电池片检验作业指导书
电池片的检验
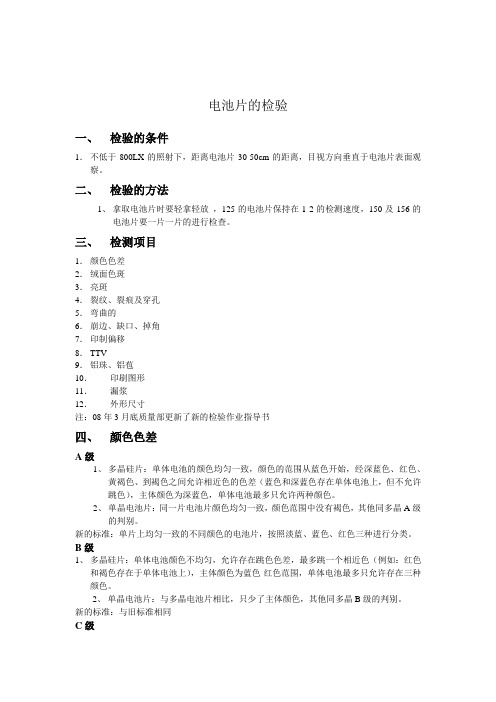
电池片的检验一、检验的条件1.不低于800LX的照射下,距离电池片30-50cm的距离,目视方向垂直于电池片表面观察。
二、检验的方法1、拿取电池片时要轻拿轻放,125的电池片保持在1-2的检测速度,150及156的电池片要一片一片的进行检查。
三、检测项目1.颜色色差2.绒面色斑3.亮斑4.裂纹、裂痕及穿孔5.弯曲的6.崩边、缺口、掉角7.印制偏移8.TTV9.铝珠、铝苞10.印刷图形11.漏浆12.外形尺寸注:08年3月底质量部更新了新的检验作业指导书四、颜色色差A级1、多晶硅片:单体电池的颜色均匀一致,颜色的范围从蓝色开始,经深蓝色、红色、黄褐色、到褐色之间允许相近色的色差(蓝色和深蓝色存在单体电池上,但不允许跳色),主体颜色为深蓝色,单体电池最多只允许两种颜色。
2、单晶电池片:同一片电池片颜色均匀一致,颜色范围中没有褐色,其他同多晶A级的判别。
新的标准:单片上均匀一致的不同颜色的电池片,按照淡蓝、蓝色、红色三种进行分类。
B级1、多晶硅片:单体电池颜色不均匀,允许存在跳色色差,最多跳一个相近色(例如:红色和褐色存在于单体电池上),主体颜色为蓝色-红色范围,单体电池最多只允许存在三种颜色。
2、单晶电池片:与多晶电池片相比,只少了主体颜色,其他同多晶B级的判别。
新的标准:与旧标准相同C级1.多晶硅片:同一片电池允许颜色不均匀(蓝色-深蓝色-红色-黄褐色-褐色)允许存在跳色色差,同以电池片上可以有≥2个相近色。
2.单晶电池片:与多晶电池片相比,颜色范围中少了褐色,其余同多晶C级的判别。
新的标准:与旧标准相同注:当单片上为均匀一致得到不同颜色,判为A级,但需按照淡蓝、蓝色、红色三种进行单测单包。
五、绒面色斑(水痕印、未制绒、未镀膜、手指印、斑点等)A级变更前:允许有轻微缺陷,缺陷部分的总面积不超过电池片总面积的10%,个数不超过3个。
A级暂定变更后:把绒面色斑分成两种类型:发白色斑和淡蓝色斑(1)发白色斑由于存在蓝色到白色的跳色,故A级片绒面色斑中决不允许有发白色斑,缺陷总面积占电池片总面积的0—30%,个数不超过5个,符合此标准的均判为B级。
电池检测系统作业指导书
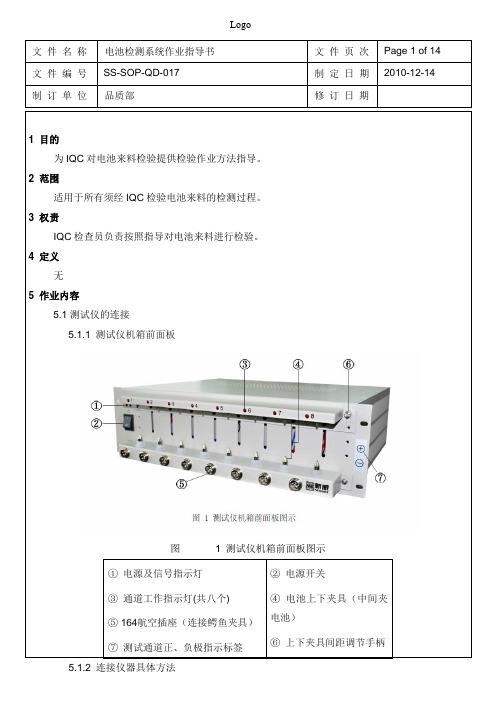
图 1 测试仪机箱前面板图示①电源及信号指示灯③通道工作指示灯(共八个) ②电源开关④电池上下夹具(中间夹5.1.2 连接仪器具体方法按上图一、图二、图三所示连接电脑。
按图四、图五连接电源,连接后打开power键,确认连接正常。
(如图六所示5.1.3.鳄鱼夹具(上图所示):图10 Windows 系统界面下启动TC53图示5.2.2在Windows系统桌面上双击“TC53”快捷方式图标启动软件;或在桌面上直接双击右图标启动软件。
是下凹显示的,表示该通道处于非测试状态;5.2.5 通道的模拟电池显示5.2.7工步设置窗口介绍5.2.7.1在工步设置栏里,用户可以设置测试流程,同时还可设置“数据记录条件“安全保护”等限制条件。
工步类型包括恒流充电、恒流放电、恒压充电、恒功率放电、恒阻放电、恒流恒压充电、搁置、暂停、循环、停止共十种,工停止选定待停止的通道→单击“右键”→选择菜单“停止”,即停止通道运行。
注意:若某些通道在“停止”菜单变灰,则表示这些通道没有工作。
“停止”命令只允许针对正在工作的通道进行接续用户可对已进入“停止”(强制停止或掉电停止)状态和“保护”状态的通道恢复原来未完成的测试工作,保证测试数据的完整性。
要执行接续操作,请:选定待执行“接续”操作的目标通道;迁移“迁移”功能是将当前通道的测试流程及断点信息迁移到目标通道。
重置工步若用户在测试过程中,需要修改正在执行的工步文件时,可使用此功能。
“重置工步备份设置备份设置功能可指定测试数据的备份目录、文件名及备份方式。
2.选择文件命名方式,若选择“自定义文件名称”,则需输入文件名;。
电池片的检验
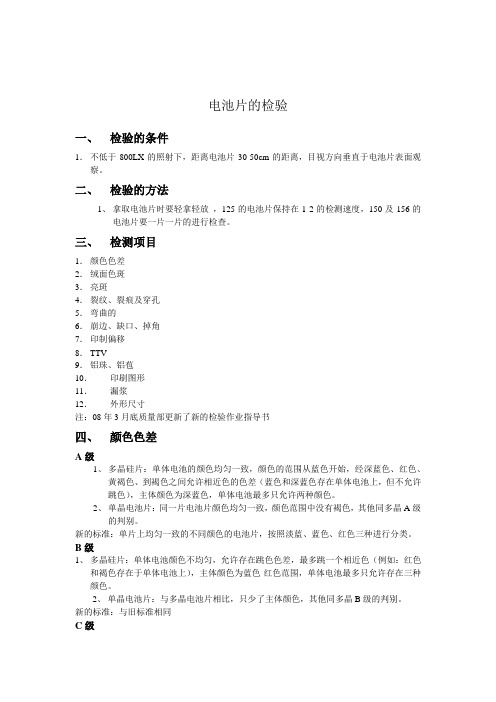
电池片的检验一、检验的条件1.不低于800LX的照射下,距离电池片30-50cm的距离,目视方向垂直于电池片表面观察。
二、检验的方法1、拿取电池片时要轻拿轻放,125的电池片保持在1-2的检测速度,150及156的电池片要一片一片的进行检查。
三、检测项目1.颜色色差2.绒面色斑3.亮斑4.裂纹、裂痕及穿孔5.弯曲的6.崩边、缺口、掉角7.印制偏移8.TTV9.铝珠、铝苞10.印刷图形11.漏浆12.外形尺寸注:08年3月底质量部更新了新的检验作业指导书四、颜色色差A级1、多晶硅片:单体电池的颜色均匀一致,颜色的范围从蓝色开始,经深蓝色、红色、黄褐色、到褐色之间允许相近色的色差(蓝色和深蓝色存在单体电池上,但不允许跳色),主体颜色为深蓝色,单体电池最多只允许两种颜色。
2、单晶电池片:同一片电池片颜色均匀一致,颜色范围中没有褐色,其他同多晶A级的判别。
新的标准:单片上均匀一致的不同颜色的电池片,按照淡蓝、蓝色、红色三种进行分类。
B级1、多晶硅片:单体电池颜色不均匀,允许存在跳色色差,最多跳一个相近色(例如:红色和褐色存在于单体电池上),主体颜色为蓝色-红色范围,单体电池最多只允许存在三种颜色。
2、单晶电池片:与多晶电池片相比,只少了主体颜色,其他同多晶B级的判别。
新的标准:与旧标准相同C级1.多晶硅片:同一片电池允许颜色不均匀(蓝色-深蓝色-红色-黄褐色-褐色)允许存在跳色色差,同以电池片上可以有≥2个相近色。
2.单晶电池片:与多晶电池片相比,颜色范围中少了褐色,其余同多晶C级的判别。
新的标准:与旧标准相同注:当单片上为均匀一致得到不同颜色,判为A级,但需按照淡蓝、蓝色、红色三种进行单测单包。
五、绒面色斑(水痕印、未制绒、未镀膜、手指印、斑点等)A级变更前:允许有轻微缺陷,缺陷部分的总面积不超过电池片总面积的10%,个数不超过3个。
A级暂定变更后:把绒面色斑分成两种类型:发白色斑和淡蓝色斑(1)发白色斑由于存在蓝色到白色的跳色,故A级片绒面色斑中决不允许有发白色斑,缺陷总面积占电池片总面积的0—30%,个数不超过5个,符合此标准的均判为B级。
电池片检验作业指导书.docx

电池片检验作业指导书1.目的本标准规定了单晶硅/多晶硅电池片来料的检验方法,通过检验确保单晶硅/ 多晶硅电池片的各项性能指标符合要求。
2.适用范围适用于本公司品质部对外购多晶硅/单晶硅电池片的来料检验。
3 •职责3.1技术工艺部工程师负责制定多晶硅/单晶硅电池片来料交付要求。
3.2品质部工程师负责制订单晶硅/多晶硅料电池片来料检验标准。
3.3品质部IQC、实验员负责多晶硅/单晶硅电池片来料质量控制点的质量控制4.工作准备4.1测试工具准备:游标卡尺、千分尺或高度计、量角规、塞尺、显微镜、电池片分选仪。
4.2检验记录:《原材料检验报告》、《检验记录表》、检验标贴。
5.检验标准5.1抽样标准:根据GB/T2828. H2003的规定,采用正常检验一次抽样方案;任何一项测试不合格,即判定批次检验不合格。
5.2检验项目和耍求:说明:外购电池片参照以下标准,我司电池片参照《好利光能科技有限公司太阳能电池片的采购标准》进行检验凡具有下列情况Z—者,必须进行例行检验:(1)更换新的电池片供应商时。
(2)电池片供应商的产品生产工艺有较大变动,可能影响产晶性能时。
(3)买卖双方任何一方认为有必要进行检验吋。
6.检验方法6.1包装(1)每包电池片均有独立的密封性包装(每包不得超过100片),每包上下两面分别用软质垫间隔,外包装有防震缓冲垫且包有PV套膜(2)装放电池片的外箱无明显的破损,且无潮湿现象。
(3)包装盒上应注明产品名称,生产厂家,产品型号,太阳能转换效率分档,生产日期,批号;外包装上应注明:易碎物品、方向向上、防潮、防震等包装运输标注。
6.2外观(1)减反射膜色泽均匀一致,同一片不能有色差,目视总面积V2cm2(2)无明显的花斑、水纹、白点、划痕和污垢和指纹印,目视总面积V2cm2(3)不得有v形缺口、裂纹;(4)崩边:目测电池片有无崩边,用游标卡尺测量崩边的尺寸,数目W2, 深度WO. 5mm,长度Wl・0mm(5)翘曲:正放电池片于测式平台上,检查电池片与平台接触是否良好,用塞尺塞入接触间隙,测量电池的翘曲度;(6)正面漏浆:目视检查是否要求,必要时用游标卡尺测量漏浆面积,数目W2,总面积<1. 5mm2(7)背面铝浆缺损:目视检查是否要求,必要时用游标卡尺测量缺损面积,无尖锐突起,圆形突起手感不明显,£L总面积小丁• 20mm2;漏印重印面积<lcm26. 3外形尺寸(1)长:平行主栅线方向,用游标卡尺测量电池片两条平行边的距离,公差±0. 5 mm;(2 )宽:垂直主栅线方向,用游标卡尺测量电池片两条平行边的距离,公差±0. 5 mm;(3)厚度:用高度计测量电池片每边的中点,测量结果的算术平均值即为厚度值,2180um6. 4电性能测试(1)功率测试:整批抽测单片功率需80%为大于标称功率,单片功率三标称功率*97%测试步骤:比用手轻轻的打开标片盒,轻轻的取出156多晶(125单晶)标准片.(如图1)b ・从侧面轻轻放置在单片测试仪上,放下时要平行滑落(如图2)c ・对放置的标准片进行栅线调整, 按照指示观察是否对齐放置(待测片必须完全与铜板完全接触)。
电池片外观判定指导书

深圳XX有限公司
缺角电池片品质判定指导书
缺角范围
使用范围
允许使用数 量
样品: 不允许使用
0片
折叠板:单片板上允许出现1片,
1:单晶缺角宽 一套折叠板上只能接收2片此范围的缺角,
2片
度≤1.0mm 但不允许2片同时存在200*200mm的范围内
深度≤1.0mm
常规组件:小于100W的组件:单片板上可以 接收数量少于2片,大于100W(含100W)的 组件,单片板上可以接收数量少于4片(但 不允许2片缺角同时出现在200*200mm的范围 内)
2-4片(黑色 背板的数量 可以放宽2-3
片)
深
度
2:单晶缺角范 围深度超过栅线 边缘
此类缺角不能做整片使用,需要进行分类 后,进行切割使用
0片
3:单晶缺角范 围深度未超过栅 线边缘,宽度小 于10mm以内的
此类缺角在使用前划片房要做背后贴胶纸用 黑色油性笔做修补工作,拉线各工序发现类 似的电池片片
备注:切割电池片所造成的切割缺口或是锯齿状现象,其参照标准还是依据上述单晶第1条款执行,对 于造成切割电池片缺口或是锯齿状的异常现象,划片房要及时调整机器的运行,监督操作工人的掰片手 法,严格控制此类不良现象的发生和流入到生产线上,鉴于我司目前还没有合适的方式来弥补多晶电池 片缺角的颜色问题,所以要求划片房在选配电池片时一定要对多晶电池片进行仔细把控,可以对出现崩 边缺角的多晶电池片采用集中切边的方式来控制,保证组件的外观。
制表:
审核:
XX有限公司
片品质判定指导书
4:单晶缺角范 围深度未超过栅 此类电池片则要集中同一方向,采用切边的 线边缘,宽度大 方式进行处理后方可以流入生产线 于10mm以上的
电池检验作业指导书

一、目的:为确保供应商来料品质符合我司及客户要求,以确保产品品质,使产线标准统一,产线顺利运转。
二、适用范围:本检验规范适用于本公司所有采购手机电池的检验作业。
三、应用文件:
MIL-STD-105E II 抽样计划表、产品承认书及工程样品、工程图纸。
四、检验工具:标配整机、万用表、游标卡尺等。
五、检验标准:
采用MIL-STD-105E表,正常检验II、单次抽样计划,AQL CR:0MA:0.65 及MI:1.5 其他可靠性及破坏性的特性测试一般取3-5PCS。
取样方式:采取分散取样方式,5箱以内,每箱都应取样;超出10箱,按(5+总箱数÷5)箱进行分散取样。
注:有关抽样标准或判定标准可视客户的要求做修订。
六、检验条件:
距离:人眼与被测物表面的距离为300~350MM。
时间:每条线检查时间不超过10S。
位置:检视面与桌面成45°;上下左右转动15°。
照明:100W冷白荧光灯,光源距被测物表面300MM ,(500~550LUX)。
检验员视力:裸视或矫正视力在1.0以上且无色盲
七、检验内容:。
电池片外观检验作业指导书
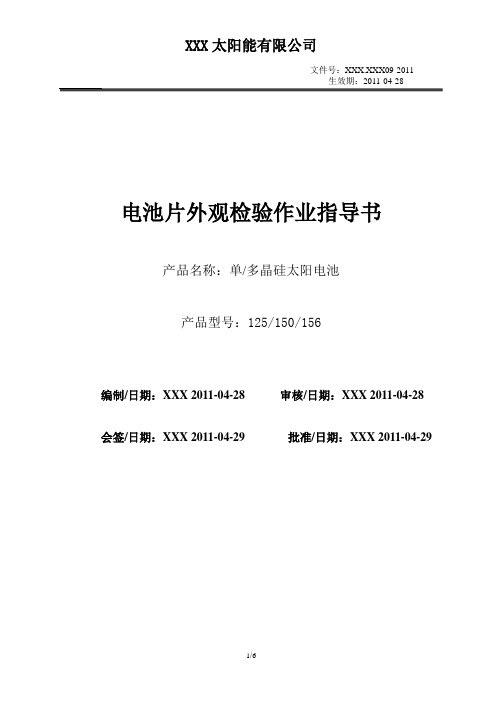
在指定位置,并做好缺陷类型及数量标识。
注意:标识不要直接贴在电池片上。
检查角度
检查位置
旋转方向
崩边电池片
<a> 5. 将电池片旋转,分别检查电池片的每一边,方法同上。 6. 将电池片平放在操作台珍珠棉上,每次取一片,从正、反两面检查电池片。拿取
方法:双手大拇指轻轻捏住电池片一面主栅线位置,其他四指托住电池片的另一 面(如下图 b)。 注意:翻动电池片时,拿住主栅线银浆部分再将其翻转过来,如下图 c。
评审区。 8. 分选结束后,需要将不合格的电池片进行记录(供应商、规格、档次、缺陷类型
和缺陷片数)。
9. 将合格电池片按照供应商、规格、档次进行区分,按照原包装分别包装
参考《电池片取放规范》)。
注意:电池片不可以隔夜放置,当天不投入生产的电池片或缺陷片要包装
好入库存储。
附:电池片缺陷(详见附录) 蓝色面:色差、指纹印、主栅线银浆脱落、有条纹或断栅线、缺银浆、少栅线。 银色面:背面银浆发黄、发黑、背面起泡、锡珠、银浆分布不均或银浆过多、 铝层不完 整。
1/7
XXX 太阳能有限公司
文件号:XXX.XXX09-2011 生效期:2011-04-28
物料规格:待检验电池片()
操作环境:光照强度≥1000Lux;
作业前准备工作
1. 清洁桌面,在桌面上垫上珍珠棉;
2. 划分好合格电池片放置区和不合格电池片放置区;
3. 按照要求戴好手指套。
作业程序:
1. 按照工作要求,将电池片从仓库领出。
2. 打开包装盒,按照《电池片取放规范》,将电池片取出并放好;
3. 以 20 片/1 次为限,对电池片进行分选;
4. 双手捏住电池片主栅线位置,将电池片竖立在操作台上(如下图 a),从图示位置
电池片检验标准指导书
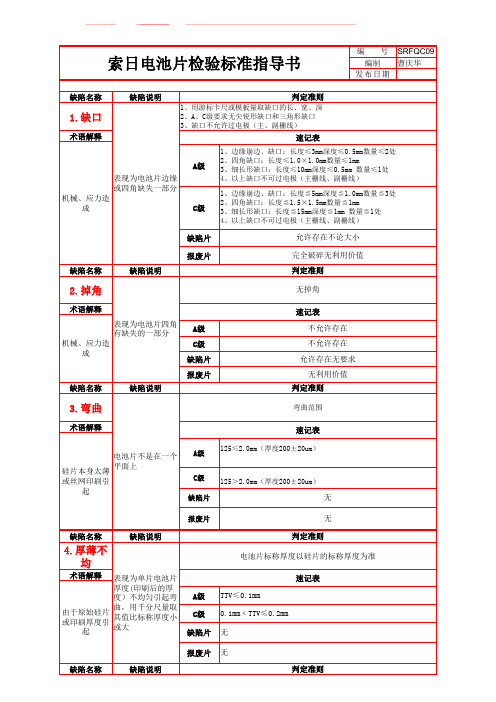
准备 确定
机台运行
索日电池片检验标准指导书
缺陷名称 缺陷说明 判定准则
1、用游标卡尺或模板量取缺口的长、宽、深 2、A、C级要求无尖锐形缺口和三角形缺口 3、缺口不允许过电极(主、副栅线)
编 号 SRFQC09 编制 曹庆华 发布日期
1.缺口
术语解释
速记表
1、边缘崩边、缺口:长度≤3mm深度≤0.5mm数量≤2处 2、四角缺口:长度≤1.0×1.0mm数量≤1mm 3、细长形缺口:长度≤10mm深度≤0.5mm 数量≤1处 4、以上缺口不可过电极(主栅线、副栅线) 1、边缘崩边、缺口:长度≦5mm深度≦1.0mm数量≦3处 2、四角缺口:长度≦1.5×1.5mm数量≦1mm 3、细长形缺口:长度≦15mm深度≦1mm 数量≦1处 4、以上缺口不可过电极(主栅线、副栅线)
扭曲<正常位置的0.3mm 扭曲>正常位置的0.3mm 超出C级要求 无利用价值的
编 号 SRFQC09 编制 曹庆华 发布日期
判定准则 明显度及所占面积 速记表
24.雨点
术语解释 表现为电池片表面 有类雨点状色斑 制绒不良造成 A级 C级 缺陷片 报废片 缺陷名称 缺陷说明
1、不明显,颜色没有偏离主题颜色 2、面积<电池片面积的30% 1、较明显,颜色已偏离主题颜色 2、面积>电池片面积的30% 超出C级要求 无利用价值的
判定准则 用模版进行量取印刷图形偏移正常位置的范围 速记表
16.印刷偏 移
术语解释 表现为正面电极图 形整体偏离正常位 置 A级 C级 缺陷片 报废片 缺陷名称 缺陷说明
偏差≤1.0mm 角度偏差≤0.5° 形不能超出电池片边缘 偏差>1.0mm 角度偏差>0.5° 极图形不能超出电池片边缘 电极图形超出C级片的要求 无
- 1、下载文档前请自行甄别文档内容的完整性,平台不提供额外的编辑、内容补充、找答案等附加服务。
- 2、"仅部分预览"的文档,不可在线预览部分如存在完整性等问题,可反馈申请退款(可完整预览的文档不适用该条件!)。
- 3、如文档侵犯您的权益,请联系客服反馈,我们会尽快为您处理(人工客服工作时间:9:00-18:30)。
电池片检验作业指导书
1.目的
本标准规定了单晶硅/多晶硅电池片来料的检验方法,通过检验确保单晶硅/多晶硅电池片的各项性能指标符合要求。
2.适用范围
适用于本公司品质部对外购多晶硅/单晶硅电池片的来料检验。
3.职责
3.1技术工艺部工程师负责制定多晶硅/单晶硅电池片来料交付要求。
3.2品质部工程师负责制订单晶硅/多晶硅料电池片来料检验标准。
3.3 品质部IQC、实验员负责多晶硅/单晶硅电池片来料质量控制点的质量控制
4. 工作准备
4.1测试工具准备:游标卡尺、千分尺或高度计、量角规、塞尺、显微镜、电池片分选仪。
4.2检验记录:《原材料检验报告》、《检验记录表》、检验标贴。
5. 检验标准
5.1抽样标准:根据GB/T2828.1-2003的规定,采用正常检验一次抽样方案;任何一项测试不合格,即判定批次检验不合格。
5.2检验项目和要求:
说明:外购电池片参照以下标准,我司电池片参照《好利光能科技有限公司太阳能电池片的采购标准》进行检验。