橡胶配方设计与功用
橡胶配方设计与功用
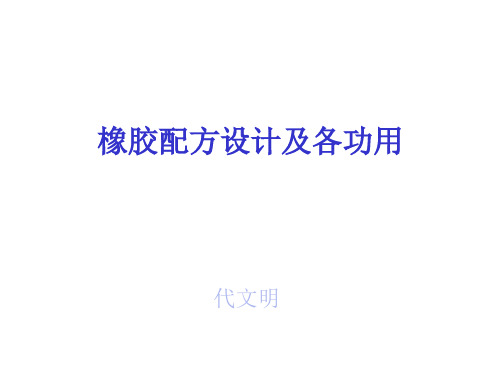
防焦剂
焦烧现象
胶料在贮存和加工过程中因受热的作用会发生早期硫化(交联)并失去流动性和再加工 的能力,这就是焦烧现象。
品类与性能 ---可以用作橡胶防焦剂的化学品有三类:
有机酸类; 亚硝基化合物类; 次磺酰胺类。
---任何防焦剂都应符合橡胶加工性能要求,即:
优良的防焦性能; 对不同促进剂和胶料选择性小; 对其他配合剂不敏感; 对胶料的硫化特性和硫化胶性能无不良影响; 贮存稳定和操作性能好; 不结块、不飞扬、易分散、不喷霜; 符合工艺安全和卫生要求。
偶合剂
• A-189, S-69, KBM803。
防护体系助剂----概述 防护体系助剂 概述
• 老化: 橡胶在加工、贮存和使用过程中,由于受内 外因素的综合影响,而逐渐失去其原有的优良性质, 这种现象叫橡胶的老化. • 常见的老化: 表面外观变软、发黏、发硬、龟裂、 发脆等,从而体现为强度下降、弹性消失、绝缘性 下降,其他的物理和化学性能也发生变化. , . • 影响老化的因素:
增塑剂(软化剂)
结构与作用 由于天然橡胶、丁苯橡胶、顺丁橡胶、异戊橡胶、 丁基橡胶和三元橡胶的分子量很大,多为无官能团 的无定型结构,且具有弹性,为了在加工时使这些 非极性分子能够相对移动产生变形,传统上是在混 炼时添加一定量的无官能团结构的脂肪烃、环烷 烃、芳香烃油品增塑剂和软化剂。对于极性橡胶, 必须配用脂肪酸或其酯,或其卤化烃类极性增塑 剂。
促进剂(触媒)
原理: 指加入胶料后能缩短硫化时间和降低硫 化温度的物质。 功用: 改变硫化速率及硫化时间,有时促进剂 可以共用,使用上称一次促进剂,如LM,DM, 及二次促进剂,如TS.
架桥剂
功用: 使橡胶由杂乱无序的分子结构,变成组 织严密完整的分子架构,即由原来可塑性 弹性体变成热固性弹性体. 种类: 硫磺,过氧化物,金属加硫(ZnO, MgO), 紫外线加硫等. 硫磺: 以硫作硫化剂同橡胶进行交联反应形成 的几种典型的交联键结构:单硫键,双硫键, 多硫键,临位多硫键,C-C交联键,环硫键;
第六章橡胶配方设
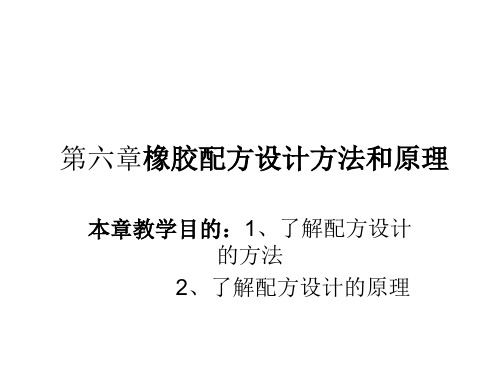
第二节 取得工艺性能的配方设计原理
• 第二节 取得工艺性能的配方设计原理 • 一、粘度(或可塑度) • 粘度过大,混炼时粉状配合剂不易混入,挤出的 半成品表面粗糟,收缩率大,半成品硫化时流动 性差,易使产品产生缺胶,气孔等缺陷。粘度过 小,混炼时颗粒极小的粉状配合剂反而分散不均 匀,成型时变形大,产品的物理机械性能下降。 • 生胶的粘度可通过塑炼方法来降低。 • 加入软化剂一般都能使胶料的粘度降低, • 加入填料均能使胶料的粘度增加。
三、 橡胶配方的表示方法
• 橡胶配方的内容包括:胶料的名称及代号、 胶料的用途、生胶及各种配合剂的用量、 含胶率、比重及胶料的物理机械性能等。 • 第一种以重量分数表示的配方,基本配方 • 第二种是以重量百分数来表示的配方 • 第三种是以体积百分数来表示的配方 • 第四种是符合生产上用的重量配方,称为 生产配方 • 四 鉴定胶料配方的物理指标
二、混炼性
• 混炼性取决于配合剂对橡胶的互溶性或湿 润性。 • 软化剂(增塑剂)、再生胶和有机配合剂 硫磺 、疏水性的填料,如炭黑等,能被橡 胶所湿润,因此容易与橡胶混合,具有很 好的混炼性。 • 当使用亲水性的填料时,在配方中应加入 一些表面活性剂,如硬脂酸、高级醇、含 氮有机化合物,某些树脂和软化剂等有助 于这些填料的分散。
六、挤出
• 应使胶料降低弹性恢复,减少挤出时口型膨胀和 有利于保持半成品的形状和尺寸等。 • (1)含胶率宜低 • (2)配用再生胶有降低挤出变形 • (3)配入油膏、矿物油、硬脂酸、石蜡等润滑性 的软化剂,有减少口型阻力。 • 七、粘着性 • (1)应选用自粘性好的生胶 • (2)选用增粘作用大的软化剂 • (3)选用补强性大的填料 • (4)容易喷出的配合剂(如蜡类、促进剂TMTD、 硫磺等)应尽量少用
橡胶配方的组成和作用及其分类
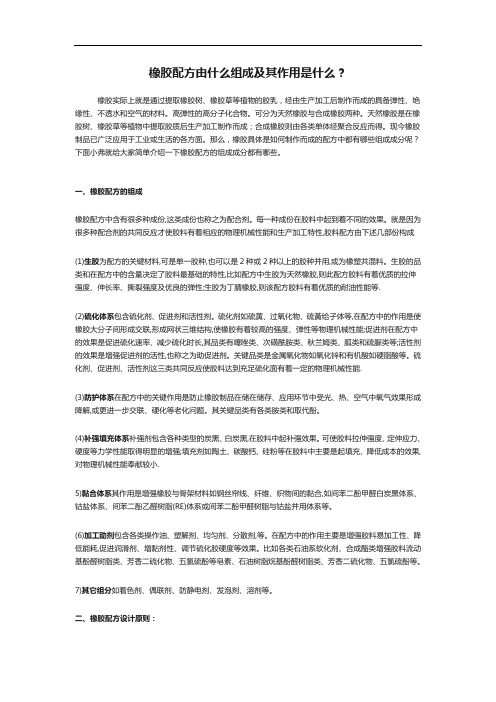
橡胶配方由什么组成及其作用是什么?橡胶实际上就是通过提取橡胶树、橡胶草等植物的胶乳,经由生产加工后制作而成的具备弹性、绝缘性、不透水和空气的材料。
高弹性的高分子化合物。
可分为天然橡胶与合成橡胶两种。
天然橡胶是在橡胶树、橡胶草等植物中提取胶质后生产加工制作而成;合成橡胶则由各类单体经聚合反应而得。
现今橡胶制品已广泛应用于工业或生活的各方面。
那么,橡胶具体是如何制作而成的配方中都有哪些组成成分呢?下面小弗就给大家简单介绍一下橡胶配方的组成成分都有哪些。
一、橡胶配方的组成橡胶配方中含有很多种成份,这类成份也称之为配合剂。
每一种成份在胶料中起到着不同的效果。
就是因为很多种配合剂的共同反应才使胶料有着相应的物理机械性能和生产加工特性,胶料配方由下述几部份构成(1)生胶为配方的关键材料,可是单一胶种,也可以是2种或2种以上的胶种并用,或为橡塑共混料。
生胶的品类和在配方中的含量决定了胶料最基础的特性,比如配方中生胶为天然橡胶,则此配方胶料有着优质的拉伸强度、伸长率、撕裂强度及优良的弹性;生胶为丁腈橡胶,则该配方胶料有着优质的耐油性能等.(2)硫化体系包含硫化剂、促进剂和活性剂。
硫化剂如硫黄、过氧化物、硫黃给子体等,在配方中的作用是使橡胶大分子间形成交联,形成网状三维结构,使橡胶有着较高的强度、弹性等物理机械性能;促进剂在配方中的效果是促进硫化速率、减少硫化时长,其品类有噻唑类、次磺酰胺类、秋兰姆类、胍类和硫脲类等;活性剂的效果是增强促进剂的活性,也称之为助促进剂。
关键品类是金属氧化物如氧化锌和有机酸如硬脂酸等。
硫化剂、促进剂、活性剂这三类共同反应使胶料达到充足硫化面有着一定的物理机械性能.(3)防护体系在配方中的关键作用是防止橡胶制品在储在储存、应用环节中受光、热、空气中氧气效果形成降解,或更进一步交联、硬化等老化问题。
其关键品类有各类胺类和取代酚。
(4)补强填充体系补强剂包含各种类型的炭黑、白炭黑,在胶料中起补强效果。
橡胶制品配方设计与胶料工艺性能的关系

橡胶制品配方设计与胶料工艺性能的关系橡胶制品是一种重要的工业原材料,广泛应用于汽车制造、电子设备、建筑材料等领域。
而橡胶制品的性能,很大程度上取决于配方设计和胶料的工艺性能。
本文将从橡胶制品配方设计与胶料工艺性能的关系进行分析,探讨影响橡胶制品性能的因素以及如何优化配方设计和胶料工艺性能。
1. 橡胶制品配方设计橡胶制品的性能由配方设计决定,配方设计包括橡胶原料的选择、添加剂的使用和配比的确定。
橡胶原料是橡胶制品的主要组成部分,其种类和质量直接影响到橡胶制品的性能。
常用的橡胶原料包括天然橡胶、合成橡胶和再生橡胶等,它们之间的性能差异较大,需根据具体的应用场景选择合适的橡胶原料。
添加剂是为了改善橡胶制品的特定性能而添加的物质,包括增塑剂、防老剂、硫化剂、填料等,其种类和用量也会影响橡胶制品的性能。
配比的确定是指各种原料和添加剂的比例,不同的配比会导致橡胶制品性能的差异,需要在实际生产过程中进行精细调整。
2. 胶料工艺性能胶料工艺性能是指橡胶原料在橡胶制品生产过程中的加工性能,包括塑炼性能、硫化性能和成型性能等。
塑炼性能是橡胶原料在混炼机中的分散性能和流动性能,它直接关系到橡胶混炼的均匀性和硫化后的性能稳定性。
硫化性能是指橡胶原料在硫化过程中的交联程度和硫化速度,它会影响橡胶制品的硬度、强度和耐磨性等。
成型性能是指橡胶原料在成型过程中的流动性和填充性能,它直接关系到橡胶制品的成型质量和外观。
配方设计和胶料工艺性能之间存在着密切的关系,配方设计的好坏会直接影响胶料工艺性能,而胶料工艺性能的优劣也会反过来影响橡胶制品的性能。
一方面,合理的配方设计可以提高橡胶原料的塑炼性能和硫化性能,使得橡胶原料更容易加工成优质的橡胶制品。
良好的胶料工艺性能可以保证橡胶原料在生产过程中有较好的流动性和填充性能,从而保证橡胶制品的成型质量。
4. 优化配方设计和胶料工艺性能的方法为了获得优质的橡胶制品,需要不断优化配方设计和胶料工艺性能。
橡胶成型技术-配方设计

五、配方设计的内容、原则与程 序
基础配方(标准配方)仅包括最基本的组分,采用传统的配合量,以生胶和配合剂鉴定为 目的,反映胶料基本工艺性能及硫化胶基本物理机械性能的配方。
基础配方的获得:
(1)ASTM美国材料实验协会((American Society of Testing Materials )标准
一、橡胶配方设计的概念
所谓橡胶配方设计,就是根据橡胶产品的性能要求和工 艺条件合理选用原材料,确定各种原材料的用量配比关系, 使得胶料的物性、工艺性和成本三者取得最佳平衡。
橡胶配方:生胶和多种配合剂按照一定比例的一种组合。
配方设计的意义
(1)决定产品成本及质量 (2)保证加工过程的顺利进行
例:设计胶管的内层胶
五、配方设计的内容、原则与程 序
(一)配方设计的内容
1、确定硫化胶的主要性能及性能指标范围
(1)已有成品:解剖成品,测试性能 (2)无成品:借鉴同类或相似产品或计算机模拟分析提出
2、确定合适的工艺条件及指标值的范围(实验确定) 3、确定主体材料和配合剂的品种与用量 4、确定原材料的指标范围
实验研究确定,参考原材料出厂检测指标,以满足制品 性能要求为准。
ZnO
St S 促M 防DPPD 重钙
合计
单价pi /(元/kg)
18 8 6.5 14 6 1.8 16 32 0.35
——
密度ρi /(g/cm3)
0.94 1.8 1 5.57 0.85 2 1.52 1.28 2.8
——
体积 /cm3
106.38 27.78 5.00 0.90 1.18 0.75 0.66 0.78 17.86
原材料 名称
NR S 促M
橡胶制品配方设计与胶料工艺性能的关系
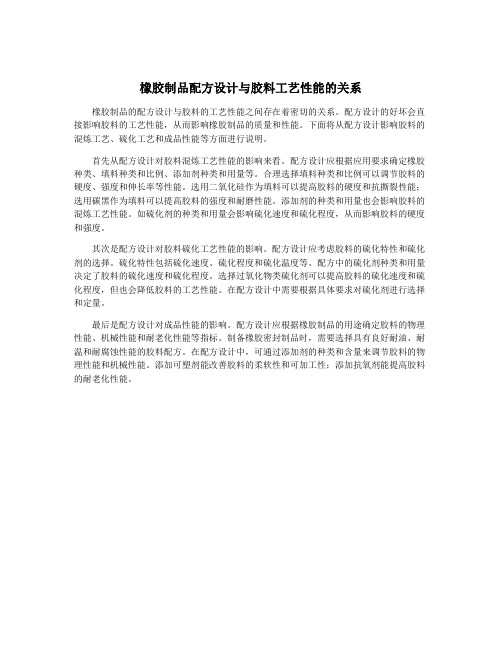
橡胶制品配方设计与胶料工艺性能的关系
橡胶制品的配方设计与胶料的工艺性能之间存在着密切的关系。
配方设计的好坏会直接影响胶料的工艺性能,从而影响橡胶制品的质量和性能。
下面将从配方设计影响胶料的混炼工艺、硫化工艺和成品性能等方面进行说明。
首先从配方设计对胶料混炼工艺性能的影响来看。
配方设计应根据应用要求确定橡胶种类、填料种类和比例、添加剂种类和用量等。
合理选择填料种类和比例可以调节胶料的硬度、强度和伸长率等性能。
选用二氧化硅作为填料可以提高胶料的硬度和抗撕裂性能;选用碳黑作为填料可以提高胶料的强度和耐磨性能。
添加剂的种类和用量也会影响胶料的混炼工艺性能。
如硫化剂的种类和用量会影响硫化速度和硫化程度,从而影响胶料的硬度和强度。
其次是配方设计对胶料硫化工艺性能的影响。
配方设计应考虑胶料的硫化特性和硫化剂的选择。
硫化特性包括硫化速度、硫化程度和硫化温度等。
配方中的硫化剂种类和用量决定了胶料的硫化速度和硫化程度。
选择过氧化物类硫化剂可以提高胶料的硫化速度和硫化程度,但也会降低胶料的工艺性能。
在配方设计中需要根据具体要求对硫化剂进行选择和定量。
最后是配方设计对成品性能的影响。
配方设计应根据橡胶制品的用途确定胶料的物理性能、机械性能和耐老化性能等指标。
制备橡胶密封制品时,需要选择具有良好耐油、耐温和耐腐蚀性能的胶料配方。
在配方设计中,可通过添加剂的种类和含量来调节胶料的物理性能和机械性能。
添加可塑剂能改善胶料的柔软性和可加工性;添加抗氧剂能提高胶料的耐老化性能。
橡胶配方设计与性能的关系
橡胶配方设计与性能的关系
概述
橡胶制品在工业和日常生活中具有广泛的应用,其性能表现与配方设计密切相关。
本文将探讨橡胶配方设计对其性能的影响。
橡胶的主要性能指标
橡胶制品的主要性能指标包括强度、弹性、耐磨性、耐腐蚀性等。
这些指标受到橡胶材料本身性质和配方设计的影响。
橡胶配方设计的基本原则
橡胶配方设计应考虑到橡胶的种类、填料、增塑剂、硬化剂等因素。
合理选择配方成分可以优化橡胶制品的性能表现。
不同配方对性能的影响
•填料种类和含量: 合适的填料种类和含量可以改善橡胶的强度和耐磨性。
•增塑剂的选择: 增塑剂的选择会影响橡胶的柔软度和弹性。
•硬化剂的配比: 硬化剂的配比直接影响橡胶的硬度和耐用性。
橡胶配方设计案例分析
以下是一个橡胶配方设计的案例分析:
•橡胶种类: 选择天然橡胶和丁腈橡胶混合使用。
•填料: 添加二氧化硅填料提高硬度和耐磨性。
•增塑剂: 选择环氧树脂作为增塑剂,提高橡胶的弹性。
•硬化剂: 使用过氧乙酸硬化剂,提高橡胶的耐用性。
总结
橡胶配方设计对橡胶制品的性能有着重要影响,合理设计配方可以改善橡胶制品的性能表现,提高其在各个领域的应用价值。
以上是橡胶配方设计与性能的关系的基本信息及探讨,希望对读者有所帮助。
橡胶的配方设计实验报告
橡胶的配方设计实验报告引言橡胶作为一种重要的材料,在工业生产和日常生活中被广泛应用。
为了满足不同应用场合对橡胶材料性能的要求,需要合理设计橡胶的配方。
本实验旨在探究橡胶的配方对橡胶性能的影响,通过变化不同配方的比例,寻找适合特定应用的橡胶配方。
材料和方法材料本实验所使用的材料有:1. 橡胶基材2. 添加剂(硫化剂、促进剂、填充剂等)3. 溶剂方法1. 橡胶基材和添加剂按照一定比例混合。
2. 将混合物放入橡胶研磨机中进行研磨,以使橡胶和添加剂均匀混合。
3. 将混合物连续过筛3次,以确保颗粒大小均匀。
4. 将混合物压制成固体板材。
5. 将板材切割成标准试样。
结果与讨论实验一:不同硫化剂用量对橡胶硬度的影响在本实验中,固定其他配方参数,仅改变硫化剂的用量,测量了制备的橡胶试样的硬度。
硫化剂用量(phr)橡胶硬度(Shore A)0 602 654 706 75从实验结果可以看出,硫化剂用量增加,试样的硬度也相应增加。
这是因为硫化剂与橡胶基材发生反应生成交联结构,提高了橡胶的硬度。
实验二:不同填充剂用量对橡胶强度的影响在本实验中,固定其他配方参数,仅改变填充剂的用量,测量了制备的橡胶试样的抗张强度。
填充剂用量(phr)橡胶抗张强度(MPa)0 1050 12100 15150 18从实验结果可以看出,填充剂用量增加,试样的抗张强度也相应增加。
这是因为填充剂可以增加橡胶的刚性,进而提高橡胶的强度。
实验三:不同促进剂用量对橡胶耐热性的影响在本实验中,固定其他配方参数,仅改变促进剂的用量,测量了制备的橡胶试样在高温下的残余压缩变形率。
促进剂用量(phr)残余压缩变形率(%)0 205 1510 1015 5从实验结果可以看出,促进剂用量增加,试样的残余压缩变形率减小。
这是因为促进剂能够提高橡胶的耐热性,减少在高温下的变形。
结论通过以上实验,我们可以得出以下结论:1. 硫化剂用量的增加会使橡胶的硬度增加。
2. 填充剂用量的增加会使橡胶的抗张强度增加。
橡胶的配方
橡胶的配方
橡胶的配方可以根据不同用途进行调整,以下是一般橡胶配方的常见成分和比例:
1. 橡胶:通常使用天然橡胶(NR)或合成橡胶(如丁苯橡胶、丁腈橡胶等)作为基础材料,比例一般在60%至80%之间。
2. 填充剂:添加填充剂可以增强橡胶的强度、硬度和耐磨性,常见的填充剂包括炭黑、白炭黑、硅灰、粉状金属氧化物等,比例一般在20%至40%之间。
3. 加工助剂:加工助剂主要用于改善橡胶的加工性能,如增塑剂、抗氧剂、硫化剂等,比例通常很小,一般在1%以下。
4. 耐热剂:耐热剂可以提高橡胶的耐高温性能,常见的耐热剂有硫酰胺类、金属氧化物等,比例一般很小,通常在2%以下。
5. 耐寒剂:耐寒剂可以提高橡胶的低温性能,常见的耐寒剂有丁苯橡胶、乙丙橡胶等,比例通常也很小,一般在5%以下。
6. 其他添加剂:根据具体需求,可以添加一些特殊功能的添加剂,如增黏剂、抗老化剂、着色剂等。
以上是一般橡胶配方的常见成分和比例,实际配方可能会根据具体情况进行调整。
需要注意的是,不同用途的橡胶材料配方会有所差异,因此在实际应用中需要根据需求进行相应的调整和优化。
橡胶配方的设计与运用
橡胶配方的设计与运用1. 设计配方应在多个方面综合考滤,1.确保指定的物性。
所谓物性大体是在如下几个方面拉伸强度、撕裂强度、定伸应力、硬度、磨耗、疲劳与疲劳破坏、回弹力、扯断伸长率等。
2.胶料加工过程中,性能优良,确保产品高产、省料。
3.成本低价格便宜。
4.所用的原材料很易采购到。
5.生产力高,加工方便,制造过程中能耗少。
6.符合环保及卫生安全要求。
一,.对各种橡胶物性要有充分地了解。
天然胶物性:A. 天然橡胶加热后慢慢软化,到130—140度则完全软化至熔融状态,温度降低至零度时渐变硬,到-70度变成脆性物质。
天然胶的回弹率在0-100度内可达50-85%升至130度时仍保持正常的使用性能。
伸长率最高可达1000%。
天然橡胶是一种结晶性橡胶,自补强性大,具有非常好的机械性能。
纯胶的拉伸强度达17—25MPA,补强硫化胶达25—35MPA,曲绕达到20万次以上,这是因为天然胶,滞后损失小,生热低的结果。
天橡胶具有较好的汽密性。
天然橡胶的老化性能差,不加老防剂的橡胶,在强烈的阳光下曝晒4—7天后即出现龟裂现象。
与一定浓度的臭氧在几秒钟内即发生裂口。
天然胶耐碱性好,但不耐强酸。
耐极性溶剂,故不耐非极性熔剂,耐油性差。
天然胶的配合,普通硫化体系硫黄用量2.0-2.4 促进剂用量1.2-0.5。
半有效硫化体系硫黄1.0-1.7促进剂2.5-1.2,有效硫化体系硫黄0.4-0.8,促进剂5.0-2.0。
普通硫黄体系多硫交联健多,而单硫健少。
多硫健能低,稳定性差,耐热、耐老化性差。
但综合物理机械性能好。
普通硫黄硫化体系,硫黄加多时易喷硫,可用不溶性硫黄替代,不容性硫黄可改善硫化胶料半成品的物理机械性能,解决高温下出现的橡胶返原因题。
可以改善拉伸、定伸应力、及弹性,胎面胶使用还可以改善磨耗。
但有一个缺点,硫速快易焦烧。
有效硫化体系不发生硫化返原现象,一般用于制造要求低蠕变率、高弹性、生热低的优良制品。
硫黄加量一般为0.6—0.7份,氧化锌为3.5-5份,载硫体一般采用TMTD 及N,N-二硫化二二吗啡啉硫黄给于体。
- 1、下载文档前请自行甄别文档内容的完整性,平台不提供额外的编辑、内容补充、找答案等附加服务。
- 2、"仅部分预览"的文档,不可在线预览部分如存在完整性等问题,可反馈申请退款(可完整预览的文档不适用该条件!)。
- 3、如文档侵犯您的权益,请联系客服反馈,我们会尽快为您处理(人工客服工作时间:9:00-18:30)。
活性剂
原理:指加入胶料后能增加促进剂活性, 减少促进剂用量,缩短 硫化时间的物质.白烟配方中,是针对白烟表面高活性 的烷基与ZnO或促进剂之间反应。 功用: 1.避免锌氧粉与促进剂被白烟吸附而影响硫化速度; 2.增加PH值:因白烟PH值约在5.8—7.3之间,带微酸性; 3.活化白烟表面,增加白烟与橡胶键结来改善物性; 活性剂的种类: 依其化学组成不同区分为: 无机活性剂: 金属氧化物,金属碳酸盐,如锌氧粉,碳酸锌,氧化 镁等; 有机活性剂: 醇类---DEG(乙二醇),PEG(聚乙二醇),尿素衍生 物,其他化合产品等;
增塑剂(软化剂)
结构与作用 由于天然橡胶、丁苯橡胶、顺丁橡胶、异戊橡胶、 丁基橡胶和三元橡胶的分子量很大,多为无官能团 的无定型结构,且具有弹性,为了在加工时使这些 非极性分子能够相对移动产生变形,传统上是在混 炼时添加一定量的无官能团结构的脂肪烃、环烷 烃、芳香烃油品增塑剂和软化剂。对于极性橡胶, 必须剂
焦烧现象
胶料在贮存和加工过程中因受热的作用会发生早期硫化(交联)并失去流动性和再加工 的能力,这就是焦烧现象。
品类与性能 ---可以用作橡胶防焦剂的化学品有三类:
有机酸类; 亚硝基化合物类; 次磺酰胺类。
---任何防焦剂都应符合橡胶加工性能要求,即:
优良的防焦性能; 对不同促进剂和胶料选择性小; 对其他配合剂不敏感; 对胶料的硫化特性和硫化胶性能无不良影响; 贮存稳定和操作性能好; 不结块、不飞扬、易分散、不喷霜; 符合工艺安全和卫生要求。
常用胶料特性介绍
• • 丁二烯橡胶(BR):CH2=CH-CH=CH2 特性:磨耗佳,弹性好,硬度高,但是止 滑性差,延伸率差,不易加工素练。
常用胶料特性介绍
• • • 丁二烯-丙烯晴橡胶(NBR): 分子式:CH2=CH-CH-CH2 CH2=CHCN 特性:耐油胶,抗张,抗压佳,目尼值高, 不易加工,耐油性是以其中含AC量为判 断。丙烯晴值(AC)含量愈高,耐油程序愈 佳。
橡胶助剂分类
按其功能,大体上可以分2类: 顺序分类包括 1功能型助剂---硫化、防护、补强、粘合、特 殊作用助剂。 2操作型助剂---塑解剂、增容剂、增塑剂、软 化剂、均匀剂、润滑剂、分散剂、增粘剂、 隔离剂、脱模剂等。
硫化体系助剂
概述
1. 硫化体系助剂包括硫化剂、促进剂、活化剂和防焦剂。 2. 硫化剂是指能和橡胶起交联作用的物质,故又称交联剂。 3. 促进剂是指加入胶料后能缩短硫化时间和降低硫化温度的物质。 4. 活性剂是指加入胶料后能增加促进剂活性,减少促进剂用量,缩短硫 化时间的物质。 5. 硫化是橡胶分子之间发生交联反应的化学过程,交联键的类型和交联 速度取决于硫化剂用量、活性、硫化温度和时间。 6. 以硫作硫化剂同橡胶进行交联反应形成的几种典型的交联键结构:单 硫键、双硫键、多硫键、临位多硫键、C-C交联键、环硫键 7. 在选择硫化体系时,还可以利用并用技术,即凡单一用某一助剂即可 达到要求的就采用单一体系;凡单一助剂不能满足要求要求时即可采 用二种或三种助剂并用体系。并用体系的显著优点在于能产生“协同 效应”。
橡胶助剂分类
按其作用,大体上可以分6类: 顺序分类包括 1硫化助剂---硫化剂(交联剂)、促进剂、活性剂、防焦剂等。 2防护助剂---抗氧剂、抗臭氧剂、抗屈挠龟裂剂、光稳定剂、UV光吸收 剂、有害金属抑制剂、物理防老剂、防白蚁剂、防霉剂等。 3补强助剂---炭黑、白炭黑、金属氧化物、无机盐、树脂等。 4粘合助剂---间甲白体系、钴盐体系粘合剂和交联剂。 5操作助剂---塑解剂、增容剂、增塑剂、软化剂、均匀剂、润滑剂、分散 剂、增粘剂、隔离剂、脱模剂等。 6特殊助剂---着色剂、发泡剂、消泡剂、增稠剂、膏化剂、湿润剂、乳化 剂、稳定剂、凝固剂、热敏剂、抗蹼剂、防腐剂、保护剂、阻燃剂、 抗静电剂、芳香剂等。
分散剂和均匀剂
• 分散剂的功能
解决胶料中粉料的分散,这主要是通过高分子脂肪 酸类分散剂润湿粉料粒子或弹性体的表面,使不同 性质和不同品类的粉料粒子之间或粉料粒子与弹性 体之间减小相对移动的阻力,达到粉料粒子均匀分 散到胶料中的目的。
•
均匀剂的主要功能
解决不同极性聚合物的共混,即解决不同极性的橡 胶之间或类橡胶或其他聚合物之间的分散。
常用胶料特性介绍
风胶(NR) 1. 取橡胶树汁液,添加些许氨和老防剂使之 凝结分块而成,愈上层杂质愈少,风胶品 质愈佳,颜色愈浅,相反,愈下层品质愈 差。 2. 分子式: 3. 特性:
常用胶料特性介绍
异戊二烯橡胶(IR): (C5H8)
常用胶料特性介绍
• 丁二烯-苯乙烯橡胶(SBR):CH2=CH2 CH2=CH-CH=CH2
A.主胶料彼此相容性问题: ---有的彼此相容,成为均相(homogeneous phase); ---有的不相容,只能机械混合. B. B.添加剂在胶料中亲和性问题: ---白烟,油,促进剂,老防剂等,在各种原料胶中之容纳量或 称亲和性问题; ---例如NR与BR掺和时,白烟与油在BR中容入较多,在NR 中较少. C.加硫速度问题: ---例如NR,EPDM掺和,NR加硫快EPDM极慢,促进剂都 被NR吃去,EPDM还不能加硫.
物理因素:热、光、机械应力、超声波、高能辐射等. 化学因素:氧、臭氧、变价金属离子,各种化学介质如水、 酸、碱、盐及微生物的作用.
防老剂
防老剂:能防止(严格地说是能延缓)橡胶老化的物质.因为橡胶老化本质是 橡胶氧化变质和臭氧化变质,所以橡胶的防老剂又称橡胶抗氧剂或 抗臭氧剂. 老化机理:橡胶的氧化过程属自由基链反应,它不仅使橡胶分子链断裂,也 能引起链交联,前者使分子量下降,表现为橡胶软化;后者使分子量 上升,表现为橡胶发硬. 分类: 按化学结构分为: 胺类, 酚类, 杂环类, 亚磷酸酯类及其他类 按外观分为: 污染型(如胺类), 非污染型(如酚类) 按防护效应分为: 抗氧化, 抗臭氧, 抗有害金属, 抗紫外线等 举例: SP, WB212,BHT等,有时老防剂在配方中共用,有的有互相激励 之效果,活性较强,与活性较低之老防剂共用,老防剂原料最贵, 加多了成本相对提高。
橡胶配方设计及各功用
代文明
原料橡胶
1. 主胶料在一般配方通常有二种以上的胶料互相掺 和,各取各种胶料的特 性,互相搭配而成,所以主胶料的选用与物性有很 大关系。 2. 掺和: (1)目的:使用单一主胶料无法达到的,掺和可以达 到:
A.物性之调和。 B.加工性之调和。 C.降低成本。
原料橡胶
(3)原料橡胶不是都可以掺和,掺和时有下列问题:
促进剂(触媒)
原理: 指加入胶料后能缩短硫化时间和降低硫 化温度的物质。 功用: 改变硫化速率及硫化时间,有时促进剂 可以共用,使用上称一次促进剂,如LM,DM, 及二次促进剂,如TS.
架桥剂
功用: 使橡胶由杂乱无序的分子结构,变成组 织严密完整的分子架构,即由原来可塑性 弹性体变成热固性弹性体. 种类: 硫磺,过氧化物,金属加硫(ZnO, MgO), 紫外线加硫等. 硫磺: 以硫作硫化剂同橡胶进行交联反应形成 的几种典型的交联键结构:单硫键,双硫键, 多硫键,临位多硫键,C-C交联键,环硫键;
偶合剂
• A-189, S-69, KBM803。
防护体系助剂----概述 防护体系助剂 概述
• 老化: 橡胶在加工、贮存和使用过程中,由于受内 外因素的综合影响,而逐渐失去其原有的优良性质, 这种现象叫橡胶的老化. • 常见的老化: 表面外观变软、发黏、发硬、龟裂、 发脆等,从而体现为强度下降、弹性消失、绝缘性 下降,其他的物理和化学性能也发生变化. , . • 影响老化的因素: