活性炭活化原理
湿法碳化 活化

湿法碳化活化湿法碳化活化是一种常见的活化方法,用于制备活性炭材料。
活性炭是一种具有高度发达的孔隙结构和巨大比表面积的碳材料,具有很强的吸附能力和化学稳定性,被广泛应用于环境保护、能源储存、电化学催化等领域。
湿法碳化活化方法通过在活化过程中添加一定的湿润剂,可以改善活化效果,提高活性炭的孔隙结构和吸附性能。
湿法碳化活化的基本原理是将碳源与活化剂混合后加热,使碳源在高温下发生碳化反应,并通过活化剂的作用形成孔隙结构。
湿法碳化活化相比于干法活化,通过添加湿润剂可以提高反应温度下的碳源活化速率,促进活化剂对碳源的均匀分散和渗透,从而得到具有更好孔隙结构和吸附性能的活性炭材料。
湿法碳化活化的湿润剂通常选择具有一定溶解性的物质,如水、醇类、有机酸等。
湿润剂的添加可以有效降低活化温度,提高碳源与活化剂的接触性能,增加反应的活性中心,从而改善活化效果。
此外,湿法活化还可以调控活化反应的速率和产物分布,使活化过程更加可控。
在湿法碳化活化过程中,湿润剂的添加量和种类、反应温度、反应时间等条件对活化效果有着重要影响。
合理选择湿润剂种类和添加量,控制反应温度和时间,可以调控活化剂的活性和选择性,优化活性炭的孔隙结构和吸附性能。
此外,湿法碳化活化还可以与其他活化方法相结合,如常见的磷酸活化、氯化锌活化等,进一步改善活化效果。
值得注意的是,湿法碳化活化方法虽然在活化效果上具有一定优势,但也存在一些问题。
首先,湿法活化过程中湿润剂的选择和添加量需要经过一定的试验和优化,否则可能导致活化效果不佳。
其次,湿法活化需要进行水洗和干燥等后续处理步骤,增加了工艺复杂性和能耗。
此外,湿法活化还存在一定的废水和废液处理问题,需要进行合理处理和回收利用。
湿法碳化活化是一种有效改善活化效果的方法,可以制备具有优良孔隙结构和吸附性能的活性炭材料。
通过合理选择湿润剂种类和添加量,控制反应条件,可以优化活化剂的活性和选择性,提高活性炭的吸附能力和化学稳定性。
活性炭制造的主要工艺过程-回转炉活化法

活性炭制造的主要工艺过程-活化法制造活性炭的关键工艺是活化。
由于所用活化剂的不同,可分为两类方法:(1)用氯化锌或磷酸等化学品为活化剂的化学品活化法;(2)用水蒸气或二氧化碳等为活化剂的气体活化法。
前者称为化学活化法,后者称为物理活化法。
其实两类活化过程都各自发生质的变化,都是化学变化的过程。
1、化学品活化法(一)氯化锌活化法以化学品氯化锌为活化剂。
将0.4~5.0份氯化锌浓溶液和1份泥炭或锯屑混合,在转炉中下燥,加热到600~700℃,成品以酸洗和水洗回收锌盐。
有时化学品活化后继续进行水蒸气活化,藉以增加活性炭的细孔。
氯化锌活化的活性炭具较多大孔。
虽然这是有效和简单的方法,但因锌化合物的环境污染而渐衰。
(二)磷酸活化法以化学品磷酸为活化剂。
炭化的或未炭化的含碳物作起始原料。
例如将研细的锯屑和磷酸混成浆状,在转炉中干燥,加热到400~600℃。
萃取回收磷酸,有时中和后回收磷酸盐。
于燥得活性炭,一般较氯化锌法的活性炭具有更细的细孔。
也可采用磷酸和水蒸气联合活化法。
近年磷酸活化法趋向广泛应用,磷酸回收等革新未见发表。
(三)氢氧化钾活化法以化学品氢氧化钾为活化剂。
将含碳原料以熔融的无水氢氧化钾处理,激烈的反应产生非常高的多孔性,比表而积可高达3000m2/g。
(四)其他化学品活化法硫酸、硫化钾、氯化铝、氯化钱、硼酸盐、硼酸、氯化钙、氢氧化钙、氯气、氯化氢、铁盐、镍盐、硝酸、亚硝气、五氧化二磷、金属钾、高锰酸钾、金属钠、氧化钠和二氧化硫均可用于活化。
2、气体活化法以水蒸气、二氧化碳或两者的混合气体为活化剂,将含碳物料和气体在转炉或者沸腾炉内,在800~1000℃高温下进行碳的氧化反应,制成细孔结构发达的活性炭。
水蒸气、二氧化碳和碳的反应是吸热反应,而氧和碳的反应是很强的放热反应,因此炉内反应温度难以控制,尤其要避免局部过热,防止不均匀活化更难,故氧或空气不宜作为活化剂。
有时使用空气和水蒸气的混合气体,用碳的燃烧作为热源。
活性炭活化原理

精心整理活性炭的活化机理及应用活性炭是一种非常优良的吸附剂,它是利用植物原料(木屑、木炭、果壳、果核)、煤和其它含碳工业废料作原料,通过物理和化学方法对原料进行破碎、过筛、催化剂活化、漂洗、烘干和筛选等一系列工序加工制造而成。
根据活化介质的不同,活性炭活化方法分为物理活化法、化学活化法和物理—化学复合活化法。
物理活化水蒸汽、二氧化碳、空气或它们的混合气体对环境污染小,因其依靠氧化碳原子形成孔隙结构,活化温度较高且活性炭得率低。
化学活化法活性炭得一.1.CO+H2般在800上述三个化学反应均是吸热反应,即随着活化反应的进行,活化炉的活化反应区域温度将逐步下降,如果活化区域的温度低于800℃,上述活化反应就不能正常进行,所以在活化炉的活化反应区域需要同时通入部分空气与活化产生的煤气燃烧补充热量,或通过补充外加热源,以保证活化炉活化反应区域的活化温度。
活化反应属于气固相系统的多相反应,活化过程中包括物理和化学两个过程,整个过程包括气相中的活化剂向炭化料外表面的扩散、活化剂向炭化料内表面的扩散、活化剂被炭化料内外表面所吸附、炭化料表面发生气化反应生成中间产物(表面络合物)、中间产物分解成反应产物、反应产物脱附、脱附下来的反应产物由炭化料内表面向外表面扩散等过活化反应通过以下三个阶段最终达到活化造孔的目的。
第一阶段是炭化时形成的但却被无序的碳原子及杂原子所堵塞的孔隙的打开,即高温下,活化气体首先与无序碳原子及杂原子发生反应。
第二阶段是打开的孔隙不断扩大、贯通及向纵深发展,孔隙边缘的碳原子由于具有不饱和结构,易于与活化气体发生反应,从而造成孔隙的不断扩大和向纵深发展。
2.化化学法、KOH以(600~800℃)在KOHKOH 的加入也加快了非碳原子N、H等的脱除,KOH活化反应成孔机理就是通过KOH与原料中的碳反应,把其中的部分碳刻蚀掉,经过洗涤把生成的盐及多余的KOH洗去,在被刻蚀的位置出现了孔。
这一过程主要发生以下反应:4KOH+—CH2一K2CO3+K2O+3H2K2CO3+2—C—2K+3COK2O+—C—2K+CO2KOHK2O+H2OC+H2OH2+COCO+H20H2+C02K2O+CO2K2CO3K2O+H22K+H2OK2O+C2K+CO在KOH活化法制备活性炭时,活化后的洗涤是关键。
活性炭工艺流程

活性炭工艺流程
《活性炭工艺流程》
活性炭是一种可以吸附有机物质和杂质的多孔炭材料,广泛应用于水处理、空气净化、医药和化工等领域。
其工艺流程是通过碳质原料的炭化、活化和筛选等步骤来制备活性炭的过程。
首先是碳质原料的选择和炭化。
通常选择木质材料、果壳、煤炭等作为原料,经过干燥和碎粉后进行高温炭化,将原料中的挥发性物质和杂质热解出来,得到初步的炭素材料。
接下来是活化的过程。
活化是指在一定条件下,将初步炭素材料中的残余杂质和碳骨架中的孔道进一步发育,增大比表面积,提高活性炭的吸附能力。
活化通常采用物理活化和化学活化两种方式进行。
物理活化是利用高温和气体流动来使炭素材料孔道扩展,而化学活化则是通过与碱性或酸性物质的作用来改变炭素材料的结构,增加孔道数量和大小。
最后是筛选和包装。
经过活化的炭素材料会经过筛选和处理,去除颗粒不均匀的部分,然后便于包装和存储。
以上就是活性炭工艺流程的基本步骤,通过这一系列的操作可以生产出不同种类和规格的活性炭产品,满足不同领域的需求。
活性炭的应用范围广泛,随着环保意识的提高,其市场需求也将持续增长。
活性炭活化原理

活性炭活化原理、火化炉性能参数1.工作原理采用水蒸汽、烟道气(主要成分为CO2)或其混合气体等含氧气体作为活化剂,在高温下与炭接触发生氧化还原反应进行活化,生成一氧化碳、二氧化碳、氢气和其它碳氢化合物气体,通过碳的气化反应(“烧失”)达到在碳粒中造孔的目的.其主要化学反应式如下:C+2H2O 2H2+CO2—18kcal ①C+H2O H2+CO-31kcal ②CO2+C 2CO—41kcal ③上述三个化学反应均是吸热反应,即随着活化反应的进行,活化炉的活化反应区域温度将逐步下降,如果活化区域的温度低于800℃,上述活化反应就不能正常进行,所以在活化炉的活化反应区域需要同时通入部分空气与活化产生的煤气燃烧补充热量,或通过补充外加热源,以保证活化炉活化反应区域的活化温度。
活化反应属于气固相系统的多相反应,活化过程中包括物理和化学两个过程,整个过程包括气相中的活化剂向炭化料外表面的扩散、活化剂向炭化料内表面的扩散、活化剂被炭化料内外表面所吸附、炭化料表面发生气化反应生成中间产物(表面络合物)、中间产物分解成反应产物、反应产物脱附、脱附下来的反应产物由炭化料内表面向外表面扩散等过活化反应通过以下三个阶段最终达到活化造孔的目的。
第一阶段是炭化时形成的但却被无序的碳原子及杂原子所堵塞的孔隙的打开,即高温下,活化气体首先与无序碳原子及杂原子发生反应.第二阶段是打开的孔隙不断扩大、贯通及向纵深发展,孔隙边缘的碳原子由于具有不饱和结构,易于与活化气体发生反应,从而造成孔隙的不断扩大和向纵深发展。
第三阶段是新孔隙的形成,随着活化反应的不断进行,新的不饱和碳原子或活性点则暴露于微晶表面,于是这些新的活性点又能同活化气体的其它分子进行反应,微晶表面的这种不均匀的燃烧就不断地导致新孔隙的形成。
活化工艺控制的主要操作条件包括活化温度、活化时间、活化剂的流量及温度、加料速度、活化炉内的氧含量等.炭化料经破碎筛分,筛选合格炭粒作为活化原料,太粗的炭粒返回破碎筛分,太细的炭粒返回作为燃料使用,合格炭粒由斗提机提升到活化炉炉顶部加入炉内,借助炭化料的重力缓慢加入,炭每隔一定时间加入活化炉的炉内,与送入的过热蒸汽反应,炭在逐步下降过程中被蒸汽加热干燥,实现活化,最后经冷却由最下端卸料口隔一段时间卸出.水蒸气先经预热至300~400℃送至活化管内作为活化介质,与炭化料并流由上而下,在流动过程中不断与炭粒接触,经过一系列活化反应,在活化管下部烧失炭变成水煤气,水煤气与活化炭一同进入冷却段后在分离管内被分离出来,由下连烟道送到底部活化管外炉膛燃烧,由二次空气管吸入空气以满足燃烧需要,燃烧产生的高温烟气,通过蓄热室将热量传递给格子阵进行热交换,维持炉温,使活化反应继续不断地进行。
活性炭生产之活化
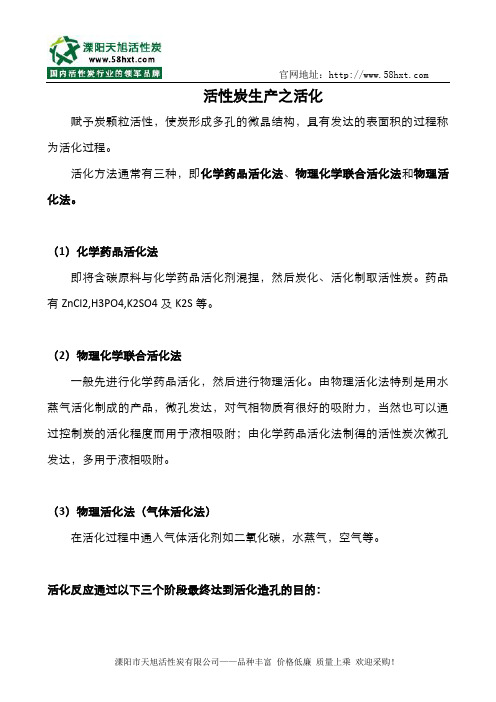
官网地址:活性炭生产之活化赋予炭颗粒活性,使炭形成多孔的微晶结构,具有发达的表面积的过程称为活化过程。
活化方法通常有三种,即化学药品活化法、物理化学联合活化法和物理活化法。
(1)化学药品活化法即将含碳原料与化学药品活化剂混捏,然后炭化、活化制取活性炭。
药品有ZnCl2,H3PO4,K2SO4及K2S等。
(2)物理化学联合活化法一般先进行化学药品活化,然后进行物理活化。
由物理活化法特别是用水蒸气活化制成的产品,微孔发达,对气相物质有很好的吸附力,当然也可以通过控制炭的活化程度而用于液相吸附;由化学药品活化法制得的活性炭次微孔发达,多用于液相吸附。
(3)物理活化法(气体活化法)在活化过程中通入气体活化剂如二氧化碳,水蒸气,空气等。
活化反应通过以下三个阶段最终达到活化造孔的目的:官网地址: 第一阶段:开放原来的闭塞孔。
即高温下,活化气体首先与无序碳原子及杂原子发生反应,将炭化时已经形成但却被无序的碳原子及杂原子所堵塞的孔隙打开,将基本微晶表面暴露出来。
第二阶段:扩大原有孔隙。
在此阶段暴露出来的基本微晶表面上的碳原子与活化气体发生氧化反应被烧失,使得打开的孔隙不断扩大、贯通及向纵深发展。
第三阶段:形成新的孔隙。
微晶表面上的碳原子的烧失是不均匀的,同炭层平行方向的烧失速率高于垂直方向,微晶边角和缺陷位置的碳原子即活性位更易与活化气体反应。
同时,随着活化反应的不断进行,新的活性位暴露于微晶表面,于是这些新的活性点又能同活化气体进行反应。
微晶表面的这种不均匀的燃烧不断地导致新孔隙的形成。
随着活化反应的进行,孔隙不断扩大,相邻微孔之间的孔壁被完全烧失而形成较大孔隙,导致中孔和大孔孔容的增加,从而形成了活性炭大孔、中孔和微孔相连接的孔隙结构,具有发达的比表面积。
气体活化的基本反应式如下:。
活性炭炭化工艺操作规范
活性炭炭化工艺操作规范炭化:成型物料的炭化,是指在较低温度(600℃以下)条件下,物料中煤焦油低分子物质的挥发和煤及沥青的热分解和固化的过程。
炭化是生产活性炭的重要工序之一,该过程是把原料隔绝空气加热,使非碳元素减少,以生产出适合活化工序所需要的碳质材料的工序,是活化前的主要准备与基础。
炭化质量好坏直接影响下一步活化的操作以及最终活性炭产品的质量。
炭化过程通常包括物料的炭化和炭化尾气处理两部分。
炭化的原理:炭化过程中大部分非炭元素—氢和氧因原料的高温分解首先以气体形式被排除,而获释的元素碳原子则组合成通称为基本石墨微晶的有序结晶生成物。
严格的说,炭化应是在隔绝空气的条件下进行,一般温度在500-600℃左右。
炭化过程:1.干燥阶段这个阶段的温度在20—150摄氏度,热解速度非常缓慢,主要是木材中所含水分依靠外部供给的热量进行蒸发,木质材料的化学组成几乎没有变化。
2.预炭化阶段这个阶段的温度为50—275摄氏度,木质材料热分解反应比较明显,木质材料化学组成开始发生变化,其中不稳定的组分,如半纤维素分解生成二氧化碳、一氧化碳和少量醋酸等物质。
以上两个阶段都要外界供给热量来保证热解温度的上升,所以又称为吸热分解阶段。
3.炭化阶段这个阶段的温度为75—400摄氏度,在这个阶段中,木质材料急剧地进行热分解,生成大量分解产物。
生成的液体产物中含有大量醋酸、甲醇和木焦油,生成的气体产物中二氧化碳含量逐渐减少,而甲烷、乙烯等可燃性气体逐渐增多。
这一阶段放出大量反应热,所以又称为放热反应阶段。
4.煅烧阶段温度上升450—500摄氏度,这个阶段依靠外部供给热量进行柱状活性炭和粉状活性炭的煅烧,排出残留在活性炭中的挥发性物质,提高活性炭的固定碳含量。
这时生成液体产物已经很少。
应当指出,实际上这四个阶段的界限难以明确划分,由于炭化设备各个部位受热量不同,木质材料的导热系数又较小,因此,设备内木质材料所处的位置不同,甚至大块木材的内部和外部,也可能处于不同热解阶段。
活性炭的KOH活化法
活性炭的KOH活化法
KOH活化法是20世纪70年代兴起的⼀种制备⾼⽐表⾯积活性碳的活化⼯艺,与氯化锌活化⼯艺相似,活化⼯艺的效果也受到活化温度、活化时间、活化剂的⽤量等因素的影响。
有⼈以⽟⽶芯为原料,利⽤KOH为活化剂,与在400-600℃碳化后的材料混合,在活化温度850℃,⽕花时间1.2h的条件下制备出⽐表⾯积⼤于2700m2/g的活性碳。
并对碳化温度,活化温度,升温速率,活化温度、活化时间以及不同KOH与原料的配⽐等因素对活性碳性能的影响进⾏了研究。
在不同的碳化温度相同的碳化时间下使⽟⽶芯碳化,测量所得炭材料的⽐表⾯积,最后确定在碳化温度为400-600℃条件可使炭材料的⽐表⾯积达到2700m2/g以上,并且碳化时间在4h的条件下可以使碳化后的炭材料的⽐表⾯积达到最⼤。
所以最后确定的碳化⼯艺为:碳化温度400-600℃,碳化时间4h。
活性炭的工作原理
活性炭的工作原理
活性炭是一种高度孔隙化的碳质材料,其工作原理是通过吸附和化学反应来去除或转化有害物质。
活性炭的孔隙结构提供了巨大的表面积,使其具有很强的吸附能力。
正因为如此,活性炭可以吸附空气中的有害气体和颗粒物。
当空气中的有害物质接触到活性炭表面时,它们会被物理吸附或化学吸附。
物理吸附是分子间的吸附作用力,而化学吸附则是通过化学反应将有害物质转化为无害物质。
活性炭常用于空气净化、水处理和防护装备等领域。
在空气净化中,活性炭被用于去除甲醛、二氧化硫、苯、氨气等有害气体。
它还可以去除异味,如烟味、厨房油烟味等。
在水处理中,活性炭被用于去除水中的有机物质、异味和颜色。
此外,活性炭还可用于防护装备,吸附化学战剂和有毒气体。
然而,由于活性炭的吸附饱和度有限,需要定期更换或再生。
一般来说,活性炭的吸附性能会随着使用时间的增加而降低。
因此,定期检查和更换活性炭是确保其有效工作的重要步骤。
活性炭的工作原理
活性炭的工作原理活性炭是一种具有高比表面积和多孔结构的吸附剂,由于其独特的性质,在环境保护、水处理、空气净化和工业生产中起着重要的作用。
活性炭的工作原理主要是通过吸附作用将有害物质从气体或溶液中去除。
活性炭通常是由天然无机物(如树木、椰壳、藤壳等)经过碳化和活化处理而成。
其特点是比表面积大、多孔结构发达,并具有良好的物理化学性质。
这些特性使得活性炭具有较高的吸附性能和催化性能。
活性炭具有很高的比表面积,通常在500-2000平方米/克之间,甚至高达3000平方米/克以上。
这是由于其多孔结构的存在,表面积因此得以增加。
这些微小的孔道提供了许多的吸附位点,使得活性炭可以吸附大量的分子。
活性炭吸附的原理主要是靠物质表面的静电力、范德华力、孔道效应等因素。
首先,活性炭表面常常带有一些极性团,如羟基(—OH)、胺基(—NH2)等,这些团可以吸引极性分子,如水分子和有机化合物。
其次,活性炭表面还带有很多孔道,这些孔道形成了一个像海绵一样的结构,使得活性炭具有很大的吸附容量。
此外,活性炭的表面电位常常较低,可以吸引带有正电荷的离子。
活性炭的孔道多种多样,可以分为微孔、中孔和宏孔。
其中,微孔是活性炭吸附的主要位置,其孔径在0.8-2纳米之间。
微孔通常具有极高的比表面积,可以吸附一些小分子,如氧气、二氧化碳、氮气等。
中孔的孔径在2-50纳米之间,可以吸附一些中等大小的分子,如水分子和一些有机物。
宏孔的孔径在50纳米以上,可以吸附较大的分子,如重金属离子和某些有机溶剂。
活性炭选择吸附物质的主要环节是靠物质分子与活性炭表面之间的分子间的相互作用力。
常见的有静电作用力、范德华力和毛细作用力。
静电作用力主要是指分子范围内两个相邻分子的电荷间的作用力。
范德华力主要是吸附分子之间的电子间的分子间力,而毛细作用力主要是指吸附分子和活性炭之间的毛细现象。
这些力对分子的吸附有重要的影响,决定了分子是否能够被活性炭吸附。
活性炭的吸附性能不仅与其孔道结构和表面性质有关,还与环境条件有关。
- 1、下载文档前请自行甄别文档内容的完整性,平台不提供额外的编辑、内容补充、找答案等附加服务。
- 2、"仅部分预览"的文档,不可在线预览部分如存在完整性等问题,可反馈申请退款(可完整预览的文档不适用该条件!)。
- 3、如文档侵犯您的权益,请联系客服反馈,我们会尽快为您处理(人工客服工作时间:9:00-18:30)。
活性炭的活化机理及应用
材研1407 朱明2014200483 活性炭是一种非常优良的吸附剂,它是利用植物原料(木屑、木炭、果壳、果核)、煤
和其它含碳工业废料作原料,通过物理和化学方法对原料进行破碎、过筛、催化剂活化、漂洗、烘干和筛选等一系列工序加工制造而成。
根据活化介质的不同,活性炭活化方法分
为物理活化法、化学活化法和物理—化学复合活化法。
物理活化水蒸汽、二氧化碳、空气
或它们的混合气体对环境污染小,因其依靠氧化碳原子形成孔隙结构,活化温度较高且活
性炭得率低。
化学活化法活性炭得率较高,孔隙发达,吸附性能好。
但此法对设备腐蚀性大,环境污染严重。
热解能量循环利用困难。
而且活性炭中残留化学药品.在应用方面受
到限制。
一.活性炭的活化机理
1.物理活化法
物理活化法一般分两步进行,先将原料在500℃左右炭化,再用水蒸汽或CO2 等气体在高温下进行活化。
高温下,水蒸汽及二氧化碳都是温和的氧化剂,碳材料内部C原子与活化剂结合并以CO+H 2或CO的形式逸出,形成孔隙结构。
物理活化法所需的活化温度一般较化学活化法高,而且活化所需的时间也更长,因此耗能比较大,成本高。
尽管有这些缺点,物理活化法在实际生产中的应用仍然十分广泛,原因在于其制得的活性炭无需过多
的后处理步骤,不像化学活化法制得的活性炭需要除去残留的活化剂。
将炭化材料在高温下用水蒸气、二氧化碳或空气等氧化性气体与炭材料发生反应,使炭材料中无序炭部分氧化刻蚀成孔,在材料内部形成发达的微孔结构。
炭化温度一般在600℃,活化温度一般在800℃∽900℃。
其主要化学反应式如下:
C+2H2O 2H2+CO2 △H=18kcal
C+H2O H2+CO △H=31kcal
CO2+C 2CO △H=41kcal
上述三个化学反应均是吸热反应,即随着活化反应的进行,活化炉的活化反应区域温度将逐步下降,如果活化区域的温度低于800℃,上述活化反应就不能正常进行,所以在活化炉的活化反应区域需要同时通入部分空气与活化产生的煤气燃烧补充热量,或通过补充外加热源,以保证活化炉活化反应区域的活化温度。
活化反应属于气固相系统的多相反应,活化过程中包括物理和化学两个过程,整个过程包括气相中的活化剂向炭化料外表面的扩散、活化剂向炭化料内表面的扩散、活化剂被炭化料内外表面所吸附、炭化料表面发生气化反应生成中间产物(表面络合物)、中间产物分解
成反应产物、反应产物脱附、脱附下来的反应产物由炭化料内表面向外表面扩散等过活化反应通过以下三个阶段最终达到活化造孔的目的。
第一阶段是炭化时形成的但却被无序的碳原子及杂原子所堵塞的孔隙的打开,即高温下,活化气体首先与无序碳原子及杂原子发生反应。
第二阶段是打开的孔隙不断扩大、贯通及向纵深发展,孔隙边缘的碳原子由于具有不饱和结构,易于与活化气体发生反应,从而造成孔隙的不断扩大和向纵深发展。
第三阶段是新孔隙的形成,随着活化反应的不断进行,新的不饱和碳原子或活性点则暴露于微晶表面,于是这些新的活性点又能同活化气体的其它分子进行反应,微晶表面的这种不均匀的燃烧就不断地导致新孔隙的形成。
2.化学活化法
化学活化法是通过将化学试剂嵌入炭颗粒内部结构,经历一系列的交联缩聚反应形成微孔。
化学活化可一步进行,即直接升温到700℃左右进行活化。
在活化前,先将活化剂水溶液与原料以一定比例浸渍一段时间,烘干后再放入惰性气氛中升温进行活化。
活化剂与原料的浸渍比是影响活性炭性能的一个重要因素,因此可以通过控制浸渍比以及不同的活化温度来制备所需的活性炭。
化学活化法制得的活性炭产率高,而且其孔隙结构比物理活化法更加发达。
按活化剂不同分ZnCl2法、KOH法、H3PO4法.相对于物理活化,化学活化有以下优点:化学活化需要较低的温度,活化产率高,通过选择合适的活化剂控制反应条件可制得高比表面积活性炭.但化学活化对设备腐蚀性大,污染环境,其制得的活性炭中残留化学药品活化剂,应用受到限制.
以KOH作为活化剂为例,原料破碎→与KOH混合→低温脱水(200~500℃)→高温活化(600~800℃)→酸洗→热水洗→蒸馏水洗→干燥→产品
在300~600℃时主要发生分子交联或缩聚反应,该阶段除一些非碳元素挥发出来外,焦油类物质的挥发是失重的主要原因。
KOH的加入,抑制了焦油的生成,提高了反应收率。
同时,KOH的加入,使得活化反应的实际温度降低了大约100℃,即在540℃左右就可反应。
在此温度下,KOH的加入也加快了非碳原子N、H等的脱除,KOH活化反应成孔机理就是通过KOH与原料中的碳反应,把其中的部分碳刻蚀掉,经过洗涤把生成的盐及多余的KOH 洗去,在被刻蚀的位置出现了孔。
这一过程主要发生以下反应:
4KOH+—CH2一K2CO3+K2O+3H2 K2CO3+2—C—2K+3CO
K2O+—C—2K+CO 2KOH K2O+H2O
C+H2O H2+CO CO+H20 H2+C02
K2O+CO2K2CO3K2O+H22K+H2O
K2O+C 2K+CO
在KOH活化法制备活性炭时,活化后的洗涤是关键。
未洗时,产品的孔很少。
先后经过酸洗、热水洗、蒸馏水洗,把产品中的非本体物质洗去,它们原来占据的空间就形成了孔.
因此,尽管洗涤比较麻烦,但一定要反复洗涤,直到洗干净为止。
二.活性炭的应用
活性炭广泛应用于工农业生产的各个方面,如石化行业的无碱脱臭(精制脱硫醇)、乙烯脱盐水(精制填料)、催化剂载体(钯、铂、铑等)、水净化及污水处理;电力行业的电厂水质处理及保护;化工行业的化工催化剂及载体、气体净化、溶剂回收及油脂等的脱色、精制;食品行业的饮料、酒类、味精母液及食品的精制、脱色;黄金行业的黄金提取、尾液回收;环保行业的污水处理、废气及有害气体的治理、气体净化;以及相关行业的香烟滤嘴、木地板防潮、吸味、汽车汽油蒸发污染控制,各种浸渍剂液的制备等。
活性炭在未来将会有极好的发展前景和广阔的销售市场。
1.活性炭在气相上的应用
空气净化活性炭空气净化活性炭,选用优质的木材或椰子壳,通过深度活化和独特的孔径调节工艺,使活性炭有丰富的孔,且孔的大小略大于有毒气体,比表面积>1300平方米/克,对于苯,甲醛,氨气等有毒有害气体具有高效能吸附能力,可有效去除室内空气中的气态污染物及有害恶臭物质,进而达到降低污染、净化空气的目的。
工业上用于:各种作业场所的除臭去毒及空调过滤网,空气净化机,中央空调过滤系统,空气过滤器,空气净化器,汽车滤清器等。
其原理是:(1)自身独特的孔隙结构活性炭是一种主要由含碳材料制成的外观呈黑色,内部孔隙结构发达、比表面积大、吸附能力强的一类微晶质碳素材料。
活性炭材料中有大量肉眼看不见的微孔,1克活性炭材料中微孔,将其展开后表面积可高达800-3000平方米,特殊用途的更高。
也就是说,在一个米粒大小的活性炭颗粒中,微孔的内表面积可能相当于一个客厅面积的大小。
正是这些高度发达,如人体毛细血管般的孔隙结构,使活性炭拥有了优良的吸附性能。
(2)分子之间相互作用力也叫“范德华引力”。
虽然分子运动速度受温度和材质等原因的影响,但它在微环境下始终是不停运动的。
由于分子之间拥有相互吸引的作用力,当一个分子被活性炭内孔捕捉进入到活性炭内孔隙中后,由于分子之间相互吸引的原因,会导致更多的分子不断被吸引,直到添满活性炭内孔隙为止。
活性炭吸附有害物质的特性活性炭为物理吸附原理,在作用过程中,依靠空气作为媒介,因此被界定为被动空气净化材料。
2.活性炭在液相上的应用
废水中的一些有机物是难于为微生物或一般氧化法所氧化分解的,如酚、苯、石油及其产品、杀虫剂、洗涤剂、合成染料、胺类化合物以及许多人工合成有机物,经生化处理后很难达到对排放要求较高的水体中排放的标准,也严重影响废水的回用,因此需要深度处理。
由于活性炭对有机物的吸附能力大,在废水深度处理中得到广泛的应用,具有以下优点:①
处理程度高,城市污水用活性炭进行深度处理后,生化需氧量BOD可降低99%,总有机碳量TOC可降到1~3mg/L。
②应用范围广,对废水中绝大多数有机物都有效,包括微生物难于降解的有机物。
③适应性强,对水量及有机物负荷的变动有较强的适应性能,可得到稳定的处理效果。
④粒状炭可进行再生重复使用,被吸附的有机物在再生过程中被烧掉,不产生污泥。
⑤可回收有用物质,例如用活性炭处理含酚废水,用碱再生吸附饱和的活性炭,可以回收酚钠盐。
⑥设备紧凑、管理方便。
3.活性炭在催化上的应用
(1)制造过氧化氢用活性炭覆盖的多孔管作阴极,使从阴极上放出的氢同压入的氧作用生成过氧化氢。
(2)使硫化氢转化为元素硫活性炭能吸附硫化氢并使氧化成元素硫,以除去气体中的硫化氢。
(3)活性炭催化均四氯乙烷脱HCl制备三氯乙烯、甲烷裂解制氢活性炭催化剂。
(4)水的脱氯作用活性炭能起吸附和催化两种作用,从水中除去氯。
(5)用于生产光气,三聚氯氰,氯乙烷,卤化磺酰,农药中间体.由于活性炭的催化作用能使氯和一氧化碳反应生成光气;使二氧化硫和氯反应生成硫酰氯;使氯和氢反应生成氯化氢;使溴和水蒸汽反应生成氢溴酸;使硫酸亚铁氧化硫酸铁;以及作为三聚氯氰聚合物反应的催化剂载体。