10钢球抗冲击实验记录
冲击实验报告

冲击实验报告一.实验目的1.掌握常温下金属冲击试验方法;2.了解冲击试验机结构、工作原理及正确使用方法。
二.实验设备JBW-300冲击试验机及20#钢试样和40Cr试样。
三.实验原理:冲击试验是根据许多机器零件在工作时受到冲击载荷作用提出来的。
冲击载荷是动载荷,它在短时间内产生较大的力,在这种情况下往往对材料的组织缺陷反映更敏感。
在冲击试验中,我们认为材料存在截面突变、即缺口,冲击动能在零件内的分布是不均匀的,在缺口处单位体积内将吸取较多的能量,从而使该处的应力、应变值增大。
因此,Ak或ak 值都是代表材料缺口敏感度。
冲击载荷与静拉伸的主要区别在于加载速度不同。
拉伸速度一般在10-4~10-2mm/s,而冲击速度为102~104mm/s,静载荷作用于构件,一般不考虑惯性力的影响,而冲击载荷作用下惯性的作用不可忽视。
四﹑试样的制备若冲击试样的类型和尺寸不同,则得出的实验结果不能直接比较和换算。
本次试验采用U型缺口冲击试样。
其尺寸及偏差应根据GB/T229-1994规定,见图1-2。
加工缺口试样时,应严格控制其形状﹑尺寸精度以及表面粗糙度。
试样缺口底部应光滑﹑无与缺口轴线平行的明显划痕。
五﹑实验原理冲击试验利用的是能量守恒原理,即冲击试样消耗的能量是摆锤试验前后的势能差。
试验时,把试样放在图1-2的B处,将摆锤举至高度为H的A处自由落下,冲断试样即可。
摆锤在A处所具有的势能为:E=GH=GL(1-cosα) (1-1)冲断试样后,摆锤在C处所具有的势能为:E1=Gh=GL(1-cosβ)。
(1-2)势能之差E-E1,即为冲断试样所消耗的冲击功A K:A K=E-E1=GL(cosβ-cosα) (1-3)式中,G为摆锤重力(N);L为摆长(摆轴到摆锤重心的距离)(mm);α为冲断试样前摆锤扬起的最大角度;β为冲断试样后摆锤扬起的最大角度。
图1-3冲击试验原理图六﹑实验步骤1. 测量试样的几何尺寸及缺口处的横截面尺寸。
材料冲击实验报告

材料冲击实验报告1. 引言材料的抗冲击性能是评估其在受到外界冲击载荷时能否保持完整性和功能性的重要指标。
为了研究材料的冲击性能,本实验通过对不同材料的冲击实验,评估材料的抗冲击能力,并分析材料的破坏机制。
本实验选取了三种常见的材料进行了冲击测试,包括金属材料 (铝合金),塑料材料 (聚丙烯)和弹性材料 (聚氨酯)。
2. 实验目的•评估不同材料的抗冲击性能;•分析不同材料的破坏机制;•探讨材料冲击性能与材料特性的关系。
3. 实验装置和材料3.1 实验装置本实验使用的实验装置包括:•冲击试验机:用于提供冲击载荷;•冲击台:固定试样并接受冲击载荷;•冲击传感器:用于测量冲击过程中的载荷;•计算机数据采集系统:用于记录和分析实验数据。
3.2 实验材料本实验选取的材料包括:1.铝合金:作为典型的金属材料,具有很高的强度和硬度。
2.聚丙烯:作为典型的塑料材料,具有良好的韧性和耐冲击性。
3.聚氨酯:作为典型的弹性材料,具有很高的延展性和回弹性。
4. 实验方法4.1 样品制备首先,将铝合金、聚丙烯和聚氨酯分别加工为具有一定尺寸的试样,保证每个试样的尺寸和几何形状一致。
4.2 实验步骤1.将制备好的铝合金试样固定在冲击台上,调整冲击试验机的参数 (如冲击速度、冲击角度等)。
2.使用计算机数据采集系统连接冲击传感器,并调试传感器使其正常工作。
3.进行铝合金试样的冲击实验。
记录冲击过程中的载荷变化,并实时通过计算机数据采集系统保存数据。
4.重复上述步骤,分别对聚丙烯和聚氨酯试样进行冲击实验。
5.对实验得到的数据进行处理和分析,评估不同材料的抗冲击性能。
5. 实验结果和讨论经过冲击实验,得到了铝合金、聚丙烯和聚氨酯试样在不同冲击载荷下的载荷变化曲线。
根据实验数据,可以得到以下结论:1.铝合金在冲击载荷下承受能力较高,其载荷变化曲线较为平缓,说明其具有较好的抗冲击性能。
2.聚丙烯在冲击载荷下表现出较好的韧性,载荷变化曲线相对平缓,但其承受能力相对铝合金较低。
冲击试验和疲劳强度实验
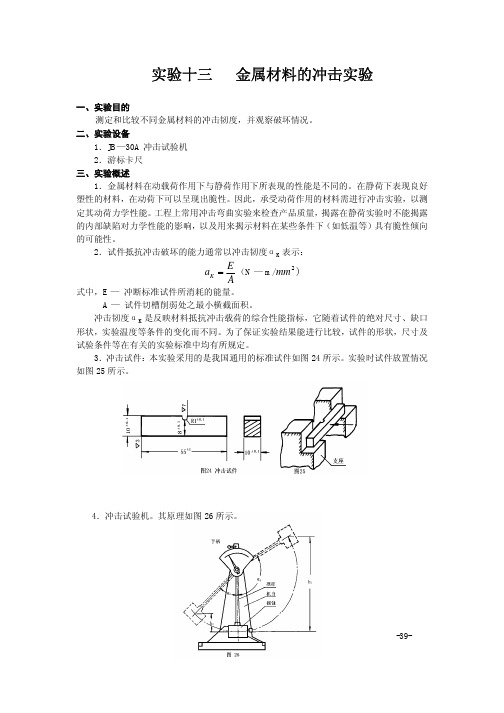
实验十三 金属材料的冲击实验一、实验目的测定和比较不同金属材料的冲击韧度,并观察破坏情况。
二、实验设备1.JB—30A 冲击试验机 2.游标卡尺 三、实验概述1.金属材料在动载荷作用下与静荷作用下所表现的性能是不同的。
在静荷下表现良好塑性的材料,在动荷下可以呈现出脆性。
因此,承受动荷作用的材料需进行冲击实验,以测定其动荷力学性能。
工程上常用冲击弯曲实验来检查产品质量,揭露在静荷实验时不能揭露的内部缺陷对力学性能的影响,以及用来揭示材料在某些条件下(如低温等)具有脆性倾向的可能性。
2.试件抵抗冲击破坏的能力通常以冲击韧度αK 表示:AE a K =(N — m/)2mm 式中,E — 冲断标准试件所消耗的能量。
A — 试件切槽削弱处之最小横截面积。
冲击韧度αK 是反映材料抵抗冲击载荷的综合性能指标,它随着试件的绝对尺寸、缺口形状,实验温度等条件的变化而不同。
为了保证实验结果能进行比较,试件的形状,尺寸及试验条件等在有关的实验标准中均有所规定。
3.冲击试件:本实验采用的是我国通用的标准试件如图24所示。
实验时试件放置情况如图25所示。
-39-4.冲击试验机。
其原理如图26所示。
绕水平轴转动的摆杆下部装有摆锤,摆锤中央凹口中装有冲击刀刃。
冲击前,装好试件,将摆锤按规定抬起一角度α1,当摆锤自由下落时,将试件冲断,由于冲断试件消耗了一部分能量,因此摆锤能继续向左运动摆起一个角度α2。
所以冲断试件的能量为)(21h h Q E −=)cos (cos 12a a Ql −=此能量E 可直接在机器的度盘上读出。
四.实验步骤1.记录室温。
2.测量试件尺寸。
3.检查机器,校正零点。
检查机器运动部分和钳口座等的固结情况。
校零点用空摆实验进行。
4.安装试件。
将摆锤拉起一角度,然后将试件放入钳口座,并用样板校正位置以对准刀刃。
5.将度盘上指示副针拨至度盘左端,准备实验。
6.冲击实验。
将电器控制盒拿在手中,操作者与观察者均远离试验机一米以上。
钢冲击实验报告
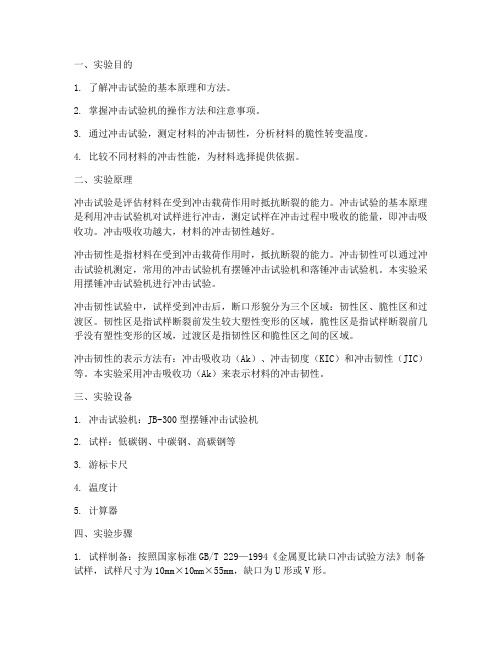
一、实验目的1. 了解冲击试验的基本原理和方法。
2. 掌握冲击试验机的操作方法和注意事项。
3. 通过冲击试验,测定材料的冲击韧性,分析材料的脆性转变温度。
4. 比较不同材料的冲击性能,为材料选择提供依据。
二、实验原理冲击试验是评估材料在受到冲击载荷作用时抵抗断裂的能力。
冲击试验的基本原理是利用冲击试验机对试样进行冲击,测定试样在冲击过程中吸收的能量,即冲击吸收功。
冲击吸收功越大,材料的冲击韧性越好。
冲击韧性是指材料在受到冲击载荷作用时,抵抗断裂的能力。
冲击韧性可以通过冲击试验机测定,常用的冲击试验机有摆锤冲击试验机和落锤冲击试验机。
本实验采用摆锤冲击试验机进行冲击试验。
冲击韧性试验中,试样受到冲击后,断口形貌分为三个区域:韧性区、脆性区和过渡区。
韧性区是指试样断裂前发生较大塑性变形的区域,脆性区是指试样断裂前几乎没有塑性变形的区域,过渡区是指韧性区和脆性区之间的区域。
冲击韧性的表示方法有:冲击吸收功(Ak)、冲击韧度(KIC)和冲击韧性(JIC)等。
本实验采用冲击吸收功(Ak)来表示材料的冲击韧性。
三、实验设备1. 冲击试验机:JB-300型摆锤冲击试验机2. 试样:低碳钢、中碳钢、高碳钢等3. 游标卡尺4. 温度计5. 计算器四、实验步骤1. 试样制备:按照国家标准GB/T 229—1994《金属夏比缺口冲击试验方法》制备试样,试样尺寸为10mm×10mm×55mm,缺口为U形或V形。
2. 试样测量:使用游标卡尺测量试样尺寸,精确到0.01mm。
3. 冲击试验:将试样放入冲击试验机的试样夹具中,调整试样位置,使缺口位于冲击方向。
4. 冲击试验机操作:打开冲击试验机电源,调整摆锤高度,使摆锤与试样距离为一定的距离。
按动冲击试验机按钮,使摆锤自由落下冲击试样。
5. 数据记录:记录冲击试验过程中冲击吸收功(Ak)、冲击韧度(KIC)等数据。
6. 冲击试验重复:对同一试样进行多次冲击试验,取平均值作为最终结果。
突起路标抗冲击性能、抗压荷载检测记录表

抗压最大力值
校核:计算:检验:
试样编号:
一、整体抗冲击性能:
要求:经质量1040g±10g的实心钢球,在突起路标上方1m的高度自由落下,突起路标上表面的中心处直径12mm的区域外不应有任何形式的破损。
试样编号
受冲击后破损情况
二、抗压荷载:
要求:以2.5mm/min的速率对突起路标进行加载,直到样品破坏或样品产生明显变形(大于3.3mm)为止,A1、A2类突起路标的最大力值应不小于160KN,A3类突起路标应不小于245KN。
试-X-XXX
XXX工程检测有限公司
突起路标抗冲击性能、抗压荷载检测记录表
记录编号:第页,共页
委托单编号:
检评规程:
委托方名称:
检测环境:温度:℃湿度: %
委托方地址:
检测日期:年日
工程名称:
检测仪器:突起路标耐冲击测定装置、0.5级电子万能材料试验机
工程部位:
仪器编号:
试样型号:
抽样人:
试样产地:
冲击实验报告总结

冲击实验报告总结
本次实验是一次关于冲击力的实验,旨在探究物体在受到不同冲击力作用下的反应。
在实验中,我们通过使用冲击力计对不同重量的物体进行了多次冲击实验,记录下了每次实验中物体受到的冲击力和位移等数据,并对数据进行了统计和分析。
通过实验,我们得出了以下几个结论:
1.物体在受到较大的冲击力作用下,会产生较大的位移。
2.不同重量的物体在受到相同的冲击力作用下,产生的位移和反应有所不同。
3.在实验中,使用冲击力计可以较为准确地记录下物体受到的冲击力和位移等数据。
通过本次实验,我们对物体在受到不同冲击力作用下的反应有了更深入的了解,并且掌握了一定的实验操作技能。
同时,我们也发现,在实验过程中需要注意安全,避免产生意外情况。
在今后的学习和科研中,我们将继续深入探究物体受力的规律和反应,为实际生产和应用提供更多的科学依据和技术支持。
- 1 -。
小球冲击测试数据收集
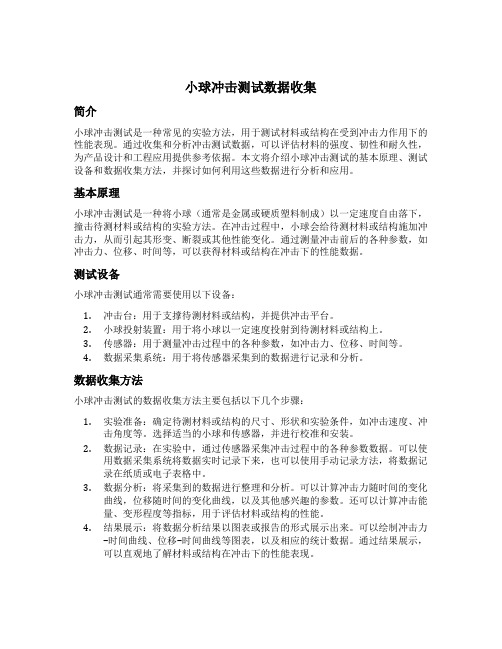
小球冲击测试数据收集简介小球冲击测试是一种常见的实验方法,用于测试材料或结构在受到冲击力作用下的性能表现。
通过收集和分析冲击测试数据,可以评估材料的强度、韧性和耐久性,为产品设计和工程应用提供参考依据。
本文将介绍小球冲击测试的基本原理、测试设备和数据收集方法,并探讨如何利用这些数据进行分析和应用。
基本原理小球冲击测试是一种将小球(通常是金属或硬质塑料制成)以一定速度自由落下,撞击待测材料或结构的实验方法。
在冲击过程中,小球会给待测材料或结构施加冲击力,从而引起其形变、断裂或其他性能变化。
通过测量冲击前后的各种参数,如冲击力、位移、时间等,可以获得材料或结构在冲击下的性能数据。
测试设备小球冲击测试通常需要使用以下设备:1.冲击台:用于支撑待测材料或结构,并提供冲击平台。
2.小球投射装置:用于将小球以一定速度投射到待测材料或结构上。
3.传感器:用于测量冲击过程中的各种参数,如冲击力、位移、时间等。
4.数据采集系统:用于将传感器采集到的数据进行记录和分析。
数据收集方法小球冲击测试的数据收集方法主要包括以下几个步骤:1.实验准备:确定待测材料或结构的尺寸、形状和实验条件,如冲击速度、冲击角度等。
选择适当的小球和传感器,并进行校准和安装。
2.数据记录:在实验中,通过传感器采集冲击过程中的各种参数数据。
可以使用数据采集系统将数据实时记录下来,也可以使用手动记录方法,将数据记录在纸质或电子表格中。
3.数据分析:将采集到的数据进行整理和分析。
可以计算冲击力随时间的变化曲线,位移随时间的变化曲线,以及其他感兴趣的参数。
还可以计算冲击能量、变形程度等指标,用于评估材料或结构的性能。
4.结果展示:将数据分析结果以图表或报告的形式展示出来。
可以绘制冲击力-时间曲线、位移-时间曲线等图表,以及相应的统计数据。
通过结果展示,可以直观地了解材料或结构在冲击下的性能表现。
数据分析与应用收集到的小球冲击测试数据可以用于以下方面的分析和应用:1.材料评估:通过分析冲击测试数据,可以评估材料的强度、韧性和耐久性。
冲击试验实验报告
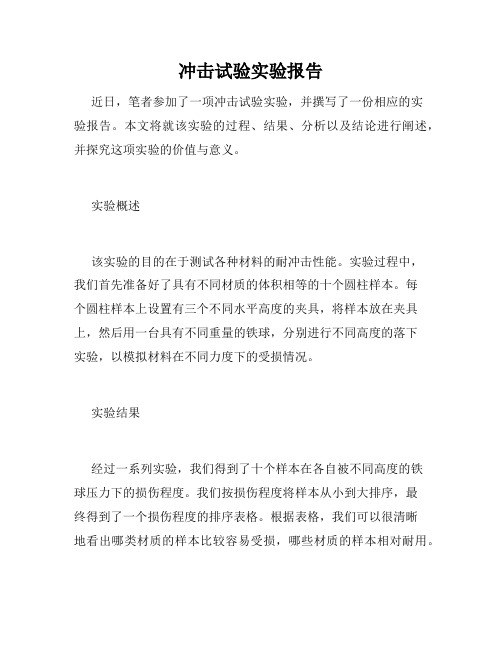
冲击试验实验报告近日,笔者参加了一项冲击试验实验,并撰写了一份相应的实验报告。
本文将就该实验的过程、结果、分析以及结论进行阐述,并探究这项实验的价值与意义。
实验概述该实验的目的在于测试各种材料的耐冲击性能。
实验过程中,我们首先准备好了具有不同材质的体积相等的十个圆柱样本。
每个圆柱样本上设置有三个不同水平高度的夹具,将样本放在夹具上,然后用一台具有不同重量的铁球,分别进行不同高度的落下实验,以模拟材料在不同力度下的受损情况。
实验结果经过一系列实验,我们得到了十个样本在各自被不同高度的铁球压力下的损伤程度。
我们按损伤程度将样本从小到大排序,最终得到了一个损伤程度的排序表格。
根据表格,我们可以很清晰地看出哪类材质的样本比较容易受损,哪些材质的样本相对耐用。
分析与讨论针对每个样本,我们还进行了详细的分析。
我们发现,当铁球以较小的高度(例如20厘米)落下时,多数样本没有显示出任何损伤,这是因为材质强度并不足以导致塑性变形。
但随着铁球落下高度的增加,样本之间的差异逐渐明显。
比如说,当铁球以60厘米的高度落下时,由铝制成的样本出现了明显的划伤和凹陷,而由碳纤维制成的样本却几乎没有受损。
这意味着在某些领域里,碳纤维可能比铝更适合用于制造耐久性产品。
结论本实验显示出了各种材料在不同力度下的耐冲击性能。
它提供了有关材料的重要信息,以指导工程师优化设计,改进材料选择和加强产品质量。
此外,该实验还提供了学生进行材料失效和破坏分析的机会,进而提升教学效果。
然而,本实验存在一定的局限性,例如未考虑材料与温度和湿度的相互作用等因素,仍需基于实际应用情景进一步研究。
因此,未来的探索和研究仍需要人们对实验方法和结果的不断探索和验证。
总之,本实验为我们展示了材料的耐久性和性能,并为工程师和研究人员提供了重要的信息,有助于设计更加优越的与产品。
同时,该实验还带来了许多教育上的益处,使我们更好地了解材料的特性和机制。