砂石骨料生产系统施工方案设计
(完整版)砂石料开采与加工方案
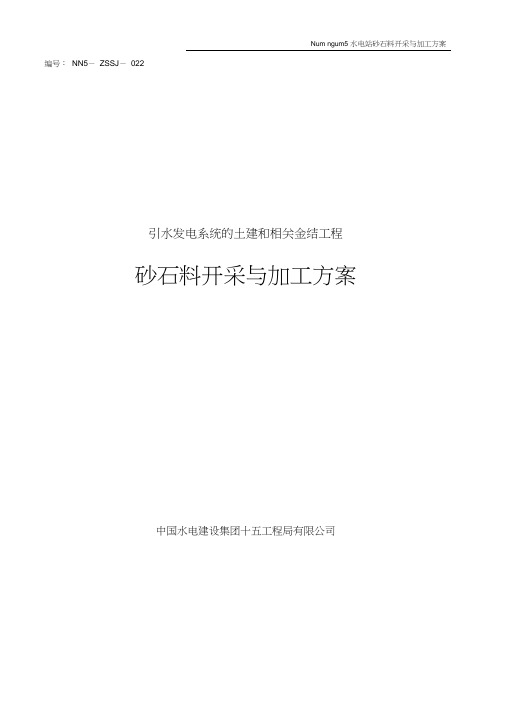
编号:NN5-ZSSJ-022引水发电系统的土建和相关金结工程砂石料开采与加工方案中国水电建设集团十五工程局有限公司2009年12月20日老挝南俄5水电站BOT项目施工技术方案目录一、工程简况 (2)二、砂石料开采方案 (2)三、采运设备选择、开采强度分析及骨料加工生产规模 (4)四、砂石料场规划 (7)五、砂石料场建设及生产计划安排. (9)南俄 5 水电站引水发电系统砂石料开采与加工方案一、工程简况南俄 5 水电站引水发电系统工程主要包括进水口、引水洞、调压井、压力管道、发电厂房和尾水洞工程,目前各工程均处于开挖和支护阶段(其中进水口开挖还剩4m至设计高程;隧洞(包括尾水洞)开挖及支护完成45%;调压井上室开挖支护完成,井筒反井钻导孔完成),除已完成部分开挖支护工程外,上述工程剩余砼111581m3,浆砌石工程7520m3(详见表1),需要砂石料约17.3万m3(其中砂子89844m3,碎石83838m3,具体见《砂石料采购计划》承包[2009]报告048 号文件),块石9200 m3。
根据我部上报的《关于再次报送牛棚河滩天然砂砾料品质检测结果及相关补充资料的报告》(编号:承包[2009]报告113 号)文件及贵部对该文件的批复,我部也进行了相应的现场探坑取样,经计算,该料场储量满足工程需要。
按施工总体安排,我部已于2009 年11月29日开始砂石料加工设备基础砼浇筑,12月4日砂石料加工设备进场。
表 1 砼及浆砌石工程量统计表、砂石料开采方案料场开采按照先主河道后河漫滩顺序分区,依次从下游向上游、从右至左次序依次开采,开采深度为3m。
开采前先将河水改道,并对表层杂物及覆盖层进行清理。
料场布置详见《牛棚砂石料场平面布置示意图》,砂石料场开采特性详见表2。
1、开采分区该料场为天然砂石料场,由于天然砂石级配在深度和平面上相差较大,而实际情况是下游以中细料为主,上游则以中粗料为主,并有少量出露的孤石。
水电站首部枢纽工程砂石加工系统设计方案
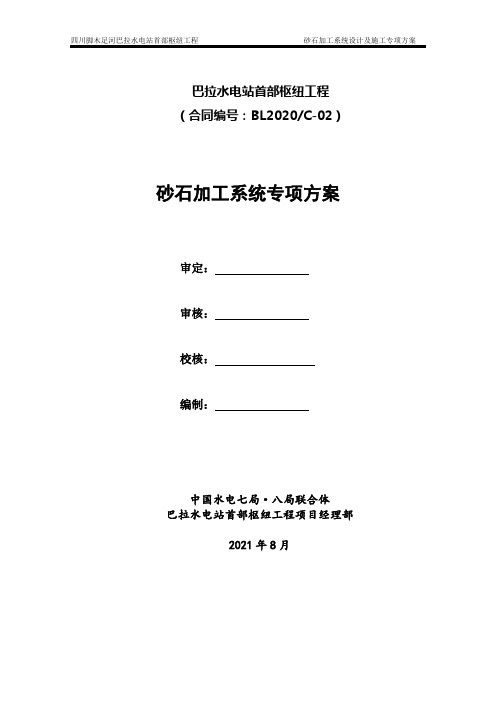
巴拉水电站首部枢纽工程(合同编号:BL2020/C-02)砂石加工系统专项方案审定:审核:校核:编制:中国水电七局·八局联合体巴拉水电站首部枢纽工程项目经理部2021年8月目录1.工程概况 (1)1.1枢纽概况 (1)1.2砂石加工系统概况 (1)2.气象与水文 (1)2.1流域概况 (1)2.2气候特征 (2)3.场地规划 (2)4.砂石生产系统设计方案 (3)4.1系统概述 (3)4.1.1系统任务 (3)4.1.2工作范围 (4)4.1.3控制性工期 (4)4.2砂石加工系统设计 (4)4.2.1设计原则及依据 (4)4.2.2料源情况 (6)4.2.3系统规模 (6)4.2.4总体设计 (7)4.2.5工艺流程设计 (8)4.2.6平面布置设计 (13)4.2.7设备选型设计 (14)4.2.8系统供水、废水处理系统设计 (16)4.2.9砂石加工系统电气设计 (16)4.2.10系统排水设计 (18)4.2.11系统主要车间结构设计 (19)4.2.12除尘、声环境保护设计 (21)4.2.13固体废弃物处理设计 (22)4.2.14临时设施设计 (22)4.2.15冬季采暖设计 (24)砂石加工系统专项设计方案1.工程概况1.1枢纽概况巴拉水电站位于四川省阿坝藏族羌族自治州马尔康市境内脚木足河上,系大渡河干流水电规划“3库28级”自上而下的第2级水电站,上接下尔呷“龙头”水库电站、下衔达维电站,地处中、高山峡谷河段。
坝址位于马尔康市日部乡色江吊桥下游约2.2km,经右岸引水至巴拉峡谷内约2km处修建地下厂房发电,并采用长尾水洞退水至峡谷外。
工程采用混合式开发,为日调节电站,开发任务为水力发电并兼顾生态用水需要。
巴拉水电站正常蓄水位2920m,最大坝高138m,相应水库容积1.277亿m ³,死水位2915m,调节库容0.163亿m³。
电站总装机容量746MW(含生态机组26MW),由一个装机3×240MW的主电站和一个装机1×26MW的生态机组组成,多年平均年发电量25.528/29.914亿kW·h(单独/联合)。
人工砂石料加工厂设计说明
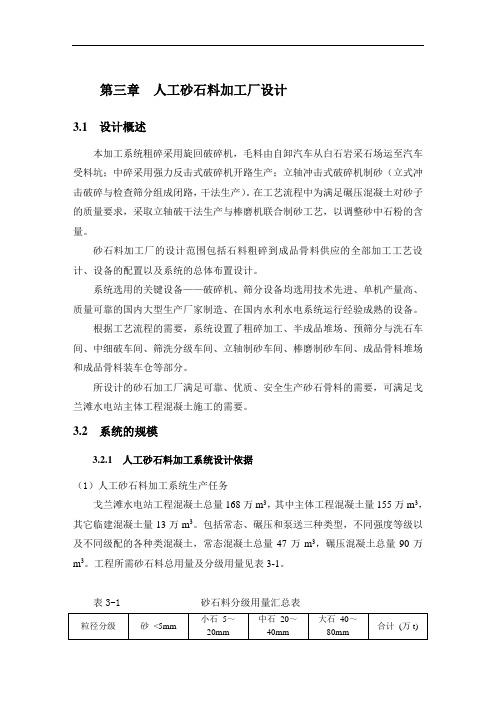
第三章人工砂石料加工厂设计3.1 设计概述本加工系统粗碎采用旋回破碎机,毛料由自卸汽车从白石岩采石场运至汽车受料坑;中碎采用强力反击式破碎机开路生产;立轴冲击式破碎机制砂(立式冲击破碎与检查筛分组成闭路,干法生产)。
在工艺流程中为满足碾压混凝土对砂子的质量要求,采取立轴破干法生产与棒磨机联合制砂工艺,以调整砂中石粉的含量。
砂石料加工厂的设计范围包括石料粗碎到成品骨料供应的全部加工工艺设计、设备的配置以及系统的总体布置设计。
系统选用的关键设备——破碎机、筛分设备均选用技术先进、单机产量高、质量可靠的国内大型生产厂家制造、在国内水利水电系统运行经验成熟的设备。
根据工艺流程的需要,系统设置了粗碎加工、半成品堆场、预筛分与洗石车间、中细破车间、筛洗分级车间、立轴制砂车间、棒磨制砂车间、成品骨料堆场和成品骨料装车仓等部分。
所设计的砂石加工厂满足可靠、优质、安全生产砂石骨料的需要,可满足戈兰滩水电站主体工程混凝土施工的需要。
3.2 系统的规模3.2.1 人工砂石料加工系统设计依据(1)人工砂石料加工系统生产任务戈兰滩水电站工程混凝土总量168万m3,其中主体工程混凝土量155万m3,其它临建混凝土量13万m3。
包括常态、碾压和泵送三种类型,不同强度等级以及不同级配的各种类混凝土,常态混凝土总量47万m3,碾压混凝土总量90万m3。
工程所需砂石料总用量及分级用量见表3-1。
表3-1 砂石料分级用量汇总表(2)系统生产能力要求根据混凝土浇筑施工高峰月强度8.67万m3/月要求,按混凝土初凝时间最大仓面浇筑能力(碾压混凝土控制),需要混凝土系统小时生产能力为260m3/h。
砂石加工系统总处理能力确定为25.2万t/月,成品料生产能力为700t/h。
3.2.2 毛料处理能力根据招标成品料生产能力的要求,并考虑到整个加工过程中的加工损耗、运输损耗、堆存损耗、石粉流失、不均衡系数等综合因素,结合我单位类似工程运行经验取22%,则毛料处理能力为:700t/h×(1+22%)= 854t/h设计处理能力取900t/h。
混凝土坝施工(砂石骨料生产系统、混凝土生产系统及运输方案、温度控制)+【水利工程施工第十二章】精品PPT

三、起重机数量的确定
• 取决于混凝土最高月浇筑强度和所选起重 机的浇筑能力。
• 1、起重机的浇筑能力计算 • 2、起重机数量的确定(根据混凝土最高
月浇筑强度确定)
第四节 混凝土温度控制和分层分块
• 混凝土大坝浇筑后容易在坝的表面及坝基 础部位产生许多裂缝。造成混凝土坝发生 裂缝的原因有:温度和湿度的变化,混凝 土本身的脆性和不均匀性,分缝分块不恰 当,结构型式不合理、施工质量基础的不 均匀沉陷等。但根本的原因可以归结为: 混凝土的变形和对变形的约束。
• (五)施工缝面处理
• 正常施工缝一般在混凝土收仓后10小时左 右用压力水冲毛,清除混凝土表面的浮浆, 以露出粗砂粒和小石为准。
四、碾压混凝土温度控制
• 温度控制标准
• 由于碾压混凝土胶凝材料用量少,抗裂能力比常 态混凝土差,因此其温差标准比常态混凝土严格。
• 对于外部无常态混凝土或侧面施工期暴露的碾压 混凝土浇筑块,其内外温差控制标准一般在常态 混凝土基础上加严2~3℃。
大坝施工栈桥布置方式
(a)单线栈桥;(b)双线栈桥;(c)主、辅栈桥 1—坝体;2—厂房;3—由辅助浇筑方案完成的部位;4—分两次升高的栈桥; 5—主栈桥;6—辅助择时,一般需考虑下列因素: • (1)枢纽布置情况,特别是坝的高度。 • (2)施工进度、强度及温度控制要求。 • (3)地形、地质条件和水文特点。 • (4)导流方式及分期和防洪渡汛措施。 • (5)拌和楼(站)的布置和生产能力。 • (6)起重机具的性能和施工队伍的技术水平、熟
• 我国在吸收美日施工经验的基础上,既有 沿用两种方法修筑的碾压混凝土坝,也采 用了改进的施工方法。
砂石骨料加工厂规划布置施工方案
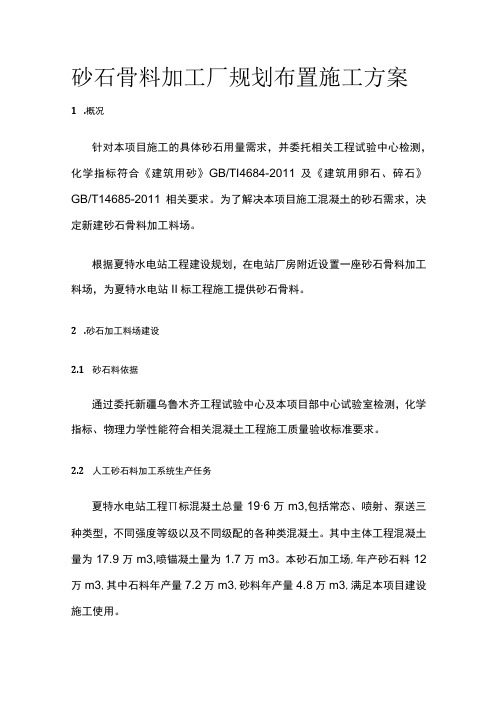
砂石骨料加工厂规划布置施工方案1.概况针对本项目施工的具体砂石用量需求,并委托相关工程试验中心检测,化学指标符合《建筑用砂》GB/TI4684-2011及《建筑用卵石、碎石》GB/T14685-2011相关要求。
为了解决本项目施工混凝土的砂石需求,决定新建砂石骨料加工料场。
根据夏特水电站工程建设规划,在电站厂房附近设置一座砂石骨料加工料场,为夏特水电站II标工程施工提供砂石骨料。
2.砂石加工料场建设2.1砂石料依据通过委托新疆乌鲁木齐工程试验中心及本项目部中心试验室检测,化学指标、物理力学性能符合相关混凝土工程施工质量验收标准要求。
2.2人工砂石料加工系统生产任务夏特水电站工程∏标混凝土总量19∙6万m3,包括常态、喷射、泵送三种类型,不同强度等级以及不同级配的各种类混凝土。
其中主体工程混凝土量为17.9万m3,喷锚凝土量为1.7万m3。
本砂石加工场,年产砂石料12万m3,其中石料年产量7.2万m3,砂料年产量4.8万m3,满足本项目建设施工使用。
本工程所需砂石料总用量及分级用量见表2.2-1o砂石料分级用量汇总表表2.2-1粒径分级砂<5mm小石5~20mm 中石20~40mm合计(万t)用量(万t)13.239.7912.5335.55本工程提供的砂砾料场砾石分级储量统计表天然建材砂石料场概况表表2.2-2材料料料场场类名位型称置出露高程(m)剥离层平均厚(m)有用层平均厚(m)剥离层体积(104m3)夹层体积(104m3)有用层储量(104m3)砂C5-1 夏砾特料河河口右岸1900—19300.3 3.516.8770砾石料场级配表表2.2-3料场名各粒径组含量(%) 总计>150 150-80 80-40 40-20 20~5 <5C5-1 14.3 8.3 12.7 18.9 14.7 31.1 100%2.3系统生产能力要求2.3.1.混凝土施工进度安排混凝土施工进度编制原则(1)混凝土施工细化进度的编制,是以本标施工总进度混凝土施工时间为依据,体现各部位混凝土主要项目施工时段;(2)满足招标文件中控制性工期要求,合理安排施工程序,使混凝土连续进行。
砂石料开采与加工系统组织设计方案

砂石料开采与加工系统组织设计方案砂石加工系统旨在生产本工程砼工程所需的各级粗细骨料,总量约为30.75万m3,骨料需求量约为66.756万t。
该系统的设计处理能力为XXX。
系统位于右岸2#弃渣场,距坝址约2km,由采料场、破碎车间、预筛分车间、筛分车间、调节料仓料仓、成品料仓和胶带输送机等组成。
2.1料场概述莲花台水电站工程提供了4个砂砾料开采料场,根据砂石加工系统布置位置及料场储量,选定右岸2#莲花台料场及左岸3#料场为系统开采料场,其它为备用料场。
2#莲花台料场距坝址平均距离约1km,3#料场位于坝址下游左岸约2.5km处,总储量大于100万m3.采料场需供应砼浇筑总量约80.11万t的毛料。
根据施工进度安排,2007年5月浇筑强度为4.85万m3,2007年10月浇筑强度6.05m3.由于6-9月份为汛期,不浇筑混凝土,砂石系统可备料生产,选月浇筑强度4.85万m3进行开采强度核算,月采运能力为11.97万t。
2.2工程项目布置说明2.2.1道路布置本系统至采料场共设2条主要交通道路,一条为莲花台料场与加工系统间道路,长约1km,一条为3#料场与系统间道路;因3#料场地处加工厂对岸,在2#弃渣场合适位置修筑跨河道路,联系两岸交通。
道路基层均采用泥结碎石路面,厚25~30cm。
采料场均为河滩式料场,料场内部根据开采情况及时修整简易通车道路。
2.2.2电主要为采石场的照明用电,可就近接引。
2.2.3碴场主要为砂砾料场表层局部剥离料的弃渣,弃于监理指定渣场。
2.3主要工程项目施工措施2.3.1采石场开采运输道路施工采石场开采运输道路包括2条砂石加工系统至采石场道路,2#莲花台料场道路利用现有简易道路拓宽形成;3#料场道路因需跨越丹江,采取大块石填筑满足过流,出露水面后采用泥结碎石填筑路面基层满足过车要求。
2.3.2料场开采方法料场的开采为水上平均厚2.5m,水下采用厚度2m,拟采用挖掘机一次性采运。
砂石骨料生产系统施工方案
砂石骨料生产系统施工方案
砂石骨料生产系统施工方案旨在确定合适的施工方法和流程,以确保整个系统
安装和运行的顺利进行。
该方案主要包括以下几个方面:
1. 地基处理
在进行砂石骨料生产系统的施工前,需要对地基进行处理,确保地基的承载能
力和稳定性。
通常情况下,可以通过地基加固、填土、排水等措施来提高地基的承载能力和稳定性。
2. 设备安装
砂石骨料生产系统的设备安装是整个施工过程中最关键的环节之一。
在安装过
程中,要严格按照设备安装说明书和相关标准操作,确保设备的安装位置准确无误,设备之间的连接正确牢固。
3. 输送系统安装
砂石骨料生产系统中的输送系统是系统正常运行的重要组成部分。
在进行输送
系统安装时,需要注意系统的布置、连接和调试,确保输送系统的正常运行。
4. 电气系统安装
砂石骨料生产系统中的电气系统是保障系统正常运行的关键。
在进行电气系统
安装时,要确保电气设备的接线正确、电气系统的接地可靠,并进行必要的电气系统调试。
5. 系统调试与试运行
在完成砂石骨料生产系统的设备安装、输送系统安装和电气系统安装后,需要
对整个系统进行调试和试运行。
通过调试和试运行,可以确保系统的各个部分正常运行,为系统的正式投入使用做好准备。
结语
通过对砂石骨料生产系统施工方案的详细规划和实施,可以确保系统的顺利安
装和运行,提高系统的生产效率和稳定性,为工程的顺利进行提供保障。
制砂工程施工方案范本
制砂工程施工方案范本一、项目概况为了满足城市建设和基础设施建设的需求,我们公司计划进行一项制砂工程项目。
该项目将利用现代化设备和技术,从天然矿石中制取合格砂石,以满足市场的需求。
本方案是根据项目的具体要求和条件而制定的,以确保项目的顺利进行。
二、工程概况1. 项目名称:制砂工程项目2. 项目地点:中国某省某市3. 项目规模:预计日产砂石约1000吨4. 项目周期:预计施工周期为12个月5. 施工内容:主要包括破碎设备、筛分设备、输送设备等的安装和调试,以及生产线的调试和生产三、施工单位1. 施工单位:我公司2. 施工负责人:XXX3. 施工人员:根据项目进度和任务量,将招募合格的工程技术人员和操作人员四、施工方案1. 设备安装本项目主要涉及破碎设备、筛分设备以及输送设备的安装工作。
我们将依据生产线的工艺流程,在项目施工现场进行设备的安装和调试工作。
在设备安装的过程中,我们将严格按照设备制造商提供的安装指南进行操作,确保设备能够安装到位并且符合安全规定。
2. 设备调试安装完成后,我们将对整个生产线进行全面的调试工作。
通过合理的运行参数设置、设备的试运行以及故障排除,最终确保生产线能够正常、稳定的生产出合格的砂石产品。
同时,我们也将对设备的运行情况进行实时监测,对设备的故障进行及时处理,以保证生产线的正常运行。
3. 生产试运行在设备调试完成后,我们将进行生产线的试运行。
根据生产线的工艺流程,我们将进行小范围的生产试验,对生产线进行全面的检查和调整,以确保生产线的生产能力、产品质量和安全稳定。
4. 正式生产经过生产试运行后,我们将正式进行生产。
在生产过程中,我们将严格按照相关的质量管理体系进行操作,确保生产出合格的砂石产品。
同时,我们也将对生产线的运行情况进行全面的监测和管理,对生产过程中出现的问题进行及时处理,以确保生产线的正常、稳定运行。
五、特殊工程1. 环保措施在项目施工过程中,我们将严格遵守相关的环保法规和标准,采取有效的措施加强对施工现场的环境保护。
砂石破碎工程施工方案
砂石破碎工程施工方案一、工程概述本项目为砂石破碎工程,主要任务是将开采的砂石原料进行破碎,加工成符合规定规格的砂石骨料。
砂石骨料是建筑行业的重要原材料,广泛应用于混凝土、砂浆等建筑材料的生产。
本工程破碎后的砂石骨料要求满足GB/T 14685-2011中II类砂石骨料标准。
二、施工内容及施工方法1. 施工内容:(1)破碎设备安装:包括破碎机、振动筛、输送带等设备的安装。
(2)原料供应系统:包括原料开采、输送、储存等环节。
(3)成品储运系统:包括成品砂石骨料的储存、运输等环节。
(4)电气控制系统:包括破碎设备的电气控制柜、传感器等设备的安装与调试。
2. 施工方法:(1)破碎设备安装:根据设备安装图纸,进行设备基础施工,然后将设备吊装至基础上,进行水平调整和固定。
破碎机安装后,进行振动筛、输送带等设备的安装,与破碎机连接,形成完整的破碎生产线。
(2)原料供应系统:采用开采设备进行原料开采,通过输送带将原料送入破碎机进行破碎。
开采过程中,要注意保持矿山生态平衡,减少对环境的影响。
(3)成品储运系统:成品砂石骨料通过输送带送入储料仓,然后通过运输车辆将成品砂石骨料运出施工现场。
(4)电气控制系统:根据电气施工图纸,进行控制柜的安装,连接传感器和破碎设备,进行调试,确保设备正常运行。
三、施工组织设计1. 施工人员:本工程所需施工人员包括项目经理、施工队长、技术员、工人等,共计约50人。
2. 施工队伍组织结构:项目经理负责整个工程的管理,施工队长负责现场施工,技术员负责技术指导,工人负责具体施工。
3. 施工进度计划:本工程预计施工周期为6个月,具体施工进度根据实际情况进行调整。
四、质量保证措施1. 严格把控原料质量,确保原料符合要求。
2. 设备安装过程中,严格按照安装图纸进行,确保设备安装正确。
3. 破碎过程中,定期检查破碎机磨损情况,及时更换磨损配件,确保破碎效果。
4. 成品砂石骨料进行严格检测,确保满足GB/T 14685-2011中II类砂石骨料标准。
砂石骨料生产施工方案
砂石骨料生产施工方案一、前言砂石骨料在建筑施工中扮演着重要的角色,是混凝土、沥青等建筑材料的基础,因此其生产施工方案对工程质量具有重要影响。
本文将就砂石骨料生产施工方案进行详细探讨,旨在提高工程施工质量,确保工程可持续发展。
二、原材料准备1. 砂石选择选择质地均匀、含泥少、粒度分布合理的石料和细砂作为原料,确保产品符合建筑要求。
2. 原材料储存砂石原料应储存在干燥通风的库房中,避免受潮和污染,保证原材料质量。
三、生产工艺1. 破碎将原材料进行破碎,控制破碎机的出料粒度,根据不同需求进行合理配置。
2. 造粒通过制砂机对破碎后的原材料进行造粒处理,调控成品颗粒的形状和大小。
3. 筛分利用筛分设备对造粒后的产品进行筛分,去除杂质和过粗、过细颗粒,确保成品质量。
4. 洗涤对砂石骨料进行洗涤处理,去除表面泥土和其他杂质,提高成品的洁净度。
5. 混合根据需求将不同粒度、质地的砂石骨料按比例混合,确保产品符合设计要求。
四、质量控制1. 检测在生产过程中,需要定期对砂石骨料的物理指标进行检测,如含泥量、砂含量、粒度分布等,确保产品质量稳定。
2. 质量追踪建立砂石骨料生产档案,记录每批次原材料的来源、生产工艺参数、检测结果等信息,实现质量追踪和问题追溯。
五、安全生产1. 设备维护定期检查和维护生产设备,确保设备正常运行,避免因设备故障导致生产事故。
2. 生产作业对生产作业人员进行岗前培训,提高操作技能和安全意识,严格执行安全操作规程,确保生产过程安全。
六、总结与展望砂石骨料生产施工方案的合理设计和严格执行对于保障工程质量具有重要意义。
本文对砂石骨料生产的原材料准备、生产工艺、质量控制和安全生产等方面进行了详细阐述,希望可以为相关行业提供参考和借鉴。
未来,我们将继续深入研究,不断完善砂石骨料生产施工方案,推动行业发展,为社会建设贡献力量。
- 1、下载文档前请自行甄别文档内容的完整性,平台不提供额外的编辑、内容补充、找答案等附加服务。
- 2、"仅部分预览"的文档,不可在线预览部分如存在完整性等问题,可反馈申请退款(可完整预览的文档不适用该条件!)。
- 3、如文档侵犯您的权益,请联系客服反馈,我们会尽快为您处理(人工客服工作时间:9:00-18:30)。
砂石骨料生产系统设计说明1.1 工程概述砂石骨料生产骨料系统位于挡水坝下游一平台上,紧临混凝土拌和系统进行布置,总占地面积约6000m2 。
砂石骨料生产系统主要承担供应主体工程混凝土总量约11.1 万m3 的生产任务,主要生产大石(40~80mm)、中石(20~40mm)、小石(5~20mm)、以及砂(<5mm), 其中粗骨料约16.5 万t ,细骨料约8.4 万t 。
砂石骨料系统布置详见附图1《砂石骨料生产系统平面布置图》1.2 料源简介本标段砂石骨料料场为黑串沟人工骨料场,位于大坝左岸耳朵岩沟支沟黑串沟右岸山脊,距坝址约1.6km ,距离砂石骨料系统约 1.1km,有公路相通,运输较为方便。
本标段总开采量为16.88 万m3 。
1.3 系统工艺流程设计1.3.1 系统设计规模本工程砂石系统以承担主体工程全部混凝土总量约11.1 万m3 所需砂石骨料的加工,系统生产能力应满足本标实际高峰月浇筑强度16500m3 / 月骨料供应,但根据招标文件要求,砂石系统生产能力满足混凝土浇筑高峰强度 2.0 万m3 / 月。
按招标文件要求进行系统设计,骨料最大粒径为80mm,最小粒径为0.15mm。
根据初步计算,成品骨料综合级配见表1。
表 1 成品骨料综合级配表⑴ 成品砂石料月需要量高峰月成品砂石料需要量:Qc=20000m3 × 2.2t/m 3 =44000t/ 月( 注:系数2.2 为每m3 混凝土中的砂石料用量)⑵ 高峰月毛料处理能力按照成品砂石料的生产要求,考虑到整个加工过程中的加工损耗、运输损耗、堆存损耗、洗石损耗、细砂石粉流失等综合因素,高峰月毛料处理能力为:Qmd=Qcη/ =4.4 ×104t/0.85=51765t / 月成品率η ={k3k4k5k6[1+v(k 1k2-1)]}-1={1.03 ×1.02 ×1.02[1+0.35(1.25 ×1.02-1)]}-1=0.85⑶ 系统设计毛料小时处理量及成品砂石料小时生产能力高峰强度月,每月工作25 天,每天工作8 小时,并考虑生产不均匀系数K=1.1,系统设计小时毛料处理量为:Q h=Q md× K/MN=51765×1.1/(25 ×8)=285t/h成品小时生产能力为:Q=Q c× K/MN=44000× 1.1/ ( 25× 8) =242t/h进过以上计算,本系统生产规模毛料小时处理量按300t/h ,成品砂石料小时生产能力为250t/h 进行设计,完全能满足高峰期月浇筑强度20000m3 的骨料供应需求。
1.3.2 工艺流程设计砂石料加工系统设计产出成品分别为大石( 80~40mm)、中石(40 ~20mm)、小石(20 ~5mm)、砂(<5mm)4 种料,设计主要采用粗碎、中碎和细碎的三段破碎及两段筛分来完成整个生产过程。
根据破碎筛分的流程,确定生产工艺流程,工艺流程图详见附图2《砂石骨料生产系统工艺流程图》。
1.3.3 加工流程设备选型1.3.3.1 选型原则(1) 生产能力满足招标文件要求, 并且要求有一定裕度;(2) 各粒径砂石料的产量能根据需要即时调整;(3) 成品砂石料储量满足混凝土高峰期浇筑5 天用量;(4) 工艺性能可靠,节约占地,建设周期短。
3.3.3.2 设备选型粗碎(第一段破碎) :粗碎原料为黑串沟人工骨料料场的开采石料,要求石料粒径控制在600mm以下。
根据生产骨料能力,选用 1 台JC1100 型颚式破碎机作为粗碎设备,破碎机的开口控制在80~140mm之间,此时,破碎机产出粒径<150mm,其产量即能达到300t/h 。
半成品堆料区:为保证成品骨料不间断供应,项目部计划设置地弄廊道半成品堆料区,毛料经粗碎后经胶带机运至半成品料堆,半成品经过GZG90-3振动给料机下料,经地弄廊道皮带机运输至筛分楼,根据给料强度,当选用2台GZG90-3振动给料机。
中碎(第二段破碎):经过筛分进入中碎破碎机的平均流量为177.35t/h ,当选用1 台GP11型反击式破碎机,破碎机的生产能力是170~190t/h ,完全满足生产需要。
细碎制砂(第三段破碎):经过筛分流程计算,进入制砂机平均流量为57.78t/h ,当选用1 台VSI5X9532 型立轴式冲击破碎机制砂,此时,洗去石粉后系统的产砂总量是94.67t/h 。
筛分楼:筛分系统分初筛和复筛,初筛:根据筛分流程计算,通过初筛的流量是300t/h ,当设置2 台2YA2460 圆振动筛分机,每台筛分机共 4 层筛网(80mm、40mm、20mm、5mm),初筛后共进入成品料堆为119.65t/h 。
复筛:设置 1 台筛分机共 2 层筛网(20mm、5mm),经过筛分流程计算,通过复筛分的流量是49.92t/h 。
选用 1 台2YKR2148圆振动筛分机,在筛分机内加水冲洗。
通过骨料加工系统级配平衡计算,经过以上设备配置,实际成品砂石骨料生产能力为280t/h ,完全满足高峰期混凝土浇筑需求。
砂石骨料加工系统主要设备及胶带机主要参数见表2,表3表 2 砂石骨料加工系统主要设备表表 3 胶带机主要参数性能表1.4 系统平面布置设计1.4.1 系统组成骨料加工系统由上料平台、粗碎车间、半成品料堆、初筛分车间、中碎车间、复筛分车间、细碎制砂车间及调节料仓以及成品料仓、供电系统、供排水系统及相应的辅助设施等组成,各车间之间用胶带机连接。
具体布置见附图1《砂石骨料加工系统平面布置图》。
⑴ 毛料上料平台毛料上料平台布置在靠近路边侧,便于毛料直接运至上料平台卸料。
上料平台用浆砌石及干砌石砌筑,砌筑高程为EL.994.0 ,上料平台坡度控制在8%~15%。
⑵ 粗碎车间粗碎车间紧邻上料平台布置,毛料经GZT1230棒条给料机送入粗碎车间中。
粗碎车间地面高程为EL.988m,为钢筋混凝土加金属结构的复合型结构,布置一台JC1100型鄂式破碎机,破碎料经J1 胶带机运输至半成品料堆。
⑶⑷筛分车间筛分车间靠近半成品料堆布置,地面高程为EL.988m,为钢筋混凝土加金属结构的复合型结构,布置2 台2YA2460圆振动筛,设80mm、40mm、20mm、5mm四层筛网。
80~150mm的骨料经J5、J7 胶带机运输至中碎车间加工;40~80mm的骨料一部分经J6 、J12 胶带机运输至进入成品料仓,一部分经J5、J6 胶带机运输至中碎车间加工。
20~40mm的骨料一部分经J8、J13 胶带机运输至进入成品料仓,5~20mm的骨料一部分经J9、J14 胶带机运输至进入成品料仓,小于5mm的骨料一部分经J15 胶带机运输至进入成品料仓。
复筛分车间布置在初筛分车间的附近,地面高程EL.988.00m ,为钢筋混凝土加金属结构的复合型结构,布置 1 台2YKR2148圆振动筛,设20mm、15mm、5mm 三层筛网。
大于20mm的骨料一部分经11#胶带机运输至进入成品料仓,一部分经8#、9#胶带机运输至细碎制砂调节料仓等待加工;15 ~20mm的骨料一部分经8#、9#胶带机运输至细碎制砂调节料仓等待加工,一部分经12#胶带机运输至成品料仓,5~15mm骨料一部分经8#、9#胶带机运输至细碎制砂调节料仓等待加工,一部分经12#、13#胶带机运输至成品料仓;小于5mm的骨料经过洗砂机后,由14#、15#胶带机运输至成品料仓。
筛分车间结构图详见附图3《筛分楼基础及钢筋图》⑸ 中碎车间中碎车间及调节料仓布置在半成品料堆与初筛分车间附近,为钢筋混凝土结构。
采用1 台GP11立轴式破碎机,加工来自初筛分过来的部分80~150mm骨料,破碎后经J3、J4 胶带机运输至筛分车间。
中碎结构详见附图4《GP11圆锥破碎机基础结构图》细碎制砂车间细碎制砂车间及调节料仓地面高程为EL.988m。
制砂车间为钢筋混凝土结构。
采用1 台VSI5X9532 立轴式破碎机,细碎后的40~20mm骨料经J8、J13 胶带机运输至成品料仓,20~5mm的骨料经J9、J14 胶带机运输至成品料仓。
细碎结构详见附图 5 《立轴破碎机基础结构图》。
⑹半成品料堆半成品料堆布置在粗碎车间附近,地弄廊道顶部及料堆地面高程为EL.988m,地弄廊道布置2 台GZG90-3 型振动给料机,经2#、3#胶带机运输至初筛分车间。
半成品料堆结构图详见附图6《半成品料堆结构图》⑺成品料仓分为成品骨料仓和成品砂仓紧邻混凝土拌和系统布置,料仓成弧形字型布置,地面高程为EL.988m,成品料仓形成 1.5%的排水坡坡度,骨料仓之间设置 5.0m高的砌石隔墙,骨料堆高9m。
成品料仓的堆存容积按7天用量考虑,其中80mm~40mm骨料仓容800t ,40mm~20mm骨料仓容1000t ,20mm~5mm骨料仓容1200t ,成品砂仓容量分为二个仓,一个为存料(脱水)仓区,另一个为供料仓区。
成品砂仓总仓容为1500t 。
1.4.2 供排水系统1.4.2.1 供水系统供水系统主要指供应骨料生产过程中的砂石骨料冲洗用水,系统最高设计用水量为300m3 /h 。
筛分车间用水筛面喷淋用水和卫生冲洗用水,筛面喷淋用水除完成对筛面骨料的冲洗外,也附带有除尘的功能。
用水量为220m3 /h 。
粗、细碎、制砂车间用水主要由破碎机除尘用,用水量分别为20m3 /h 。
系统零星用水主要是公共项目用水,如消防用水,道路养护用水及事故抢修用水等(系统室外管路的泄露消耗也计入本部分),其用水量为20m3 /h 。
在1# 泵站设置 2 台IS125-100-315B 离心泵抽水,通过DN500 主水管输送至砂石骨料加工系统直供。
以DN500mm作为主供水管(长600m),进入砂石系统内。
用DN50mm钢管分别引至粗碎、细碎、制砂车间和其它零星部位,用DN250钢管引至筛分车间。
根据系统的布置特点,把系统分为 3 个消防区:粗碎车间消防区、中碎车间和筛分车间消防区、细碎制砂车间消防区。
各生产车间全部配备干粉灭火器。
消防主管直接从经过该小区的供水管上分支安装。
表 4 供水系统主要设备、材料和工程量表砂石骨料加工系统所产生的污水通过场内排水沟和排水管道汇集后进入砂石骨料加工系统沉砂池。
场内采用M7.5 浆砌石排水沟,净断面为800mm× 800mm。
沉砂池占地面积为50m2 ,深2m。
在砂石骨料加工系统配置一台PC300反铲定时进行沉砂池的清理工作,避免细砂的淤积。
将沉砂池的出口高程设置在距地面深0.5m 的位置,将沉砂池面层的清静水排到水循环利用单位。
1.5 生产系统环境文明施工1.5.1 防尘设计砂石骨料加工系统在生产过程中产生大量的粉尘,必须采用综合防尘措施,以保证作业地点的空气中含尘浓度符合国家卫生标准和三废排放标准的要求。