金刚石烧结制品重点
金刚石线的主要工艺流程

金刚石线的主要工艺流程
金刚石线是一种高硬度、高强度的切割工具,广泛应用于石材、混凝土、陶瓷等材料的切割加工中。
其主要工艺流程包括原料选择、制备金刚石磨料、制备金刚石线、烧结金刚石线等几个步骤。
原料选择是制备金刚石线的第一步。
金刚石线的主要原料是金刚石磨料和金属粉末。
金刚石磨料是由天然金刚石或合成金刚石经过研磨、筛分等工艺制成的粉末,其粒径大小决定了金刚石线的粗细程度。
金属粉末则是用于烧结金刚石线的材料,常用的有镍、铜、铁等。
制备金刚石磨料是制备金刚石线的关键步骤之一。
制备金刚石磨料的工艺流程包括原料筛选、研磨、洗涤、干燥等几个步骤。
其中,研磨是最关键的一步,需要使用高速旋转的研磨机将金刚石磨料研磨成细小的颗粒,以便后续制备金刚石线时能够更好地与金属粉末结合。
接下来,制备金刚石线是金刚石线制备的核心步骤。
制备金刚石线的工艺流程包括将金刚石磨料与金属粉末混合、压制成线状、烘干等几个步骤。
其中,压制成线状是最关键的一步,需要使用专门的金刚石线压制机将混合好的金刚石磨料和金属粉末压制成线状,以便后续烧结时能够更好地固化。
烧结金刚石线是制备金刚石线的最后一步。
烧结金刚石线的工艺流
程包括将制备好的金刚石线放入烧结炉中进行高温烧结,使金刚石磨料和金属粉末充分结合,形成坚硬的金刚石线。
烧结温度和时间是影响金刚石线质量的关键因素,需要根据不同的金刚石线规格和用途进行调整。
金刚石线的主要工艺流程包括原料选择、制备金刚石磨料、制备金刚石线、烧结金刚石线等几个步骤。
这些步骤都是相互关联、相互依存的,只有每个步骤都做好了,才能制备出质量优良、性能稳定的金刚石线。
金刚石工具生产工艺流程
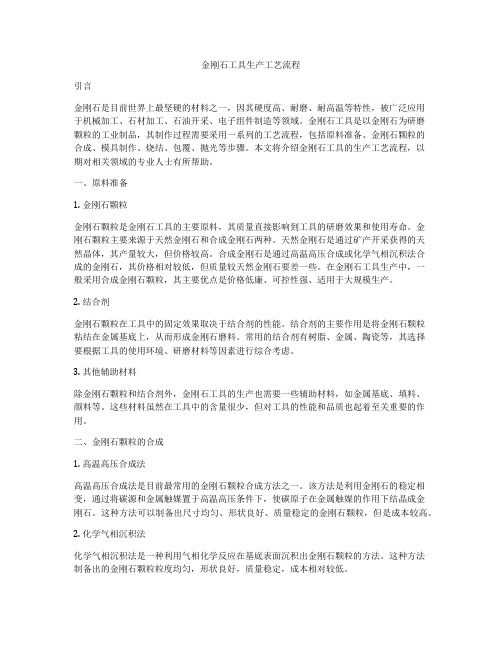
金刚石工具生产工艺流程引言金刚石是目前世界上最坚硬的材料之一,因其硬度高、耐磨、耐高温等特性,被广泛应用于机械加工、石材加工、石油开采、电子组件制造等领域。
金刚石工具是以金刚石为研磨颗粒的工业制品,其制作过程需要采用一系列的工艺流程,包括原料准备、金刚石颗粒的合成、模具制作、烧结、包覆、抛光等步骤。
本文将介绍金刚石工具的生产工艺流程,以期对相关领域的专业人士有所帮助。
一、原料准备1. 金刚石颗粒金刚石颗粒是金刚石工具的主要原料,其质量直接影响到工具的研磨效果和使用寿命。
金刚石颗粒主要来源于天然金刚石和合成金刚石两种。
天然金刚石是通过矿产开采获得的天然晶体,其产量较大,但价格较高。
合成金刚石是通过高温高压合成或化学气相沉积法合成的金刚石,其价格相对较低,但质量较天然金刚石要差一些。
在金刚石工具生产中,一般采用合成金刚石颗粒,其主要优点是价格低廉、可控性强、适用于大规模生产。
2. 结合剂金刚石颗粒在工具中的固定效果取决于结合剂的性能。
结合剂的主要作用是将金刚石颗粒粘结在金属基底上,从而形成金刚石磨料。
常用的结合剂有树脂、金属、陶瓷等,其选择要根据工具的使用环境、研磨材料等因素进行综合考虑。
3. 其他辅助材料除金刚石颗粒和结合剂外,金刚石工具的生产也需要一些辅助材料,如金属基底、填料、颜料等。
这些材料虽然在工具中的含量很少,但对工具的性能和品质也起着至关重要的作用。
二、金刚石颗粒的合成1. 高温高压合成法高温高压合成法是目前最常用的金刚石颗粒合成方法之一。
该方法是利用金刚石的稳定相变,通过将碳源和金属触媒置于高温高压条件下,使碳原子在金属触媒的作用下结晶成金刚石。
这种方法可以制备出尺寸均匀、形状良好、质量稳定的金刚石颗粒,但是成本较高。
2. 化学气相沉积法化学气相沉积法是一种利用气相化学反应在基底表面沉积出金刚石颗粒的方法。
这种方法制备出的金刚石颗粒粒度均匀,形状良好,质量稳定,成本相对较低。
3. 氧化还原法氧化还原法是一种利用金属氧化物和还原剂相互作用的方法,制备出金刚石颗粒。
烧结保温时间对金刚石工具产品性能的影响

烧结 工序 是粉 末 冶 金 制 品生 产 过 程 中的一 个 关
键工序, 也 是 对 最 终 产 品 性 能 与 质 量 影 响 最 直 接 的 工
2 实 验
本文中 以 C o为 基 础 配 方 产 品 , C o为 主 体 , 占 7 O , 配以 1 7 的C u , 其他 元素 Ni 、 Mn 、 S n 、 Z n等 占
YA N G Li ~ q i n g, LU o Yi ng,I U o We n — l a i
( 1 . Gu i l i n Te b o n Su p e r h a r d Ma t e r i a l Co . ,Lt d. ,Gu i l i n,Gu a n g xi 5 4 1 0 0 4; 2 . Gu a n g xi Ke y La b o r a t o r y o f S u p e r h a r d Ma t e r i a l ,Gu i l i n,Gu a n g  ̄ 5 4 1 0 0 4)
l 3 , 以此来 设 计 配 方 进 行 研 究 , 粉 料 的粒 度 为 3 0 0
序, 因此通 过研 究烧 结 工 艺 对 产 品性 能 的影 响 , 对 我 们 更 为清 晰 、 更 为 深 入 掌 握 产 品 的 性 能 有 着 重 要 作 用 。本 文重 点研究 了烧结 工艺 中烧结 温 度 、 烧 结时 间
V 01 . 28 De c . 2O1 6
烧 结 保 温 时 间对 金 刚 石 工 具 产 品 性 能 的 影 响
杨理清 , 骆 颖, 罗文 来
( 1 . 桂林 特 邦新 材 料 有 限公 司 , 广 西 桂林 5 4 1 0 0 4 ;2 . 广西超硬材料重点实验室 , 桂林 5 4 1 0 0 4 )
烧结金刚石划锯片安全操作及保养规程
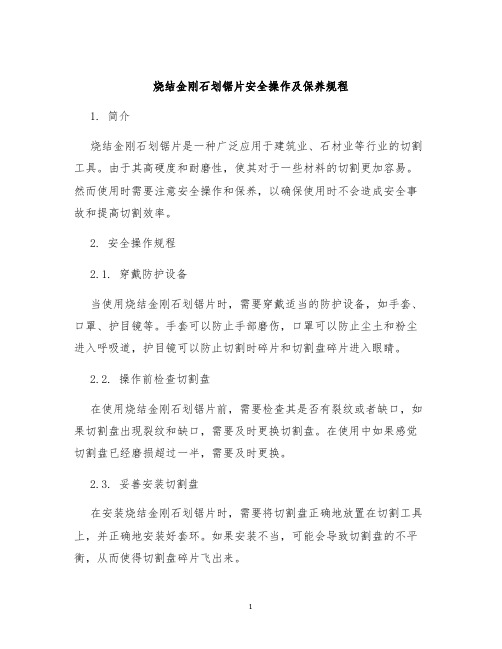
烧结金刚石划锯片安全操作及保养规程1. 简介烧结金刚石划锯片是一种广泛应用于建筑业、石材业等行业的切割工具。
由于其高硬度和耐磨性,使其对于一些材料的切割更加容易。
然而使用时需要注意安全操作和保养,以确保使用时不会造成安全事故和提高切割效率。
2. 安全操作规程2.1. 穿戴防护设备当使用烧结金刚石划锯片时,需要穿戴适当的防护设备,如手套、口罩、护目镜等。
手套可以防止手部磨伤,口罩可以防止尘土和粉尘进入呼吸道,护目镜可以防止切割时碎片和切割盘碎片进入眼睛。
2.2. 操作前检查切割盘在使用烧结金刚石划锯片前,需要检查其是否有裂纹或者缺口,如果切割盘出现裂纹和缺口,需要及时更换切割盘。
在使用中如果感觉切割盘已经磨损超过一半,需要及时更换。
2.3. 妥善安装切割盘在安装烧结金刚石划锯片时,需要将切割盘正确地放置在切割工具上,并正确地安装好套环。
如果安装不当,可能会导致切割盘的不平衡,从而使得切割盘碎片飞出来。
2.4. 控制切割深度在切割材料的过程中,需要控制切割深度。
如果切割深度超过了烧结金刚石划锯片的厚度,可能会导致切割盘的磨损、切割面粗糙或者切割盘碎片飞出来。
2.5. 避免锯刀侧倾在使用烧结金刚石划锯片时,应尽量避免锯刀侧倾,因为侧倾可能会导致切割盘碎片飞出来。
如果需要调整锯刀的位置,应该先停机,然后再进行调整。
在调整切割深度和角度的时候,也应该先停机,然后进行调整。
2.6. 避免使用过高转速在使用烧结金刚石划锯片时,需要避免使用过高的转速。
如果转速过高,可能会使得烧结金刚石划锯片的表面速度超过了其可以承受的极限,从而导致切割盘的磨损、故障和切割盘碎片飞出来。
2.7. 妥善放置切割工具在使用烧结金刚石划锯片时,需要妥善放置切割工具,以防止切割盘碎片或者切割工具伤人。
在使用完成后,需要将切割工具放置在安全地方,防止孩子或者其他人误触。
3. 保养规程3.1. 妥善保管在使用完成后,需要对烧结金刚石划锯片进行妥善保管。
金刚石磨料 烧结 钎焊 电镀工艺

金刚石磨料烧结钎焊电镀工艺金刚石磨料是一种非常硬的材料,具有优异的磨削性能和高耐磨性。
金刚石磨料广泛应用于机械加工、电子、航空航天等行业,逐渐成为各行各业中不可或缺的材料。
金刚石磨料的生产过程分为烧结、钎焊和电镀三个步骤。
下面我们将详细介绍这三个工艺。
首先是烧结工艺。
烧结是将金刚石颗粒与金属粉末混合后,在高温高压条件下进行热处理,使金刚石颗粒与金属粉末形成牢固的结合。
烧结工艺包括原料的混合、成型和热处理三个步骤。
在原料的混合阶段,金刚石颗粒和金属粉末按一定比例混合,并加入一定的粘结剂,形成均匀的混合物。
混合物经过预压处理后,进入成型阶段。
成型可采用压制法或注射法,将混合物压制成所需形状的坯体。
然后将坯体放入高温高压的烧结炉中进行热处理。
在高温高压条件下,金属粉末熔化,与金刚石颗粒形成结合,最终形成坚固的金刚石材料。
接下来是钎焊工艺。
钎焊是将烧结得到的金刚石工具与金属或合金基体进行连接。
钎焊工艺包括金属基体的清洗、钎焊剂的涂布、加热和冷却四个步骤。
钎焊前,需要对金属基体进行清洗,以去除表面污物和氧化物。
然后在金属基体上涂布钎焊剂,钎焊剂能够降低钎焊温度,并提高钎焊强度。
将烧结得到的金刚石工具放置在金属基体上,然后加热到钎焊温度,使钎焊剂熔化并与金属基体及金刚石工具形成连接。
最后,冷却金刚石工具,使其与金属基体牢固连接在一起。
最后是电镀工艺。
电镀是将金刚石颗粒和金属沉积于基体表面,以提高金刚石工具的耐磨性。
电镀工艺包括基体的准备、电解液的配制、电镀过程和后处理四个步骤。
电镀前,需要对基体进行准备,包括清洗和表面处理,以保证电镀层的质量。
然后准备电解液,通常采用金属盐类和一定添加剂配制而成。
将准备好的基体放入电解槽中,与阳极连接。
将金刚石颗粒加入电解槽,经过一段时间的电镀,金刚石颗粒沉积在基体表面形成金刚石电镀层。
最后,对金刚石电镀层进行后处理,例如抛光和清洗,以提高表面质量。
综上所述,金刚石磨料的生产过程主要包括烧结、钎焊和电镀三个工艺。
自蔓延烧结在金刚石制品中的应用

自蔓 延 烧 结在 金 刚石 制 品 中 的应 用
邵 俊 永 刘 明耀 夏 举 学 。 (. 1河南 工业 大学 材 料科 学与 工程 学 院 , 郑州 400 ) 50 7
(. 2 郑州磨料磨具磨削研究所 , 郑州 400 ) 50 7
摘要 本 文主要介 绍 了 自蔓延 高温合 成技 术 的发 展 和特 点 , 阐述 了 自蔓延 高 温合 成技 术在 金 刚石 制 品
F n l tp i t u he is e h tn e o b u he e e r h d o h HS a pl ai n n d a n o l n i al i o ns o tt s u st a e d t e f r rr s a c e ft e S p i t si i mo d to sma — y t c o
u a t e f cur .
Ke wo d s r- r p g t g h g e e a u e s n h ss y rs e p o a a i ih t mp r t r y t e i ;dimo d p o ucs a pl ai n; f n a n r d t p i to c
21 o 0 0年 4月 第3 O卷
第 2期
金刚石与磨料磨具工程
Dim o d & Ab a ie gne rn a n r sv sEn i ei g
金刚石锯片烧结炉工艺流程

金刚石锯片烧结炉工艺流程金刚石锯片烧结炉工艺流程是指将金刚石粉末和金属粉末混合后,在高温高压下进行烧结,制成金刚石锯片的过程。
该工艺流程主要包括原料准备、混合、压制、烧结、冷却、切割和检验等环节。
1. 原料准备金刚石锯片烧结炉的原料主要包括金刚石粉末、金属粉末和添加剂。
其中金刚石粉末是制备金刚石锯片的主要原料,其粒径大小和形状对烧结后的金刚石锯片质量有很大影响。
金属粉末的种类和比例也会影响烧结后的金刚石锯片的性能。
添加剂的作用是促进金刚石粉末和金属粉末的烧结,提高金刚石锯片的强度和硬度。
2. 混合将金刚石粉末、金属粉末和添加剂按一定比例混合均匀。
混合的过程需要注意控制混合时间和混合速度,以避免金刚石粉末的磨损和变形。
3. 压制将混合后的原料放入压制模具中,进行压制。
压制的目的是将原料压成所需形状和尺寸的坯体,以便进行后续的烧结处理。
压制的压力和时间需要根据原料的性质和压制模具的形状和尺寸进行调整。
4. 烧结将压制好的坯体放入烧结炉中进行烧结。
烧结的过程需要控制温度、压力和时间等参数,以保证金刚石粉末和金属粉末的烧结。
烧结的温度和时间需要根据原料的性质和烧结炉的型号进行调整。
烧结后的金刚石锯片具有较高的硬度和强度。
5. 冷却将烧结后的金刚石锯片从烧结炉中取出,进行冷却。
冷却的过程需要控制冷却速度,以避免金刚石锯片的热裂和变形。
6. 切割将冷却后的金刚石锯片进行切割,制成所需形状和尺寸的金刚石锯片。
切割的过程需要使用专业的切割设备和工具,以保证金刚石锯片的质量和精度。
7. 检验对制成的金刚石锯片进行检验,包括外观检查、尺寸测量、硬度测试和强度测试等。
检验的目的是确保金刚石锯片的质量符合要求,以便投入使用。
总之,金刚石锯片烧结炉工艺流程是一个复杂的过程,需要掌握一定的专业知识和技能。
只有严格按照工艺流程进行操作,才能制备出质量优良的金刚石锯片。
连续式热压烧结金刚石制品的研究

总第 1 9 9期
连 续 式 热 压 烧 结 金 刚石 制 品 的研 究
周 浩 钧 ,尹 育 航 。 ,陶 洪 亮 , 段 文 远
( 1 . 西 安 建 筑 科 技 大 学 材 料 与矿 资学 院 , 陕西 7 1 0 0 5 5 )
( 2 . 广 东 奔 朗新 材 料 股 份 有 限公 司 , 佛山 5 2 8 3 1 3 )
中 图分类 号 T Q1 6 4 ;T G7 4 文献 标 志码 A 文章编 号 1 0 0 6 — 8 5 2 X( 2 0 1 4 ) 0 1 — 0 0 5 3 — 0 4
DOI :1 0 . 1 3 3 9 4 / i . c n k i . j g s z z . 2 0 1 4 . 1 . 0 0 1 2
Xi’ an 7 1 0 05 5,Chi n a) f 2.M o n t e — Bi an c o Di am o n d Appl i c at i o n s Co. ,Lt d. ,Fo s ha n 52 8 3 13,Chi n a)
Ab s t r a c t Si n t e r i n g i s t he ke y t o t he p e r f or ma nc e o f d i a mo n d p r od uc t s. Two ki n ds of s i nt e r i ng pr o c e s s e s, na me l y c o nt i nuo us — hot p r e s s i n g a nd t r a d i t i o na l ho t pr e s s i ng,a r e s t ud i e d by pr e pa r i ng s a w bl a d e s a mp l e s wi t h
- 1、下载文档前请自行甄别文档内容的完整性,平台不提供额外的编辑、内容补充、找答案等附加服务。
- 2、"仅部分预览"的文档,不可在线预览部分如存在完整性等问题,可反馈申请退款(可完整预览的文档不适用该条件!)。
- 3、如文档侵犯您的权益,请联系客服反馈,我们会尽快为您处理(人工客服工作时间:9:00-18:30)。
金刚石烧结制品重点公司内部档案编码:[OPPTR-OPPT28-OPPTL98-OPPNN08]简答题:1.什么叫做比表面比表面与颗粒的哪些性质有关2.论述影响松装密度、流动性和压制性的因素及之间的关系.3..叙述压坯密度与压制压力之间的变化规律.4.叙述再结晶与晶粒长大的动力学过程.5.为什么金属结合剂的金刚石制品常常采用热压烧结6.叙述液相烧结过程.7.简述结合剂的组成性能与加工材质和加工方式的关系.8.叙述金属结合剂的对金刚石烧结制品使用性能的影响。
9.需制造某种磨具5片,已知磨具的单片质量为530克,所选用的结合剂成分配比(质量分数%)为Cu78Sn12Ag7Zn3,外加石墨1%。
求各种粉末的用量。
(设投料系数为10.如何判断混合结合剂后,其是否混合均匀11.结合剂贮存应注意什么12.磨具产品的测试主要有哪些内容13.简要列出配方设计的试验工作的一般程序。
14.已知非金刚石层体积和金刚石层体积分别为:Vi=13.56cm3,V=12.35cm3。
采用冷压成型工艺,结合剂成型密度的γ=7.5g/cm3,金刚石浓度为100%。
求金刚石用量和结合剂用量(包括非金刚石层的结合剂用量)。
15.叙述热压法工艺特点为。
16.冷压烧结过程中500℃的保温阶段坯体内主要发生什么变化为什么此阶段十分重要17.冷压烧结时,冷却阶段对最终产品的性能有什么影响18.如果金刚石磨具出现废品时,通过镜下观察发现其组织结构不均匀,在实际生产中,我们应从哪几个方面分析其产生的原因。
19.叙述金刚石在切割过程中磨损情况。
20.根据切割工件材料特点对选择金刚石和结合剂有什么要求。
21.对于长为40mm,高为5mm,厚为4mm的节块,计算1000个节块金刚石用量、金刚石层结合剂用量、过渡层料的用量。
假设成型密度为8.89g/cm3,金刚石的浓度按50%计算。
22.选择焊料一般要满足什么样的要求。
23.写出一般金刚石锯片制造工艺流程24.叙述锯片开刃过程。
25.在制造金刚石钻头时,调整胎体硬度的方法主要有哪些26.为什么说钻头胎体的硬度选择在使用过程中起着重要的作用。
27、壁薄工程钻头对胎体材料有什么特殊要求。
28、叙述比表面积对金属粉末性质的影响。
30、在粉末受压制时,粉末在压力下主要发生哪些变形,各有什么特点,其对压制时的密度产生什么样的影响。
31、压制后坯体的密度会产生不均匀的现象的原因是什么,如何减少坯体其密度不均匀性。
32、在压制工艺过程中,一般都设定一段保压时间,为什么33、根据烧结理论,在等温烧结过程中主要发生哪三个阶段,叙述各阶段的特点。
34、从热力学观点出发,简要说明等温烧结的动力。
35、在烧结过程中,叙述粘合作用的主要特征。
36、叙述烧结时,扩散传质的特点。
37、什么是热压烧结38、叙述温度对烧结制品的影响39、概念题:耐磨性、强度、韧性、硬度、粘结性能、金刚石浓度、弹性后效、粉末冶金、烧结、松装密度、压制性、流动性40.粉末冶金的优点41、为什么常常用粉末冶金方法制造金刚石工具42、请用胡克定理推导粉末受压时的侧压力公式43、影响成型密度差异的原因有哪些你是如何采用方法来减小密度差异44、烧结过程:1.烧结颈形成阶段形成原因:在升温过程和等温烧结初期,发生以下特征:(1)坯体内的吸附气体和添加剂的挥发;(2)颗粒表面的氧化物被还原;(3)变形颗粒的回复再结晶;(4)颗粒表面原子的扩散及晶体结合;(5)颗粒的之间点扩大到面,就形成烧结颈。
宏观特征:(1)颗粒形状未发生明显变化,(2)孔隙之间形成连续网络,孔隙之间的总表面没有明显减少,(3)烧结体也没有明显的收缩(4)使得烧结体强度和导电性明显的增加;2.烧结颈长大和闭孔形成阶段形成原因:(1)原子向颗粒结合面的大量迁移使烧结颈扩大,(2)颗粒间距离缩小,形成连续的孔隙网络。
同时由于晶粒长大,(3)晶界越过孔隙移动,而被晶界扫过的地方,孔隙大量消失。
宏观特征:(1)烧结体收缩;(2)密度和强度增加;3.闭孔减少和球化阶段形成原因: (1) 多数孔隙被完全分隔,闭孔数量大为增加,(2)孔隙形状趋近球形并不断缩小,(3)晶粒粗化。
特征: (1)小孔的消失和孔隙数量的减少,(2)烧结体仍可缓慢收缩。
这一阶段可以延续很长时间,但是仍残留少量的隔离小孔隙不能消除。
烧结驱动力:化学梯度的产生推动物质的位移,从而才形成了粉末或压坯的烧结。
从热力学观点看,坯体的烧结过程是系统自由能减小的过程,对等温烧结来说,也就是系统过剩自由能降低的过程。
过剩自由能包括表面能和晶格畸变能,因表面能的降低比晶格畸变能的减小要大得多,所以我们可将表面能的降低视为等温烧结过程的驱动力。
驱动力表现为三个方面:1、颗粒烧结颈的增大和颗粒表面的平直化,粉末体的总比表面积和总表面自由能减小2、烧结体的内孔隙体积和表面积减小3、粉末颗粒的内晶畸变的消除表面张力的作用下,颗粒凸面产生向心应力,可用拉普拉斯方程:σ= - 2γ/r而在烧结颈的曲面上产生向外的应力为:σb=γ(1/x-1/ρ) ≈ -γ/ρ(x>>ρ)在这两个力的作用下,物质由表面向颈面流动: ρ一般大于r,当两球相互靠近后,ρ增大,σb减小,减小烧结动力。
直到趋于平衡,停止烧结。
表面应力使颗粒表面和颈曲面上的蒸汽压变化,由开尔文公式可求出平面与曲面上的饱和蒸汽压差,说明物质由颗粒表面蒸发,在烧结颈表面沉积,随着烧结颈长大,压差↓由式知,DP球> DP颈,表明颗粒表面蒸汽压大于颈曲面蒸汽压,这样将导致颗粒表面上物质蒸发并通过气相扩散迁移到烧结颈曲面上凝结下来,使得烧结颈长大。
在烧结颈部因受到拉应力的作用,空位形成能降低→产生过剩空位浓度,使烧结颈处空位浓度大于平衡空位浓度。
考虑在烧结颈部与附近区域空位浓度的差异,有:空位浓度梯度:△Cv/ρ= -CvoγΩ/(kTρ2)可以发现:↑γ(活化)、↓ρ(细粉),均有利于提高空位浓度梯度,增加烧结的扩散驱动力。
可将系统内空位浓度视为烧结动力在烧结温度下,金属粉末的塑性大大增加,屈服强度显着下降。
因而,烧结外力场的作用有可能会超过材料的屈服应力σy,导致粉末晶体产生位错,使得物质以晶面滑移或整排运动形式迁移,这样的烧结机构被称为塑性流动。
和粘性流动不同,塑性流动只有当外应力σ超过材料屈服点时才能产生。
蒸发与凝聚1)传质条件:a.粉体在高温下有较大的蒸气压;b.凸凹面压差大ΔP↑ (要求颗粒小) ;c.有足够高的温度。
2)传质机理:由于颗粒表面(凸面蒸气压比颈部(凹面)蒸气压高,故质点从表面蒸发通过气相传递凝聚到颈部,而使颈部逐渐被填充。
这种传质过程仅仅在高温下蒸气压较大的系统内进行,如氧化铅、氧化铍和氧化铁的烧结。
溶解-沉淀传质1)传质机理●由于表面张力的作用,颗粒某些部位(颗粒接触点)受压,某些部位受拉,受压处固相溶解度比受拉处固相溶解大(Kingery 模型);●由于小颗粒溶解度比大颗粒溶解度大(LSW 模型),因此颗粒在颗粒接触点处溶解或小颗粒溶解,通过液相传质,而在颗粒自由表面或大颗粒上沉淀,从而出现晶粒长大和晶粒形状的变化。
液相烧结的条件液相烧结必须满足以下三方面的条件,才会发挥液相有利的作用。
1.润湿性如θ=0,则表明液相对固相完全润湿,如0<θ<90,则是部分润湿,如θ>90,则表明不润湿2.溶解度液相形成后固相物质在液相中要有一定的溶解度,因为1)固相有限溶解于液相可改善润湿性,2)固相溶于液相可增加液相量,3)固相溶于液相可以在液固相之间进行原子扩散,有利于液相的作用,4)溶在液相中的固相在冷却时的析出可填补固相颗粒表面缺陷和间隙,并增大固相颗粒分布均匀性3.液相数量也即必须有一定数量的液相,以确保液相能填满固相间隙,当然液相量不能过多,否则不能保持烧结体的形状,液相量以占体积的20~50%为宜。
1.液相生成与颗粒重排阶段液相形成后,由于毛细管力的作用,如图所示。
图中ψ为两面角,σ表面张力。
在表面张力作用下,将会使固相颗粒趋于更致密的排列,以这一阶段烧结体密度上升很快。
2.固相溶解与析出阶段由于固相在液相中有一定的溶解度,在液相形成后,与液相接触的固相溶解于液相达饱和程度。
对具有曲率半径为r的颗粒,其饱和溶解度与平面之差为:△C=2γslδ3/KT?1/∞式中:C∞-平面处饱和溶解度曲率半径越小,溶解度越大由于大小颗粒以及颗粒凹凸面的溶解度是有差别的,所以将会发生溶解度大的小颗粒和颗粒凸面先溶解然后沉积在溶解度低的大颗粒和颗粒凹面上3.骨架形成阶段●经过前两个阶段,固相颗粒之间相互靠拢,在固相颗粒与固相颗粒接触之间发生固相烧结,这种固相颗粒之间的烧结形成类似于骨架一样的固体颗粒连接形态。
●这一阶段致密速率已很低,在固相颗粒间仍存在体积扩散与晶粒长大。
●固相颗粒的形状以及分布取决于固相物质的结晶学特征和液相的润湿性。
定义:热压又称为加压烧结,是把粉末装在模腔内,在加压的同时使粉末加热到正常烧结温度或更低一些,经过较短时间烧结成致密而均匀的制品,热压可将压制和烧结两个工序一并完成,可以在较低压力下迅速获得冷压烧结所达不到的密度。
本质:热压是一种强化烧结。
热压烧结时,驱动力除表面张力外,又加上了外压的作用。
在外压下,粉粒间接触部位产生塑性流动或蠕变,使颗粒间距缩短,缩颈长大的动力学过程进行得更为方便。
受压处固相溶解度大。
热压方法的最大优点是可以大大降低成形压力和缩短烧结时间,(2)热压压力仅为冷压成形的1/10,可以压制大型制件;(3)热压时,粉末热塑性好,可以压成薄壁管、薄片及带螺纹等异型制品;(4)粉末粒度、硬度对热压过程影响不明显,因此可压制一些硬而脆的粉末结合剂中铜和锡的优缺点,论述为什么选用铜锡合金作为磨具的主要结合剂优点:1)电解铜粉成型性好,广泛用于冷压成型后烧结,压坯不易塌落;2)某些元素的微量加入可以使铜对碳材料从不润湿变成润湿,如,钛3)纯铜对碳化物和骨架材料的相容性很好,如W,WC等;4)纯铜的耐磨性优于青铜,可烧结性好;5)铜可与Sn,Zn,Mn,Ni,Ti等制成性能优异的合金,例如Cu-Sn-Ti,Cu-Ni-Mn,Cu-Ni-Zn及663青铜等。
铜的缺点如下:1)纯铜的变形性大,不宜制成高质量的工具,铜基合金会有某种程度上的改观;2)铜、铁间的互溶性不好,彼此溶解度很低,这将对铁基结合剂的应用和推广带来一定的麻烦;3)由于铜的强度低,对碳材料的润湿性差,所以对金刚石的把持力和粘结力都不高;4)铜与锡、钛在大气中的可烧结性不好,氧化严重,必须在真空或保护气氛下烧结,使工具成本增加。
锡的优点1)改善可烧结性;2)易形成金属间化合物,可以改善磨损性能和降低变形性(降低挠度);3)适于添加到冷压成型胎体中,靠液相在固体粉末中的虹吸现象产生毛细管力使胎体收缩;4)降低液态合金的表面张力,降低内界面张力,降低接触角; 5)改善铁基胎体的磨损性能和变形性,这是因为锡在铁基胎体中可以形成Fe3 Sn和Fe70Sn15 C15金属间化合物和复式碳化物。