SMT表面组装技术SMT基础培训资料
SMT工艺基础培训

2021/9/17
23
SMT回流后常见不良
锡珠
1、锡膏解冻时间是否足够 2、网底是否定时清洗 3、钢网太厚 4、钢网开口形状 5、贴片压力是否过大 6、升温时,速度太快 7、车间的温、湿度
2021/9/17
24
SMT回流后常见不良
错件、漏件、元件反向 冷焊、锡珠、 翻件、偏位、元件浮高 焊盘缺损、氧化污染 PCB线路缺损、露铜、PCB起泡分层、绿油、划伤、
2、按生产工艺分:锡膏钢网和红胶钢网,而锡膏钢网又可分为无铅 锡膏钢网和有铅锡膏钢网。
3、钢网的规格我们公司现在主要用的是420MM*520MM、 584MM*584MM和736MM*736MM三种规格的,现在主要选用以 736*736MM为主,以减少订钢网时间。
2021/9/17
4
钢网知识
4、锡膏钢网模块厚度选取: A、0402元件一般选用0.12MM厚度的钢网,0603元件以上可用
1F =103mF =106uF=109nF=1012pF
2021/9/17
28
SMT元件的认识
电 感:L
单位:亨利(H)、毫亨(mH)、微亨(uH)
1H=103mH=106uH
2021/9/17
22uH(微亨)
6.8uH(微亨)
29
SMT元件的认识
二极管:D 有方向
二极管的特性:单向导电性能
三极管:Q 有方向
2021/9/17
17
回流曲线各区的功能
• Soak 均温区的功能 1、使PCB板、元件与Pad均匀吸热,减少它们之间的温差; 2、焊膏活性剂开始工作,去除管脚与Pads上面的氧化物;
3、保护管脚与Pads在高温的环境下不再被氧化;
SMT基础知识培训教材

文件更改记录SMT基础知识培训教材一、教材内容1.SMT基本概念和组成2.SMT车间环境的要求.3.SMT工艺流程.4.印刷技术:4.1 焊锡膏的基础知识.4.2 钢网的相关知识.4.3 刮刀的相关知识.4.4 印刷过程.4.5 印刷机的工艺参数调节与影响4.6 焊锡膏印刷的缺陷,产生原因及对策.5.贴片技术:5.1 贴片机的分类.5.2 贴片机的基本结构.5.3 贴片机的通用技术参数.5.4 工厂现有的贴装过程控制点.5.5 工厂现有贴装过程中出现的主要问题,产生原因及对策.5.6 工厂现有的机器维护保养工作.6.回流技术:6.1 回流炉的分类.6.2 GS-800热风回流炉的技术参数.6.3 GS-800 热风回流炉各加热区温度设定参考表.6.4 GS-800 回流炉故障分析与排除对策.6.5 GS-800 保养周期与内容.6.6 SMT回流后常见的质量缺陷及解决方法.6.7 SMT炉后的质量控制点7.静电相关知识。
《SMT基础知识培训教材书》二.目的为SMT相关人员对SMT的基础知识有所了解。
三.适用范围该指导书适用于SMT车间以及SMT相关的人员。
四.参考文件3.1 IPC-6103.2 E3CR201 《SMT过程控制规范》3.3 创新的WMS五.工具和仪器六.术语和定义七.部门职责八.流程图九.教材内容1.SMT基本概念和组成:1.1SMT基本概念SMT是英文:Surface Mounting Technology的简称,意思是表面贴装技术.1.2SMT的组成总的来说:SMT包括表面贴装技术,表面贴装设备,表面贴装元器件及SMT管理.2.SMT车间环境的要求2.1 SMT车间的温度:20度---28度,预警值:22度---26度2.2 SMT车间的湿度:35%---60% ,预警值:40%---55%2.3 所有设备,工作区,周转和存放箱都需要是防静电的,车间人员必须着防静电衣帽. 3.SMT工艺流程:4. 印刷技术:4.1 焊锡膏(SOLDER PASTE)的基础知识4.1.1 焊锡膏是将焊料粉末与具有助焊功能的糊状焊剂混合而成的一种浆料,通常焊料粉末占90%左右,其余是化学成分.4.1.2 我们把能随意改变形态或任意分割的物体称为流体,研究流体受外力而引起形变与流动行为规律和特征的科学称为流变学.但在工程中则用黏度这一概念来表征流体黏度性的大小. 4.1.3 焊锡膏的流变行为焊锡膏中混有一定量的触变剂,具有假塑性流体性质.焊锡膏在印刷时,受到刮刀的推力作用,其黏度下降,当到达摸板窗口时,黏度达到最低,故能顺利通过窗口沉降到PCB 的焊盘上,随着外力的停止,焊锡膏黏度又迅速回升,这样就不会出现印刷图形的塌落和漫流,得到良好的印刷效果. 4.1.4 影响焊锡膏黏度的因素4.1.4.1 焊料粉末含量对黏度的影响:焊锡膏中焊料粉末的增加引起黏度的增加. 4.1.4.2 焊料粉末粒度对黏度的影响:焊料粉末粒度增大时黏度会降低.4.1.4.3 温度对焊锡膏黏度的影响:温度升高黏度下降.印刷的最佳环境温度为23+/-3度. 4.1.4.4 剪切速率对焊锡膏黏度的影响:剪切速率增加黏度下降.黏度粒度 温度4.2 钢网(STENCILS)的相关知识4.2.1 钢网的结构一般其外框是铸铝框架,中心是金属模板,框架与模板之间依靠丝网相连接,呈”刚—柔---刚”结构.4.2.3 目前我们对新来钢网的检验项目4.2.3.1 钢网的张力:使用张力计测量钢网四个角和中心五个位置,张力应大于30N/CM.4.2.3..2 钢网的外观检查:框架,模板,窗口,MARK等项目.4.2.3.3 钢网的实际印刷效果的检查.4.3 刮刀的相关知识4.3.1 刮刀按制作形状可分为菱形和拖尾巴两种;从制作材料上可分为橡胶(聚胺酯)和金属刮刀两类.4.3.2 目前我们使用的全部是金属刮刀,金属刮刀具有以下优点:从较大,较深的窗口到超细间距的印刷均具有优异的一致性;刮刀寿命长,无需修正;印刷时没有焊料的凹陷和高低起伏现象,大大减少不良.4.3.3 目前我们使用有三种长度的刮刀:300MM,350MM,400MM.在使用过程中应该按照PCB板的长度选择合适的刮刀.刮刀的两边挡板不能调的太低,容易损坏模板.4.3.4 刮刀用完后要进行清洁和检查,在使用前也要对刮刀进行检查.4.4 印刷过程4.4.1印刷焊锡膏的工艺流程:焊锡膏的准备支撑片设定和钢网的安装调节参数印刷焊锡膏检查质量结束并清洗钢网4.4.1.1 焊锡膏的准备从冰箱中取出检查标签的有效期,填写好标签上相关的时间,在室温下回温4H,再拿出来用锡膏摇均器摇匀锡膏,目前我们使用摇匀器摇3MIN-4MIN。
SMT基础知识(培训资料)
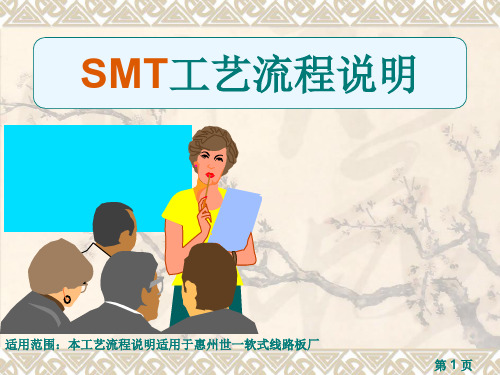
作业流程说明 《烘烤工序》
基本要求及注意事项: 1、FPC摆放烘烤时需将FPC滩开,避免折叠及重压,以免压伤FPC; 2、每个铝盆放置数量根据产品尺寸不同进行定义;整枚产品一般为100枚/层,单个产品
一般为600PCS/铝盆; 2、烘烤条件根据不同机种的需要按照烤箱管理卡要求进行; 3、使用测温计每班需对烤箱温度进行点检,确认是否与烤箱管理卡相符合; 4、拿取烤箱内的FPC时,需先将烤箱电源关闭后再将门打开,双手带耐高温手套,站在
SMT与我们日常生活息息相关,我们使用的计算机、手机、打印机、复印机、掌上 电脑、快译通、电子记事本、DVD、VCD、CD、随身听、摄象机、传真机、微波炉、高 清晰度电视、电子照相机、IC卡,还有许多集成化程度高、体积小、功能强的高科技控 制系统,都是采用SMT生产制造出来的,可以说如果没有SMT做基础,很难想象我们能 使用上这些使生活丰富多采的商品。
盘装tray盘管装盘装tray盘管装第5页表面贴装元件的种类有源元件陶瓷封装无源元件单片陶瓷电容钽电容厚膜电阻器薄膜电阻器轴式电阻器clccceramicleadedchipcarrier陶瓷密封带引线芯片载体dipdualinlinepackage双列直插封装sopsmalloutlinepackage小尺寸封装qfpquadflatpackage四面引线扁平封装bgaballgridarray球栅阵列smc泛指无源表面安装元件总称smd泛指有源表面安
第3页
名词解释
FPC: FPC是Flexible Printed Circuit的简称,又称软性线路板 PCB: PCB是Printed Circuit Board的简称,又称印刷电路板 锡膏:英文名称Solder,无铅锡膏成分一般为Sn/Ag/Cu,含量比为96.5:3.0:0.5,有铅锡膏成 分一般为Sn/Pb63:37. 热电偶:由两种不同金属制成的传感器,受热时,在温度测量中产生一个小的直流电压 硅胶:化学式xsio 2·yh 2o。透明或乳白色粒状固体。具有开放的多孔结构,吸附性强,能吸 附多种物质。如吸收水分,吸湿量约达40%。如加入氯化钴,干燥时呈蓝色,吸水后呈红色。 可再生反复使用。 模板:用于装载、固定FPC、薄板的载具。通用材质有铝合金、玻璃纤维、合成石。 钢网:英文名:MASK,是指使锡膏按指定位置印刷到线路板焊盘上的模具。 FEEDER:贴片机上用于安装物料的专用治具,根据不同尺寸元器件使用FEEDER不同。 刮刀:印刷机专用工具,其作用是将锡膏沿钢网孔壁压到产品焊盘上。
SMT表面组装技术SMT培训资料
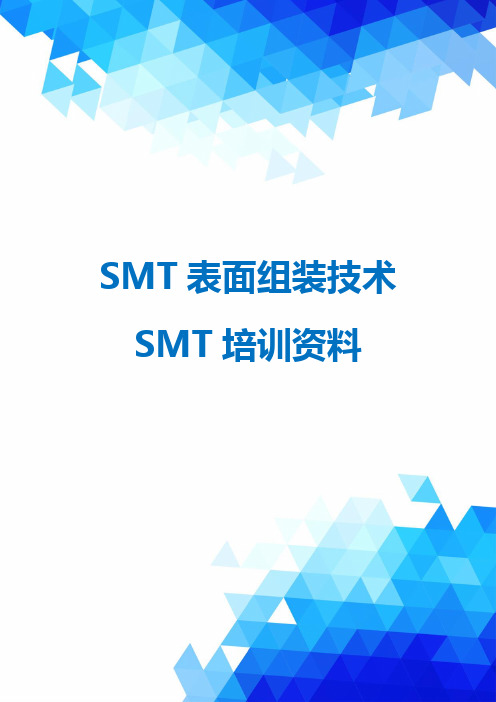
SMT表面组装技术SMT培训资料SMT培训手册上册SMT基础知识目录一、SMT简介二、SMT工艺介绍三、元器件知识四、SMT辅助材料五、SMT质量标准六、安全及防静电常识第一章SMT简介SMT是Surfacemounttechnology的简写,意为表面贴装技术。
亦即是无需对PCB钻插装孔而直接将元器件贴焊到PCB表面规定位置上的装联技术。
SMT的特点从上面的定义上,我们知道SMT是从传统的穿孔插装技术(THT)发展起来的,但又区别于传统的THT。
那么,SMT与THT比较它有什么优点呢?下面就是其最为突出的优点:1.组装密度高、电子产品体积小、重量轻,贴片元件的体积和重量只有传统插装元件的1/10左右,一般采用SMT之后,电子产品体积缩小40%~60%,重量减轻60%~80%。
2.可靠性高、抗振能力强。
焊点缺陷率低。
3.高频特性好。
减少了电磁和射频干扰。
4.易于实现自动化,提高生产效率。
5.降低成本达30%~50%。
节省材料、能源、设备、人力、时间等。
1.电子产品的高性能及更高装联精度要求。
2.电子科技革命势在必行,追逐国际潮流。
SMT有关的技术组成SMT从70年代发展起来,到90年代广泛应用的电子装联技术。
由于其涉及多学科领域,使其在发展初其较为缓慢,随着各学科领域的协调发展,SMT 在90年代得到讯速发展和普及,预计在21世纪SMT将成为电子装联技术的主流。
下面是SMT相关学科技术。
•电子元件、集成电路的设计制造技术•电子产品的电路设计技术•电路板的制造技术•自动贴装设备的设计制造技术•电路装配制造工艺技术•装配制造中使用的辅助材料的开发生产技术第二章SMT工艺介绍SMT工艺名词术语1、表面贴装组件(SMA)(surfacemountassemblys)采用表面贴装技术完成装联的印制板组装件。
2、回流焊(reflowsoldering)通过熔化预先分配到PCB焊盘上的焊膏,实现表面贴装元器件与PCB焊盘的连接。
smt基础知识培训.doc
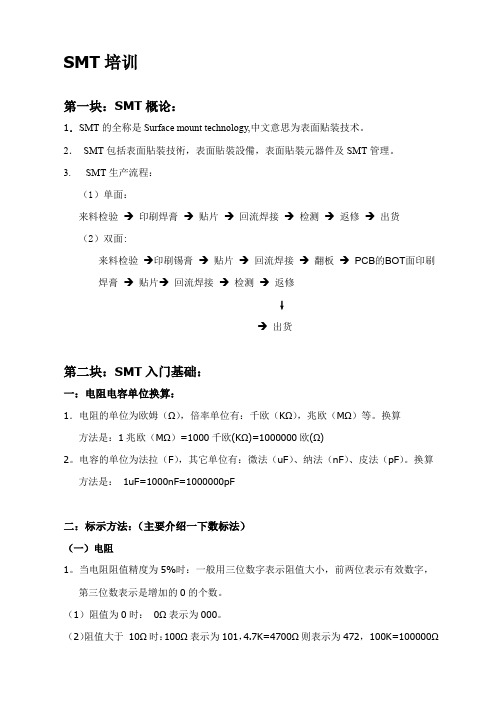
SMT培训第一块:SMT概论:1.SMT的全称是Surface mount technology,中文意思为表面贴装技术。
2.SMT包括表面貼裝技術,表面貼裝設備,表面貼裝元器件及SMT管理。
3. SMT生产流程:(1)单面:来料检验→印刷焊膏→贴片→回流焊接→检测→返修→出货(2)双面:来料检验→印刷锡膏→贴片→回流焊接→翻板→PCB的BOT面印刷焊膏→贴片→回流焊接→检测→返修↓→出货第二块:SMT入门基础:一:电阻电容单位换算:1.电阻的单位为欧姆(Ω),倍率单位有:千欧(KΩ),兆欧(MΩ)等。
换算方法是:1兆欧(MΩ)=1000千欧(KΩ)=1000000欧(Ω)2。
电容的单位为法拉(F),其它单位有:微法(uF)、纳法(nF)、皮法(pF)。
换算方法是:1uF=1000nF=1000000pF二:标示方法:(主要介绍一下数标法)(一)电阻1。
当电阻阻值精度为5%时:一般用三位数字表示阻值大小,前两位表示有效数字,第三位数表示是增加的0的个数。
(1)阻值为0时:0Ω表示为000。
(2)阻值大于10Ω时:100Ω表示为101,4.7K=4700Ω则表示为472,100K=100000Ω则表示104。
(3)阻值小于10Ω时:在两个数字间加字母“R”。
4.7Ω表示为4R7,5.6Ω表示为5R6, 8Ω可先写成8.0Ω的格式,这样就可表示为8R0。
2.当电阻大于0805大小(包括0805大小)且阻值精度为1%时:一般用四位数字表示阻值大小,前三位表示有效数字,第四位数表示是增加的0的个数。
(1)阻值为0时:0Ω表示为0000。
(2)阻值大于10Ω时:100Ω表示为1000,4.7K=4700Ω则表示为4701,100K=100000Ω则表示1003。
(3)阻值小于10Ω时:仍在第二位加字母“R”。
4.7Ω表示为4R70, 5.6Ω表示为5R60, 8Ω可先写成8.00Ω的格式,这样就可表示为8R00。
SMT工艺基础培训

SMT工艺基础培训1. 简介表面贴装技术(Surface Mount Technology,简称SMT)是一种常用于电子设备制造的工艺。
相较于传统的插针式组装技术,SMT工艺具有高效、高质量和成本较低的优势。
本文将介绍SMT工艺的基础知识和流程。
2. SMT工艺的基本原理SMT工艺的基本原理是将电子元器件直接焊接到印刷电路板(Printed Circuit Board,PCB)的表面上,通过高温熔化焊接剂,将元器件牢固地固定在PCB上。
SMT工艺主要由以下几个部分组成:贴装设备、焊接剂、PCB和元器件。
2.1 贴装设备SMT贴装设备主要包括贴片机、回流焊炉和波峰焊机。
贴片机用于自动将元器件精确地放置在PCB上,回流焊炉用于加热焊接剂使其熔化并与PCB和元器件形成可靠的焊点,波峰焊机则用于焊接插针式元器件。
2.2 焊接剂焊接剂是将元器件和PCB连接在一起的关键材料。
常用的焊接剂有无铅焊膏、铅锡焊膏和银浆焊膏。
焊接剂的选择应根据元器件和PCB 的要求来确定。
2.3 PCBPCB是SMT工艺的载体,通过电路设计将元器件连接在一起。
PCB 通常由铜箔、绝缘材料和防护层组成。
PCB的质量和设计对SMT工艺的成功与否至关重要。
2.4 元器件元器件是SMT工艺中的核心部件,包括电阻、电容、集成电路等。
元器件的选择应根据电路设计的要求来确定,同时需要考虑元器件的尺寸和焊接特性。
3. SMT工艺流程SMT工艺流程包括PCB板贴装、焊接和检测三个主要步骤。
3.1 PCB板贴装PCB板贴装是SMT工艺的第一步,主要包括元器件排列、元器件粘贴和元器件定位三个阶段。
在元器件排列阶段,根据电路设计,在PCB上规划元器件的位置。
在元器件粘贴阶段,使用贴片机将元器件精确地放置在PCB上。
在元器件定位阶段,通过视觉系统或传感器来检测并调整元器件的位置,保证其精确度。
3.2 焊接焊接是SMT工艺中的关键步骤,主要包括回流焊接和波峰焊接两种方法。
SMT表面组装技术电子厂SMT人员内部培训资料

SMT表⾯组装技术电⼦⼚SMT⼈员内部培训资料SMT⼈员培训资料第⼀部分:安全⽣产第⼆部分:⼯艺流程第三部分:物料识别第四部分:机器操作第五部份:关键岗位SMT2010-4-1第⼀部分:安全⽣产⼀、机器运⾏中禁⽌⾝体任何部分或其它物品进⼊机器内部⼆、禁⽌在运⾏当中移动机器上安装的物件(如料盘、Feeder)三、如遇险情,⽴刻按下红⾊圆形“紧急停⽌键”四、安全⽣产图⽚(参照已做好的图⽚)MPM印刷机如误按红⾊紧急停⽌按键会切断电源中断⽣产当有⼈在检查机器时不可开机,严禁两⼈同时操作机器出现意外不可在机器运⾏时取出FEEDER ,以防损坏机器机器运⾏时不可把⼿或其它异物伸⼊机器内,以防发⽣意外。
需要更换FEEDER 或检查设备必须先按下F6机器停⽌运⾏机器运⾏中不可以把⼿伸⼊机器内拾取物料或料盘机器运⾏当中不可以取放FEEDER ,以免发⽣碰撞拾取物料或料盘时应先按下STOP 键停机再打开安全门取放FEEDER 时应先按下红⾊STOP 键停机再打开安全门机器运⾏中不可以把⼿伸⼊机器内拾取物料或料盘机器运⾏中不可以把头部伸⼊机器安全门以内观看第⼆部分:⼯艺流程⼀、SMT 定义⼆、流程图第三部分:物料识别⼀、电阻警告:⼩⼼底座夹伤⼿警告:⼩⼼刮⼑错误⽅式:运⾏中不可进⼊机器内取料错误⽅式:运⾏中不可取出飞达清洗、更换刮⼑时应注意刮⼑⼝锋利,当⼼伤⼿及损坏钢⽹1、电阻的符号:R2、电阻的单位:欧姆:Ω千欧:KΩ兆欧:MΩ3、单位换算:⼀兆欧(1MΩ)=⼀百万欧姆(106Ω)1MΩ=1000KΩ=1000000Ω4、电阻丝印的识别。
如:第⼀个数字表⽰电阻值⾸位数第⼆个数字表⽰电阻值的第⼆位数第三个数字表⽰第⼆位数后⾯有⼏个“0”举例:表⽰阻值33KΩ=33000Ω表⽰阻值330Ω表⽰阻值33Ω⼆、电容1、电容的符号:C2、电容的单位:法拉:F微法:MF(NF)⽪法:PF3、单位换算:⼀法拉(1F)=⼀百万微法(106MF)⼀微法(1MF)=103NF=⼀百万⽪法(106PF)1F=106MF=109NF=1012PF三、电感1、电感的符号:L2、电感的单位:亨:H毫亨:mH微亨:nH3、单位换算:⼀亨(1H)=⼀千毫亨(1000mH)⼀毫亨(1mH)=⼀千微亨(1000nH)1H=1000mH=1000000nH四、⼆极管1、⼆极管⽤字母“D”表⽰,有正负极性五、三极管六、球引脚芯⽚元件BGA(有⽅向,标记点与PCB对应)七、⼤芯⽚元件QFP(有⽅向,标记点与PCB对应)⼋、内存ICSOP(有⽅向,标记点与PCB对应)九、烧录ICSOP(有⽅向,标记点与PCB对应)物料的包装⽅式:料盘标签认识:⼗、红胶:起粘连固化作⽤2-12℃保存,使⽤前需室温下解冻4⼩时⼗⼀、锡膏1、有铅锡膏:锡铅混合物,主要成份是合⾦焊料粉,约占锡膏重量的85﹪-90﹪。
SMT基础知识培训资料

SHENZHEN DBK ELECTRONICS CO.,LTD
SMT基础知识培训
迪比科工程部 2014-10-27
SMT基本知识1 smt简介
电子电路表面组装技术(Surface Mount Technology,SMT),称为表面贴装或表面安装技术。
它是一种将无引脚或短引线表面组装元器件(简称 SMC/SMD,中文称片状元器件)安装在印制电路板 (Printed Circuit Board,PCB)的表面或其它基板的 表面上,通过回流焊或浸焊等方法加以焊接组装的电
SMT回流焊技术 回流焊或浸焊等方法加以焊接组装的电路装连技术。
回流焊概述
回流焊又称“再流焊”或“再流焊机”或“回流 炉”(Reflow Oven),它是通过提供一种加热环境,使焊锡膏受热融 化从而让表面贴装元器件和PCB焊盘通过焊锡膏合金可靠地结合在 一起的设备。根据技术的发展分为:气相回流焊、红外回流焊、远 红外回流焊、红外加热风回流焊和全热风回流焊。另外根据焊接特 殊的需要,含有充氮的回流焊炉。目前比较流行和实用的大多是远
电子元件的发展,集成电路(IC)的开发,半导体材料的多元应 用。
电子科技革命势在必行,追逐国际潮流。
SMT基本工艺构成要素 印刷(红胶/锡膏)--> 检测(可选AOI全自动或者目视检测)-->贴 装(先贴小器件后贴大器件:分高速贴片及集成电路贴装)-->检测(可选 AOI 光学/目视检测)--> 焊接(采用热风回流焊进行焊接)--> 检测(可分 AOI 光学检测外观及功能性测试检测)--> 维修(使用工具:焊台及热风
- 1、下载文档前请自行甄别文档内容的完整性,平台不提供额外的编辑、内容补充、找答案等附加服务。
- 2、"仅部分预览"的文档,不可在线预览部分如存在完整性等问题,可反馈申请退款(可完整预览的文档不适用该条件!)。
- 3、如文档侵犯您的权益,请联系客服反馈,我们会尽快为您处理(人工客服工作时间:9:00-18:30)。
SMT表面组装技术SMT基础培训资料第 1 页共28 页SMT基础知识培训教材一、教材内容1.SMT基本概念和组成2.SMT车间环境的要求.3.SMT工艺流程.4.印刷技术:4.1焊锡膏的基础知识.4.2钢网的相关知识.4.3刮刀的相关知识.4.4印刷过程.4.5印刷机的工艺参数调节与影响4.6焊锡膏印刷的缺陷,产生原因及对策.5.贴片技术:5.1贴片机的分类.5.2贴片机的基本结构.5.3贴片机的通用技术参数.5.4工厂现有的贴装过程控制点.5.5工厂现有贴装过程中出现的主要问题,产生原因及对策.5.6工厂现有的机器维护保养工作.6.回流技术:6.1回流炉的分类.6.2GS-800热风回流炉的技术参数.6.3GS-800热风回流炉各加热区温度设定参考表.6.4GS-800回流炉故障分析与排除对策.6.5GS-800保养周期与内容.6.6SMT回流后常见的质量缺陷及解决方法.6.7SMT炉后的质量控制点7.静电相关知识。
《SMT基础知识培训教材书》二.目的为SMT相关人员对SMT的基础知识有所了解。
适用范围该指导书适用于SMT车间以及SMT相关的人员。
四.工具和仪器五术语和定义六.部门职责七.流程图八.教材内容1.SMT基本概念和组成:1.1SMT基本概念SMT是英文:SurfaceMountingTechnology的简称,意思是表面贴装技术.1.2SMT的组成总的来说:SMT 包括表面贴装技术,表面贴装设备,表面贴装元器件及SMT 管理.2.SMT 车间环境的要求2.1SMT 车间的温度:20度---28度,预警值:22度---26度 2.2SMT 车间的湿度:35%---60%,预警值:40%---55%2.3所有设备,工作区,周转和存放箱都需要是防静电的,车间人员必须着防静电衣帽. 3.SMT 工艺流程: OK NO OK NONOOKOKOKNONO OKNOOK4.印刷技术:4.1焊锡膏(SOLDERPASTE)的基础知识4.1.1焊锡膏是将焊料粉末与具有助焊功能的糊状焊剂混合而成的一种浆料,通常焊料粉末占90%左右,其余是化学成分.4.1.2我们把能随意改变形态或任意分割的物体称为流体,研究流体受外力而引起形变与流动行为规律和特征的科学称为流变学.但在工程中则用黏度这一概念来表征流体黏度性的大小.4.1.3焊锡膏的流变行为焊锡膏中混有一定量的触变剂,具有假塑性流体性质.焊锡膏在印刷时,受到刮刀的推力作用,其黏度下降,当到达摸板窗口时,黏度达到最低,故能顺利通过窗口沉降到PCB的焊盘上,随着外力的停止,焊锡膏黏度又迅速回升,这样就不会出现印刷图形的塌落和漫流,得到良好的印刷效果.4.1.4影响焊锡膏黏度的因素4.1.4.1焊料粉末含量对黏度的影响:焊锡膏中焊料粉末的增加引起黏度的增加. 4.1.4.2焊料粉末粒度对黏度的影响:焊料粉末粒度增大时黏度会降低.4.1.4.3温度对焊锡膏黏度的影响:温度升高黏度下降.印刷的最佳环境温度为23+/-3度.4.1.4.4剪切速率对焊锡膏黏度的影响:剪切速率增加黏度下降.黏度黏度黏度粉含量粒度温度4.1.5焊锡膏的检验项目4.1.6SMT工艺过程对焊锡膏的技术要求4.2钢网(STENCILS)的相关知识4.2.1钢网的结构一般其外框是铸铝框架,中心是金属模板,框架与模板之间依靠丝网相连接,呈”刚—柔---刚”结构.4.2.2钢网的制造方法4.2.3目前我们对新来钢网的检验项目4.2.3.1钢网的张力:使用张力计测量钢网四个角和中心五个位置,张力应大于30N/CM.4.2.3..2钢网的外观检查:框架,模板,窗口,MARK等项目.4.2.3.3钢网的实际印刷效果的检查.4.3刮刀的相关知识4.3.1刮刀按制作形状可分为菱形和拖尾巴两种;从制作材料上可分为橡胶(聚胺酯)和金属刮刀两类.4.3.2目前我们使用的全部是金属刮刀,金属刮刀具有以下优点:从较大,较深的窗口到超细间距的印刷均具有优异的一致性;刮刀寿命长,无需修正;印刷时没有焊料的凹陷和高低起伏现象,大大减少不良.4.3.3目前我们使用有三种长度的刮刀:300MM,350MM,400MM.在使用过程中应该按照PCB板的长度选择合适的刮刀.刮刀的两边挡板不能调的太低,容易损坏模板.4.3.4刮刀用完后要进行清洁和检查,在使用前也要对刮刀进行检查.4.4印刷过程4.4.1印刷焊锡膏的工艺流程:焊锡膏的准备支撑片设定和钢网的安装调节参数印刷焊锡膏检查质量结束并清洗钢网4.4.1.1焊锡膏的准备从冰箱中取出检查标签的有效期,填写好标签上相关的时间,在室温下回温4H,再拿出来用锡膏摇均器摇匀锡膏,目前我们使用摇匀器摇3MIN-4MIN。
4.4.1.2支撑片设定和钢网的安装根据线体实际要生产的产品型号选择对应的模板进行支撑片的设定,并作好检查. 参照产品型号选择相应的钢网,并对钢网进行检查:主要包括钢网的张力,清洁,有无破损等,如OK则可以按照机器的操作要求将钢网放入到机器里.4.4.1.3调节参数严格按照参数设定表对相关的参数进行检查和修改,主要包括印刷压力,印刷速度,脱模速度和距离,清洗次数设定等参数4.4.1.4印刷锡膏参数设定OK后,按照DEK作业指导书添加锡膏,进行机器操作,印刷锡膏.4.4.1.5检查质量在机器刚开始印刷的前几片一定要检查印刷效果,是否有连锡,少锡等不良现象;还测量锡膏的厚度,是否在6.8MIL—7.8MIL之间.在正常生产后每隔一个小时要抽验10片,检查其质量并作好记录;每隔2小时要测量2片锡膏的印刷厚度.在这些过程中如果有发现不良超出标准就要立即通知相应的技术员,要求其改善.4.4.1.6结束并清洗钢网生产制令结束后要及时清洗钢网和刮刀并检查,技术员要确认效果后在放入相应的位置.4.5印刷机的工艺参数的调节与影响4.5.1刮刀的速度刮刀的速度和锡膏的黏度有很大的关系,刮刀的速度越慢,锡膏的黏度越大;同样,刮刀的速度越快,锡膏的黏度就越小.调节这个参数要参照锡膏的成分和PCB元件的密度以及最小元件尺寸等相关参数.目前我们一般选择在30—65MM/S.4.5.2刮刀的压力刮刀的压力对印刷影响很大,压力太大会导致锡膏印的很薄.目前我们一般都设定在8KG左右.理想的刮刀速度与压力应该是正好把锡膏从钢板表面刮干净,刮刀的速度与压力也存在一定的转换关系,即降低刮刀速度等于提高刮刀的压力,提高了刮刀速度等于降低刮刀的压力.4.5.3刮刀的宽度如果刮刀相对于PCB过宽,那么就需要更大的压力,更多的锡膏参与其工作,因而会造成锡膏的浪费.一般刮刀的宽度为PCB长度(印刷方向)加上50MM左右为最佳,并要保证刮刀头落在金属模板上.4.5.4印刷间隙印刷间隙是钢板装夹后与PCB之间的距离,关系到印刷后PCB上的留存量,其距离增大,锡膏量增多,一般控制在0—0.07MM4.5.5分离速度锡膏印刷后,钢板离开PCB的瞬时速度即分离速度,是关系到印刷质量的参数,其调节能力也是体现印刷机质量好坏的参数,在精密印刷机中尤其重要,早期印刷机是恒速分离,先进的印刷机其钢板离开锡膏图形时有一个微小的停留过程,以保证获取最佳的印刷图形.4.6焊锡膏印刷的缺陷,产生的原因及对策4.6.1缺陷:刮削(中间凹下去)原因分析:刮刀压力过大,削去部分锡膏.改善对策:调节刮刀的压力4.6.2缺陷:锡膏过量原因分析:刮刀压力过小,多出锡膏.改善对策:调节刮刀压力4.6.3缺陷:拖曳(锡面凸凹不平0原因分析:钢板分离速度过快改善对策:调整钢板的分离速度4.6.4缺陷:连锡原因分析:1)锡膏本身问题2)PCB与钢板的孔对位不准3)印刷机内温度低,黏度上升4)印刷太快会破坏锡膏里面的触变剂,于是锡膏变软改善对策:1)更换锡膏2)调节PCB与钢板的对位3)开启空调,升高温度,降低黏度4)调节印刷速度4.6.5缺陷:锡量不足原因分析:1)印刷压力过大,分离速度过快2)温度过高,溶剂挥发,黏度增加改善对策:1)调节印刷压力和分离速度2)开启空调,降低温度5.贴片技术5.1贴片机的分类5.1.1按速度分类中速贴片机高速贴片机超高速贴片机5.1.2按功能分类高速/超高速贴片机(主要贴一些规则元件)多功能机(主要贴一些不规则元件)5.1.3按贴装方式分类顺序式同时式同时在线式5.1.4按自动化程度分类手动式贴片机全自动化机电一体化贴片机5.2贴片机的基本结构贴片机的结构可分为:机架,PCB传送机构及支撑台,X,Y与Z/θ伺服,定位系统,光学识别系统,贴装头,供料器,传感器和计算机操作软件.5.3贴片机通用的技术参数5.4工厂现有的贴装过程控制点5.4.1SMT贴装目前主要有两个控制点:5.4.1.1机器的抛料控制,目前生产线上有一个抛料控制记录表用来控制和跟踪机器的运行状况.5.4.1.2机器的贴装质量控制,目前生产上有一个贴片质量控制记录表用来控制和跟踪机器的运行状况.5.5工厂现有的贴片过程中主要的问题,产生原因及对策5.5.1在贴片过程中显示料带浮起的错误(Tapefloat)5.5.1.1原因分析及相应简单的对策:5.5.1.1.1根据错误信息查看相应Table和料站的feeder前压盖是否到位;5.5.1.1.2料带是否有散落或是段落在感应区域;5.5.1.1.3检查机器内部有无其他异物并排除;5.5.1.1.4检查料带浮起感应器是否正常工作。
5.5.2元件贴装时飞件5.5.2.1原因分析及相应简单的对策:5.5.2.1.1检查吸嘴是否堵塞或是或是表面不平,造成元件脱落。
若是则更换吸嘴;5.5.2.1.2检查元件有无残缺或不符合标准。
在确认非吸取压力过大造成的基础上向供应商或是厂商反馈;5.5.2.1.3.检查Supportpin高度是否一致,造成PCB弯曲顶起。
重新设置Supportpin;5.5.2.1.4.检查程序设定元件厚度是否正确。
有问题按照正常规定值来设定;5.5.2.1.5.检查有无元件或其他异物残留于传送带或基板上造成PCB不水平。
;5.5.2.1.6.检查机器所设定的贴片高度是否合理,太低(贴装压力过大,致使元件弹飞);5.5.2.1.7.检查锡膏的黏度变化情况,锡膏黏性不足,元件在PCB板的传输过程中掉落;5.5.2.1.8.检查机器贴装元件所需的真空破坏压是否在允许范围内。
若是则需要逐一检查各段气路的通畅情况;5.5.3贴装时元件整体偏移5.5.3.1原因分析及相应简单的对策:5.5.3.1.1.检查是否按照正确的PCB流向放置PCB;5.5.3.1.2检查PCB版本是否与程序设定一致;5.5.4.PCB在传输过程中进板不到位5.5.4.1原因分析及相应简单的对策:5.5.4.1.1.检查是否是传送带有油污导致;5.5.4.1.2.检查Board处是否有异物影响停板装置正常动作;5.5.4.1.3.检查PCB板边是否有赃物(锡珠)是否符合标准。