PCBA外观--无铅焊点检验标准
某公司PCBA资料外观检验标准
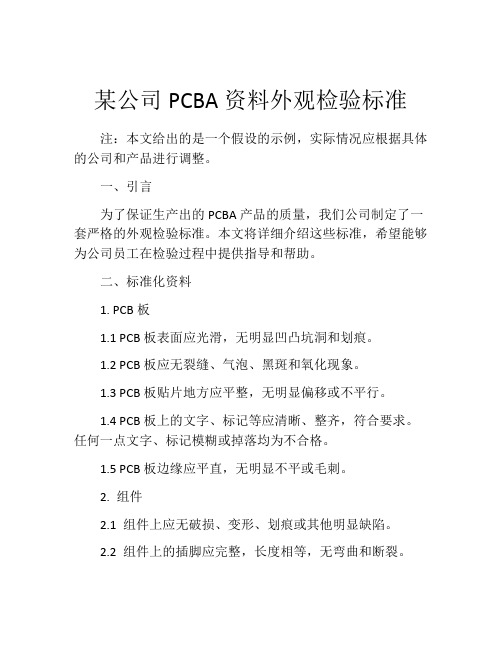
某公司PCBA资料外观检验标准注:本文给出的是一个假设的示例,实际情况应根据具体的公司和产品进行调整。
一、引言为了保证生产出的PCBA产品的质量,我们公司制定了一套严格的外观检验标准。
本文将详细介绍这些标准,希望能够为公司员工在检验过程中提供指导和帮助。
二、标准化资料1. PCB板1.1 PCB板表面应光滑,无明显凹凸坑洞和划痕。
1.2 PCB板应无裂缝、气泡、黑斑和氧化现象。
1.3 PCB板贴片地方应平整,无明显偏移或不平行。
1.4 PCB板上的文字、标记等应清晰、整齐,符合要求。
任何一点文字、标记模糊或掉落均为不合格。
1.5 PCB板边缘应平直,无明显不平或毛刺。
2. 组件2.1 组件上应无破损、变形、划痕或其他明显缺陷。
2.2 组件上的插脚应完整,长度相等,无弯曲和断裂。
2.3 组件上的焊点应均匀、无气泡、无明显渗透、无分层。
同时焊点的封度应保持良好。
2.4 组件的上表面或保护层应整齐、无泡、无皱褶、无明显瑕疵。
2.5 组件的结构应牢固、无松动、无缺损。
3. 整体功能3.1 PCBA上所有连接线路的通电和短路都应测量一次,测试设备读数正确,报警,显示一致。
3.2 PCB板上测试点的读数应符合其规格范围,且不得有异常信号,如短路、开路等。
3.3 整个PCBA可正常呼吸灯,并符合规格要求。
3.4 没有其他未列出的损坏、缺陷等。
三、检验过程1. 前检1.1 所有PCBA必须在生产前检查一遍,检查目的是发现潜在的问题。
1.2 前检应由生产人员进行,结果必须由质量控制人员审核和签字确认。
2. 初检2.1 初检应在PCBA生产完成后的第一时间进行。
2.2 初检应由一名质量控制人员进行,检查结果必须记录在检验表格上。
2.3 PCBA有任何一个不合格项,则PCBA必须送回生产部门重新制作。
3. 终检(出货前检验)3.1 终检是产品质量的最后一个把关,不得有任何疏漏。
3.2 所有产品必须经过严格的终检,通过检验后才能出货。
PCBA 检验标准 焊点基本要求

PCBA检验标准焊点基本要求1 范围本标准规定了PCBA的软钎焊焊点的总体质量要求和主要种类的焊点缺陷。
本标准适用于华为公司内部工厂及PCBA外协工厂的SMT、波峰焊及手工焊后对PCBA上焊点的锡铅焊点和无铅焊点的检验。
本部分标准应与本标准的第三、四部分联合使用。
2 规范性引用文件下列文件中的条款通过本标准的引用而成为本标准的条款。
凡是注日期的引用文件,其随后所有的修改单(不包括勘误的内容)或修订版均不适用于本标准,然而,鼓励根据本标准达成协议的各方研究是否可使用这些文件的最新版本。
凡是不注日期的引用文件,其最新版本适用于本标准。
3 焊点基本要求本标准给出各种级别电子装联产品软钎焊焊点的外观合格性总体要求和典型缺陷,包括SMT焊点、THT焊点、端子焊点。
本标准中的焊点的焊接方法包括但不限于回流焊、波峰焊、拖焊、浸焊、烙铁焊、电阻焊。
作为例外,引线和焊端外表面浸了锡、钯、金的,其焊点外观检验以具体设计文件要求为准,本标准只能参照执行。
不能单凭一般性的外表来判断焊点好坏。
合格的焊点必须呈现润湿特征,焊料良好地附着在被焊金属表面。
润湿的焊点,其焊缝外形特征是呈凹形的弯液面,判定依据是润湿时焊料与焊盘,焊料与引线 / 焊端之间的界面接触角较小或接近于零度。
通常焊料合金的范围很宽,可以表现出从很低甚至接近0度的接触角直到接近90度的接触角。
如果焊接面有部分面积没有被焊料合金润湿,则一般认定为不润湿状态,这时的特征是接触角大于90°。
如图1之A、B所示,焊点润湿角都不超过90度,合格;但C、D所示接触角虽然超过90度,属于例外情况,也是合格的,原因是焊点轮廓由于设计要求延伸到焊接区域外部边缘和阻焊膜。
图1 几种典型润湿角度本标准提供了锡铅焊点和无铅焊点可视检查标准,无铅的图片均标以:所有锡铅焊点应当有光亮的,大致光滑的外观,并在被焊金属表面形成凹形的弯液面。
通常无铅焊点表面更灰暗、粗糙一些,接触角通常更大一些。
pcba外观检验标准与手法

PCBA(Printed Circuit Board Assembly)外观检验标准与手法如下:一、外观检验标准元件焊点:焊锡球应符合最小电气间隙,焊锡球应固定在免清除的残渣内或覆盖在保形涂覆下。
焊锡球的直径应≤0.13mm,否则会被拒收。
元件侧立:宽度对高度比例不超过二比一,元件可焊端与PAD表面应完全润湿,元件大于1206类时将被拒收。
元件立碑:片式元件末端翘起(立碑)将无法通过检验。
元件扁平、L形和翼形引脚偏移:最大侧面偏移不大于引脚宽度或0.5mm(0.02英寸),否则会被拒收。
圆柱体端帽可焊端侧面偏移:侧面偏移≤元件直径宽度或PAD宽度25%,否则会被拒收。
片式元件矩形或方形可焊端元件侧面偏移:侧面偏移≤元件可焊端宽度或PAD宽度50%,否则会被拒收。
J形引脚侧面偏移:侧面偏移≤引脚宽度50%,否则会被拒收。
元件反向:元件上的极性点与PCB二极管丝印方向一致,否则将被拒收。
元件锡量过多:最大高度焊点可以超出PAD或延伸至可焊端的端帽金属镀层顶部,但不可延伸至元件体,否则将被拒收。
元件空焊:元件引脚与PAD之间焊接点良湿润饱满,元件引脚无翘起,否则将被拒收。
元件冷焊:回流过程锡膏完全延伸,焊接点上的锡完全湿润且表面光泽,否则将被拒收。
元件少件或多件:BOM清单要求某个贴片位号需要贴装元件却未贴装元件或不需要贴装元件却已贴装元件,将被拒收。
元件损件:任何边缘剥落小于元件宽度或元件厚度25%,末端顶部金属镀层缺失最大为50%(各末端),否则将被拒收。
元件起泡和分层:起泡和分层的区域不超出镀通孔间或内部导线间距的25%,否则将被拒收。
二、外观检验手法目视检验:通过肉眼或低倍放大镜对PCBA进行外观检查,主要查看上述问题点。
自动光学检测(AOI):通过高倍放大镜和摄像机对PCBA进行自动扫描,对图像进行识别和处理,发现和记录存在的问题。
电子显微镜检测(SEM):利用电子显微镜对PCBA进行高倍放大,以便发现更细微的问题。
PCBA外观检验标准

1.目的建立PCBA外观目视检验,使产品检验之判定有所依循,同时依此检验结果的回馈、分析、矫正,以确保产品之质量。
2.适用范围本标准通用于本公司生产任何产品PCBA的外观检验(在无特殊规定的情况外)。
包括公司内部生产和发外加工的产品。
特殊规定是指:因零件的特性或其它特殊需求,则PCBA的标准可加以适当修订,但其有效性应超越通用型的外观标准。
3.职责3.1IQC负责根据本规范对公司外协加工返回的PCBA进行检验。
3.2IPQC负责根据本规范对公司自加工的PCBA进行检验。
4.作业程序及标准要求4.1产品来料包装4.1.1为防止PCBA损坏,来料需双层防护:防护外箱(防静电周转箱或纸箱)+内部隔离(防静电珍珠棉或气泡棉),PCBA板之间以及PCBA板与箱体之间应用适当的空间,不可挤压。
4.1.2每层PCBA板应用纸板或防静电珍珠棉隔开,顶层加一层防静电珍珠棉。
若为周转箱则顶面有大于50mm的空间,保证周转箱叠放时不要压到。
4.2检验作业规范4.2.1检验前应先确保检验环境的光照应充足,工作平台清洁、接地。
4.2.2在接触前,为防止元件被静电击坏、手指污染,应戴上ESD防护手套或指套、防静电手环并确保接地。
4.2.3若在无可靠的静电防护条件时,应手持电路板边缘部位,禁止用裸手触摸导体、焊接点及层压板表面。
4.2.4检验目视距离约30-40cm,必要时以放大镜等工具辅助确认。
4.2.5检验发现的不合格时应贴上不合格指示标签,同时单独存放于不合格品区或框内。
4.2.6返修或返工PCBA时应将原不合格指示标签贴回原处,以便品质重点核查。
4.2.7返修或返工后的产品应按正常程序报检,检验除原不合格处重点检查外,其余也需按正常流程作全面检验。
4.2.8检验合格后,由检验员在PCBA版的安装正面的右上角螺丝孔处,用黑色记号笔划一条过孔斜线。
如下图示例:4.2.9检验合格的PCBA经调试合格后,应及时喷三防漆(双面)。
PCBA外观检验标准

翰硕/百一宽带科技(深圳)有限公司一.名词解释:⏹缺件: PCB上相应位置未按要求贴装组件.⏹空焊: 组件脚未吃锡或吃锡少与焊点面积的3/4(贴片组件为吃锡面积小于组件宽度的1/2).⏹连锡: 由于作业异常,将原本在电气上不通的俩点用锡连接.⏹错件: PCB上所贴装组件与BOM上所示不符⏹虚焊: 组件引脚未良好吃锡,无法保证有效焊接(包括假焊)⏹冷焊: 焊点表面成灰色,无良好湿润.⏹反向: 组件贴装后极性与文件规定的相反⏹立碑: 贴片组件一端脱离焊盘翘起,形成碑状⏹反背: 组件正面(丝印面)朝下,但焊接正常⏹断路: 组件引脚断开或PCB板上线路断开⏹翘起: 线路铜箔或焊盘脱离PCB板面翘起超过规格⏹多件: 文件指示无组件的位置,而对应PCB板面上有组件存在⏹锡裂: 通常是焊点受到外力后,焊接点和组件引脚分离,对焊接效果产生影响或隐患⏹浮高: 组件与PCB表面的距离超过规定高度⏹混料: 不同料号或版本的物料混用⏹裸铜: PCB表面防焊绿漆被破坏,铜箔直接暴露在空气中⏹空脚: 组件至少有一个引脚悬空或未完全焊接到位⏹偏移: 组件偏移出焊盘范围超过规格要求⏹锡洞: 焊点上出现空洞的大小超过规格要求而影响焊接质量⏹脏污: 混浊性污染造成目视组件困难或赃物还有可能污染到板面其它部分⏹少锡: 焊点表面仅有一层薄锡或锡未充满焊点.⏹异物: 板面残留除正常焊接以外的其它物质,如:油污,纤维丝,胶状物等⏹破损: PCB纹或残缺⏹及组件表面有裂⏹目的:⏹本文件為數字衛星摟收機之PCBA板的最終檢驗(FQC)工作引導!⏹適用范圍:⏹本文件適用於翰碩/百一公司衛星摟收機之PCBA.二.抽样方案⏹4.1 批量(Lot Size): PCBA的最终检验是以一批的数量为基础来执行的.⏹4.2 抽样计划(Sampling Plan): 采用美军军标MIL-STD-105E(II)单次抽样检验计划. 规定的AQL为: CRI=0, MAJ=0.4, 同时定义: 三个次缺=一个主缺,主次缺合并计算.⏹4.3 抽样方法(Sampling Method): 采用随机抽样的方式随线均匀抽齐全部样本.三.缺点定义⏹严重缺点(CRITICAL DEFECT, 简写为CRI): 不良缺陷, 足使产品失去规定的主要或全部功能, 或者可能带来安全问题, 或者为客户或市场拒绝接受的缺点, 称为严重缺点.⏹主要缺点(MAJOR DEFECT, 简写为MAJ): 不良缺陷, 足使产品失去部分功能, 或者相对严重的结构及外观异常, 从而显著降低产品使用性的缺点, 称为主要缺点.⏹次要缺点(MINOR DEFECT, 简写为MIN): 不良缺陷, 可以造成产品部分性能偏差, 或者一般外观缺点, 虽不影响产品性能, 但会使产品价值降低的缺点, 称为次要缺点.四.允收/拒收的判定⏹任何一批的抽样检验结果, 其不合格品(不良品)数小于或等于抽样计划规定的允收数量, 则整批允收. 不合格品(不良品) 须经生产部返修, 再经FQC检验, 直至修复之不良品符合要求⏹任何一批的抽样检验结果, 其不合格品(不良品)数大于或等于抽样计划规定的拒收数量, 则整批拒收. 拒收批的处理依据相关文件的规定办理.⏹不论任何一个(1 Piece)样本上有多少个质量缺陷项, 都应记录在日报及入库单中. 当板子存在任何主要缺陷时, FQC须填写相应的<<生产异常通知单>> ,同时IPQC 要加强在产线针对此类问题的巡检.⏹检验过程中发现不良品后,不应停止检验,还需检够规定的抽验数量.不论整批拒收与否, 不合格品必须剔除. 剔除之不合格品依据相关文件的规定处置.五.检验条件⏹在正常室内白色冷莹光灯管的照明条件(灯光强度为100-300流明).即正常的40w日光灯下;⏹将待测品置于检测者面前,目距约30cm.⏹应以两种角度观察:正常方式,视线与待检件呈45度角以利光反射; 垂直方式,视线与待检件垂直.每面停留时间为5秒钟;六.以下標示的注解⏹#:严重缺点⏹×:主要缺点⏹△:次要缺点⏹ N:个数⏹ L:长度⏹ H:高度⏹ D: 直径⏹ W:宽度七.板面之标记⏹△丝印/条形码模糊(可以辨认/扫描) 或条形码倾斜>15°⏹△ICT/PASS标签漏贴﹑多贴﹑贴错位置⏹△ICT/PASS标签贴住丝印﹑焊盘﹑测试点及螺丝孔⏹△贴片组件表面丝印无法辨认⏹×丝印/条形码漏印﹑方向错乱﹑影像重迭﹑模糊(不可辨认/扫描)⏹×丝印/条形码缺损影响辨认且无法扫描⏹×条形码﹑版本贴纸漏贴⏹重工应在PCB四角做点状标记﹐从右上角开始顺时针依次记录各重工项目.八.P C B A之防焊绿漆:如无特殊要求(如散件出货等),则依以下规格检验⏹a. 每面不露铜划/刮伤(浅划/刮伤)目视无影响可忽略不计⏹b.刮伤面积×线路上露铜每处面积S≧9mm2 N≧3×非线路露铜每处面积S≧16mm2 N≧5×每面划/刮伤总数N>5 ×每面累计面积 S>1cm2⏹所有露铜性划/刮伤,不可使PCB线路受损超过铜箔厚度的20%,且须经过补漆处理方可允收.⏹要求两个划/刮伤之间距离至少大于2cm.⏹所补绿漆除满足上述规格外,还应以目视是否明显来判定可否允收九.金属材质组件(如t u n e r﹑射频头﹑s c a r t接口等)⏹×生锈﹑变形﹑断裂﹑压痕累计S>9mm2⏹×印刷字体残缺﹑模糊不可辨认⏹×杂质﹑黑点累计面积S≧16 mm2⏹×不可去除之杂质﹑黑点D≧0.8mm , 600mm2面积内N≧4或每面N≧7⏹△不可去除之杂质﹑黑点D<0.8mm , 600mm2面积内N≧6或每面N≧9⏹△印刷字体模糊但可辨认划/刮伤W<0.2mm L≦10mm 忽略不计⏹△每处面积S<<4mm2 但1cm2面积内大于二处⏹× W>0.2mm L>10mm N≧3⏹×每处面积S>4mm2 或1cm2面积内大于二处十.塑料材质组件(如s c a r t座)散件出货⏹×杂质﹑白斑﹑烧焦﹑缺损划/刮伤⏹× W>0.2mm L>5mm N>2 (每面十一.修复品检验电路板修整﹕凡成品﹑半成品,其PCB铜箔或焊盘(PAD)断裂﹑剥离或脱落均属之十二.修复品报废条件⏹PCB铜箔剥离或脱落超过5 cm以上(单一线路)⏹PCB铜箔剥离或脱落3条以上, 且均超过3 cm以上⏹PCB焊垫(PAD)脱落3个以上⏹因高温导致PCB颜色改变成深黄色十三.修复品点胶規定⏹△压合后胶外露的直径, 超过金道或PAD铜箔宽度的一半⏹△胶沾到其它区域或部品,但不影响组装⏹△修补双面板时, 胶溢流到贯穿孔内⏹×胶沾到其它部品影响组装.十四.修复品补漆⏹×散件出货之PCBA每面补漆超过二处⏹△补漆宽度大于线宽的3倍或大于点状面积的2倍⏹△覆盖测试点或焊盘十五.修复品每块板允许的最大修补数⏹×主板点胶数N>3﹐电源板﹑显示板及核心板点胶数N>1⏹×同一组件点胶数大于1个.⏹×飞线总长度大于板长﹑飞线单面超过二条或整块板超过三条⏹点胶﹑飞线﹑补漆异常同时存在时﹐各异常数不超过二点十六.修复品接飞线比例⏹×正常生产接批飞线比例>0.4%⏹×改件品&返修品接飞线比例>3% (以一次改件为原则,2次以上重工改件需MRB决定飞线比例)8. 0 组件安装与焊锡工艺标准图示说明装 1. 横向偏移而突出焊垫的部分不超过组件宽度的1/2,即A≦1/2WACC2. A≦1/2W ACC3. A≧1/2W MAJ4. 纵向偏移电极超过焊盘,即A≦0MAJ5. 纵向偏移组件的电极与焊垫的重迭部分至少为电极宽度的1/5, 即B≦1/5AMAJ6. 三极管三个电极最大偏移量小于或等于三极管电极宽度 (W) 的1/2或0.5mm(此二者以最小为准),即A≦1/2WACC7. 三极管电极突出焊垫, 即D>0MAJ8. B1, B2, B3≧1/2W或0.5mmMAJBAABBB1D9. 三极管倾斜, 但三个电极均未超出焊垫ACC10.零件间距离小于0.2mm即A≦0.2mmMIN11.零件与相邻线路间距离小于0.2mm即A≦0.2mmMIN12. 圆柱状零件电极纵向偏移超出焊垫, 即B≧0MAJ13. 圆柱状零件水平偏移超过电极直径 (D) 的1/4,即A≧1/4DMAJ14. 引脚为”鸥翼”状的零件横向偏移超过电极宽度(W) 的1/2, 即A≧1/2WMAJ15. 引脚为”鸥翼”状的零件纵向偏移超出焊垫, 即B ≧0 MAJ表面贴装AAA1. 溢胶沾染焊盘MIN2. 溢胶a. 溢胶造成电极与PAD 占有红胶b. PAD 溢胶造成焊接不良MAJ3. 胶稍多但未沾染PAD 与引脚ACC影 响 组 装安装孔上过多的焊锡(不平)影响机械组装MAJ溢胶贴片焊锡工艺1.表面黏装型焊锡工艺:上锡高度最少为电极高度的1/4, 最高可超过电极高度, 不能有焊锡浸入电极以外的零件主体部位2.未润湿面积应小于焊盘的25%H1>1/4H2H1>1/4H2ACC3. 焊锡延伸至零件电极以外踫到主体部位MIN4. 锡尖a. 向上不可使组件引脚长度超过本文规定b. 横向超过焊盘范围或使绝缘距离小于0.2mmMAJ5. 连锡或短路MAJ1. 锡点:a. 锡与脚位接触成内弧形b. 锡点表面光洁, 良好湿润.c. 锡点将整个锡位覆盖ACC2. 冷焊锡点表面折皱MAJ T/H组件焊接3. 裂锡, 分层, 焊锡切口MAJ4. T/H组件空焊a. 引脚未上锡b. pad及引脚和灌孔上锡(润湿)不足周围面积的3/4无铅波峰焊接参见EDA-AXXX-005AMAJ5. 锡洞(气孔):穿透性针孔或贯穿性锡洞造成焊点未正常湿润小于焊盘或孔壁面积的25%M IN6. 双面板T/H孔焊锡: 上下层都上锡完整, 锡点程内弧形ACC7. 双面板T/H孔上层未焊锡组件面垂直填充少于75%MAJ8. 包焊:T/H型零件引脚不可见,但从组件面可以确认引脚在孔内.MIN贴片元1. 贴片型组件焊锡后倾斜角度超过15度且不影响功能及组装MINT/ H 组件焊接件倾斜2. 贴片型组件焊锡后倾斜角度超过15度且不影响功能及组装MIN3. T/H型零件在没有安装/配合要求的情况下, 最大倾斜角度超过15度MIN4. 元器件本体到焊盘之间的距离(H)小于0.4mm,大于1.5mmMIN组件浮高1. 无特别要求的贴片型零件最大浮起高度未超过0.25mm或零件高度的1/4ACC2. 无特别要求的贴片型零件最大浮起高度超过0.25mm或零件高度的1/4MIN3. 无特别要求的T/H型零件浮起高度超过0.8mmMIN4.a. 倾斜高度超过1.5mmb. 零件脚未露出MAJ组件破损1. 贴片组件有明显裂缝、破损、表面针孔、切割不良、电镀不良、电极端发黑MAJ2. 组件表面的绝缘涂层受到损伤,造成组件内部的金属材质暴露在外或元件严重形变MAJ1. PCB线路铜箔缺口宽度大于铜箔宽度的30%,即W2>30%W1MAJ插件倾斜W1 W2PCB2. PCB铜箔出现剥离现象(翘起超过一个铜箔厚度)MAJ3. PCB不直接相通的导体间连锡MAJ4. 板变形a.PCB变形大于对角线长度0.75%b.PCBA变形大于对角线长的1%MAJ数码管数码管之间亮度不一比较明显MAJ数码管显示多笔划或少笔划MAJ焊盘修复焊盘点胶范围﹐超过金道或PAD铜箔宽度的一半MIN锡。
pcba测试检验标准
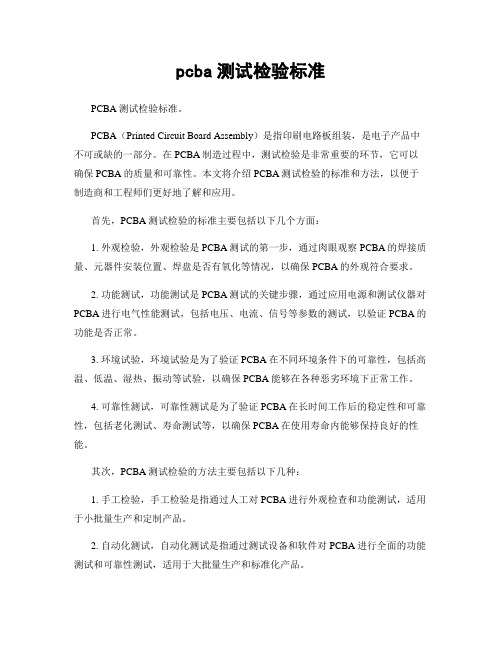
pcba测试检验标准PCBA测试检验标准。
PCBA(Printed Circuit Board Assembly)是指印刷电路板组装,是电子产品中不可或缺的一部分。
在PCBA制造过程中,测试检验是非常重要的环节,它可以确保PCBA的质量和可靠性。
本文将介绍PCBA测试检验的标准和方法,以便于制造商和工程师们更好地了解和应用。
首先,PCBA测试检验的标准主要包括以下几个方面:1. 外观检验,外观检验是PCBA测试的第一步,通过肉眼观察PCBA的焊接质量、元器件安装位置、焊盘是否有氧化等情况,以确保PCBA的外观符合要求。
2. 功能测试,功能测试是PCBA测试的关键步骤,通过应用电源和测试仪器对PCBA进行电气性能测试,包括电压、电流、信号等参数的测试,以验证PCBA的功能是否正常。
3. 环境试验,环境试验是为了验证PCBA在不同环境条件下的可靠性,包括高温、低温、湿热、振动等试验,以确保PCBA能够在各种恶劣环境下正常工作。
4. 可靠性测试,可靠性测试是为了验证PCBA在长时间工作后的稳定性和可靠性,包括老化测试、寿命测试等,以确保PCBA在使用寿命内能够保持良好的性能。
其次,PCBA测试检验的方法主要包括以下几种:1. 手工检验,手工检验是指通过人工对PCBA进行外观检查和功能测试,适用于小批量生产和定制产品。
2. 自动化测试,自动化测试是指通过测试设备和软件对PCBA进行全面的功能测试和可靠性测试,适用于大批量生产和标准化产品。
3. 抽样检验,抽样检验是指通过对PCBA进行抽样检测,以代表整个批次的质量水平,适用于中等规模生产和一般产品。
4. 定期检验,定期检验是指对PCBA进行定期的环境试验和可靠性测试,以确保PCBA的长期稳定性和可靠性,适用于长周期生产和高可靠性产品。
总之,PCBA测试检验是确保PCBA质量和可靠性的重要环节,制造商和工程师们应该根据标准和方法对PCBA进行全面的测试检验,以确保产品质量和客户满意度。
PCBA外观检验标准 (完整)

文件批准Approval Record文件修订记录Revision Record:1、目的Purpose:建立PCBA外观检验标准,为生产过程的作业以及产品质量保证提供指导。
2、适用范围Scope:2.1本标准通用于本公司生产任何产品PCBA的外观检验(在无特殊规定的情况外)。
包括公司内部生产和发外加工的产品。
2.2 特殊规定是指:因零件的特性,或其它特殊需求,PCBA的标准可加以适当修订,其有效性应超越通用型的外观标准。
3、定义Definition:3.1标准【允收标准】 (Accept Criterion):允收标准为包括理想状况、允收状况、拒收状况等三种状况。
【理想状况】 (Target Condition):此组装情形接近理想与完美的组装结果。
能有良好组装可靠度,判定为理想状况。
【允收状况】 (Accept Condition):此组装情形未符合接近理想状况,但能维持组装可靠度故视为合格状况,判定为允收状况。
【拒收状况】(Reject Condition):此组装情形未能符合标准,其有可能影响产品的功能性,但基于外观因素以维持本公司产品的竞争力,判定为拒收状况。
3.2 缺陷定义【致命缺陷】(Critical Defect):指缺陷足以造成人体或机器产生伤害,或危及生命财产安全的缺陷,称为致命缺陷,以CR表示的。
【主要缺陷】(Major Defect):指缺陷对制品的实质功能上已失去实用性或造成可靠度降低,产品损坏、功能不良称为主要缺陷,以MA表示的。
【次要缺陷】(Minor Defect):系指单位缺陷的使用性能,实质上并无降低其实用性,且仍能达到所期望目的,一般为外观或机构组装上的差异,以MI表示的。
3.3焊锡性名词解释与定义:【沾锡】(Wetting) :系焊锡沾覆于被焊物表面,沾锡角愈小系表示焊锡性愈良好。
【沾锡角】 (Wetting Angle) 被焊物表面与熔融焊锡相互接触的各接线所包围的角度(如附件),一般为液体表面与其它被焊体或液体的界面,此角度愈小代表焊锡性愈好。
PCBA外观检验标准
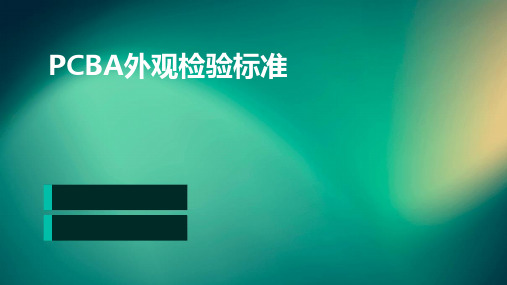
04 PCBA外观检验流程
初Hale Waihona Puke 目视检查总结词初步目视检查是外观检验的第一步, 主要通过肉眼观察PCB板的表面是否 存在明显的缺陷或异常。
目的
确保PCBA的质量和可靠性,及时发现 并处理潜在的问题,防止不合格产品 流入下一道工序或最终用户手中。
检验的重要性
确保产品质量
通过外观检验,可以及时发现并处理 PCBA上存在的各种问题,如焊接缺 陷、元器件缺失或错位等,从而保证 产品的质量和可靠性。
提高生产效率
维护企业形象
高质量的产品可以提升企业的形象和 信誉,增强消费者对企业的信任和忠 诚度。
利用机器视觉技术进行高精度、高效率的外 观检测,提高检测的可靠性和准确性。
人工智能与大数据分析
结合人工智能和大数据技术,对检测数据进 行深度分析,挖掘潜在问题,为优化标准提
供有力支持。
THANKS FOR WATCHING
感谢您的观看
针孔
总结词
针孔是指PCB板表面出现的小孔洞,可能是由于制造过程中化学沉铜、电镀等工 艺问题造成的。
详细描述
针孔会导致PCB板的导电性能下降,影响电气性能和可靠性。针孔可能是由于制 造过程中化学沉铜、电镀等工艺问题造成的,也可能是由于原材料质量不佳或生 产环境差等原因。
气泡
总结词
气泡是指PCB板表面或内部存在气体,可 能是由于制造过程中加热或化学反应产 生的。
检查结果记录与报告
要点一
总结词
记录检查结果并生成报告是外观检验流程的重要环节,有 助于对检验结果进行汇总和分析,并为后续处理提供依据 。
- 1、下载文档前请自行甄别文档内容的完整性,平台不提供额外的编辑、内容补充、找答案等附加服务。
- 2、"仅部分预览"的文档,不可在线预览部分如存在完整性等问题,可反馈申请退款(可完整预览的文档不适用该条件!)。
- 3、如文档侵犯您的权益,请联系客服反馈,我们会尽快为您处理(人工客服工作时间:9:00-18:30)。
補救處置 1.調整助焊劑發泡槽氣壓及定時清洗。 2.調整預熱溫度與過爐速度之搭配。 3.PWB Layout設計加開氣孔。 4.調整框架位置。 5.錫波加高或清除錫渣及定期清理錫爐。 6.更換零件或增加浸錫時間。 7.去廚防焊油墨或更換PWB。 8.調整過爐速度。
線腳長
特點
OK
NG
零件線腳吃錫後,其焊點線腳長度超 過規定之高度者。
•
人生得意须尽欢,莫使金樽空对月。1 1:44:32 11:44:3 211:44 10/20/2 020 11:44:32 AM
•
安全象只弓,不拉它就松,要想保安 全,常 把弓弦 绷。20. 10.2011 :44:321 1:44Oc t-2020- Oct-20
•
加强交通建设管理,确保工程建设质 量。11:44:3211 :44:321 1:44Tu esday , October 20, 2020
錫洞
特點
OK
NG
於焊點外表上產生肉眼清晰可見之貫 穿孔洞者。
允收標準
無此現象即為允收,若發現即需二次 補焊。
影響性
1.電路無法導通。
2.焊點強度不足。 造成原因 1.零件或PWB之焊墊銲錫性不良。 2.焊墊受防焊漆沾附。 3.線腳與孔徑之搭配比率過大。 4.錫爐之錫波不穩定或輸送帶震動。 5.因預熱溫度過高而使助焊劑無法活化。 6.導通孔內壁受污染或線腳度錫不完整。 7.AI零件過緊,線腳緊偏一邊。
補救處置 1.定時清除錫槽內之錫渣。 2.清洗發泡管或調整發泡氣壓。 3.調整焊錫爐輸送帶速度。 4.調整焊錫爐錫溫與預熱。 5.調整焊錫液面。 6.養成正確使用吸錫槍使用方法,及時保
持桌面的清潔。
錫裂
特點
NG
NG
於焊點上發生之裂痕,最常出現在線 腳周圍、中間部位及焊點底端與焊墊間。
允收標準
無此現象即為允收,若發現即需二次 補焊。
補救處置
1.調高預熱溫度。 2.調慢輸送帶速度,並以Profile確認板面
溫度。 3.更新助焊劑。 4.確認錫波高度為1/2板厚高。 5.清除錫槽表面氧化物。 6.變更設計加大零件間距。 7.確認過爐方向,以避免並列線腳同時過
爐,或變更設計並列線腳同一方向過爐。
翹皮
特點
NG
NG
印刷電路板之焊墊與電路板之基材產 生剝離現象。
清潔的作用。 3.Flux比重過低。 4.過爐角度太小。
補救處置 1.調高錫溫或調慢過爐速度。 2.調整預熱溫度。 3.調整Flux比重。 4.調整錫爐過爐角度。
錫尖
特點
OK
NG
在零件線腳端點及吃錫路線上,成形 為多餘之尖銳錫點者。
允收標準
錫尖長度須小於0.2mm,未達者須二 次補焊。
影響性
1.易造成安距不足。
•
牢记安全之责,善谋安全之策,力务 安全之 实。202 0年10 月20日 星期二1 1时44 分32秒 Tuesday , October 20, 2020
•
相信相信得力量。20.10.202020年10月 20日星 期二11 时44分 32秒20 .10.20
谢谢大家!
•
树立质量法制观念、提高全员质量意 识。20. 10.2020 .10.20 Tuesday , October 20, 2020
允收標準
φ≦0.8mm → 線腳長度小於2.5mm φ>0.8mm → 線腳長度小於3.5mm
影響性 1.易造成錫裂。 2.吃錫量易不足。 3.易形成安距不足。
造成原因 1.插件時零件傾斜,造成一長一短。 2.加工時裁切過長。
補救處置 1.確保插件時零件直立,亦可以加工Kink
的方式避免傾斜。 2.加工時必須確保線腳長度達到規長度。 3.注意組裝時偏上、下限之線腳長。
補救處置 1.PWB過爐前以80~100℃烘烤2~3小時。 2.嚴格要求PWB在任何時間任何人都不得
以手觸碰PWB表面,以避免污染。 3.變更零件腳成型方式,避免Coating落於
孔內,或察看孔徑與線徑之搭配是否有 風孔之現象。
短路
特點
OK
NG
在不同線路上兩個或兩個以上之相鄰 焊點間,其焊墊上之焊錫產生相連現象。
1.調高預熱溫度。 2.調慢輸送帶速度,並以Profile確認板面
溫度。 3.更新助焊劑。 4.確認錫波高度為1/2板厚高。 5.清除錫槽表面氧化物。 6.變更設計加大零件間距。 7.確認過爐方向,以避免並列線腳同時過
爐,或變更設計並列線腳同一方向過爐。
漏焊
特點
OK
NG
零件線腳四週未與焊錫熔接及包覆。
無鉛焊點檢驗規范
冷焊
特點
OK
NG
焊點呈不平滑之外表,嚴重時於線腳 四周,產生縐褶或裂縫。
允收標準
無此現象即為允收,若發現即需二次 補焊。
影響性 焊點壽命較短,容易於使用一段時間
後,開始產生焊接不良之現象,導致功能 失效。 造成原因 1.焊點凝固時,受到不當震動(如輸送皮帶
震動)。 2.焊接物(線腳、焊墊)氧化。 3.潤焊時間不足。
•
作业标准记得牢,驾轻就熟除烦恼。2 020年1 0月20 日星期 二11时4 4分32 秒11:44:3220 October 2020
•
好的事情马上就会到来,一切都是最 好的安 排。上 午11时4 4分32 秒上午1 1时44 分11:44:3220.1 0.20
•
一马当先,全员举绩,梅开二度,业 绩保底 。20.10. 2020.1 0.2011:4411:44 :3211:4 4:32Oc t-20
錫渣
特點
NG
NG
焊點上或焊點間所產生之線狀錫。
允收標準 無此現象即為允收,若發現即需二次
補焊。
影響性
1.易造成線路短路。
2.造成焊點未潤焊。
造成原因 1.錫槽焊材雜度過高。 2.助焊劑發泡不正常。 3.焊錫時間太短。 4.焊錫溫度受熱不均勻。 5.焊錫液面太高、太低。 6.吸錫槍內錫渣掉入PWB。
傾倒。 5.調整錫爐或重新補焊。
錫橋
特點
OK
NG
在同線路上兩個或兩個以上之相鄰焊 點間,其焊墊上之焊錫產生相連現象。
允收標準
無此現象即為允收,若發現即需二次 補焊。
影響性
對電氣上毫無影響,但對焊點外觀上 易造成短路判斷之混淆。 造成原因 1.板面預熱溫度不足。 2.輸送帶速度過快,潤焊時間不足。 3.助焊劑活化不足。 4.板面吃錫高度過高。 5.錫波表面氧化物過多。 6.零件間距過近。 7.板面過爐方向和錫波方向不配合。
力或以機械方式固定零件,減少震動。
•
树立质量法制观念、提高全员质量意 识。20. 10.2020 .10.20 Tuesday , October 20, 2020
•
人生得意须尽欢,莫使金樽空对月。1 1:44:32 11:44:3 211:44 10/20/2 020 11:44:32 AM
•
安全象只弓,不拉它就松,要想保安 全,常 把弓弦 绷。20. 10.2011 :44:321 1:44Oc t-2020- Oct-20
•
加强交通建设管理,确保工程建设质 量。11:44:3211 :44:321 1:44Tu esday , October 20, 2020
•
安全在于心细,事故出在麻痹。20.10. 2020.1 0.2011:44:3211 :44:32 October 20, 2020
•
踏实肯干,努力奋斗。2020年10月20 日上午1 1时44 分20.10. 2020.1 0.20
•
追求至善凭技术开拓市场,凭管理增 创效益 ,凭服 务树立 形象。2 020年1 0月20 日星期 二上午1 1时44 分32秒1 1:44:32 20.10.2 0
•
严格把控质量关,让生产更加有保障 。2020 年10月 上午11 时44分2 0.10.20 11:44O ctober 20, 2020
•
安全在于心细,事故出在麻痹。20.10. 2020.1 0.2011:44:3211 :44:32 October 20, 2020
•
踏实肯干,努力奋斗。2020年10月20 日上午1 1时44 分20.10. 2020.1 0.20
•
追求至善凭技术开拓市场,凭管理增 创效益 ,凭服 务树立 形象。2 020年1 0月20 日星期 二上午1 1时44 分32秒1 1:44:32 20.10.2 0
影響性
1.造成電路上焊接不良,不易檢測。
2.嚴重時電路無法導通,電氣功能失效。
造成原因 1.不正確之取、放PWB。 2.設計時產生不當之焊接機械應力。 3.剪腳動作錯誤。 4.剪腳過長。 5.錫少。
補救處置 1.PWB取、放接不能同時抓取零件,且須
輕取、輕放。 2.變更設計。 3.剪腳時不可扭彎拉扯。 4.加工時先控制線腳長度,插件避免零件
錫少
特點
OK
NG
焊錫未能沾滿整個錫墊,且吃錫高度 未達線腳長1/2者。
允收標準
焊角須大於15度,未達者須二次補焊。
影響性
錫點強度不足,承受外力時,易導致 錫裂,其二為焊接面積變小,長時間易引 響焊點壽命。
造成原因 1.錫溫過高、過爐時角度過大、助焊劑比
重過高或過低、後檔板太低。 2.線腳過長。 3.焊墊(過大)與線徑之搭配不恰當。 4.焊墊太相鄰,產生拉錫。
2.易刺穿絕緣物,而造成耐壓不良或短路。
造成原因 1.較大之金屬零件吸熱,造成零件局部吸
熱不均。 2.零件線腳過長。 3.錫溫不足或過爐時間太快、預熱不夠。 4.手焊烙鐵溫度傳導不均。
補救處置 1.增加預熱溫度、降低過爐速度、提高錫
槽溫度來增加零件之受熱及吃錫時間。 2.裁短線腳。 3.調高溫度或更換導熱面積較大之烙鐵頭。