刀的生产工序及工艺
切削刀具生产工艺流程

切削刀具生产工艺流程
《切削刀具生产工艺流程》
切削刀具是机械加工中不可或缺的工具,其生产工艺流程非常复杂,需要经过多道工序才能完成。
下面就来详细介绍一下切削刀具的生产工艺流程。
首先,切削刀具的生产需要原材料,一般来说,刀具的主要原料是高速钢、硬质合金等。
这些原料需要经过熔炼、锻造、热处理等工序才能成为可用的刀具材料。
接下来是刀具的精密加工工序。
这包括数控车床加工、磨削、磨齿等工艺。
在这个环节中,需要对刀具的外形和精度进行加工,以确保刀具的质量和工作效率。
随后是刀具的镶接工艺。
有些切削刀具需要在刀身上进行镶接硬质合金刀片,这需要通过焊接或钎焊等方法将刀片固定在刀身上。
最后是刀具的表面处理。
这包括镀层、抛光、喷涂等工艺,可以提高切削刀具的耐磨性和耐腐蚀性,延长刀具的使用寿命。
总的来说,切削刀具的生产工艺流程包括原材料准备、精密加工、镶接和表面处理等多个环节。
每个环节都需要严格控制,以确保刀具的质量和性能达到设计要求。
希望通过这个介绍,可以让大家更加了解切削刀具的生产工艺流程。
刀具工艺流程
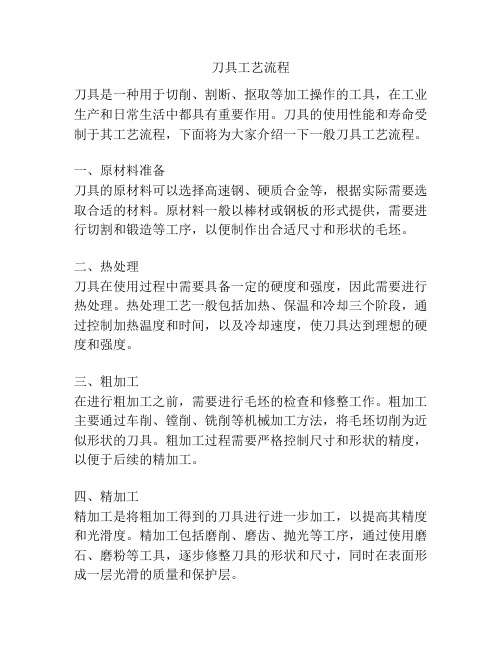
刀具工艺流程刀具是一种用于切削、割断、抠取等加工操作的工具,在工业生产和日常生活中都具有重要作用。
刀具的使用性能和寿命受制于其工艺流程,下面将为大家介绍一下一般刀具工艺流程。
一、原材料准备刀具的原材料可以选择高速钢、硬质合金等,根据实际需要选取合适的材料。
原材料一般以棒材或钢板的形式提供,需要进行切割和锻造等工序,以便制作出合适尺寸和形状的毛坯。
二、热处理刀具在使用过程中需要具备一定的硬度和强度,因此需要进行热处理。
热处理工艺一般包括加热、保温和冷却三个阶段,通过控制加热温度和时间,以及冷却速度,使刀具达到理想的硬度和强度。
三、粗加工在进行粗加工之前,需要进行毛坯的检查和修整工作。
粗加工主要通过车削、镗削、铣削等机械加工方法,将毛坯切削为近似形状的刀具。
粗加工过程需要严格控制尺寸和形状的精度,以便于后续的精加工。
四、精加工精加工是将粗加工得到的刀具进行进一步加工,以提高其精度和光滑度。
精加工包括磨削、磨齿、抛光等工序,通过使用磨石、磨粉等工具,逐步修整刀具的形状和尺寸,同时在表面形成一层光滑的质量和保护层。
五、涂层处理为了提高刀具的抗磨、抗腐蚀和降低表面摩擦系数,常常需要进行涂层处理。
常见的涂层材料有TiN膜、TiAlN膜等,涂层工艺一般包括准备表面、涂覆材料、热处理和检验等多个环节。
六、检验和调试经过上述工艺流程,得到的刀具需要进行质量检验和调试。
检验包括外观检查、尺寸测量、硬度测量等,以确保刀具符合设计要求。
调试则是测试刀具的切削性能、使用寿命和稳定性等方面的指标,以保证刀具能够正常使用。
七、包装和出厂经过质量检验和调试后,合格的刀具将进行包装和标识,以方便销售和运输。
包装方式一般根据刀具的类型和材料的不同而有所差异,通常采用塑料袋、纸盒和木箱等包装方式。
包装完成后,刀具将按照客户需求进行分类存放,并准备出厂。
刀具工艺流程是为了制造出具有优良性能和使用寿命的刀具,不同类型的刀具工艺流程可能有所差异。
螺丝刀的生产工艺流程

螺丝刀的生产工艺流程Manufacturing a screwdriver involves a complex process that requires a combination of specialized machinery, skilled workers, and quality control measures. 螺丝刀的生产涉及一个复杂的过程,需要专门的机器、熟练的工人和质量控制措施的结合。
The first step in the production process is the selection of high-quality materials, such as steel or aluminum, which will determine the durability and performance of the screwdriver. 生产过程的第一步是选择高质量的材料,如钢或铝,这将决定螺丝刀的耐用性和性能。
Once the materials are selected, they are then shaped and molded into the desired screwdriver design using a combination of cutting, bending, and stamping techniques. 一旦选择了材料,它们就会使用切割、弯曲和冲压技术的组合来成型并制成所需的螺丝刀设计。
This process requires precision and attention to detail to ensure that each screwdriver meets the necessary specifications. 这个过程需要精密和对细节的关注,以确保每个螺丝刀符合必要的规格。
After the screwdriver heads are formed, they are then attached tothe handles using a variety of methods, such as welding, adhesivebonding, or threading. 在螺丝刀头形成后,它们会使用各种方法,如焊接、粘接或螺纹连接,与手柄连接。
美工刀生产工艺

美工刀生产工艺美工刀是一种广泛应用于美术制作、手工制作和工艺制作等领域的工具,它具有锋利的刀片和舒适的握持感,可以高效准确地完成各种切割、修整和修饰任务。
美工刀的生产工艺经过多年的发展和实践总结,逐渐形成了一套完善的流程,下面将对美工刀的生产工艺进行详细介绍。
首先,美工刀的材料通常采用优质的不锈钢作为刀片材料,这种材料具有较高的硬度和耐磨性,能够满足刀片经常使用下的割切要求。
同时,刀柄部分通常采用聚酯树脂或塑料材料制作,这种材料具有较好的韧性和抗老化性能,能够保证刀柄的稳定性和寿命。
其次,美工刀的生产过程通常分为刀片的制作和刀柄的制作两个环节。
刀片的制作主要包括材料的选择、切割、磨削、锻烧和淬火等工序。
首先,根据美工刀的使用要求,选取适当的不锈钢材料进行切割,经过切割后,进行磨削工序,以获得一定的刀片形状和轮廓。
然后,进行锻烧处理,以增加刀片的硬度和耐磨性。
最后,对刀片进行淬火处理,以提高刀片的韧性和弹性。
刀柄的制作则包括选择合适的材料、注塑成型、打磨和组装等工序。
首先,根据刀片的尺寸和形状,选取合适的聚酯树脂或塑料材料进行注塑成型,以制作刀柄的外形和握持部分。
然后,对刀柄进行打磨处理,以提高握持的舒适性和手感。
最后,将刀片和刀柄组装在一起,通过螺纹和锁定机构进行固定。
再次,美工刀的质量控制主要体现在刀片的硬度和耐磨性、刀柄的稳定性和握持舒适性等方面。
刀片的质量通常通过硬度测试和耐磨性测试进行评估,确保刀片可以满足不同割切任务的需求。
刀柄的质量则主要体现在聚酯树脂或塑料材料的稳定性和强度方面,保证刀柄可以长时间使用而不变形或破裂。
同时,还需要考虑刀柄的握持舒适性,通过人体工学设计和握持试验等手段,使刀柄适合不同使用者的手型和习惯。
最后,在美工刀的生产过程中,还需要考虑到环保和安全因素。
在材料选择时,优先选择环保材料,减少对环境的污染。
在生产过程中,加强安全管理,如刀片磨削时要佩戴护目镜和手套,防止刀柄注塑时的热熔料喷溅等。
陶瓷刀的生产工艺
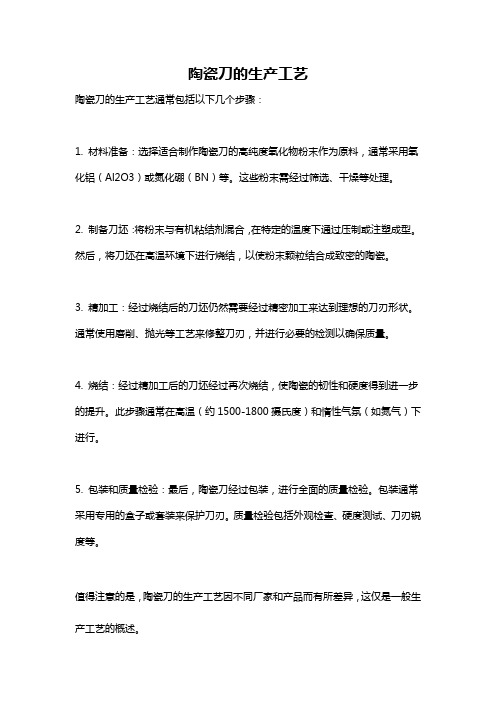
陶瓷刀的生产工艺
陶瓷刀的生产工艺通常包括以下几个步骤:
1. 材料准备:选择适合制作陶瓷刀的高纯度氧化物粉末作为原料,通常采用氧化铝(Al2O3)或氮化硼(BN)等。
这些粉末需经过筛选、干燥等处理。
2. 制备刀坯:将粉末与有机粘结剂混合,在特定的温度下通过压制或注塑成型。
然后,将刀坯在高温环境下进行烧结,以使粉末颗粒结合成致密的陶瓷。
3. 精加工:经过烧结后的刀坯仍然需要经过精密加工来达到理想的刀刃形状。
通常使用磨削、抛光等工艺来修整刀刃,并进行必要的检测以确保质量。
4. 烧结:经过精加工后的刀坯经过再次烧结,使陶瓷的韧性和硬度得到进一步的提升。
此步骤通常在高温(约1500-1800摄氏度)和惰性气氛(如氮气)下进行。
5. 包装和质量检验:最后,陶瓷刀经过包装,进行全面的质量检验。
包装通常采用专用的盒子或套装来保护刀刃。
质量检验包括外观检查、硬度测试、刀刃锐度等。
值得注意的是,陶瓷刀的生产工艺因不同厂家和产品而有所差异,这仅是一般生产工艺的概述。
日本刀与唐刀锻造工艺
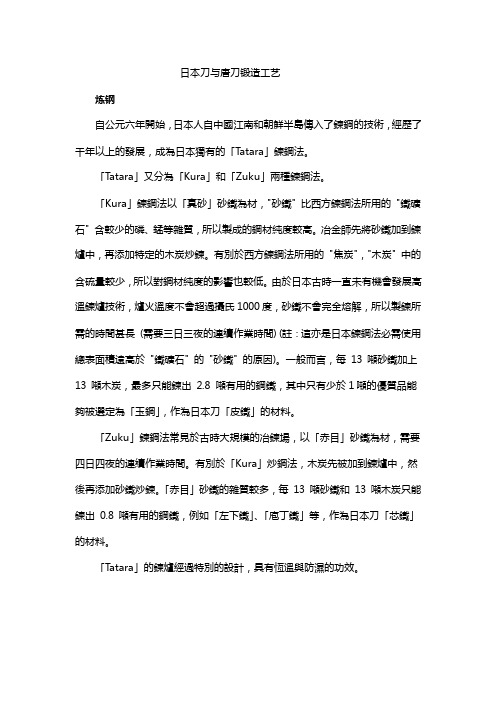
日本刀与唐刀锻造工艺炼钢自公元六年開始,日本人自中國江南和朝鮮半島傳入了鍊鋼的技術,經歷了千年以上的發展,成為日本獨有的「T atara」鍊鋼法。
「T atara」又分為「Kura」和「Zuku」兩種鍊鋼法。
「Kura」鍊鋼法以「真砂」砂鐵為材,"砂鐵" 比西方鍊鋼法所用的"鐵礦石" 含較少的磷、錳等雜質,所以製成的鋼材純度較高。
冶金師先將砂鐵加到鍊爐中,再添加特定的木炭炒鍊。
有別於西方鍊鋼法所用的"焦炭","木炭" 中的含硫量較少,所以對鋼材純度的影響也較低。
由於日本古時一直未有機會發展高溫鍊爐技術,爐火溫度不會超過攝氏1000度,砂鐵不會完全熔解,所以製鍊所需的時間甚長(需要三日三夜的連續作業時間) (註:這亦是日本鍊鋼法必需使用總表面積遠高於"鐵礦石" 的"砂鐵" 的原因)。
一般而言,每13 噸砂鐵加上13 噸木炭,最多只能鍊出2.8 噸有用的鋼鐵,其中只有少於1噸的優質品能夠被選定為「玉鋼」,作為日本刀「皮鐵」的材料。
「Zuku」鍊鋼法常見於古時大規模的冶鍊場,以「赤目」砂鐵為材,需要四日四夜的連續作業時間。
有別於「Kura」炒鋼法,木炭先被加到鍊爐中,然後再添加砂鐵炒鍊。
「赤目」砂鐵的雜質較多,每13 噸砂鐵和13 噸木炭只能鍊出0.8 噸有用的鋼鐵,例如「左下鐵」、「庖丁鐵」等,作為日本刀「芯鐵」的材料。
「T atara」的鍊爐經過特別的設計,具有恆溫與防濕的功效。
炒鍊以後,得到一整塊素質不均的鐵塊。
冶金師會用大鎚將鐵塊打碎,再將碎鐵分門別類。
「Kura」的完成品有「玉鋼」、「破面」、「鐵滓」等;「Zuku」的完成品有「左下鐵」、「庖丁鐵」等。
「玉鋼」的碳含量約為1.0 到1.5%,「左下鐵」約為0.7%,「庖丁鐵」約為0.1 到0.3%。
「T atara」鍊製的鋼鐵含極少雜質,材料容易焊合,最適用於鍛製刀劍,更是製作日本刀「折返鍛鍊」工序中的必要條件。
刀的生产工序及工艺

刀具制品的生产工艺前言刀的生产工序及工艺主要有选料、开料成型、打眼冲孔、调直、热处理、打背砂、水磨、抛光、表面处理,开利口、手柄安装,本材料主要了解刀的生产工序及涉及的工艺。
一:生产工序1:开料成型• 按产品尺寸做开料模具、根据材料、硬度、厚度、大小来选择设备。
一般选用方法:2mm的用60T,2.5mm的用60T或80T,3mm、3.5mm的用80T或120T。
•按图纸要求做成型模具、油压或单冲冲压成型,按产品实际厚度选择一般按以下公式计算:平刃冲模的冲裁力:P=KLSτ(N)注:1T=9800N L—冲裁周边长度mm;S—坯料厚度mm τ—抗剪强度Mpa ;K—系数,间隙不均,刃口钝化等τ—抗剪强度碳钢38~47 K一般取1.25~1.32:打眼• 如刀具需要孔位一般还需要上冲床打眼或钻床钻眼机器的选用:16T冲床眼位大小:尽量统一尺寸,选用直径4mm或6mm形状位置尺寸的控制:如两边铆合的塑料手柄,一般用3颗子母钉,平头,铆接加固,头钉起手柄定位作用,中间的起紧固手柄作用(为大眼,如直径6mm),尾钉起加固作用(考虑易装配,尾眼为长眼,可偏移)3:调直•一般的板材经过冲压成型容易变形,热处理前必须有这么一道调直工艺,使用调直机进行。
4:热处理• 一般刀肉都使用马氏体不锈钢生产,如选用3Cr13、4CR13、5Cr15MoV等的一些带钢材料,经热处理后淬火回火工艺增加材质的硬度从而使刀具具有耐磨性。
主要工艺流程如下图:三步曲:①加热℃②保温③冷却从而得到不同的组织和性能的方法。
②①③t- 6 -5:打砂• 打周边、一般胚体还还会存在一些披锋,马氏体在未经过表面处理前还会有一定的绣迹,就要经过打周边把这些披锋和锈迹打掉。
•刀具打砂使用砂轮机和砂带机进行,先粗砂再幼砂,粗砂幼砂石指砂轮的粒度,一般的五金制品厂都会有自己的砂房。
6:水磨• 在水磨机上进行,根据不同类型的刀,采用不同的磨法,其中有单面磨、双面磨、逼牙,这几种工艺都可以通过水磨工艺进行,其中逼牙代表有牛排刀,三文治刀,面包刀的牙都是用水磨逼出。
刀剪磨削工艺

刀剪磨削工艺磨削是常用的精加工方法,磨削质量直接影响工件的精度和品质,刀剪产品加工的关键技术在于磨削和抛光。
刀剪磨削不同于普通磨削,其磨削特点有磨削量大、表面硬度高、纹理细密等,属一次性强力磨削。
在磨削过程中会产生磨焦、卷刃、塌头、刀剪口线不直,剪根有台阶、裂纹、纹理过粗等缺陷。
第一章介绍了刀剪产品的市场竞争趋势,对国内外刀剪产品的情况进行对比,并介绍了本文的课题来源、目标、内容和工作方案。
第二章综述了目前国内刀剪磨削方法;从磨具磨料、磨削面等方面说明刀剪的磨削特征;并分析刀剪磨削技术的发展和关键技术。
第三章对刀剪磨削力的计算进行分析。
文中列出磨削力计算经验公式、实用公式及理论计算公式,根据磨削方式的不同选择磨削力计算公式,在设计时可以反复多次计算确定各项磨削参数,并进行强度校核。
第四章提出砂轮对刀剪进行磨削加工过程中产生的磨削热是影响刀剪表面质量的重要因素,分析了磨削热的产生,讨论了磨削温度对刀剪产品的影响;对刀剪磨焦作了较详细的分析,磨削刀剪时选择合适的砂轮、冷却方式及磨削量等参数,确保刀剪产品的磨削质量。
第五章从刀剪加工工艺分析了刀剪裂纹的产生和扩展,根据刀剪的形状和磨削部位等确定危险截面,对产生的危险裂纹从受力方面进行分析。
通过断裂力学理论对民用剪刀裂纹处的应力强度因子和应力状况进行分析,由切向磨削力和法向磨削力计算出临界裂纹,并举例进行计算和验证。
通过刀具开裂成因及其改进举例分析,提出相应的改进措施。
最后,对本文的研究结果进行了总结并对进一步工作进行展望。
1.1刀剪产品市场竞争趋势刀剪行业是我国历史悠久的传统行业,现正名副其实地呈现了“小商品,大市场”的喜人形势。
2003年国际刀剪进出口总额是36亿美元,我国刀剪出口总额是4.1l亿美元,占世界出口总额的lO%左右,其中一半以上是对外来料加工,市场空间非常广阔。
我国出口产品高档次不多,基本都是中低档产品。
随着中国加入世界贸易组织,我国的刀剪行业将更多地参与国际市场竞争。
- 1、下载文档前请自行甄别文档内容的完整性,平台不提供额外的编辑、内容补充、找答案等附加服务。
- 2、"仅部分预览"的文档,不可在线预览部分如存在完整性等问题,可反馈申请退款(可完整预览的文档不适用该条件!)。
- 3、如文档侵犯您的权益,请联系客服反馈,我们会尽快为您处理(人工客服工作时间:9:00-18:30)。
刀具制品的生产工艺
前言
刀的生产工序及工艺主要有选料、开料成型、打眼冲孔、调直、热处理、打背砂、水磨、抛光、表面处理,开利口、手柄安装,本材料主要了解刀的生产工序及涉及的工艺。
一:生产工序
1:开料成型
• 按产品尺寸做开料模具、根据材料、硬度、厚度、大小来选择设备。
一般选用方法:2mm的用60T,2.5mm的用60T或80T,3mm、3.5mm的用80T或120T。
•按图纸要求做成型模具、油压或单冲冲压成型,按产品实际厚度选择一般按以下公式计算:
平刃冲模的冲裁力:P=KLSτ(N)注:1T=9800N L—冲
裁周边长度mm;S—坯料厚度mm τ—抗剪强度Mpa ;
K—系数,间隙不均,刃口钝化等τ—抗剪强度碳钢
38~47 K一般取1.25~1.3
2:打眼
• 如刀具需要孔位一般还需要上冲床打眼或钻床钻眼
机器的选用:16T冲床
眼位大小:
尽量统一尺寸,选用直径4mm或6mm形状位置尺寸的控制:如两边铆合的塑料手柄,一般用3颗子母钉,平头,铆接加固,头
钉起手柄定位作用,中间的起紧固手柄作用(为大眼,如直径6mm),尾钉起加固作用(考虑易装配,尾眼为长眼,可偏移)
3:调直
•一般的板材经过冲压成型容易变形,热处理前必须有这么一道调直工艺,使用调直机进行。
4:热处理
• 一般刀肉都使用马氏体不锈钢生产,如选用3Cr13、4CR13、
5Cr15MoV等的一些带钢材料,经热处理后淬火回火工艺增加材质的硬度从而使刀具具有耐磨性。
主要工艺流程如下图:
三步曲:
①加热
℃
②保温
③冷却
从而得到不同的组织和性能的方法。
②
①③
t
- 6 -
5:打砂
• 打周边、一般胚体还还会存在一些披锋,马氏体在未经过表面处理前还会有一定的绣迹,就要经过打周边把这些披锋和锈迹打掉。
•刀具打砂使用砂轮机和砂带机进行,先粗砂再幼砂,粗砂幼砂石指砂轮的粒度,一般的五金制品厂都会有自己的砂房。
6:水磨
• 在水磨机上进行,根据不同类型的刀,采用不同的磨法,其中有单面磨、双面磨、逼牙,这几种工艺都可以通过水磨工艺进行,其中逼牙代表有牛排刀,三文治刀,面包刀的牙都是用水磨逼出。
7:抛光通常以抛光轮作为抛光工具,抛光轮可分三种方
式:
1)非缝合式整布轮。
多用细软棉布制成,宜抛光形状复杂工件,或用于小型工件的精抛光。
2)缝合式。
多用粗布、无纺布及细平布等制成,缝线可采用同心圆式螺旋式及直辐射形式,宜抛光各种镀层及形状较简单的工作。
3)风冷布轮。
采用45度角线裁法,呈环形皱褶状,中间装有金属圆盘,具有通风散热的特点,宜抛光大型工件。
•镜光利用高速电机驱动用羊毛轮(市面有售),配合大青腊对刀肉进行镜面磨光。
一般情况是在进行抛磨工件之前先给羊毛轮进行打蜡,待羊毛轮上粘满青腊后才开始进行抛磨,用干净的棉布轮在经过镜面后的工件表面摩擦,将前面所有工序完成后的工件擦干净
8:表面处理
1:常见刀具刀肉表面处理工艺有镀钛、抛砂光、抛镜光、喷砂、热转印、喷不粘漆。
2:常见手柄表面处理工艺有铝氧化、PP加橡塑(二次注塑)、披覆、电脑锣等。
3:常见打字唛工艺有激光、钢印、蚀印、丝印、移印等。
9:开利口
•一般金属刀具开利口按使用工具来分开有三种方式,砂轮开利口,砂带开利口,水转盘开利口。
•开利口的要求:
1:锋利度可以使用刀具锋利度测试仪测试,或手测。
2:刀口是否有烧痕一般的砂轮和砂带开利口如师傅操作不当会出现
烧口,发黄、可以目测。
8:刀手柄归类
•刀手柄按使用材料来区分可分为7大类
1:木柄木柄常用材料有花梨木、彩木、杂木、孙枝、黑檀等2:夹心柄两边为金属中间夹塑料或者其他材料
3:钢头钢头可分为单钢头、双钢头和假钢头
4:塑料柄常用材料有电木、PP、PP加橡塑、ABS、POM等
5:空心柄空心柄一般是通过焊接抛光而成
6: G10柄是一种由玻璃纤维布与环氧数脂所合成的复合材料、一般有黑色、红色、蓝色、绿色等颜色、一般使用电
脑锣进行表面处理。
7:铝柄铝柄一般在小刀上比较常用,常见为铝氧化着色
总结
刀的档次区别主要来源于刀肉和手柄材料的选取及刀的外观设计。
生产刀肉的进口材料有山特维克12C27、440C,国产材料有CR13、2CR13、3CR13、4CR13、5CR15MOV、7CR17MOV 等。
其高中低档材料主要区别在于热处理后的硬度、耐磨性、韧性及防锈能力。