可靠性分析技术(FMEA)
FMEA是一种可靠性设计的重要方法

FMEA是一种可靠性设计的重要方法FMEA(Failure Mode and Effects Analysis,失效模式及影响分析)是一种可靠性设计的重要方法。
它通过系统性地分析可能的失效模式与其潜在影响,旨在识别并消除或减轻潜在失效的风险,从而提高产品、系统或过程的可靠性。
FMEA的基本原理是先通过分析系统的设计、功能、构造、工作原理等方面,确定可能的失效模式,再分析各失效模式的潜在影响。
FMEA通常包含以下步骤:1.确定FMEA的范围和目的:明确分析的范围和要达到的目标,例如分析一些特定产品的可靠性问题、分析一些特定工作流程的潜在风险等。
明确目的有助于更好地确定分析的重点和方向。
2.组建FMEA团队:FMEA需要多学科的团队参与,例如设计、工程、质量等部门的成员。
他们应具备相应领域的专业知识和经验,能够全面理解和分析系统,从不同角度提出有益意见。
3.收集系统信息:收集系统的设计资料、技术规范、产品手册、相关数据等。
了解系统的设计特点、工作原理、功能要求以及与其他系统的接口等信息。
4.确定分析的对象:确定要分析的系统、产品或过程,并明确分析的边界和范围。
可以将系统划分为不同的子系统或模块进行分析。
5.识别失效模式:通过头脑风暴、故障树分析、过程流程图等方法,系统地识别可能的失效模式。
对于每个失效模式,需要描述其性质、影响范围、持续时间、概率等信息。
6.评估失效影响:对每个失效模式进行量化或定性评估,分析其潜在影响。
包括对产品性能、安全性、可靠性、可用性等方面的影响进行评估,并将其与设计要求进行对比。
7.评估风险严重性:根据失效的潜在影响和频率,评估每个失效模式的风险严重性。
通常使用风险矩阵或风险指数来进行评估和排序。
8.提出改进措施:针对风险严重性较高的失效模式,制定改进措施以减轻或消除潜在失效的风险。
这些措施可以包括改进设计、增加冗余、调整工艺流程等。
9.跟踪和监控改进措施:实施改善措施后,需要对其有效性进行跟踪和监控,以确保风险得到控制并持续改进。
FMEA简述

缺陷产品;不需要分拣;需要向供应商提供反馈
触感令人略微感觉不舒服。
1
非常低 没有可觉察到的影响
没有可觉察到的影响或没有影响
没有可觉察到的影响。
注:绿色为公司重点采用的相关评判标准,灰色为不常用标准。
十、第五版FMEA内容——失效原因
· 由小组结合特定的知识和经验来确定 · 失效原因能够直接确定或者通过理解失效的原理来确定
八、第四版FMEA
过程步骤/功能
要求
潜在失效模式
潜在失效影 响
SEV 严重度
分类
潜在失效原因
OCC发生 度
现行过程控制 预防
Plasma清洗
芯片背面 无污染
D/B 焊胶层 芯片背面污染 脱落,电参
失效
8
Plasma能量&时间参 数不恰当 Plasma工艺气压值偏 小或偏大
气体流量偏小
1.限制参数编辑权限,仅工程部负责人有
· 描述失效模式对客户的影响:
- 内部客户(下一个操作/后续操作/操作目标) - 外部客户(下一级/OEM/经销商)政府法律法规
- 产品或产品最终用户/操作者 - 立法机构
要求 四个螺钉
失效模式
影响
最终顾客:座垫松动,有噪音。
少于四个螺钉 制造和装配:由于受影响的部分,因而停止发
运,并进行额外挑选和返工。
1.要求作业员每班检查气罐接口是否漏气 2.气体流量超出范围时,设备自动报警
DET RP 探测度 N
4 64
4 64 2 32
推荐措施 NONE NONE NONE
Action Results/实施结果
职责和目标完 成日期
采取的措施 和有效日期
SE V 严重 度
FMEA分析报告

FMEA分析报告FMEA(Failure Mode and Effects Analysis)是一种系统性的风险评估方法,常用于分析产品或过程中的潜在问题和可能的影响。
这篇报告将介绍FMEA分析的目的,步骤和优势,并通过一个实例进行详细说明。
一、FMEA分析的目的二、FMEA分析的步骤1.确定分析的范围:明确需要分析的产品或过程的范围和目标。
2.收集团队:组建一个多学科的团队,包括设计人员、工程师、生产人员等。
3.识别潜在的故障模式:对产品或过程进行详细审查,识别可能出现的故障模式。
4.评估故障的严重程度:分析每个故障模式可能引发的后果,评估其对产品性能和安全性的影响。
5.评估故障发生的可能性:分析每个故障模式发生的概率或频率,并将其与已有的统计数据或历史记录进行比较。
6.评估故障的检测能力:评估现有的探测和防范措施对于检测和防止故障的效果。
7.计算风险优先级:根据故障的严重程度、发生可能性和检测能力计算每个故障模式的风险优先级,确定应优先处理的故障模式。
8.制定改进措施:根据风险优先级,制定相应的改进措施,减少或消除故障的可能性和后果。
9.实施改进措施:将改进措施应用到产品设计或过程中,确保其有效性和可持续性。
10.监控和追踪效果:通过定期监测和追踪,评估改进措施的效果和持续性,并根据需要进行调整和改进。
三、FMEA分析的优势1.预测潜在问题:通过系统性的分析,FMEA能够预测产品或过程中可能出现的问题,并提前采取措施避免或降低潜在的风险。
2.提高产品质量:通过识别并改进潜在问题,FMEA能够改善产品的质量和可靠性,提高顾客满意度。
3.降低故障率和维修成本:通过消除或减少故障的可能性,FMEA能够降低产品或过程的故障率和维修成本。
4.加强团队协作:FMEA需要一个多学科的团队进行分析和讨论,促进了团队成员之间的协作和沟通。
5.持续改进:FMEA是一个持续改进的过程,通过监测和追踪改进措施的效果,不断优化和改进产品或过程。
FMEA的定义

FMEAFMEA是一种可靠性设计的重要方法。
它实际上是FMA(故障模式分析)和FEA(故障影响分析)的组合。
它对各种可能的风险进行评价、分析,以便在现有技术的基础上消除这些风险或将这些风险减小到可接受的水平。
目录50年代初,美国第一次将FMEA思想用于一种战斗机操作系统的设计分析;60年代中期,FMEA技术正式用于航天工业(Apollo计划);1976年,美国国防部颁布了FMEA的军用标准,但仅限于设计方面。
70年代末,FMEA技术开始进入汽车工业和医疗设备工业。
80年代初,进入微电子工业。
80年代中期,汽车工业开始应用过程FMEA确认其制造过程。
1988年,美国联邦航空局发布咨询通报要求所有航空系统的设计及分析都必须使用FMEA。
1991年,ISO-9000推荐使用FMEA提高产品和过程的设计。
1994年,FMEA又成为QS-9000的认证要求。
编辑本段产品分类概要由于产品故障可能与设计、制造过程、使用、承包商/供应商以及服务有关,因此FMEA又细分为:DFMEA:设计FMEAPFMEA:过程FMEAEFMEA:设备FMEASFMEA:体系FMEA其中设计FMEA和过程FMEA最为常用。
DFMEA:设计FMEA设计FMEA(也记为d-FMEA)应在一个设计概念形成之时或之前开始,并且在产品开发各阶段中,当设计有变化或得到其他信息时及时不断地修改,并在图样加工完成之前结束。
其评价与分析的对象是最终的产品以及每个与之相关的系统、子系统和零部件。
需要注意的是,d-FMEA在体现设计意图的同时还应保证制造或装配能够实现设计意图。
因此,虽然d-FMEA 不是靠过程控制来克服设计中的缺陷,但其可以考虑制造/装配过程中技术的/客观的限制,从而为过程控制提供了良好的基础。
进行d-FMEA有助于:· 设计要求与设计方案的相互权衡;· 制造与装配要求的最初设计;· 提高在设计/开发过程中考虑潜在故障模式及其对系统和产品影响的可能性;· 为制定全面、有效的设计试验计划和开发项目提供更多的信息;· 建立一套改进设计和开发试验的优先控制系统;· 为将来分析研究现场情况、评价设计的更改以及开发更先进的设计提供参考。
什么是FMEA(FMECA)
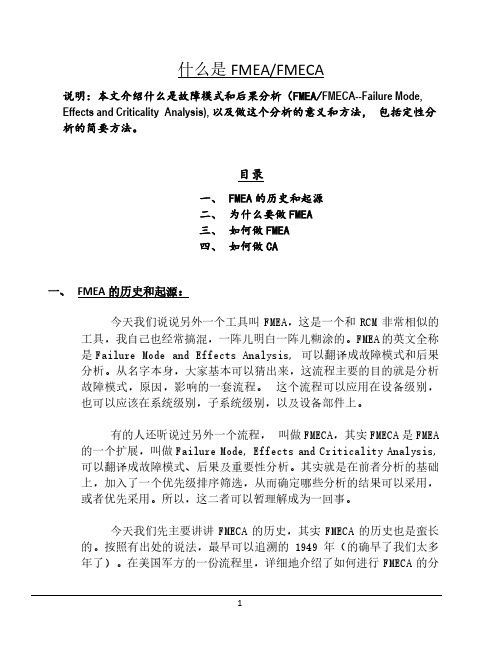
什么是FMEA/FMECA说明:本文介绍什么是故障模式和后果分析(FMEA/FMECA--Failure Mode, Effects and Criticality Analysis), 以及做这个分析的意义和方法,包括定性分析的简要方法。
目录一、FMEA的历史和起源二、为什么要做FMEA三、如何做FMEA四、如何做CA一、FMEA的历史和起源:今天我们说说另外一个工具叫FMEA,这是一个和RCM非常相似的工具,我自己也经常搞混,一阵儿明白一阵儿糊涂的。
FMEA的英文全称是Failure Mode and Effects Analysis, 可以翻译成故障模式和后果分析。
从名字本身,大家基本可以猜出来,这流程主要的目的就是分析故障模式,原因,影响的一套流程。
这个流程可以应用在设备级别,也可以应该在系统级别,子系统级别,以及设备部件上。
有的人还听说过另外一个流程,叫做FMECA,其实FMECA是FMEA 的一个扩展,叫做Failure Mode, Effects and Criticality Analysis,可以翻译成故障模式、后果及重要性分析。
其实就是在前者分析的基础上,加入了一个优先级排序筛选,从而确定哪些分析的结果可以采用,或者优先采用。
所以,这二者可以暂理解成为一回事。
今天我们先主要讲讲FMECA的历史,其实FMECA的历史也是蛮长的。
按照有出处的说法,最早可以追溯的1949年(的确早了我们太多年了)。
在美国军方的一份流程里,详细地介绍了如何进行FMECA的分析,流程编号是MIL-P-1629 (当然,这份流程后来在80年代又进行了修改,编号也变成了MIL-STD-1629A)。
在上世纪60年代初期,美国航空航天局(NASA)曾经大量使用了FMECA流程进行分析。
其中著名的阿波罗计划,维京计划,旅行者计划,麦哲伦计划,伽利略计划以及美国第一个空间站计划,都进行了FMECA分析。
我曾经拜读过1966年NASA编写的阿波罗计划FMECA实施流程,全文共37页,具体的实施方法和现如今没有太大改变。
FMEA在机械设计中的可靠性分析

FMEA在机械设计中的可靠性分析简介在机械设计领域中,可靠性是一个至关重要的指标,决定了产品在使用过程中的稳定性和安全性。
为了评估和提高机械产品的可靠性,工程师们通常会采用FMEA(Failure Mode and Effects Analysis)分析方法。
什么是FMEAFMEA是一种系统性的分析方法,旨在识别产品或系统可能存在的潜在故障模式和故障对系统功能的影响。
通过对潜在故障模式的识别和评估,可以帮助设计团队在设计阶段识别和消除设计缺陷,从而提高产品的可靠性。
FMEA的工作原理FMEA分析通常分为三个关键步骤:识别潜在故障模式、评估潜在故障的影响和严重性、确定并实施改进措施。
在识别潜在故障模式阶段,团队会收集和整理可能的故障模式,包括设备失效、材料损坏、操作错误等。
接着进行评估,根据潜在故障的影响和严重性对它们进行排序,并确定优先处理的故障。
最后,设计团队根据评估结果提出改进和预防措施,避免潜在故障的发生。
FMEA在机械设计中的应用在机械设计中,FMEA的应用可以帮助设计团队避免或减少设计缺陷,降低产品的故障率和维修成本。
通过FMEA分析,设计团队可以识别潜在的故障模式和问题,及早进行改进,确保产品在生产和使用过程中的可靠性和安全性。
例如,在设计一个机械零部件时,可以通过FMEA分析识别可能的故障模式,如材料疲劳、装配不当等,从而改进设计和工艺,提高产品的可靠性。
结论FMEA作为一种重要的分析方法,在机械设计中扮演着关键的角色。
通过FMEA分析,设计团队可以及早发现并解决潜在的故障问题,提高产品的可靠性和安全性。
因此,在机械设计过程中,设计团队应该充分利用FMEA这一工具,从而设计出高质量、可靠性强的机械产品。
FMEA在电子产品可靠性测试中的应用
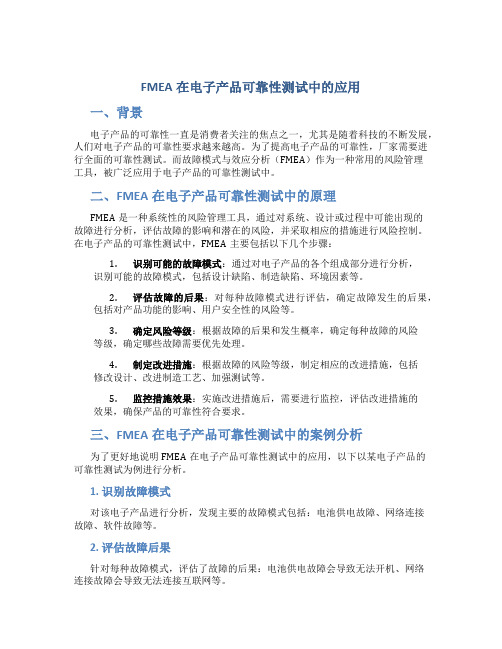
FMEA在电子产品可靠性测试中的应用一、背景电子产品的可靠性一直是消费者关注的焦点之一,尤其是随着科技的不断发展,人们对电子产品的可靠性要求越来越高。
为了提高电子产品的可靠性,厂家需要进行全面的可靠性测试。
而故障模式与效应分析(FMEA)作为一种常用的风险管理工具,被广泛应用于电子产品的可靠性测试中。
二、FMEA在电子产品可靠性测试中的原理FMEA是一种系统性的风险管理工具,通过对系统、设计或过程中可能出现的故障进行分析,评估故障的影响和潜在的风险,并采取相应的措施进行风险控制。
在电子产品的可靠性测试中,FMEA主要包括以下几个步骤:1.识别可能的故障模式:通过对电子产品的各个组成部分进行分析,识别可能的故障模式,包括设计缺陷、制造缺陷、环境因素等。
2.评估故障的后果:对每种故障模式进行评估,确定故障发生的后果,包括对产品功能的影响、用户安全性的风险等。
3.确定风险等级:根据故障的后果和发生概率,确定每种故障的风险等级,确定哪些故障需要优先处理。
4.制定改进措施:根据故障的风险等级,制定相应的改进措施,包括修改设计、改进制造工艺、加强测试等。
5.监控措施效果:实施改进措施后,需要进行监控,评估改进措施的效果,确保产品的可靠性符合要求。
三、FMEA在电子产品可靠性测试中的案例分析为了更好地说明FMEA在电子产品可靠性测试中的应用,以下以某电子产品的可靠性测试为例进行分析。
1. 识别故障模式对该电子产品进行分析,发现主要的故障模式包括:电池供电故障、网络连接故障、软件故障等。
2. 评估故障后果针对每种故障模式,评估了故障的后果:电池供电故障会导致无法开机、网络连接故障会导致无法连接互联网等。
3. 确定风险等级根据故障的后果和发生概率,确定了各种故障的风险等级,并确定了优先处理的故障模式。
4. 制定改进措施针对每种故障模式,制定了相应的改进措施,包括优化电池管理系统、加强网络连接测试等。
5. 监控措施效果实施改进措施后,对产品进行了再次可靠性测试,监控了改进措施的效果,确保电子产品的可靠性得到提升。
FMEA、DFMEA、PFMEA学习资料

FMEA管理模式(Failure Mode and Effect Analysis,失效模式及效应分析)什么是FMEA"FMEA(Failure Mode and Effect Analysis,失效模式和效果分析)是一种用来确定潜在失效模式及其原因的分析方法。
具体来说,通过实行FMEA,可在产品设计或生产工艺真正实现之前发现产品的弱点,可在原形样机阶段或在大批量生产之前确定产品缺陷。
FMEA最早是由美国国家宇航局(NASA)形成的一套分析模式,FMEA是一种实用的解決问题的方法,可适用于许多工程领域,目前世界许多汽车生产商和电子制造服务商(EMS)都已经采用这种模式进行设计和生产过程的管理和监控。
FMEA的具体内容FMEA有三种类型,分別是系统FMEA、设计FMEA和工艺FMEA,1)确定产品需要涉及的技术、能够出现的问题,包括下述各个方面:需要设计的新系统、产品和工艺;对现有设计和工艺的改进;在新的应用中或新的环境下,对以前的设计和工艺的保留使用;形成FMEA团队。
理想的FMEA团队应包括设计、生产、组装、质量控制、可靠性、服务、采购、测试以及供货方等所有有关方面的代表。
2)记录FMEA的序号、日期和更改内容,保持FMEA始终是一个根据实际情況变化的实时现场记录,需要强调的是,FMEA文件必须包括创建和更新的日期。
3) 创建工艺流程图。
工艺流程图应按照事件的顺序和技术流程的要求而制定,实施FMEA需要工艺流程图,一般情況下工艺流程图不要轻易变动。
4)列出所有可能的失效模式、效果和原因、以及对于每一项操作的工艺控制手段:对于工艺流程中的每一项工艺,应确定可能发生的失效模式.如就表面贴装工艺(SMT)而言,涉及的问题可能包括,基于工程经验的焊球控制、焊膏控制、使用的阻焊剂(soldermask)类型、元器件的焊盤图形设计等。
对于每一种失效模式,应列出一种或多种可能的失效影响,例如,焊球可能要影响到产品长期的可靠性,因此在可能的影响方面应该注明。
- 1、下载文档前请自行甄别文档内容的完整性,平台不提供额外的编辑、内容补充、找答案等附加服务。
- 2、"仅部分预览"的文档,不可在线预览部分如存在完整性等问题,可反馈申请退款(可完整预览的文档不适用该条件!)。
- 3、如文档侵犯您的权益,请联系客服反馈,我们会尽快为您处理(人工客服工作时间:9:00-18:30)。
控制、风险减小的任务列表
•系统工程师 •可靠性工程师 •项目组长 •研发工程师
DVP 测试验证 Control Plan
FMEA分析思路
当前是怎么设计的 ?
常规的设计思路
可能会发生哪些问题 ?
过去发生过什 设计准则 么问题? 实际上 设计经验 还会发生什么 冗余设计 这就是 问题? FMEA ! 工程计算 经验积累 试验确认
FMEA=填表 设计人员不了 解FMEA 不合适的时间 开展FMEA
第30页
解决方案
辅助分析工具
故障模式定义不明确 故障原因不全面
第31页
功能图
用于描述各零件产品与功能的对应关系
第32页
边界图
用于描述分析的边界范围和接口,说明各组件、零部件 之间的关系
E D B A C G
H
F
第33页
P图
P图是用于确定和描述噪声控制因素和错误状态的稳健 性(Robustness)工具。
可靠性分析技术—— FMEA
咨询总监 王玮 2014年6月
内容安排
1
FMEA概述 DFMEA工程实施 DFMEA实施难点与解决方案
2 3 4 4
典 E A Analysis Effect 故障模式影响分析(Potential Failure Mode and Effects Analysis,简记为FMEA) 是分析系统中每一产品所有可能产生的故障模式及其对系 统造成的所有可能影响,并按每一个故障模式的严重程度、 检测难易程度以及发生频度予以分类的一种归纳分析方法。
• 脚踏板 • 执行器 • 转速传感器
第54页
P图(续)
顾客使用:顾客的哪些不当使用会对分析对象造成不利影响。
对于控制器:
外部接线错误
第55页
P图(续)
随时间改变:分析对象随运行时间的加长出现的疲劳磨损 等。
对于控制器:
• 参数漂移 • 记录芯片电量衰减
第56页
P图(续)
外部环境:使用环境对分析对象造成的不良影响。
控制因子:设计过程中所有因素的集合,其目的是减少 错误状态的发生。
第36页
干扰因子
个体差异:各零部件、总成之间的差异,包含设计、生 产,以及与各接口部件之间的关系 内部环境:分析对象的接口零部件对其产生的影响 顾客使用:顾客的哪些不当使用会对产品造成的不利影 响。 随时间改变:分析对象随运行时间的加长出现的疲劳磨 损等。 外部环境:使用环境对分析对象造成的不良影响。
接上页
是否要 纠正?
否 是
建议纠正措施
确定责任人和完 成日期 纠正措施效果判 定
否
是否满 足要求?
是
生成控制计划
评审通过
DFMEA工程实施
成立FMEA 小组
FMEA 分析
FMEA 评审
第20页
成立DFMEA项目组
典型的DFMEA团队:
系统工程师(强制) 设计工程师(强制) 可靠性工程师 过程工程师 试验工程师 质量工程师 。。。。
干扰因子
输入信号
系统描述
理想功能 错误状态
控制因子
第34页
P图
输入信号:指分析对象运行所需的基本条件。 理想功能:分析对象需要完成的功能,反映了产品的设 计意图或功能需求。 错误状态:与预期功能的偏差或非预期的分析对象的输 出。
功能丧失; 功能降低; 间歇性功能; 非预期功能。
第35页
Failure Mode
第3页
FMEA是什么 ?
FMEA是: 有计划的可靠性方式 系统的风险分析方式 文件方式
第4页
FMEA的历史
六十年代,Apollo计划。
1974年,MIL-STD-1629,80年,MIL-STD-1629 A。 七十年代后期,美国汽车工业采用FMEA作为风险评估工具。
1992年,我国颁布GJB1391-92《故障模式、影响及危害性分 析程序》
第52页
P图(续)
个体差异:各零部件、总成之间的差异,包含设计、生产, 以及与各接口部件之间的关系(参照边界图) 对于控制器:
• 虚焊、漏焊、错焊; • 电源转换模块、调理电路、A/D转换电路、CPU、转速处理电路、驱动 器 • 性能参数指标超差
第53页
P图(续)
内部环境:分析对象的接口零部件对其产生的影响 对于控制器:
第21页
DFMEA分析步骤
•5 •故障原因分析 •4 •故障影响分析 •3 •故障模式分析 •2 •系统定义
•1 •收集数据,了解系统 组成及原理
功能图 边界图 P图
第22页
DFMEA分析步骤
•10 •实施效果 •9 •建议实施 •8 •改进建议 •7 •风险评估
•6
•当前控制方法 预防 检测
第23页
对于控制器:
•振动、冲击 •气密性 •盐雾 •温度:-43℃~60℃ •电磁兼容
第57页
P图
控制因子:设计过程中所有因素的集合,其目的是减少 错误状态的发生。
对于控制器:
设计要求 筛选试验、过程控制 性能调试、系统联调 环境试验 使用说明书
第58页
控制器P图
第59页
控制器FMECA
技术应用
FMEA工具与技术使用
组织
1
流程
Level 1 基础
定义
守规 职责 产品研发过程
当前FMECA工作常见问题
FMEA=填表
设计人员不了解FMEA 不合适的时间开展FMEA 故障模式定义不明确 故障原因不全面
风险分析和控制准则不清晰
第29页
解决方案 进行FMEA 技术培训 建立FMEA 工作模板 建立FMEA 作业指导书 制定FMEA 计划 实施FMEA 节点控制 将FMEA 纳入产品流程
应实施完成的FMEA
情况2:现有设计或工艺过程改进
对改进部分实施FMEA,参考原有FMEA,注重改进对原 有系统或工艺过程的影响
情况3:现有设计或工艺过程的应用环境、使用 方式等发生变化
注重环境等变化后的外界因素对原有系统、工艺流程 的影响
第6页
为什么要实施FMEA
事先花时间对设计进行分析,事先低成本进行改进
第37页
P图与FMEA的关系
P图的理想功能对应FMEA中的功能 P图的错误状态对应FMEA中的故障模式 P图的干扰因子对应FMEA中的故障原因 P图的控制因子对应FMEA中的现行控制
第38页
解决方案
制定符合企业需求的风险判定准则 RPN值作为风险 分析唯一标准
我们应该优先控制哪个故障模式 ? Ford:
第26页
内容安排
1
FMEA概述 DFMEA工程实施 DFMEA实施难点与解决方案
2 3 4 4
典型案例分析
总结与讨论
FMEA 的成熟过程
Mature Level
4
革新
Level 4 扩展及提高
嵌入 PLM 全方位应用及有效改进
3
Level 3 反馈
R&D 阶段的有效应用
技术
2
Level 2 启动
严重度(S) 严重度×发生度 RPN=S×O×D
第39页
解决方案
提出可明确执行的控制措施 落实人和执行时间 控制措施可以是
技术更改 补充试验 评审确认 等等
控制准则不 清晰
第40页
内容安排
1
FMEA概述 DFMEA工程实施 DFMEA实施难点与解决方案
2 3 4 4
典型案例分析
总结与讨论
P图
干扰因子:能够导致分析对象功能故障的非预期的因素, 分为5类。
个体差异(PP: Piece-to-piece Variation) 内部环境(SI: System-interaction) 顾客使用(CU: Customer Usage and Duty Cycle) 随时间改变(DG: Changes over Time or Mileage) 外部环境(EE: Environment)
• • • • • 齿杆位置信号, 温度信号, 油压信号, 数字信号, 电源
第50页
P图
错误状态:与预期功能的偏差或非预期的分析对象的输 出。
对于控制器
无控制信号输出; 控制错误; 间歇输出;
第51页
P图
干扰因子:能够导致分析对象功能失效的非预期的因素, 分为5类。
个体差异 内部环境 顾客使用 随时间改变 外部环境
1991年,ISO9000推荐,1994年,QS9000强制实施
2007年我国将颁布GJB/Z1391A-2006《故障模式、影响及危 害性分析指南》,增补了大量内容。
2008年发布QS9000FMEA参考手册第四版,FMEA 技术作为风 险控制的主要手段之一。
第5页
什么时间做FMEA
情况1:新设计、新技术、新工艺
FMEA分析对象—柴油机控制器
第42页
功能图
用以确定分析对象及其各组成部分(下属部件) 应具有的功能。
系统功能分解
系统结构层次关系 系统功能层次和结构层次的对应关系
第43页
控制系统功能图
第44页
边界图
边界图用于描述分析的边界范围和接口,说明各组件、零 部件之间的关系。
E
B D A C G
内容安排
1
FMEA概述 DFMEA工程实施 DFMEA实施难点与解决方案
2 3 4 4
典型案例分析
总结与讨论
最佳实践:FMEA 全流程
系统或详细产品结构信息
/BOM FMEA硬/软件分析
存储/重用故障模式、 原因、预防措施等