下料问题的优化设计
板材下料优化方案

板材下料优化方案在木材加工行业中,如何最大程度地提高板材利用率和降低浪费是一个非常重要的问题。
传统的板材下料方式往往存在很大的浪费,而采用优化的板材下料方案可以有效地减少浪费,并提高生产效率。
本文将介绍一种常用的板材下料优化方案,通过优化下料方案来实现降低浪费,提高板材利用率。
一、了解板材规格和尺寸在制定下料优化方案之前,我们首先需要详细了解所使用的板材的规格和尺寸。
包括板材种类、厚度、长度、宽度等。
只有了解了板材的规格和尺寸,才能更好地制定下料方案,减少浪费。
二、利用计算软件进行优化可以借助计算机软件来进行板材下料的优化计算。
通过输入板材规格和需要裁剪的零件尺寸,计算软件可以自动生成最优的下料方案。
这些软件使用了高效的算法,可以快速且精准地进行优化计算。
例如,常用的下料软件有OptiCut、CutList Plus等。
三、合理设计零件尺寸在进行板材下料时,合理设计零件的尺寸也是非常重要的。
尽量避免设计过大或过小的零件,这样既可以减少浪费,又可以提高板材利用率。
同时,还可以考虑设计一些通用型的零件,以减少特定尺寸零件的数量,进一步降低浪费。
四、考虑边缘利用率和余料利用在进行板材下料时,除了面积利用率外,还要考虑板材的边缘利用率和余料利用。
通过合理规划下料方案,将板材边缘利用到最大化,并且合理利用余料,可以有效地减少浪费,提高板材利用率。
五、避免过多的切割在进行板材下料时,可以尽量避免过多的切割。
过多的切割不仅会增加加工的难度,还会增加浪费的可能性。
因此,在制定下料方案时,要避免过多的切割,尽量保持零件的形状和数量的简单性。
六、考虑批量生产的需求在制定板材下料方案时,还要考虑到批量生产的需求。
如果需要批量生产同样的零件,可以通过合理的下料方案来提高生产效率和板材利用率。
例如,可以将相同尺寸的零件集中进行下料切割,避免浪费和重复工作,提高生产效率。
七、严格控制切割误差和损耗在进行板材下料过程中,切割误差和材料损耗是无法完全避免的。
钣金下料工艺的优化的思考

钣金下料工艺的优化的思考
钣金下料工艺的优化是指通过对下料工艺进行调整和改进,提高钣金件的生产效率、降低生产成本、提高产品质量和减少工艺缺陷。
下面,我将从工艺参数的优化、设备和工具的改进以及智能化生产等方面进行思考。
1. 工艺参数的优化
通过合理调整下料工艺中的各项参数,可以提高钣金加工的效率和质量。
应根据钣金材料的类型、厚度和硬度等特性,科学确定切割速度、进给速度和切削深度等参数。
要根据具体的产品要求,合理选择切割工具的形状和材质,以提高切削效率和切削质量。
还应根据不同的工件形状和结构特点,合理确定切割路线和切割方向,以减少切割失误和提高下料精度。
2. 设备和工具的改进
钣金下料工艺的优化还需要结合先进的设备和工具来提高生产效率和产品质量。
要选用高精度的数控切割机床和自动下料机,以实现高效、精确的下料加工。
在选用切削工具时,要选择耐磨性好、切削力小的高硬度材料,并且要定期检修和更换切削工具,以保证切削效果和刀具寿命。
3. 智能化生产
随着信息技术的发展,智能化生产已经成为钣金加工的新趋势。
通过引入智能制造技术,可以实现钣金下料过程的自动化和智能化,提高生产效率和产品质量。
可以利用传感器和反馈控制系统,实现对切削过程的实时监测和自动调整,以降低质量缺陷和生产事故的发生概率。
可以利用计算机辅助设计和仿真技术,对下料工艺进行优化和预测,以提前发现潜在问题并予以解决。
下料问题的逐级优化方法
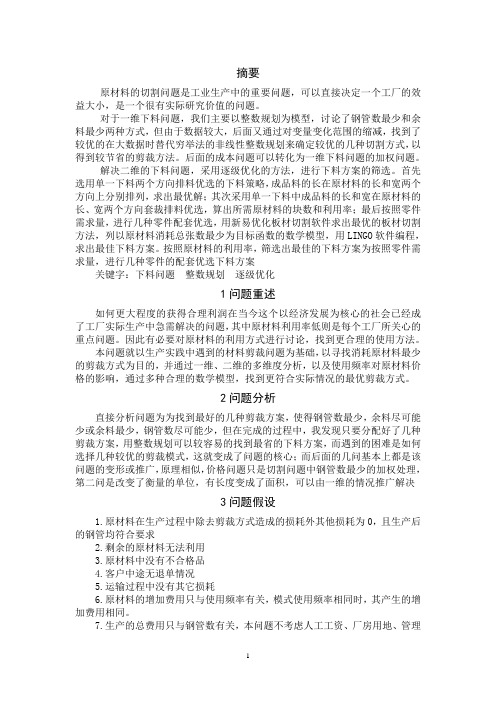
摘要原材料的切割问题是工业生产中的重要问题,可以直接决定一个工厂的效益大小,是一个很有实际研究价值的问题。
对于一维下料问题,我们主要以整数规划为模型,讨论了钢管数最少和余料最少两种方式,但由于数据较大,后面又通过对变量变化范围的缩减,找到了较优的在大数据时替代穷举法的非线性整数规划来确定较优的几种切割方式,以得到较节省的剪裁方法。
后面的成本问题可以转化为一维下料问题的加权问题。
解决二维的下料问题,采用逐级优化的方法,进行下料方案的筛选。
首先选用单一下料两个方向排料优选的下料策略,成品料的长在原材料的长和宽两个方向上分别排列,求出最优解;其次采用单一下料中成品料的长和宽在原材料的长、宽两个方向套裁排料优选,算出所需原材料的块数和利用率;最后按照零件需求量,进行几种零件配套优选,用新易优化板材切割软件求出最优的板材切割方法,列以原材料消耗总张数最少为目标函数的数学模型,用LINGO软件编程,求出最佳下料方案。
按照原材料的利用率,筛选出最佳的下料方案为按照零件需求量,进行几种零件的配套优选下料方案关键字:下料问题整数规划逐级优化1问题重述如何更大程度的获得合理利润在当今这个以经济发展为核心的社会已经成了工厂实际生产中急需解决的问题,其中原材料利用率低则是每个工厂所关心的重点问题。
因此有必要对原材料的利用方式进行讨论,找到更合理的使用方法。
本问题就以生产实践中遇到的材料剪裁问题为基础,以寻找消耗原材料最少的剪裁方式为目的,并通过一维、二维的多维度分析,以及使用频率对原材料价格的影响,通过多种合理的数学模型,找到更符合实际情况的最优剪裁方式。
2问题分析直接分析问题为为找到最好的几种剪裁方案,使得钢管数最少,余料尽可能少或余料最少,钢管数尽可能少,但在完成的过程中,我发现只要分配好了几种剪裁方案,用整数规划可以较容易的找到最省的下料方案,而遇到的困难是如何选择几种较优的剪裁模式,这就变成了问题的核心;而后面的几问基本上都是该问题的变形或推广,原理相似,价格问题只是切割问题中钢管数最少的加权处理,第二问是改变了衡量的单位,有长度变成了面积,可以由一维的情况推广解决3问题假设1.原材料在生产过程中除去剪裁方式造成的损耗外其他损耗为0,且生产后的钢管均符合要求2.剩余的原材料无法利用3.原材料中没有不合格品4.客户中途无退单情况5.运输过程中没有其它损耗6.原材料的增加费用只与使用频率有关,模式使用频率相同时,其产生的增加费用相同。
优化线材下料方案

优化线材下料方案编制人:审核人:审批人:年月日目录1、编制依据................................................................................................ 错误!未定义书签。
2、工程概况................................................................................................ 错误!未定义书签。
2.1工程基本概况___________________________________________________________ 错误!未定义书签。
2.2建筑设计概况___________________________________________________________ 错误!未定义书签。
3、基础设计及要求.................................................................................... 错误!未定义书签。
3.1基础设计 _______________________________________________________________________________ 8 3.2基础的确定 _____________________________________________________________ 错误!未定义书签。
3.3基础的验收要求_________________________________________________________ 错误!未定义书签。
3.4防雷接地 _______________________________________________________________ 错误!未定义书签。
优化下料流程提高下料效率和材料利用率
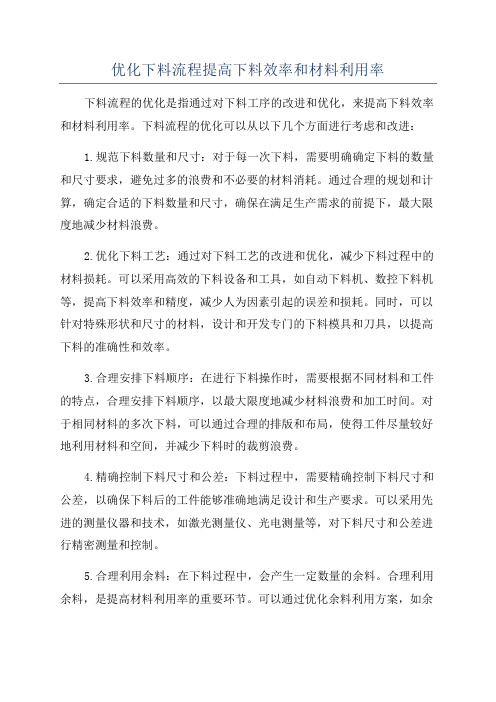
优化下料流程提高下料效率和材料利用率下料流程的优化是指通过对下料工序的改进和优化,来提高下料效率和材料利用率。
下料流程的优化可以从以下几个方面进行考虑和改进:1.规范下料数量和尺寸:对于每一次下料,需要明确确定下料的数量和尺寸要求,避免过多的浪费和不必要的材料消耗。
通过合理的规划和计算,确定合适的下料数量和尺寸,确保在满足生产需求的前提下,最大限度地减少材料浪费。
2.优化下料工艺:通过对下料工艺的改进和优化,减少下料过程中的材料损耗。
可以采用高效的下料设备和工具,如自动下料机、数控下料机等,提高下料效率和精度,减少人为因素引起的误差和损耗。
同时,可以针对特殊形状和尺寸的材料,设计和开发专门的下料模具和刀具,以提高下料的准确性和效率。
3.合理安排下料顺序:在进行下料操作时,需要根据不同材料和工件的特点,合理安排下料顺序,以最大限度地减少材料浪费和加工时间。
对于相同材料的多次下料,可以通过合理的排版和布局,使得工件尽量较好地利用材料和空间,并减少下料时的裁剪浪费。
4.精确控制下料尺寸和公差:下料过程中,需要精确控制下料尺寸和公差,以确保下料后的工件能够准确地满足设计和生产要求。
可以采用先进的测量仪器和技术,如激光测量仪、光电测量等,对下料尺寸和公差进行精密测量和控制。
5.合理利用余料:在下料过程中,会产生一定数量的余料。
合理利用余料,是提高材料利用率的重要环节。
可以通过优化余料利用方案,如余料利用方案的设计和规划,余料的再加工和利用等,有效地提高材料利用率,减少浪费。
6.加强质量管理:在下料生产过程中,加强质量管理是保证下料效率和材料利用率的关键。
通过建立和完善质量管理体系,加强对下料工艺和质量要求的控制和监督,及时发现和解决问题,以确保下料的质量和效率。
综上所述,通过规范下料数量和尺寸、优化下料工艺、合理安排下料顺序、精确控制下料尺寸和公差、合理利用余料和加强质量管理等措施,可以有效地提高下料效率和材料利用率,降低生产成本,提高企业竞争力。
工程学问题下料最佳方案

工程学问题下料最佳方案工程学中的下料指的是将原材料按照设计要求进行切割、裁剪、加工等操作,以便制造出符合产品要求的零部件或产品。
下料的质量和效率直接影响着整个生产流程的顺利进行,因此如何选择最佳的下料方案成为工程学中的重要问题。
在选择下料方案时,需要考虑原材料的特性、产品的设计要求、生产设备的性能以及生产效率等因素。
本文将针对下料过程中的材料选择、下料方式、下料工艺和下料设备等方面进行探讨,以寻找最佳的下料方案。
一、材料选择1. 材料特性在下料过程中,材料的特性是影响下料方案选择的重要因素。
首先需要考虑材料的硬度、韧性、厚度、形状以及表面粗糙度等特性。
不同材料的特性会影响切割前的处理方式、切割工具的选择以及下料过程中的加工参数设定。
此外,材料的成本、可供性和环保性也需要考虑在内。
在选择下料方案时,需要综合考虑材料的特性和成本,以便为下料过程提供最佳的原材料选择。
2. 材料类型根据材料的类型不同,下料方案也会有所差异。
常见的材料类型包括金属材料、塑料材料、木材等。
不同类型的材料需要采用不同的下料工艺和设备,以确保下料过程的质量和效率。
在选择下料方案时,需要根据产品设计要求和生产设备的性能,综合考虑材料的类型,以寻找最佳的下料方案。
二、下料方式1. 切割方式在下料过程中,常见的切割方式包括火焰切割、等离子切割、激光切割、水切割、机械切割等。
不同的切割方式适用于不同类型的材料和产品,具有不同的优势和局限性。
火焰切割适用于钢铁等金属材料,具有成本低、加工速度快的优势;等离子切割适用于不锈钢、铝合金等特殊材料,具有高速切割和高精度的优势;激光切割适用于各种类型的材料,具有非接触式加工、高精度和高效率的优势;水切割适用于石材、陶瓷等非金属材料,具有无热变形、无污染和高精度的优势;机械切割适用于木材、塑料等材料,具有成本低、操作简单的优势。
在选择下料方式时,需要综合考虑材料的特性、产品的设计要求以及生产设备的性能,以寻找最佳的切割方式。
下料优化计算方法(一)
下料优化计算方法(一)下料优化计算1. 简介•下料优化计算是指通过计算和算法来优化材料的使用,减少浪费,提高生产效率的过程。
•本文将介绍下料优化计算的基本概念和常用方法。
2. 基本概念•下料:指将原材料按照设计要求切割成特定尺寸的过程。
•材料利用率:指在下料过程中,有效利用原材料的比例。
•下料浪费:指在下料过程中,未能有效利用原材料的部分。
3. 常用方法3.1. 一维下料优化计算•一维下料优化计算主要针对直线切割的情况,通过算法来确定切割方案,使得材料的利用率最高。
3.2. 二维下料优化计算•二维下料优化计算主要针对平面切割的情况,通过算法来确定切割方案,使得材料的利用率最高。
•常用的算法包括:矩形递归、最佳动态规划、最优旋转递归等。
3.3. 三维下料优化计算•三维下料优化计算主要针对立体切割的情况,通过算法来确定切割方案,使得材料的利用率最高。
•常用的算法包括:三维装箱问题求解、分支界定法、副高搜索法等。
4. 应用领域•下料优化计算广泛应用于各个行业,如木工、金属加工、纺织、塑料加工等。
•运用下料优化计算可以有效减少原材料的浪费,降低生产成本,提高生产效率。
5. 结论•下料优化计算是一种能够有效提高材料利用率的方法,具有重要的实际应用价值。
•随着计算机技术的不断发展,下料优化计算的方法和算法也逐渐完善,将在未来得到更广泛的应用。
6. 注意事项•在进行下料优化计算时,需要考虑以下几个方面:–材料的规格和特性;–切割模式和切割工艺;–切割顺序和切割方向;–批量和生产时间;–设备和工具的限制。
7. 优化效果评估•在进行下料优化计算之后,需要对优化效果进行评估,以确定方案的可行性和效率。
•常用的评估指标包括:材料利用率、切割效率、生产成本、工时等。
8. 优化案例•下面是一个简单的下料优化案例,以一维下料为例:–原材料长度:10米–待加工工件尺寸:2米–切割模式:直线切割•切割方案:–第一段:2米–第二段:2米–第三段:2米–第四段:2米–第五段:2米•材料利用率:100%•切割效率:100%•生产成本:最小化•工时:最小化9. 总结•下料优化计算是一项重要的生产优化技术,可以帮助企业减少浪费,提高生产效率。
复杂下料问题的优化模型及求解方法研究
复杂下料问题的优化模型及求解方法研究xx年xx月xx日CATALOGUE目录•引言•复杂下料问题的数学模型•优化求解方法•实验与验证•结论与展望•参考文献01引言随着制造业的快速发展,下料问题已成为制约企业生产效率提高的关键因素之一。
在生产实践中,由于材料种类繁多、尺寸差异大、切割方式各异等因素,导致下料问题变得异常复杂和困难。
因此,研究复杂下料问题的优化模型及求解方法具有重要的现实意义。
意义阐述通过对复杂下料问题的深入研究,可以为企业提供更加精准的下料方案,提高原材料的利用率和生产效率,降低生产成本,同时也有助于推动制造业的数字化、智能化发展。
背景介绍研究背景与意义VS研究现状与问题现状概述目前,国内外学者已对下料问题进行了广泛的研究,提出了许多不同的优化模型和求解方法。
然而,在实际应用中,这些方法往往难以取得理想的效果,特别是在处理复杂下料问题时,存在着求解速度慢、求解精度低、鲁棒性差等问题。
存在的问题现有的优化模型和求解方法在下料问题中的主要问题包括:1)模型建立不够精确,导致求解结果与实际生产需求存在较大偏差;2)求解算法效率低下,无法在短时间内得出优化结果;3)对于复杂下料问题的处理能力不足,难以满足实际生产中的多样化需求。
本研究旨在解决复杂下料问题的优化模型及求解方法,主要研究内容包括:1)建立精确的数学模型,以提高模型的预测能力和鲁棒性;2)设计高效的求解算法,以提高求解速度和精度;3)结合实际生产需求,对模型和算法进行实验验证和性能评估。
本研究将采用理论分析和实验验证相结合的方法,具体包括:1)对复杂下料问题进行数学建模,建立相应的优化模型;2)设计相应的求解算法,包括遗传算法、模拟退火算法、蚁群算法等;3)通过实验验证和性能评估,对模型和算法进行优化和改进。
研究内容研究方法研究内容与方法02复杂下料问题的数学模型复杂下料问题是在满足一系列限制条件下,从给定的物料清单中选择最优的切割方案,以达到成本最低、材料浪费最少的目标。
下料问题的优化设计
下料问题的优化设计 Document number:NOCG-YUNOO-BUYTT-UU986-1986UT题1、[下料问题的优化设计]某车间有一大批长130cm的棒料,根据加工零件的要求,需要从这批棒料中成套截取70cm长的毛坯不少于100根,32cm 长的毛坯不少于100根,35cm长的毛坯不大于100根。
要求合理设计下料方案,使剩下的边角料总长最短。
根据题目意义,运用优化设计理论和方法,完成设计全过程;工程问题分析:数学模型建立及特征分析:优化方法选择;优化程序设计(解析优化);计算结果分析;结论及体会。
基于MATLAB一维优化下料问题分析0 前言生产中常会通过切割、剪裁、冲压等手段,将原材料加工成所需大小零件,这种工艺过程,称为原料下料问题。
在生产实践中,毛坯下料是中小企业的一个重要工序。
怎样减少剩余料头损失是节约钢材、降低产品成本、提高企业经济效益的一个重要途径。
在毛坯下料中我们常会遇到毛坯种类多、数量大的情况,如不进行周密计算则因料头而造成的钢材损失是相当可观的。
为使料头造成的钢材损失减少到最小程度,我们可依据预定的目标和限制条件统筹安排,以最少的材料完成生产任务。
1 一维优化下料问题的具体模型分析设原材料长度为L,数量充足。
需要切割成n(n≥0)种不同规格的零件,根据既省材料容易操作的原则,人们已经设计好了n种不同的下料方式,设第j种下料方式中可下得第i种零件ij a个,又已知第i种零件得需要量为i b个, j x表示第B种下料方式所消耗得零件数目, j c表示第j B种下料方式所得余料(j=1, j2 , , n, j x∈ Z)。
满足条件的切割方案有很多种,现在要求既满足需要又使所用原材料数量最少,即最优下料方案满足:μp=min (∑j c j x)约束条件:∑ij a j x=i b,j x∈Z。
线性规划数学模型根据线性规划算法,约束条件包括两部分:一是等式约束条件,二是变量的非负性。
钣金下料工艺的优化的思考
钣金下料工艺的优化的思考钣金下料是钣金加工中的重要工艺环节,下料质量的好坏直接影响到整个零件的加工质量和生产效率。
如何优化钣金下料工艺成为了当前钣金加工企业急需解决的问题之一。
本文将从工艺流程、设备选择、材料利用率等方面进行思考,探讨如何优化钣金下料工艺,提高生产效率和产品质量。
一、工艺流程的优化1. 合理设计工艺流程在进行钣金下料加工时,首先要对产品进行合理的工艺分析和设计,包括材料的选择、下料工艺流程、切割方式等。
通过对产品结构的分析和材料特性的了解,可以确定合理的下料顺序和工艺参数,避免产生浪费和加工品质不佳的问题。
2. 优化下料工序在进行下料加工时,要适时进行下料工序的优化和精简,尽可能减少加工过程中的繁琐步骤和时间浪费。
采用一次性成型工艺,避免反复加工,可以显著降低生产成本和提高生产效率。
3. 加强工艺管理建立科学的工艺管理制度,制定明确的工艺标准,规范化生产过程,对每道工序进行严格管理和控制,确保产品的加工质量和稳定性。
及时总结、分析和修正加工过程中出现的问题,不断改进和优化工艺流程。
二、设备选择的优化1. 选用先进设备在钣金下料加工中,选择性能稳定、精度高的先进设备是提高生产效率和产品质量的关键。
如数控剪板机、数控冲床等高精度加工设备,可以实现自动化和智能化生产,提高加工精度和生产效率。
2. 合理配置设备钣金下料加工过程中,应根据产品的特点和加工需求,合理配置设备,确保能够满足不同规格和要求的产品加工。
还要做好设备的维护保养工作,保证设备的正常运转和稳定性。
三、材料利用率的优化1. 合理采购材料钣金下料加工前,对材料进行合理的采购和管理是优化材料利用率的关键。
要根据产品的加工要求和规格,合理选择材料种类和规格,避免产生大量的浪费和材料报废。
2. 提高利用率在进行下料加工时,要充分利用原材料,尽可能减少废料和余料的产生。
通过合理的下料方案和工艺参数设置,最大限度地提高利用率,降低材料成本。
- 1、下载文档前请自行甄别文档内容的完整性,平台不提供额外的编辑、内容补充、找答案等附加服务。
- 2、"仅部分预览"的文档,不可在线预览部分如存在完整性等问题,可反馈申请退款(可完整预览的文档不适用该条件!)。
- 3、如文档侵犯您的权益,请联系客服反馈,我们会尽快为您处理(人工客服工作时间:9:00-18:30)。
题1、[下料问题的优化设计]某车间有一大批长130cm的棒料,根据加工零件的要求,需要从这批棒料中成套截取70cm长的毛坯不少于100根,32cm 长的毛坯不少于100根,35cm长的毛坯不大于100根。
要求合理设计下料方案,使剩下的边角料总长最短。
根据题目意义,运用优化设计理论和方法,完成设计全过程;工程问题分析:数学模型建立及特征分析:优化方法选择;优化程序设计(解析优化);计算结果分析;结论及体会。
基于MATLAB一维优化下料问题分析
0 前言
生产中常会通过切割、剪裁、冲压等手段,将原材料加工成所需大小零件,这种工艺过程,称为原料下料问题。
在生产实践中,毛坯下料是中小企业的一个重要工序。
怎样减少剩余料头损失是节约钢材、降低产品成本、提高企业经济效益的一个重要途径。
在毛坯下料中我们常会遇到毛坯种类多、数量大的情况,如不进行周密计算则因料头而造成的钢材损失是相当可观的。
为使料头造成的钢材损失减少到最小程度,我们可依据预定的目标和限制条件统筹安排,以最少的材料完成生产任务。
1 一维优化下料问题的具体模型分析
设原材料长度为L,数量充足。
需要切割成n (n≥0)种不同规格的零件,根据既省材料容易操作的原则,人们已经设计好了n 种不同的下料方式,设第j 种下料方式中可下得第i 种零件
ij
a 个,又已知第i 种零件得需要量为i
b 个, j x
表示第
j
B 种下料方式所消耗得零件数目, j c
表示第
j
B 种下料方式所得余料(j=1, 2 , ⋯,
n, j x
∈ Z)。
满足条件的切割方案有很多种,现在要求既满足需要又使所用原材料数量最少,即最优下料方案满足:μp=min (∑j c j
x )约束条件:∑
ij a j x =i
b ,
j
x ∈Z 。
线性规划数学模型
根据线性规划算法,约束条件包括两部分:一是等式约束条件,二是变量的非负性。
出变量的非负要求外,还有其他不等式约束条件,可通过引入松弛变量将不等式约束化成等式约束形式。
如果是求最大值的,则松弛模型最优解对应的目标函数值必大于或等于整数规划最优解对应的目标函数值;如果问题是求最小值,则松弛模型最优解对应的目标函数值必于或等于整数规划最优解对应的目标函数值。
因此对于最优下料方案模型为:
[]()1
1
min 1n
p j j
j n
ij j j
j j f c x a x b x z μ==+⎧
==⎪⎪⎪=⎨⎪⎪∈⎪⎩∑∑
由式(1)的线性规划(LP)引入松弛变量
()20][min 1
1
⎪⎪⎪⎪⎩
⎪⎪⎪⎪⎨⎧
>===∑∑==j n
j i
j ij n
j j
j p x b x a x c f μ 如果得到的最优解是整数,则求解结束。
该最优解也是式(1)的最优解。
否则,得到的最优解只是式(1)的最优解的一个下界。
这样可以把式(1)划分为两个子问题。
再对式(3)和式(4)继续上述过程。
若在某一时刻得到了一个全整数解xm,则xm 为式(1)的一个上界。
此时 ,若打算从子问题k 开始分支,而这一问题的下界为xk>xm,则这一分支不必再考虑了,因为在这一分支中不会找到小于xm 的解。
如果xk<xm,则分支过程还要继续 。
MATLAB 一维优化算法
求解整数线性规划MATLAB程序 :
function [ x, y] = ILp ( f, G, h, Geq, heq, lb, ub, x, id, options)
global upper op t c x0 A b Aeq beq ID options;
if nargin < 10, options = optimset( { } ) ; options. Disp lay = ’off’;
op tions. LargeScale = ’off’; end
if nargin < 9, id = ones( size ( f) ) ; end
if nargin < 8, x = [ ] ; end
if nargin < 7 | isemp ty( ub) , ub = inf*ones( size ( f) ) ; end
if nargin < 6 | isempty( lb) , lb = zeros( size ( f) ) ; end
if nargin < 5, heq = [ ] ; end
if nargin < 4, Geq = [ ] ; end
upper = inf; c = f; x0 = x; A = G; b = h; Aeq = Geq; beq = heq; ID
= id;
ftemp = ILP ( lb ( : ) , ub ( : ) ) ;
x = opt; y = upper;
function ftemp = ILP ( vlb, vub)
global upper op t c x0 A b Aeq beq ID options;
[ x, ftemp, how ] = linp rog ( c, A, b, Aeq, beq, vlb, vub, x0, op-
tions) ;
if how < = 0
return;
end;
if ftemp - upper > 0. 00005 % in order to avoid error
return;
end;
ifmax( abs( x*ID - round ( x*ID) ) ) < 0. 00005
if upper - ftemp > 0. 00005 % in order to avoid error
op t = x’; upper = ftemp;
return;
else
op t = [ op t; x’] ;
return;
end;
end;
notintx = find ( abs( x - round ( x) ) > = 0. 00005) ; % in order to avoid error
intx = fix( x) ; tempvlb = vlb; tempvub = vub;
if vub ( notintx(1, 1) , 1) > = intx( notintx(1, 1) , 1) + 1;
tempvlb (notintx(1, 1) , 1) = intx( notintx(1, 1) , 1) + 1;
ftemp = IntLP ( tempvlb, vub) ;
end;
if vlb ( notintx(1, 1) , 1) < = intx( notintx(1, 1) , 1)
tempvub ( notintx(1, 1) , 1) = intx( notintx(1, 1) , 1) ;
ftemp = IntLP ( vlb, tempvub) ;
end;
2 线性规划实例分析
某车间有一大批长130cm的棒料,根据加工零件的要求,需要从这批棒料中成套截取70cm长的毛坯不少于100根,32cm长的毛坯不少于100根,35cm 长的毛坯不大于100根。
要求合理设计下料方案,使剩下的边角料总长最短。
分析:对于一维下料问题都可以用组合最优化的方法给出合理的下料方式。
该题要求剩余边角料总长最短,可以转化为求使用原材料的量最少。
设x1, x2, x3分别表示所需3种不同长度的棒料零件数,则70x1+32x2+35x3≤130(xi∈
Z+,i=1, 2, 3)。
其中x1≤1 ,表1给出下料方案。
表1 下料方案
由表1可列出目标函数及其约束条件
()1234561213452
34
min 2825283122510024100
52100
(1,2,3,4,5,6)j f x x x x x x x x x x x x x x x x z j +⎧=+++++⎪
+≥⎪⎪
+++≥⎨⎪++≤⎪⎪∈=⎩
用上面的MATLAB 程序求解方程组(5) > > c = [ 28, 25, 28, 31, 2,25];
> >A = [1, 1, 0, 0, 0;1,0, 1, 2, 4; 0,1,2,1,0;0,0,3]; > > b = [ 100; 100; 100 ];
> > [ x, f ] = ILp ( c, [ ] , [ ] , A, b, [ 0, 0, 0, 0, 0,0, ] , [ inf, inf, inf, inf, inf, inf,] ) ; x =[ 0 100 0 0 25 0]
由此可知按B2方式下100根,B5方式下25根,其余方式都不用,按这种方式下料最高。
3 结论及体会
通过用MATLAB 软件按
照一维下料问题优化进行分析,优化下料要求最大限度地节约原材料,提高原材料的利用率。
本次设计又加深了对机械优化设计的认识,提高了自己分析问题、解决实际问题的能力;利用软件可以快速、简洁的解决问题。