交联电缆绝缘老化强度变化率超标原因及改善
10kV交联电缆终端故障原因分析及制作要点
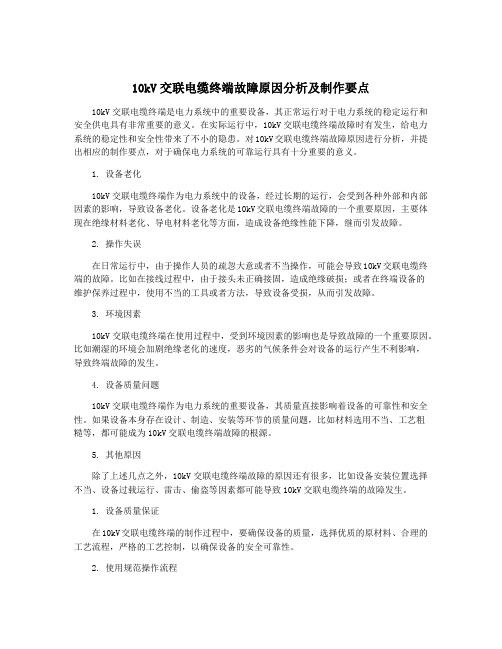
10kV交联电缆终端故障原因分析及制作要点10kV交联电缆终端是电力系统中的重要设备,其正常运行对于电力系统的稳定运行和安全供电具有非常重要的意义。
在实际运行中,10kV交联电缆终端故障时有发生,给电力系统的稳定性和安全性带来了不小的隐患。
对10kV交联电缆终端故障原因进行分析,并提出相应的制作要点,对于确保电力系统的可靠运行具有十分重要的意义。
1. 设备老化10kV交联电缆终端作为电力系统中的设备,经过长期的运行,会受到各种外部和内部因素的影响,导致设备老化。
设备老化是10kV交联电缆终端故障的一个重要原因,主要体现在绝缘材料老化、导电材料老化等方面,造成设备绝缘性能下降,继而引发故障。
2. 操作失误在日常运行中,由于操作人员的疏忽大意或者不当操作,可能会导致10kV交联电缆终端的故障。
比如在接线过程中,由于接头未正确接固,造成绝缘破损;或者在终端设备的维护保养过程中,使用不当的工具或者方法,导致设备受损,从而引发故障。
3. 环境因素10kV交联电缆终端在使用过程中,受到环境因素的影响也是导致故障的一个重要原因。
比如潮湿的环境会加剧绝缘老化的速度,恶劣的气候条件会对设备的运行产生不利影响,导致终端故障的发生。
4. 设备质量问题10kV交联电缆终端作为电力系统的重要设备,其质量直接影响着设备的可靠性和安全性。
如果设备本身存在设计、制造、安装等环节的质量问题,比如材料选用不当、工艺粗糙等,都可能成为10kV交联电缆终端故障的根源。
5. 其他原因除了上述几点之外,10kV交联电缆终端故障的原因还有很多,比如设备安装位置选择不当、设备过载运行、雷击、偷盗等因素都可能导致10kV交联电缆终端的故障发生。
1. 设备质量保证在10kV交联电缆终端的制作过程中,要确保设备的质量,选择优质的原材料、合理的工艺流程,严格的工艺控制,以确保设备的安全可靠性。
2. 使用规范操作流程对于10kV交联电缆终端的制作操作,必须要按照规范的操作流程进行,严格执行操作规程,避免因操作失误而导致的故障发生。
交联聚乙烯(XLPE)电缆绝缘老化问题探析

上接第 150 页
算出的时间间隔△t 就是相应桥臂上的脉 1j
由于局部放电侵蚀绝缘,以致发生老 化形态,而使绝缘性降低,导致绝缘击穿。
2.3 电树枝 主要是由于绝缘内部放电产生的细微 开裂,形成细小的通道,其通道内空,管壁 上有放电产生的碳粒痕迹。通道分支少而 清晰,呈树枝状。 电树枝按产生的机理分为以下几种类 型: (1)由于机械应力的破坏使 XLPE 绝缘 产生应变造成气隙和裂纹,引发电树枝放 电。机械应力一方面是因为电缆生产、敷设 运行中不可避免地弯曲、拉伸等外力产生 应力,另一方面是由于电缆在运行中电动 力对绝缘产生的应力。 (2)气隙放电造成电树枝的发展。现 代的生产工艺尽管可以消除交联电缆生产 线中某些宏观的气隙,但仍有 1~10 μ m 或 少量的 20~30 μ m 的气隙形成的微观多孔 结构。多孔结构中的放电形式主要以电晕 放电为主。通道中的放电所产生的气体压 力增加,导致了树枝的扩展和形状的变化。 (3)场致发射效应导致树枝性放电。在 高电场作用下,电极发射的电子由于隧道 效应注入绝缘介质,电子在注入过程中获 得足够的动能,使电子不断地与介质碰撞 引起介质破坏,导致树枝放电。 (4)缺陷。缺陷主要是导体屏蔽上的 节疤和绝缘屏蔽中的毛刺以及绝缘内的杂 质和空穴。这些缺陷使绝缘内的电场集中, 局部场强提高。引起场致发射,导致树枝性
冲信号0或1状态在时间轴上的宽度。其中:
,α =2; < 0,α =1;v -u > 0, jo j
β =2;vjo-uj < 0,β =1。启动各桥臂△
10kV交联聚乙烯电缆绝缘劣化及修正

10kV 交联聚乙烯电缆绝缘劣化及修正供电工程中,10kV 交联聚乙烯(XLPE)电缆的应用范围广,且敷设量大。
除电力系统和工矿企业的输配电网使用外,还涉及许多大型建筑物、高层建筑及工业、生活园区的供电工程。
由于10kV 供电电源有中性点直接接地及不接地2种系统;10kV XLPE 电缆又有6.0/10kV 、8.7/10kV 、8.7/15kV 3种绝缘电压的等级供设计人员选用,故在10kV XLPE 电缆的绝缘水平设计时应严加区分。
我国应用XLPE 电缆的初期,一些设计人员仅依据电缆缆芯间的额定电压不得低于使用回路工作电压的技术要求进行绝缘水平设计。
忽略了XLPE 电缆对缆芯与绝缘屏蔽层或护套间的额定电压U0(相对地电压)的特殊规定,因而所设计的XLPE 电缆相对地电压U0等于系统额定相电压值,造成电缆绝缘裕度不足。
电缆交付使用后,无法承受系统出现的过电压,屡屡发生电缆绝缘被击穿的事故。
笔者正是在这一情况下,对一批在系统额定相电压值条件下运行的6.0/10kV XLPE 电缆进行了长期的追踪观察。
1.故障统计与分析某工程供电系统于1991年2月并网投运,10kV 电源为中性点经消弧线圈接地系统,所用电缆为国内早期批量生产的E-T 型结构6.0/10kV XLPE 电缆,长约30km 。
该电缆长期处于额定相电压值条件下做无绝缘裕度运行。
14年来,这批电缆承受系统单相接地故障期间非故障相电压升高80余次;接地故障持续时间累计超过7h 15min 。
其中,因故障线路带有重要负荷而不能及时撤除运行,致使接地持续时间长达2h 15min 。
电缆各种类型的损坏累计达46次,其中电缆本体绝缘被击穿30次,占故障总数的65.22%。
在长年的追踪观察中,发现这批6.0/10kV XLPE 电缆因水树现象被击穿、在主绝缘层形成孔洞。
同时还发现了早期生产的XLPE 电缆因设备、工艺条件所限,致使电缆主绝缘层出现薄厚不均和同心度差等问题。
35KV及以下电力交联电缆故障的原因及对策

35KV及以下电力交联电缆故障的原因及对策摘要:电缆是工厂企业供电必不可少的材料,应用十分广泛,一旦电缆发生故障,不仅影响企业的正常生产,而且可能引起一连串的恶性连锁反应,如配套电器设备的烧毁,火灾事故的发生,其损失不可估量。
因此如何预防电缆故障,是我们工程技术人员重要的任务。
本文以35KV及以下电力交联电缆故障进行了分析。
关键词:35KV 交联电缆故障对策电缆是工厂企业供电必不可少的材料,应用十分广泛,一旦电缆发生故障,不仅影响企业的正常生产,而且可能引起一连串的恶性连锁反应,如配套电器设备的烧毁,火灾事故的发生,其损失不可估量。
因此如何预防电缆故障,是我们工程技术人员重要的任务。
本文以35KV及以下电力交联电缆故障进行分析。
首先要搞清楚电缆故障可能出现在哪里,为什么会出现故障,并提出解决办法、预防措施,把可能出现的事故消灭在萌芽状态,保证电缆安全正常运行,为企业的正常生产打下坚实的基础。
一、一般电缆故障多发点及原因(一)一般电缆故障多发点一根电缆敷设安装完毕,一旦送电就形成一个强大的电场,电流、电压随时都在寻找薄弱环节突破。
总结以往的工作经验,一般电缆最容易出故障多在电缆的中间连接头和终端头及其附近,特别是中间连接头的制作要求更高,故存在事故隐患的可能性更大。
另外,如电缆安装质量不高,电缆受到外部机械创伤或长期过负荷运行同样也会造成电缆故障。
(二)电缆故障产生的原因1. 由电缆的中间连接头、终端头制作质量不高而造成的。
制作过程中,如果半导体层爬电距离处理不够、制作时热收缩造成内部含有杂质、汗液及气隙等,在电缆投入运行后,都将使其中的杂质在强大的电场作用下发生游离,产生树枝放电现象。
另外,在制作过程中,如果导线压接质量不好,使接头接触电阻过大而发热,或热收缩过度等造成了绝缘老化,从而使绝缘层老化击穿,导致电缆接地短路或相间短路,使电缆产生“放炮”现象,同时伤及附近其他的电缆。
2. 电缆终端或中间连接头的金属屏蔽接地不完善造成的。
中压交联电缆绝缘线芯质量控制对策
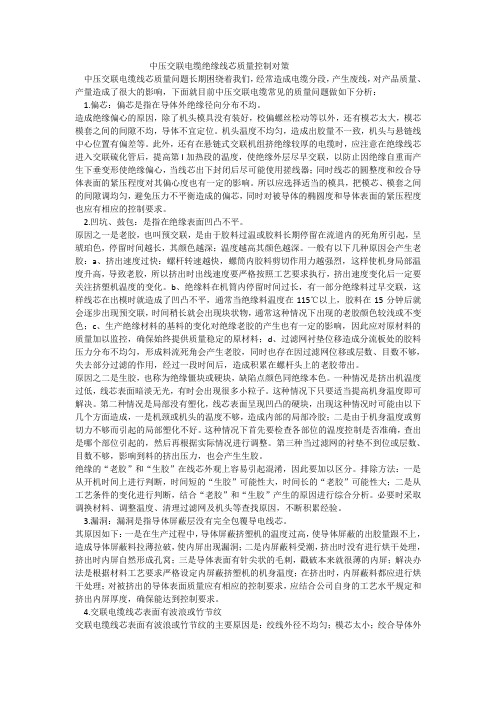
中压交联电缆绝缘线芯质量控制对策中压交联电缆线芯质量问题长期困绕着我们,经常造成电缆分段,产生废线,对产品质量、产量造成了很大的影响,下面就目前中压交联电缆常见的质量问题做如下分析:1.偏芯:偏芯是指在导体外绝缘径向分布不均。
造成绝缘偏心的原因,除了机头模具没有装好,校偏螺丝松动等以外,还有模芯太大,模芯模套之间的间隙不均,导体不宜定位。
机头温度不均匀,造成出胶量不一致,机头与悬链线中心位置有偏差等。
此外,还有在悬链式交联机组挤绝缘较厚的电缆时,应注意在绝缘线芯进入交联硫化管后,提高第I加热段的温度,使绝缘外层尽早交联,以防止因绝缘自重而产生下垂变形使绝缘偏心,当线芯出下封闭后尽可能使用搓线器;同时线芯的圆整度和绞合导体表面的紧压程度对其偏心度也有一定的影响。
所以应选择适当的模具,把模芯、模套之间的间隙调均匀,避免压力不平衡造成的偏芯,同时对被导体的椭圆度和导体表面的紧压程度也应有相应的控制要求。
2.凹坑、鼓包:是指在绝缘表面凹凸不平。
原因之一是老胶,也叫预交联,是由于胶料过温或胶料长期停留在流道内的死角所引起,呈琥珀色,停留时间越长,其颜色越深;温度越高其颜色越深。
一般有以下几种原因会产生老胶:a、挤出速度过快:螺杆转速越快,螺筒内胶料剪切作用力越强烈,这样使机身局部温度升高,导致老胶,所以挤出时出线速度要严格按照工艺要求执行,挤出速度变化后一定要关注挤塑机温度的变化。
b、绝缘料在机筒内停留时间过长,有一部分绝缘料过早交联,这样线芯在出模时就造成了凹凸不平,通常当绝缘料温度在115℃以上,胶料在15分钟后就会逐步出现预交联,时间稍长就会出现块状物,通常这种情况下出现的老胶颜色较浅或不变色;c、生产绝缘材料的基料的变化对绝缘老胶的产生也有一定的影响,因此应对原材料的质量加以监控,确保始终提供质量稳定的原材料;d、过滤网衬垫位移造成分流板处的胶料压力分布不均匀,形成料流死角会产生老胶,同时也存在因过滤网位移或层数、目数不够,失去部分过滤的作用,经过一段时间后,造成积累在螺杆头上的老胶带出。
10kV交联电缆终端故障原因分析及制作要点

10kV交联电缆终端故障原因分析及制作要点
一、背景介绍
10kV交联电缆是电力系统中常用的一种电力输送方式,它具有体积小、重量轻、输电容量大、可靠性高等优点。
在使用过程中,电缆终端部分容易发生故障,导致电力系统的
运行受阻。
需要对10kV交联电缆终端故障原因进行分析,并提出相应的制作要点,以提高其可靠性和稳定性。
二、故障原因分析
1. 终端压力不足:电缆终端的压力不足会导致接触不良,增加电缆的电阻,产生局
部过热现象,进而导致电缆终端的故障。
2. 终端绝缘老化:长期使用后,电缆终端的绝缘材料会逐渐老化、变硬、变脆,降
低绝缘性能,容易出现故障。
3. 终端连接不牢固:终端连接不稳固或者连接面积不足,会导致电缆终端的电流过载,使得电缆终端过热,产生故障。
4. 终端保护不完善:在安装和使用过程中,对电缆终端的保护不完善,如未进行防水、防腐处理,容易导致电缆终端的故障。
5. 终端接地不良:电缆终端接地不良会导致电缆终端的电势差过大,产生局部放电,引发故障。
对于10kV交联电缆终端的制作,需要注意终端压力、绝缘材料、连接牢固、保护措施和接地等方面的问题,以确保电缆终端的可靠性和稳定性。
只有对终端故障原因进行深入
分析,并采取相应的制作要点,才能提高电力系统的运行效率和可靠性。
关于交联聚乙烯绝缘电缆常见的问题及其原因分析

关于交联聚乙烯绝缘电缆常见的问题及其原因分析一、交联的三种方式1、交联电缆性能交联就是将聚乙烯的线型分子结构通过化学交联或高能射线的辐照交联,转变成立体网状分子结构。
从而大大地提高了它的耐热性和耐环境应力开裂,减少了它的收缩性,使其受热以后不再熔化。
交联聚乙烯绝缘电缆其长期允许工作温度可达90βc o2、交联方法交联绝缘的品种虽多,但主要分为物理交联和化学交联两大类。
物理交联也称为辐照交联一般适用于绝缘厚度较薄的低压电缆。
中高压电缆一般采用过氧化物交联即用化学交方法是将线性分子通过化学交联反应起来,转化为立体网状结构。
化学交联一般还可分为过氧化物交联和硅烷交联接枝交联两种。
2.1 辐照交联辐照是采用高能粒子射线照射线性分子聚合物,在其链上打开若干游离基团,简称为接点。
接点活性很大,可把两个或几个线性分子交叉联接起来。
它的优点为:生产速度快,占用空间小;可加工材料种类多,几乎所有聚合物,产品品种多;产品用更好的耐热、耐磨和较高电气性能;可阻燃;电耗低。
但存在一些问题:设备一次投资大;对大截面电缆的辐照不均匀,经反复照射后电缆弯曲次数太多;设备开工率低。
2.2 过氧化物交联交联聚乙烯料是以低密度聚乙烯、过氧化物交联剂,抗氧剂等组成的混合物料。
加热时,过氧化物分解为化学活性很高的游离基,这些游离基夺取聚乙烯分子中的氢原子,使聚乙烯主链的某些碳原子为活性游离基并相互结合,即产生C-C交联键,形成了网状的大分子结构。
它主要优点是适合各种电压等级和各种截面的交联聚乙烯绝缘电力电缆生产,特别是35kV及以上的中高压电缆。
2.3 硅烷交联硅烷交联又称温水交联也是化学交联的一种,它有两步法、一步法和共聚法等多种方法。
硅烷接枝和挤出分在两道工序进行的称为二步法,硅烷接枝交联工艺,它是接枝和挤出分成两个工序进行,第一步由绝缘料厂将硅烷交联剂与基料在挤出机上接枝和挤出造粒,该料称为A料,同时还提供催化剂和着色剂的母料,称B料。
10kV交联电缆终端故障原因分析及制作要点

10kV交联电缆终端故障原因分析及制作要点10kV交联电缆终端故障是电力系统中常见的问题,它会导致电力系统的可靠性下降,从而影响电力供应的稳定性。
对10kV交联电缆终端故障的原因进行分析,并且了解其制作要点非常重要。
本文将对10kV交联电缆终端故障的原因进行分析,并且探讨终端制作的要点。
1. 环境因素:环境因素是导致10kV交联电缆终端故障的主要原因之一。
高温、湿度、盐雾等恶劣环境会导致10kV交联电缆终端的绝缘老化、劣化,最终导致故障的发生。
2. 施工质量:施工质量也是导致10kV交联电缆终端故障的重要原因之一。
不规范的施工操作、接头材料选用不当、接头接触不良等都会导致10kV交联电缆终端的故障。
3. 设备质量:10kV交联电缆终端的设备质量直接影响了其故障率。
如果使用质量不过关的设备,比如终端套管、接头、屏蔽套管等,都会增加10kV交联电缆终端的故障发生概率。
4. 运行过载:10kV交联电缆终端在长时间的过载运行下,会造成终端局部过热,终端材料老化,从而引起故障。
5. 其他原因:除了以上几点外,10kV交联电缆终端故障的原因还包括电缆制造质量、设计不合理、终端绝缘子损坏等。
二、10kV交联电缆终端制作要点1. 选材要点:对终端材料的选择非常关键。
终端材料需要具有良好的绝缘性能、耐高温、耐电压、耐侯性能。
在选用终端材料时,需要确保其符合国家标准和电力行业标准。
2. 施工要点:在10kV交联电缆终端制作过程中,施工要严格按照操作规程、施工工艺和标准进行。
施工人员需要严格按照标准要求进行操作,避免施工过程中出现失误。
3. 质检要点:在终端制作完成后,需要进行严格的质量检验。
主要检查终端套管、绝缘子、电缆屏蔽层、端子等设备和部件的安装质量,以及电缆的接地、套管的固定等是否符合标准要求。
4. 运行监测:对10kV交联电缆终端进行定期的运行监测,及时发现故障隐患,采取预防措施,防止故障的发生。
5. 防护措施:10kV交联电缆终端在制作完成后,需要进行防腐、防水、防潮处理,以延长终端的使用寿命。
- 1、下载文档前请自行甄别文档内容的完整性,平台不提供额外的编辑、内容补充、找答案等附加服务。
- 2、"仅部分预览"的文档,不可在线预览部分如存在完整性等问题,可反馈申请退款(可完整预览的文档不适用该条件!)。
- 3、如文档侵犯您的权益,请联系客服反馈,我们会尽快为您处理(人工客服工作时间:9:00-18:30)。
浅谈交联电缆绝缘老化强度变化率超标原因及改善
[导读]交联聚乙烯(XLPE)电缆绝缘的热老化试验在国家标准GB/T12706-2008与IEC60502中规定不得超过±25%(即老化后和老化前的中间值之差除以老化前的中间值)。
交联聚乙烯绝缘的热老化项目在标准中列入型式试验。
一般在首次试验合格后,工艺和材料没有重大变化时,不再进行该试验。
但往往一些客户在技术协议中会提到这项试验,从而就需要进行热老化试验。
当我们在试验时,发现抗张强度变化率不稳定,在生产的同一批交联线芯有合格有不合格(不合格的都是超标的现象大于+25%),但断裂伸长率变化甚小,从未超出规定值。
为此有必要对交联绝缘线芯老化强度不合格问题进行分析整改。
一、引言
交联聚乙烯(XLPE)电缆绝缘的热老化试验在国家标准GB/T12706-2008与IEC60502中规定不得超过±25%(即老化后和老化前的中间值之差除以老化前的中间值)。
交联聚乙烯绝缘的热老化项目在标准中列入型式试验。
一般在首次试验合格后,工艺和材料没有重大变化时,不再进行该试验。
但往往一些客户在技术协议中会提到这项试验,从而就需要进行热老化试验。
当我们在试验时,发现抗张强度变化率不稳定,在生产的同一批交联线芯有合格有不合格(不合格的都是超标的现象大于+25%),但断裂伸长率变化甚小,从未超出规定值。
为此有必要对交联绝缘线芯老化强度不合格问题进行分析整改。
二、原因分析
交联绝缘线芯老化强度不合格的原因分析是一个复杂的过程,国内各电缆企业往往被交联绝缘线芯老化系数K1、K2值不能达标而困扰,而这一指标是对交联绝缘线芯绝缘品质评价的主要指标之一。
但究其主要原因有以下三点:1、高温高速下绝缘中产生的热应力对交联聚乙烯绝缘热老化性能的影响;2、冷却水温对交联聚乙烯绝缘热老化性能的影响;3、交联过程中产生的副产物对交联聚乙烯绝缘热老化性能的影响。
三、解决的措施
1、硫化工艺改进:
试验选在我公司NOKIA(十段)智能硫化交联生产线上,我们通过调整工艺达到减小交联绝缘在生产过程中的内部应力来改善老化强度不合格的问题。
削除热应力的措施有很多,NOKIA早在1996年就提出采用冷却退火装置,使进入冷却段的交联绝缘线芯表面再恢复到结晶熔化温度110℃左右,再进入正常冷却过程,可以改善电缆的绝缘品质。
但我公司没有在线应力松驰装置,要想改善只能重新调整工艺线速度使之缓慢冷却,减少交联绝缘在硫化过程中的内外层绝缘温差的问题,从而改善交联的绝缘品质。
我公司NOKIA生产线配备了一套NCC硫化计算软件,控温选速比较合理。
初次调整硫化工艺是把原来的最高硫化管壁温度450℃降低到400℃,最高电缆表面温度由原来的275℃降低到260℃。
但由于是十段硫化生产线,虽然已降低了管壁温度和电缆表面温度但线速度仍然比较快,内外层绝缘温差还是比较大。
后经研究决定,想要让进入冷却段之前的线芯内外层绝缘温差减小,只有缩短硫
化管长度,也就是把最后几节硫化管加热温度设低至预冷段的温度(约120℃),这也就相当于增加了预冷段的长度使之缓慢冷却。
但到底降低几节硫化管温度才合适呢?目前按我公司NOKIA(十段)硫化线为例,我们经多次实践验证,降低4段硫化管温度最佳。
以下是我们工艺调整后计算的YJV8.7/10KV400平方的硫化工艺供参考。
2、冷却水温要求
我公司的循环冷却水系统采用的是集中供水系统,在厂房边建了一个长20米、宽10米、深3米的大水池供三台交联线生产用。
整个循环冷却水系统原理是由多个水泵将外水池的水通过一个总管抽过来,然后再分支出三路水管分别供
应三台交联,回水再通过一根总管集中流入到大水池。
从冷却效果及操作控制方面来看都比较好,唯一不足之处是冬天由于环境温度较低再加上冷却水池面积较大,使得进入冷却管的水温很低,刚从硫化管出来的线芯马上进入温度很低的冷却水骤冷,势必会产生绝缘的内应力。
为了提高冷却水的温度,经研究决定在回水处安装一个水温感应阀。
通过水温感应阀来控制水池中的水位得到我们想要的温度,我们需要的水温在30℃~40℃左右,低于30℃就自动往外排水,高于40℃就自动往里加水。
这样一来可以有效的控制好冷却水的温度,不必担心因水温过低产生绝缘的内应力。
3、降低交联绝缘中副产物浓度
在交联过程中会产生诸如苯乙酮、枯基醇和α2亚甲基苯乙烯之类的挥发***联副产物,这些副产物气体会在绝缘内停留相当长的时间。
查阅相关文献,交联副产物在刚挤制的绝缘中分布浓度高,这些低分子的副产物在绝缘中分布是不均匀的,使得交联聚乙烯绝缘的结晶不均匀,因此,老化前的抗张强度低。
在空气箱中进行老化试验时,高温作用下,交联副产物由于内部气压高而得到尽快的挥发,并且由于高温的作用,交联聚乙烯原来不均匀的晶域被全部破坏,在接着的室温静置过程中,形成了分布均匀的结晶,从而,提高了老化后的抗张强度。
针对这一现象,我们公司建立了烘房系统。
不同规格、电压等级的交联线芯规定了不同的烘放时间,烘房的温度设定基本在65℃。
另外采用了烘房后,原本刚下线的交联线芯需要停放4天时间,现在只需1天时间且除气效果比以前要好,大大提高了线芯流转的效率。
四、实施效果
通过采取以上三种措施,我们验证生产的以下交联电缆经老化试验测试,绝缘老化抗张强度变化率均在标准要求±25%范围内,见下表。
五、结论
1、在生产过程中,不要盲目的追求生产效率,要合理的选择线速度和温度生产。
2、对冷却水温的要求,在不同的季节环境下要采取相应的措施,确保水温在我们的要求范围内。
3、大力提倡采用烘房除气,这不但可以改善交联产品的质量,还可以提高生产效率。