橡胶配方设计第三章
第三章 橡塑制品厂典型车间工艺设计与布置

(十一)胶料的运输和控制
(四)塑炼
橡 塑 制 品 厂 工 艺 设 计
B、密炼机塑炼方法: a、一段塑炼法:塑炼周期短,占地面积小,且操 作简便。但塑炼胶的可塑性较低,适用于可塑性 要求不太高的塑炼胶(如轮胎胎面塑炼胶)的制备。 b、分段塑炼法:用于制备较高可塑性塑炼胶,由 于密炼机塑炼的塑炼胶热可塑性较大,所以实际 生产中制备较高可塑性的塑炼胶(如轮胎帘布胶) 时,常用分段塑炼法塑炼。 c、化学塑解剂塑炼法:提高塑炼效率,缩短塑炼 时间降低塑炼胶弹性复原和收缩 。
(六)压延
橡 塑 制 品 厂 工 艺 设 计
①胶片压延:压片、压型、贴合。 ②纺织物挂胶:贴胶、擦胶 贴胶分为贴胶和压力贴胶。
(七)压出
橡 塑 制 品 厂 工 艺 设 计
①热喂料压出法 是目前国内采用的主要压出方法。其设 备结构简单,动力消耗小,胶料均匀一致; 半成品表面光滑,规格尺寸稳定。但由于 胶料需要热炼,增加了压出作业工序,使 总体的动力消耗大,占地面积大。 热喂料压出法可分为有芯压出和无芯 压出,按半成品组合形式,可分为整体压 出和分层压出。
(二)切胶
橡 塑 制 品 厂 工 艺 设 计
切胶目的 (1)便于称量 (2)便于投料 (3)保护设备 ①单刀油压立式切胶机:适用于中小规 模工业生产。 ②多刀卧式切胶机前者:适用于大规模 工业生产。
(二)切胶
橡 塑 制 品 厂 工 艺 设 计
“先烘胶后切胶”及“先切胶后烘胶”两种 工艺特点对比: “先烘胶后切胶”特点:切胶容易、速度快、 动力消耗较少、切胶机易损伤程度小,但 烘胶胶温的均匀性较差,烘胶时间较长。 “先切胶后烘胶”特点:烘胶胶温的均匀性 好,烘胶时间短,但动力消耗较大,切胶 机易损伤程度较大。
橡胶配方设计整理
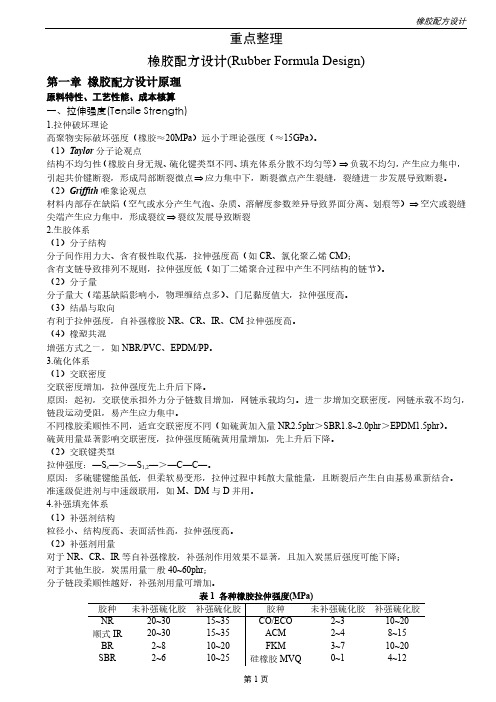
重点整理橡胶配方设计(Rubber Formula Design)第一章橡胶配方设计原理原料特性、工艺性能、成本核算一、拉伸强度(Tensile Strength)1.拉伸破坏理论高聚物实际破坏强度(橡胶≈20MPa)远小于理论强度(≈15GPa)。
(1)Taylor分子论观点结构不均匀性(橡胶自身无规、硫化键类型不同、填充体系分散不均匀等)⇒负载不均匀,产生应力集中,引起共价键断裂,形成局部断裂微点⇒应力集中下,断裂微点产生裂缝,裂缝进一步发展导致断裂。
(2)Griffith唯象论观点材料内部存在缺陷(空气或水分产生气泡、杂质、溶解度参数差异导致界面分离、划痕等)⇒空穴或裂缝尖端产生应力集中,形成裂纹⇒裂纹发展导致断裂2.生胶体系(1)分子结构分子间作用力大、含有极性取代基,拉伸强度高(如CR、氯化聚乙烯CM);含有支链导致排列不规则,拉伸强度低(如丁二烯聚合过程中产生不同结构的链节)。
(2)分子量分子量大(端基缺陷影响小,物理缠结点多)、门尼黏度值大,拉伸强度高。
(3)结晶与取向有利于拉伸强度,自补强橡胶NR、CR、IR、CM拉伸强度高。
(4)橡塑共混增强方式之一,如NBR/PVC、EPDM/PP。
3.硫化体系(1)交联密度交联密度增加,拉伸强度先上升后下降。
原因:起初,交联使承担外力分子链数目增加,网链承载均匀。
进一步增加交联密度,网链承载不均匀,链段运动受阻,易产生应力集中。
不同橡胶柔顺性不同,适宜交联密度不同(如硫黄加入量NR2.5phr>SBR1.8~2.0phr>EPDM1.5phr)。
硫黄用量显著影响交联密度,拉伸强度随硫黄用量增加,先上升后下降。
(2)交联键类型拉伸强度:—S x—>—S1,2—>—C—C—。
原因:多硫键键能虽低,但柔软易变形,拉伸过程中耗散大量能量,且断裂后产生自由基易重新结合。
准速级促进剂与中速级联用,如M、DM与D并用。
4.补强填充体系(1)补强剂结构粒径小、结构度高、表面活性高,拉伸强度高。
橡胶工业手册第三册配方与基本工艺

上篇配方设计第一章配方设计第一节概述天然橡胶和合成橡胶的纯胶性能都比较差,无法满足制品的使用要求,加入多种配合剂后才能获得改善。
橡胶、配合剂及其配比的方案,即为橡胶配方。
根据制品各种性能要求,制定橡胶配方,通过试验、调整和验证,最后确定胶料的各种组分及其配比的过程,即称谓橡胶配方设计。
橡胶性能配方,主要研究配方组分与硫化胶及混炼胶性能之间的关系,探求组分对橡胶各种性能的影响和贡献。
橡胶制品配方则主要研究硫化橡胶物理机械性能和化学性能与橡胶只怕你实际使用性能之间的关系,探求硫化橡胶性能对制品使用性能的影响和贡献。
这两类配方所研究的对象和内容虽然不同,但又互相联系,不可分割,由此形成橡胶配方设计体系。
一、配方设计的变迁和发展一、配方组成的多样化现代配合组分可分为五个体系:1.主体材料:生胶、再生胶2.硫化体系:硫化机、促进剂、活性剂、防焦剂。
3.操作体系:增塑剂(化学增塑剂、物理增塑剂)。
4.性能体系:补强剂、防老剂、着色剂、发泡剂、芳香剂、增硬剂。
5.成本体系:填充剂、增容剂。
一个具有实际意义的配方通常含有不同体系二、配合剂品种的专用化适合氯丁橡胶的硫脲类促进剂不适合于其他类型的橡胶。
适合天然橡胶的植物系物理增塑剂并不适合合成橡胶。
三、配合效果的提高四、配方设计过程的简化科学的数理方法用于配方设计:等高线法、实验设计法、三角坐标法及电子计算机法等。
用计算机进行配方试验的数据处理、优选配方,可以通过少量试验获得大量有用的信息,使配方设计发生了根本性变化。
二、配方设计的基本要求和配方分类为获取最佳的共和平衡性能,三个目的1.改善橡胶使用性能。
2.改进橡胶的工艺性能。
配以操作助剂。
3.不影响或少影响性能的前提下,配入填充材料,降低成本。
橡胶配方按其作用分为:试验(或检验)配方、性能配方和制品配方。
试验(或检验)配方。
通用橡胶基础配方:三、橡胶配合中出现的反常现象1.实验室得到的配方,在生产中不一定有满意结果。
NBR橡胶的配方设计精选文档

N B R橡胶的配方设计精选文档TTMS system office room 【TTMS16H-TTMS2A-TTMS8Q8-NBR密封件配方设计一、常用橡胶用途及性能:1051 丙烯晴含量 41% ML75 SG 稍污染型1052 丙烯晴含量 33% ML50 SG 非污染型1053 丙烯晴含量 29% ML60 SG 非污染型1052M30丙烯晴含量33% ML30 SG 非污染型DN223丙烯晴含量 33%ML 35 SG非污染型丙烯晴含量 50% ML75 SG非污染型1965 丙烯晴含量 19% ML65 SG 非污染型DN401丙烯晴含量 18% ML78 SG 非污染型1043丙烯晴含量 29%ML 80 SG稍污染型N230SL丙烯晴含量 35% ML42 SG 非污染型N260S丙烯晴含量 15% ML62 SG 非污染型1052M40丙烯晴含量 33% ML40 SG 非污染型特性:1、ACN↑耐油性好,非极性或弱极性矿物油,植物油,液体燃料和有较高的稳定性。
2、耐热性优于NR SBR CR 可在120℃下长期使用。
3、属半导体材半料。
4、耐油与压缩永久变形平衡,耐油性与电性能平衡。
5、丙烯晴含量对NBR分类:ACN% 43%以上极高ACN%NBR36-42%以上高31-35% 中高25-30 中24%以下低总结:ACN%越高,耐油性愈好耐热性改善,但TG差,ACN%越低,低温性好,但耐油偏差。
且ML会升高,压缩永久变形好。
一般ACN%在29%可过F17.过F19 须用1965或DN401生胶。
二、共聚物组成(ACN含量)对NBR的影响.项目ACN含量特点密度低→→→高大加工性(流动性)低→→→高良好硫化速度低→→→高快定伸应力、拉伸强度低→→→高大硬度低→→→高大耐磨性低→→→高良好永久变形低→→→高大耐油性低→→→高良好耐化学药品性低→→→高良好耐热性低→→→高良好和极性聚合物的相容低→→→高大弹性低→→→高小耐寒性低→→→高差透气性低→→→高差和增塑剂操作油的相容低→→→高差三、硫化体系一般NBR配方采用半有效硫化体系,例如:TT/CZ,这种硫化体系,具有耐热性较好的效果,SUL/TS压缩歪和焦烧最优。
橡胶配方设计--02-1

硬度测定:邵尔A 7.硬度测定:邵尔A型 磨耗测定: 8.磨耗测定: 磨耗体积
0-100度 100度
)/ρ, 61Km Km, V=(m前-m后)/ρ,cm3/1.61Km,
滚筒磨耗
磨耗指数= 磨耗指数=V标/V试
阿克隆磨耗
疲劳的测试: 9.疲劳的测试: 压缩疲劳: (1)压缩疲劳:1)温升 2)变形 屈挠龟裂: (2)屈挠龟裂:裂口大小及 出现裂口的时间 拉伸疲劳: (3)拉伸疲劳:疲劳寿命计算 10. 10.压缩永久变形 )]*100 100% K=[(h0-h2)/(h0-h1)]*100% 11. 11.粘弹性 (1)摆锤式回弹仪 (2)蠕变 (3)应力松弛 动态粘弹性能(DMA) 动态模量及tgδ (DMA)、 (4)动态粘弹性能(DMA)、动态模量及tgδ
硫化橡胶的性能测试
P/bh, 1.拉伸强度 σ=P/bh,Mpa 定伸应力, 2.定伸应力,Mpa 100% 300% 100%,300%,Mpa 3.扯断伸长率 ,% є=[(L1-L0)/L0]*100% = ]*100 100% 扯断永久变形: 4.扯断永久变形: S=(L2- L0)/ L0 ,% 撕裂强度: 5.撕裂强度: P/h, Φ=P/h,KN/m 6.有效弹性和滞后损失
橡胶配方设计原理及工艺
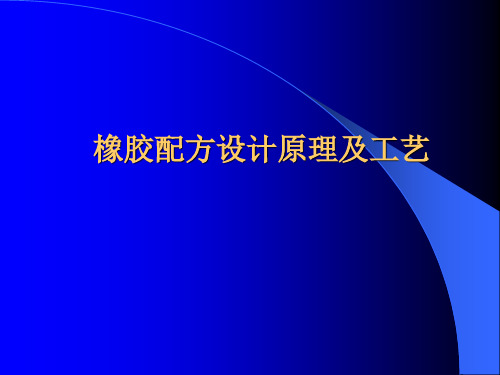
3制定基本配方和性能试验项目 制定基本配方步骤如下: 1确定生胶的品种和用量; 根据主要性能指标确定主体胶料品种;用量与含胶率有关。 2)确定硫化体系。根据生胶的类型和品种,硫化工艺及产品性能要求来确定。 3)确定补强剂品种和用量。根据胶料性能 比重及成本确定。 4)确定软化剂品种和用量。根据生胶及填料种类,胶料性能及加工条件确定。 5)确定防老剂品种和用量。根据产品使用环境的条件来确定。 6)确定其它专用配合剂的品种和用量。如着色剂,发泡剂等)
20˚C
75˚C
150˚C
偏差加大:包容胶活动性增强所致;
Ef/Eg
胶种
纯胶基本硬度
填料品种
估算硬度
NBR
44
FEF,HAF
+1/2份数
CR
44
ISAF
+1/2份数+2
NR
40
SAF
+1/2份数+4
SBR
40
SRF
+1/3份数
IIR
35
陶土
+1/4份数
碳酸钙
+1/7份数
油
-1/2份数
填料与硬度的关系
一 配方设计定义 橡胶材料是生胶与多种配合剂构成的多相体系; 橡胶制品的性能取决于橡胶分子本身;以及各种配合剂性质及它们之间的相互作用关系。 定义:根据产品的性能要求及工艺条件,合理选用原材料,制订各种原材料的用量配比关系的设计方法。 配方设计决定着产品质量、成本和加工性能。
现代橡胶配方设计

2、基本原则
(1)在不降低产品质量的情况下降低成本
(2)在保持成本不变的情况下提高产品的性能
3、一般原则
(1)满足制品的性能要求;(2)设计的配方易于加工
(3)原材料价廉易得; (4)重点设计主要性能
(5)充分考虑交互作用; (6)配方成本低,能耗低
(7)201配9/1方1/18尽可能简化
(8)符合环保与卫生要求
②体积分数配方计算:Vi%=mi/ρ i×[100/∑(mi/ ρi)]
③生产配方计算:Mi=mi×(Q/ ∑mi)
2019/11/18
含配合剂母胶的配方计算:
例如:促进剂M母胶配方
NR
100
促进剂M 20
ZnO
5
合计
125
X促M母=1/(20/125)=6.25份 母胶中: XNR=6.25×(100/125)=5份 XZnO=6.25× (5/125)=0.25份
1. 质量份数表示(mi): 以生胶分数为100份,其余配合剂相应质量份数表示。
2. 质量百分数( mi % ):= mi /∑mi ×100% 以胶料总质量为100,生胶和配合剂质量所占比例数来 表示,主要用于计算原材料质量成本和含胶率。
3. 体积百分数表示(Vi% ): = Vi /∑Vi ×100% 以胶料总体积为100,生胶和配合剂体积所占比例数来 表示,主要用于计算原材料体积成本。
配方1的炼胶成本:P炼胶1=1.2×1.2=1.44(元) 配方1硫化成本:P硫化1=(4/60)×10=0.67(元) 总成本:P总1= P胶1+ P炼胶1+ P硫化1=19.32(元) 2每019件/11制/18 品的利润:R1=P价格—P总1= 21.6-19.32=2.28(元)
橡胶配方设计
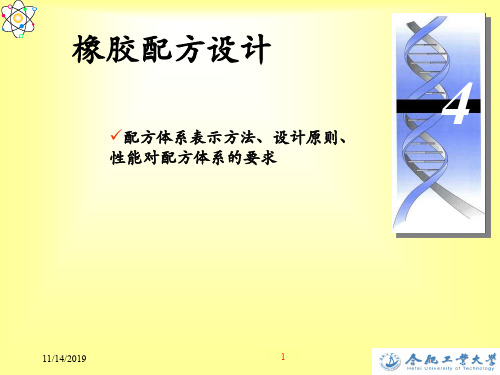
11/14/2019
20
4.2.2 配合体系与撕裂强度的关系
指将带有切口的试片撕裂时所需的最大力,其单位为N/m。 ⑴ 橡胶品种
天然橡胶、氯丁橡胶等结晶性橡胶的撕裂性较好。几种橡胶的抗 撕裂性强弱顺序是:NR>CR>SBR>NBR ⑵ 硫化体系 多硫键具有较高的撕裂强度。 ⑶ 填充体系 粒子细、活性大的炭黑、白炭黑补强时,撕裂强度明显改善;炭 黑用量一般在50~60phr时可获得最高撕裂强度。但用量过大时撕 裂强度反而下降。 ⑷ 增塑体系 适当加入增塑剂有助于撕裂强度的提高,主要是一些树脂类如古 马隆树脂、酚醛树脂等。
炼性主要取决于配合剂与橡胶之间的浸润性。 疏水性填充剂,如炭黑容易被橡胶所浸润,混炼性能较好;亲水
性填充剂,如碳酸钙、陶土、白炭黑等,不易被橡胶浸润,混炼 性能较差。可通过化学改性,或加入表面活性剂加以改进。 增塑剂与橡胶的相容性一般较好,易于分散。
11/14/2019
31
3 配合体系对包辊性能的影响 胶料的包辊性能主要取决于生胶的强度和粘着性能。 影响生胶强度的因素包括生胶的分子量及其拉伸结晶性能。天
所谓配方设计就是如何确定这种比例关系,是橡胶制品生产 过程中的关键环节。
11/14/2019
2
4. 1.1 橡胶配方设计的原则
橡胶配方设计的任务是力求使橡胶制品在性能、成本和工艺可行 性三个方面取得最佳的综合平衡。通常,要遵循以下几条原则:
⑴ 充分了解制品的性能要求、使用条件;半成品的性能一般应 高于成品指标的15%。
然橡胶具有最好的包辊性能,乳聚合成橡胶次之,溶聚的,特别 是分子量分布较宽的橡胶包辊性能较差。改善的途径有以下几种 ⑴ 通过加入活性、结构性高的填充剂,如炭黑、白炭黑等增加生 胶的强度,进而提高胶料地包辊性能。 ⑵ 加入增粘性增塑剂 如高芳烃操作油、松焦油、古马隆树脂、 酚醛树脂等。 ⑶ 与少量天然橡胶并用。
- 1、下载文档前请自行甄别文档内容的完整性,平台不提供额外的编辑、内容补充、找答案等附加服务。
- 2、"仅部分预览"的文档,不可在线预览部分如存在完整性等问题,可反馈申请退款(可完整预览的文档不适用该条件!)。
- 3、如文档侵犯您的权益,请联系客服反馈,我们会尽快为您处理(人工客服工作时间:9:00-18:30)。
10
100/0
SBR/BR
9
75/25
50/50
8
25/75
lgE/Pa
7
0/100
6
-100
-80
-60
-40
-20
0
20
温度/℃
SBR/BR并用胶的模量与温度的关系
二、硫化体系 (1)C-SX-C>C-S-C>C-C (2)S用量增大,耐寒性差 采用高硫低促,对于结晶橡胶可提高交联密度; 对于非结晶橡胶可降低交联密度。
二.硫化体系:-C-SX-C <C-S2-C <C-S-C<C-C EPDM采用DCP交联,热撕裂差,有时少量配用“S” CR采用ZnO MgO NBR采用镉镁硫化体系或过氧化物,前者适宜于高 温高压密封,后者高压下易压碎 IIR采用树脂硫化或醌肟硫化 通用胶以低硫高促或含硫载体促进剂
三.填充剂 白炭黑 ,ZnO,MgO,Al2O3和硅酸盐 一般无机填料比炭黑类补强胶料的耐热性好。
四.软化剂 选用具有热稳定性和不挥发的品种 (高粘度的石蜡油改善耐热性) 硫化时能起聚合作用的软化剂 (如固马隆、PIB、齐聚酯)
五.防护体系 胶种与所对应的耐热防老剂(1)挥发性小的;
(2)分子量大;(3) 能与橡胶进行反应结合。 通常4010NA,4020,4010,NBC,RD,D,
A
耐热输送带覆盖胶
-4
Peak: 454.6 °C
Residual Mass: 32.86 % (699.3 °C)
-5
200
300
400
500
600
Temperature /°C
NBR
一.橡胶的选择 橡胶的软化温度:极性-Cl -F -CN -COOC4H9 橡胶的热稳定性:提高键能如Si-O 和C-O 橡胶的化学稳定性:减少弱键“=” ,HNBR
Sulfur CR
50
Long Service Life
0 0
50
100
150
200
Life Expected (1000Km)期望寿命(1000公里 )
耐热性:橡胶在长时间热氧化作用下保持 原有物性的能力
1. 合成新的弹性体,使它们的化学结构具 有高的耐热性
2. 选择适当的硫化体系 3. 填加能提高耐温等级的新型填料 4. 新型防老剂、稳定剂 5. 软化剂选用粘度大,高温减量少为宜
• 热氧老化后性能变化率 • 热失重
FKM
TG /% 100 90 80 70 60 50 40
100
MVQ
Mass Change: -5.08 % Peak: 239.4 °C
Peak: 342.2 °C
Mass Change: -13.22 %
DTG /(%/min) 0 -1 -2
-3
Mass Change: -48.84 %
三、合理的软化增塑体系提高耐寒性 软化剂降低分子间作用力,降低形变时所产生
的应力,显著降低脆性温度,提高耐寒性能。 癸二酸酯和邻苯二甲酸酯 二丁酯>二辛酯 凝固点低的软化剂降低Tg
四、填料少用或不用,选用软质或球形填料
各种增塑剂对NBR耐寒性的影响
增塑剂
空白 邻苯二甲酸二辛酯 邻苯二甲酸二丁酯 邻苯二甲酸丁基·月桂
酯 邻苯二甲酸丁基·苄酯
磷酸三苯甲酯
脆性温度Tb /℃
增塑剂
脆性温度Tb /℃
-29.5
磷酸三苯酯
-30-37.5己二酸辛酯-43-37.5
壬二酸二辛酯
-44.7
-42
癸二酸二辛酯
-49
-37
癸二酸丙二醇酯
-36.5
-29.5
液体古马隆
-27.5
• 橡胶的耐寒系数采用室温(25℃)下的形变值 ε25与指定温度下的形变值εi之比来表示,耐寒 系数K为: K = εi / ε25
第三章 特种橡胶及功能性材料
• 随着高分子科学的发展以及工业需求量的增加,特 种橡胶的应用越来越广泛,赋予橡胶制品特殊的性 能,满足特定使用环境的要求。
• 功能橡胶:阻燃、导电、磁性、吸水膨胀等
Ch1、耐热橡胶
Temperature in the Engine Compartment over last 25 Years 近25年汽车发动机舱温度变化
SBR1500 100
ZnO 10
SA
2
防D 1.5
HAF 30
SRF 50
10#机油 8
古马隆树脂 6
松焦油 5
促TMTM 1
促DM 1.5
促T.T
2
S
0.5
耐热胶管
EP35 100
ZnO 8
SA 2
FEF 120
环烷油 50
芳烃油 30
促M 1
促T.T 1
S
1
Ch2 耐寒橡胶
A —玻璃态;B —过渡区;C —高弹态;D —过渡区;E —粘流态; Tg —玻璃化温度; Tb —脆性温度; Tf —粘流温度
• 显然,当温度接近Tg 时,与室温下形变值相比, 接近Tg 的形变值很小,K值接近于零。加入增 塑剂可使高弹态的范围向低温方向扩展。
Ch3 耐油橡胶
油类介质(燃油、矿物油、润滑油)中使用,油 渗透到橡胶中使其发生溶胀
耐油性:抗油类渗透作用的能力 溶解度参数相差越大,橡胶难溶胀
苯胺点表示油中含芳香族成分与脂肪族成分 比例的尺度,或与等量的苯胺能够一起溶解的最 低温度。
苯胺点高的油:橡胶难溶胀 苯胺点低的油:橡胶易溶胀
(一)橡胶选择 根据制品的使用条件和其他性能指标加以调整 (1)NBR中-CN含量高低、HNBR、NBR/树脂酚 醛、
NBR/三元尼龙、NBR/PVC 高温下选用-CN含量高 30~40% 低温下选用-CN含量低 15~30% (2)ACM : 150˚C~180˚C 不耐水、弹性差 (3)FKM(氟橡胶):200˚C~250˚C且耐油性好, 弹性差,低温性差 (4)ECO CO(氯醇、氯醚橡胶)-50˚C ~150˚C (4)交联聚乙烯醇:耐石油溶剂优良,耐水性差 (5)FMVQ(氟硅橡胶):高低温性好、成本高。 橡胶的耐油性取决于橡胶及油的极性
Peak Permanent Temperature
Max Service Temperature oC
High Service Temperature
Target of Timing Belt Performance 同步带寿命的目标
200
Current
150
Target
HNBR
100
HNBR/NBR peroxide
随着温度下降,链段活动能力减弱,松弛过程减慢, 硬度、模量和分子内摩擦增大,弹性显著降低。 Tg是橡胶完全丧失弹性时的特定起始温度; Tb 是橡胶在外来冲击力下出现断裂时的最高温度。 一、橡胶选择: 分子链的柔性 BR VHQ NR SBR IIR EPDM
NBR (-CN含量大小选择) CR ACM FPM (1)主链含双键或醚键:BR NR CO Q