注塑工艺制程检查表
注塑车间检查表

冷却时间均在规格内 抽查包装箱或者其它包装物核对填
写项目是否完整、有无错误 是否在不合格区域?有无责任人,
完成期限?有无复检?报废有无记
检查结果(填写不符合内容)
符合打○
19
所有检验人员经过培训上岗,具 清点当班人数,核对培训记录,当
备能力
面问答
20
检验人员有GP或RoHS方面的培 训
清点当班人数,核对培训记录,当 面问答
对比规定的温度和实际显示的温度
10 11
12
现现场场是是否否有 有受受控控的的作《业成指型导参书数表
》 注塑原料温度(螺杆温度)是否
受控
实际查看,是ቤተ መጻሕፍቲ ባይዱ和生产的一致
实际查看,是否和生产的一致 供货商推荐的温度、《成型参数表 》要求的温度、实际显示的温度均 在规格内
13 射出速度是否受控
《成型参数表》要求的速度、实际 显示的速度均在规格内
实际测量 查看IPQC检验记录,核对信赖度
25 所有信赖度测试受控
测试是否完整、是否在规格之内,
频率合适,并观察实际测试
26
CP中如有规定对某特性进行SPC 查看核对CP舆IPQC的巡检记录表
管控,实际是否有执行
及相关记录
27 各区域内是否有其他产品
目视检查
28 机器是否漏油\漏水
目视检查
29 斑马线是否破损
南通大明电子科技有限公司
注塑过程检查表
序 号
1
检查项目
检查方法
所有技朮、操作人员经过培训上 清点当班人数,核对培训记录,当
岗,具备能力
面问答
2
以上人员有GP或RoHS方面的培 清点当班人数,核对培训记录,当
MM0011-02A 注塑成型工艺点检表
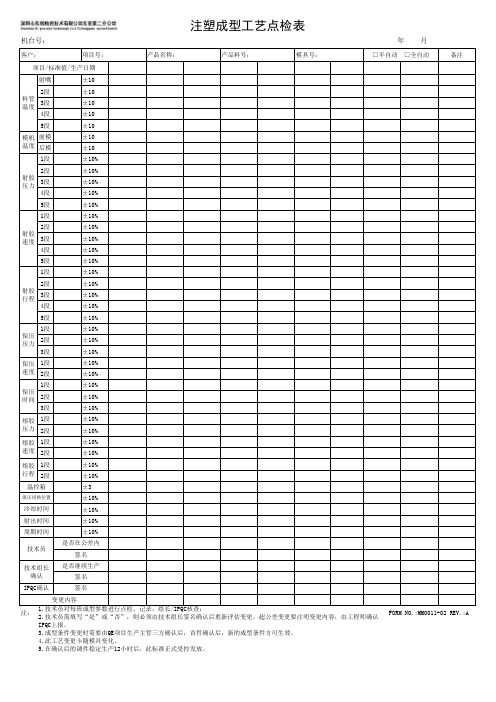
备注射嘴±102段±103段±104段±105段±10前模±10后模±101段±10%2段±10%3段±10%4段±10%5段±10%1段±10%2段±10%3段±10%4段±10%5段±10%1段±10%2段±10%3段±10%4段±10%5段±10%1段±10%2段±10%3段±10%1段±10%2段±10%1段±10%2段±10%3段±10%1段±10%2段±10%1段±10%2段±10%1段±10%2段±10%±3±10%±10%±10%±10%注:注塑成型工艺点检表机台号:年 月客户:项目号:产品名称:产品料号:模具号:FORM NO.:MM0011-02 REV.:A 料管温度项目/标准值/生产日期射胶压力模机温度射胶速度射胶行程保压压力保压速度熔胶压力保压时间熔胶速度熔胶行程保压切换位置温控箱射出时间冷却时间技术员是否在公差内签名周期时间签名是否继续生产技术组长确认变更内容2.技术员需填写“是”或“否”,则必须由技术组长签名确认后重新评估变更。
超公差变更要注明变更内容,由工程师确认IPQC上报。
3.成型条件变更时需要由QE项目生产主管三方确认后,首件确认后,新的成型条件方可生效。
4.此工艺变更卡随模具变化。
5.在确认后的调件稳定生产12小时后,此标准正式受控发放。
□半自动 □全自动IPQC确认签名。
标准注塑周期核查表

产品名称
模具代号:
塑料名称
注塑机型:
项目类型 项目序号
项目名称
1 开模时间(见附表1)
2 合模时间(见附表1)
3 射胶时间(见附表1)
4 保压时间(见附表1)
注塑机型
5 6
冷却时间(见附表2) 顶出时间(见附表1)
7 机型>=180T >=350T
8 半自动
9 机械手(+2/+3)
10 高温料(+2)
11 铝/铍铜内模
冷 运热油
15 三板模/倒装模/叠模/其他特殊模具
16 1-2行位/3个以上
17 内行位/抽Core
模具结构 18 多处斜顶
19 二次顶出/多次顶出/顶出抖动
20 模温高温
21 内置嵌件
热流道
22 熱唧嘴 23 熱流道
24 粘模
审核结果 未达标
设计周期 实际周期
时间增减
+2/+4 +2
+2/+3 +2 -3 -3 +3 +5 +3
+1/+2 +2 +2 +2
+1到+4 +2X -3 -4 +1 +1 +3 +2 +1 +2 +3 +1 +2 +2/+3 +5 +2
+1到+3 标准周期
达标 制表:赵
利峰
表
时间统计
25 出模不良(捡用/检查)
26 冷却不良
27 深Core、骨、柱
制程检查表
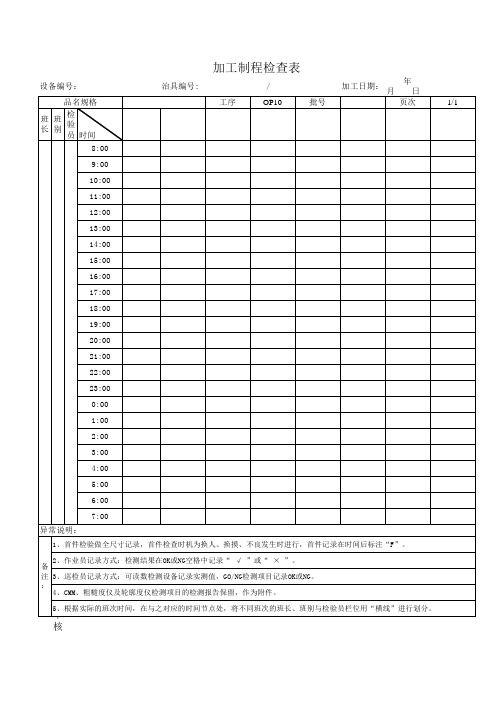
3:00
4:00
5:00Βιβλιοθήκη 6:007:00 异常说明:
1、首件检验做全尺寸记录,首件检查时机为换人、换摸、不良发生时进行,首件记录在时间后标注“F”。
2、作业员记录方式:检测结果在OK或NG空格中记录“ √ ”或“ × ”。 备 注 3、巡检员记录方式:可读数检测设备记录实测值,GO/NG检测项目记录OK或NG。 :
4、CMM、粗糙度仪及轮廓度仪检测项目的检测报告保留,作为附件。
5审、根据实际的班次时间,在与之对应的时间节点处,将不同班次的班长、班别与检验员栏位用“横线”进行划分。 核
设备编号:
品名规格
班 长
班 别
检 验 员
时间
8:00
加工制程检查表
治具编号:
/
加工日期:
年 月 日
工序
OP10
批号
页次
1/1
9:00
10:00
11:00
12:00
13:00
14:00
15:00
16:00
17:00
18:00
19:00
20:00
21:00
22:00
23:00
0:00
1:00
2:00
注塑制程检验表

机显数:
8:00~10:00
10:00~12: 00
12:00~14:00
14:00~16: 00
16:00~18:00 18:00~20:30
出模数不准确
首件试生产 1次/天
重点尺寸1 (标准: 重点尺寸2 (标准: 重点尺寸3 (标准:
每一个模号试产1个,产品外观、尺寸是否正常。 是□
(外观要求:不可有披锋溢出、端子歪斜、变形等现象)
□让步接收
合计
江门市杰马科技有限公司
机台号:
Seemarket Technology Co., Ltd.
注塑制程检验表
日期:
IPQC:
审核:
产品名称:
材料规格:
生 1、产外批观次巡号拉:检查。 (检查频次:1次
检查组装 (检查数量 1啤)
首件检验
出模数: 入库单 号:
抽检检验记录,抽
样标准AQL Ⅱ,级
别:
数
量:
抽样
注数意量::每天产量与产品
数量误差要少于300个
检验项目 表面
检验标准
无颜色色差,哑光、顶白、黑 点 无不饱胶、缩水、变形
外观
无气泡、水纹、银纹、色纹
无油污、污物
披锋
无披锋、堵孔
其他
检验记录
不良数
判定
最终判定
□允收
□拒收
如判定拒收,请记录注塑产品的处理方式:
) ) )
否□
异常记录
判定
注意:1、注塑车间开机停机后要通知IPQC及时进行首检,检验合格后方可生产。 2、IPQC每天要检查初始生产的产品,观察是否出现少胶、粘模、披锋等不良现象。 3、检查外观合格后,即可通知生产员工,将产品放入蓝色待检筐中。
注塑成型工艺点检表

点检人
2、端盖生产工艺: 1)、模具温度:模芯和模腔的温度必须控制在50——70℃,两者温差要小 于6 ℃,且模腔温度较高。模具温度未达到要求不允许生产。(需现场测 试) 2)、注塑压力:控制在70——90kg/cm2(通常),根据实际情况可放宽至 100kg/cm2,但不允许超过100kg/cm2。 3)、保压:保压时间控制在5——20s,尽量控制在8s;根据注塑机的类 型,最高保压压力控制在50——70kg/cm2内。(注意:注射压力和液压系 统的压力是两个不同的概念,注射压力是指螺杆或柱塞端面处作用于机筒 内熔融塑料单位面积上的力。我们通过压力表和设备操作屏检测到的实际 为液压系统的压力)。
位置
7 8 9 10 11 12 13 14 15 16 17 18
1、口框生产工艺: 1)、模具温度:模芯和模腔的温度必须控制在50——70℃,两者温差要小 于6 ℃,且模腔温度较高。模具温度未达到要求不允许生产。(需现场测 试) 2)、注塑压力:控制在70——90MPa(通常),根据实际情况可放宽至 125MPa,但不允许超过125MPa。 3)、保压:保压时间控制在5——20s,尽量控制在8s;根据注塑机的类 型,最高保压压力控制在50——70MPa内。(注意:注射压力和液压系统的 压力是两个不同的概念,注射压力是指螺杆或柱塞端面处作用于机筒内熔 融塑料单位面积上的力。我们通过压力表和设备操作屏检测到的实际为液 压系统的压力)。
点检时间 标准值
注塑成型工艺点检表
机台编号
项目 分类 标准值 1段 射出 压力 2段 3段 4段 1段 射出 速度 2段 3段 4段 1段 射出 位置 2段 3段 7
注塑制程巡检记录表

机号:
产品名称/零件号:
检查时间 时分
检验标准
检验类型
熔 接 线
缩 水
缺 料
银 纹
拉飞划 丝边伤
《注塑检验作业指导书》 巡检
《注塑检验
《注塑检验作业指导书》 巡检
《注塑检验作业指导书》 巡检
《注塑检验作业指导书》 巡检
《注塑检验作业指导书》 巡检
《注塑检验作业指导书》 巡检
《注塑检验作业指导书》 巡检
日期:
班组:
检验项目
重量 尺寸1 尺寸2 尺寸3 尺寸4 判 定
检查人
备注:打“√”表示合格,打“×”表示不合格,“NA”表示不适用,尺寸和重量需填写实际测量数据。
异常处置
注塑成型工艺点检表

192021222324123456压力速度位置1段2段193段204段211段222段233段244段11段22段33段44段561段2段3段1段2段3段1段2段3段前模后模点检人审核1、口框生产工艺:1)、模具温度:模芯和模腔的温度必须控制在50——70℃,两者温差要小于6 ℃,且模腔温度较高。
模具温度未达到要求不允许生产。
(需现场测试)2)、注塑压力:控制在70——90MPa (通常),根据实际情况可放宽至125MPa ,但不允许超过125MPa 。
3)、保压:保压时间控制在5——20s ,尽量控制在8s;根据注塑机的类型,最高保压压力控制在50——70MPa 内。
(注意:注射压力和液压系统的压力是两个不同的概念,注射压力是指螺杆或柱塞端面处作用于机筒内熔融塑料单位面积上的力。
我们通过压力表和设备操作屏检测到的实际为液压系统的压力)。
2、端盖生产工艺:1)、模具温度:模芯和模腔的温度必须控制在50——70℃,两者温差要小于6 ℃,且模腔温度较高。
模具温度未达到要求不允许生产。
(需现场测试)2)、注塑压力:控制在70——90kg/cm2(通常),根据实际情况可放宽至100kg/cm2,但不允许超过100kg/cm2。
3)、保压:保压时间控制在5——20s ,尽量控制在8s;根据注塑机的类型,最高保压压力控制在50——70kg/cm2内。
(注意:注射压力和液压系统的压力是两个不同的概念,注射压力是指螺杆或柱塞端面处作用于机筒内熔融塑料单位面积上的力。
我们通过压力表和设备操作屏检测到的实际为液压系统的压力)。
保压压力保压速度保压时间模具温度分类标准值夜班实际点检值(时间)储料注塑时间(S )模温机温度冷却时间成型周期项目射出压力射出速度射出位置注塑成型工艺点检表生产日期机台编号产品名称产品图号(编码)标准值点检时间。
- 1、下载文档前请自行甄别文档内容的完整性,平台不提供额外的编辑、内容补充、找答案等附加服务。
- 2、"仅部分预览"的文档,不可在线预览部分如存在完整性等问题,可反馈申请退款(可完整预览的文档不适用该条件!)。
- 3、如文档侵犯您的权益,请联系客服反馈,我们会尽快为您处理(人工客服工作时间:9:00-18:30)。
注塑产品连续生产中会遇到设备故障维修,员工中午吃饭等,应策划停机多久需要重
新进行作业准备验证,首件检验,是否中午员工吃饭接机等,因为停机后模温会降
低,如PP材料,停机半小时以内回复生产后产品不会产生太大影响,但ABS材料停机10
分钟以上可能会导致注塑机内材料讲解风险,产品变形风险,外观缺料等风险
注塑产品常见的不良有油污、缺料、裂纹、发白、削缺、收缩变形、明显的熔接痕
注塑调机工序影响产品尺寸,针对产品尺寸(关键装配尺寸)识别为特殊特性的,对
应调机过程应识别为特殊过程,并策划到对应的文件中,如过程特殊特性清单、PFMFA
、控制计划、作业指导书或工艺卡中
注塑机热流道温度、射出位置、射出压力、射出速度、保压压力、保压速度、保压时
间、储料位置、储料压力、储料速度、储料背压、冷却时间、成型周期等影响注塑成
型关键参数需进行工艺策划,形成作业指导文件
注塑调机为特殊过程,针对影响产品关键装配吃好吃的调机参数,如热流道温度、射
出位置、射出压力、射出速度、保压压力、保压速度、保压时间、储料位置、储料压
力、储料速度、储料背压扥需进行工艺验证,并保留验证记录
注塑工艺原则上严禁使用回料,回料二次加工会产生材料讲解风险,导致物料断裂
物料的存储环境原则上需遵循厂家物料说明书要求执行,如有特殊温湿度等环境要求 的,需按要求环境存放;如物料说明书无特殊要求,物料的存储需按照工厂工艺文件 物料有效期管理原则上需遵循物料有效期标识进行管理,并建立物料保质期台账,对 于过期物料需粘贴不合格品标识并隔离,原则上报废处理,如需使用需经过试验、验 证及评审;对于物料无特殊保质期要求的,需策划定期进行产品复检(建议呆滞没6个 生产现场所使用的物料是否经过进货检验并合格,以保证物料的性能符合要求,如: 燃料特性、密度、拉伸强度、弯曲模具、冲击强度、热变形温度等。 以PP+GF20料为例要求如下: 1.燃料特性:应满足GB88410《100mm/min或UL94 HB级; 2.密度:1.05±0.02g/cm³ 3.拉伸强度:》55MPa 4.弯曲模量:》3600MPa 5.冲击强度:》60J/M 热变形温度:》110℃ 来料检验应策划注塑原材料、蒙皮等有颜色要求的外观检验项目,如对色板样件的管 控,需客户签字封样(适用时),并对样件建立有效期台账,每月对样件进行盘点, 避免样件过期或出现色差、划伤等异常 成品应建立标准样件,进行签样封存并注明有效期,同时对样件建立有效期台账,每 月对样件进行盘点,避免样件过期或产生划伤等异常 样件按照类型分开存放,同类型的已外观件或结构件进行区分存放 生产现场使用的物料需进行产品信息标识和物料装配标识,产品信息标识需包含物料 规格、型号、批次及厂家等信息,并符合作业指导书策划要求 生产现场注塑原材料加料过程中,需对原材料粒子进行防护避免落入灰尘和混入杂 物,如鼓风机在容器内吸料,需对容器加盖子进行防护 生产现场的物料是否进行有效的防护,包装无破损,原材料无裸露,不同物料不同状 态是否进行隔离区分并标识 针对有环境要求的注塑料是否有进行策划并实施管控,如温湿度 生产现场是否使用回料,回料是否进行标识注明回料,回料的使用配比,需要严格根 据作业文件执行并保留使用记录 工厂是否明确物料紧急放行权限,对物料未检验紧急放行的是否通知到顾客,必要时 需得到顾客同意,一旦发现产品不合格货存在缺陷是否通知顾客召回;紧急放行物料 需做标识并建立批次追溯信息,控制放行数量 注塑产品加料和烘烤作业需要形成作业指导书,对于料筒加料数量应考虑产品重量 (毛重)和烘烤时间,策划加料警戒线,持续保持物料烘烤时间满足要求 注塑加料工序涉及2个(含)以上物料同时加料的,需对加料比例和配方进行文件策 划,并对加料配比进行记录监控 注塑料回料的使用(配比),需进行作业文件策划员工操作 注塑涉及外观要求的产品需策划注塑料烘烤时间和温度要求,以通过烘烤作业减少水 分、避免产品外观料花、气痕,降低产品不合格率;注塑原材料加料应建立质量记录 对烘烤时间和开机时间进行监控 原料烘烤工艺要求: 1.烘料温度是否在策划的控制范围内(60-140)℃,如PP料温度控制在70-95℃,PA6 料温度控制在110-130℃; 2.原材料烘烤时间是否满足文件策划要求,如PP料烘烤时间》2H,PA6料烘烤时间》 4H; 3.原材料烘烤时间和温度的策划需进行充分地验证,如烘烤的目的是为减少水分,避 加料作业需按照作业指导书执行,核对加料物料名称、规格型号、供应商、批次等信 息,对涉及配比(配方)的需按文件执行,填写加料记录表;连续生产物料(一次烘 烤不续加除外)物料加料数量严格按照物料加料警戒线执行,物料高度不得低于警戒 加料烘烤工序作业人员需了解烘烤料筒物料警戒线控制方法,烘烤工序对产品实物质 注塑料烘烤设备温度管理影响产品外观质量,应对烘烤设备上的温度计识别为B类量具 烘烤作业需按照作业指导书执行,确认烘烤温度,确认温度计在校准有效期内,对烘 烤开始时间,开机生产时间进行记录 家里烘烤温度,应策划到首件检验规范中进行确认和记录
10.储料压力要求(20-140)MPa
11.储料速度要求(3-90)%
12.储料背压要求(3-25)MPa
注塑产品完成后需要切换其它颜色型号产品是,需要策划洗机工艺形成作业文件(料
筒的清洗),如不同夜色对产品外观有影响,不同材料对产品性能有影响,例如PP材
料产品生产完切换ABS产品,注塑机里面残留PP材料,再生产ABS材料产品时会出现2种
加料烘烤
47
加料烘烤
48
注塑成型
49注塑成型50源自注塑成型工艺 验证51
注塑成型工艺 验证
52
注塑成型
53
注塑成型
54
调机
55
调机
56
注塑成型
57
注塑成型
58
注塑成型
59
注塑成型
60
注塑成型
61
注塑成型
62
注塑成型
63
注塑成型设备 工装管理
64
注塑成型设备 工装管理
65
注塑成型设备 工装管理
66
注塑成型设备 工装管理
90 不合格品控制
注塑工艺制程检查表
评分等级参考 新进人员是否按照岗位说明书进行培训并记录;顶岗人员或者调岗人员是否按照新的 岗位进行培训并记录 生产实习人员是否有对应的实习证,转正后是否有对应的资格证书;检验人员需进行 检验方法、量检具使用及不合格品管理等培训 点检中,是否对点检的项目能有效点检,对点检出现的异常能否有对应的方案进行操 生产人员与检验人员是否能有效按照作业指导书的要求进行操作与检验 人员能力一时管理需形成文件,对各岗位人员资质进行要求,明确规定所需培训科目 并且严格按照培训要求进行;在线的操作员全部通过上岗考核,并有相关考核记录和 注塑工序作业人员上岗前需经过作业方法、设备安全操作、设备工装维护保养点检等 方面培训;设计关键工序的,需进行关键工序培训并明确岗位重要性及对产品实物质量 生产作业和检验人员应定期对顾客反馈质量问题进行学习,了解本岗位出现的失效, 避免再次发生 有识别关键岗位,并且有“三定”管理,作业员与关键岗位清单一致
序号 1
2 3 4 5
6
7 8
项目 人员
人员 人员 人员 人员
人员
人员 人员
9
文件策划
10
文件策划
11
文件策划
12
文件策划
13
文件策划
14
文件策划
15
文件策划
16 设备工装管理
17 设备工装管理
18 设备工装管理 19 设备工装管理
20 设备工装管理
21 设备工装管理
22
环境
23
环境
24
物料储备和使 用
等,如产品使用回料需进行工艺验证,燃料特性、密度、拉伸强度、弯曲强度、热变
注塑成型关键参数需文件策划对其过程参数进行监控记录
生产过程控制计划、作业指导书、检验文件是否对特殊特性进行传递,对控制计划要
求及特殊特性应进行有效传递
调机前需进行设备预热,避免因动模、定模、料筒、热流道温度不够导致产品缺料,
造成调机产品模数增加,损失质量成本;
等,应策划返工返修作业指导书,并严格按照文件执行,返工后产品需进行百分百全
检,返修后的产品涉及产品降级使用的需通知到顾客,获得让步放行许可,对于不能
返工返修的产品进行报废处理
注塑成型工序需按照作业指导书执行,确认工艺参数满足工艺卡要求,确认首件外观
、尺寸、结构满足检验规范和样件要求
注塑调机特殊过程,应策划“三定”管理,作业人员、工艺参数、设备应与策划一
67
取件
68 出水口披锋 69 出水口披锋
70 出水口披锋
71
包装
72
包装
73
产品检验
74
产品检验
75
产品检验
76
产品检验
77
产品检验
78
产品检验
79
产品检验
80
产品检验
81
产品检验
82
产品检验
83
产品检验
84
产品检验
85
产品检验
86 不合格品控制
87 不合格品控制
88 不合格品控制 89 不合格品控制
配分
对注塑机流道温度、射出位置、射出压力、射出速度、保压压力、保压速度、保压时 间、储料位置、储料压力、储料速度、储料背压等关键工艺参数是否进行了有效验 证,并策划作业文件进行管口,关键工艺参数是否被记录和监控。 工艺验证应提供一下资料: 1.工艺变更申请评审记录; 2.工艺验证报告:包含工艺验证计划、良率、CPK、MSA报告、试模记录等资料; 3.工艺变更通知等
致,现场粘贴三定(关键制程)标识
生产现场发现的不合格品如有油污、缺料、裂纹、发白、削缺、收缩变形、明显的熔
接痕等,需进行隔离标识,通知IPQC确认,对于可以返工返修的,按照返工返修作业