热处理技术标准
JB-T 9210-1999真空热处理技术标准(1)

书山有路勤为径,学海无涯苦作舟
JB/T 9210-1999 真空热处理技术标准(1)
前言
本标准是对ZB J36 01590《真空热处理》的修订.
本标准与ZB J36 01590 在以下主要技术内容上有所改变:
真空淬火炉,真空回火炉有效加热区的温度偏差由通常不得超过
±10℃改为±5℃;真空退火炉有效加热区的温度偏差由不得超过±15℃改为±8℃;
真空淬火炉和真空退火炉的加热元件对地绝缘电阻应大于2 kΩ,回火炉应大于500 kΩ改为真空淬火炉,回火炉和退火炉的加热元件对地绝缘电阻应大于2 kΩ;
按有关规定作了编辑性修改.
本标准自实施之日起代替ZB J36 01590.
本标准由全国热处理标准化技术委员会提出并归口.
本标准负责起草单位:上海市机械制造工艺研究所.
本标准主要起草人:屠恒悦,梅志强.
本标准于1990 年4 月19 日首次发布.
1、范围
本标准规定了真空热处理设备的特殊要求,真空热处理常用金属材料,真空热处理的工艺过程及其基本工艺参数.
本标准适用于金属的真空淬火,真空回火,真空退火,真空固溶热处理及真空时效等工艺.
2、引用标准。
热处理标准

热处理相关标准汇总一、热处理基础GB/T 7232—1999 金属热处理工艺术语GB/T 8121-1987 热处理工艺材料名语术语GB/T 12603—1990 金属热处理工艺分类及代号 GB/T 13324—1991 热处理设备术语JB/T 8555-1997 热处理技术要求在零件图样上的表示方法JB/T 9208—1999 可控气氛分类及代号二、工艺方法GB/T 16923—1997 钢件的正火与退火GB/T 16924-1997 钢件的淬火与回火GB/T 18177—2000 钢件的气体渗氮GB/T 18683—2002 钢铁件激光表面淬火JB/T 3999-1999 钢件的渗碳与碳氮共渗淬火回火JB/T 4155—1999 气体氮碳共渗JB/T 4202—1999 钢的锻造余热淬火回火处理JB/T 4215—1996 渗硼JB/T 4218-1994 硼砂熔盐渗金属JB/T 6048-1992 盐浴热处理JB/T 6956—1993 离子渗氮JB/T 7500—1994 低温化学热处理工艺方法选择通则JB/T 7529—1994 可锻铸铁热处理JB/T 7711-1995 灰铸铁件热处理JB/T 7712—1995 高温合金热处理JB/T 8418—1996 粉末渗金属JB/T 8929—1999 深层渗碳JB/T 9197-1999 不锈钢和耐热钢热处理JB/T 9198-1999 盐浴硫氮碳共渗JB/T 9200—1999 钢铁件的火焰淬火回火处理JB/T 9201—1999 钢铁件的感应淬火回火处理JB/T 9207-1999 钢件在吸热式气氛中的热处理JB/T 9210-1999 真空热处理三、质量检验及评定GB/T 224—1987 钢的脱碳层深度测定法GB/T 225—1988 钢的淬透性末端淬火试验方法GB/T 226—1991 钢的低倍组织及缺陷酸蚀检验法GB/T 227-1991 工具钢淬透性试验方法GB/T 1979—2001 结构钢低倍组织缺陷评级图GB/T 4335-1984 低碳钢冷轧薄板铁素体晶粒度测定法GB/T 4462—1984 高速工具钢大块碳化物评级图GB/T 5617—1985 钢的感应淬火或火焰淬火后有效硬化层深度的测定GB/T 6401-1986 铁素体奥氏体型双相不锈钢中α—相面积含量金相测定法GB/T 9450—1988 钢件渗碳淬火有效硬化层深度的测定和校核GB/T 9451-1988 钢件薄表面总硬化层深度或有效硬化层深度的测定. GB/T 9452—1988 热处理炉有效加热区测定方法GB/T 11354-1989 钢铁零件渗氮层深度测定和金相组织检验GB/T 13298-1991 金属显微组织检验方法GB/T 13299—1991 钢的显微组织评定方法GB/T 13302-1991 钢中石墨碳显微评定方法GB/T 13305—1991 奥氏体不锈钢中α—相面积含量金相测定法GB/T 13321—1991钢铁硬度锉刀检验方法GB/T 14979-1994 钢的共晶碳化物不均匀度评定法GB/T 15749-1995 定量金相手工测定方法JB/T 5069-1991 钢铁零件渗金属层金相检验方法JB/T 5074-1991 低、中碳钢球化体评级JB/T 6049-1992 热处理炉有效加热区的测定JB/T 6050—1992 钢铁热处理零件硬度检验通则JB/T 6051-1992 球墨铸铁热处理工艺及质量检验JB/T 6141 1-1992重载齿轮渗碳层球化处理后金相检验JB/T 6141 2-1992重载齿轮渗碳质量检验JB/T 6141 3—1992重载齿轮渗碳金相检验JB/T 6141 4-1992重载齿轮渗碳表面碳含量金相判别法JB/T 6954—1993 灰铸铁接触电阻加热淬火质量检验和评级JB/T 7709-1995 渗硼层显微组织、硬度及层深检测方法JB/T 7710—1995 薄层碳氮共渗或薄层渗碳钢件显微组织检测JB/T 7713—1995 高碳高合金钢制冷作模具显微组织检验JB/T 8420-1996 热作模具钢显微组织评级JB/T 8881-2001 滚动轴承零件渗碳热处理技术条件JB/T 9204—1999 钢件感应淬火金相检验JB/T 9205—1999 珠光体球墨铸铁零件感应淬火金相检验JB/T 9206—1999 钢铁热浸铝工艺及质量检验JB/T 9211-1999 中碳钢与中碳合金结构马氏体等级JB/T 10174-2000 钢铁零件强化喷丸的质量检验方法JB/T 10175—2000 热处理质量控制要求四、热处理工艺材料JB/T 4390-1999 高、中温热处理盐浴校正剂JB/T 4392—1999 有机物水溶性淬火介质性能测定方法JB/T 4393—1999 聚乙烯醇合成淬火剂JB/T 5072—1991热处理保护涂料一般技术要求JB/T 6955-1993 热处理常用淬火介质技术要求JB/T 7530—1994 热处理用氩气、氮气、氢气一般技术条件JB/T 7951—1999 淬火介质冷却性能试验方法JB/T 8419-1996 热处理工艺材料分类及代号JB/T 9199-1999 防渗涂料技术条件JB/T 9202—1999 热处理用盐JB/T 9203—1999 固体渗碳剂。
热处理的标注标准
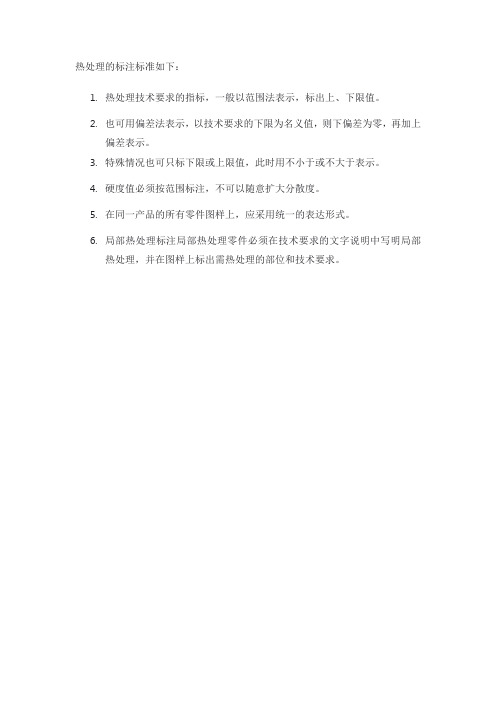
热处理的标注标准如下:
1.热处理技术要求的指标,一般以范围法表示,标出上、下限值。
2.也可用偏差法表示,以技术要求的下限为名义值,则下偏差为零,再加上
偏差表示。
3.特殊情况也可只标下限或上限值,此时用不小于或不大于表示。
4.硬度值必须按范围标注,不可以随意扩大分散度。
5.在同一产品的所有零件图样上,应采用统一的表达形式。
6.局部热处理标注局部热处理零件必须在技术要求的文字说明中写明局部
热处理,并在图样上标出需热处理的部位和技术要求。
热处理技术标准

热处理技术标准《热处理技术标准》同学们,你们知道什么是热处理技术吗?今天就让我们一起来揭开热处理技术的神秘面纱吧!热处理技术呀,简单来说就是一种对材料进行特殊处理的方法,它可以让材料变得更加强壮、耐用呢。
就好像我们锻炼身体可以让我们更健康一样,材料经过热处理也会变得更厉害哦!那热处理技术具体是怎么做的呢?它主要包括加热、保温和冷却这几个步骤。
就好像我们做饭的时候要先把食材加热,然后让它保持一定的温度一段时间,最后再让它冷却下来一样。
在热处理中,不同的材料需要不同的温度和时间来进行处理,这样才能达到最好的效果。
为什么要进行热处理呢?这是因为很多材料在使用之前,可能存在一些不足之处。
比如说,有些金属材料可能不够硬,容易变形;有些可能不够耐磨,用不了多久就会磨损。
而通过热处理,就可以改善这些问题啦。
它可以改变材料的组织结构,从而提高材料的性能,比如硬度、强度、韧性、耐磨性等等。
我们先来看看硬度吧。
经过热处理后,材料的硬度可以大大提高哦。
就像我们的铅笔,HB 的铅笔就比较软,写字容易模糊,而2B 的铅笔就硬一些,写字就更清晰。
材料也是一样,硬度提高了,就更能抵抗外界的压力和磨损啦。
强度也是很重要的一个方面呢。
热处理可以让材料变得更能承受拉力、压力等各种力量,就像我们的肌肉变得更强壮了,就能提起更重的东西一样。
这样材料在使用过程中就不容易断裂或者损坏啦。
韧性也不能忽视哦。
如果材料太脆了,就很容易破裂。
但是经过热处理,材料的韧性可以增加,就像我们的橡皮一样,有一定的弹性,不容易被轻易折断。
还有耐磨性呀。
有些材料需要经常和其他东西摩擦,如果不耐磨,很快就会被磨坏了。
通过热处理,可以让材料表面变得更加耐磨,就像我们的鞋底,如果很耐磨,就能穿很久呢。
那热处理技术都有哪些常见的方法呢?其中一种就是退火啦。
退火就像是让材料好好地休息一下。
把材料加热到一定温度,然后慢慢冷却,这样可以消除材料内部的应力,让材料变得更柔软、更有韧性。
热处理的标准

热处理的标准热处理是一种通过加热和冷却金属材料来改变其物理和机械性能的工艺。
在工业生产中,热处理被广泛应用于各种金属制品的生产过程中。
热处理的标准对于保证产品质量和性能至关重要。
本文将介绍热处理的标准以及其在工业生产中的重要性。
首先,热处理的标准包括了对于加热温度、保温时间、冷却速率等工艺参数的规定。
这些参数的选择对于最终产品的性能具有决定性的影响。
例如,对于碳钢材料的热处理,通常需要将材料加热至临界温度以上,然后进行保温一定时间,最后以适当的速率冷却至室温。
这些参数的选择需要根据具体材料的成分和要求来确定,因此热处理的标准需要根据不同材料的特性进行具体规定。
其次,热处理的标准还包括了对于产品性能的要求。
不同的产品对于硬度、韧性、强度等性能有着不同的要求,因此热处理的标准需要明确规定产品在经过热处理后应具备的性能指标。
这些性能指标不仅需要符合国家标准,还需要满足具体行业的要求,例如航空航天、汽车制造、机械加工等行业对于产品性能有着严格的要求,因此热处理的标准需要根据不同行业的需求进行具体规定。
最后,热处理的标准对于产品质量和性能的保证至关重要。
通过严格执行热处理的标准,可以保证产品具有一致的性能和质量。
同时,热处理的标准也可以帮助企业降低生产成本,提高生产效率。
通过科学合理的热处理工艺,可以减少产品的废品率,提高产品的利用率,从而降低生产成本,提高企业的竞争力。
总之,热处理的标准对于保证产品质量和性能具有重要意义。
通过严格执行热处理的标准,可以确保产品具有一致的性能和质量,满足不同行业的需求。
因此,企业在生产过程中应严格遵守热处理的标准,确保产品质量,提高生产效率,降低生产成本,从而获得更好的经济效益。
机械零部件热处理相关标准
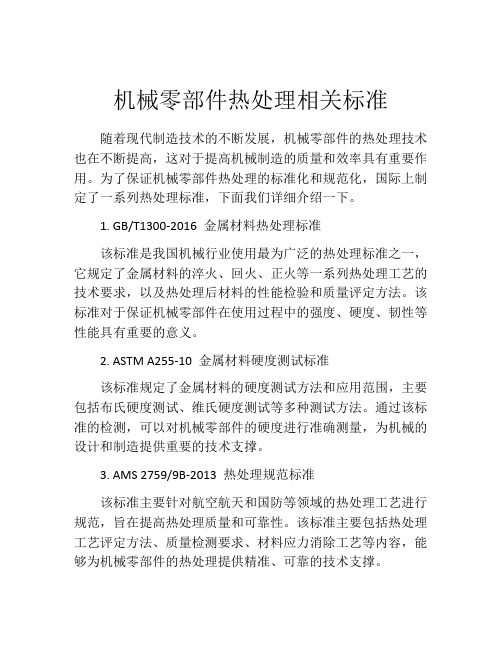
机械零部件热处理相关标准随着现代制造技术的不断发展,机械零部件的热处理技术也在不断提高,这对于提高机械制造的质量和效率具有重要作用。
为了保证机械零部件热处理的标准化和规范化,国际上制定了一系列热处理标准,下面我们详细介绍一下。
1. GB/T1300-2016 金属材料热处理标准该标准是我国机械行业使用最为广泛的热处理标准之一,它规定了金属材料的淬火、回火、正火等一系列热处理工艺的技术要求,以及热处理后材料的性能检验和质量评定方法。
该标准对于保证机械零部件在使用过程中的强度、硬度、韧性等性能具有重要的意义。
2. ASTM A255-10 金属材料硬度测试标准该标准规定了金属材料的硬度测试方法和应用范围,主要包括布氏硬度测试、维氏硬度测试等多种测试方法。
通过该标准的检测,可以对机械零部件的硬度进行准确测量,为机械的设计和制造提供重要的技术支撑。
3. AMS 2759/9B-2013 热处理规范标准该标准主要针对航空航天和国防等领域的热处理工艺进行规范,旨在提高热处理质量和可靠性。
该标准主要包括热处理工艺评定方法、质量检测要求、材料应力消除工艺等内容,能够为机械零部件的热处理提供精准、可靠的技术支撑。
4. JIS G 3193-2008 热轧产品的尺寸、重量及形状公差标准该标准主要规定了热轧产品的尺寸、质量和形状公差等要求,为机械零部件的制造提供标准化的技术要求和检测方法。
以上是目前机械零部件热处理相关的几个标准,它们的制定和实施,为机械制造行业的高效、精准生产提供了可靠保障。
在实际应用中,机械制造企业需要根据自身的生产需求和技术条件,选择合适的标准进行执行,并加强对标准的监督和检查,确保机械零部件的热处理达到标准化和规范化的要求。
热处理国家标准大全
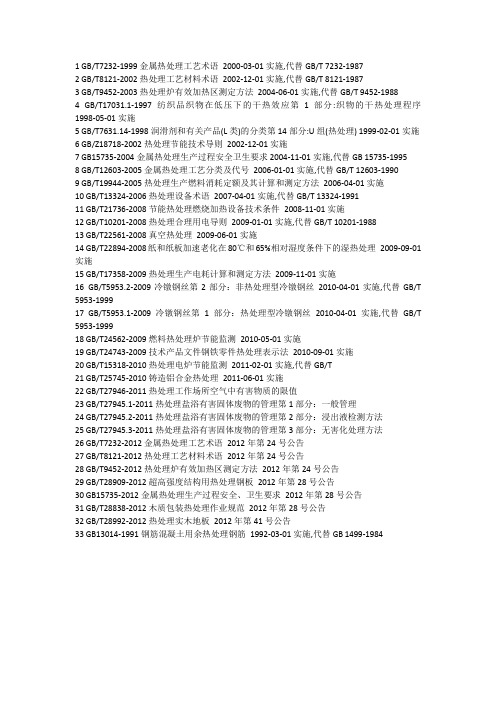
1 GB/T7232-1999金属热处理工艺术语2000-03-01实施,代替GB/T 7232-19872 GB/T8121-2002热处理工艺材料术语2002-12-01实施,代替GB/T 8121-19873 GB/T9452-2003热处理炉有效加热区测定方法2004-06-01实施,代替GB/T 9452-19884 GB/T17031.1-1997纺织品织物在低压下的干热效应第1部分:织物的干热处理程序1998-05-01实施5 GB/T7631.14-1998润滑剂和有关产品(L类)的分类第14部分:U组(热处理) 1999-02-01实施6 GB/Z18718-2002热处理节能技术导则2002-12-01实施7 GB15735-2004金属热处理生产过程安全卫生要求2004-11-01实施,代替GB 15735-19958 GB/T12603-2005金属热处理工艺分类及代号2006-01-01实施,代替GB/T 12603-19909 GB/T19944-2005热处理生产燃料消耗定额及其计算和测定方法2006-04-01实施10 GB/T13324-2006热处理设备术语2007-04-01实施,代替GB/T 13324-199111 GB/T21736-2008节能热处理燃烧加热设备技术条件2008-11-01实施12 GB/T10201-2008热处理合理用电导则2009-01-01实施,代替GB/T 10201-198813 GB/T22561-2008真空热处理2009-06-01实施14 GB/T22894-2008纸和纸板加速老化在80℃和65%相对湿度条件下的湿热处理2009-09-01实施15 GB/T17358-2009热处理生产电耗计算和测定方法2009-11-01实施16 GB/T5953.2-2009冷镦钢丝第2部分:非热处理型冷镦钢丝2010-04-01实施,代替GB/T 5953-199917 GB/T5953.1-2009冷镦钢丝第1部分:热处理型冷镦钢丝2010-04-01实施,代替GB/T 5953-199918 GB/T24562-2009燃料热处理炉节能监测2010-05-01实施19 GB/T24743-2009技术产品文件钢铁零件热处理表示法2010-09-01实施20 GB/T15318-2010热处理电炉节能监测2011-02-01实施,代替GB/T21 GB/T25745-2010铸造铝合金热处理2011-06-01实施22 GB/T27946-2011热处理工作场所空气中有害物质的限值23 GB/T27945.1-2011热处理盐浴有害固体废物的管理第1部分:一般管理24 GB/T27945.2-2011热处理盐浴有害固体废物的管理第2部分:浸出液检测方法25 GB/T27945.3-2011热处理盐浴有害固体废物的管理第3部分:无害化处理方法26 GB/T7232-2012金属热处理工艺术语2012年第24号公告27 GB/T8121-2012热处理工艺材料术语2012年第24号公告28 GB/T9452-2012热处理炉有效加热区测定方法2012年第24号公告29 GB/T28909-2012超高强度结构用热处理钢板2012年第28号公告30 GB15735-2012金属热处理生产过程安全、卫生要求2012年第28号公告31 GB/T28838-2012木质包装热处理作业规范2012年第28号公告32 GB/T28992-2012热处理实木地板2012年第41号公告33 GB13014-1991钢筋混凝土用余热处理钢筋1992-03-01实施,代替GB 1499-1984。
astm热处理标准

astm热处理标准ASTM 热处理标准ASTM(美国材料与试验协会)热处理标准是在材料热处理过程中使用的一系列标准规范,目的是确保制造商在材料加工中遵循一致的标准。
本文将详细介绍ASTM热处理标准的重要性和应用范围,并讨论其中的一些关键方面。
第一部分:ASTM热处理标准简介ASTM热处理标准是由工作委员会根据专家的贡献和研究结果制定的。
这些标准的主要目的是确保材料在经历热处理过程后具备所需的性能和特征。
ASTM热处理标准通常涵盖了材料的热处理方法、处理温度、冷却速率、热处理设备要求等方面。
第二部分:ASTM热处理标准的重要性遵循ASTM热处理标准的重要性不言而喻。
以下是几个关键原因:1. 质量控制:ASTM热处理标准确保了材料的一致性和可靠性,从而有助于提高产品的质量和性能。
2. 安全保障:热处理过程可能涉及高温和危险化学物质,遵循ASTM热处理标准可确保操作员的安全,并防止潜在的事故和损害。
3. 符合法规:许多国家和地区对于特定应用领域的材料要求使用符合ASTM热处理标准的产品。
第三部分:ASTM热处理标准的应用范围ASTM热处理标准适用于各个行业和领域,涵盖了各种材料和热处理过程。
以下是一些常见的应用范围:1. 金属材料:ASTM热处理标准广泛应用于各种金属材料的热处理过程,如钢、铝、铜等。
2. 塑料材料:ASTM热处理标准也适用于一些塑料材料的热处理,如热塑性塑料的热膨胀和热固化塑料的固化过程。
3. 玻璃材料:ASTM热处理标准包括玻璃材料的退火、强化和淬火等热处理过程。
第四部分:ASTM热处理标准的关键方面1. 标准编号和命名:ASTM热处理标准由唯一的标准编号和命名,以便于在行业中准确定位和使用。
2. 热处理过程:ASTM热处理标准详细规定了不同材料的热处理过程,包括加热温度、保温时间、冷却速率等。
3. 测试和检测:ASTM热处理标准通常包含对热处理后材料性能进行测试和检测的要求和方法。
- 1、下载文档前请自行甄别文档内容的完整性,平台不提供额外的编辑、内容补充、找答案等附加服务。
- 2、"仅部分预览"的文档,不可在线预览部分如存在完整性等问题,可反馈申请退款(可完整预览的文档不适用该条件!)。
- 3、如文档侵犯您的权益,请联系客服反馈,我们会尽快为您处理(人工客服工作时间:9:00-18:30)。
焊接热处理技术标准目次1范围2引用文件3一般规定4焊接热处理加热方法与设备5焊接热处理工艺6焊接热处理工艺措施7质量检查与技术文件1范围引用文件本标准依据DL/T819-2002编制规定了火力发电厂钢制承压管道、部件(包括承压部件与非承压部件)在制作、安装、检修过程中对焊件进行焊接热处理的要求。
本标准适用于用加热方法对焊件进行的预热、后热和焊后热处理。
3一般规定3.1人员3.1.1焊接热处理人员应该经过专门的培训,取得资格证书。
没有取得资格证书的人员只能从事辅助性的焊接热处理工作,不能单独作业或对焊接热处理结果进行评价。
焊接热处理人员包括热处理技术人员和热处理-r.o3.1.2热处理技术人员的职责是:a) 应熟悉相关规程,熟练掌握、严格执行本规程,组织热处理人员的业务学习;b) 负责编制焊接热处理施工方案、作业指导书等技术文件;c) 指导并监督热处理工的工作;d) 收集、汇总、整理焊接热处理资料。
3.1.3热处理工的职责是:。
) 执行本规程,按焊接热处理施工方案、作业指导书、工艺卡进行施工;b) 记录热处理操作过程;c) 在热处理后进行自检。
.3.2安全要求3.2.1焊接热处理作业时应穿戴必要的劳动防护用品,防止烫伤、触电。
3.2.2应遵守施工现场对电器设备、易燃易爆物品的安全规定,工作场所应放置足够数量的灭火器材并设置高温、有电等警示牌。
3.2.3采用电加热时,至少应有两人值班;采用中频感应加热时,控制室应采取屏蔽措施。
拆装热处理加热装置之前必须确认已切断电源;焊接热处理工作完毕应检查现场,确认无引起火灾的危险后方可离开。
3.2.4作业过程中,应对含苯电容采取措施防止苯污染。
3.2.5保温材料的性能应满足工艺及环保要求。
产品质量应符合GB/T 16400—1996《绝热用硅酸铝棉及其制品》的要求。
焊接热处理加热方法与设备4.1加热方法4.1.1焊接热处理常用的加热方法有电加热(如电阻炉加热、柔性陶瓷电阻加热、远红外加热、工频感应加热、中频感应加热)和火焰加热(如氧一乙炔、高压煤油、天然气、液化石油气等)。
4.1.2中频感应加热宜用于对厚度小于或等于30mm的焊件进行加热。
4.2加热设备4.2.1设备应满足工艺要求,参数调节灵活、方便,通用性好,运行稳定、可靠,并满足安全要求。
4.2.2设备的控温精确度应在±5'U以内。
计算机温度控制系统的显示温度应以自动记录仪的温度显示为准进行调整。
计算机打印的焊接热处理记录曲线与标准记录纸对照,其背景表格的读数误差不大于0.5%。
4.2.3焊接热处理所使用的计量器具必须经过校验,并在有效期内使用。
维修后的计量器具,必须重新校验。
4.3.1 电阻炉加热设备的基本要求是:a) 电热元件应合理布置,炉内有效加热区的范围应符合GB 9452—1988的要求;b) 工作温度应满足热处理工艺的要求,有效加热区的温度不均匀性应小于等于20"C。
4.3.2柔性陶瓷电阻加热设备的基本要求是:a) 加热器的技术要求应符合附录A的规定;b) 当同炉使用多根(片)加热器时,其电阻值的偏差值应不超过5%。
4.3.3感应加热设备的基本要求是:a) 根据焊件的几何形状来确定感应线圈的形状,对管座、接管进行感应加热时,应避免尖角效应;b) 感应线圈应采取绝缘措施;c) 输出功率和频率必须能满足工作要求,输出功率误差应不超过±5%。
4.3.4火焰加热设备的基本要求是:当使用氧一乙炔加热时,应采用瓶装气体。
在乙炔气瓶上应装设止回阀,防止回火。
5焊接热处理工艺5.1评定5.1.1 焊接热处理工艺必须按照SD 340—1989的规定,在相应的焊接工艺评定工作中进行评定。
5.1.2实际采用的焊接热处理工艺应与所评定的内容一致。
5.2预热5.2.1预热方式5.2.1.1预热方式分为局部预热和整体预热。
5.2.1.2电加热适用于整体预热和局部预热。
火焰加热适用于现场局部预热。
5.2.1.3当管子外径大于219mm或壁厚大于等于20mm时,应采用电加热进行预热,预热升温速度应符合6.4.4的要求。
预热宽度从对口中心开始,每侧不少于焊件厚度的3倍,且不小于100mm。
5.2.2预热温度5.2.2.1确定焊件的预热温度时,应综合考虑以下几个因素:a) 钢材的焊接性;b) 焊件厚度、接头型式;c) 环境温度;d) 焊接材料的潜在含氢量和结构拘束度;e) 异种钢焊接时,预热温度的选择应根据合金成分高的一侧或焊接J生差的—侧进行选择。
5.2.2.2常用钢的预热温度见附录B。
5.2.3重新焊接按要求应该预热的焊件重新焊接时应重新预热。
5.3后热5.3.1有冷裂纹倾向的焊件,当焊接工作停止后,若不能立即进行焊后热处理,应进行后热。
其加热宽度应不小于预热时的宽度。
5·3.2对马氏体型钢(如F12钢或P91钢等)的焊接,如要进行后热,应在马氏体转变结束后进行。
5.4焊后热处理5.4.1当符合DL 5007—1992中5.0.20.3条、6.0.2条、DL/T 752—2001中6.1、5.3条规定,或其他规程、工艺文件有要求时,应进行焊后热处理。
5.4.2焊后热处理温度选择应按下述原则综合考虑:a) 不能超过Acl,一般应在A。
1以下30℃~50℃;’b) 对调质钢,应低于调质处理时回火温度;c) 对异种钢,按合金成分低一侧钢材的Acl选择。
5.4.3常用钢的焊后热处理温度与恒温时间见附录C。
5.4.4升、降温速度应按下述原则控制:a) 对承压管道和受压元件,焊接热处理升、降温速度为6250/3(单位为℃/h,其中d为焊件厚度1Tlrll)且不大于300"C/h。
降温时,300"C 以下可不控制。
b) 对主管与接管的焊件(如管座),应按主管的壁厚计算焊接热处理的升、降温速度;对返修焊件其恒温时间按焊件的名义厚度计算,计算方法见附录C。
5.4.5在制定焊后热处理工艺时,应考虑下列因素:a) 对有再热裂纹倾向的钢种,焊后热处理温度应避开敏感温区,升、降温时,应尽快通过温度敏感区,且避免在此温度区间停留;b) 对有第二类回火脆性的钢种,焊后热处理应采用快速冷却的方式;c) 冷拉焊接接头所用的加载工具,必须待焊接热处理完毕后,方可拆除。
6焊接热处理工艺措施6.1温度测量6·1·1根据加热方法,可以选用接触法或非接触法测定焊件温度。
柔性陶瓷电阻加热、电阻炉加热一般采用接触法测温;感应加热可以采用接触法测温,也可采用非接触法测温;火焰加热一般采用非接触法测温。
6·1·2接触法测温一般采用热电偶、测温笔、接触式表面温度计等;非接触法测温一般采用红外测温仪。
6.1.3热电偶测温应按如下要求:,a) 应根据热处理的温度和仪表的型号选择热电偶。
宜选用防水型的铠装热电偶。
热电偶的直径与长度应根据焊件的大小、加热宽度、固定方法选用。
b) 热电偶的安装位置,应以保证测温准确可靠、有代表性为原则。
对于管径大于或等于273mm的管道,测温点应在焊缝中心按圆周对称布置,且不少于两点;水平管道,测温点应上下对称布置;分区控温时,热电偶的布置应与加热装置相对应;当用一个热电偶同时控制多个焊件时,该热电偶应布置在有代表性的焊接接头上。
c) 采用柔性陶瓷电阻加热进行预热时,热电偶应布置在加热区以内,同时,还应使用其他方法检测坡口处的温度。
d) 热电偶固定采用储能压焊的方法,安装时必须保证热电偶的热端与焊件接触良好,热处理结束后应将点焊处打磨干净。
e) 在安装热电偶时,应注意以下几点:1)感应加热时,热电偶的引出方向应与感应线圈相垂直。
2)热电偶冷端温度不稳定时,必须使用补偿导线,必要时应采取补偿措施。
热电偶与补偿导线的型号、极性必须相匹配。
6.2加热范围与加热装置的安装6.2.1加热范围6.2.1.1对承压管道及其返修焊件的加热,宜采用整圈加热的方法,加热宽度从焊缝中心算起,每恻不小于管子壁厚的3倍,且不小于60mm。
同时应采取措施降低周向和径向的温差。
6.2.1.2主管(或壳体)与接管的加热,宜采用环形加热的方法,加热宽度应不小于两者中较大厚度的3倍。
6.2.2柔性陶瓷电阻加热器的安装6.2.2.1安装加热器时,应将焊件表面的焊瘤、焊渣、飞溅清理干净,使加热器与焊件表面贴紧,必要时,应制作专用的夹具。
加热器的布置宽度至少应比要求的加热宽度每侧多出60mm。
6.2.2.2当用绳形加热器对管道进行预热时,坡口两侧布置的加热器应对称,加热器的缠绕圈数、缠绕密度应尽可能相同,缠绕方向应相反。
6.2.2.3对水平放置的直径大于273mm的管道或大型部件进行焊后热处理时,宜分区控制温度。
6.2.2.4 用一个测温点同时控制多个焊接接头加热时,各焊接接头加热器的布置方式应相同,且保温层宽度和厚度也应尽可能相同。
6.2.3感应线圈的安装感应线圈安装时,应避免匝间短路,且应避免剩磁。
6.3温差控制与保温6.3.1焊接热处理恒温过程中,承压管道在加热范围内,任意两点间的温差应小于50E;压力容器在加热范围内,最大温差不宜大于65E。
6.3.2焊接热处理的保温宽度从焊缝坡口边缘算起,每侧不得少于管子壁厚的5倍,且每侧应比加热器的安装宽度增加不少于100mm。
6.3.3焊接热处理的保温厚度以40mm~60mm为宜,感应加热时,可适当减小保温厚度。
对水平管道,可以通过改变保温层厚度来减小管道上下部分的温差。
6.4火焰加热工艺措施6.4.1用火焰加热进行热处理时,应根据焊件大小选择喷嘴型号与数量;当使用多个喷嘴时,应对称布置,均匀加热。
6.4.2火焰焰心至工件的距离应在10mm以上;喷嘴的移动速度要稳定,不得在一个位置长期停留。
火焰加热时,应注意控制火焰的燃烧状况,防止金属的氧化或增碳。
6.4.3火焰加热应以焊缝为中心,加热宽度为焊缝两侧各外延不少于50mn~火焰加热的恒温时间按每毫米焊件厚度保温lmin计算。
加热完毕,应立即使用干燥的保温材料进行保温。
7质量检查与技术文件7.1质量检查8.1.1焊接热处理升温前应进行下列核查:a) 加热及测温设备、器具是否符合工艺要求;b) 加热装置的布置、温度控制分区是否合理;c) 加热范围是否符合标准或规范要求,保温层的宽度、厚度是否合适;d) 温度测点的安装方法、位置和数量是否符合工艺要求;e) 设定的加热温度、恒温时间、升、降温速度等是否符合工艺要求;f) 是否符合现场安全要求。
7.1.2焊接热处理后自检的要求是:a) 工艺参数在控制范围以内,并有自动记录曲线;b) 热电偶无损坏、无位移;c) 焊接热处理记录曲线与工艺卡吻合;d) 焊件表面无裂纹、无异常。
7.1.3硬度检验应符合下列规定:a) 当热处理自动记录曲线与工艺卡不符或无自动记录曲线时,应做硬度检查,硬度检查结果应符合DL 5007—1992中8.0.6条和DL/T 752—2001中8.5条或其他规程、工艺文件的要求。