压铸件毛坯质量检验标准 (规范)
压铸件检验规范

合格(装饰面)
0.3~0.6mm
2
整个被检面积≤10个(占总面积的1/6)
合格(非装饰面)
小于1mm2
任意1平方厘米的范围内≤3个砂眼的密 集性不超过所在面积的1/6
非直观面
注:大于1mm以上的砂眼允许的数目;各产品在设计加工时,在总技术要求里具体 写出。也可与厂家协商后确定。表5:来自缺陷类型检验内容
号 类型
检验内容
表面质量 1级 2级 3级
说明
检验状况
深度不大于mm 1 流痕
面积不大于总面积的%
0.05 0.07 0.15 5 15 30
装饰面不允许, 非装饰面1~2级, 内表面3级。
深度不大于mm
1/5 1/4 壁厚 壁厚
长度不大于铸件最大轮廓 尺寸的mm
1、在同一部位
1/10
1/5
对应处不允许同 时存在。
表3、
根据产品使用情况,铸件表面不装饰面非 装饰面和内表面缺陷允收如表:
铸件表面质量级别
1级 2级 3级
缺陷面积不超过总面积的百分数%
5
20 40
表4:
外观缺陷允许范围参照表:
缺陷类型 缺陷面积
检验内容 缺陷个数
检验状况
无
无
合格(重要表面)
通过后序加工达到
砂眼
0.2mm2 任意1平方厘米的范围内≤3个
培训目的
了解压铸件基本检验要求 掌握压铸件检验的基本方法
铸件检验项目
铸件尺寸的检验 铸件外观的检验 化学成分的分析 铸件重量的检验 表面粗糙度
铸件尺寸的检验
铸件尺寸应符合图样的要求 铸件加工余量根据图样要求,此尺寸为检验重点控制,必须符 合图样要求,满足切削工艺 特殊尺寸要求: 检验前应先熟悉图纸,了解加工后的成品关键 技术要求 铸件变形后的尺寸不得超过机加工余量或铸件本身公差(如表1)
压铸件外观检验标准
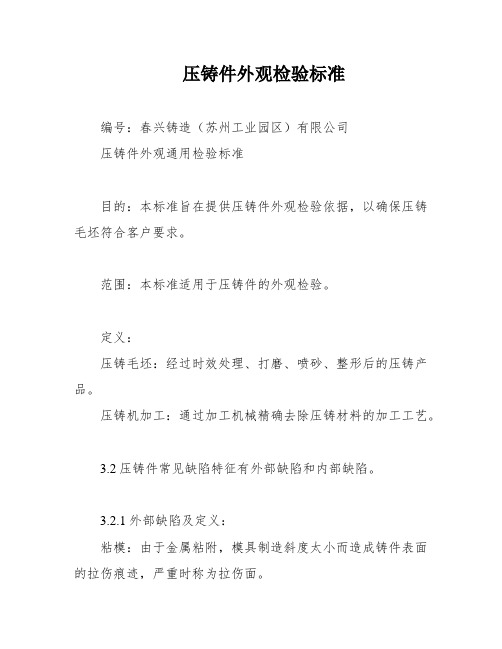
压铸件外观检验标准编号:春兴铸造(苏州工业园区)有限公司压铸件外观通用检验标准目的:本标准旨在提供压铸件外观检验依据,以确保压铸毛坯符合客户要求。
范围:本标准适用于压铸件的外观检验。
定义:压铸毛坯:经过时效处理、打磨、喷砂、整形后的压铸产品。
压铸机加工:通过加工机械精确去除压铸材料的加工工艺。
3.2压铸件常见缺陷特征有外部缺陷和内部缺陷。
3.2.1外部缺陷及定义:粘模:由于金属粘附,模具制造斜度太小而造成铸件表面的拉伤痕迹,严重时称为拉伤面。
分层:铸件上局部存在明显的金属层次。
裂纹:铸件表面有呈直线状或波浪形的纹路,在外力作用下有发展趋势。
变形:由于收缩不均或外力导致压铸件几何形状与图纸不符。
流痕:压铸件表面与金属液流动方向一致的条纹,无发展趋势。
水纹:铸件表面上呈现的光滑条纹,肉眼可见,但用手感觉不出,颜色不同于基体金属的纹路,用#砂布稍擦几下即可去除。
冷隔:在压铸件表面,明显、不规则、下陷的线形纹路(有穿透与不穿透两种),形状细小而狭长,有时交接边缘光滑,有断开的可能。
龟裂毛刺:由于模具型腔表面产生热疲劳而形成的铸件表面上的网状凸起痕迹和金属刺。
凹陷:铸件的厚大部分表面有平滑的下凹现象。
欠铸:铸件表面有浇不足的部位,导致轮廓不清。
飞边、毛刺:在分型面边缘出现金属薄片,或粗糙、锋利的棱角。
错位:铸件的一部分与另一部分在分型面上错开,发生相对位移。
3.2.2内部缺陷及定义:砂孔:在压铸件中,由于压铸的特殊性,铝合金是在高温、高速、高压的状态下成型的,所以压铸件内部是不可避免的存在孔洞,我们统称这些孔洞为砂孔。
缩孔:铸件凝固过程中,金属补偿不足所形成的呈现暗色、形状不规则的孔洞。
气孔:因卷入气体而导致的压铸件内部的孔状缺陷,解剖后外观检查或探伤检查,气孔具有光滑的表面、形状为圆形。
脆性:铸件基体金属晶粒过于粗大或极小,使铸件易断裂或破碎。
渗漏:压铸件经耐压试验,产生漏气、渗水。
本标准的目的是确保压铸毛坯符合客户要求。
压铸件外观通用检验标准(带图实例)
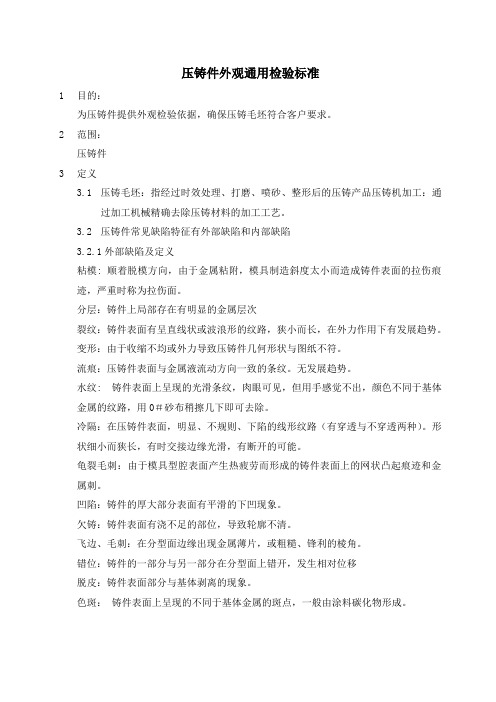
压铸件外观通用检验标准
1目的:
为压铸件提供外观检验依据,确保压铸毛坯符合客户要求。
2范围:
压铸件
3定义
3.1压铸毛坯:指经过时效处理、打磨、喷砂、整形后的压铸产品压铸机加工:通
过加工机械精确去除压铸材料的加工工艺。
3.2压铸件常见缺陷特征有外部缺陷和内部缺陷
3.2.1外部缺陷及定义
粘模: 顺着脱模方向,由于金属粘附,模具制造斜度太小而造成铸件表面的拉伤痕迹,严重时称为拉伤面。
分层:铸件上局部存在有明显的金属层次
裂纹:铸件表面有呈直线状或波浪形的纹路,狭小而长,在外力作用下有发展趋势。
变形:由于收缩不均或外力导致压铸件几何形状与图纸不符。
流痕:压铸件表面与金属液流动方向一致的条纹。
无发展趋势。
水纹: 铸件表面上呈现的光滑条纹,肉眼可见,但用手感觉不出,颜色不同于基体金属的纹路,用0#砂布稍擦几下即可去除。
冷隔:在压铸件表面,明显、不规则、下陷的线形纹路(有穿透与不穿透两种)。
形状细小而狭长,有时交接边缘光滑,有断开的可能。
龟裂毛刺:由于模具型腔表面产生热疲劳而形成的铸件表面上的网状凸起痕迹和金属刺。
凹陷:铸件的厚大部分表面有平滑的下凹现象。
欠铸:铸件表面有浇不足的部位,导致轮廓不清。
飞边、毛刺:在分型面边缘出现金属薄片,或粗糙、锋利的棱角。
错位:铸件的一部分与另一部分在分型面上错开,发生相对位移
脱皮:铸件表面部分与基体剥离的现象。
色斑:铸件表面上呈现的不同于基体金属的斑点,一般由涂料碳化物形成。
压铸件检验标准

文件名称压铸件检验标准生效日期页码 1 of 3 使用状态文件编号版本 A / 0 审核拟定目的确保本公司压铸件制程或进料品质符合客户要求。
范围适应于压铸件制程或进料入库检验。
抽样标准MIL-STD-105E单次Ⅱ级正常检验;CR=0;MA=1.0;MI=2.5。
检验环境在正常光源条件下,距离30cm远检验,以及适宜的角度检验产品。
参照标准1、GB / T2828.1-2003逐批检查计数抽样及抽样表。
2、GB / T 6414-1999铸件尺寸公差。
3、GB/T 11350机械加工余量。
4、GB/T 15115-94铝合金压铸标准。
5、GB 7000.1-2007灯具第一部分:一般要求与试验。
序号检验项目接收标准检验工具及方法缺陷描述缺陷等级致命(CR)严重(MA)轻微(MI)1外观物件的外表面之合模线不能高出平面0.05mm。
目视样板手感卡尺塞规物件的外表面之合模线高出平面0.05mm以上。
√物件的边沿、孔位不能有刺手的披锋及尖角。
物件的边沿、孔位有刺手的披锋及尖角。
√孔位周边披锋,组装后可遮盖。
孔位周边披锋,组装后不能遮盖。
√孔位周边披锋,不影响产品或对内部接线无损伤。
孔位周边披锋,影响产品组装或不能装配。
√影响产品装配,或对内部接线有损伤。
√物件表面不能有明显缩水痕。
物件的主视面,有明显缩水痕。
√物件的次要面缩水面积≤2mm2,缩水深度0.05mm。
√产品外表面及口边不能有缺料痕。
产品外表面及口边,有明显的缺料痕。
√产品孔边缺料,在组装后可遮盖,不影响产品结构。
产品孔边缺料,在组装后不可遮盖,但不影响产品结构。
√产品孔边缺料,在组装后可遮盖,但影响产品的组装、结构。
√缺料面积≤4mm2,不影响产品组装、结构。
√表面龟裂纹明显,但经加工可除去,不影响产品外观。
表面龟裂纹明显,但经加工不可除去,影响产品外观。
√序号检验项目接收标准检验工具及方法缺陷描述缺陷等级致命(CR)严重(MA)轻微(MI)1外观产品外表面花纹痕迹明显,经后续加工可消除。
压铸首末件及定时检验规范(含表格)
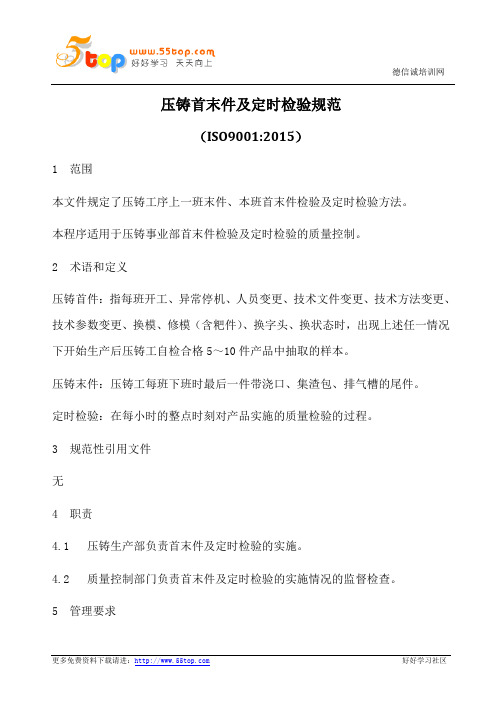
压铸首末件及定时检验规范(ISO9001:2015)1 范围本文件规定了压铸工序上一班末件、本班首末件检验及定时检验方法。
本程序适用于压铸事业部首末件检验及定时检验的质量控制。
2 术语和定义压铸首件:指每班开工、异常停机、人员变更、技术文件变更、技术方法变更、技术参数变更、换模、修模(含粑件)、换字头、换状态时,出现上述任一情况下开始生产后压铸工自检合格5~10件产品中抽取的样本。
压铸末件:压铸工每班下班时最后一件带浇口、集渣包、排气槽的尾件。
定时检验:在每小时的整点时刻对产品实施的质量检验的过程。
3 规范性引用文件无4 职责4.1 压铸生产部负责首末件及定时检验的实施。
4.2 质量控制部门负责首末件及定时检验的实施情况的监督检查。
5 管理要求5.1 压铸工序首末检验及定时检验5.1.1 首末件检验及定时检验标准:压铸工对照“压铸首件送检通知单”项目、检验作业指导书、修模通知等技术标准中的所有项目采取目测的方式进行自检,压铸班长、巡检对照检验作业指导书、修模通知等技术标准中的所有项目采取目测的方式进行互检、专检。
5.1.2 上一班的末件检验:压铸工对上一班的末件进行自检,自检合格后放在指定工作台上,由压铸班长、巡检分别进行互检、专检。
5.1.3 本班首件检验5.1.3.1 压铸工在开始生产压铸首件时,先去除首件浇冒口、飞皮,并对首件进行检验后,填写“压铸首件送检通知单”随首件交质量专检台,涉及换模、换字头、修模后的首件产品,压铸工应将修模前的样件和修模后的首件一同送质量专检台,并在“压铸首件送检检查记录”上登记。
5.1.3.2 压铸巡检按检验作业指导书、修模通知等要求对本班首件产品的尺寸及外观进行全面检查,涉及盖类字样位置检测的必须进行划线检查,并在“压铸首件送检检查记录”上进行记录。
5.1.3.3 有打磨要求的盖类产品在首件检验合格后,压铸巡检安排将上述产品交表面处理工序进行试打磨验证,表面处理工序应在30分钟内完成试打磨验证,打磨巡检确认效果并在“盖类产品打磨验证记录表”上记录。
铸造毛坯件检验规范
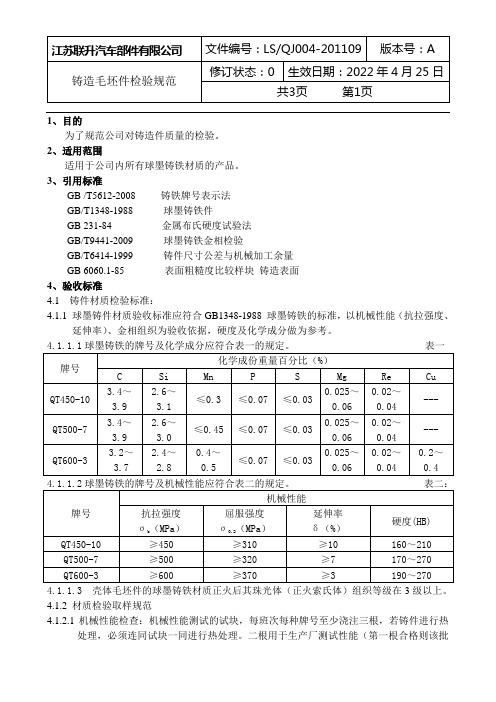
1、目的为了规范公司对铸造件质量的检验。
2、适用范围适用于公司内所有球墨铸铁材质的产品。
3、引用标准GB /T5612-2008 铸铁牌号表示法GB/T1348-1988 球墨铸铁件GB 231-84 金属布氏硬度试验法GB/T9441-2009 球墨铸铁金相检验GB/T6414-1999 铸件尺寸公差与机械加工余量GB 6060.1-85 表面粗糙度比较样块铸造表面4、验收标准4.1 铸件材质检验标准:4.1.1 球墨铸件材质验收标准应符合GB1348-1988 球墨铸铁的标准,以机械性能(抗拉强度、延伸率)、金相组织为验收依据,硬度及化学成分做为参考。
4.1.1.3 壳体毛坯件的球墨铸铁材质正火后其珠光体(正火索氏体)组织等级在3级以上。
4.1.2 材质检验取样规范4.1.2.1机械性能检查:机械性能测试的试块,每班次每种牌号至少浇注三根,若铸件进行热处理,必须连同试块一同进行热处理。
二根用于生产厂测试性能(第一根合格则该批次合格,余下试块(留有生产日期、包次标识)留存。
若第一根试块不合格,测试剩余二根,若第二根不合格则该批次产品全部报废,若第二根合格,应加试第三根,合格则判定该炉产品合格,若第三根不合格则该批次产品全部报废)。
材质检验报告(原档)保存期为5年。
4.1.2.2金相组织检查:球铁铸件从每包铁水的最后一型附铸金相试块或铸件本体进行金相检验,依次往前直到合格(或本包铁水所浇铸件检验完)为止。
附铸试块应能代表本体。
若试块不好,应对铸件本体破件进行检验。
若金相检验由问题,加倍抽查。
金相本体试块应按天分类以月为单位保存,保存期为6个月,检验报告保存期5年。
球化等级要求在3级以上,石墨大小要求为5~7级。
4.1.2.3化学成分检查:每天必须分析每炉铁水(炉前)及至少两炉铸件(炉后)的化学成分。
炉前主要化验C、Si和S,炉后所有元素全部化验。
每天第一炉溶清后必须检测C、Si、Mn、P和S,之后C、Si每炉化验检测。
压铸件外观通用检验标准
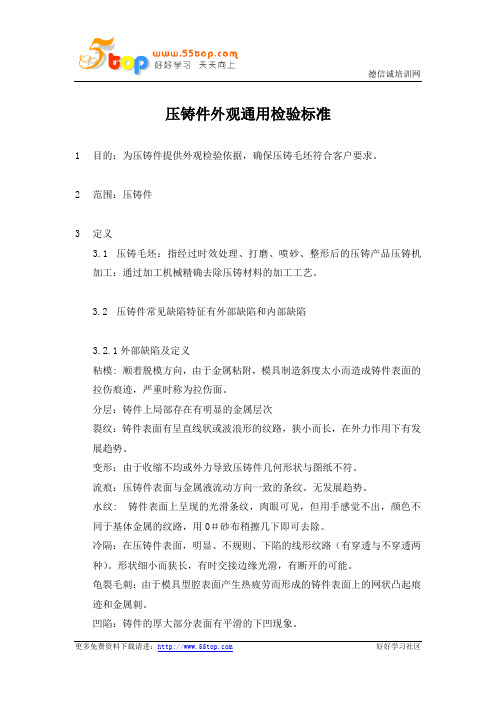
压铸件外观通用检验标准1目的:为压铸件提供外观检验依据,确保压铸毛坯符合客户要求。
2范围:压铸件3定义3.1压铸毛坯:指经过时效处理、打磨、喷砂、整形后的压铸产品压铸机加工:通过加工机械精确去除压铸材料的加工工艺。
3.2压铸件常见缺陷特征有外部缺陷和内部缺陷3.2.1外部缺陷及定义粘模: 顺着脱模方向,由于金属粘附,模具制造斜度太小而造成铸件表面的拉伤痕迹,严重时称为拉伤面。
分层:铸件上局部存在有明显的金属层次裂纹:铸件表面有呈直线状或波浪形的纹路,狭小而长,在外力作用下有发展趋势。
变形:由于收缩不均或外力导致压铸件几何形状与图纸不符。
流痕:压铸件表面与金属液流动方向一致的条纹。
无发展趋势。
水纹: 铸件表面上呈现的光滑条纹,肉眼可见,但用手感觉不出,颜色不同于基体金属的纹路,用0#砂布稍擦几下即可去除。
冷隔:在压铸件表面,明显、不规则、下陷的线形纹路(有穿透与不穿透两种)。
形状细小而狭长,有时交接边缘光滑,有断开的可能。
龟裂毛刺:由于模具型腔表面产生热疲劳而形成的铸件表面上的网状凸起痕迹和金属刺。
凹陷:铸件的厚大部分表面有平滑的下凹现象。
欠铸:铸件表面有浇不足的部位,导致轮廓不清。
飞边、毛刺:在分型面边缘出现金属薄片,或粗糙、锋利的棱角。
错位:铸件的一部分与另一部分在分型面上错开,发生相对位移脱皮:铸件表面部分与基体剥离的现象。
色斑:铸件表面上呈现的不同于基体金属的斑点,一般由涂料碳化物形成。
32.2内部缺陷及定义砂孔:在压铸件中,由于压铸的特殊性,铝合金是在高温、高速、高压的状态下成型的,所以压铸件内部是不可避免的存在孔洞,我们统称这些孔洞为砂孔。
缩孔:铸件凝固过程中,金属补偿不足所形成的呈现暗色、形状不规则的孔洞,即为缩孔气孔:因卷入气体而导致的压铸件内部的孔状缺陷,解剖后外观检查或探伤检查,气孔具有光滑的表面、形状为圆形。
脆性:铸件基体金属晶粒过于粗大或极小,使铸件易断裂或破碎渗漏:压铸件经耐压试验,产生漏气、渗水硬点:机械加工过程或加工后外观检查或金相检查:铸件上有硬度高于金属基体的细小质点或块状物使刀具磨损严重,加工后常常显示出不同的亮度。
压铸件检验标准

1/100
1。0
回转件之平衡度检查
须符合设计之规定
专用治具
√
1/100
1.0
注:1.每批货必须附上“出厂检验报告”。
2。新产品料件必须提供原料材质证明。
厂商确认:正峰品管部:
年月日年月日
2.颜色符合图面要求及色样
目视
√
2.5
表面处理
依图面之要求
目视
√
2.5
附着力测试
用小刀划横直各6条间隔2mm小方格,用透明胶带粘上90秒后撕掉胶带检视表面层,不得有脱落现象
小刀/直尺
胶带
√
每批3~5pcs
化学成分试验
须符合图面之要求,视品质状况不定期而为之
托外实验
√
新品确认2pcs以上
检验项目
检验标准
上海正峰工业有限公司
压铸件检验标准
一.适用范围:
所有外购压铸件入厂之检验依据。
二.权责部门:
品管部IQC
三。时机:
供应商材料之进料检验。
四。检验项目及执行标准:
检验项目
检验标准
检查方
法/量具
缺点分类
Ⅱ水准
AQL%
CR
MA
MI
规格尺寸(配合尺寸)
依图面要求
视图面精度要求而定
√
1/100
1。0
外观检查
1.不得有流痕、花纹、网状毛翅、缩孔缩松、气孔、冷隔、脆性、硬点等压铸缺陷;
检查方
法/量具
缺点分类
Ⅱ水准
AQL%
CR
MA
MI
物理性能测试(抗拉伸、抗疲劳、抗弯曲强度)
须符合图面及设计之要求(视品质状况不定期而为之)
- 1、下载文档前请自行甄别文档内容的完整性,平台不提供额外的编辑、内容补充、找答案等附加服务。
- 2、"仅部分预览"的文档,不可在线预览部分如存在完整性等问题,可反馈申请退款(可完整预览的文档不适用该条件!)。
- 3、如文档侵犯您的权益,请联系客服反馈,我们会尽快为您处理(人工客服工作时间:9:00-18:30)。
压铸件毛坯质量标准生效日期2016年5月09日
页码
3 试验方法及检验规则
3.1 化学成分
3.1.1 铝合金化学成分的检验方法,检验规则和复检应符合GB/T15115的规定。
3.1.2 化学成分的试样也可取自压铸件,但必须符合GB/T15115的规定。
3.2 力学性能
3.2.1 力学性能的检验方法,检验频率和检验规则应符合GB/T15115的规定。
3.2.2 采用压铸件本体为试样时,切取部位的尺寸、测试形式由供需双方商定。
3.3 压铸件几何尺寸的检验可按检验批量抽检或按GB2828、GB2829的规定进行,检验结果应符合本标准3.3的规定。
3.4 压铸件表面质量的出厂检验应逐件检查,检验结果应符合本标准的规定。
3.5 压铸件表面粗糙度按GB/T6060.1的规定执行。
3.6 压铸件需抛光加工的表面按GB/T 6060.4的规定执行。
3.7 压铸件需喷丸、喷沙加工的表面按GB/T 6060.5的规定执行。
3.8 压铸件内部质量的试验方法及检验规则可以包括:X射线照片、无损探伤试验、金相图片和压铸件剖面等,其检验结果应符合本标准2.1.6的规定。
3.9 其它试验方法及检验规则按GB/T15114的规定执行。
4 压铸件的交付、包装、运输与储存
4.1 供方应提供需方一份检验证明,用来说明每批压铸件的检验符合本标准的规定。
4.2 合格压铸件交付时,必须附有检验合格证。
其上应写明下列内容:产品名称、产品号、合金牌号、数量、交付状态、制造厂名。
检验合格印记和交付时间。
有特殊检验项目者,应在检验合格证上注明检验的条件和结果。
4.3 压铸件的包装应牢固,能保证产品在运输和储存期的安全和清洁。
包装箱面或标签上应注明产品名称、产品号、数量、制造日期及收发单位名称。
4.4 产品应贮存于干燥、通风、无腐蚀性气体的环境中。