超硬刀具加工淬火件实现以车代磨工艺
以车代磨工艺在加工同一外圆不同硬度产品中的应用

I 刀 具
工艺 以车代磨 在加工同一外圆 产 品 不 同硬度 中的应用
南 阳市 红 阳锻 造 有 限公 司 ( 河南 4 7 3 0 0 0 ) 王 玲 张永强 张喜平 秦淑萍 许 静
我 们公 司是 加 _ 丁工 程 汽 车支 承 轴 的专 业 生 产 厂
0 . 1 2 O . O 8 3 0 0 6 0 0 O . 1 O 0 . 1 2 O . 0 8
1 0 . 5 ai r n / 件 9 . 8 mi n / 件
9 . 1 mi n / 件 1 0 . 3 ai r n / 件 9 . 6 m i n / 件 9 m i n / 件 9 . 7 a r i n / 件
片是无 修光 刃刀 片 的两 倍 ,因此 决 定 采 用 带 有 修 光
刃_ 乃片 。
( 2 ) 切削参 数 的选 择 选 定 此 刀 片 后 ,我 们 针 对 淬火 部位 刀具 磨损 快 这 一 问题 ,决 定采 用 低转 速 ,
以降低 刀 片磨 损 ,延 长 刀 片使 用 寿命 。产 品 在 半 精 加 工外 圆时余 量 为 0 . 6— 0 . 7 m m,单 边 余 量 为 0 . 3~ 0 . 3 5 a r m,下 面是 对切 削参 数 所 做 的试 验 ( 精 车 外 圆 时淬火 部位 精车 分二 次走 刀 ,背 吃刀量 分别 为 0 . 2~
尺寸 有差 异 和 刀 具 不 耐 用 等 问题 ,现 已 在 同 行 的 指 点及 公 司技 术 攻关 小组 的努 力 下 基 本 解 决 了上 述 问
题 ,在此将 解 决 方 案 总 结 如下 ,以便 于 有类 似 产 品
在尺 寸控制 上有 难度 ,不容 易保 证产 品 图尺寸要 求 。
硬车削方案学习.pptx

刀具材质
切削速度
刀具寿命
效率
华菱 BN-H10
145m/min
3件/刃
提高20%
某品牌CBN
120m/min
2件/刃
----
加工难点:1.风电轴承常用材质50Mn,42CrMo,淬火后硬度为HRC50以上,工件表面存在断续切削;2.一般淬火后硬车余量较大,约为2~6mm
华菱BN-H10效率提高20%寿命提高50%
什么是硬车削?
通常所说的硬车削是指把淬硬钢的车削作为最终加工或精加工的工艺方法。淬硬钢通常指淬火后具有马氏体组织,硬度高,强度也高,几乎没有塑性的工件材料。 当淬硬钢的硬度>55HRC时,其强度sb约为2100~2600N/mm2。通常,工件在热处理淬硬之前就已完成粗加工工序,只有精加工在淬硬状态下进行。
加工工况:强断续切削端面 加工材料:20CrMnTi齿轮,HRC58-62 选用刀片:BN-H21 WNGA080404 切削参数:ap=0.15mm,Fr=0.1mm/r,Vc=117m/min,干切
刀具材质
刀具寿命
最终失效形式
华菱 BN-H21
600件
正常磨损
某品牌PCBN
100件
破损碎裂
华菱BN-H21寿命提高了5倍,强断续加工时不崩损、不碎裂
高速钢本身作为刀具材料,热处理后硬度动辄HRC65甚至更高;那么用什么刀具才能加工高硬度高速钢呢
高速钢的加工特点
第25页/共40页
加工难点:(1)硬度高,(2)加工余量大(3)切槽切削阻力大(4)部分有断续切削冲击,刀片易崩刃。
加工材料:高速钢 工件硬度:HSD90选用刀片:BN-S20 RCMX120700切削参数:Fr=0.20mm/r,Vc=35m/min,干切
PCBN刀具以车代磨新工艺实践

c N 的热 传导 率 为 10 W/ K,热导 B 30 m・ 性虽然赶不上金刚石 ,但是在各类 刀具材料 中 P B 的热导性仅次于金 刚石 ,大大高于高速 C N 钢和硬质合金 。C N 的导热系数是纯铜的 32 B . 倍 ,是硬质合金的 2 倍 ,与陶瓷的导热系数的 0 比率为 3 . ,热扩散率 比值为 6 . ,而且随着 71 55
而 可 以免 除退 火 ,并 能 简 化 工 艺 ,大 幅度 地 节
省 工 时和 能耗 。
磨工艺 。
电劫 工其 2l5 o ( o)
1 )在 滚齿 工序 使 用切 圆顶 滚 刀 ,保 证齿 顶
3 基于2 CM T 0r n i 材料齿 轮渗碳 淬火后 以车 代磨新工艺实践
传 统 的 小 模 数 齿 轮 加 工 工 艺 , 基 于
2 C Mn 材料 的齿 轮淬 火层 硬 度 可达 到 5 0 r Ti 8~
圆与分 度 圆的 同心度。齿坯加工时齿顶 圆留量 约 0 1mm ( .5 单边) ,保证顶切 。 2 )将最终磨 内孔工序改为 以车代磨 。设备 选择 C 6 4 普通车床 。没有选择数控车床 或 A 10 者车削 中心 ,主要原 因是考虑此类零件 的批量
关键词 立方氮化硼 (E ) 刀具 以车代磨 C3 N 1 引言
立方氮化硼 ( B C N)是 自然界不存在的物 质 ,有单 晶体 和多 晶体之分 。C N 是氮化 硼 B
( BN)的 同素 异 构体 之一 ,结 构与 金 刚石 相似 ,
在 9 0 以下无任何变化 ,且 稳定。与铁 系材 0" C
金 刚 石 的 耐 热 性 (0 7 0~ 8 0 0 ℃) 几 乎 高 l 。 倍
CBN刀具车削加工淬火钢件的切削参数范围

CBN刀具车削加工淬火钢件的切削参数范围CBN刀具车削加工淬火钢件,已经是非常普遍的一种现象,采用CBN刀具以车代磨加工淬火钢件效率成倍提高,而且干式切削,车削加工过程中不添加切削,绿色环保,更适合制造业的绿色制造。
CBN刀具虽然广泛应用于淬火钢件的车削加工,但很多工人还不太了解CBN刀具的切削参数,经常刚上去就出现崩刀、打刀现象。
主要就是不了解CBN刀具的切削参数,用硬质合金刀具的参数测试,效果不好。
小编在机械加工行业摸爬滚打了十几年,还算是有一点小心得,今天分享给大家。
在先介绍CBN刀具车削加工淬火钢件的切削参数范围之前,先来了解一下淬火钢都有哪些难加工问题。
1、淬火钢件的粗加工:车削加工淬火过的齿轮,齿圈的生产过程中,一些齿轮、齿圈淬火或渗碳淬火后,硬度一般在HRC55以上,而且变形严重,如高铁齿轮,工程机械大齿圈,重工行业用大齿圈等,这些大型齿轮齿圈淬火后变形量非常大,这就涉及到淬火钢粗加工。
同样,在模具钢生产过程中,淬火钢的粗加工也经常看到,但很多厂家采取的措施也五花八门,有的先把大余量线切割掉,有的用硬质合金刀具慢慢啃,有的用立方氮化硼(PCBN)刀具多次走刀才能完成加工,工人感慨粗加工淬火钢是有劲使不出,干着急,没办法。
2、淬火钢件的断续加工:间断切削加工一直是个难题,何况是动辄HRC60左右的淬火钢。
特别是在高速车削淬火钢时,刀具在间断车削淬火钢时会以每分钟100次以上的冲击来完成加工,对刀具的抗冲击性能是个很大的挑战。
以汽车齿轮加工为例,淬硬齿轮以车代磨已经成为一种趋势,据了解,作为齿轮产业的三大市场之一,车辆齿轮占据了齿轮市场总额的62%,其中汽车齿轮又占据了车辆齿轮市场份额的62%。
也就是说,汽车所用齿轮占有了整个齿轮市场近40%的比重,可见齿轮对于汽车产业的重要性。
虽然淬火钢的以车代磨和硬车削已经很普及,其实汽车淬硬齿轮加工过程中仍然遇到很多问题,如一些汽车齿轮内孔有油孔,这就出现间断切削加工难题,很多CBN刀具在高速运转时期遇到油孔容易崩刀,齿轮的位置公差难以保证,等等3、淬火钢件的切槽加工:举一个简单的例子,同步器滑套啮合槽淬火后的硬车削加工,虽然立方氮化硼刀具厂家开发出了同步器滑套专用立方氮化硼切槽刀具,但PCBN刀具的寿命仍然不尽如人意。
用CBN刀片以车代磨的光洁度

用CBN刀片以车代磨的光洁度淬硬工具钢、轴承钢、渗碳钢以及耐热合金、镍基合金、钨铬钴合金等材料的加工中,以车代磨的得到广泛应用,超硬刀具作为以车代磨工艺的刀具材料,在此不再赘述;本文根据以车代磨齿轮和齿轮轴的表面光洁度实验,从刀具角度浅谈影响以车代磨的光洁度几种因素。
1,若能采用刚性好的标准数控车床加工,刀具的刚性好和刃口锋利,则以车代磨的光洁度可达Ra0.3μm,尺寸精度可达0.01mm,可达到用数控磨床加工的水平。
2,以车代磨时的数控刀杆选择;较低端数控车刀刀杆,一般采用材料是45钢调质到HB210-240,而在以车代磨工艺中,采用的刀柄硬度应提高1.5倍,一般刀柄材料采用42CrMo 材料为佳,热处理硬度HRC45左右可获得较好的刚性。
这样可以能把让刀震刀风险降到最低,来获得较好的加工表面光洁度和精度。
3,以车代磨加工中,刀杆前端的伸出长度尽可能短(不得大于刀杆高度的1.5倍),可最大限度避免震刀问题。
以车代磨出现振刀纹一般是系统刚性不好的原因,而刀杆,刀片角度以及工件的装卡方式、机床主轴可卡盘精度都影响以车代磨的表面光洁度4,工件的长径比:以车代磨时,工件长径最好比不大于4:1,当工件的长径比大于4:1时,一半多采用跟刀架,超过8:1时采用跟刀架的同时采用反向车削;这样方能适当避免振刀。
5,刀片材质:CBN刀片是最适合作为以车代磨的刀具材料,华菱超硬BN-H20牌号CBN刀片以车代磨加工齿轮轴时,除了在直径方向的公差略孙于精密磨削外,光洁度和公差级别在同类刀具中均是首屈一指的。
由于BN-H20采用的是非金属基结合剂,其热导率更高,耐磨性和寿命更长,而在以车代磨加工中,判定刀片的实效形式一般为加工表面粗糙度的下降。
BN-H20由于采用超细晶粒CBN,刀片在高温切削加工中,使得刃口的微观沟槽磨损降到了最低。
6,冷却液的使用:以车代磨使用BN-H20牌号CBN刀片,是可以加冷却液,而且能够获得更好的刀具寿命。
替代磨削的经济性好的硬车刀具和技术

替代磨削的经济性好的硬车刀具和技术用在汽车工业的大多数硬零件是在淬硬后加工到最后几何形状的。
目前,磨削是用于这些零件的重要的方法,这些零件包括轴承、齿轮、轴和小齿轮。
但是,感谢机床刚性的改善和聚晶立方氮化硼(PCBN)刀具的进展,硬车削正作为一种替代磨削的经济性好的方法在普及。
使用各种镶刃或整体车刀片完成硬度在洛氏45到68范围材料的硬车削。
自从它在80时代中期推出以来,这种工艺的普及程度已戏剧性地加添,并且PCBN刀具的销售现在每年超过25亿美圆。
很明显,越来越多的制造商正在认得硬车削的优点。
但是归因于PCBN刀具的成本,很多人依旧把它看作是一个昂贵的工艺。
用PCBN进行硬车削真的更贵?当PCBN刀具的成本比传统刀具高10到20倍时,讨论表明它们在综合生产率和刀具寿命方面效率要高10到300倍。
在某种程度上,这些发觉是基于每个零件分摊的刀具成本分析。
为了更好地了解硬车削的经济效益,考虑一些有时被会计部门忽视的因素是有帮忙的。
这些因素包括刀具换刀时间、调整时间、加工时间、机床维护、零件质量和机床原始成本。
硬车削的经济性好可能归功于机床本身。
磨床比CNC车床的投资大得多,CNC车床通常是磨床成本的三分之一到二分之一。
还有,在加工本领方面CNC车床柔性更大。
换刀能在两分钟之内完成,没有对于更换砂轮必需的生产时间的损失。
这些柔性允许小批量零件的快速、经济性好的生产。
低的维护也是一个好处,作为磨损的PCBN刀具能被快速地拿走并更换新的刀片,而且不需要修正或修正来维持切削轮廓。
CNC车床和磨床相比还占据更少的空间,不需要液槽系统,而且在很多硬车削应用里甚至不需要冷却液。
由于硬车削通过从工件上剥软化的切屑来有效地去除金属,通常不推举冷却液。
这有助于在除去有使用冷却液引起的环境损害的同时降低成本。
干加工还削减花在政府管制的切屑处理和回收处理上的时间和金钱。
在较少的加工时间下获得良好的表面干净度虽然已经知道磨削在相对较高的进给率下得到良好的表面干净度,但用PCBN刀片硬车削能以明显更高的金属切除率获得同等或更好的表面干净度。
使用立方氮化硼刀具以车代磨的切削参数与风险
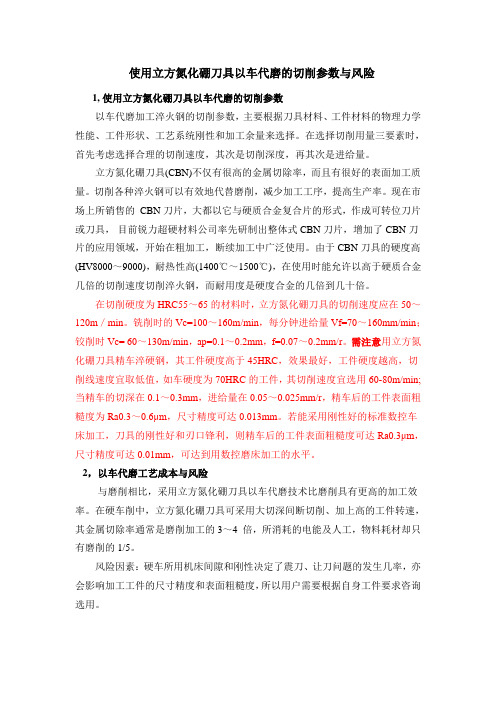
使用立方氮化硼刀具以车代磨的切削参数与风险1, 使用立方氮化硼刀具以车代磨的切削参数以车代磨加工淬火钢的切削参数,主要根据刀具材料、工件材料的物理力学性能、工件形状、工艺系统刚性和加工余量来选择。
在选择切削用量三要素时,首先考虑选择合理的切削速度,其次是切削深度,再其次是进给量。
立方氮化硼刀具(CBN)不仅有很高的金属切除率,而且有很好的表面加工质量。
切削各种淬火钢可以有效地代替磨削,减少加工工序,提高生产率。
现在市场上所销售的CBN刀片,大都以它与硬质合金复合片的形式,作成可转位刀片或刀具,目前锐力超硬材料公司率先研制出整体式CBN刀片,增加了CBN刀片的应用领域,开始在粗加工,断续加工中广泛使用。
由于CBN刀具的硬度高(HV8000~9000),耐热性高(1400℃~1500℃),在使用时能允许以高于硬质合金几倍的切削速度切削淬火钢,而耐用度是硬度合金的几倍到几十倍。
在切削硬度为HRC55~65的材料时,立方氮化硼刀具的切削速度应在50~120m/min。
铣削时的Vc=100~160m/min,每分钟进给量Vf=70~160mm/min;铰削时Vc= 60~130m/min,ap=0.1~0.2mm,f=0.07~0.2mm/r。
需注意用立方氮化硼刀具精车淬硬钢,其工件硬度高于45HRC,效果最好,工件硬度越高,切削线速度宜取低值,如车硬度为70HRC的工件,其切削速度宜选用60-80m/min;当精车的切深在0.1~0.3mm,进给量在0.05~0.025mm/r,精车后的工件表面粗糙度为Ra0.3~0.6μm,尺寸精度可达0.013mm。
若能采用刚性好的标准数控车床加工,刀具的刚性好和刃口锋利,则精车后的工件表面粗糙度可达Ra0.3μm,尺寸精度可达0.01mm,可达到用数控磨床加工的水平。
2,以车代磨工艺成本与风险与磨削相比,采用立方氮化硼刀具以车代磨技术比磨削具有更高的加工效率。
在硬车削中,立方氮化硼刀具可采用大切深间断切削、加上高的工件转速,其金属切除率通常是磨削加工的3~4 倍,所消耗的电能及人工,物料耗材却只有磨削的1/5。
SKD11淬火后车削加工刀片
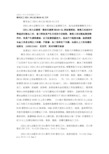
SKD11淬火后车削加工刀片精车加工SKD11淬火后HRC58-62刀片精车加工SKD11淬火后HRC58-62刀片SKD11淬火后精车刀片(精车加工高硬度刀片,高光洁度耐磨精车刀片)SKD11淬火后硬度一般洛氏硬度HRC58-62,表面硬度高,陶瓷刀具相对中等速度切削加工时,前刀面容易产生贝壳形片状剥落,陶瓷刀具切削高硬度钢件时,容易产生磨粒磨损,后刀面磨损量较大。
造成尺寸超差问题。
涂层硬质合金刀具易出现让刀问题,不耐磨、加工效率低下问题。
如遇以上刀具问题欢迎致电156******** 吴百利郑州华菱市场部高速加工SKD11淬火后的刀片【车削刀片、铣削刀片等数控刀片新牌号】精车SKD11淬火后的刀片(含车削刀片、铣削刀片等数控刀片)---华菱超硬刀具公司研制的刀片材质BN-H10,BN-H20,BN-S20牌号数控刀片(机夹刀片)广泛应用于RC45-HRC79之间SKD11淬火后和超级合金材料中,解决了传统硬质合金刀头加工SKD11淬火后件或超级合金时效率低,频繁更换刀片加工精度差形位公差难以保证问题,解决了硬质合金刀片及涂层刀片,陶瓷刀片不耐用,刀具磨损过快要么烧刀、要么崩刀甚至打刀问题。
并在车削,铣削,镗削,切槽加工HRC45-HRC68之间高硬度淬火件,如9SiCr 、T8、T10、H13工具钢淬火件,车削硬度HRC60左右渗碳SKD11淬火后20CrMnTi、20Cr,铸钢浇钢件的冒口车削加工,高速钢、高锰钢、高铬钢、高铬高镍合金的粗加工和高速精加工,模具钢等淬火材料留磨量大采用“以车代磨或以车代粗磨”领域中。
此新材质PCBN超硬合金数控刀片也适合加工热处理后硬度大于HRC50调质钢料加工,40Cr 、4 2CrMo淬硬钢及65HRC以上淬火硬钢,Cr12MoV模具钢淬火料HRC62以上的金加工车削刀片或返修硬面,高速钢轧辊硬度HSD75以上的翻新及车削,HRC62-H RC68硬度淬火后GCr15轴承钢,65Mn材质大型淬火后发兰,轴类,盘类零件的车削外圆端面以及切槽加工刀具,铣削高铬钢钢板,镗削齿轮及齿轮轴的内孔及模具材料,耐磨钢板HB400以上硬化钢,部分氮化钢如心轴(芯轴)在硬度在H RC70以上及硬化钢的以车削、铣削、镗削,切槽代磨削加工刀片。
- 1、下载文档前请自行甄别文档内容的完整性,平台不提供额外的编辑、内容补充、找答案等附加服务。
- 2、"仅部分预览"的文档,不可在线预览部分如存在完整性等问题,可反馈申请退款(可完整预览的文档不适用该条件!)。
- 3、如文档侵犯您的权益,请联系客服反馈,我们会尽快为您处理(人工客服工作时间:9:00-18:30)。
超硬刀具加工淬火件实现以车代磨工艺
随着现代技术的不断发展,越来越多的高硬度淬火件出现在加工现场,刚开始多数选择磨削方式作为最后加工工序,来保证淬火件的尺寸和精度。
但随着刀具行业的不断研究、实践,最终研制出可以车代磨的车刀刀具材料—硬质合金刀具、陶瓷刀具、立方氮化硼刀片。
下面就具体介绍一下以车代磨的工艺及什么情况下可选择以车代磨工艺加工淬火件。
一、以车代磨的含义及工艺
所谓的以车代磨简单来说就是车削代替磨削作为精加工工序或最后加工工序,完成图纸要求尺寸和精度。
刚开始出现淬火件时磨削加工是主流,磨削可以很好的保证淬火件的尺寸,尤其是精度要求体现的更好。
就如轴类淬火件的加工工艺为车加工—热处理—磨削。
但是随着淬火件的批量生产和更多的大型,复杂淬火件的出现,对于磨削来说,效率太低。
大型淬火件热处理后变形量大,余量大,磨削每次只能小余量磨削,而且遇到复杂的淬火件时找不到相对应的磨床磨削。
之后通过刀具行业的不断努力研究、实践,最终研制出了可实现以车代磨的车刀刀具材料。
分别是硬质合金刀具,陶瓷刀具,立方氮化硼刀片。
现在如加工轴类淬火件的加工工艺为粗加工—热处理—精加工。
以上三种刀具最先研制出的是硬质合金刀具,在现代还是机械制造厂的主流车刀刀具。
之后是陶瓷刀具—立方氮化硼刀片。
其中由于淬火件是经过热处
理后的工件,故硬度高,耐磨性好。
选择刀具材料的同时需考虑刀具材料的刀体硬度,耐磨性和抗冲击性。
以上三种刀具按硬度来说:立方氮化硼刀片>陶瓷刀具>硬质合金刀具,从韧性上来说:立方氮化硼刀片>硬质合金刀具>陶瓷刀具。
可见加工淬火件立方氮化硼刀片是最有优势的。
二、什么情况下选择以车代磨工艺
虽说目前已实现以车代磨工艺,但车削并不是完全代替了磨削加工淬火件。
如淬火件精度要求较高时可选择磨削方式,那什么情况下可选择以车代磨工艺,请看以下分析:
(1)在数控机床上加工复杂的表面和几个复杂的表面,车削代替磨削工序可以减少1/3——2/3的劳动量,而且能保证很高的位置精度。
(2)形状复杂的内孔或小孔。
如采用磨削,要求砂轮的形状也相应复杂,有的时候无法磨削,这时采用车削最为有利。
(3)一个零件几个表面(外圆、内孔、端面、阶台、沟槽)都需磨削,这时采用车削,一道工序即可完成,可减去磨削用的工装。
(4)零件淬火后易变形和留余量小时易造成废品,这时可留余量大一些,待淬火后,再用超硬刀具切除多余余量,再磨削,以减少因变形大而产生的废品,此时可以选择韧性好的立方氮化硼刀片(非金属粘合剂立方氮化硼刀片)进行大余量硬车削。
(5)在加工载荷变动量很大的,困难条件下使用的表面高频零件,采用超硬刀具加工,工件表面组织和物理力学性能较磨削时好,可以延长零件的使用寿命。
三、以车代磨加工淬火件的车刀刀具材料
在一开始就介绍了可以车代磨的刀具材料:硬质合金刀具,陶瓷刀具,立方氮化硼刀片,并对三种刀具从硬度和韧性上做出分析,其中立方氮化硼刀片是最适合加工淬火件的刀具材料。
由于淬火件经过热处理后的硬度高,属于难加工材料的一种,从硬度上来划分以上三种刀具适合的加工范围。
硬质合金刀具:由于本身刀体硬度低,故只适合加工硬度HRC45以下的淬火件,低速切削效果较好;
陶瓷刀具:众所周知脆性大是陶瓷刀具的缺点,只适合加工硬度HRC45-55之间的小余量的淬火件,并且尽量避免断续切削;
立方氮化硼刀片:由于具备较高的硬度和耐磨性,良好的抗冲击性能,故适合加工HRC45以上的淬火件。
尤其是我国华菱超硬研制的非金属粘合剂立方氮化硼刀片BN-S20牌号,不仅可大余量加工淬火件,而且可断续切削,解决了传统立方氮化硼刀片不能粗加工和断续加工的问题。
华菱超硬是一家集立方氮化硼刀片设计,生产,技术服务于一体的中国民族刀具品牌企业,其刀具方案可全方位、高效的完成硬材料加工行业领域的各种零部件的车削、铣削等一系列加工。
目前被广泛应用于高硬度材料,热处理
后的高硬度工件,和其他难切削材料的零件领域。
自创立以来,与多家机械零部件商家建立了长期合作伙伴关系,刀具产品覆盖了中国高硬度切削和高速切削产品领域的90%的市场。
四、华菱超硬非金属粘合剂立方氮化硼刀片BN-S20牌号的切削参数。
1、线速度:工件材料硬度越高,其切削速度应越小。
使用立方氮化硼刀片BN-S20牌号进行车加工淬火件时,刀片能够承受的切削速度为80——
200m/min,常用范围为90——150m/min;当采用大切深或强力断续切削时,切速应保持在50——100m/min。
2、吃刀深度:以车代磨淬火件时,其切深一般在0.1——0.3mm之间。
当热处理变形或者加工余量大时,立方氮化硼刀片BN-S20牌号可以承受7mm左右吃刀深度,进行大余量一次走刀完成加工。
3,进给量:进给量通常可以选择0.05——0.25mm/r之间,具体数值视表面粗糙度值和生产率要求而定。
当表面粗糙度要求为Ra=0.3——0.4µm时,采用立方氮化硼刀片可以代替精磨,由于加工效率高的原因,车削比用磨削经济得多。
五、总结
随着以车代磨工艺的普遍发展,为机械制造商解决了很多难加工问题,并且随着现代技术的不断发展,会出现越来越多的高硬度难加工材料,这对于刀
具行业来说,只要不断推陈出新,研制出新的高硬度,高质量,高效率的刀具材料或刀片牌号,就能推动机械制造业的发展。