SEET-神鹰-热压罐成型工艺安全性分析
热压罐成型复合材料成型工艺的常见缺陷及对策
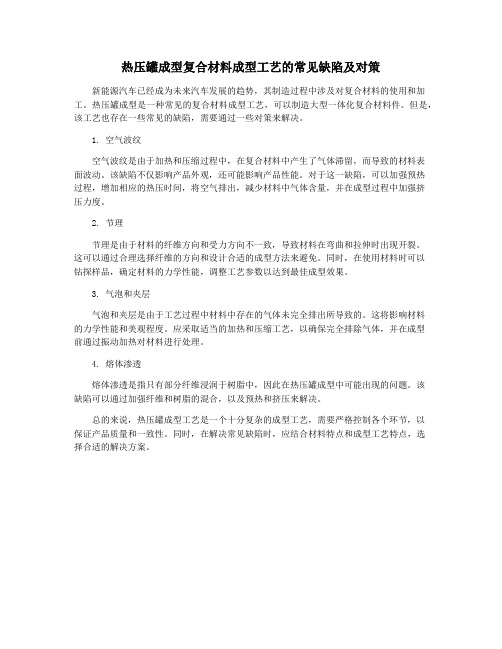
热压罐成型复合材料成型工艺的常见缺陷及对策
新能源汽车已经成为未来汽车发展的趋势,其制造过程中涉及对复合材料的使用和加工。
热压罐成型是一种常见的复合材料成型工艺,可以制造大型一体化复合材料件。
但是,该工艺也存在一些常见的缺陷,需要通过一些对策来解决。
1. 空气波纹
空气波纹是由于加热和压缩过程中,在复合材料中产生了气体滞留,而导致的材料表
面波动。
该缺陷不仅影响产品外观,还可能影响产品性能。
对于这一缺陷,可以加强预热
过程,增加相应的热压时间,将空气排出,减少材料中气体含量,并在成型过程中加强挤
压力度。
2. 节理
节理是由于材料的纤维方向和受力方向不一致,导致材料在弯曲和拉伸时出现开裂。
这可以通过合理选择纤维的方向和设计合适的成型方法来避免。
同时,在使用材料时可以
钻探样品,确定材料的力学性能,调整工艺参数以达到最佳成型效果。
3. 气泡和夹层
气泡和夹层是由于工艺过程中材料中存在的气体未完全排出所导致的。
这将影响材料
的力学性能和美观程度。
应采取适当的加热和压缩工艺,以确保完全排除气体,并在成型
前通过振动加热对材料进行处理。
4. 熔体渗透
熔体渗透是指只有部分纤维浸润于树脂中,因此在热压罐成型中可能出现的问题。
该
缺陷可以通过加强纤维和树脂的混合,以及预热和挤压来解决。
总的来说,热压罐成型工艺是一个十分复杂的成型工艺,需要严格控制各个环节,以
保证产品质量和一致性。
同时,在解决常见缺陷时,应结合材料特点和成型工艺特点,选
择合适的解决方案。
热压罐成型复合材料成型工艺的常见缺陷及对策
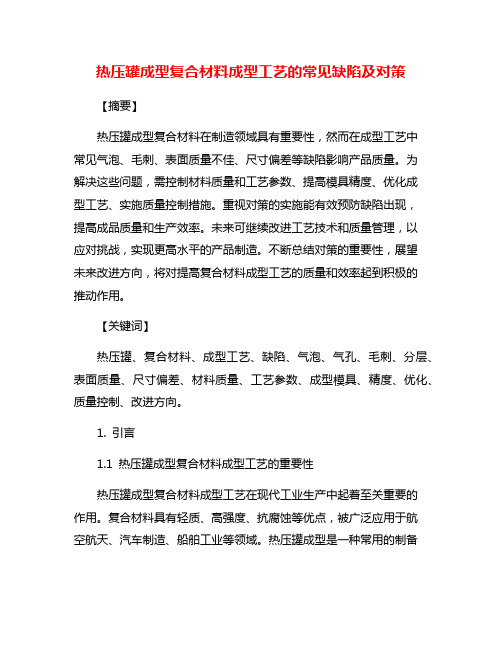
热压罐成型复合材料成型工艺的常见缺陷及对策【摘要】热压罐成型复合材料在制造领域具有重要性,然而在成型工艺中常见气泡、毛刺、表面质量不佳、尺寸偏差等缺陷影响产品质量。
为解决这些问题,需控制材料质量和工艺参数、提高模具精度、优化成型工艺、实施质量控制措施。
重视对策的实施能有效预防缺陷出现,提高成品质量和生产效率。
未来可继续改进工艺技术和质量管理,以应对挑战,实现更高水平的产品制造。
不断总结对策的重要性,展望未来改进方向,将对提高复合材料成型工艺的质量和效率起到积极的推动作用。
【关键词】热压罐、复合材料、成型工艺、缺陷、气泡、气孔、毛刺、分层、表面质量、尺寸偏差、材料质量、工艺参数、成型模具、精度、优化、质量控制、改进方向。
1. 引言1.1 热压罐成型复合材料成型工艺的重要性热压罐成型复合材料成型工艺在现代工业生产中起着至关重要的作用。
复合材料具有轻质、高强度、抗腐蚀等优点,被广泛应用于航空航天、汽车制造、船舶工业等领域。
热压罐成型是一种常用的制备复合材料制品的工艺方法,通过热压的方式将树脂基复合材料与增强材料加热固化,形成具有特定性能和形状的制品。
热压罐成型复合材料成型工艺的重要性体现在以下几个方面:通过热压罐成型可以实现复合材料高效率、高质量的生产,提高生产效率和制品质量。
热压罐成型工艺可以实现复合材料的复杂成型,满足不同领域对复合材料制品的各种需求。
热压罐成型技术可以有效控制制品的成型过程,减少工艺参数对成品性能的影响,确保制品的稳定性和一致性。
热压罐成型复合材料成型工艺的重要性在于提高生产效率、提高制品质量、满足市场需求,是现代工业制造中不可或缺的一环。
通过对该工艺的研究和不断改进,可以更好地发挥其优势,推动复合材料产业的发展。
1.2 研究目的和意义1.了解热压罐成型复合材料成型工艺的重要性和发展趋势,为提高产品质量和性能提供技术支持。
2.分析常见缺陷对产品品质和成型效率的影响,找出问题根源,提出相应的改进措施。
热压罐成型复合材料成型工艺的常见缺陷及对策

热压罐成型复合材料成型工艺的常见缺陷及对策热压罐成型复合材料是一种常见的加工工艺,它具有高强度、轻质、耐腐蚀等优点,被广泛应用于航空航天、汽车制造、建筑等领域。
在实际生产中,热压罐成型复合材料也存在一些常见的缺陷,这些缺陷严重影响了产品的质量和性能。
为了解决这些问题,本文将对热压罐成型复合材料常见的缺陷及对策进行详细分析和探讨。
常见缺陷一:气泡热压罐成型复合材料中最常见的缺陷之一就是气泡。
气泡是由于树脂在固化过程中释放气体或未溶解的气体从复合材料中逸出而导致的,如果未能有效排除气泡就会影响复合材料的力学性能和外观质量。
对策:可以采用真空充注法将树脂浸渍过程中释放的气体排出,避免气泡的产生。
可以在制造过程中加压处理,利用高压将未溶解的气体挤出复合材料,从而减少气泡的产生。
还可以对材料的工艺参数进行精确控制,以减少气体的溶解和释放。
常见缺陷二:结构不均匀在热压罐成型复合材料中,由于树脂的流动性差、树脂和纤维的分布不均匀等因素,导致产品的结构不均匀,这会严重影响产品的力学性能和外观质量。
对策:针对结构不均匀的问题,可以采用以下对策来加以解决。
可以在制造过程中采用振动和震荡等方式,使树脂和纤维更均匀地分布在复合材料中。
可以通过优化成型工艺参数,比如调整充填速度、加热温度等,来控制材料的流动性,从而改善产品的结构均匀性。
还可以在制造过程中采用逐层堆叠的方式,使树脂和纤维更均匀地分布在复合材料中。
常见缺陷三:表面缺陷热压罐成型复合材料的表面往往容易出现一些缺陷,比如气孔、坑洞、刮痕等,这些表面缺陷不仅影响了产品的外观质量,还可能导致产品的力学性能下降。
对策:针对表面缺陷问题,可以采用以下对策来加以解决。
可以优化模具设计,提高产品的表面光洁度,减少表面缺陷的产生。
可以在成型过程中采用真空吸取或压紧模,使树脂充分填充模具,减少气体和空隙的产生,从而减少表面缺陷。
还可以在模具表面涂覆一层润滑剂,减少模具与复合材料的摩擦力,从而减少表面缺陷的产生。
热压罐成型复合材料成型工艺的常见缺陷及对策

热压罐成型复合材料成型工艺的常见缺陷及对策热压罐成型复合材料成型工艺是一种广泛应用于航空、汽车、船舶等领域的高性能材料成型技术。
由于其具有质量轻、刚性高、耐高温耐腐蚀等优点,因此备受青睐。
在实际生产中,热压罐成型复合材料成型工艺常常会出现各种缺陷,影响产品质量和性能。
本文将重点介绍热压罐成型复合材料成型工艺中常见的缺陷及相应的对策。
一、气泡气泡是热压罐成型复合材料成型工艺中常见的缺陷之一。
气泡的存在会导致制品的密度不均匀,影响其力学性能和耐久性。
气泡的形成原因主要包括树脂充填不足、工装表面粗糙和工艺参数设置不当等。
对策:1. 提高树脂充填效率,保证充填充分;2. 提高工装表面光洁度,减少气泡的产生;3. 调整工艺参数,如温度、压力和时间,使树脂更好地充填并排除气泡。
二、裂纹裂纹是热压罐成型复合材料成型工艺中另一个常见的缺陷。
裂纹的存在会降低制品的强度和韧性,影响其使用寿命。
裂纹的形成主要受到成型温度、成型压力和成型时间的影响,同时也与工装的设计和加工精度有关。
对策:1. 控制成型温度,避免温度过高导致树脂的膨胀收缩,产生裂纹;2. 合理控制成型压力,保证树脂充填充分但不会过大导致裂纹;3. 控制成型时间,避免过长造成树脂过度固化产生裂纹;4. 设计合理的工装结构,减少应力集中和变形,避免裂纹的产生。
三、毛刺对策:1. 优化模具的设计,减少脱模力和剪切力,避免毛刺的产生;2. 提高模具表面的加工精度和光洁度,减少毛刺的生成;3. 采用表面喷涂、电镀等方法,形成一层平滑的保护层,减少毛刺的产生。
四、变形变形是热压罐成型复合材料成型工艺中常见的内部缺陷。
制品的变形会导致尺寸偏差和形状不规则,影响其使用功能和外观美观。
变形的产生主要与工装设计、成型参数和材料性能有关。
对策:1. 优化工装设计,减少应力集中和变形;2. 调整成型参数,如温度、压力和时间,使成型过程更加稳定;3. 选择合适的复合材料,提高材料的强度和韧性,减少变形的产生。
热压罐成型工艺 PPT
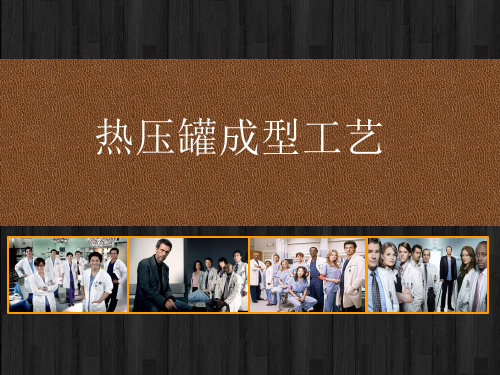
热压罐成型的模具---设计与使用要求
序号 1 2 3 4 5 6 7 8
名称 强度刚度
成型面 配合与定 位 温度场
脱模 随炉件安 排 容差分配 维护保养
设计要求
按工艺使用要求设计模具的强度、刚度,除 真空和正压力外,还应考虑翘曲热变形等。
表面光洁度、硬度满足成型、脱模要求,标 记定位、装配刻线
组合模具应设计装配定位机构,并应保证组 装精度满足制品精度要求
热压罐外观
热压罐内部
通用型热压罐主要技术参数:
真空度:0~0.1MPa 正压力:0~5MPa
加热温度:室温~400℃
热压罐系统要为复合材料的聚合反应创造一个理想的温度和压力环境,它是 由热压罐主体和一系列的子系统组成的,主要包含以下几个部分:
1、热压罐主体; 2、加压系统;3、真空系统;4、加热系统; 5、冷却系统;6、进料系统;7、控制系统;8、鼓风系统;9、仪表阀门
80~100
热压罐成型的模具---模具用材料
特点及要求 应具有导热快、比热容低、刚度高、质量轻、热膨胀系数小、耐热、热稳定性好、 使用寿命长、制造成本低、使用和维护简便、便于运输等特点。 材料 铝:轻、导热性好,但热胀系数高、表面硬度低,适合精度、协调关系不高的产 品。 钢:加工精度高、刚强度高、硬度高、使用寿命长,适合大多数产品。缺点是质 量大,热容量高。 铸钢或铸铁:可代替钢降低成本,但各点温差大、表面容易产生砂眼。 橡胶:随形好、易于配合,适合于制造共固化模。缺点是尺寸稳定性差。 玻纤复合材料:质量轻、成本低,适合于简单型面制品。缺点是材料的模量低。 碳纤复合材料:轻、模量高、刚性好、与碳纤维复材构件的热胀系数一致,能够 赋予制品高精度。缺点是成本高。 木材:质轻价廉,适合制造一次性使用的模具。
热压罐成型复合材料成型工艺的常见缺陷及对策
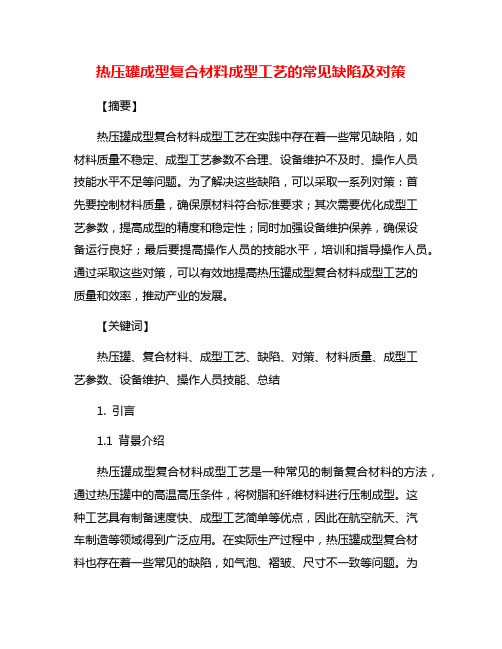
热压罐成型复合材料成型工艺的常见缺陷及对策【摘要】热压罐成型复合材料成型工艺在实践中存在着一些常见缺陷,如材料质量不稳定、成型工艺参数不合理、设备维护不及时、操作人员技能水平不足等问题。
为了解决这些缺陷,可以采取一系列对策:首先要控制材料质量,确保原材料符合标准要求;其次需要优化成型工艺参数,提高成型的精度和稳定性;同时加强设备维护保养,确保设备运行良好;最后要提高操作人员的技能水平,培训和指导操作人员。
通过采取这些对策,可以有效地提高热压罐成型复合材料成型工艺的质量和效率,推动产业的发展。
【关键词】热压罐、复合材料、成型工艺、缺陷、对策、材料质量、成型工艺参数、设备维护、操作人员技能、总结1. 引言1.1 背景介绍热压罐成型复合材料成型工艺是一种常见的制备复合材料的方法,通过热压罐中的高温高压条件,将树脂和纤维材料进行压制成型。
这种工艺具有制备速度快、成型工艺简单等优点,因此在航空航天、汽车制造等领域得到广泛应用。
在实际生产过程中,热压罐成型复合材料也存在着一些常见的缺陷,如气泡、褶皱、尺寸不一致等问题。
为了提高产品质量和生产效率,需要对这些常见缺陷进行深入分析,并制定相应的对策来解决这些问题。
本文将从控制材料质量、优化成型工艺参数、加强设备维护保养、提高操作人员技能水平等方面进行讨论,为热压罐成型复合材料成型工艺的改进提供参考。
2. 正文2.1 热压罐成型复合材料成型工艺存在的常见缺陷热压罐成型复合材料是一种常用的制备工艺,在许多领域都有广泛的应用。
这种工艺也存在一些常见的缺陷,影响材料的质量和性能。
以下是热压罐成型复合材料成型工艺存在的一些常见缺陷:1. 母材和增强材料不充分混合:在成型过程中,如果母材和增强材料没有充分混合,会导致材料性能不均匀,出现局部强度不足的现象。
2. 难以排气:在热压罐成型过程中,由于材料层间存在气泡,导致成型后出现气孔,影响材料的密实性和强度。
3. 成型温度控制不当:如果成型温度过高或过低,都会影响材料的物理性能,例如过高的温度会导致材料烧损,过低的温度则会影响材料的结晶度。
热压罐成型复合材料成型工艺的常见缺陷及对策
热压罐成型复合材料成型工艺的常见缺陷及对策作者:胡大豹来源:《科技风》2019年第34期摘要:随着先进复合材料在飞机上的大量应用,复合材料低成本成为目前面临的重要课题,飞机复合材料构件种类繁多,工艺控制难度大,缺陷会严重影响符合材料构件表面质量,本文对热压罐成型符合财力结构制造缺陷的形成机制进行分析,包括等厚板孔隙缺陷,整体成型中的分层扩展,建立复合材料热压罐工艺制造缺陷分析系统,为航空复合材料主承力结构制造缺陷控制,促进工程应用奠定技术基础。
关键词:热压罐;复合材料;成型工艺;缺陷热压罐成型方法具有许多其他工艺不具备的优点,可制造形状复杂的制件,制品质量问题,成型工艺灵活,适于生产大面积整体成型构件,纤维含量高,孔隙率低。
热压罐成型工艺具有设备投资高,成型周期长的特点,热压罐成型复合材料构件主要缺陷包括外形尺寸与内部治理等,内部质量包括分层,夹杂等。
造成缺陷的原因种类繁多,包括制造中的人机料法环各环节的相关工序。
本文分析非等厚板材常见缺陷产生原因,分析内容对复合材料零件質量控制具有一定的借鉴作用。
一、热压罐成型工艺特点热压罐成型工艺主要是将复合材料毛坯或交接结构用真空密封在热压罐中,用罐体内部均匀温度场对成型中的零件施加温度压力,使其成为所需要的形状与质量状态的成型工艺方法。
其成型工艺特点主要是罐内压力均匀,真空带内的零件在均匀压力下成型。
适用范围广,成型工艺稳定,热压罐温度条件几乎满足所有聚合物基复合材料的成型工艺要求。
可保证成型的及零件质量问题,热压罐成型工艺制造的层合板孔隙率较低,相对其他成型工艺成型层板力学性能稳定。
热压罐工艺存在一些不足,投资建造大型热压罐的费用很高,需专人操作,成型过程中耗费大量能源,形状复杂的结构不适用热压罐成型工艺,可根据具体情况选择RTM低成本成型工艺。
二、内部质量(一)非等厚层板缺陷分析复合材料零件的内部质量主要通过无损检测方法判定,零件的材料类型,外形尺寸不同,产生的缺陷不同。
热压罐成型复合材料成型工艺的常见缺陷及对策
DOI:10.19392/j.cnki.1671 ̄7341.201934125热压罐成型复合材料成型工艺的常见缺陷及对策胡大豹中航飞机股份有限公司㊀陕西西安㊀710089摘㊀要:随着先进复合材料在飞机上的大量应用ꎬ复合材料低成本成为目前面临的重要课题ꎬ飞机复合材料构件种类繁多ꎬ工艺控制难度大ꎬ缺陷会严重影响符合材料构件表面质量ꎬ本文对热压罐成型符合财力结构制造缺陷的形成机制进行分析ꎬ包括等厚板孔隙缺陷ꎬ整体成型中的分层扩展ꎬ建立复合材料热压罐工艺制造缺陷分析系统ꎬ为航空复合材料主承力结构制造缺陷控制ꎬ促进工程应用奠定技术基础ꎮ关键词:热压罐ꎻ复合材料ꎻ成型工艺ꎻ缺陷㊀㊀热压罐成型方法具有许多其他工艺不具备的优点ꎬ可制造形状复杂的制件ꎬ制品质量问题ꎬ成型工艺灵活ꎬ适于生产大面积整体成型构件ꎬ纤维含量高ꎬ孔隙率低ꎮ热压罐成型工艺具有设备投资高ꎬ成型周期长的特点ꎬ热压罐成型复合材料构件主要缺陷包括外形尺寸与内部治理等ꎬ内部质量包括分层ꎬ夹杂等ꎮ造成缺陷的原因种类繁多ꎬ包括制造中的人机料法环各环节的相关工序ꎮ本文分析非等厚板材常见缺陷产生原因ꎬ分析内容对复合材料零件质量控制具有一定的借鉴作用ꎮ一㊁热压罐成型工艺特点热压罐成型工艺主要是将复合材料毛坯或交接结构用真空密封在热压罐中ꎬ用罐体内部均匀温度场对成型中的零件施加温度压力ꎬ使其成为所需要的形状与质量状态的成型工艺方法ꎮ其成型工艺特点主要是罐内压力均匀ꎬ真空带内的零件在均匀压力下成型ꎮ适用范围广ꎬ成型工艺稳定ꎬ热压罐温度条件几乎满足所有聚合物基复合材料的成型工艺要求ꎮ可保证成型的及零件质量问题ꎬ热压罐成型工艺制造的层合板孔隙率较低ꎬ相对其他成型工艺成型层板力学性能稳定ꎮ热压罐工艺存在一些不足ꎬ投资建造大型热压罐的费用很高ꎬ需专人操作ꎬ成型过程中耗费大量能源ꎬ形状复杂的结构不适用热压罐成型工艺ꎬ可根据具体情况选择RTM低成本成型工艺ꎮ二㊁内部质量(一)非等厚层板缺陷分析复合材料零件的内部质量主要通过无损检测方法判定ꎬ零件的材料类型ꎬ外形尺寸不同ꎬ产生的缺陷不同ꎮ非等厚板是基本的复合材料结构形式ꎬ广泛应用于航空航天等翼面及壳体结构ꎬ非等厚板材的树脂流动包括沿垂直于层板方向流进吸胶层ꎬ与在层板内沿平行纤维方向流出两种形式ꎮ面内尺寸大于厚度尺寸时ꎬ可认为树脂只沿厚度方向流动ꎮ压力传递与温度分布较均匀ꎬ出现缺陷比例较低ꎮ在厚度梯度区树脂可沿厚度方向流动ꎬ存在渗流机制与剪切流机制之间的耦合作用ꎮ树脂有由平板向梯度区流动的趋势ꎮ非等厚层板外压作用下梯度区纤维可能发生滑移ꎬ层板在过渡区出现富脂等缺陷ꎮ由于复合材料的各向异性ꎬ引起膨胀系数与热应变的各向异性ꎮ在铺层长短搭接处出现分层等缺陷[1]ꎮ非等厚层板受力及树脂流动示意图(二)曲率构件缺陷分析工程制造中ꎬ对非等厚层板在铺叠时采取多次抽真空压实ꎬ可通过预吸胶工艺吸走多余的树脂ꎮ梯度宽度减小会增加缺陷的比例ꎬ铺层变化应避免突变ꎬ阶梯宽度应大于2MMꎬ尽量降低产生缺陷的比例ꎮ曲率构件包括L型与U型等曲率半径变化较大的构建ꎬ由于其本身的曲面结构ꎬ其成型过程比平板复杂ꎮ弧形构件预浸体系受外界压力后ꎬ内部形成应力状态ꎮ剪切应力大致拐角区域在密实中纤维发生剪切变形ꎮ造成纤维变形[2]ꎮ拐角区是缺陷密集区ꎬ阴模成型时ꎬ铺叠过程中纤维易架桥ꎬ拐角易产生富树脂ꎬ阳模成型时ꎬ拐角厚度偏薄ꎬ易造成分层等缺陷ꎮ影响拐角区缺陷的主要因素包括材料及铺层设计ꎬ受模具圆角半径等影响ꎬ圆角半径设计过小可能在拐角区发生纤维拉断等制造缺陷ꎬ设计复合材料结构时ꎬ拐角处尽量给出较大半径ꎬ复合材料层压零件最小圆角半径按经验公式rmin=1+0.1n计算ꎮN为拐角处层数ꎬ用阳模铺贴rȡtꎬ用阴模铺贴Rȡ2tꎬR为圆角半径ꎮt为平板区域的厚度ꎮ三㊁外形尺寸影响零件外形尺寸的因素主要由固化变形导致的尺寸变化ꎬ从变形产生机理可分为热应力ꎬ温度梯度与树脂固化度等ꎮ复合材料铺层在不同主轴方向具有不同的热膨胀系数ꎬ温度改变引起热膨胀与铺层方式关系密切ꎮ曲率零件即使采用对称铺层ꎬ成型过程中材料因温度变化效应在应变在各方向并非一致ꎮ导致复合材料结构件的回弹固化变形ꎮ对称蒲城弯曲零件受温差δt作用ꎬ零件拐角变为θ+δθꎮ热固性树脂在聚合反应时ꎬ交联密度增加伴随体积减小ꎬ固化收缩过程中横向收缩应变大于轴向ꎮ固化早期反应树脂处于粘流态ꎬ但不产生残余应力ꎮ热固性树脂的化学反应速度与所处温度有关ꎬ如零件部位温度在固话中保持均匀分布ꎬ各部位温度在固话中无法保持均匀分布ꎬ基体树脂的反应造成树脂模量与固化收缩应变不一致ꎮ薄层板差异很小ꎮ厚层板由于其低的横向热传导系数ꎬ层板中间温度小于表面温度ꎬ化学反应热迅速增加ꎮ固化过程层板内部显著的温度与固化梯度ꎮ较快的加热速率影响模具温度场均匀性ꎬ内部产生明显的温度梯度ꎮ较慢的加热速率会造成工时的增加ꎮ四㊁结语非等厚板材梯度区的分层的主要区域ꎬ与树脂的二维流动有关ꎬ合理的铺层设计可有效解决过渡区的缺陷ꎮ模具与零件相互作用等是影响固化变形的主要因素ꎮ结构设计及生产过程控制等是减少变形的有效方法ꎮ曲率构件拐角是缺陷产生的密集区ꎬ与刮胶区受力有关ꎬ通过合理的设计模具ꎬ可大大改善产品质量ꎮ参考文献:[1]史晓辉.基于热压成型工艺的热塑性复合材料在民机上的应用[J].科技视界ꎬ2019(09):4 ̄6+22.[2]董广雨ꎬ丁玉梅ꎬ杨卫民ꎬ谢鹏程.连续碳纤维复合材料热压成型工艺条件优化研究[J].化工新型材料ꎬ2018ꎬ46(08):71 ̄74.931㊀科技风2019年12月机械化工。
国内外复合材料工艺设备发展述评之八热压罐成型
三、发展趋势和挑战
随着科学技术的不断进步和市场需求的变化,复合材料工艺设备的发展趋势 也在不断变化。未来,模压成型设备将更加注重自动化、智能化和绿色化。例如, 通过引入机器人技术和先进的数控系统,实现设备的自动化操作和无人化生产; 通过采用新型的环保材料和节能技术,实现生产的绿色化和可持续性。
然而,在发展的过程中,我们也面临着一些挑战。首先,如何将先进的自动 化技术应用到传统的复合材料生产中,实现两者的有机结合,是一个亟待解决的 问题。其次,随着环保要求的日益严格,如何在保证产品质量的前提下,实现生 产的环保和可持续性,也是一个重要的课题。最后,如何提高设备的可靠性和稳 定性,降低设备的维护成本,也是我们需要解决的一个重要问题。
3、个性化和多样化:随着消费者需求的多样化,复合材料制品的形状、尺 寸和性能也要求更加多样化和个性化。因此,设备制造商需要针对不同领域和产 品的需求,提供更加灵活和多样化的设备方案。
4、智能化和自动化:通过引入人工智能、机器视觉等技术,实现设备的智 能化和自动化控制,可以提高设备的精度和稳定性,减少人工干预和操作失误, 提高产品质量和生产效率。
感谢观看
存在的问题与挑战
虽然国内外在热压罐成型技术方面取得了一定的进展,但仍存在一些问题和 挑战。具体表现在以下几个方面:
1、设备成本高:目前,高端热压罐成型设备的价格较高,给一些中小型企 业带来较大的经济压力。
2、技术水平有待提高:与发达国家相比,我国在热压罐成型技术方面还存 在一定差距,需要进一步提高技术水平和研发能力。
国内外复合材料工艺设备发展 述评之八热压罐成型
目录
01 引言
03 国内外发展现状
02 热压罐成型技术概述 04 参考内容
引言
热压罐成型复合材料成型工艺的常见缺陷及对策
热压罐成型复合材料成型工艺的常见缺陷及对策热压罐成型复合材料成型是一种常见的制造工艺,它可以生产出具有优良性能的复合材料制品,被广泛应用于航空航天、汽车、船舶、建筑等领域。
由于材料的特殊性和成型工艺的复杂性,常常会出现各种缺陷,影响产品的质量和性能。
本文将就热压罐成型复合材料成型工艺常见的缺陷及对策进行详细的介绍。
一、常见的缺陷1. 毛细孔毛细孔是指在复合材料制品内部出现的微小气孔。
造成毛细孔的原因有很多,比如树脂固化不完全、吸湿、气泡等,常常出现在厚度较大的复合材料制品中。
2. 气泡气泡是指在复合材料制品内部或表面出现的气体囊泡。
气泡的出现会导致产品密度不均匀,降低其抗压强度和韧性。
3. 残余应力残余应力是指在成型过程中产生,但又没有完全消除的应力。
残余应力会导致产品在使用过程中产生变形或开裂现象。
4. 凹坑和凸起凹坑是指在产品表面出现的凹陷,凸起则是指在产品表面出现的凸起。
这些缺陷会影响产品的外观质量。
5. 产品几何尺寸不合格由于成型过程中操作不当或模具设计不合理等原因,产品的几何尺寸可能出现偏差,不符合设计要求。
二、对策要避免毛细孔的出现,首先要保证树脂的固化充分,可以加长固化时间或提高固化温度。
其次要保持材料的干燥状态,避免吸湿现象的发生。
在成型过程中需要注意排气,尽量避免气泡的出现。
对于气泡的对策,可以采用真空吸气技术,在成型过程中对材料进行真空处理,尽量排除内部空气,减少气泡的生成。
还可以在树脂中添加消泡剂,提高材料的抗气泡能力。
残余应力的消除是一个比较复杂的问题,可以通过优化成型工艺、合理设计模具结构等措施来减少残余应力的产生。
在产品成型后,可以通过热处理或添加应力消除功能层来消除残余应力。
对于凹坑和凸起,可以通过优化模具结构、调整成型参数等措施来改善产品表面质量。
选用适当的脱模剂和表面处理工艺也能减少这些表面缺陷的发生。
产品几何尺寸不合格的原因有很多,可能是成型模具设计不合理,也可能是操作过程中出现失误。
- 1、下载文档前请自行甄别文档内容的完整性,平台不提供额外的编辑、内容补充、找答案等附加服务。
- 2、"仅部分预览"的文档,不可在线预览部分如存在完整性等问题,可反馈申请退款(可完整预览的文档不适用该条件!)。
- 3、如文档侵犯您的权益,请联系客服反馈,我们会尽快为您处理(人工客服工作时间:9:00-18:30)。
一、热压罐成型工艺
热压罐成型技术是航空、航天领城应用最广泛的成型技术之一,它能在宽广范圈内适应各种材料对加工工艺条件的要求。
二、工艺过程包括:
1、模具清理和脱模剂涂抹。
2、预浸料裁切与铺叠。
3、真空袋组合系统制作和坯件装袋.
真空袋组合系统制作需要采用各种辅助材料,其中包括:真空袋材料(改性尼龙薄膜或聚酸胺薄膜)、橡胶密封胶条、有孔或无孔隔离膜(聚四氟乙烯或改性氟塑料)。
吸胶材料、透气材料、脱模布和周边胶条等。
按图、所示顺序将坯件与各种辅助材料依次组合并装袋,形成真空组合系统。
装袋后应进行真空检漏,确认无误后,便可闭合锁锁热压罐门,升温固化。
1.真空袋.
2.透气材料.
3.压板0
4.有孔隔离层
5.预浸料叠层,
6.有孔脱模布,
7.吸胶材料,
8.隔离膜面.
9.底模板,10.周边挡条.
11.周边密封带 12.热压罐金属基板 13.密封胶条,14.真空管路。
4、固化。
各种树脂体系的固化制度,应根据各种不同树脂体系的固化反应特性和物理特性分别给
予制定,要慎重考虑加压时机和关闭真空系统的时机。
固化完毕要控制降温速率,以防止因
降温速度过快导致制品内部产生残余应力。
5、出罐脱模。
罐内温度降至接近室温时方可出罐脱模。
6、检测与修整。
三、成型过程中的危险性分析
由于根据现场使用方介绍,所有预浸料工序均外委完成,该工房主要进行铺料和成型工序,在此仅对成型过程中的危险性进行分析。
1、辅助材料可燃性
由下图可以看出,热压罐成型过程的物理化学变化,一般都会达到120-160℃,因此热压罐
成型工艺所选择的辅助材料都应该在此温度范围内不应发生化学变化,物理性能稳定。
各种
材料均选用阻燃材料,不应存在发生火灾的危险。
2、设备的阻燃性
设备的系统分为:罐体、罐门、开门系统、加热系统、冷却系统、加压系统、空气循环系统、真空系统、隔热系统、控制系统等组成,产品的设计均按照国家机电产品安全标准要求
设计。
设备的原材料、电气元器件均按照阻燃设计,隔热材料为阻燃材料,不存在发生火灾
的隐患。
设备电气系统均进行安全防护、接地可靠,不存在引发火灾危险。
3、产品主材的危险性
本设备加工产品为树脂型复合材料,主要构成成份为树脂、纤维、固化剂、交联促进剂等。
在几种组分中:固化剂、交联剂用量极少,纤维没有可燃性,最为可能发生危险的应该是树脂。
对环氧树脂的安全评价:造成液态物质燃烧的一个关键参数就是“闪点”,在安全评价中要用
物质的“闪点”来判定其燃烧等级。
可是在标准手册中给出的环氧树脂的“闪点”差别很大!在“新编危险物品安全手册”(化学工业出版社2001年4月第一版)在428 页中给出的环氧树脂
闪点为4. 4 ℃按此手册数据值,环氧树脂火灾危险性分类为甲B 类;根据GB1 3690-92“危险化学品安全技术全书”615页关于环氧树脂一节内容介绍,环氧树脂性能如下:“相对分子质
量350-8000,CAS 号23969-06-0,危险性类别第3. 2 类中闪点,燃烧性易燃,闪点无意义,
爆炸下限12mg/m3,引燃温度490℃,爆炸上限无资料。
”进一步查阅GB13690-92 中华人民
共和国国家标准,在“常用危险化学品的分类及标志”第3. 2 类所列的997 种常用危险化学品
明细表无环氧树脂记载。
如按第3. 2 类中闪点来判别环氧树脂火灾危险性分类为乙类。
根据环氧树脂引进技术提供的
安全数据来看,双酚A型通用树脂"闪点"为大于200℃,按此数据环氧树脂火灾危险性分类
为丙类,那么环氧树脂火灾危险性分类究竟是甲、乙、丙类中哪一类呢?
这类问题应该引起制订安全标准的部门重视!如果将环氧树脂划为甲B 类,那么将要加大安
全设施的投资,如果划为丙类可能会使一些使用落后技术生产的环氧树脂的用户,在安全措
施不到位的情况下产生事故隐患。
按照目前国内环氧树脂生产技术差距很大,以及有关环氧树脂的安全数据标准不统一的实际
情况,应该对具体的生产厂出品的具体牌号实样检测其“闪点”,在积累数据的基础上适时的
制订相关标准。
环氧树脂是否属危险物品?在“新编危险物品安全手册”(化学工业出版社2001 年4 月第一版)p428 是这样写的:“危规分类及编号易燃液体GB3. 2 类32197------。
危险特性易燃闪点4. 4℃”
按此闪点环氧树脂属甲类火灾危险物品。
而在中华人民共和国国家标准“危险货物品名表”(GB1 2268-90)这个标准中,环氧树脂是否属危险物品划定得非常详细。
在本标准编号为32197 栏目中是这样划定的:“含一级易燃溶剂的合成树脂(闪点-1 8—23℃)如:醇酸树脂、酚醛树脂、有机硅树脂、环氧树脂。
”由标准的描述,可非常清楚地知道含一级易燃溶剂的合成树脂(闪点-1 8—23℃)的环氧树脂才属于危险物品的范畴。
哪些闪点大于23℃的环氧树脂就不在此列。
为此不分清红皂白地将环氧树脂统统作为危险物
品来处理,是不符合国家标准的规定的。
而我们进行热压罐成型选择的环氧树脂其闪点都大于70℃,引燃温度大于490℃。
在成型过
程中产品处于真空环境,已与氧气隔绝,温度也远低于490℃,产品不可能存在被引燃的风险。
•结论
综上,采用热压罐成型技术制备复合材料整个过程是安全的,不存在消防隐患。