驻车制动杆台架试验规范
3-4 汽车制动性能检测标准(二)

3-4 汽车制动性能检测标准(二)
导入新课:提问:路试制动性能的诊断参数有哪些
一、台式检测行车制动性能检测
1、制动力要求
汽车、汽车列车在制动试验台上测出的制动力应符合下表的要求,对空载检测制动力有质疑时,可用表中规定的满载检验制动力要求进行检测。
(表)台式检测制动力要求
2、制动力平衡要求
在制动力增长全过程中,左右轮制动力差与该轴左右轮中制动力大者之比对前轴应≤20%,对后轴应≤24%。
3、制动协调时间
制动协调时间是指在紧急制动时,从踏板开始动作至车轮制动力达到表4-3所规定的制动力的75%时所需时间。
汽车单车制动协调时间应≤0.6s,汽车列车制动协调时间应≤0.8s。
4、车轮阻滞力
车轮阻滞力是指行车和驻车制动装置处于完全释放状态,变速器置空档位置时,试验台驱动车轮所需的作用力。
汽车各车轮的阻滞力
不得大于该轴轴荷的5%。
5、制动完全释放时间
是指从松开制动踏板到制动消除所需要的时间。
单车的制动完全释放时间不得大于0.8s。
二、驻车制动性能检测
当采用制动试验台检查车辆驻车制动力时,车辆空载,乘坐一名驾驶员,使用驻车制动装置,驻车制动力的总和应不小于该车在测试状态下整车重量的20%;对总质量为整备质量1.2倍以下的汽车,此值应为15%。
三、计算实例
课本P41页。
归纳小结:1、台架试验的制动性能的标准的判断
作业:解释名词:制动协调时间、车轮阻滞力、制动完全释放时间。
驻车制动杆台架试验规范

驻车制动操纵杆台架试验规范前言本标准编写格式符合GB/T1.1-2009标准规定。
本标准通过纸版发布,是受控文件,复印的文件为非受控文件,仅供参考。
驻车制动操纵杆台架试验规范1 范围本规范适用于机械式驻车制动操纵杆总成的外观、结构、参数及性能等的台架试验;本标准适用于驻车制动操纵杆总成的台架试验。
2 规范性引用文件下列文件对于本文件的应用是必不可少的,凡是注日期的引用文件,仅注日期的版本适用于本文件。
凡是不注日期的引用文件,其最新版本(包括所有的修改单)适用于本文件。
QC/T484 汽车油漆涂层GB/T1818 金属表面洛式硬度试验方法GB/T4340.1 金属维式硬度试验第1部分:试验方法3. 试验内容及要求3.1 外观质量3.1.1 不允许有碰伤、损坏、锈蚀及毛刺等缺陷。
3.1.3 棘轮板的齿形应规则、统一,与棘爪啮合应牢固。
3.1.3 铆接牢固,铆接部位无龟裂等,铆后该部位涂无色透明漆。
3.1.4 操纵应灵活、可靠,无卡滞、噪声等缺陷。
3.3 涂层质量涂层表面应光滑平整、色泽一致;漆膜厚度不低于30μm。
3.3热处理要求棘轮板与棘爪应渗碳淬火、回火,齿部表面硬度为HR30N64-73,在550HV的硬化深度为0.15-0.30mm。
3.4 偏摆范围在操纵杆的动作范围内,驻车制动杆的偏摆量不得超过3mm,耐久性试验后不超过5mm。
3.5 抗拉强度3.5.1 按钮与推杆在98N的轴向力下不得松动、脱落。
3.5.3 驻车制动杆手柄在经受热循环试验后,其手柄拉脱力应不小于300N,转动力矩应不小于5.0N·m,且无龟裂、变形等。
3.6 圆周方向负荷强度试验后应满足3.4的要求。
3.7 横向刚性按4.7的方法试验,Q点的横向偏移不超过5mm。
3.8 横向负荷强度试验后应满足3.4的要求。
3.9 止动强度按4.9的方法试验后,应满足3.4的要求。
3.10 快速操作耐久性试验后应满足3.4的要求。
汽车制动性能台架试验检测法
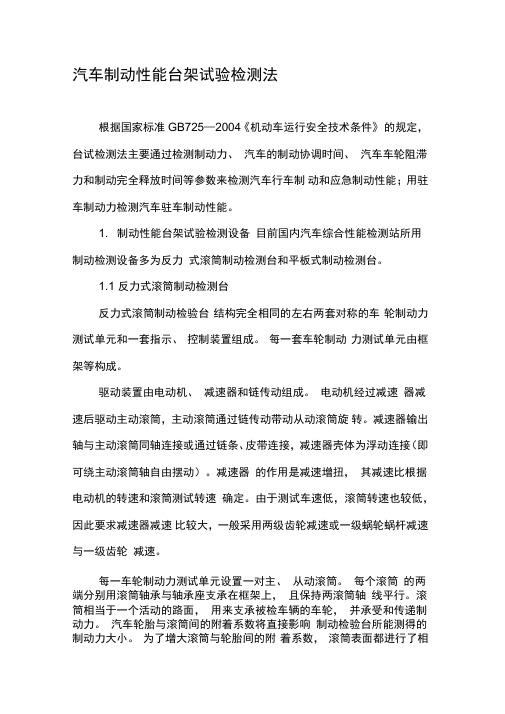
汽车制动性能台架试验检测法根据国家标准GB725—2004《机动车运行安全技术条件》的规定,台试检测法主要通过检测制动力、汽车的制动协调时间、汽车车轮阻滞力和制动完全释放时间等参数来检测汽车行车制动和应急制动性能;用驻车制动力检测汽车驻车制动性能。
1. 制动性能台架试验检测设备目前国内汽车综合性能检测站所用制动检测设备多为反力式滚筒制动检测台和平板式制动检测台。
1.1 反力式滚筒制动检测台反力式滚筒制动检验台结构完全相同的左右两套对称的车轮制动力测试单元和一套指示、控制装置组成。
每一套车轮制动力测试单元由框架等构成。
驱动装置由电动机、减速器和链传动组成。
电动机经过减速器减速后驱动主动滚筒,主动滚筒通过链传动带动从动滚筒旋转。
减速器输出轴与主动滚筒同轴连接或通过链条、皮带连接,减速器壳体为浮动连接(即可绕主动滚筒轴自由摆动)。
减速器的作用是减速增扭,其减速比根据电动机的转速和滚筒测试转速确定。
由于测试车速低,滚筒转速也较低,因此要求减速器减速比较大,一般采用两级齿轮减速或一级蜗轮蜗杆减速与一级齿轮减速。
每一车轮制动力测试单元设置一对主、从动滚筒。
每个滚筒的两端分别用滚筒轴承与轴承座支承在框架上,且保持两滚筒轴线平行。
滚筒相当于一个活动的路面,用来支承被检车辆的车轮,并承受和传递制动力。
汽车轮胎与滚筒间的附着系数将直接影响制动检验台所能测得的制动力大小。
为了增大滚筒与轮胎间的附着系数,滚筒表面都进行了相应加工与处理,目前采用较多的有下列五种:1.1.1 开有纵向浅槽的金属滚筒,在滚筒外圆表面沿轴向开有若干间隔均匀、有一定深度的沟槽。
这种滚筒表面的附着系数最高可达0.65 。
当表面磨损且沾有油、水时,附着系数将急剧下降。
为改进附着条件,有的制动台表面进一步作拉花和喷涂处理,附着系数可达0.75 以上。
1.1.2 表面粘有熔烧铝矾土砂粒的金属滚筒。
这种滚筒表面无论干或湿时其附着系数可达0.8 以上。
1.1.3 表面具有嵌砂喷焊层的金属滚筒,喷焊层材料选用NiCrBSi 自熔性合金粉末及钢砂。
ZD-10汽车制动试验台操作规程

ZD-10汽车制动试验台操作规程及维护保养
1.操作规程
1.1打开仪表电源开关,接通电源,确认仪表显示为零,进入工作状态,否则按复位键清零。
1.2打开电机控制箱电源开关,接通电源。
1.3需要检测的汽车以4千米/小时的速度驶上试验台,汽车车轮应清洁干净,不得有石子和铁钉。
检测的车轮支承在两滚筒之间,汽车中心线应与滚筒轴线垂直,停稳后确定汽车处于空挡状态。
1.4按下“双轮”键,左右台架滚筒正向转动,2秒钟后仪表箱两侧指示灯开始闪烁,此时司机踏下制动踏板进行制动,车轮停止转动,滚筒也停止转动。
1.5仪表显示出左右轮的制动力数值,不对称数值,按一下“打印”键,即打印出当前左右轮制动力数值、制动过程曲线。
1.6按下驱车按钮,左右台架的滚筒反向转动,同时开动汽车驶出试验台。
1.7在试验时如果发生意外情况需要停止测试时,可按仪表上的“急停”按钮。
1.8汽车轴重不得超过10吨。
2.设备的维护保养
2.1要经常清扫,保持试验台清洁,滚筒上不得沾有油污。
2.2每月须给传动链条和链轮加40号机油润滑(可加黄油)。
2.3每半年须给轴承加润滑脂一次。
2.4每年须对设备标定一次。
2.5减速箱每年换油一次。
2.6发现链条松紧不当,应进行调整,带座轴承边上张紧螺栓调整是链条松紧用的,一般链条松紧程度以松边中间处下垂量为8-10mm。
货车、客车制动器台架试验方法-QC-T-479-1999
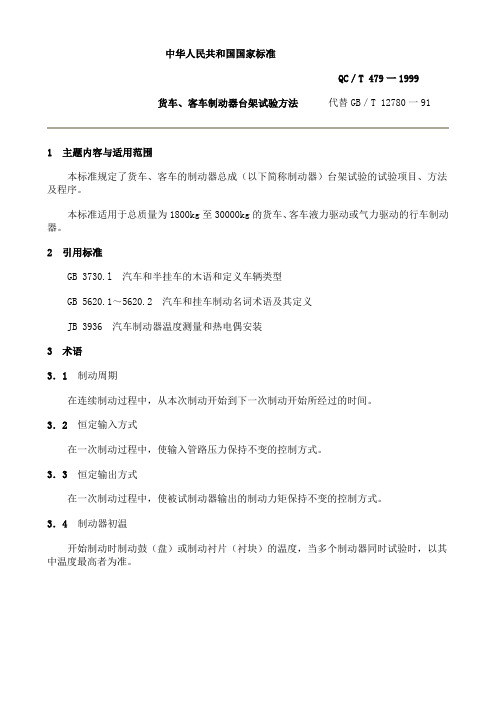
中华人民共和国国家标准QC/T 479一1999货车、客车制动器台架试验方法代替GB/T 12780一911 主题内容与适用范围本标准规定了货车、客车的制动器总成(以下简称制动器)台架试验的试验项目、方法及程序。
本标准适用于总质量为1800kg至30000kg的货车、客车液力驱动或气力驱动的行车制动器。
2 引用标准GB 3730.l汽车和半挂车的木语和定义车辆类型GB 5620.1~5620.2汽车和挂车制动名词术语及其定义JB 3936汽车制动器温度测量和热电偶安装3 术语3.1 制动周期在连续制动过程中,从本次制动开始到下一次制动开始所经过的时间。
3.2 恒定输入方式在一次制动过程中,使输入管路压力保持不变的控制方式。
3.3 恒定输出方式在一次制动过程中,使被试制动器输出的制动力矩保持不变的控制方式。
3.4 制动器初温开始制动时制动鼓(盘)或制动衬片(衬块)的温度,当多个制动器同时试验时,以其中温度最高者为准。
3.5 最大制动力矩3.6 最小制动力矩3.7 平均制动力矩指一次制动过程中的上制动过程,制动力矩与制动时间所围的面积,除以主制动时间所得的纵坐标值。
3.8 制动时间制动器作用的时间包括制动力增长时间,主制动时间、放松时间。
3.9 拖磨在不切断输入动力情况下进行制动。
4 符号5 试验项目5.1 制动器效能试验5.2 制动器热衰退恢复试验5.3 制动器噪声测定5.4 制动衬片/衬块磨损试验6 试验条件6.1 试验设备惯性式试验设备(单端或双端)及测量记录仪器。
6.2 被试制动器应为符合图纸及技术文件规定的合格制动器。
6.3 试验台转动惯量的确定车辆总质量加上旋转部分当量修正值,然后把相当于该质量的转动惯量按各轴制动力分配比分配。
旋转部分的修正值取空车质量的7%。
所选飞轮片的转动惯量(应考虑试验台旋转部分的惯量)允差±5%。
制动检验台安全操作规程正式版

制动检验台安全操作规程正式版第一章总则第一条为了保证制动检验台的正常运行和作业的安全性,制定本规程。
第二条本规程适用于制动检验台的日常运行、检验作业等场合。
第三条制动检验台操作人员须认真学习和遵守本规程,并加强对其他人员的教育。
第四条任何人不得违反本规程进行操作。
第五条制动检验台操作人员在制动检验台操作过程中应严格遵守安全操作规程和操作规范,确保工作平安无事故发生。
第二章安全技术措施第六条所有操作人员必须经过系统正规的培训和考核合格后方能上岗工作,对未经正规培训和考核合格的人员不得擅自操作。
第七条操作人员在上岗前必须穿戴好相应的安全装备和防护设备,包括头盔、防护眼镜、防护手套等。
第八条操作人员在操作过程中应按照操作指南的要求进行操作,并不得随意拆卸、修理检测设备。
第九条制动检验台设备的维护保养工作必须由专业人员进行,非专业人员不得进行保养、维修等操作。
第十条制动检验台设备出现异常情况时,操作人员应立即停止操作,并向维修人员报告,禁止采取私自处理方式。
第十一条严禁操作人员将任何物品放置在制动检验台设备上,以免影响设备的正常使用。
第十二条操作人员应保持工作场地整洁,保持通道畅通,避免照明灯被遮挡,以确保操作的安全性和准确性。
第三章应急措施第十三条发现制动检验台设备出现故障或异常情况时,操作人员应立即停止操作并向监工报告,等待专业人员处理。
第十四条操作人员在操作过程中如遇火灾等紧急情况,应立即按规定的应急程序进行处置,并采取措施确保自身的安全。
第十五条操作人员在发现在操作过程中发现其他人员存在安全隐患时,应及时提醒其采取安全防护措施,并向监工汇报。
第四章违纪处分和责任追究第十六条对于未经正规培训擅自上岗操作的人员,将立即停止其工作,并按规定进行处理。
第十七条对于违反本规程造成事故的操作人员将按照事故的严重性追究其法律责任,并依工作程序进行相应处罚。
第十八条对于故意破坏设备、取消安全装备擅自操作的人员,将追究其法律责任,并按规定进行处分。
汽车制动性能台架试验方法
Internal Combustion Engine & Parts
· 165 ·
盾构机中心回转体脱落结构修复技术研究
李锦富
(深圳市市政工程总公司隧道公司,深圳 518000)
摘要院本文通过深圳地铁 3 号线南延线 3131 标福耀益区间盾构机中心回转体与刀盘脱落,泡沫和水等碴土改良材料不能输送到 刀盘前方,导致盾构机改良系统瘫痪,需对盾构机改良系统进行结构修复,本文分析和总结了中心回转体的故障现象和成因,并提出 了解决盾构机问题的一些方法和方法,使盾构机改良系统结构得到修复,盾构施工风险安全可控。
关键词院汽车;制动性能;台架;试验方法
0 引言 汽车台架试验是最近几年车辆进行制动性评价的主 要方法,相比汽车道路试验,台架试验具有空间要求小、试 验成本低、精度高、重复性好等优点。根据国家机动车运行 安全技术条件等标准和法规,用台架试验方法检测汽车的 制动性能是否良好主要从它的制动力,车辆制动需要协调 的时间,完全释放制动力的时间以及该车轮子的阻滞力等 各方面的数据进行精确分析,最终检测得出汽车制动性能 是否合格。 1 制动性能台架试验检测设备 我国目前用于检测汽车制动性能的台架试验检测设 备大体分为两种,反力式滚筒制动检测和平板式制动检测 设备。 1.1 反力式滚筒制动检测台 本文首先就反力式滚筒制动检测台的结构以及它的 作用来进行一个具体的描述,首先是反力式滚筒的组成, 主要分为六个大的系统。驱动装置和滚筒装置是其中的主 干及最为核心的部分,滚筒紧连着驱动装置中的链传动, 以链传动为能量装置带动滚筒转动,并同时控制好与主转 筒连接在一起的减速器,使得可以方便地起到减速增扭的 作用。减速器的性能是需要被重要考虑的因素,车辆在进 行滚筒测试的时候一般速率要求得特别低,因此减速器就 要在其中发挥巨大作用,减速器减速作用必须明显,性能 必须可靠。我国目前滚筒制动检测台的减速器一般采用三 种:两级齿轮减速、一级蜗轮蜗杆减速及一级齿轮减速。 反力式滚动制动检测台主要分为一主一次两个滚筒, 每个滚筒分别由其轴承与其轴承座支撑于框架中,两个滚 筒相互平行,以滚筒代替路面对车辆制动性能好坏进行检 测,即通过滚筒与轮胎间的附着系数对汽车制动力的大小 进行测定,因此滚筒制动检测台对于滚筒的加工不可或 缺。我国目前进行汽车制动性能检验的滚筒经加工处理后 主要分为五种,第一种是在金属滚筒表面上设置纵向浅 槽,浅槽设计务必做到均匀一致,沟槽深度均一,以增加滚 筒表面附着系数,据研究者调查发现,这种金属滚筒表面 的附着系数最高可达 0.65,但是该种滚筒存在一定的缺陷 就是一旦表面沾上油脂水滞或是出现轻微的磨损,附着系 数将急剧降低,研究人员为了改善这一缺点对滚筒做了进 要要要要要要要要要要要要要要要要要要要要要要要
制动检验台操作规程
制动检验台操作规程1. 引言制动检验台作为车辆制动性能测试的重要设备,在车辆制动领域扮演着关键的角色。
制动检验台的检验工作可以帮助车主和驾驶员及时发现车辆制动性能不良的问题,提供客观的数据依据和技术支持,维护道路行车安全。
在进行制动检验之前,驾驶员应该掌握正确的操作方法,按照规范的操作流程进行检验。
2. 制动检验流程在进行制动检验时,驾驶员应按照以下流程进行操作:2.1 进行准备工作•确保制动检验台设备工作正常;•清理车辆制动系统油污、灰尘等杂质;•定位车辆制动系统检测点,并与制动检验台对应位置对接。
2.2 进行制动检测•开始检测前先进行热身,进行一段时间的车速加速冷减,到达稳定状态后进行检测;•发动汽车,将汽车开至制动检验台上方,与对应的传感器接触;•在经过制动检测台时,保持车速在制定范围内,按照要求用一定力度进行制动,持续2-3秒钟,记住所得的数据;•按照上述操作,对每个制动点进行检测;•完成检查后,关闭检测台设备,停车。
3. 操作注意事项在进行制动检测时,驾驶员应当注意以下事项:•检查车辆制动系统并消除问题;•操作人员应熟悉设备使用方法,并严格按照规定进行操作;•保证车辆制动系统处于正常工作状态,避免发生事故;•操作人员在车辆行驶过程中严格按照相关规定和制动检验要求进行操作,注意安全;•在检测过程中,保持操作台及其周围环境良好,禁止喧哗、乱丢杂物等不当行为;•如发现毛刺或者其他影响制动检验的物品应该尽快清理干净。
4.本文阐述了制动检验台的操作规程,希望通过规范的操作流程和注意事项,能够帮助驾驶员及时发现车辆制动性能问题,保障道路安全。
同时,此操作规程也应当被广泛应用于车辆制动检验中,提升检测质量和效率。
汽车手刹驻车制动系统试验台架设计
Equipment Manufacturing Technology No.01,20181设计目的汽车手刹驻车制动系统应能确保汽车驻车制动的可靠性,特别是在驻坡时不能出现溜坡这种危险情况发生,现其可靠性验证主要依赖于整车道路试验。
但整车道路试验的驻坡次数有限,不能充分验证其耐久可靠性,且试验周期较长,不利于系统的设计开发。
现亟须通过台架试验,在短期内实现充分验证其耐久可靠性,为手刹驻车制动系统的设计开发提供验证支持,提供设计效率。
2汽车手刹驻车制动系统汽车手刹驻车制动系统由手刹,左右拉索、后制动器、后制动盘、后轮毂等零件组成,如图1所示。
汽车停止后,驾驶员拉起手刹,带动拉索驱动制动器夹紧制动盘,防止汽车轮毂转动,实现驻车制动;当汽车要启动时,驾驶员按下手刹解锁按钮放下手刹,带动拉索驱动制动器松开对制动盘的夹紧,解除驻车制动。
汽车在斜坡上行驶时,驾驶员踩刹车停车后,拉起手刹实现驻坡,此时汽车所受重力沿斜坡向下的分力对轮毂产生向下的溜坡转矩,拉起手刹后制动器的制动转矩应与溜坡转矩相平衡,避免汽车下滑溜坡。
汽车手刹驻车制动系统应确保在最极限的条件下,即汽车为设计满载重量,在设计最大驻车坡度上驻车制动的可靠性。
汽车满载状态下在设计最大驻车坡度上溜坡转矩的计算公式:M =mg ×sin θ×R 式中:M 为溜坡转矩;m 为汽车满载质量;θ为设计最大驻车坡度;R 为车轮静半径。
3试验台架设计3.1试验台架设计要求为了实现对手刹驻车制动系统的可靠性验证,试验台架需将手刹驻车制动系统所有零件按实车布置要求集成安装,并模拟驾驶员拉起手刹、解锁放下手刹的循环动作,在驻车制动时按汽车满载状态下在最大设计坡度上驻坡所受的溜坡转矩对轮毂进行加载,对手刹驻车制动系统的耐久可靠性进行充分验证。
3.2设计设计的试验台架由以下三部分组成:1)后轮毂安装及转矩加载机构;2)手刹安装及操纵机构;3)拉索安装装置。
制动检验台安全操作规程
制动检验台安全操作规程一、操作前准备1.操作人员必须具备相关的技术培训和操作证书,且必须经过安全培训。
2.检查制动检验台的设备状态,确保设备完好无损、稳定可靠,如有异常情况要及时报告维修。
3.查阅相关的操作手册和制动检验标准,了解检验规程和参数要求。
4.穿戴相应的个人防护装备,如安全帽、防护眼镜、防滑鞋等。
二、操作步骤1.将待检车辆停放到指定位置,确保车辆稳定无异响。
2.使用制动检验台上的操作控制器,将车辆安全抬升到合适的高度,同时使用安全锁定装置固定车辆。
3.使用探测器或传感器将制动台与车轮紧密连接,确保有良好的接触。
4.根据车辆类型和检验要求,选择合适的制动检验模式和参数。
5.启动制动检验台,确保设备运行正常,观察车轮和制动器的工作状态。
6.在设定的速度下,观察车轮的滚动情况和制动器的制动效果,记录相关数据和参数。
7.完成检验后,及时停止制动检验台的运行,将车辆降下并解除固定装置。
8.将车辆从制动检验台上移动至指定位置,清理工作区域以及检验台的残留物。
三、安全注意事项1.严禁擅自更改、拆卸、修理制动检验台的任何零部件。
2.操作人员必须熟悉设备的工作原理和操作方法,严禁未经培训的人员操作。
3.在检验过程中,严禁站在车辆和检验台的旁边、下面或后面等危险区域。
4.使用制动检验台时,必须确保车辆的制动系统处于正常工作状态。
5.在启动制动检验台之前,必须确保操作区域内没有其他人员和障碍物。
6.在检验过程中,严禁将手、脚或其他物体放入车轮和制动器之间的空隙。
7.在操作过程中,如发现设备异常,应立即停止操作并报告维修,严禁擅自继续操作。
8.长时间连续工作后,制动检验台可能会发生过热现象,应停机降温后再继续操作。
9.在操作过程中,要密切观察制动检验台和车辆的运行状态,如发现异常情况要及时报告。
10.操作人员要遵守工作纪律,遵守相关规定,严禁饮酒、吸烟和使用手机等干扰操作的行为。
以上就是制动检验台的安全操作规程,操作人员必须严格遵守,确保操作人员和设备的安全。
- 1、下载文档前请自行甄别文档内容的完整性,平台不提供额外的编辑、内容补充、找答案等附加服务。
- 2、"仅部分预览"的文档,不可在线预览部分如存在完整性等问题,可反馈申请退款(可完整预览的文档不适用该条件!)。
- 3、如文档侵犯您的权益,请联系客服反馈,我们会尽快为您处理(人工客服工作时间:9:00-18:30)。
驻车制动操纵杆台架试验规范
前言
本标准编写格式符合GB/T1.1-2009标准规定。
本标准通过纸版发布,是受控文件,复印的文件为非受控文件,仅供参考。
驻车制动操纵杆台架试验规范
1 范围
本规范适用于机械式驻车制动操纵杆总成的外观、结构、参数及性能等的台架试验;
本标准适用于驻车制动操纵杆总成的台架试验。
2 规范性引用文件
下列文件对于本文件的应用是必不可少的,凡是注日期的引用文件,仅注日期的版本适用于本文件。
凡是不注日期的引用文件,其最新版本(包括所有的修改单)适用于本文件。
QC/T484 汽车油漆涂层
GB/T1818 金属表面洛式硬度试验方法
GB/T4340.1 金属维式硬度试验第1部分:试验方法
3. 试验内容及要求
3.1 外观质量
3.1.1 不允许有碰伤、损坏、锈蚀及毛刺等缺陷。
3.1.3 棘轮板的齿形应规则、统一,与棘爪啮合应牢固。
3.1.3 铆接牢固,铆接部位无龟裂等,铆后该部位涂无色透明漆。
3.1.4 操纵应灵活、可靠,无卡滞、噪声等缺陷。
3.3 涂层质量
涂层表面应光滑平整、色泽一致;漆膜厚度不低于30μm。
3.3热处理要求
棘轮板与棘爪应渗碳淬火、回火,齿部表面硬度为HR30N64-73,在550HV的硬化深度为0.15-0.30mm。
3.4 偏摆范围
在操纵杆的动作范围内,驻车制动杆的偏摆量不得超过3mm,耐久性试验后不超过5mm。
3.5 抗拉强度
3.5.1 按钮与推杆在98N的轴向力下不得松动、脱落。
3.5.3 驻车制动杆手柄在经受热循环试验后,其手柄拉脱力应不小于300N,转动力矩应不小于5.0N·m,且无龟裂、变形等。
3.6 圆周方向负荷强度
试验后应满足3.4的要求。
3.7 横向刚性
按4.7的方法试验,Q点的横向偏移不超过5mm。
3.8 横向负荷强度
试验后应满足3.4的要求。
3.9 止动强度
按4.9的方法试验后,应满足3.4的要求。
3.10 快速操作耐久性
试验后应满足3.4的要求。
3.11 棘轮啮合性能
按4.11的方法试验后,棘爪应能与最近的棘轮齿啮合。
3.13 耐久性
按4.13的方法试验后,应满足3.4的要求。
4 试验方法
4.1 外观检查
用目测和手感检查质量,其结果符合3.1条要求。
4.3 涂层检查
按QC/T484-1999中TQ6的规定检验漆层质量,其结果应符合3.3要求。
4.3 热处理检测
按GB/T1818-1994检测齿部表面硬度,按GB/T4340.1-1999检测500HV的硬化深度,其结果应符合4.3条的规定。
4.4 偏摆范围检测
在操纵杆的动作范围内,在Q点施加横向力5N,测新产品和耐久性试验后C点的偏摆量,其结果应符合3.4条的规定。
4.5 抗拉强度试验
驻车制动杆手柄以(80℃/4h--室温/0.5h---30℃/3h--室温/17.5h)为一个循环,经4个循环试验后,观察其手柄的外观,并测拉脱力和转动力矩,应符合3.5的规定。
4.6 圆周方向负荷强度试验
Z点固定,制动杆的位置应在棘轮的第八啮合齿槽处,在Q点加R方向及与此相反方向负荷900N 各5次,试验后应满足3.4的要求。
4.7 横向刚性试验
在Q点加L方向及与此相反方向负荷50N左右各一次,试验后应满足3.7的要求。
4.8 横向负荷强度试验
在Q点加L方向及与此相反方向负荷500N左右各一次,试验后应满足3.4的要求。
4.9 止动强度试验
在全行程位置,在Q点加R方向负荷400N一次;在制动杆初始位置,在Q点加R方向的反方向负荷500N一次;试验后应满足3.9的要求。
其中C点是指揿钮端部,Q点和R点是指距C点50mm处手柄的上面和侧面。
见图1所示。
图1 止动强度试验施力图
4.10 快速操作耐用久性试验
在0.5S时间内,以800N的力作用于Q点,使制动杆运动到极限位置,然后返回,此为一个循环;如此动作30个循环,试验后应满足3.11的要求。
4.11 棘轮啮合性能试验
室温条件下,全行程中,作以下试验:拉起制动杆→按下放松按钮→释放放松按钮,试验结果应满足3.13的要求。
4.13 耐久性试验
从总成图示安装状态,以16齿/s速度拉制动杆,在棘轮第八啮合槽处,与棘爪啮合保持1.5s,然后脱开并使制动杆拉回位。
以此为一循环反复操作5万次,试验完后应满足3.4的要求。
其负荷--行程关系如图2所示:
图2 负荷--行程关系如图。