,其中A为精密型、B为一般型、C为普通型、D为特殊需求型。
对于高精度要求的工件,应选择精密型的中心孔标准;而对于一般加工要求的工件,则可以选择一般型或普通型的中心孔标准。
中心孔的选用标准应考虑加工方式和精度要求。
不同的加工方式对中心孔的选用标准也有所要求,如钻孔、铣削、车削等加工方式对中心孔的要求也不尽相同。
根据工件的加工精度要求来选择合适的中心孔标准也是至关重要的。
在加工高精度工件时,应选择更高精度的中心孔标准,以保证加工精度和质量。
中心孔的选用标准还需考虑被加工零件的后续加工工序。
有些工件在中心孔定位时需要进行多次加工,因此需要考虑后续加工工序对中心孔的要求,选择适合的中心孔标准。
在选择中心孔标准时还要考虑工件加工后的稳定性和可靠性,以确保全过程加工的顺利进行。
第二篇示例:中心孔是机械设备上常见的一种孔型,其作用是用来定位和固定零件。
为了保证设备的正常运行和使用寿命,选用合适的中心孔标准至关重要。
下面我们来详细介绍中心孔选用标准及其重要性。
一、中心孔的作用中心孔通常位于轴端或座部,用来定位轴心位置和确保零件间的相对位置。
在安装和组装机械设备时,通过中心孔可以快速准确地定位零件,提高生产效率和产品质量。
中心孔还可以起到固定零件的作用,避免零件在运动过程中发生错位或脱落。
1. 直径尺寸:中心孔的直径应符合相应的标准规定,可以避免因孔径过大或过小导致的轴心不准确或轴心偏移现象。
毕业设计中心孔加工工艺部分
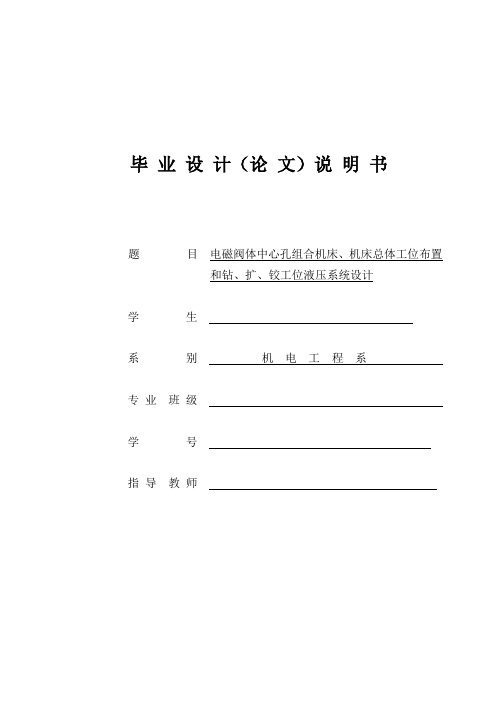
毕业设计(论文)说明书题目电磁阀体中心孔组合机床、机床总体工位布置和钻、扩、铰工位液压系统设计学生系别机电工程系专业班级学号指导教师毕业设计(论文)任务书电磁阀体中心孔组合机床、机床总体工位布置设计(论文)题目:和钻、扩、铰工位液压系统设计系:机电工程系专业:机械设计制造及其自动化班级:学号:学生:指导教师:接受任务时间教研室主任(签名)系主任(签名)1.毕业设计(论文)的主要内容及基本要求①、设计依据:依据实物测绘出25升电磁阀体零件图;生产纲领5万件/年。
编制电磁阀体中心孔加工工序卡片;绘制电磁阀体中心孔加工组合机床加工示意图;并确定钻、扩、铰工位动作循环。
②、设计该机床钻、扩、铰孔工位液压系统,编写其液压系统设计计算说明书;液压元件各细表;绘制液压系统原理图。
③、绘制液压缸装配图和一零件图。
2.指定查阅的主要参考文献及说明①、《液压传动》西南交通大学出版社②、《机械制造技术基础》西南交通大学出版社③、《机械设计手册》机械工业出版社④、《组合机床设计》机械工业出版社目录中文摘要 (Ⅰ)英文摘要 (Ⅱ)前言 (1)第一章电磁阀体中心孔加工工艺 (2)1.1 零件分析 (2)1.2 明确设计要求 (2)1.3对电磁阀体总体加工工艺方案设计 (2)1.3.1确定毛坯制造形式 (2)1.3.2基准的选择 (3)1.3.4电磁阀体中心孔加工中心孔的槽的加工部分 (3)1.3.5电磁阀体总体加工工艺 (3)1.4 确定工作循环 (3)1.5 专用机床的概述 (4)第二章编制中心孔加工工艺 (6)2.1确定加工方案 (6)2.1.1刀具的选择 (6)2.2钻孔 (6)2.2.1钻削时的进给量 (6)2.2.2确定其各加工余量 (6)2.2.3确定麻花钻直径并选择 (6)2.2.4确定主轴速度的转速 (7)2.3扩孔 (7)2.3.1扩孔钻的选择 (7)2.3.2扩孔时的速度 (7)2.3.3扩孔时的转速 (8)2.4铰孔 (8)2.4.1铰刀的选择 (8)2.4.2铰刀的速度 (8)2.4.3铰刀转速 (8)2.5计算切削力 (8)2.5.1钻孔时的切削力 (8)2.5.2扩孔时的扭矩 (9)2.6钻、扩、铰切削的功率 (9)2.6.1钻孔时的功率 (9)2.6.2扩孔时的功率 (9)第三章液压传动的设计 (10)3.1负载分析 (10)3.2速度图和负载图的绘制 (11)3.3液压缸主要参数的确定 (12)3.3.1稳定性验算 (13)3.4液压缸的组成 (15)3.4.1缸筒和缸盖的联接 (15)3.4.2活塞和活塞杆的联接 (15)3.4.3液压缸的密封 (16)3.5液压系统的拟定 (17)3.5.1液压回路的选择 (17)3.5.2缸筒的厚度 (21)3.5.3螺栓的计算 (21)3.5.4端盖厚度计算 (22)3.5.5缸体连接计算 (22)3.6液压元件的选择 (24)3.6.1选择液压泵 (24)3.6.2阀类元件辅助元件 (25)3.7液压系统的性能验算 (27)3.7.1回路压力损失验算 (28)3.7.2油液温升验算 (28)第6章结论 (30)参考文献 (31)致谢 (32)附录A:加工工序卡 (33)摘要电磁换向阀是液压传动中用来改变油路的重要零件,针对该零件的加工,特别设计一组合机床,按流水线运作,实现自动化加工。
浅谈中心孔与轴类加工
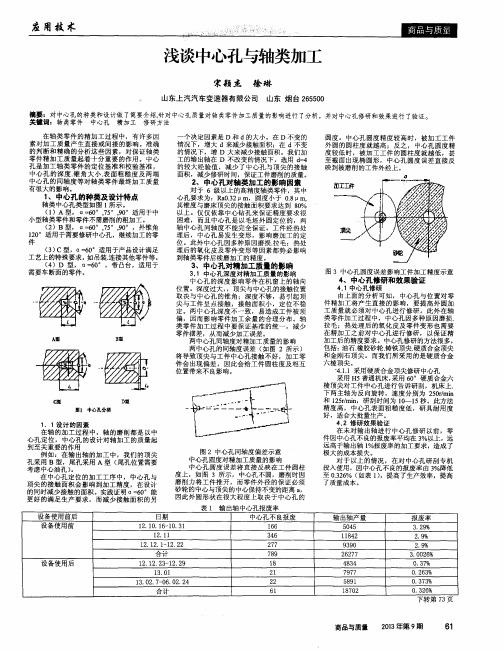
1 、中心孔 的种类及设计特点
轴类中心孔类型如 图 l 所示 。 ( 1 )A型 , a= 6 0 。, 7 5 。, 9 0 。适用于中 小型轴 类零件和零件不需磨削的粗加工 。 ( 2 )B型 , a= 6 0 。, 7 5 。, 9 0 。,外锥角 1 2 0 。适用 于需要修研 中心孔,继续加工的零 件 ( 3 ) C型 ,Q= 6 0 。适用 于产品设计满 足 工艺上 的特殊 要求 , 如吊装 . 连接 其他零件 等。 ( 4 )D 型 , a= 6 0 。 ,带 凸台 ,适用 于 需要车 断面 的零件 。
一
A 煎
B 垫 l
谮一
C 型 D 型
在精加工之 前对 中心 孔进行 修研 , 以保 证精 加工后的精度要求。中心孔修研 的方法 很多, 包括 : 油石. 橡胶砂轮 . 铸铁 顶尖 . 硬质 合金顶尖 和 金刚石项尖 。而我们 所采用 的是硬质合 金 六棱顶尖 。
‘ 4 . 1 . 1采用硬质合 金顶尖修 研中心孔 采用 H 5 普通机床 , 采用 6 0 。硬质 合金六 棱项尖对 工件 中心孔进行 告诉研 刮,机床上 . 下两 主轴为反 向旋转 ,速度 分别为 2 5 0 r / mi n 和 1 2 5 r / mi n ,研刮时间为 l O —l 5秒 。此方法 精度 高, 中心 孔表面粗糙 度低 ,研 具耐用度 好 ,适合大批量生产 。 4 . 2修研效果验证 在未对 输 出轴 进行 中心孔修研 以前,零 件因 中心孔不 良的报废率平均在 3 %以上 , 远 远高于输 出轴 1 %报废率的加工要求 ,造成 了 极大 的成本损失 。 对于 以上 的情 况,在对 中心孔研刮 专机 投入使用,因中心孔不 良的报废率 由 3 %降低 至0 . 3 2 6 %( 如表 1 ) ,提高 了生产效率 ,提高 了 质量 成 本 。
中心孔的标准
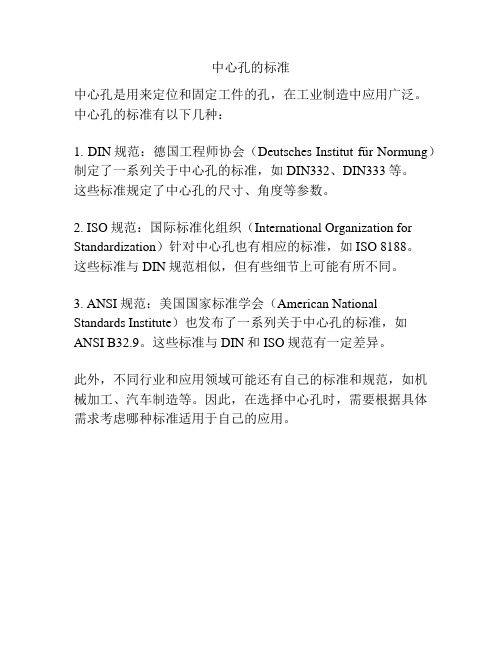
中心孔的标准
中心孔是用来定位和固定工件的孔,在工业制造中应用广泛。
中心孔的标准有以下几种:
1. DIN规范:德国工程师协会(Deutsches Institut für Normung)制定了一系列关于中心孔的标准,如DIN332、DIN333等。
这些标准规定了中心孔的尺寸、角度等参数。
2. ISO规范:国际标准化组织(International Organization for Standardization)针对中心孔也有相应的标准,如ISO 8188。
这些标准与DIN规范相似,但有些细节上可能有所不同。
3. ANSI规范:美国国家标准学会(American National Standards Institute)也发布了一系列关于中心孔的标准,如ANSI B32.9。
这些标准与DIN和ISO规范有一定差异。
此外,不同行业和应用领域可能还有自己的标准和规范,如机械加工、汽车制造等。
因此,在选择中心孔时,需要根据具体需求考虑哪种标准适用于自己的应用。
车床简便打中心孔方法
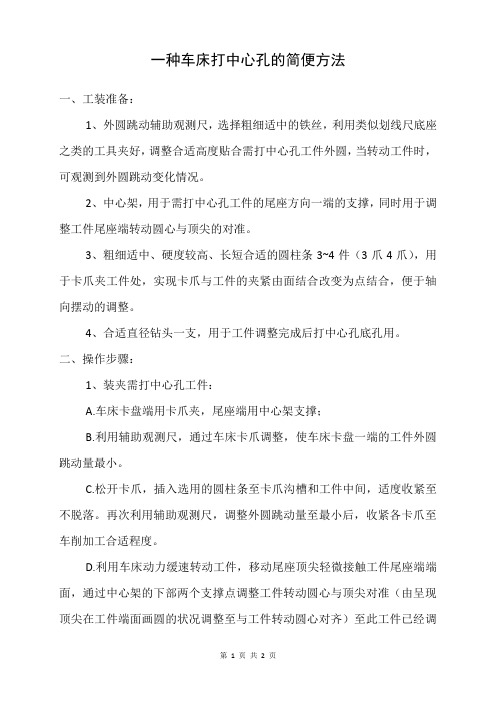
一种车床打中心孔的简便方法一、工装准备:1、外圆跳动辅助观测尺,选择粗细适中的铁丝,利用类似划线尺底座之类的工具夹好,调整合适高度贴合需打中心孔工件外圆,当转动工件时,可观测到外圆跳动变化情况。
2、中心架,用于需打中心孔工件的尾座方向一端的支撑,同时用于调整工件尾座端转动圆心与顶尖的对准。
3、粗细适中、硬度较高、长短合适的圆柱条3~4件(3爪4爪),用于卡爪夹工件处,实现卡爪与工件的夹紧由面结合改变为点结合,便于轴向摆动的调整。
4、合适直径钻头一支,用于工件调整完成后打中心孔底孔用。
二、操作步骤:1、装夹需打中心孔工件:A.车床卡盘端用卡爪夹,尾座端用中心架支撑;B.利用辅助观测尺,通过车床卡爪调整,使车床卡盘一端的工件外圆跳动量最小。
C.松开卡爪,插入选用的圆柱条至卡爪沟槽和工件中间,适度收紧至不脱落。
再次利用辅助观测尺,调整外圆跳动量至最小后,收紧各卡爪至车削加工合适程度。
D.利用车床动力缓速转动工件,移动尾座顶尖轻微接触工件尾座端端面,通过中心架的下部两个支撑点调整工件转动圆心与顶尖对准(由呈现顶尖在工件端面画圆的状况调整至与工件转动圆心对齐)至此工件已经调整至车床轴向最佳状态。
2、在尾座端面打中心孔:A.换下顶尖,换上装好合适钻头的钻夹头,在工件尾座端面钻出中心孔底孔。
B.更换钻头为中心钻,修出需要的中心孔。
至此完成打中心孔任务。
三、注意事项:1、调整外圆跳动时,由于细长轴的中部车削相对难度较大,尽量满足中部跳动最小的要求,将工件的跳动留在尾座端(跳动较大的情况,可以考虑两端分摊跳动量),车削加工时两端部让刀量较小,减小加工变形量。
2、尾部对中心时,在加工余量不存在问题的情况下,不考虑工件外圆跳动调整,只需调整工件转动圆心对准顶尖。
3、有需要打中心孔后进行外圆面车削加工的,在中心架支撑位置选择时,既要考虑尾座端工件调整的适宜性,还要考虑打中心孔之后的外圆加工过程中的中心架位置更换的适宜性,以减少位置更换次数,节约时间。
- 1、下载文档前请自行甄别文档内容的完整性,平台不提供额外的编辑、内容补充、找答案等附加服务。
- 2、"仅部分预览"的文档,不可在线预览部分如存在完整性等问题,可反馈申请退款(可完整预览的文档不适用该条件!)。
- 3、如文档侵犯您的权益,请联系客服反馈,我们会尽快为您处理(人工客服工作时间:9:00-18:30)。
中心孔加工
中心孔的加工工艺-
一.引言
中心孔又称顶尖孔,按国标GB145-1985,中心孔可分A
型中心孔,B型中心孔,C型中心孔,R型中心孔。
中心孔国家规定以外,还有JB/ZQ4236-4237-1986标准。
二.中心孔的作用
中心孔是轴内零件的基准,又是轴内零件的工艺基准,也是轴类零件的测量基准,所以中心孔对轴类零件的作用是非常重要的。
中心孔有:60、75、90度,其基准是60、75、90度的圆锥面。
三.根据精度等级确定中心孔加工的工艺方法
中心孔的基准面分别是:60、75、90度的圆锥面,同时也是轴类零件加工的工作面,所以,中心孔工作面质量的好坏,直接影响轴类零件的外圆质量。
在中心孔加工时,工艺方法主要从提高圆锥面质量和加工效率两个方面进行编制的,所以根据轴类零件的不同精度等级的要求和企业的生产现状,确定加工中孔的工艺方法如下:
(1)零件标准公差等级要求为IT10-IT12时,其标准公差值在0.04-0.012mm 之间。
中心孔的工艺为:车外圆—车端面—钻中心孔。
(2)零件标准公差等级要求为IT8-IT9,其标准公差值在0.014-0.036mm之间,中心孔的工艺为:车外圆—车端面—钻中心孔—车端面—钻中心孔—热处理—研中心孔圆锥面。
(3)零件标准公差等级要求为IT6-IT7,其标准公差值在0.006-0.012,中心孔的工艺为:粗车—热处理—(调质)—车外圆—车端面—钻中心孔—车端面—钻中心孔—粗研中心孔圆锥面—热处理—研中心孔圆锥面。
以上加工中心的工艺方法:一方面确保零件两端中心孔轴线同轴度误差控制在公差要求范围之内,另一方面确保中心孔圆锥面的几何形状误差和表面粗糙度控制在允许的范围之内,达到提高加工效率。
降低加工成本的目的。
四.加工中心孔几何精度和降低表面粗糙度的方法
中心孔的质量主要由几何精度、表面粗糙度中心孔圆锥面来影响的,加工中心孔圆锥面的加工方法有很多,常用的加工方法有下面6种方法:
(1)中心钻直接加工出圆锥面
(2)用硬质合金激光圆锥面
(3)用铸铁棒研圆圆锥面
(4)用橡皮砂轮研圆圆锥面
(5)用万能磨床磨削圆锥面
(6)用中心孔磨床磨削圆锥面
零件两端中心孔轴线的同轴度是由车加工中心孔来保证的,中心孔圆锥面几何形状和表面粗糙度也是由车工加工中心孔来打基础的,而研中心孔圆锥面而则是提高圆锥几何精度和降低表面粗糙度的辅助方法。
五.常用中心孔类型的改进
中心孔共有10种类型,但是常用的是国际GB145—1985A型中心孔和B型,A型中心孔主要用于零件的
加工后,中心孔不在继续使用;B型中心孔主要用于零件加工后,中心孔还要继续使用,所以120锥面是保护60度锥面的,为了提高工艺性和加工精度。
将圆锥面改成如图所示,这样也同样起到保护60度的作用。
60度B型中心孔是用60度B型中心钻加工出来的(见图3),所以L1的长度由中心钻L1来决定来决定的。
(中心孔L1的长度由零件的精度和自重来决定,而不能由B型中心钻L1来决定,因为L1过长将影响零件的加工精度。
六.结语
通过中心孔加工工艺粗初步探索和研究,在实践中不仅提高了零件的加工质量,而且为螺纹轴类零件的工艺设计提供了经验。